Advanced electrode boilers dramatically reduce the risk of explosion, fire, and noxious emissions associated with fossil fuel burning units In industry, gas-fired boilers have largely been the standard for many decades to produce steam as well as heat process water. However, not all boilers are created equal in terms of safety. By definition, combustion-fueled boilers Read more
Industry News
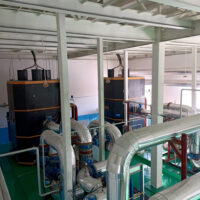
Advanced electrode boilers dramatically reduce the risk of explosion, fire, and noxious emissions associated with fossil fuel burning units
In industry, gas-fired boilers have largely been the standard for many decades to produce steam as well as heat process water. However, not all boilers are created equal in terms of safety. By definition, combustion-fueled boilers can emit harmful vapors, leak gas, and even cause explosions and fires.
In a recent example, a natural gas boiler was cited as the cause of a massive explosion and fire at a food processing plant in eastern Oregon that injured six and caused severe damage to the facility’s main building. Given the risks, many processors are turning to a new generation of electric boilers to dramatically reduce these hazards.
“With gas burning boilers, any gas leak can increase the risk of an explosion wherever there are fuel lines, fumes, flames, or storage tanks. So, gas units must be continually monitored or periodically inspected,” says Robert Presser, Vice President of Acme Engineering Products, who notes that state and municipal safety guidelines vary depending on boiler type and the expected frequency of inspection. Acme Engineering is a North American manufacturer of boilers for large industrial and commercial applications. The company is an ISO 9001:2015 certified manufacturer of environmental controls and systems with integrated mechanical, electrical and electronic capabilities.
In gas-fired boilers, explosions can result in the ignition and instantaneous combustion of highly flammable gas, vapor, or dust that has accumulated in a boiler. The force of the explosion is often much greater than the boiler combustion chamber can withstand.
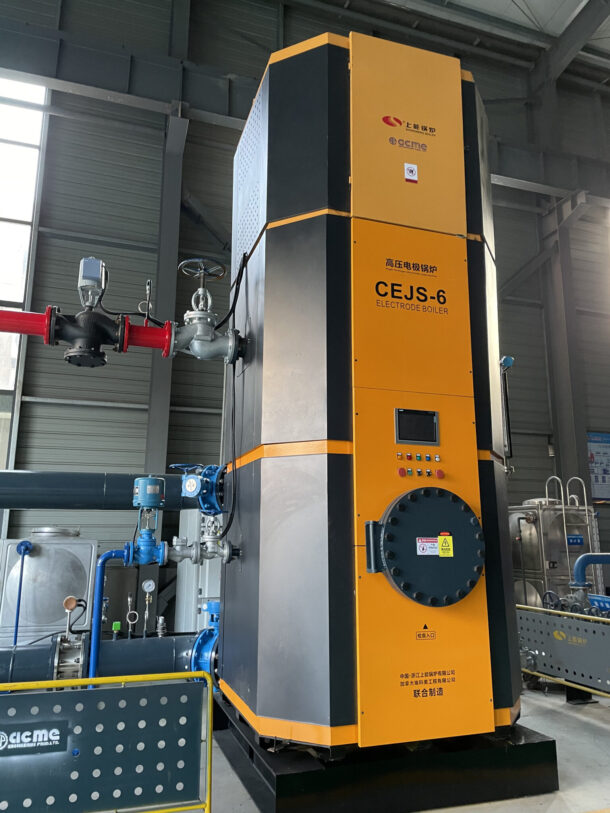
Minor explosions, known as flarebacks or blowbacks, can also suddenly blow flames many feet from firing doors and observation ports, seriously burning anyone in the path of a flame.
Natural gas-fired boiler emissions also pose potential hazards in the form of emissions. This can include nitrogen oxides (NOx), carbon monoxide (CO), nitrous oxide (N2O), volatile organic compounds (VOCs), sulfur dioxide (SO2), and particulate matter (PM), as well as the greenhouse gasses carbon dioxide (CO2) and methane (CH4), which accelerate global warming.
In addition, fossil fuel burning boilers can also face potentially dangerous operational issues stemming from excessive heat accumulation, particularly if the water is too low in the system to properly absorb the heat. High heat conditions can compromise the boiler, electrodes, and other equipment essential to operation.
To dramatically improve operator and environmental safety, industry is turning toward modern electric boilers that eliminate many of these risks. The most advanced electrode boilers not only match the capacity of large gas or oil-fired boilers but are safer and more compact, maximizing energy efficiency, improving reliability, and minimizing maintenance.
