Whether completing repairs, a remodel or a new build, having the right pipe connections is paramount to completing a quality project. There are a lot of plumbing technologies available to pros, but not every option improves a project’s quality and efficiency like push-to-connect fittings. The leader of push-to-connect plumbing, SharkBite, wants to reiterate the importance of using Read more
Copper
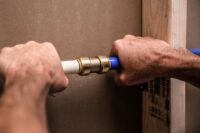
Whether completing repairs, a remodel or a new build, having the right pipe connections is paramount to completing a quality project. There are a lot of plumbing technologies available to pros, but not every option improves a project’s quality and efficiency like push-to-connect fittings. The leader of push-to-connect plumbing, SharkBite, wants to reiterate the importance of using the best tools available, knowing quality products will help plumbers complete jobs fast and with confidence. In doing so, the Reliance Worldwide Corporation (RWC) brand is underscoring the reasons its fittings are always an asset on pros’ trucks:
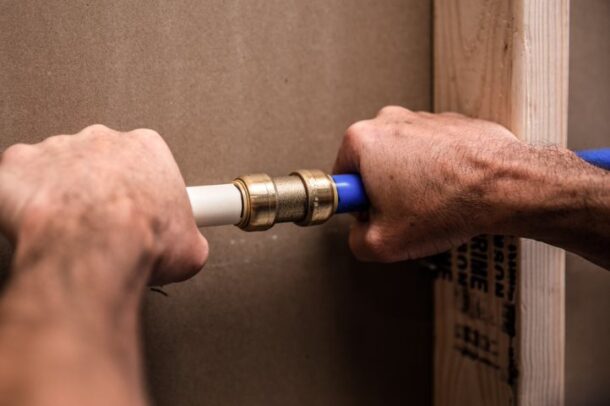
- They’re compatible with PEX, copper, CPVC, HDPE and PE-RT, polybutylene and PVC pipes, allowing pros to transition from one pipe to another in any combination.
- Fittings don’t require tools, soldering or glue.
- They can be installed without having to wait for pipes to dry.
- Fittings can be buried once wrapped in self-adhering silicone tape.
- They can be installed behind the walls.
- They’re easy to install in tight spaces.
With these capabilities, push-to-connect fittings save time on the job site, improving versatility, efficiency and quality for pros. If you’d like more details to share with your audience, please reach out. I’d be happy to set up an interview, discuss a byline opportunity or provide further information.
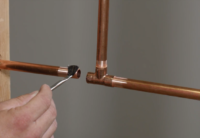
There’s a strong chance you’ve installed or spotted copper pipe somewhere in a home or building. Copper is the metal of choice for potable water systems for a variety of reasons – the most important being that it is non-toxic and safe for drinking. The naturally occurring metal element is also preferred for various application Read more
There’s a strong chance you’ve installed or spotted copper pipe somewhere in a home or building. Copper is the metal of choice for potable water systems for a variety of reasons – the most important being that it is non-toxic and safe for drinking. The naturally occurring metal element is also preferred for various application types due to its high conductivity of electricity and heat, corrosion/fire resistance and durability.
The process of joining copper pipe and fitting is called soldering (or sweating), which is a critical step in the copper installation process. Solder is a metal or metallic alloy that historically consisted of lead (known as lead-based solder) and tin in various proportions. Today, due to the Safe Water Drinking Act and lead-free restrictions, solders that contain more than 0.2% lead are not permitted for use in potable water systems.
Solders that are safe to use on potable water systems contain a percentage of tin and a combination of other non-toxic metals. The melting point of solder is lower than copper, and when heated, solder melts and fuses the piping together once completely cooled.
Learning how to solder copper pipe can seem daunting at first, but by applying proper techniques and avoiding typical errors, it becomes much easier to execute a leak-free pipe joint.
Let’s explore five common mistakes to avoid during the soldering process.
Choosing the Wrong Products
In addition to choosing the proper type of solder for your application, you will need to select the right type of copper pipe and flux, a compound that promotes the flow of molten solder between the pipe and fitting through a process known as capillary action.
