Tip of the Week: Different generations of homeowners have different home improvement needs, but fundamentals of customer service are still key overall. Lowe’s State of the Pro report found that better communication ranked as the No. 1 deciding factor across all generations when deciding between two final quotes – with 60% of homeowners citing ‘not Read more
Just the Tip
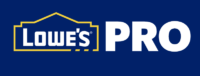

Tip of the Week: Different generations of homeowners have different home improvement needs, but fundamentals of customer service are still key overall. Lowe’s State of the Pro report found that better communication ranked as the No. 1 deciding factor across all generations when deciding between two final quotes – with 60% of homeowners citing ‘not responsive to communication’ as a major challenge. Read more about what homeowners look for in their relationships with Pros here.
For more information on the latest for Pros, please visit Lowes.com/Pro.
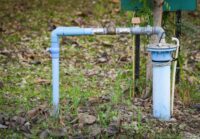
Private well water is not filtered and disinfected before entering a home, unlike municipal water. Even though well water is exempt from specific requirements for public water sources, it still needs to be clean and safe to consume. Installing a well water treatment system is necessary to eliminate typical well water impurities such as coliform Read more
Private well water is not filtered and disinfected before entering a home, unlike municipal water. Even though well water is exempt from specific requirements for public water sources, it still needs to be clean and safe to consume. Installing a well water treatment system is necessary to eliminate typical well water impurities such as coliform bacteria, iron, nitrates, and sulfate.
When removing undesirable components from a well water, distillers, whole-house water filters, water softeners, and disinfection systems are all viable solutions. This is true in all areas of the country, in fact, check out residential well drilling in Indianapolis for information in that area.
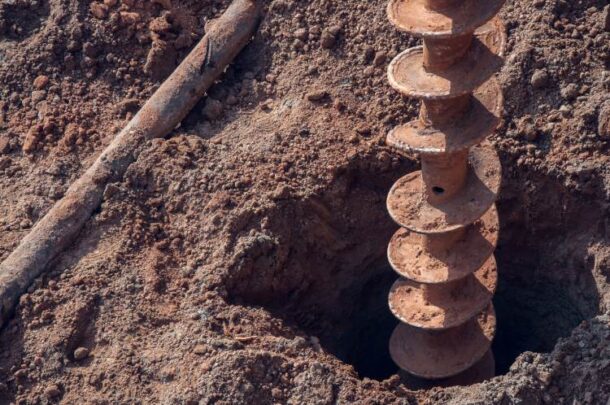
How Well Water Gets Adulterated
Most well water requires little filtering if the screen and pump are kept in good condition. But there are several ways for a well to get polluted.
It is simple for toxic substances to leak into the aquifer and contaminate the groundwater close to your well, or polluted water can enter improperly built or neglected wells. Private well owners should be mindful of any surrounding land-use activities that could have a detrimental impact on groundwater quality. This includes livestock grazing and feeding activities, insecticides, herbicides, fertilizers, and unlawful disposal.
Additionally, putting septic tanks too close to a well will contaminate your freshwater source if there is a sewage leak. In addition, the water supply can be contaminated by naturally occurring substances like iron and manganese, as well as runoff from populated regions.
Keeping Up Water Well
Ensure a sufficient water supply and ongoing water safety. To assure water quality, a testing facility should test well water yearly for E. coli and total coliform bacteria.
Extensive testing is advised every three years for total dissolved solids, pH, and tests about land use that is now taking place or anticipated to occur near the well. Additionally, seek tests that will assist in determining the cause of any overt stains, tastes, or smells in the water.
Yearly inspections of water wells are also recommended for evidence of harm or pollution. Make sure the 100 feet surrounding the well are free of any objects or debris that might contaminate the water.
Well Water Treatment System
You must accurately assess the well water quality and grasp how the well water treatment system functions to have the best and most effective treatment system.
Most water treatment methods work best under certain circumstances. For instance, the well water in this area is naturally acidic and contains iron. Since many iron filtration systems cannot wholly remove iron from acidic water, the acidity of the well water must first be handled.