Although many facility engineers are familiar with gas-fired boilers, many believe that electric boilers cannot match the output of the traditional, fossil fuel burning units. Due to considerable advances in electric boiler technology, however, such technology can now match the capacity of large gas or oil-fired boilers in a much smaller footprint.
Presser explains that electric boilers utilize the conductive and resistive properties of water to carry electric current and generate steam. An A.C. current flows from an electrode of one phase to ground using the water as a conductor. Since chemicals in the water provide conductivity, the current flow generates heat directly in the water itself. The more current (amps) that flows, the more heat (BTUs) is generated, and the more steam produced.
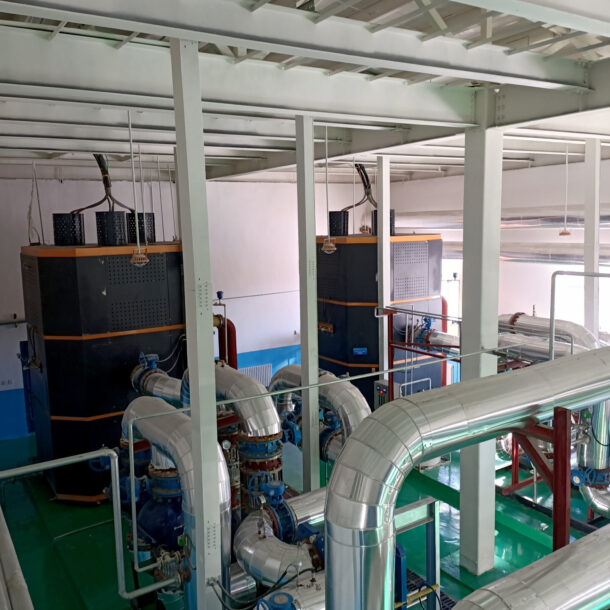
As an example, in Acme’s CEJS High Voltage Electrode Steam Boiler, almost 100% of the electrical energy is converted into heat with no stack or heat transfer losses. The electrodes of the jet type electrode steam boiler are vertically mounted around the inside of the pressure vessel. This enables the unit to produce maximum amounts of steam in a minimum amount of floor space, with boiler capacity from 6MW to 52MW. Operating at existing distribution voltages, 4.16 to 25 KV with up to 99.9% efficiency, the boiler can produce up to 170,000 pounds of steam per hour. With pressure ratings from 105 psig to 500 psig, the boilers are designed to ASME Section 1, and are certified, registered pressure vessels at the location of the boiler.
“With the jet type electrode boilers, there are no combustion hazards because there are no flames, fumes, fuel lines or storage tanks, which minimizes the risk of explosions and fires,” says Presser. In case of an electrical short, the breaker that protects the high voltage circuit trips in a matter of milliseconds, protecting the boiler and the electrical network. There is no chance of electrical mishap or fire from the boiler.
Since the design does not rely on combustion, it does not create emissions that would endanger the operator or environment. In addition, the design eliminates many environmental issues associated with fuel burning boilers such as fuel fumes, fly ash, and large obtrusive exhaust stacks.
The approach resolves safety issues related to potentially excessive heat accumulation with the system as well. Low water protection is absolute since the absence of water prevents current from flowing and the electrode boiler from producing steam. Unlike conventional electric boilers or fossil fuel boilers, nothing in the electrode boiler is at a higher temperature than the water itself. This prevents the risk of dangerous heat build up in the boiler, electrodes, and other important components even if scaling should occur, and thermal shock is eliminated.
“Electric boilers, and specifically the electrode units, are inherently the safest boiler design today. These units do not need an operator because if anything goes wrong, the breaker trips, preventing further escalation of the issue,” explains Presser.
The electric boilers also improve safety by reducing industrial noise, which is an OSHA regulated issue. Under OSHA’s Noise Standard, the employer must lower noise exposure through engineering controls, administrative controls, or Hearing Protection Devices (HPDs) to attenuate the occupational noise received by the employee’s ears to within levels specified.
