Chase Center isn’t just an arena, it’s a destination. Officially opened on Sept. 6, 2019, the new state-of-the-art venue is a sports and entertainment hub and a beacon for the entire Bay Area. Home to one of the NBA’s most iconic franchises, the six-time NBA Champion Golden State Warriors, the arena hosts concerts and events Read more
Featured Articles
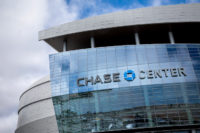
Chase Center isn’t just an arena, it’s a destination.
Officially opened on Sept. 6, 2019, the new state-of-the-art venue is a sports and entertainment hub and a beacon for the entire Bay Area. Home to one of the NBA’s most iconic franchises, the six-time NBA Champion Golden State Warriors, the arena hosts concerts and events and will boast a booming culinary and retail presence.
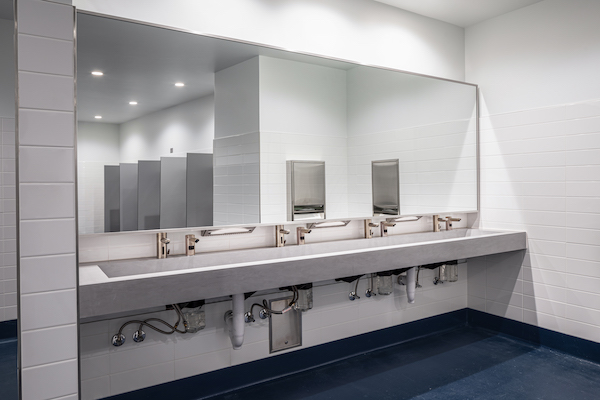
With a beautiful skyline overlooking the San Francisco Bay and an upscale aesthetic throughout the entire facility, Chase Center is one-of-a-kind. The 18,064-seat privately-financed arena’s design is matched only by its commitment to sustainability. Engineered to achieve LEED Gold certification, the facility has adopted numerous eco-friendly practices.
With a need for commercial restroom products that are both sustainable and eye-catching, Chase Center relied on Sloan products as part of the larger focus on a seamless, world-class fan experience for the new era of entertainment in San Francisco.
San Francisco Sustainability
Nestled in San Francisco, one of the most drought-stricken regions in the United States, Chase Center specified Sloan flushometers to help combat water shortage and recycle the earth’s most precious resource. Sloan Royal 111-1.28 SFSM and Royal 186-0.125 SFSM Sensor Flushometers — equipped with reclaimed water features — are specifically designed to withstand the harsh conditions presented by reclaimed water while conserving water at the same time. Sloan flushometers are an effective complement to Sloan ST-2459 wall-hung water closets as well as SU-1009 and SU-7009 urinals in restrooms throughout all levels of the arena. These Sloan water closets and urinals are designed to withstand the wear and tear that comes with a high-traffic environment. Chase Center hosts a 41-game NBA regular season and a full slate of concerts throughout the year. Not only do these Sloan fixtures meet the high durability needs of the arena, but also the vitreous china composition presents an easy-to-clean, sleek aesthetic.
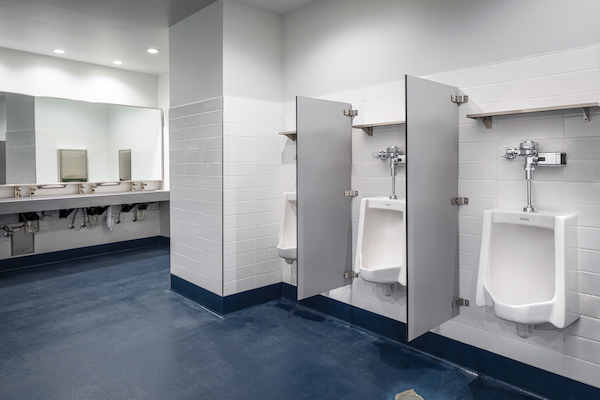
Brushed Nickel by the Bay
The state-of-the-art sports and entertainment destination needed restroom products that met its sustainability standards and created a high-end aesthetic that would leave a lasting impression on guests. The solution was Sloan’s custom Brushed Nickel finishes for EAF-250-ISM Faucets and matching ESD-2000 Soap Dispensers. When these products were specified for the entire facility, they created a unified aesthetic and added an element of comfort for the whole arena. Thanks to Physical Vapor Deposition (PVD) properties of the Brushed Nickel finish, fingerprints and watermarks do not appear on the products, minimizing maintenance concerns and contributing to their aesthetic value. Sloan’s Brushed Nickel faucets and soap dispensers were paired with 2, 4, and 5-station Designer Series™ Gradient trough sinks to complement the design. These sensor-activated faucets and soap dispensers provide users a more hygienic, touch-free handwashing solution. Additionally, Sloan SF-2350 Polished Chrome faucets were paired with SS-3002 vitreous china lavatories.
“One of Chase Center’s goals is to create a place that will provide people with lasting memories,” said Michael Sciortino, VP, Operations, Golden State Warriors/Chase Center. “Thanks to Sloan’s beautiful products and their ability to save water by using reclaimed water flushometers, we’re able to make the restroom a part of that unforgettable experience, while also contributing an eco-friendly solution.”
