Known as quick-connect, push-on or push-fit, these breakthrough plumbing products are often at the center of plucky online debates. Since entering the U.S. plumbing market in 2004, the design and technology of push-to-connect fittings have revolutionized the industry as a quick, reliable, tool-free solution for connecting small potable water pipes. Driven by feedback from plumbers Read more
brass
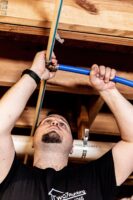
Known as quick-connect, push-on or push-fit, these breakthrough plumbing products are often at the center of plucky online debates. Since entering the U.S. plumbing market in 2004, the design and technology of push-to-connect fittings have revolutionized the industry as a quick, reliable, tool-free solution for connecting small potable water pipes. Driven by feedback from plumbers, this product class has evolved robust designs made of materials like rubber, silicon, brass and stainless steel, incorporating key components such as o-ring seals and gripping mechanisms.
But are they best used only as a temporary fix as some users claim, or can you count on them for a variety of long-term uses? We let the facts flow freely so you can make an informed decision on whether to give these fittings a try.
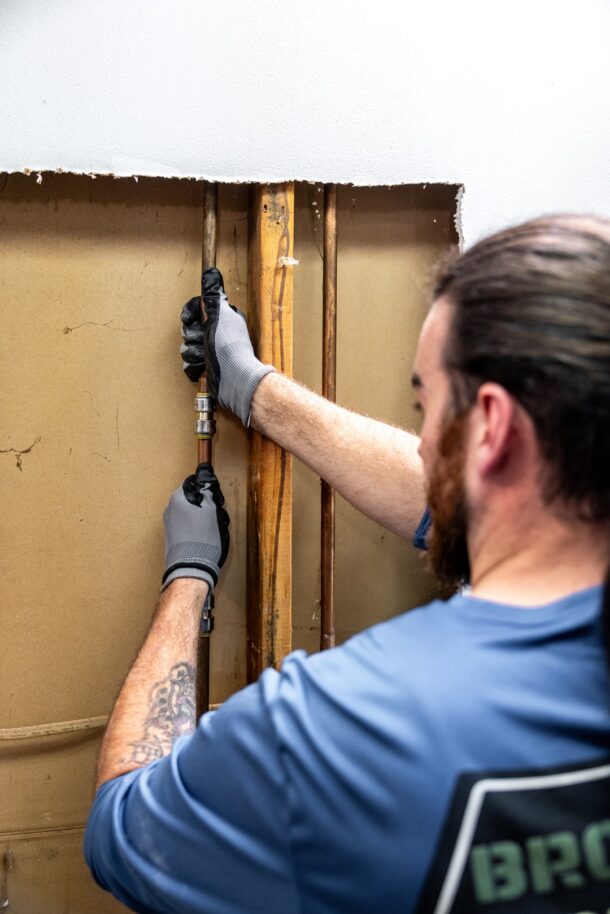
Rapid Adoption and Evolution
Two decades of innovation have made push-to-connect fittings indispensable for applications ranging from residential plumbing to advanced manufacturing. The most common uses are in residential service and repair, including some new builds. They went through a lead-free transition to newer models that are stronger and more durable, accelerating adoption further.
The American-made SharkBite Max model sets the industry standard with a stainless-steel retainer around the outside and a pressure rating of 250 psi. This doubled the burst pressure limit of the original model, the most popular push-to-connect fitting. A deeper insertion depth allows the new model’s steel teeth to engage the pipe more effectively, creating a stronger connection that eliminates the need for an interior tube liner.
Primary Benefits and Advantages of Push-to-Connect Fittings
Using push-on fittings means shorter installation times, fewer errors to correct, and easy, versatile disconnections and reconfigurations. No soldering, crimping, glue or special tools are needed for installation. Unlike conventional approaches, the pipe doesn’t need to be dry before making a connection. Water can be pouring out of a pipe and these fittings can still be quickly connected without a tool, even in a tight space, making them an excellent option for pipe repairs.
Knowing leaks and pipe aging are inevitable, it’s a good practice to keep some push-fit fittings handy. If it’s a failed joint pinhole leak, a push-to-connect fitting can be a fast, reliable and inexpensive solution, especially in areas where pipes are prone to freezing and bursting.
Other strengths of today’s push-fit models include:
- Perfect for transitioning between pipe materials, including copper, PVC, PEX, CPVC, PE-RT and HDPE (SDR-9)
- Fitting rotates around the pipe even after it’s connected
- Strong manufacturer warranties (SharkBite Max warranty is 25 years)
- Code approved to be buried underground (when wrapped in silicone tape) or installed behind walls
- Compliant with all regulatory changes
The simplicity and efficiency of push fittings have streamlined a handful of core plumbing tasks and even helped address labor shortages by making it easier to get new plumbers out in the field performing repairs quickly. They’ve also made basic and emergency plumbing repairs accessible to DIYers. However, despite their versatility, they’re not ideal for every situation.
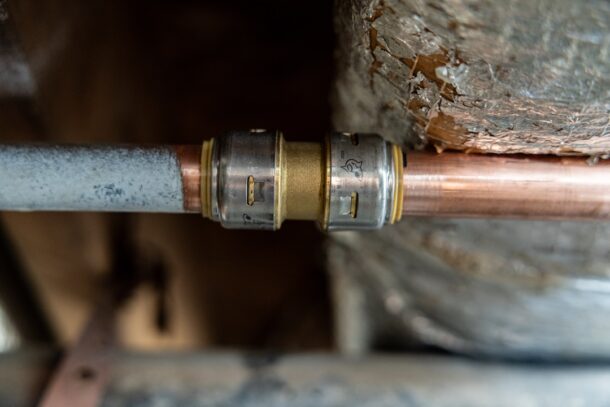
Drawbacks, Limitations and Criticisms
Push fittings must be used in the right way to capitalize on their advantages. In the rare case when there’s a problem, installing them improperly or in a spot they’re not designed for is almost always the cause. By keeping a few points in mind, you can make the right decision every time on when and where to use them.
