Hailed for savings directly related to installation and labor time, Sioux Chief’s StrongArm bracketing systems provide a clean and strong solution for Stub Outs. Sioux Chief’s StrongArm video demonstrates the high quality and versatility of the product.Rough plumbing manufacturer, Sioux Chief, announced the launch of its new StrongArm product video that enables plumbing contractors and wholesalers to Read more
contractors
Hailed for savings directly related to installation and labor time, Sioux Chief’s StrongArm bracketing systems provide a clean and strong solution for Stub Outs. Sioux Chief’s StrongArm video demonstrates the high quality and versatility of the product.Rough plumbing manufacturer, Sioux Chief, announced the launch of its new StrongArm product video that enables plumbing contractors and wholesalers to know more about Sioux Chief design innovation, product features and installation techniques.Each StrongArm is pre-assembled with either one or two LockBlocks™ or PEX Bend Supports for toilet, lavatory, sinks or hose bib Stub Outs. Sioux Chief offers many options that allow the brackets to be mounted to the face of the studs, inside the stud cavity or directly to the pipe vent.“The StrongArm bracketing system was created because plumbing contractors who install PEX tubing and other flexible pipe materials told us they needed a very secure bracketing system — something that sheetrockers can’t tear up and that also removes the torch from the job site.” Said Rex Baer, Vice President of Product Development at Sioux Chief.Key features of the StrongArm are:Rigidly secures to any copper, PEX or CPVC CTS Stub Out and prevents any movementVersatile for 16″ and 24″ stud bays with either one or two pre-installed LockBlock devicesEliminates the need to solder Stub OutsRemoves the risk that Stub Outs will be damaged by other tradesThe new Sioux Chief rough plumbing video series offers plumbing contractors need-to-know information about time, labor and money saving innovations in Sioux Chief’s Supply, Drainage and Support categories.Sioux Chief products are sold through wholesale plumbing distributors nationwide.
via Sioux Chief Launches StrongArm™ Product Video | Sioux Chief Blog.
ModCon Boiler Piping for Peak Performance Join Bob Rohr, Caleffi training and education manager, as he discusses ModCon boiler piping and dives into these topics: – Not your grandfather’s boiler: what makes ModCon piping unique? – The top three concerns for piping a ModCon… it’s all about the flow! – How can ModCons benefit from additional Read more
ModCon Boiler Piping for Peak Performance
Join Bob Rohr, Caleffi training and education manager, as he discusses ModCon boiler piping and dives into these topics:
– Not your grandfather’s boiler: what makes ModCon piping unique?
– The top three concerns for piping a ModCon… it’s all about the flow!
– How can ModCons benefit from additional mass or fluid capacity?
– Have you heard about hybrid boiler piping? It could be the ideal method for your installations!
Answers to these questions and more will be addressed during the webinar presented by Bob Rohr.
Coffee With Caleffi™ training webinars are intended for contractors, designers and wholesalers. A Certificate of Participation is provided upon your request (simply say “Yes” in the post-webinar survey).
You can register by clicking the link below and following the instructions. After registering, you will be immediately forwarded a confirming e-mail containing log-in details for attending the webinar. When training time comes, grab a coffee, tune in and learn more about Caleffi’s innovative products and how they can add value to your work.
If you have questions on content, please direct them to bob.rohr@caleffi.com and be sure to follow us @CaleffiUS.
All Coffee with Caleffi webinars are free.
via GoToWebinar : Webinars Made Easy. Award-Winning Web Casting & Online Seminar Hosting Software.
FRANKLIN PARK, IL — Sloan’s newest online education course covers the entire vitreous china fixture product line, including sinks, toilets and urinals, to complete the commercial restroom. The free course, which lasts about 15 minutes, can be taken at any time. The non-technical course presents a broad overview of the Sloan vitreous china fixture line Read more
FRANKLIN PARK, IL — Sloan’s newest online education course covers the entire vitreous china fixture product line, including sinks, toilets and urinals, to complete the commercial restroom. The free course, which lasts about 15 minutes, can be taken at any time.
The non-technical course presents a broad overview of the Sloan vitreous china fixture line:
* Small, retrofit and standard-sized washdown urinals;
* Wall-hung and floor-mount water closets, including High-Efficiency Toilets that operate with dual-flush and other water-efficient flushometers;
* Gravity Series single- and dual-flush tank toilets;
* Undermount, drop-in and wall-hung lavatory sinks; and
* Four Waterfree Urinal models.
The vitreous china fixtures course also covers specification tips, applicable plumbing codes and standards, and specific features, such as Sloan’s Universal Fixtures, which allow a single fixture to operate with multiple flush volumes of your favorite Sloan flushometer.
“This course is ideal for wholesalers, building owners, engineers, contractors, architects—anyone who would like to know more about Sloan’s vitreous china fixtures,” says Mark Lawinger, Sloan fixtures product line manager. “I definitely recommend the course to professionals who are new to Sloan, as well as those who are familiar with our products and would like a good refresher.”
Access the free course, as well as Sloan’s other online courses, at: http://sloanvalve.com/Continuing_Education.aspx.
