https://vimeo.com/1106478682 Milwaukee PipelineInfrastructure Report CardThe 2025 OESP Dave Nelsen Scholarship WinnersCorn SweatPACKOUT™ Rack KitPodcasts Milwaukee Pipeline Pipeline is Milwaukee Tool’s exclusive trade‑media reveal event, held annually. It has evolved from past symposium formats (like their New Product Symposium) and has carried the “Pipeline” name since 2020. As with past years, expect a mix of trade‑specific Read more
Featured Articles
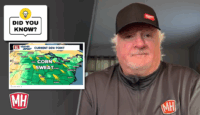
Table of Contents
Milwaukee Pipeline
Pipeline is Milwaukee Tool’s exclusive trade‑media reveal event, held annually. It has evolved from past symposium formats (like their New Product Symposium) and has carried the “Pipeline” name since 2020. As with past years, expect a mix of trade‑specific equipment (electrical, plumbing, outdoor, mechanical), system enhancements, and smart innovations integrated with their One‑Key ecosystem. Mechanical Hub Media will be onsite to share coverage to our audience, August 21st. Stay tuned for more information.
Infrastructure Report Card
The American Society of Civil Engineers’ (ASCE) 2025 Report Card for America’s Infrastructure, released in March 2025, assigns the U.S. an overall grade of C, which marks the highest infrastructure assessment since the report began in 1998. John and Tim’s home state of Illinois received a C-, while Eric’s state of Minnesota edged out Illinois to receive a solid C.
The 2025 OESP Dave Nelsen Scholarship Winners
The National Association of Oil and Energy Service Professionals (OESP) recently announced the winners of the 2025 Dave Nelsen Scholarship at its annual Eastern Energy Expo in Atlantic City, NJ. The scholarship was established in 1999 to remember and recognize the commitment to education made by OESP member Dave Nelsen. It is awarded to students or technicians who are currently or planning to attend a technical college or trade school, pursuing a career in the oil and energy industry.
Corn Sweat
Yes, it’s a thing! In fact, if you’re in Iowa or Illinois during peak growing season and it’s 93°F but feels like 105°F—it’s likely not just the sun. Corn sweat refers to the humidity released into the atmosphere by corn plants through transpiration—a natural process where plants draw water from the soil and release it as water vapor through tiny pores in their leaves.
PACKOUT™ Rack Kit
PACKOUT™ Rack Kit is a versatile and durable modular storage system, delivering ultimate PACKOUT™ access and organization with sliding drawers that allow access to storage without unstacking. This solution can stack and expand across a wall to accommodate the needs of any fleet, jobsite, or shop. For more information visit HERE.
Podcasts
Appetite For Construction Podcast: The guys talk to Marlena Pahlman, Marketing Project Manager with GF Building Flow Solutions/Uponor, as she takes us on a road show with the “Uponor Leading with Water Tour” a mobile experience organized by GF Building Flow Solutions Americas. The mobile unit showcases Uponor’s products and services in the commercial domestic water design and installation sector. The tour features a mobile unit with interactive displays, product demonstrations, and educational resources designed to engage with professionals in the construction industry. LISTEN HERE
Make Trades Great Again Podcast: Eric and Andy invite a longtime listener and friend of the pod, Luke Cazaly into the virtual studio. Luke does refrigeration work in Australia. They talk new refrigerants, business and more…or something like that, you can say whatever you feel works for you. LISTEN HERE

Down with the SicknessMTGA & AFC PodcastsStressed Cities https://vimeo.com/1105921404 Down with the Sickness In this update, we talk about the cost of doing business for a 1-3-man shop if the owner or employee calls in sick. We also talk about the most stressed cities in America, and snowblowers in August? MTGA & AFC Podcasts To Read more
Table of Contents
Down with the Sickness
In this update, we talk about the cost of doing business for a 1-3-man shop if the owner or employee calls in sick. We also talk about the most stressed cities in America, and snowblowers in August?
MTGA & AFC Podcasts
To listen: https://mechanical-hub.com/podcasts/
More info on Milwaukee Tool: https://www.milwaukeetool.com
OESP Dave Nelson Scholarship Winners
Stressed Cities
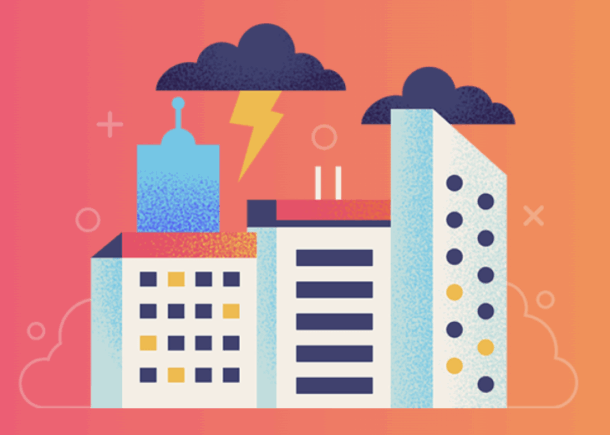