The well water must be checked for chemical pollutants, bacteria, unpleasant tastes and smells, and stains before selecting a well water filter system. In addition, iron, manganese, total dissolved solids, pH, calcium, hardness, alkalinity, turbidity, arsenic, nitrate, and other substances must also be analyzed.
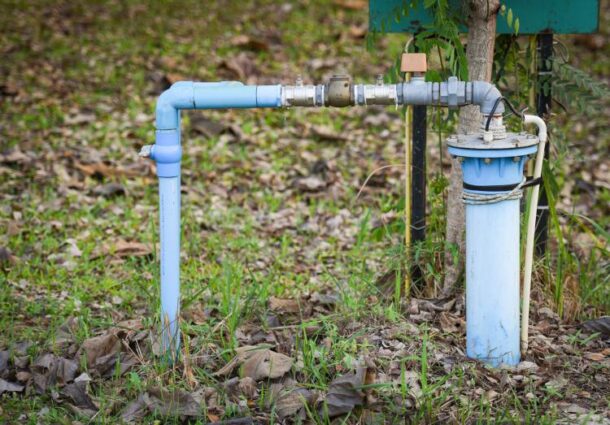
Different Well Water Treatment Systems
There are multiple varieties of well water treatment systems, each designed to eliminate certain impurities from your water source. These systems consist of:
- Water Softeners
- Whole House Filters
- Reverse Osmosis Systems
- Chemical Disinfection Systems
- UV Disinfection Systems
- Distillation Systems
What Is The Cost Of Treating Well Water?
It varies depending on the approach you choose. Some home systems utilize more hardware and need more upkeep than others. Some well-related systems cost more money upfront but require little maintenance or special care throughout their lifespan.
Hydrowells Well Water Treatment System
Hydrowells team is pleased to provide a 100% client satisfaction promise and an on-time guarantee. In addition, we ensure that our staff members are well qualified and outfitted to handle the variety of well-servicing requirements for your house result.
Our objective is to offer our clients extremely competent well drilling services. We take pleasure in providing consumers with dependable, warm service they can rely on. For any emergency, our knowledgeable crew is on call around-the-clock.
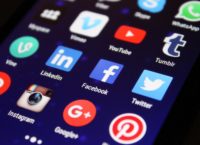
Plumbing and heating, ventilation, and air conditioning (HVAC) contractors have unique challenges when it comes to marketing. You’re working in hidden spaces, and potential clients usually don’t know much about you until something goes wrong. Even then, your work is often invisible, with the only evidence being a bill or the lack of one. In Read more
Plumbing and heating, ventilation, and air conditioning (HVAC) contractors have unique challenges when it comes to marketing. You’re working in hidden spaces, and potential clients usually don’t know much about you until something goes wrong.
Even then, your work is often invisible, with the only evidence being a bill or the lack of one. In other words, this isn’t exactly a field where word-of-mouth works as well as it does for hotels or restaurants.
So what can you do to grow your business?
The answer lies in digital marketing strategies that will get you more leads, clients, and sales in today’s connected world. But, the trick is knowing which tactics are worth your time and which aren’t.
In this article, we’ll give you some essential digital marketing tips for plumbing and HVAC contractors so that you know how to market yourself effectively online. If you’re ready to dive in, read on!
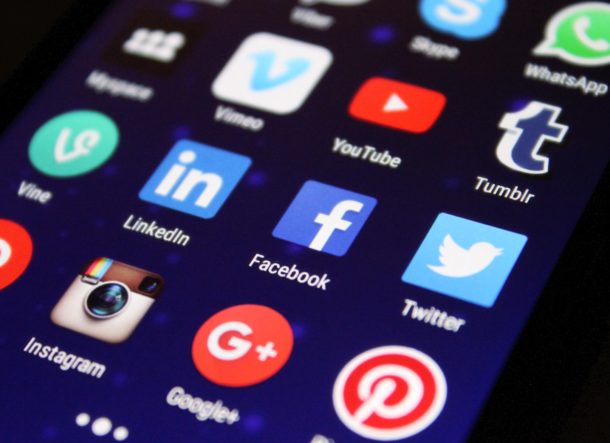
#1. Go Social
With more than 4.6 billion users worldwide, social media platforms are an ideal place to boost your online presence and gain more eyeballs. That said, social media marketing can be tricky, but it can also be extremely effective. You have to be careful not to fall into the trap of posting to your social channels just to publish something.