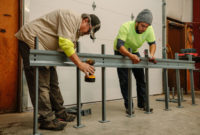
From Devil’s Tower in the east to the Grand Tetons and Yellowstone National Park in the west, Wyoming is known for its natural beauty and opportunities for outdoor recreation. With six people per square mile, only Alaska is more sparsely populated. Wyomingites are accustomed to a unique set of challenges. Driving one hundred or more Read more
From Devil’s Tower in the east to the Grand Tetons and Yellowstone National Park in the west, Wyoming is known for its natural beauty and opportunities for outdoor recreation. With six people per square mile, only Alaska is more sparsely populated.
Wyomingites are accustomed to a unique set of challenges. Driving one hundred or more miles in a day is relatively commonplace. Daily temperature swings can easily exceed 40°F. Summer temps break 100°F, and golf ball-sized hail can materialize at any time. In the winter, the mercury is known to plunge well into the double digit sub-zero realm. And then there’s the wind…
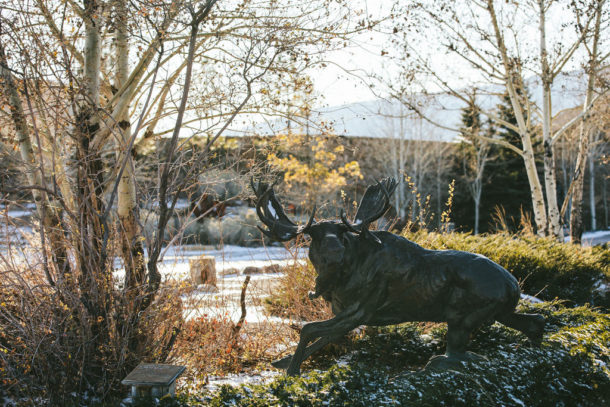
Downtown Cody is full of bronze statues commemorating its wild heritage and the rich wildlife that surrounds – and sometimes enters – town.
Mechanical contractors in the Cowboy State have evolved to take all of this in stride. There aren’t but a dozen or two commercial outfits in Wyoming; one or two in each community – maybe.
“As the name implies, we serve the Bighorn Basin, which is essentially the territory between the Bighorn and Absaroka mountain ranges,” said Will Poindexter, VP at Basin Mechanical in Cody, WY. The company is known for its quality work in the commercial and industrial spaces. “We’ll go as far as the Colorado or Idaho border when needed.”
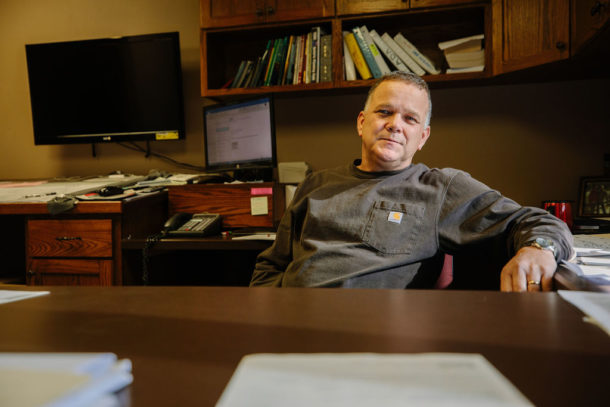
Basin Mechanical VP Will Poindexter. Basin Mechanical is a commercial Plumbing, heating and cooling contractor based out of Cody, Wyoming.
“Schools and hospitals are big markets for us,” he continued. “There are a number of general contractors who call on us when they’re working on educational or medical facilities anywhere in the state. We also deal with water treatment and other municipal facilities quite frequently.”
Even the kitchen sink
Basin Mechanical’s company logo – a pack mule loaded with everything from golf clubs to drafting equipment – is humorous by design, yet symbolic of how a commercial contractor in Wyoming needs to travel.
“The mule is a throwback to 40 years ago when the company’s founder, Gordon Allison, moved to Cody with everything he owned, mules and all, to start the company and to forge a new life,” explained Poindexter. “But in a way, it resembles how we travel to jobsites across the state. Supply houses are few and far between, and depending when and where a job takes place, it’s entirely possible that roads could be shut down. Everything we could possibly need must be on the truck.”
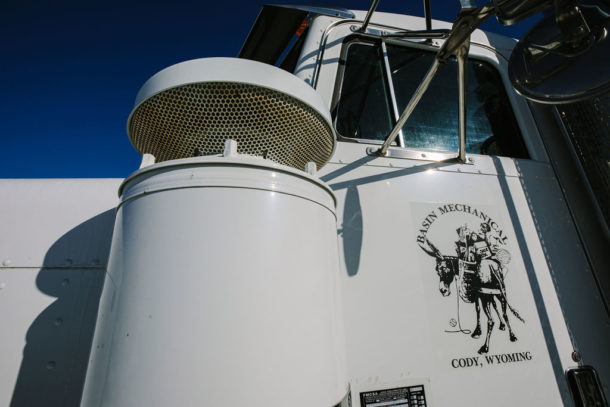
Given the many miles between supply houses and jobsites, Basin Mechanical travels to jobs with a semi-truck containing everything they may need on the project, which is a can’t miss on the highways with the company’s unique pack mule logo.
So Basin regularly travels with a tractor trailer. In other places, that might seem like overkill for a medium-sized company tackling medium-sized projects, but not in Wyoming.
