The REHAU Group will sell its business in Russia to the local management and will withdraw completely from the country. A corresponding preliminary agreement has now been signed by both parties. REHAU had already announced on March 4, 2022, to ramp down its business in Russia in a controlled manner. The development of the past Read more
Industry News
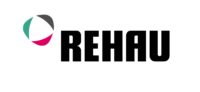
The REHAU Group will sell its business in Russia to the local management and will withdraw completely from the country. A corresponding preliminary agreement has now been signed by both parties.
REHAU had already announced on March 4, 2022, to ramp down its business in Russia in a controlled manner. The development of the past weeks has made further decisions unavoidable.
The REHAU Group has been active in Russia for around 30 years and has served the market there primarily with polymer-based solutions for the window, construction and furniture sectors.
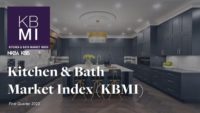
Growth bolstered by an increase in price points despite material shortages and higher labor costs The National Kitchen & Bath Association (NKBA) – the world’s leading non-profit trade association for the kitchen and bath industry providing tools, research, certification, and events to thousands of professionals – has released its Kitchen & Bath Market Index (KBMI) for Q1 Read more
Growth bolstered by an increase in price points despite material shortages and higher labor costs
The National Kitchen & Bath Association (NKBA) – the world’s leading non-profit trade association for the kitchen and bath industry providing tools, research, certification, and events to thousands of professionals – has released its Kitchen & Bath Market Index (KBMI) for Q1 of 2022. The quarterly report, which is aimed at measuring the health of the kitchen and bath industry, found that the industry enjoyed a successful opening quarter of the year, growing 12.6% in Q1, with industry professionals expecting further growth as the year continues.
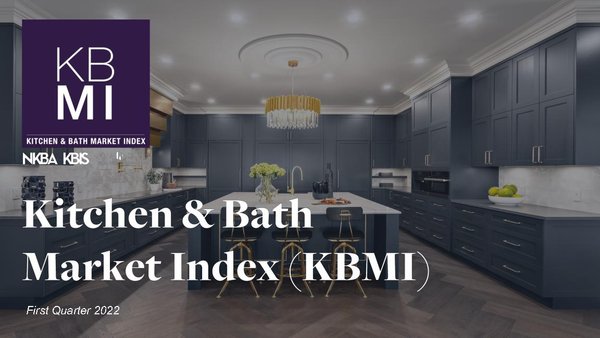
“Despite a number of ongoing economic hardships, from material shortages to higher labor costs, we’re excited to see our industry continue to grow and be optimistic about the future,” said Bill Darcy, Chief Executive Officer, NKBA. “As the world shifts toward a new normal, we’ve seen the kitchen and bath industry continue to adapt to the times by evolving e-commerce practices, stocking up on available products, and turning toward historically underutilized brands to fulfill customer needs.”
While price points have continued to rise, demand for remodeling projects has stayed strong, enabling the industry to continue to grow in the new year. In the KBMI Q1 report, all kitchen and bath industry segments reported high single-digit sales growth year-over-year (YOY) except for manufacturers, who reported double-digit sales growth of 10.3%. Not only were sales numbers up compared to 2021, but quarter-over-quarter (QOQ) sales accelerated for all segments of the industry.
2022 full-year sales growth expectations have also increased after a successful first quarter, with professionals anticipating +15.1% growth for the year, up from the 9.4% reported just three months ago. In the latest KBMI report, the kitchen and bath industry rated future business conditions a 78.6 on a 100-point scale, displaying cautious optimism about the future of the industry. Rising interest rates and low resale inventory have been tailwinds for big remodeling projects as consumers leverage home equity and other discretionary income to ‘trade up in place.’ Despite additional inflationary pressures potentially pricing out some homeowners, the industry reported a healthy number of backlogged projects, allowing the sector to feel confident about the road ahead.
“From manufacturers and designers to contractors and retailers, the entire kitchen and bath industry has had to adjust to the ever-evolving times that we live in. Despite the ongoing headwinds and potential unknown challenges ahead, all signs currently suggest that 2022 will be another strong year for the industry,” continued Darcy.
Among the report’s key findings were:
- Material Shortages Cause Delays and Cancellations: As the ongoing worldwide material shortage continues, kitchen and bath industry professionals have reported serious delays to their projects. Forty-three percent (43%) of building and construction firms report most of their projects were behind schedule in Q1 2022. Firms have tried to get out ahead of projects by pre-ordering as often as they can, however, industry-wide backorders and shipping delays prevent them from maintaining timelines. A further consequence of these material delays has been client cancellations due to long timelines, as 46% of building and construction firms had clients cancel and/or postpone projects in Q1. While this is a slight improvement from Q4 2021’s 50% cancellation/postponement rate, the trend continues to be a concern for the industry moving forward.