You should be using social media to engage with your audience and build relationships with people who might need your services. Use the right social media channels for your business. If your industry is visual, Instagram, TikTok, and Pinterest might be a better fit than Facebook.
If you’re an HVAC contractor, Facebook and Instagram are great places to start. If you’re a plumbing contractor, you might want to try a combination of Facebook, Instagram, and Twitter.
#2. HVAC Contractors: Start With Lead Generation
The best way to generate leads for your business is to offer something for free. Whatever your industry, there are likely organizations that could use your services but don’t have the money to pay for them. You can help these organizations by offering your services for free, and in exchange, they’ll give you something: their contact information.
This type of marketing is called lead generation, and it’s a great way to attract new clients and grow your business without spending any money. There are organizations that could use your services just about everywhere.
Start by thinking about your local community and the places you spend time: your kids’ school, your church, your gym, your sporting events, and more. Throughout the year, these places celebrate birthdays, host fundraisers, and hold other events. You can offer your services for free, and in exchange, you’ll get the contact information of everyone involved.
#3. Invest in An Engaging Content Marketing Strategy
You might not be a content marketing pro, but chances are that you have something to say. And if you want people to pay attention to you, you need to say it in a way that’s easy to find, read, and share.
Most businesses should have an editorial calendar, which is a schedule for publishing content. Your calendar should include topics that are relevant to your industry, your clients, and your business.
Organize your calendar by topic and make sure to include content for all of your marketing channels. If you’re an HVAC contractor, for example, you might create a blog post about how to choose the right type of air filter, publish a how-to on installing solar panels, or create a HVAC salary guide to help HVAC business owners hire top talent.
Or, if you’re a plumbing contractor, you might write an article on how to winterize your water heater or create a training video or tutorial video showing how to unclog a drain using a plunger. Whatever your industry, there are topics that will interest your clients.
#4. Take Advantage of Local SEO
Local SEO is the art of making sure your business is listed on the best local directories and maps. It’s also about optimizing your website and social media profiles for local search. You want to ensure that when potential clients search for your services in your area, your business appears at the top of relevant searches.
That way, you don’t need to go door to door to find new clients. Depending on which state you’re in, your clients may also be able to find you through state-level directories like Angie’s List. If you’re a plumber, you should add your business to Yelp, Google My Business, and Plumbers.org.
If you’re an HVAC contractor, your business should be listed on Yelp, Angie’s List, HomeAdvisor, and Local.com. Make sure that each of your local listings has accurate contact information, including a telephone number. You can also use your listings to add information about your business, including hours of operation and specialties.
#5. Set Up a Responsive Website
In today’s digital world, having a website is a must for businesses. It’s safe to say that your website is the foundation of your online marketing. Think of it like your 24/7 online store. It’s where potential clients will learn about your business, see what you can offer, how to contact you and decide whether you’re right for them.
This also means that your site needs to be accessible on any device and optimized for search. You don’t want your potential clients to have to squint to read your content every time they open your site and try to learn more about your service.
#6. Leverage User-Based Advertising
Social media advertising is growing in popularity because it’s one of the most effective ways to reach your target audience. You can target users on Facebook and Instagram based on their age, location, interests, hobbies, and more.
When you run a social media ad, you’re paying to get your ad in front of an audience that Facebook has identified as relevant to your business. When you’re advertising on Facebook, make sure that you’re creating your ads with the right mindset: you’re trying to get people to click, not to buy.
#7. Plumbing Contractors: Try Display Ads and Podcasting
If you’re a plumbing contractor, you might be ready to get more inventive with your marketing strategy. You might have the best marketing strategy in the world, but if potential clients can’t find it, you’re wasting your time.