“Distances and volatile weather might be unique to the western states,” said Poindexter. “But we battle some of the same challenges that contractors everywhere deal with, especially the workforce shortage. Finding enough skilled manpower can be really tough. With about 10,000 people in all, Cody isn’t home to a huge workforce.
Curbing labor
One of Basin’s answers to the workforce challenge is working smarter, not harder.
“Labor is always an issue, so we’re constantly looking for products or systems that will minimize our time in the field. From press fittings to design software, if we can take hours off a job while simultaneously increasing the quality of our product, we want to learn more about it.”
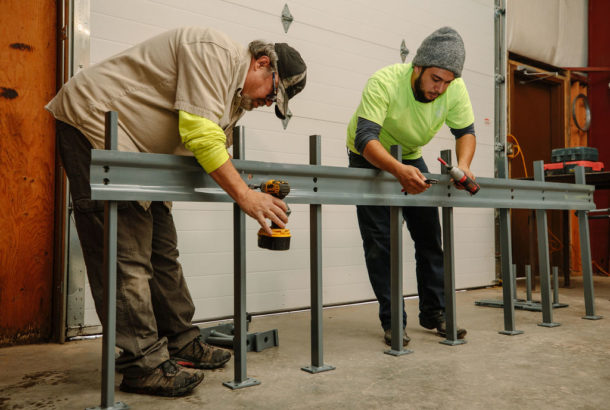
David Ellis, Jobsite Supervisor (L) and Ryan Meier, Apprentice assemble the Watts LavEx in preparation for installation.
One of the most recent solutions Basin has implemented comes from the use of Watts LavEx lavatory carriers. Schools in particular generally feature large restrooms with multiple sinks. It takes quite a bit of time to individually hang each lavatory and ensure each sink is at an identical height.
“The LavEx carriers are available for applications from one to four sinks,” said Poindexter. “With this system, we can rapidly install multiple sinks on a single, rock solid structure.”
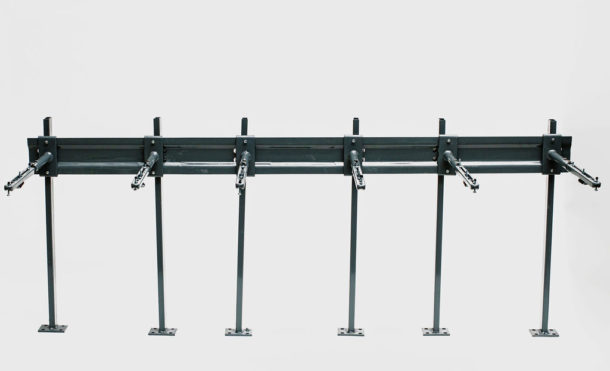
Watts LavEx
Designed for use through a block wall, LavEx carriers are ideal for prefabrication or on-site construction. Both the height of the carriers and the length of the support arms are quickly adjustable.
“It took us 15 minutes to completely assemble the four-sink LavEx carrier the first time we used one,” said Basin Jobsite Supervisor, David Ellis. “The height of the track that carries the support arms gets measured on either side of the unit, and that’s it; all the sinks will be perfectly level at the same height.”
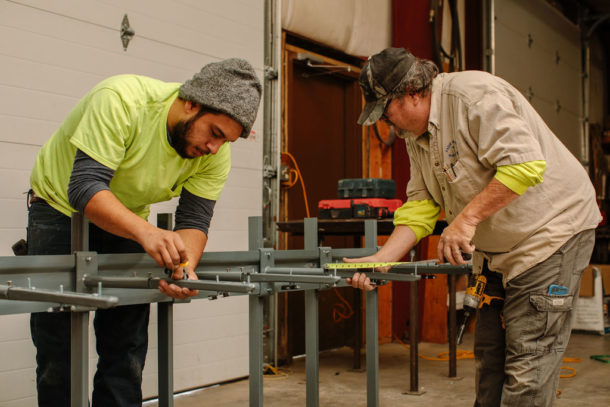
Ryan Meier, Apprentice (L) and David Ellis, Jobsite Supervisor assemble the Watts LavEx in preparation for installation.
“The units are designed for block wall applications, but could easily be used through a 2-by-six wall because they’re free-standing,” he continued. “Everything about the system is heavy duty, so we can assemble them in our shop, place them in the truck, and make minor adjustments in the field.”
Trusted source
“We tend to be a little hesitant while implementing new technologies we find, only because we need to be sure that the quality and support is there before we’ll install it in a customer’s facility,” said Poindexter. “But the lav carriers come from a brand whose commercial products we use all the time. We get great results with Watts components. A lot of our jobs feature Watts trench drains, mixing valves, and pressure reducing valves. It’s all readily available at our wholesalers, too.
Winter in northwest Wyoming always slows the pace of work to a degree, but ongoing Basin projects include a new manufacturing facility downtown, a wastewater treatment plant, and in nearby Thermopolis, a new rehab center.
Poindexter and Ron Couture, Estimator and Project Manager, are busy bidding projects for 2020 and beyond.
There’s a new school in Sheridan currently in the design phase, the Wild Sheep Foundation is building a new visitor center in Dubois, two new pharmacies are planned in Powell and Worland, and Powell Valley Healthcare is soon adding a new emergency room.