Flux is also formulated to remove any oxidation from pipe and actually etches pipe surface in preparation for the soldering process to be successful. Important variables, such as ambient temperature, local code guidelines, and any jobsite time limitations, should all be considered prior to purchasing your soldering supplies.
Below, we’ve included some brief guidelines to keep in mind for your next soldering project.
- Copper Pipe
- Type K: Has the thickest wall and strongest durability. It is commonly used for commercial plumbing, such as underground water mains for potable water supply and HVAC lines.
- Type L: Wall thickness falls between Type K and M. Typically used for interior hot and cold-water distribution.
- Type M: Has the thinnest wall and is the most popular choice for domestic plumbing systems due to its light weight, decreased rigidity and affordability.
- Copper DWV: Commonly used in older homes for vents and drains. No longer a popular choice among modern-day homeowners, as there are more cost-effective options available.
- Flux
- Petroleum-based Flux (or Petrolatum Flux): Flushing required and designed to provide superior wetting properties for better solder flow. Compatible with all common plumbing solder alloys, such as copper, copper-coated metals, brass, zinc, galvanized iron, lead and tin.
- Hot Weather Flux: Specially formulated for hot weather climates and will not separate in temperatures up to 135°F.
- Water-soluble Flux: Water flushable and compatible with all common plumbing solder alloys.
- Tinning Flux: Available in both water-soluble and petroleum-based formulas. Enhanced with tinning powder particles to pre-tin piping and improve the flow of solder/enable even heating of a fitting, which is necessary when soldering larger diameter piping systems. Compatible with all common plumbing solder alloys. Check out this article to learn how to expertly solder low-lead brass using tinning flux.
Although petroleum-based fluxes are safe to use, they are required to be flushed with a chemical solution from the piping system due to their water insolubility. However, water-soluble fluxes become self-cleaning and flush away once water enters the system. Refer to manufacturer instructions for product-specific application and safety guidelines to ensure proper use.
- Solder
- Tin-antimony Solder: Contains 95% and 5% antimony. Lead-free and safe for water supply lines. Designed for use in plumbing applications where frequent extreme temperature changes and vibrations occur (refrigeration, cooling equipment and heat ducts); can also be used to solder electronics. Melting range is 450°F to 464°F. Has an unlimited shelf life.
- Copper-tin Solder: Contains 97% tin and 3% copper. Lead-free and safe for water supply lines. Designed for sweating copper and brass plumbing joints. Melting range is 440°F to 572°F. Has an unlimited shelf life.
- Silver-bearing solder: Contains silver, copper, bismuth and tin. Lead-free and safe for water supply lines. Ideal for low-lead brass applications. Has a wide melting range (420°F to 460°F) that enables more time for soldering joints.
Skipping the Prep
Failure to properly prep both the pipe and fitting is arguably one of the most critical mistakes in the soldering process. To achieve a properly sealed joint, oxidation and oils on the copper surfaces must be removed using special cleaning tools. Otherwise, it’s likely the solder will not completely fill the cup of the fitting, resulting in a weak or leaky joint.
Each of the following steps should be completed as you prep copper pipe for the perfect joint:
- After cutting the copper to the desired length, deburr (or ream) the inside of pipe end using a deburring tool to remove any small bumps or roughness (known as burrs) on the inside diameter or the pipe. If this step is overlooked, pipe pressure will decrease and water flow will be restricted. Any leftover burrs or copper shavings could cause noisy pipes when water enters the system.
- Remove oils and dirt from the outside of pipe end and polish clean with an abrasive sand cloth, open mesh cloth, nylon grit pad or tube cleaning brush. For wet applications, a nylon grit pad or open-mesh cloth are ideal due to their self-cleaning abilities.
- Clean all openings of the fitting hub with a fitting brush.
Applying Too Much Flux
It can be tempting to use a large glob of flux while soldering. However, we recommend evenly applying a thin layer of this product with an acid brush to copper pipe and the inside of a fitting – any excess flux should be removed prior to connecting them.