You can use display ads to get your message in front of a more general audience. You can write an article or create a video and then promote it with display ads on social media and on major websites.
You can also try podcasting. Podcasts are a great way to engage your audience, and they’re growing in popularity. You can talk about your industry and answer your clients’ most pressing questions. You can even interview experts in your field or conduct interviews with your team members.
Conclusion
Your business is unique. That means you need a unique marketing strategy that works for you and your clients. These digital marketing tips will get you started, but don’t forget to experiment to see which one works and which one does not at the moment.
In this fast-paced world, you may find that a strategy that doesn’t work for your business today could be your secret sauce tomorrow. Keep an eye out for trends and try new things. With a little effort and these essential digital marketing tips, you’ll be well on your way to a successful business.
Guest Author
Andre Oentoro is the founder of Breadnbeyond, an award-winning explainer video company. He helps businesses increase conversion rates, close more sales, and get positive ROI from explainer videos (in that order).
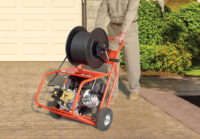
Grease clogged pipes produce problems. But the right drain cleaning equipment, Chris Fantauzzo contends, turns those problems into profits. “Health inspectors, for instance, want restaurants to clean grease traps regularly – often every six months,” the owner of Mercer Drain Cleaning Service says. Bar owners, municipal authorities, and homeowners, he adds, also suffer grease, sediment Read more
Grease clogged pipes produce problems. But the right drain cleaning equipment, Chris Fantauzzo contends, turns those problems into profits.
“Health inspectors, for instance, want restaurants to clean grease traps regularly – often every six months,” the owner of Mercer Drain Cleaning Service says. Bar owners, municipal authorities, and homeowners, he adds, also suffer grease, sediment, sand, and ice.
And every problem, he says, is a business opportunity.
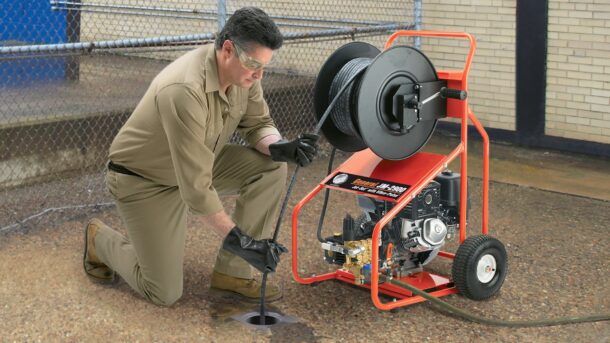
RIGHT EQUIPMENT
That’s why Fantauzzo’s company near Trenton, NJ added the popular, reliable JM-2900™ gas-powered water jet from General Pipe Cleaners to Mercer’s extensive mix of drain-cleaning and inspection solutions.
“When a drain cleaning cable goes through grease, the grease closes behind the cable, still leaving the line clogged,” he explains. But the JM-2900 hits soft clogs with a wall-to-wall stream of high-pressure water – and flushes them away.
Performance like that boosts Fantauzzo’s business. One of his competitors recently tried clearing a cast iron residential line – but the blockage returned a few days later.
“The guy just snaked through a whole mess of toilet paper, which almost immediately re-clogged the pipe,” he recalls. “We blasted the blockage downstream with our JM-2900 – and removed the wad from the house trap. Problem solved – permanently!”
An economical alternative to larger gas-powered jets, the JM-2900 is lighter and more maneuverable – yet maintains the same pressure and flow rate as competitive jets.
Power comes from a proven 13 hp (389 cc) engine connected directly to a 3000 psi, 4 gpm triplex pump. The 200 ft capacity hose reel with reel brake is mounted on a rugged, heavy-duty frame with two flat-free foam core tires for maximum stability and easy handling.
General’s powerful gas and electric-powered water jets – with on-demand Vibra-Pulse® for greater nozzle thrust around tight bends and down long lines – offer professional drain cleaners indispensable weapons against all sorts of soft blockages. With a wide variety of “Jet-Set” models available, experts like Fantauzzo admire the line’s reliability, rugged technology, transportability, and safety features.