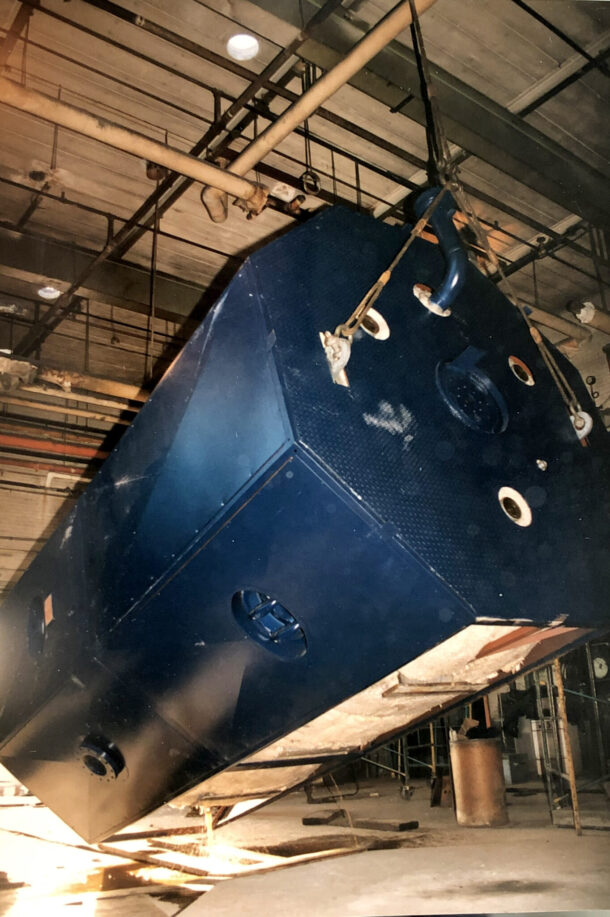
In this regard, the electric units are also exceptionally quiet compared to fuel fired boilers. “Unlike gas-powered burners that throttle like turbine engines almost continually, electric boilers keep operational noise levels down,” says Presser. “Because the loudest boiler component is a circulating pump motor, you can have a conversation next to one without the need to elevate your voice.”
While safety of the electrode units is superior, there are also significant benefits in terms of reliability and maintenance. The absence of excessive temperatures and burnout assures longer operating life. The boilers have a minimum number of components and electrical controls. With no fuel residues, along with fewer parts and simple control systems, cleaning and maintenance requirements are reduced, and reliability is enhanced.
Processors have long sought to improve safety, yet options have been limited. Now, as safer, more energy-efficient alternatives become more widely available in the form of state-of-the-art electrode boilers, companies can protect their people and processes more completely while minimizing required maintenance.
For more info, contact Robert Presser at Acme Engineering at e-mail: rpresser@acmeprod.com, phone: 888 880-5323, or web: www.acmeprod.com/
Del Williams is a technical writer based in Torrance, California.
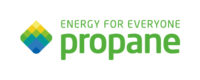
U.S. Department of Energy Awards $10 Million in Funding The Propane Education & Research Council (PERC) is partnering with Colorado State University (CSU) and 2G Energy to examine decarbonized district energy systems with renewable propane-powered combined cooling heat and power (CCHP). The project is one of six that was selected by the U.S. Department of Energy Read more
U.S. Department of Energy Awards $10 Million in Funding
The Propane Education & Research Council (PERC) is partnering with Colorado State University (CSU) and 2G Energy to examine decarbonized district energy systems with renewable propane-powered combined cooling heat and power (CCHP).
The project is one of six that was selected by the U.S. Department of Energy (DOE) to receive $10 million in funding from the Advanced Manufacturing Office (AMO) through the Technical Partnerships Funding Opportunity. The Opportunity supports funding for renewably supplied district energy systems and the development of regional smart manufacturing pilot initiatives.
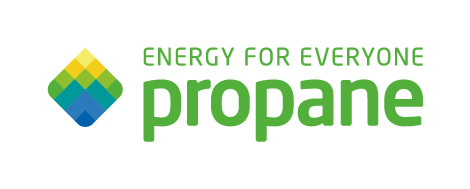
“District energy systems provide multiple buildings with heating and/or cooling from a central plant,” said Jim Bunsey, director of commercial business development at PERC. “These systems increase efficiency and reduce emissions compared to individual building systems. They also provide a reliable and resilient source of thermal energy that is particularly useful for large energy users such as manufacturing facilities, healthcare campuses, and military bases.”
While district energy systems traditionally use fossil fuels, they can also incorporate renewable fuels for enabling low-carbon, flexible, energy-efficient CHP systems, which support the electrical grid.
“The research will help show that district energy systems can operate seamlessly with renewable fuels,” said Bunsey. “By incorporating propane-powered CHPs into these systems, it’s possible to provide necessary energy services in conjunction with onsite solar generation and simultaneously support the electrical grid.”