Sloan is the world’s leading manufacturer of commercial plumbing systems and has been in operation since 1906. Headquartered in Franklin Park, Illinois, the company is at the forefront of the green building movement and provides sustainable restroom solutions by manufacturing water-efficient products such as flush valves, electronic faucets and soap dispensing systems, sink systems and vitreous china fixtures for commercial, industrial and institutional markets worldwide.
For more information about this and other continuing education courses, contact Sloan, 10500 Seymour Avenue, Franklin Park, IL 60131.
Telephone 800-9-VALVE-9 (982-5839) or visit www.sloanvalve.com.
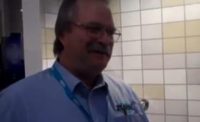
Orlando Plumbing Company finds success ‘The Modern Way’ No job in the Orlando area is too small – or too big – for Modern Plumbing Industries, Inc. (MPI). On the residential side, the Winter Springs company gets a constant flow of testimonials from customers like Ken, who wrote, “Modern Plumbing is fast, friendly and Read more
Orlando Plumbing Company finds success ‘The Modern Way’
No job in the Orlando area is too small – or too big – for Modern Plumbing Industries, Inc. (MPI). On the residential side, the Winter Springs company gets a constant flow of testimonials from customers like Ken, who wrote, “Modern Plumbing is fast, friendly and gets the job done when they say they will. Prices are the best I can find. They follow up and schedule the work to be done very fast. They are simply the best.”
At the other end of spectrum, The Whiting-Turner Contracting Company called on Modern to coordinate plumbing work for the University of Central Florida’s Burnett School of Biomedical Sciences, a 198,000-square-foot research facility. The LEED Silver project included offices, laboratories and a vivarium with more than 24 miles of piping.
When the project was finished in 2009, Modern received an ABC Eagle Award for construction excellence for its work, which included:
• Domestic water, animal water, and laboratory water systems
• Reverse osmosis water systems
• Chemical waste, storm and sanitary systems
• Two natural gas systems
• Lab vacuum, compressed air (regular and high pressure), carbon dioxide and two specialty gas systems
“Regardless of the size of the job, we give our customers the same high level of service, which we call The Modern Way,” said Charles Bracco, Vice President, in a recent interview. “It’s a philosophy based on taking pride in what we do, providing service with honesty and integrity, and doing things right the first time.”
Modern Plumbing is also taking advantage of today’s technology with a dynamic website, including a blog, and a strong social media presence designed to attract service and repair customers. “A large commercial contractor isn’t going to visit our website to see if we can do a $5 million project for them,” said Bracco. “But having an informative and helpful website is crucial for connecting with our service customers, and we will continue to invest in that marketing channel.”
Modern Plumbing also equips its service technicians and project supervisors with iPads that connect with the office as well as the company’s Building Information Modeling (BIM) system. “A foreman in the field can see the complete model right on the iPad,” said Bracco.
Nearly four decades of service
Back in 1972, Frank Bracco moved from New Jersey to Orlando and opened Modern Plumbing Industries three years later. Charles was born in 1977 followed by his brother Anthony. As the boys grew, so did Modern.
“Central Florida was growing quickly in the late 1970s, and my father worked on 600-plus new houses per year for U.S. Homes,” Bracco said. “He got right into the residential housing market, but when mortgage rates spiked in the early 1980s, he quickly saw greater opportunity in commercial markets.”
Frank Bracco built the company to include four business units: plumbing, site work, irrigation and fire-sprinkler. But in the late 1980s, he decided to downsize and focus on the company’s core competency, which had always been plumbing.
By the mid 1990s, Modern was growing again and began to see increases in project size. “Our job size grew from about $100,000 to more than $1 million by 1997 and eventually became the $5 and $6 million projects we are doing today,” Bracco said.
During the recent economic downturn, the company reduced its workforce, but was one of the few contractors that didn’t cut wages, Bracco said. “We had a strong balance sheet, which was a big help,” he added. “Other companies that were highly leveraged with a lot of debt found it very challenging to get through the recession.”
Today, Modern Plumbing has about 70 employees and a well-diversified portfolio of projects, including biomedical research facilities, hospitals, medical offices, schools, offices and hotels. The company serves commercial, industrial, and residential customers in Seminole, Orange and Osceola counties as well as the surrounding Central Florida region.
“One of the big challenges our industry is facing today is a shortage of skilled labor,” Bracco said. “Our company has always been active in apprenticeships in Seminole County. But we have to figure out how to get the kids in high school interested in plumbing or we won’t have anyone to build new projects over the next few decades. While plumbing is hard work, if you get some experience and learn in the field, there are plenty of opportunities to make a good living and move up to being a foreman or manager.”
Modern believes in safety first. Bracco is a strong supporter of OSHA and other safety standards. “We conduct regular training for team members who are in the field, and many of our foreman have earned the OSHA 30 hour certification,” he added. “That emphasis on safety is just one of the reasons that general contractors who focus on quality will call us for a plumbing quote on their projects. We’re known as a company that gets the job done right.”
