The Plastics Pipe Institute, Inc. (PPI) announced the winners of its Projects and Members of the Year program during its annual meeting held on May 5, 2020. A Project of the Year and a Member of the Year were selected for each of the five PPI divisions: Building and Construction, Drainage, Energy Piping Systems, Municipal and Industrial plus Power and Communications. The meeting was conducted on-line due to the coronavirus pandemic. PPI is the major North American trade association representing all segments of the plastic pipe industry.
“This year was a little different for us because it was the first time we could not physically congratulate each winner,” stated PPI President David Fink. ”But just as in years past, the nominated projects in each of our five divisions were remarkable and the winners exceptional. It was a healthy competition, and that must be very satisfying to the winners.”
The association’s annual awards program recognizes projects and members for exceptional contributions to the industry. Submissions in the association’s divisions are reviewed, evaluated and voted upon by the PPI members.
The PPI winning projects and members are:
PPI Building & Construction Division Project of the Year
- Vancouver International Airport Geoexchange System, Vancouver, Canada
- PPI Member Company: Versaprofiles, Saint-Lazare-de Bellechasse, Canada
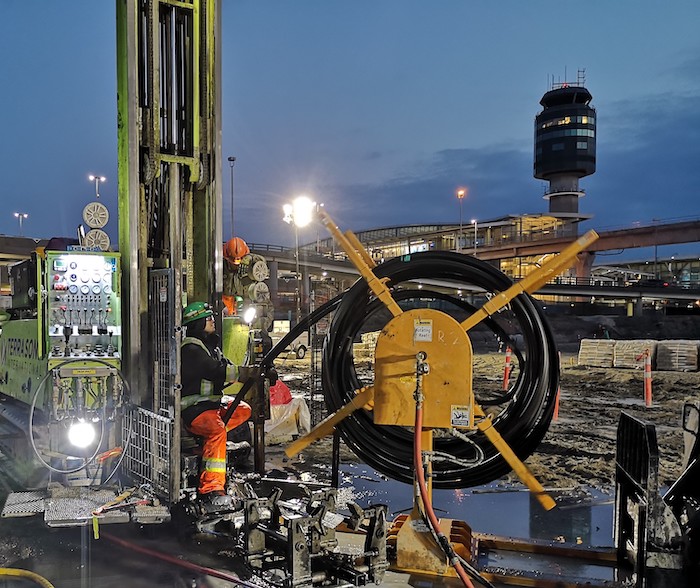
The Vancouver International Airport’s new Central Utilities Building (CUB) will improve efficiency by centralizing all of the equipment needed to meet the airport’s heating, cooling and electrical demand. To achieve this goal, the project will rely on one of the largest Geoexchange systems in Canada. Geoexchange technology uses the earth’s renewable energy, just below the surface, to heat or cool buildings. This system will provide sustainable heating and cooling for the terminal.
The borefield for the CUB Geoexchange system is substantial in size— 841 boreholes at 500 feet each in depth that equals 79.64 miles (420,500 feet) of drilled borehole and 159.28 miles (841,000 feet) of 1.25-inch HDPE 4710 piping. The Geoexchange system is expected to substantially reduce CO2 emissions from heating and cooling demands by 30 to 35 percent.
PPI Drainage Division Project of the Year
- Hugh K. Leatherman Sr. Terminal, North Charleston, South Carolina
- PPI Member Company: Advanced Drainage Systems, Inc., Hilliard, Ohio
The original storm drainage design for the new terminal incorporated reinforced concrete pipe and concrete box culverts. During the design phase of the project, the engineer became concerned about joint separation and the potential for infiltration due to predicted sub-surface soil settlement along the Cooper River. In order to mitigate joint separation and possible infiltration, Advanced Drainage Systems’ HP Storm Polypropylene Pipe was selected as the storm drain conveyance pipe for the entire project due to its ease of handling, extended joint, double gaskets, and flexible design. As a result of the redesign, some 27,000 feet of ADS HP STORM was used to convey all storm water on the 280+ acre site.