Applying too much flux will not only result in uselessly wasted product, but could also cause severe pipe damage over time. Once heat is applied to flux it turns to an acid; however, any excess flux will melt and travel through the inside of pipe, which may result in pitting and corrosion.
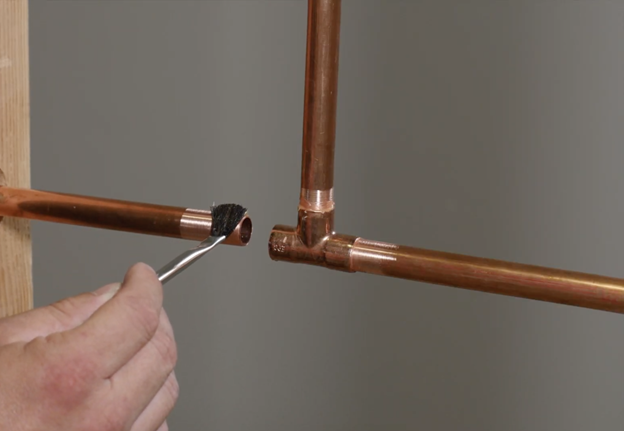
Overheating the Joint
When heating the fitting to sweat the copper pipe, make sure you remove the flame as soon the solder melts. As solder melts, flux will pull the solder into the fitting cup. Too much heat will cause excess solder flow or flux to burn out, which will increase the chance of a leak path.
Pro Tip: Never heat solder directly because you risk melting and breaking it off completely. It’s best to heat the joint evenly and then position the tip of the flame to the bottom of the fitting hub. The solder will flow toward the heat source and ensure the joint is completely filled.
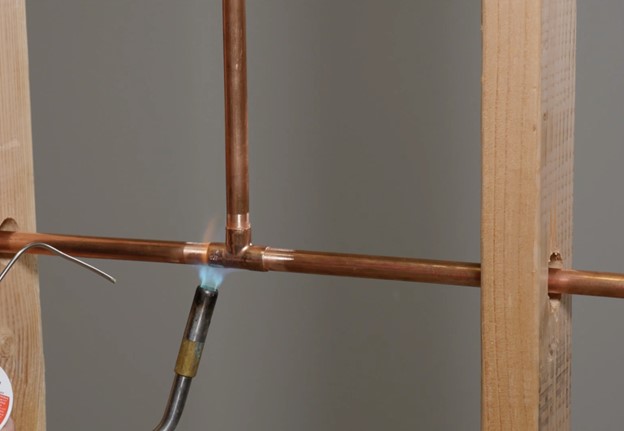
Neglecting Clean Up
While the joint is still warm, immediately wipe away any leftover flux or solder drips with a dry rag to ensure copper pipe longevity. Excess flux may seem harmless; however, it can cause Verdigris, a greenish-blue discoloration commonly found on copper, bronze and brass, to form and destroy copper pipe over time. An old, rusting penny and the Statue of Liberty are great examples of Verdigris in action.

READY FOR YOUR NEXT SOLDERING PROJECT?
For a step-by-step guide on how to solder copper pipe, check out the video below.
Author’s biography: Sean Comerford is a Technical Customer Service Specialist at Oatey Co. He is a third-generation tradesman with nearly 20 years of plumbing experience, including serving as the lead plumber for commercial/residential new construction, service and fire protection jobs. He holds a State of Ohio Fire Protection License for Sprinkler and Standpipe.
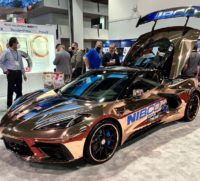
NIBCO’s Wrot Racer® C8 Corvette kicks off its tour at AHR Expo 2022 before visiting qualified distributors throughout the United States to celebrate the introduction of Wrot Racer push fittings. NIBCO INC. announces its Wrot Racer® “Start Me Up” promotion to celebrate its next generation of push fittings that it recently launched. The multi-faceted promotion centers on Read more
NIBCO’s Wrot Racer® C8 Corvette kicks off its tour at AHR Expo 2022 before visiting qualified distributors throughout the United States to celebrate the introduction of Wrot Racer push fittings.