Here are the main things to consider for a smooth experience:
Initial Cost: The best push-to-connect fittings can be a bit pricier than soldering or crimping. You’ll save big on labor installing them faster, but the upfront cost per fitting can be higher.
Compatibility Limits: While leading push-fit fittings are compatible with almost all pipe types, they don’t work with everything, like galvanized steel or flexible hoses. And they still require specific fittings for certain transitions, like polybutylene to CTS tubing. This adds a step to some jobs and possibly to inventory management.
Not for All Applications: Standard push fittings are certified for potable water and radiant heating installations, limiting their use in industrial plumbing. Exceeding the certified limits (250 psi and 200°F for Max fittings) can lead to failures, so they’re not suitable for all high-pressure or high-temperature applications.
Designed for Single Use: While push-to-connect fittings can be removed if you need to adjust or test, they’re not designed to be reused multiple times in permanent installations. The integrity of the seal may be compromised with repeated removal and reinsertion.
Spotting Leaks: All push-to-connect fittings rely on o-rings for sealing. If the fitting isn’t installed correctly — such as failing to deburr the pipe — or gets jarred out of place inadvertently, the o-ring can get damaged, potentially leading to leaks. Although rare, leaks inside the fitting can be tougher to spot, so they might not be noticed immediately.
You’re best off choosing manufacturers that are transparent about the materials they use in their fittings, especially the o-rings since they keep the seal. For example, SharkBite Max o-rings are made of a specific type of rubber called EPDM (Ethylene Propylene Diene Monomer), chosen for its durability, flexibility and chemical resistance:
- EPDM is known for its resistance to aging and degradation, making it suitable for long-term plumbing applications
- It maintains its flexibility even at lower temperatures, ensuring a good seal
- EPDM is specifically selected for its resistance to chloramine, a disinfectant chemical often added to municipal water
Of these concerns, leaks are the most hotly debated. Some professionals still hesitate to use push-to-connect fittings behind walls because of concerns about long-term reliability and potential hidden leaks. But after two decades of continuous improvement and in-wall use by plumbers in homes and other buildings across America, these isolated instances can always be traced back to user error. Common causes of fitting failure include:
- Pipe that is unevenly cut, not deburred or not free of debris, potentially preventing a secure seal
- Using the wrong fitting for the wrong application
- Not marking the insertion depth to ensure that you pushed the pipe all the way into the fitting
- Not wrapping fittings in silicone tape that protects it from soil contaminants
- Rough or repeated disconnection
When it comes to quality, the widespread adoption of push-to-connect fittings speaks for itself. But don’t take anyone’s word for it. Test them out for yourself and you’ll see why they’ve become so popular with pros everywhere.
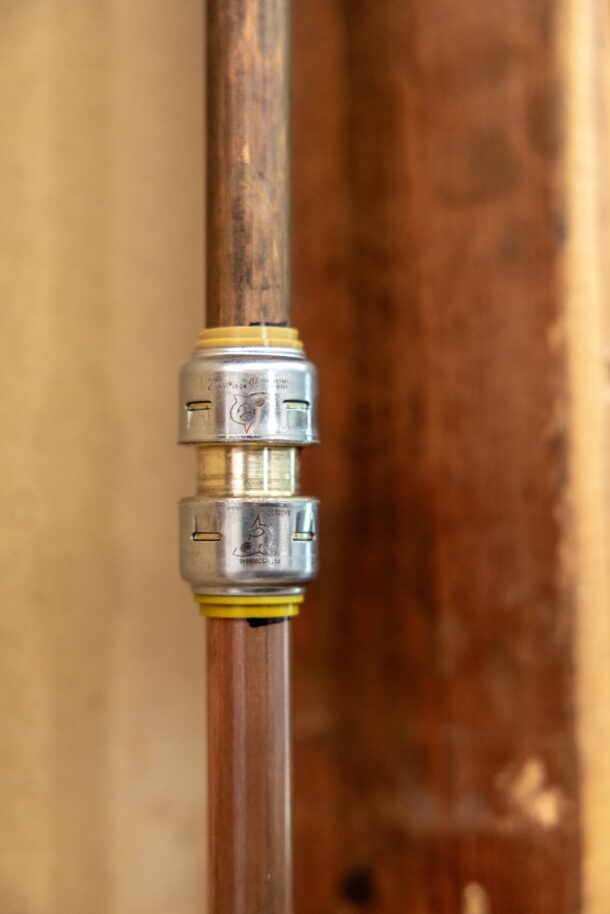
Plumbers Shape the Evolution of Push-to-Connect Technology
You can play a role in shaping this product’s evolution by sharing your thoughts and experiences directly with manufacturers. The best way to help drive the evolution of plumbing technology is for plumbers of all skill levels to share and connect online—post product reviews and reach out with comments and questions on social media or through company websites. Equipment manufacturers can serve you best when they hear from you often, and the most innovative tend to be more responsive to feedback.
Some manufacturers have employees who will share free resources like training materials and demonstrations to help plumbers integrate their game-changing products. If you ask nicely, they might even send someone to walk the job site with you when they can. Dropping the company a line on your favorite social channel is a great way to make another connection that’s built to last.
Written by Matt Glenn, senior product manager at RWC, a market leader and manufacturer of water control systems and plumbing solutions for residential, commercial and industrial applications.