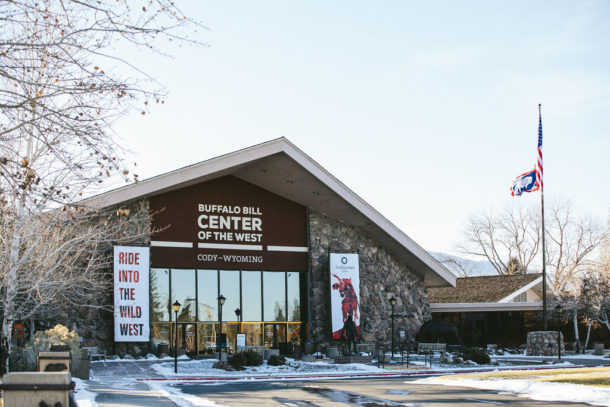
Known as both the Heart of the West and the Rodeo Capital of the World, Cody, WY, is full of old western flair and museums of every kind.
“We do everything as though our reputation depends on it, because it does,” concluded Poindexter. “Though the country’s wide open, the communities are small, so everything we do is noticed, and noted. Our reputation for quality work means everything in our part of the country.”
Plenty of room, and work, to grow. With the right resources in place, and solid work ethic, Basin Mechanical’s got a recipe to get the jobs done properly.
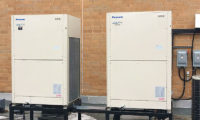
Medical offices are complex spaces with unique requirements, and often have older, inefficient design and systems that need upgrading. Retrofits are necessary to ensure patient comfort and care, but as medical offices can’t simply shut down, it can be challenging to complete an update. A recent example of a successful medical office HVAC retrofit is Read more
Medical offices are complex spaces with unique requirements, and often have older, inefficient design and systems that need upgrading. Retrofits are necessary to ensure patient comfort and care, but as medical offices can’t simply shut down, it can be challenging to complete an update.
A recent example of a successful medical office HVAC retrofit is a project in Kentville, Nova Scotia. Through a collaborative effort the stakeholders were able to effectively schedule the overhaul of all the interior zones in the medical building to bring it up to current standards and fit the requirements of the office. The owners wanted an energy-efficient heating and cooling system that was easy to use and would allow for independent control in each space as well as savings on future energy bills.
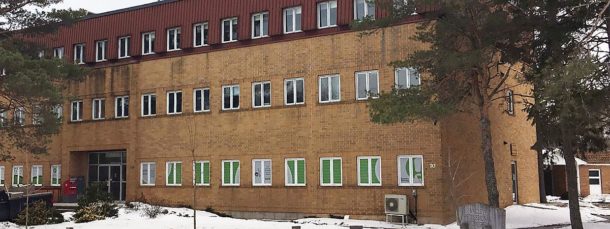
Given that the renovations needed to be done while the offices conducted regular business, the challenge was to work with minimal disruption. Additionally, work had to be completed outside of the medical office’s regular hours of operation, meaning there was a small time frame during which work could be done each day. Panasonic also had to work with limited space for the heating and cooling units and that had to be concealed as much as possible.
PANASONIC SOLUTION
Due to the space and installation restrictions as well as the features the client wanted, a new three-way Panasonic (heat recovery) Variable Refrigerant Flow (VRF) system with a combination of multiport and individual heat recovery boxes was designed. The advantages of this state-of-the-art system include individual and precise control of heating and cooling needs in different areas rather than a single temperature setting for the whole building. This allows everyone to enjoy a comfortable indoor environment, conserving energy and generating cost-savings on energy bills. Plus, installing a VRF system allows owners/operators to optimize the lifecycle cost of the project and realize long-term savings thanks to its energy efficient technology.
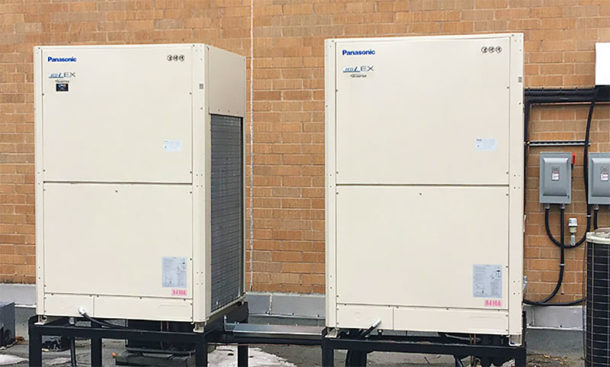
The advantages of the system include easy installation and minimum intrusion to the envelope of the building, as copper pipes that contain refrigerant are being used instead of extensive and costly ductwork. Customers also benefit from pre-installation training and technical support, which is essential for successful operation of the unit.
CUSTOMER EXPERIENCE
The project was a great success, with the units operating smoothly to keep the office temperature comfortable while saving energy. The overall feedback from users has been that they appreciate being able to have independent control of the heating and cooling in their area, and that temperatures are well maintained throughout the building. The system is simple, user-friendly and efficient, and the indoor units blend in nicely with the interior and are aesthetically pleasing.
Chuck Hazel, the senior mechanical contractor from C.Tech Refrigeration, a division of the Baxter Group of Companies was very happy with the outcome.