NIBCO INC. announces its Wrot Racer® “Start Me Up” promotion to celebrate its next generation of push fittings that it recently launched. The multi-faceted promotion centers on the Wrot Racer C8 Corvette that will tour the U.S., making stops at distributor locations that have qualified.
The “Start Me Up” promotion provides a quick and easy way for distributors to take on immediate inventory of the new Wrot Racer copper push fittings. Distributors who meet the minimum stocking order requirement will receive a free marketing kit that includes POP merchandising.
NIBCO’s Wrot Racer Corvette began its tour at AHR Expo in Las Vegas on January 31, before moving to the West Coast, making various stops along the way, including Phoenix and Los Angeles. The “Start Me Up” promotion runs through 2022.
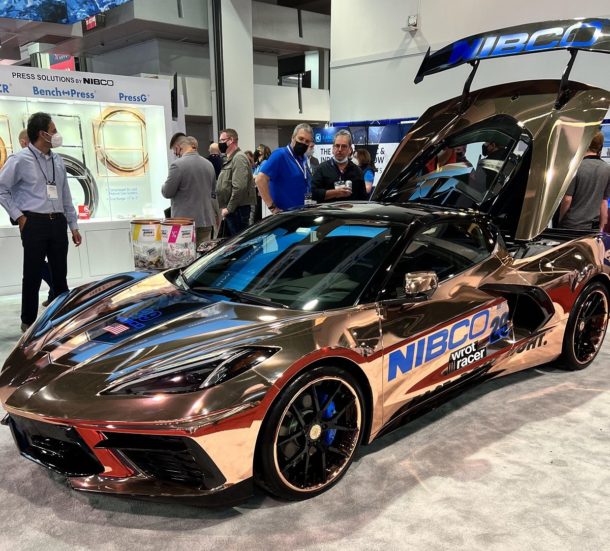
“We’re excited for our Wrot Racer Corvette to head out on the road to visit qualifying distributors across the U.S.,” said Ashley Martin, executive vice president, NIBCO INC. “This is a great opportunity for distributors to create additional coverage for their businesses and for everyone attending to have fun!”
Introduced in 2021, Wrot Racer push fittings are a line of premium copper push fittings that are engineered to join copper, CPVC-CTS, PEX and PE-RT (with stiffeners) for easy transition between piping systems. With a patented fitting design, installations are easily made within seconds.
Wrot Racer push fittings are made with 99.9 percent pure wrot copper. Naturally lead free, the fittings feature antimicrobial properties and are dezincification resistant, providing for safe, clean drinking water connections for both residential and commercial applications.
Available in 1/2″ to 1″ sizes, the lightweight and compact Wrot Racer fittings are able to be installed wet or dry and can handle applications up to 200 psi and 200 degrees. The new fittings feature stainless steel gripper rings to ensure a secure connection. Wrot Racer fittings are ideal for tight-space installations and can also be removed and reused, avoiding wasted materials.
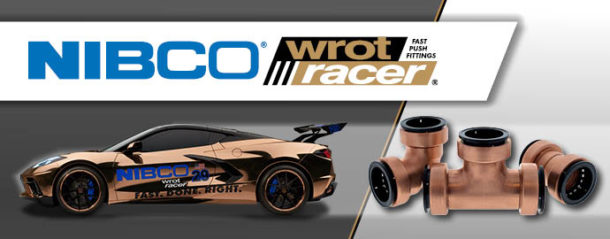
To learn more about how NIBCO’s Wrot Racer Corvette can make an appearance, contact your local NIBCO sales representative, visit nibco.com/wrotracer/ or email Customerservice@nibco.com. Contractors should contact their local distributor to see if it is on the Wrot Racer tour list.
