Installing the right water filtration in industrial applications comes with a long list of benefits. A good filtration system helps lengthen the equipment life, cuts down the maintenance costs, creates a shield against hazardous chemicals, and lowers the effluent costs. It is how meticulously the water filtration process is planned and executed that makes or Read more
Air Venting Process
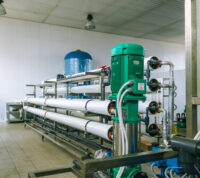
Installing the right water filtration in industrial applications comes with a long list of benefits. A good filtration system helps lengthen the equipment life, cuts down the maintenance costs, creates a shield against hazardous chemicals, and lowers the effluent costs.
It is how meticulously the water filtration process is planned and executed that makes or breaks the overall system. Anything could take a faulty turn when executing a filtration process. For instance, a wrong pump might cripple the filtration process, a seemingly harmless glitch during installation can cause irreversible filter damage, or an incorrect filter material can set the filter on a course towards pre-mature failure.
With a myriad of details and calculations involved, employing the right filtration solution for an application is no easy feat. However, becoming familiar with the most common (and frequently occurring) filtration mistakes can help ensure they’re avoided during the process.
This article discusses common pitfalls associated with selecting, installing, and using water filtration in industrial applications.
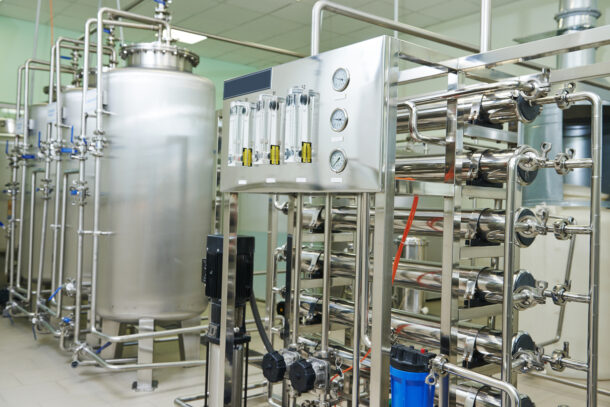
Getting the Sizing Wrong for Equipment and Filter Elements
As with everything, the planning stages are critical for installing and running a smooth filtration system. This is the stage that typically sees some of the costliest filtration mistakes – including the ones resulting from sizing issues
Faulty Filtration Equipment Sizing
When investing in filtration equipment, it’s paramount that the sizing aligns with what the application needs. The metric to consider when choosing the filter equipment is – the amount of liquid that the production would be running.
For instance, purchasing equipment that can push about 100 gallons a minute will not be of any use if a specific filtration step can only handle 10 gallons a minute. Not factoring in the flow rate during the process can negatively impact the production output.
Faulty Micron Rating
Filter specs can be customized as per the requirements of specific equipment. The customization options here typically include the core material, length, micron rating, diameter, filter media, and end cap configuration.
Among all the given options, micron rating is the trickiest to determine and has complete control over the filtration efficiency. If it’s too large, the contaminates can flow right through the filter. If it’s too small, the flow rate becomes obstructed.
A lot of research goes into finding the appropriate micron size. Most of it is associated with factors like the size and the consistency of the contaminants the equipment aims to filter.
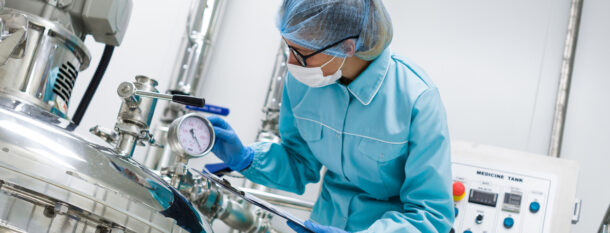
Employing Incompatible Materials For Filter Elements
The core, the seals, and the filter media come together to form a fully-functional filter. For a filter to achieve an optimal outcome, each element needs to be compatible with the fluid’s temperature and chemistry.
The core can be seen as the backbone of a filter. When the core itself is incompatible with the fluid, it can give in to the water pressure and practically crush the filter. This unleashes the trapped contaminants into the downstream fluid.