- Luxury Products In Demand, Come With Longest Lead Times: The KBMI for Q1 2022 found that luxury products once again are the most popular category for consumers. However, these products also come with the longest wait times. An increasing number of industry professionals (55%) report differing lead times across luxury, mass market, and entry-level products/materials. Seventy-nine percent (79%) of those indicating a difference say lead times for luxury products/materials are the longest. Consumers choosing to move forward with big project remodels are often opting for high-end products, associating quality and durability with the higher price tag.
- Labor Remains Elusive and Expensive: Industry professionals reported labor availability as having a significant impact on their businesses and their ability to keep up with demand, rating the overall impact a 6.7 on a 10-point scale. Industry professionals continue struggling to find qualified labor, raising rates by 18% on average to retain and/or attract talent. Seventy-six percent (76%) of designers are increasing labor rates 21% on average to retain existing employees, saying competition for qualified labor is fierce.
To learn more, visit here.
Grenada, Miss. — Milwaukee Tool is excited to announce construction on their newest facility in Mississippi. Located in Grenada County, Mississippi, Milwaukee’s latest expansion will accommodate the company’s growing power tool accessories and power tool business, and will also serve as a centralized repair facility. The new location will create more than 800 new jobs, and Read more
Grenada, Miss. — Milwaukee Tool is excited to announce construction on their newest facility in Mississippi. Located in Grenada County, Mississippi, Milwaukee’s latest expansion will accommodate the company’s growing power tool accessories and power tool business, and will also serve as a centralized repair facility. The new location will create more than 800 new jobs, and is planned to open in mid-2023.

“We’re thrilled to, once again, expand our footprint in the state of Mississippi, where we’ve been able to recruit some of the best talent in the country,” said Steve Richman, Milwaukee Tool Group President. “Our success is the result of our talented people and the culture we’ve created; it is unparalleled in the industry. We are committed to investing in new talent, and the right opportunities to continue meeting the needs of our distributor and user partners with the speed and agility that defines who we are as a company.”
Milwaukee® is investing more than $60 million into advanced technology and manufacturing equipment at their new 563,000-square-foot Grenada location. The facility will house critical accessory manufacturing capabilities, and will join the company’s other service hub in Greenwood, IN, as one of Milwaukee Tool’s main axis points for service operations.
Milwaukee Tool, which employs more than 10,000 people in the U.S., has continually expanded their footprint domestically and globally as their company experiences incredible double-digit growth. In Mississippi, the company has invested more than $209 million in domestic expansion projects over the last 5 years and employs 4,400 people.
More About Milwaukee’s Growth & U.S. Investments
Milwaukee Tool is a global company with manufacturing, distribution, and operations presences across North America, South America, Europe, Asia, and Australia. The company has designed, engineered, and manufactured products in the United States for nearly 100 years.
In the last year, Milwaukee® has invested $216 million in domestic expansion projects. In addition to this new Grenada location, the company’s other domestic presences include Greenwood, Olive Branch, Clinton, and Jackson, MS, as well as in Brookfield, Menomonee Falls, Milwaukee, West Bend, Mukwonago, and Sun Prairie, Wis., Cookeville, Tenn., Chicago, Ill., and Greenwood, Ind.
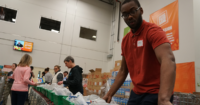
Recent monetary donations to Feeding America and Meals on Wheels will help provide children, seniors and other Americans with reliable access to nutritious meals. Rooted in the company’s heightened desire to do more, Saniflo USA, a division of Group SFA, has donated to Feeding America to provide 6000 meals to families in need. One dollar Read more
Recent monetary donations to Feeding America and Meals on Wheels will help provide children, seniors and other Americans with reliable access to nutritious meals.
Rooted in the company’s heightened desire to do more, Saniflo USA, a division of Group SFA, has donated to Feeding America to provide 6000 meals to families in need. One dollar helps provide at least 10 meals secured by Feeding America on behalf of local member food banks. The company also donated to Meals on Wheels providing 100 meals to those in need.
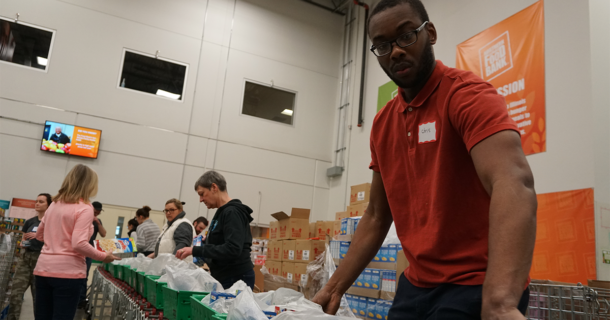
“We believe in the power of food to nourish communities across the United States,” says Regis Saragosti, CEO of SFA Saniflo North America. “With millions of Americans without access to nutritious meals, we must help however we can.”