With the awarded funds, CSU will conduct a field demonstration of an integrated CCHP unit in a district energy system that uses the waste heat to drive a turbo-compression chiller, a technology developed at the university.
“This is important research for the commercial industry as it could be used to power critical infrastructure and facilities such as schools, hospitals, and large commercial complexes,” Bunsey said.
To learn more about this project and the benefits of propane, visit Propane.com.
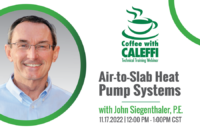
You’re invited to our complimentary educational series, Coffee with Caleffi™. The popular series is an online technical training webinar and is intended for engineers, contractors, designers and wholesalers. What’s next? Air-to-Slab Heat Pump Systems Thursday, Nov. 17 12:00 – 1:00 p.m. CST Technical Content Level: Intermediate REGISTER TODAY Air to water heat pump technology is steadily gaining traction. When a heat Read more
You’re invited to our complimentary educational series, Coffee with Caleffi™. The popular series is an online technical training webinar and is intended for engineers, contractors, designers and wholesalers.
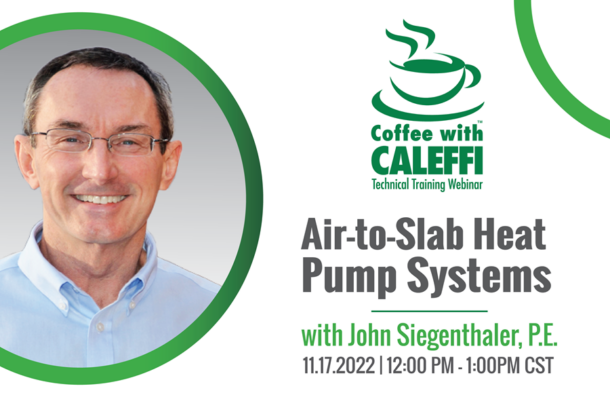
What’s next?
Air-to-Slab Heat Pump Systems
Thursday, Nov. 17
12:00 – 1:00 p.m. CST
Technical Content Level: Intermediate
Air to water heat pump technology is steadily gaining traction. When a heat pump’s coefficient of performance is maximized, energy efficiency and resiliency benefits are substantial. How can engineers, designers and installers effectively apply this emerging technology to high thermal mass floor heating applications? Which commercial systems are good candidates for this type of design?
Hydronics expert John Siegenthaler, P.E. will detail the approaches that can best utilize this technology.
You’ll learn:
→ Do all air to water heat pump systems need buffer tanks?
→ How does the thermal mass of a floor slab compare to that of a buffer tank? → What is a simple way to control a heat pump supplying a heated floor slab? → What are the benefits of using constant circulation in “garage-type” floor heating systems?
Siegenthaler is a seasoned industry leader and passionate teacher, eager to share his over 40 years’ experience in the understanding and proper application of water-based engineering principles with our audience. He is the principal of Appropriate Designs and a regular contributor to industry publications.
It’s easy to join us. Simply register today!
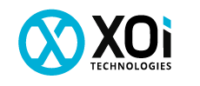
Roundup highlights B2B partners that support startups across all business functions and empower growth XOi Technologies, a leading provider of technician-focused technology solutions, has been named to Inc. Business Media’s inaugural Power Partner Awards honoring B2B organizations across the globe that have proven track records supporting entrepreneurs and helping startups grow. The list recognizes 252 Read more
Roundup highlights B2B partners that support startups across all business functions and empower growth
XOi Technologies, a leading provider of technician-focused technology solutions, has been named to Inc. Business Media’s inaugural Power Partner Awards honoring B2B organizations across the globe that have proven track records supporting entrepreneurs and helping startups grow. The list recognizes 252 firms in marketing and advertising, health and human resources, financial planning, engineering, logistics, and security, as well as other areas of business.
XOi’s advanced cloud-based solution allows field service technicians to utilize, aggregate and analyze critical job data and maximize customer value through industry-leading efficiency, accuracy and accountability.
All 252 Power Partners companies received top marks from clients for being instrumental in helping leadership navigate the dynamic world of startups. These B2B partners support entrepreneurs across various facets of the business, including hiring, compliance, infrastructure development, cloud migration, fundraising, etc., allowing founders to focus on their core missions.