“Until we get our General trailer-mounted jet,” Fantauzzo smiles, “our JM-2900 handles 4″ and larger diameter lines!”
RELIABILITY VITAL
A General equipment user for over 15 years, he also owns a compact, portable JM-1450 electric water jet for smaller jobs – 1-1/2″ to 4″ lines.
The powerful JM-1450 generates 1500 psi at 1.7 gallons per minute – yet only pulls 13 amps. Also equipped with Vibra-Pulse® and General’s standard safety features, it’s powered by a 1-1/2 hp dual capacitor enclosed motor with an in-line ground fault circuit interrupter.
Fantauzzo says he “picked products I already trusted” when starting Mercer. Now his ample arsenal only sports General drain-cleaning and inspection solutions:
- A Gen-Eye® video system with digital locator.
- Two Speedrooter 91 root cutting machines for long, tough jobs.
- A compact Sewerooter T-4™ mid-range machine.
- Two Power-Vee® hand-held, auto-feed drain cleaners.
- A Kinetic Water Ram® – the lightweight, innovative, hand-held device that safely, quickly and cleanly clears clogs with powerful bursts of compressed air.
Fantauzzo often teams tools for optimal productivity. “We precisely spot and diagnose problems with our Gen-Eye, for instance – then use the right drain cleaner to complete the job.”
But water jets can’t clear heavy stoppages like tree roots, Fantauzzo cautions, and don’t replace cable machines. “That’s why we have our Speedrooter 91’s and Metro. Each tool has specific advantages. And each complements the other.”
REPUTATION CRITICAL
Fantauzzo offers a 30-day warranty on every drain-cleaning job. He never advertises. And 100% of his central New Jersey business comes from his fast growing roster of satisfied customers.
“But I can’t give a warranty if I don’t do the job right,” Fantauzzo says. “And I can’t do the job right if I don’t have the right tools.”
That’s why he’s built his business around drain-cleaning and inspection equipment from General Pipe Cleaners.
“I run my whole company with General products,” he declares. “They enhance our professional image!”
For more information, visit www.drainbrain.com/jets, or call the Drain Brains® at General 800-245-6200.
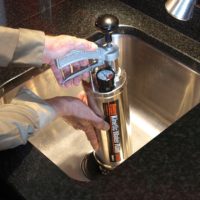
“I don’t want competitors to know I use this tool. Some customers think I have super powers.” That’s Omar Taylor talking about the lightweight, compact Kinetic Water Ram® from General Pipe Cleaners. The innovative tool safely, quickly and cleanly clears clogged sinks and showers, toilets and tubs with Kinetic Energy. And it’s given the young Read more
“I don’t want competitors to know I use this tool. Some customers think I have super powers.”
That’s Omar Taylor talking about the lightweight, compact Kinetic Water Ram® from General Pipe Cleaners.
The innovative tool safely, quickly and cleanly clears clogged sinks and showers, toilets and tubs with Kinetic Energy. And it’s given the young, Indiana-based plumber a clear competitive edge.
Taylor comes from three generations of professionals. In business for over six years, he routinely subcontracts for a major national plumbing and drain cleaning company specializing in franchise services.
“Jobs that take guys an hour with cable machines, I do in just 5 minutes,” he says. “It’s like they say in the movie, ‘Who you gonna call?’ With my Kinetic Water Ram, I handle emergencies super quick!”