Meals on Wheels America, a leadership organization supporting more than 5,000 community-based programs across the United States, is dedicated to addressing senior isolation and hunger. Their network serves virtually every community in the country. Along with more than two million staff and volunteers, it delivers nutritious meals, friendly visits and safety checks that enable America’s seniors to live nourished lives with independence and dignity.
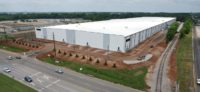
Located in Huntsville, Alabama, this warehouse will house high-volume STERLING Vikrell bathing and showering fixtures to meet growing U.S. demand Kohler Co., a global leader in kitchen and bath products, opened a state-of-the-art warehouse in Huntsville, Alabama, to support growing customer demand for its high-volume STERLING Vikrell bath and shower fixtures. This greenfield build comprises Read more
Located in Huntsville, Alabama, this warehouse will house high-volume STERLING Vikrell bathing and showering fixtures to meet growing U.S. demand
Kohler Co., a global leader in kitchen and bath products, opened a state-of-the-art warehouse in Huntsville, Alabama, to support growing customer demand for its high-volume STERLING Vikrell bath and shower fixtures.
This greenfield build comprises a total of 546,000 square feet and is located near Kohler’s existing manufacturing plant, which produces STERLING Vikrell products that are popular among the nation’s top single-family homebuilders, home improvement retailers, and a vast number of multi-family developers, plumbers, and remodelers.
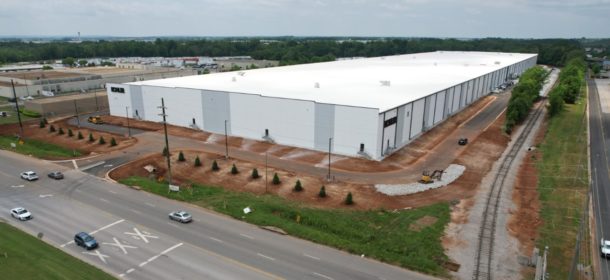
Kohler Co. cut the ribbon at its state-of-the-art warehouse in Huntsville, Alabama, to support growing customer demand for the company’s high-volume STERLING Vikrell bath and shower fixtures. The distribution warehouse comprises 546,000 square feet and is located near Kohler’s existing manufacturing plant, which produces STERLING Vikrell products that are popular among the nation’s top single-family homebuilders, home improvement retailers, and a vast number of multi-family developers, plumbers, and remodelers.
“In the past, our business has been constrained by a lack of warehouse storage, which challenged us in providing the level of consistent quick delivery our customers expect,” said Norb Schmidt, Senior Vice President-Kitchen & Bath Operations. “The new warehouse and enhanced stocking strategy will greatly reduce lead times and improve delivery efficiency. We are pleased to expand our presence in Huntsville and Madison County and contribute to the local economy.”
On Tuesday, May 10, Kohler Co. leaders celebrated the warehouse completion with a ribbon-cutting ceremony on-site, which included company CEO David Kohler, and Senior Vice President-HR, Stewardship & Sustainability Laura Kohler, along with Kohler associates, local officials and Burns & McDonnell, the design-build contractor for the project.
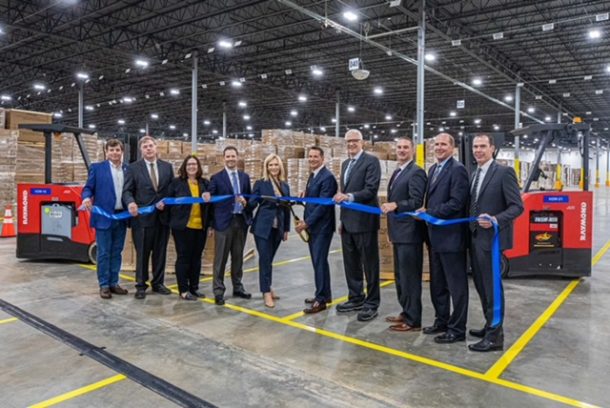
The ceremony was attended by Kohler leaders and associates, as well as local officials. Kohler Co. CEO David Kohler (center) is shown cutting the ribbon, and was joined by (left to right) Dale Strong, Chairman-Madison County Commission; Tommy Battle, Mayor-Huntsville; Ginger King, VP, HR-Kohler Kitchen & Bath; Norb Schmidt, SVP-Kohler Kitchen & Bath Operations; Laura Kohler, SVP-Kohler Co. HR, Stewardship & Sustainability; David Kohler; Tom Adler, CFO-Kohler Co.; Shawn Oldenhoff, President-Kohler Kitchen & Bath North America; Paul Finley, Mayor-Madison; and Mike Fenske, President & GM-Global Facilities, Burns & McDonnell.
The Huntsville warehouse opening comes on the heels of Kohler announcing in February, the construction of a second Vikrell production facility and distribution center in Casa Grande, Arizona, which is set to be operational by August 2023 to support the company’s growing customer base in the western U.S.