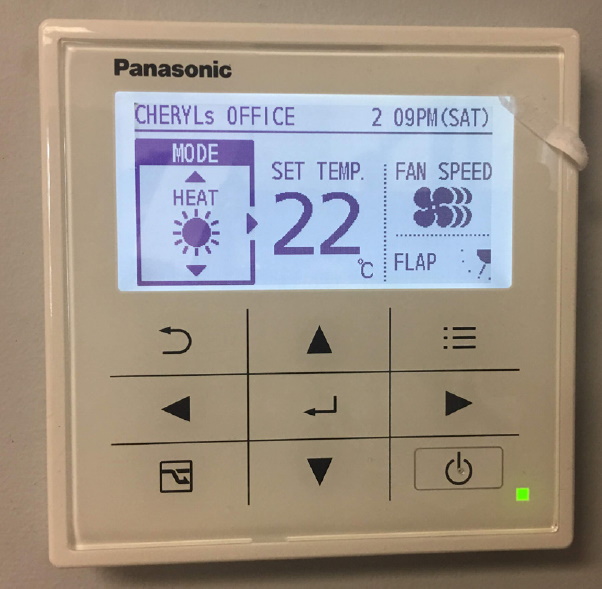
“We got a lot of support from Panasonic – from pre-installation to installation and post-installation. The Panasonic VRF system was easy to install and has been seamless for the client. Panasonic delivered on their promise of a top-quality system and I would recommend and work with them on future projects.”
PROJECT SYNOPSIS
CHALLENGES: Medical offices are complex spaces with unique requirements, and often have older, inefficient design and HVAC systems that need upgrading. Retrofits are necessary to ensure patient comfort and care, but as medical offices can’t simply shut down, it can be challenging to complete an update. The building was looking for a solution to replace their existing HVAC solution that was flexible with their requirements and could be completed with minimal disruption outside of regular business hours.
SOLUTIONS: Due to the space and installation restrictions as well as the features the client wanted, a new three-way Panasonic heat recovery Variable Refrigerant Flow (VRF) system with a combination of multiport and individual heat recovery boxes was designed.
RESULTS: The project was a great success, with the units operating smoothly to keep the office temperature comfortable while saving energy. The overall feedback from users has been that they appreciate being able to have independent control of the heating and cooling in their area, and that temperatures are well maintained throughout the building.
To learn more visit www.panasonic.com/ca/vrf
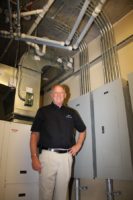
With modest beginnings more than a century ago in 1894, Episcopal Homes in St. Paul, Minn., has grown to provide hundreds of residents with senior care while offering a wide variety of amenities, including a fitness center, pool, salon, theatre, cocktail lounge and fine dining. The continued growth with aging baby boomers created the need Read more
With modest beginnings more than a century ago in 1894, Episcopal Homes in St. Paul, Minn., has grown to provide hundreds of residents with senior care while offering a wide variety of amenities, including a fitness center, pool, salon, theatre, cocktail lounge and fine dining.
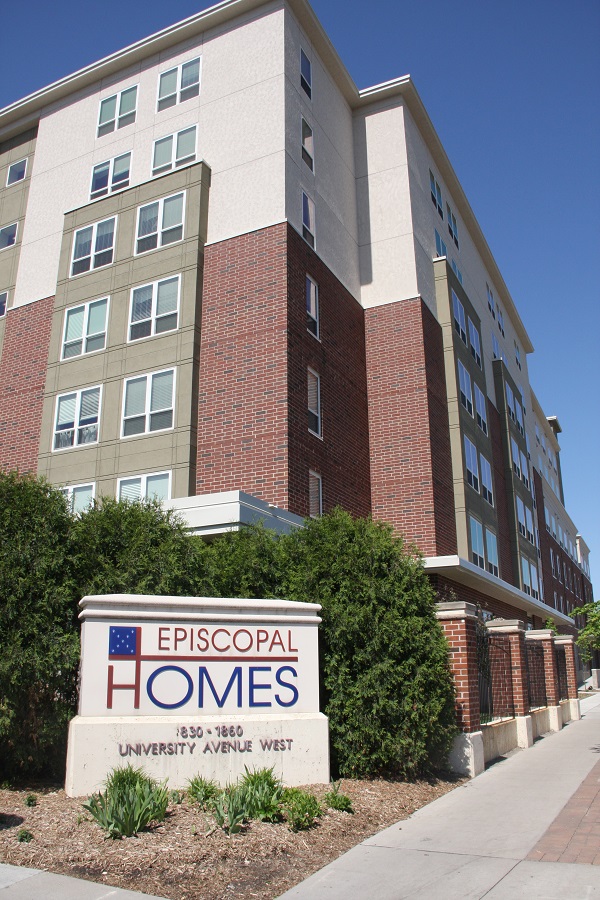
The continued growth with aging baby boomers created the need for yet another expansion, prompting owners to invest $45 million for 168 more units to the ever-growing complex. The project included a seven-story, post-tension, concrete-engineered building, and R.T. Moore Co., a Burnsville, Minn.-based contractor, was chosen for the plumbing and mechanical work.