“Trusted B2B partners provide guidance and expertise that founders rely on at various steps of their organization’s journey,” said Scott Omelianuk, editor-in-chief of Inc. Business Media. “Partners that possess a demonstrated ability to deliver quality support are at the core of entrepreneurship and help bring big ideas to life.”
With XOi’s full suite of standardized workflows, job documentation capabilities, and technician training and enablement solutions, teams can build deep and easily accessible institutional knowledge bases that support real-time decision-making and data-based continuity. Service teams can apply these extensive data-science capabilities to analyze those foundational elements and strategically respond to evolving data trends and forecasts.
“At XOi, we’re investing in technology solutions that are designed to meet the real-world challenges field service technicians face on the job every day,” said Aaron Salow, CEO and founder of XOi. “Our unique platform empowers techs through each stage of a project, from the time they set foot on the site through completion, with powerful data indexing and analytics. By focusing on the real experience of techs in the field, we’re helping business owners enhance operations and productivity in an industry that’s rapidly changing and experiencing unprecedented uncertainty.”
For more information about XOi, visit https://xoi.io.
Inc. partnered with leading global social and media intelligence platform Meltwater to develop a proprietary methodology that uses sentiment from online conversations about organizations and translates it into numerical scores. Companies were evaluated on commitment, reliability, trust, creativity, supportiveness, and other virtues that offer value to clients. Inc. also conducted surveys to gather client testimonials as part of the process.
To view the complete list, go to https://www.inc.com/power-partner-awards/2022.
Falls Church, Va. — The Plumbing-Heating-Cooling Contractors — National Association’s (PHCC) Educational Foundation is proud to announce the winners of the national plumbing and HVAC apprentice contests. The contests were held October 5th & 6th in Charlotte, North Carolina on the tradeshow floor during the PHCC—National Association’s CONNECT 2022 event. A total of eighteen plumbing Read more
Falls Church, Va. — The Plumbing-Heating-Cooling Contractors — National Association’s (PHCC) Educational Foundation is proud to announce the winners of the national plumbing and HVAC apprentice contests. The contests were held October 5th & 6th in Charlotte, North Carolina on the tradeshow floor during the PHCC—National Association’s CONNECT 2022 event. A total of eighteen plumbing and ten HVAC apprentices from across the nation took part in the contests.
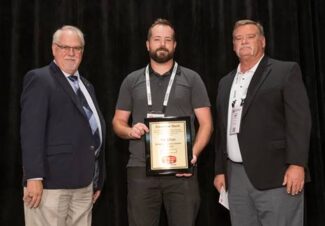
PHCC Educational Foundation Chair Kevin Tindall, Plumbing Contest Winner Jake Elsbecker and Plumbing Contest Chair Jim Steinle.
Plumbing Apprentice Contest Winners
- First place: Jake Elsbecker, from Midwestern Mechanical in Spencer, Iowa. He was sponsored by Zoeller.
- Second place: Scott Hicks, Jr. from TD Industries in Houston, Texas. He was sponsored by the International Code Council.
- Third place: Alex Estevez from B Wagner Contracting in Allentown, New Jersey. He was sponsored by the Copper Development Association.
HVAC Apprentice Contest Winners
- First Place: Sebastian Uhde, from Magnolia Plumbing, Heating and Cooling in Washington D.C. He was sponsored by the PHCC National Auxiliary.
- Second place: Harrison Bosler, from Howe Inc. in Sioux Falls, South Dakota. He was sponsored by NIBCO, INC.
- Third Place: Sean Reed, from Reddick and Sons in Manassas, Virginia. He was sponsored by RIDGID.
The plumbing apprentices were required rough-in a bathroom system. The set-up includes a toilet, sink and shower, complete with supply, waste and vent lines, plus cleanouts and extra features designed to test the contestants’ knowledge and skills. The test set-up includes a variety of pipe materials – cast iron, copper, and PVC and corresponding joining methods.
The HVAC competitors were required to complete a written test, demonstrate proper brazing techniques and perform a hands-on diagnostic on an HVAC package unit, with system errors created by the Foundation’s contractor volunteers for the competition. The competitors also had to perform a pressure and leak test, demonstrate proper refrigerant recovery procedures and the ability to accurately take a variety of instrument readings.
A dedicated team of contractor volunteers arrived two days before the competitions to assemble the competitor test benches, distribute the materials and supplies and setup the testing areas. They monitor the competitions, evaluate the apprentices’ work and provide constructive feedback on each competitor’s performance following the event.