The filter media is the shield that stands between the fluid and the contaminants. When the fluid temperature or chemicals react negatively with the media, it simply bloats and clogs – impeding the flow rate. The risk reaches its peak when the fluid chemicals are too aggressive for the media to handle, causing it to dissolve completely.
Sealing materials like an o-ring or a gasket practically guard the clean side of the filter from the contaminated side. When the seal itself is dysfunctional, the unfiltered fluid merges with the clean fluid resulting in a situation commonly known as “bypass”. When neglected long enough, these seals can either dissolve or erode – opening a passageway for the unclean fluids to flood in. A great approach to avoid filtration fiascos from filter elements would be to follow a chemical compatibility chart.
Performing A Flawed Installation
One of the common errors that can pop up during the installation process includes the reversal of the pipe housings (when the inlet and outlet housings get swapped).
Typically, filters can only handle fluid flow in a single direction (exceptions include filters that are made for backflushing). Unless the system requires liquid filter bags, the usual flow direction is always from the outside in.
Such an installation flaw can obstruct the flow rate and eventually knock down the filter. Most inlet and outlet pipes are labeled with the flow direction to help installation teams perform the task accurately. The filter equipment manual also comes with comprehensive instructions to maintain high accuracy during installation.
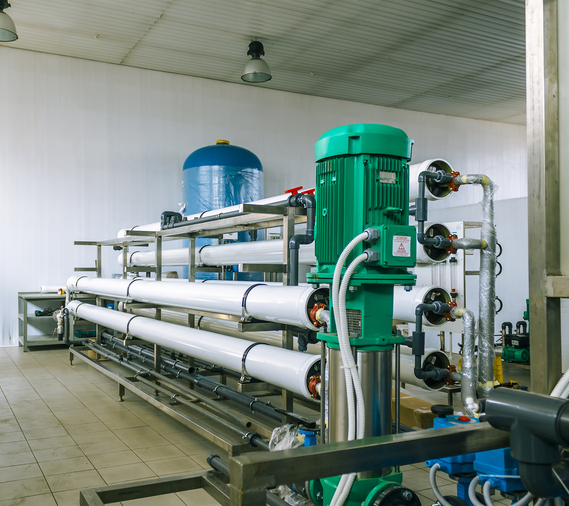
Selecting the Wrong Type of Pump
Pumps are what get the water flowing. In other words, they are the force behind driving the liquid through the filters. The outcome of a filter process depends on the type of pump employed in the system. It’s critical to ask the following questions when researching the right type of pump:
- What is the size of production runs?
- What is the viscosity of the liquid?
- What are the components within the process stream that may cause resistance to the flow rate?
- How far does the liquid travel?
Skipping the Air Venting Process
Once the filtration equipment is up and running, a critical step to remember would be to vent the air from the filter housings as the water seeps into them.
When ignored, the air trapped within the housing can form a bubble. This obstructs the liquid from filling up the housing completely. As a result, the overall flow rate declines.
Filter housings typically come with a built-in vent port or a vent valve that acts as the air’s escape route. To ensure the highest filter efficiency, the valve must be closed only when all the air leaves the housing.
Final Words
Even the smallest of “filtration glitches” can trigger irreversible damages down the line. As far as mistakes with water filtration are concerned, simply installing and running the process successfully is not the end of the task.
A filtration system demands regular maintenance to ensure the filter runs efficiently for a long time. A lack of maintenance can lead to clogged filters and loosened seals – degrading the quality of the final outcome.
Lastly, it’s critical to leave no doubt unaddressed when working with water filtration. In most cases, seeking the help of a professional is the best approach to getting everything “just right” and avoiding expensive losses down the line.
Author Bio: Mark Ligon is the marketing manager at Commercial Filtration Supply. He oversees the development of business strategies and marketing of filtration products, including bag filters, cartridge filters, and strainers. Ligon writes about various liquid filtration applications to educate process and facility managers on best practices, ensuring they properly understand and care for their filter systems.