The plumbing and mechanical piping included PEX in sizes 2″ and down. The plumbing system used 32,000 feet of ½” to 2″ Uponor AquaPEX® pipe along with 2,200 ½” to 2″ ProPEX® engineered polymer (EP) expansion fittings. The mechanical system used more than 4,000 feet of ½” to 2″ Wirsbo hePEX™ pipe along with PEX-a Pipe Support from Uponor. The pipe support, which is listed for plenums, also provides increased hanger spacing similar to copper pipe and helps to limit the natural expansion and contraction of PEX.
Dean Kirchoff, lead mechanical project manager for R.T. Moore, and a master plumber with 30 years of experience in the industry, said using PEX helped them stay on budget with labor and material savings. “Using PEX allowed us the flexibility to route the lines and minimize conflicts with other trades,” he added. “Plus, the pipe can be joined without the use of glues or flame.”
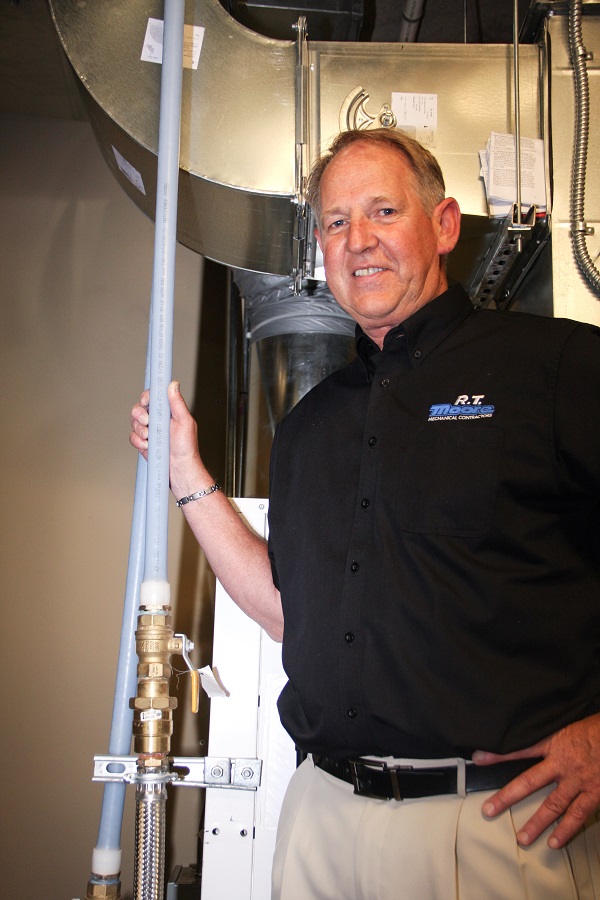
R.T. Moore chose Associated Mechanical Contractors from Shakopee, Minn., to install the hydronic and HVAC system. “The system is a condenser water closed-loop system set up with a dead band on the loop with the water temperature between 76°F and 84°F,” Kirchoff said. “Within that range, there is no mechanical equipment operating – no chiller or boilers. When the condenser water falls below 76°F, the boiler system adds hot water to the system. When the condenser water gets above 84°F, the cooling tower adds chilled water to the system. This allows the heat pumps to work within the dead-band range at the maximum efficiency.”
R.T. Moore worked with Uponor early on to assist with the sizing and sleeve layout locations for each of the plumbing, condenser loop and condensate draining systems. “We maximized the flexibility of the system design using multiport tees with PEX, thus decreasing the amount of joints in the system,” Kirchoff said. “We also installed risers from the first floor to the seventh floor, grouping bathrooms and grouping the kitchens.”
Episcopal Homes was very satisfied with the final result. “This project was successful because of the experience of its contractors and their superior workmanship,” Anne Kamiri, special projects coordinator for Episcopal Homes, said. “The project has received much praise and recognition from the community.”
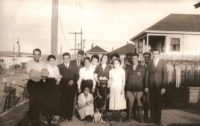
Located in the East Bay area of Oakland, near the hollow ground of Oakland Alameda Coliseum, AB&I Foundry has been finding ways to build on its legacy and cutting-edge innovations for over a century. In fact, as a leading producer of cast iron soil pipe, fittings and castings with a distinct black and silver look Read more
Located in the East Bay area of Oakland, near the hollow ground of Oakland Alameda Coliseum, AB&I Foundry has been finding ways to build on its legacy and cutting-edge innovations for over a century. In fact, as a leading producer of cast iron soil pipe, fittings and castings with a distinct black and silver look, one may also wonder where and how the Oakland Raiders came about creating their brand identity nearly 70 years ago. It’s said that AB&I’s Boscacci family was vital in assisting the Raiders establish their community footing and possibly sharing their tradition colors.
Community and team are critical to the history and the future of AB&I. When you drive by the foundry, you can’t miss the big mural that runs a city block on the wall outside of the company. It shows the history of the company through various milestones and despite the location in an industrial area, the wall has never been defaced. One might surmise that this is the ultimate type of respect AB&I has built in the community through their commitment of employing, educating and providing for generations of families. How did it start?