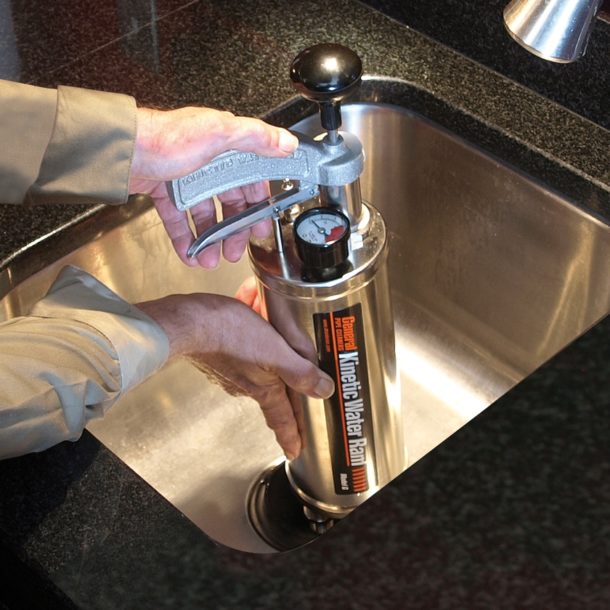
Fast, Clean Work
That’s why Taylor prefers General’s pioneering tool for rapidly clearing many common residential and commercial clogs. Call it his “secret identity”!
“I’ve earned a reputation for prompt, clean service with minimal disruption,” he says. “Most customers can’t believe how fast I handle their problems.”
Kinetic Water Ram unleashes a powerful burst of compressed air that drives a shock wave (kinetic energy) through water at 4,700 ft./second – instantly breaking up the stoppage. There’s no pressure build-up within the system, either. The shock wave bypasses stacks and vents. 98% of the force is directed down the line and only 2% against pipe walls.
The Kinetic Water Ram easily clears hair, rust, grease, sediment, and scale from lines from 1-1/4″ up to 4″ in diameter. It’s especially effective clearing slow draining tubs when the stoppage is on the far side of a drum trap – or through narrow lines in trailer homes that can be hard on a snake.
Amazing Versatility
Taylor first learned of the Kinetic Water Ram when a training supervisor watched him struggle snaking the old trap of a clogged basement shower drain.
“After a while he said, ‘Let me show you how to really do it, son’,” Taylor recalls. “The supervisor got his Kinetic Water Ram, pumped it up, and immediately cleared the clog.”
That’s when Taylor became a true believer.
“The Kinetic Water Ram is perfect for all kinds of drain cleaning problems,” he claims. “It’s amazing on grease in kitchen sinks, hair and scum in bathtubs, and toilet paper and disposable wipes in commodes.”
An optional toilet attachment screws onto the front of the Kinetic Water Ram – permitting firmer positioning in the bowl and acting like a powerful plunger.
The Pro’s Favorite
And Omar Taylor’s not the only “true believer.”
“It takes longer to write-up the bill than to unclog a drain with that tool.” says Dale Smith, owner of D. Smith Plumbing Services in Jayess, Mississippi.
“When several people call you early in the morning or late at night, you can’t afford to spend 3 or 4 hours at each place,” Smith adds. “The Kinetic Water Ram lets me do multiple jobs daily – with time to spare.”
Dale Smith calls it “amazing” on bathtubs. “I’ve cleared hundreds – many with old-fashioned lever-actuated stoppers that prevent me from using a cable machine,” he notes. “Kinetic Water Ram handles them all.”
Compact Design Scores Points
Smith also values the tool’s portability.
“In the past, I’ve snaked through roof vents to clear clogs,” he says. That meant dragging a heavy, awkward cable machine to the roof. “Now I can handle most jobs with my lightweight Kinetic Water Ram.”
General’s tool comes standard with flexible cone seals from 1-1/4″ to 4″ in diameter, caulking hose, and five tapered valves for sealing openings from 1-1/4″ through 4”. A Schraeder valve for use with an external air compressor when clearing difficult blockages is also provided.
Boosting Professionalism & Productivity
“It’s super-simple to use,” Omar Taylor concludes.
Simply pump the Kinetic Water Ram to the desired pressure, plug overflows to prevent splash back, and firmly position the flexible cone over the drain opening. One snap of the trigger unleashes a powerful shock wave, instantly clearing clogs.
That’s especially important when customers see Taylor clearing clogged drains with such amazing speed and cleanliness.
“They think I’m a ‘Super Hero’ of Indiana plumbers,” Taylor jokes. “That’s why I like keeping my Kinetic Water Ram secret from competitors!”