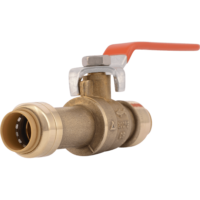
As the deep winter freeze arrives, frozen or burst pipes can become prevalent. Dealing with an unexpected leak is the last thing anyone wants to tackle in the middle of a busy season; but if it happens, there’s a quick solution to restoring ruptured pipes with no specialty tools, soldering, crimping or glue required: SharkBite push-to-connect Read more
As the deep winter freeze arrives, frozen or burst pipes can become prevalent. Dealing with an unexpected leak is the last thing anyone wants to tackle in the middle of a busy season; but if it happens, there’s a quick solution to restoring ruptured pipes with no specialty tools, soldering, crimping or glue required: SharkBite push-to-connect slip and transition fittings.
“SharkBite gives you a wide range of slip fittings and valves to repair burst copper or CPVC pipes quickly,” said Michael Kornegay, SharkBite Product Manager. “Up to two inches of damaged pipe can be removed using a single fitting, even in wet lines, and a drain valve can be easily added to prevent future freezing.”
Ideal for working with multiple pipe types and in tight spaces, SharkBite’s Brass Push transition fittings can be installed in wet lines and can transition between pipe types, including PEX, copper, CPVC, PVC, polybutylene, HDPE and PE-RT pipes, making them one of the most versatile solutions.
“SharkBite’s push-to-connect transition fittings come with color-coordinated collars for each specific pipe material,” Kornegay continued. “The tool-free transition fittings allow for quick and easy repair of copper pinhole leaks and replacement of brittle polybutylene pipe or broken CPVC.”
Since pipes are at a higher risk of freezing and bursting in the winter, it pays to have a solution like SharkBite’s push-to-connect slip and transition fittings handy for a quick fix. Follow these steps to get the job done fast:
- Cut the pipe cleanly – Be sure the pipe is clean of scratches or debris. If working with copper pipe, use a deburr tool or sandpaper to remove any sharp edges or burrs.
- Measure and mark the insertion depth – Use SharkBite’s Deburr & Gauge Tool to mark the insertion depth on the damaged pipe.
- Make the connection – Push the fitting to the insertion marks. Then, turn on the water and check the connection.
When it comes to repairing a burst, frozen pipe, SharkBite push-to-connect slip and transition fittings save time. Pipe transitions make working with PEX, copper, CPVC, PVC, polybutylene, HDPE and PE-RT pipes hassle free, and SharkBite offers the flexibility of repairing the damaged pipe in wet lines under full flow.
“Just cut, push and done,” Kornegay said. “These SharkBite products allow you to quickly repair those frozen, burst pipes in a short amount of time, so you can finish a job with ease and move on to the next.”
Learn more about SharkBite’s repair options at SharkBite.com.
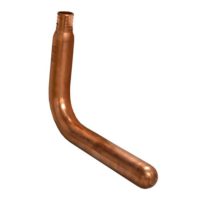
Jones Stephens, an industry leader in the manufacture and distribution of plumbing products, has launched a new line of Copper Stub Outs. Jones Stephens’ new Stub Outs line is a comprehensive assortment offering a broad range of product options sure to deliver the quality and reliability that installers expect on the job site. Essential for Read more
Jones Stephens, an industry leader in the manufacture and distribution of plumbing products, has launched a new line of Copper Stub Outs. Jones Stephens’ new Stub Outs line is a comprehensive assortment offering a broad range of product options sure to deliver the quality and reliability that installers expect on the job site.
Essential for any plumber, the new Stub Out product line provides a complete menu of sizes and styles that will support a job’s specific applications. Made with high quality, lead-free materials, Jones Stephens Stub Outs allow plumbers to install with confidence: each one carries the IAPMO approval and has a one-year Jones Stephens warranty.
The new line offers Stub Outs with both crimp and cold expansion designs for PEX connections with CPVC Socket connections arriving in Fall of 2020. The variety of styles include straights and elbows with and without mounting flanges and include closed end options for pressure testing. Additionally, the line includes Copper Tub/Shower Valve Connectors.
The new Stub Outs are available in a wide assortment of diameter and length sizes, ensuring that plumbers will find the exact dimension and configuration that they need to do the job.
To find out more information, visit www.jonesstephens.com.