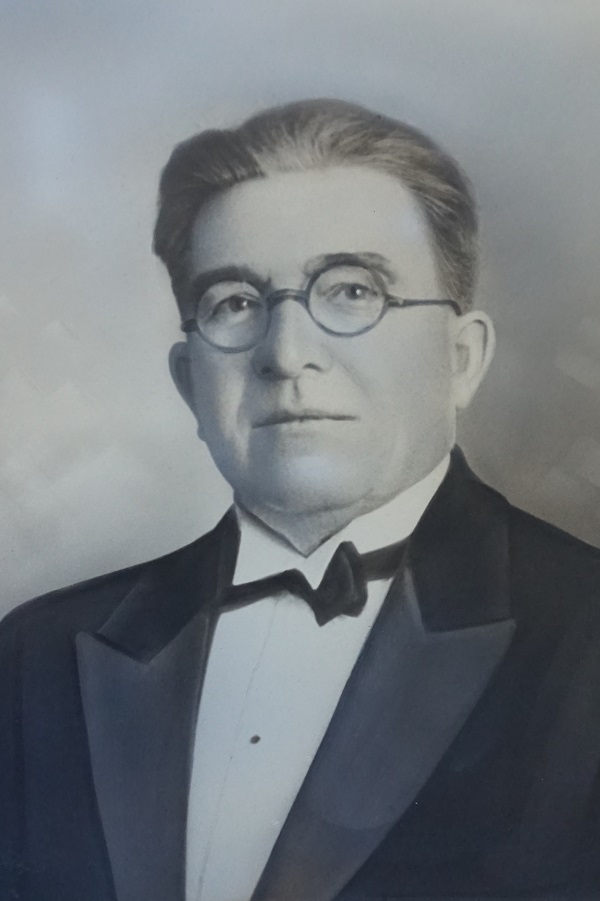
Joseph Boscacci
Joseph Boscacci emigrated from Switzerland to the U.S. in the 1890s, bringing with him an artisan craft. In the wake of the Great San Francisco earthquake and fire of 1906, the young Boscacci worked at General Foundry in San Francisco making bronze statuary, brass street lamps and ornate iron work that was needed for the city’s rebuilding effort.
He also ran his own foundry business on the weekends in the backyard of his home in Oakland. Boscacci and his five sons made a variety of castings, including cast iron fittings, window sash weights and cast iron stove tops for wood burning cook stoves. He called his company American Brass & Iron.
As the decades unfolded and American industry grew, so did the need for cast iron pipe and fittings. By the 1920s, all the Boscacci brothers were involved in the family business. In 1941 the company was moved to their current location on San Leandro Street in Oakland. Just after World War II, brothers Arnold and Eugene took over the foundry and rebranded to AB&I.
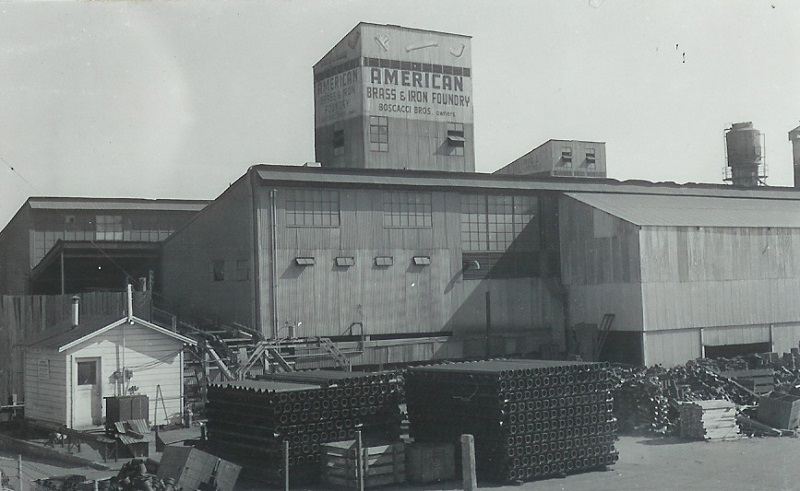
American Brass and Iron Foundry in the 1920s
It was the post-war return of the GI’s and housing boom (not too mention ensuing baby boom), that reignited the ever-entrepreneurial Boscacci family back into full production of cast iron pipe and fittings to the ever-increasing demands caused by massive construction boom.
By 1950, AB&I was a leading West Coast foundry and was a founding member of the Cast Iron Soil Pipe Institute (CISPI). Later, AB&I was among the first to champion no-hub cast iron pipe, fittings and couplings, creating its own machines to make no-hub cast iron soil pipe. Ingenuity, forward-thinking and a little risk taking also drove the family to implement automated manufacturing methods.
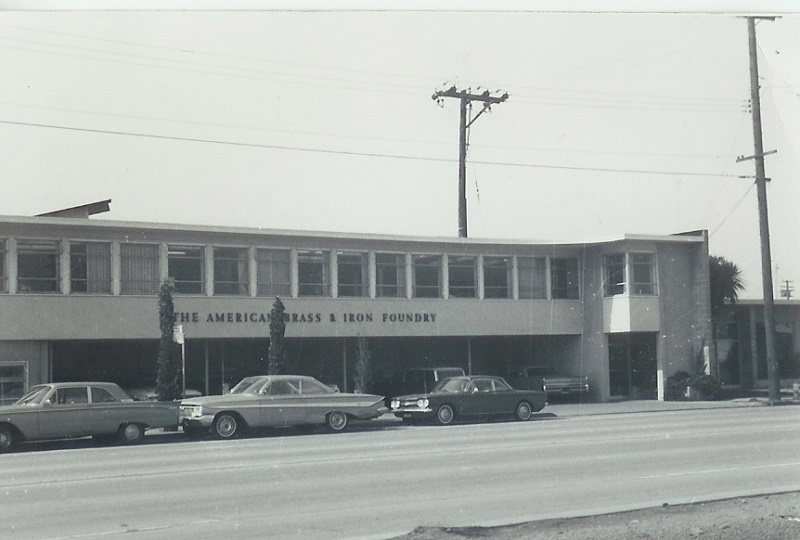
AB&I in the early 1960s
In the 1960s, the company expanded from selling products mainly in California to distribution across the Western United States. AB&I recognized that establishing relationships was fundamental to the company’s future. They sustained close supply-chain engagement with distributors lasting decades. It was the legacy of those early relationships that still exists today. AB&I believes that integrity is paramount to the company’s success and that you must “do what you say you will do and that best practices in business start with common sense, developing good relationships and attention to detail.”