A change in leadership
After 38 years of running Modern Plumbing Frank Bracco moved into semi-retirement this September, still coming into the office, but not every day. This was the culmination of a transition of leadership that began a decade ago.
Back in 2003, Charles Bracco was working in California and Anthony Bracco was at the University of South Florida in Tampa. “We decided to move back home, work with our dad and see what we could do with the business,” Bracco said. “We knew that succession planning is always a big challenge for family businesses, and we wanted to put a structure in place to make the transition from one generation to the next.”
Over the next few years, the three Braccos talked about the direction to take the company and the infrastructure needed to follow that path. While the recession slowed their planning, the younger Braccos steadily played a greater role in the organization, supported by their father and the company’s long-time employees. Charles is now the General Manager and Anthony is the Director of Sales and Marketing.
“We felt that doing service and repair work provided the critical flow of revenue during the recession, and we mostly stuck with projects within a 25-mile radius of our office,” Bracco said. “We also took on projects near the homes of our technicians, who live in different counties, in order to minimize their drive time.”
As the result of a lagging economy in Central Florida, Modern Plumbing expanded its geographic scope, taking on major commercial projects like the Vaccine Gene Therapy Institute (VGTI) biomedical research facility in Port St. Lucie and the Air Force Technical Applications Center at Patrick Air Force Base near Cocoa Beach. “We can team up with our general contractors to do work around Florida or at military bases outside the state,” Bracco said.
Looking ahead to 2014, Bracco expects the non-residential markets to pick up steam in the coming year. “Between new schools, hotels, UCF and the theme parks, we think Central Florida is going to be a hotbed of new construction activity,” he said. “To the east, renovation of the Daytona International Speedway and construction of a Hard Rock hotel and retail complex mean a lot of new work in the Daytona Beach area. With a great team in place, we see lots of good opportunities to keep growing our company in the next few years.”
Modern Plumbing Industries, Inc.
255 Old Sanford Oviedo Rd.
Winter Springs, FL, 32708
407.327.6000
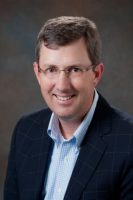
So I travel a lot, in the air almost every week. I am in Atlanta, flying on to Michigan for a few days. I am a 1K on United, flew over 100,000 miles with them last year, will be about the same this year. That is a big deal, when I call for help they Read more
So I travel a lot, in the air almost every week. I am in Atlanta, flying on to Michigan for a few days. I am a 1K on United, flew over 100,000 miles with them last year, will be about the same this year. That is a big deal, when I call for help they know my number, ask how is Mr. Hinshaw today?
I am in Atlanta, waiting a gate 15 for my flight leaving at 5:30 PM. It boarded at 4:55 just fine, I am in 3 C, sat down and promptly fell asleep. Woke up at 6:00, still sitting on the runway, which is not a good thing. The Captain comes on, tells us we are heading back to the gate, some sort of mechanical issue. Full disclosure, I am glad we went back to the gate. I am confident that any sort of problem on an airplane can be fixed better 5 feet off the ground than they can at 30,000 feet.
When we got back to the gate, the pilot says we are going to disembark. Get off the plane. That is a very bad thing, means they are sure that plane is not going anywhere. So we get off the plane, I look at the surrounding gates, notice that there is a flight going to the same city leaving from gate 14, in 45 minutes, how great is that?
All good until I hear them announce that flight is cancelled due to mechanical problems. Wow, two planes going to same city, adjacent gates, and both with mechanical problems. Unbelievable.
I get on the phone, my United agent says, how are you Mr. Hinshaw? I tell her not so well, she says I know, you are stuck in Atlanta! She says both the flights to my city are down, she had already booked me on a Delta flight leaving in two hours, exit row, aisle seat! How great is that. Gets even better. At the Delta gate I witnessed the best gate agent ever.
He called out each passenger by name as he checked their boarding pass: how are we doing Mr. Jones, what a great hat Mrs. Smith. Every customer. It was amazing. I was there an hour early, watched him in action on the flight before mine. When he was finished with the earlier flight, he asked me where I was from. Told him Colorado, he asked if I could recommend a ski resort. I told him we had been to Copper Mountain several times, and while we did not ski, we had friends who did and they said it was excellent. And it is close to Denver, at least compared to some that are a lot further up the mountain. He actually took notes, thanked me for the reference.
How long has it been since you or someone from your company has delighted a customer? Where they were not just satisfied, but rather you turned them into raving fans. Where the experience was exceptional, much better than they had ever imagined. It may be as a result of a problem that occurred (my experience with United), or the fact that they showed they cared while doing their job, such as Delta. Either way, it is so rare that a company goes above and beyond that we are amazed when it happens.
So equip your employees to make a difference in the lives of your customers, to provide an outstanding experience. In most cases our customers have not actually done a project of this magnitude before, no matter if we are talking about a new comfort system, a total remodel of the master bath or a 5 KW solar system installed on the roof. We may have done 40 jobs just like this in the past, but not in this home. This may be the first time this customer has ever opened up their home in this manner; they don’t know what is going to happen next. Make sure your team helps them feel good about it,