PPI Energy Piping Systems Division Project of the Year
- Henderson Municipal Gas (HMG) PA 12 Gas Pipe Installation, Henderson, Kentucky
- PPI Member Company: Teel Plastics, Inc., Baraboo, Wisconsin
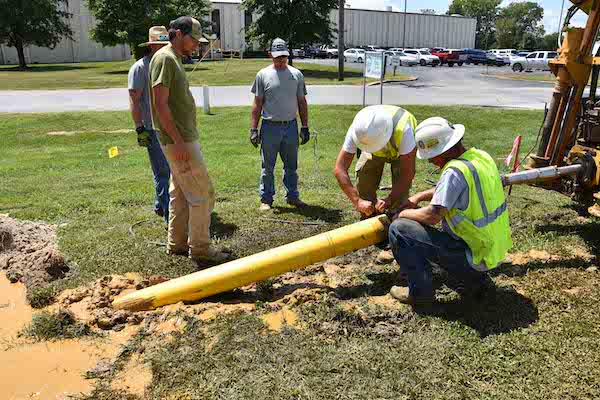
In a multi-stage project, the City of Henderson, Kentucky installed 2,720 feet of polyamide 12 (PA 12) gas pipe extruded by Teel Plastics. This marked the first PA 12 installation under the PHMSA Mega Rule effective January 2019, which allows PA 12 to be installed without a special permit.
HMG installed the pipe through an industrialized area of the city. To minimize disruption to businesses, Henderson installed it underneath driveways and existing utilities. HMG buried sections using horizontal directional drilling (HDD), pulling the pipe through bored holes and fusing the sections together. More ductile and much lighter than steel, PA 12 made the HDD installation much easier than it would have been with steel pipe.
PPI Municipal & Industrial Division Project of the Year
- Colsman Tunnel Sewer Sliplining, Centennial, Colorado
- PPI Member Company: WL Plastics, Ft. Worth, Texas
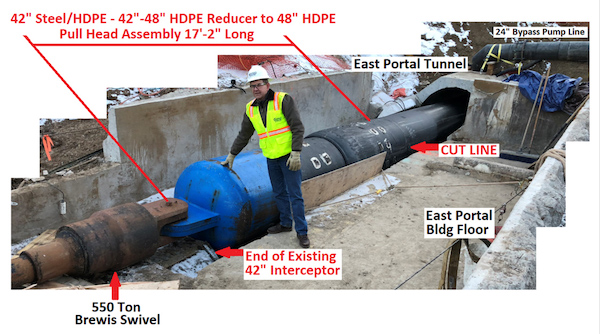
To rehabilitate a deteriorating brick sewer, 48-diameter HDPE pipe was sliplined into the old sewer. Flow was not allowed to stop during the pull, so a custom completely sealed pull head had to be designed and built so that sewage would not fill the drill string during the pull in. Another restriction was that the staging area only allowed for no more than 200 feet of pipe to be out of the tunnel at once. So, the pipe string was pulled as each stick of pipe was fused and added to the string of pipe. Total pull length was more than 8,000 feet. Custom winch system was brought in for the heavy pull that included two spools of wire cable to get the length required.
PPI Power & Communications Division Project of the Year
- Alliant Energy Private Fiber Optic Network, Madison, Wisconsin
- PPI Member Company: Teel Plastics, Baraboo, Wisconsin
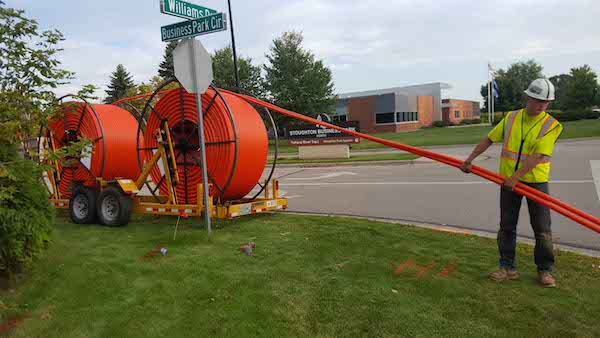
Teel conduit is being installed across Alliant’s service area in Iowa and Wisconsin to improve its telecom network’s security, speed, and reliability. For a utility with a large service area including more than 970,000 electric and 420,000 natural gas customers, reliability and capacity are is crucial during critical events. The conduit will protect the existing infrastructure and allow for later expansion of network capabilities while providing cost savings to Alliant Energy.
The cost savings associated with installation of the conduit and fiber benefits Alliant Energy in multiple ways. Replacing their telecommunication carriers with their own network will protect them from future price increases. Alliant Energy will also decrease their reliance on over-the-air communication, such as microwave radios. In addition, the fiber optic network serves as a gateway for Alliant Energy to work on advances in energy efficiency and technology, which would not be possible without a private fiber network.