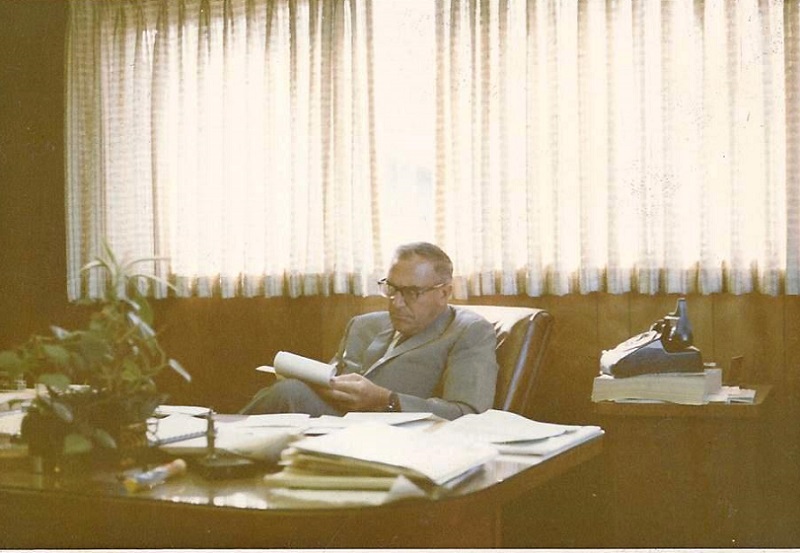
Arnold Boscacci, mid-1960s
By the third generation of Boscacci family leadership, AB&l’s mission was sternly focused on ways to use new technology to make the best cast iron pipe and fittings in the Western US. Allan Boscacci was now making decisions and with most of the work still being completed by hand, he began to introduce higher production levels and enhance modernization efforts. AB&I was predictably ahead of its time environmentally, installing bag houses to capture foundry smoke, and water treatment plants to clean and reprocess foundry water long before it was a requirement.
In 1969, AB&I was the first soil pipe foundry to install a Disamatic (DISA ) molding machine, automating foundry processes which allowed a higher-quality fitting at a much faster rate.
In the 1980s, AB&I was among the first American manufacturers to engage in profit sharing with all team members and to truly practice “open book” management. By the early 1990s, AB&I was the first foundry to totally automate its pipe production.
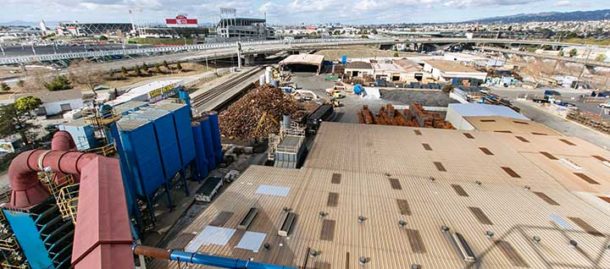
Overhead at AB&I Foundry in Oakland
The industry has seen its share of attrition. In its glory, America had 39 foundries that and only three remain today. Consistent with being the “Foundry of the Future,” today’s AB&I has the most sophisticated molding machine in the world, a DISA 270A, and is among those making the highest-quality cast iron pipe and fittings in the world.
AB&I joined McWane, Inc., a large family-owned manufacturer, but remains Boscacci family led. Kurt Winter, Allan ‘s oldest son-in-law drives AB&I to be “better, faster and more innovative,” just as the three generations of foundry men before him.
AB&I supports our plumbing industry with vigorous involvement and are highly active with leading national, regional and local industry organizations including: ASA, MCAA, PHCC, ICC, IAPMO, DBIA, ASPE, ASTM and CISPI.
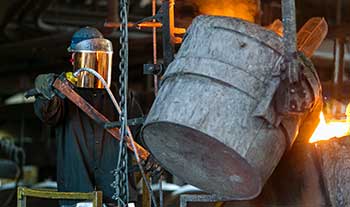
Custom casting at AB&I Foundry
Today’s AB&I, which employs over 200 team members, is a thoroughly modem, technology-driven foundry committed to responsible manufacturing and safety. They are an environmentally conscience U.S. manufacturer that have invested millions in environmental programs involving air, land and water. In fact, AB&’ls water treatment system is set up so that every drop of rainwater that hits their roof is captured and run through a filtration process and recycled. AB&I aims to be great stewards of the environment for future generations.
Next month will will look at the future of AB&I and share a recent Q&A interview with their team.