PodcastsBrand Loyalty https://vimeo.com/1103994967 On this update we talk about the dog days of summer and how to stay cool and hydrated. We also touch upon jobsite safety, and we tackle branding. Do you see what we think you see? What?! now that’s dedication. Finally, new podcasts are brewing. Podcasts MTGA and Appetite Podcasts: https://mechanical-hub.com/podcasts/ Brand Read more
Table of Contents
On this update we talk about the dog days of summer and how to stay cool and hydrated. We also touch upon jobsite safety, and we tackle branding. Do you see what we think you see? What?! now that’s dedication. Finally, new podcasts are brewing.
Podcasts
MTGA and Appetite Podcasts: https://mechanical-hub.com/podcasts/
Brand Loyalty

Check out more from our sponsor Viega here: https://www.viega.us/en/homepage/systems/valves.html?utm_source=mechanical+hub&utm_medium=email&utm_campaign=us-en-2025-2025+national&utm_content=enewsletter&utm_term=readsix

Artificial IntelligenceAge & TenureThe Insurance Factor Recently, we caught up with Mike Prencavage Jr., owner, The Family Plumber, Los Alamitos, Calif., for a quick conversation regarding jobsite safety. Employees should be a top priority in any business, especially the trades. Safety should be top priority for every business, especially in the trades. Can you provide Read more
Table of Contents
Recently, we caught up with Mike Prencavage Jr., owner, The Family Plumber, Los Alamitos, Calif., for a quick conversation regarding jobsite safety. Employees should be a top priority in any business, especially the trades.
Safety should be top priority for every business, especially in the trades. Can you provide a some of your company’s protocols, which may consist of safety meetings, reporting, etc.?
Prencavage Jr.: I would encourage companies to make safety learning fun, yet impactful. Every week, we host an all-hands-on company meeting to ensure that all team members are properly trained on hazards in the workplace. Our shop foreman is responsible for providing detailed examples and often real-world situations that can occur to which protocols must be adhered. Most companies believe or expect common sense to prevail when it comes to protecting employees; however, safety on any jobsite big or small needs to be trained on and re-enforced. Random jobsite visits from project managers are a must to ensure that all team members are performing work safely as to not endanger themselves or homeowners.

Artificial Intelligence
MH: How can the implementation of Artificial Intelligence (AI) technology help with safety protocols?
Prencavage Jr.: AI in different forms can help with developing, implementing or enforcing proper protocols within your business. The biggest examples of these are utilizing AI to create situational poster boards for your office or breakroom. Setting meeting reminders or technician meeting periods to review and train on safety standards. Also, companies that use passive integrated driving devices that record and score drivers’ safety behind the wheel.
Age & Tenure
MH: Does age or tenure play into increases jobsite accidents?
Prencavage Jr.: Most senior employees understand or have experienced the result of cutting corners with safety standards. Receive a cut, bruise or worse once in your life and it changes the way you think about approaching certain risky situations. Age plays a factor because more often than not; you don’t know what you don’t know. Youthfulness is great, but certainly doesn’t put a bulletproof vest around you. It’s best practice if you share the worst-case scenarios with younger employees as much as possible with the hope that if they encounter something similar, they are well prepared to the take the right steps for safety.
The Insurance Factor
MH: Finally, in terms of insurance, why should safety be prioritized?
Prencavage Jr.: Insurance is already one of the highest expenditures on a P&L for most construction trade businesses. The last thing a company would want is file claims against a policy that increases those rates, not to mention possible revocation. Insurance companies are looking for potential hazards all of the time, and in doing so, they can often perform random standard compliance checks on companies. It’s best to always have your company compliance ready as to not have a policy canceled.
Check out The Family Plumber, https://thefamilyplumber.com
Sign up for the Mechanical Hub weekly newsletter, https://mechanical-hub.com/enewsletter/

Mechanical Hub in Germany
Table of Contents
Visiting a German Trade School
While spending some time with his family in Germany, The Hub’s John Mesenbrink spent a day with Uber content creator and great guy Bruno Friedmann visiting the Gewerbeschule Bühl trade school, a heat pump installation at a logistic center and his shop. What a great day to see how the Germans teach and perform HVAC, plumbing, hydronics, etc.!
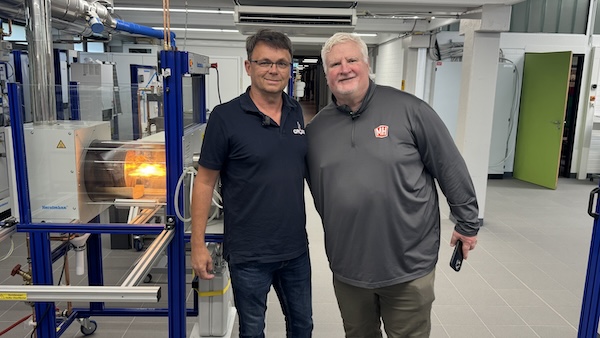
Check out our podcasts
Appetite for Construction—A talk with Steve “Wheels” Wieland: https://www.buzzsprout.com/1203956/episodes/17503421
MTGA—Bid Work vs. Time and Material:
https://www.buzzsprout.com/1198388/episodes/17427050
Sign up for our FREE Mechanical Hub newsletter, https://mechanical-hub.com/enewsletter/