Most Americans seek out – and spend more – at businesses with good bathrooms while canceling businesses with messy ones Businesses that fail to keep their restrooms clean and maintained are unwittingly flushing away customers’ repeat business and sales. According to the Healthy Handwashing Survey™ from Bradley Corporation, almost 60% of Americans make it a point to Read more
coronavirus
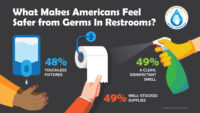
Most Americans seek out – and spend more – at businesses with good bathrooms while canceling businesses with messy ones
Businesses that fail to keep their restrooms clean and maintained are unwittingly flushing away customers’ repeat business and sales. According to the Healthy Handwashing Survey™ from Bradley Corporation, almost 60% of Americans make it a point to stop at a business and will spend more money at the establishment if they know it has clean and maintained restrooms.

In fact, those age 25-44 are even more likely to shell out more cash based on the condition of a business’ restroom.
Conversely, there are negative business repercussions for experiencing a restroom in poor condition. More than half of Americans say an unclean or unpleasant public bathroom shows poor management and causes them to lower their opinion of the overall establishment. The 55+ age group is especially turned off by unkempt restrooms with more than 60% reporting a damaged impression of the overall business.
Almost 20% say a sloppy restroom actually makes them less likely to clean up after themselves.
The business fallout of unpleasant restrooms
Perhaps most damaging for customer-facing businesses is that 52% say a bad restroom experience causes them to vow not to return in the future or think twice about doing so. Another 32% will either tell a friend or post a comment on social media about the negative encounter.
While there are a variety of restroom maintenance issues that may tarnish customers’ restroom experiences, the most common ones include clogged or unflushed toilets; an overall appearance that is old, dirty or unkempt; unpleasant smells; and empty or jammed dispensers for soap, toilet paper and hand towels.
“Restroom maintenance may seem like a business no brainer but limited budgets and facility staffing issues mean that companies are doing more with less staff and resources,” says Jon Dommisse, vice president of marketing and corporate communication, Bradley Corporation. “Nevertheless, customers place a high value on clean restrooms – and reward businesses that offer them. It’s incumbent upon facility managers to prioritize regular restroom cleaning and make sure that everything is in good working order.”

Understanding the aversion to touching restroom surfaces
“In 2023, Americans continue to be in an elevated state of germ consciousness and don’t like touching things in shared public restroom spaces,” adds Dommisse. “As a result, people use all sorts of techniques to avoid coming into contact with surfaces.”
62% use a paper towel to avoid touching toilet flushers and faucet and door handles. 43% operate the flusher with their foot. 31% hover over the toilet seat and 27% open and close doors with their behind to eliminate contact. Women are considerably more likely than men to use these evasive actions.
With so many people deliberately avoiding contact with restroom surfaces, it’s not surprising that 82% believe it is important to have touchless fixtures in a public restroom. Another 60% are more likely to return to a business that offers touch-free technology like faucets, flushers, soap and towel dispensers in its restrooms.
“When asked what restroom improvements they’d like to see, cleanliness topped the list,” Dommisse said. “After that, Americans want touchless fixtures and better stocking of supplies, such as toilet paper, soap and paper towels.”

The annual Healthy Handwashing Survey from Bradley Corp. queried 1,025 American adults Jan. 4-10, 2023, about their handwashing habits, concerns about the coronavirus and flu and their use of public restrooms. Participants were from around the country and were fairly evenly split between men (45%) and women (55%).
For more information, visit www.bradleycorp.com/handwashing.
Companies and building managers can access free resources at the Code Council’s Coronavirus Response Center. Washington, D.C. – As local and state governments are beginning a phased reopening of their economies, the International Code Council has compiled a guide of safety precautions and considerations for businesses looking to resume in-office activities. Acting as an aggregate Read more
Companies and building managers can access free resources at the Code Council’s Coronavirus Response Center.
Washington, D.C. – As local and state governments are beginning a phased reopening of their economies, the International Code Council has compiled a guide of safety precautions and considerations for businesses looking to resume in-office activities. Acting as an aggregate information hub, the Code Council’s Coronavirus Response Center offers relevant information for building professionals and potential occupants to understand the impact the pandemic has had on the industry, as well as for companies who are currently creating plans and strategies to move back into their offices.
Ahead of reopening efforts, the Code Council has made it a priority to educate businesses, office managers and building safety professionals on an important but often-overlooked safety precaution – preparing an office building for re-occupancy. With many buildings reducing or turning off normal system operations during stay-at-home orders, it is critical to properly inspect and prepare a vacant building ahead of resuming regular activities. Without proper preparation and maintenance, the building may pose unrealized hazards to incoming occupants, whether from a heating, ventilation, and air conditioning (HVAC) or plumbing system to a powerless carbon monoxide detector.
Due to the wide range of aspects necessary for reopening a previously unoccupied building, the Code Council’s Coronavirus Response Center covers topics include:
- Addressing any temporary changes needed to building access and exit patterns to accommodate temporary reopening protocols such as employee health screenings, disposal of PPE, or any areas specifically designated for decontamination.
- Visually inspecting and testing the operation of building entrances and exits including doors, revolving doors, and garage doors for proper operation and ensure they are free from obstructions.
- If a building’s water distribution system has been shut down or seen reduced flow, flushing the pipe system with clean, potable water to remove any unwanted debris.
- Facilitating adequate physical distancing protocols, and considerations for revising maximum occupant loads for all buildings and spaces to accommodate 75 gross SF/occupant.
- Closing common areas where personnel are likely to congregate and interact or enforcing strict physical distancing protocols.
- Guidance on disinfecting communal areas from FEMA and the CDC
“COVID-19 has had an unprecedented impact on our society, both economically and socially. As we continue to learn to navigate the new normal and discover what that actually entails, having easy access to information on topics like how to properly prepare a vacant building for reoccupation is crucial, especially during reopening efforts,” said Dominic Sims, CBO and CEO, International Code Council.
Access to the Code Council’s Coronavirus Response Center can be found here, while the full list of tips and considerations for reopening buildings can be found here.
The COVID-19 pandemic is causing commercial buildings such as day care facilities, hotels, schools and health clubs to remain closed for abnormally long periods. When the coast is clear to begin reopening, ensuring safe and sanitary plumbing water will be of utmost importance. Plumbing systems left idle can be susceptible to harmful bacteria such as Read more
The COVID-19 pandemic is causing commercial buildings such as day care facilities, hotels, schools and health clubs to remain closed for abnormally long periods. When the coast is clear to begin reopening, ensuring safe and sanitary plumbing water will be of utmost importance. Plumbing systems left idle can be susceptible to harmful bacteria such as Legionella which can proliferate to dangerous concentrations.
Experienced water maintenance managers know susceptible systems should be flushed before reusing. Important considerations should not be overlooked such as ensuring all service lines are purged and dead legs drained.
Several factors determine if the system equipment requires treatment such as how long a system is left idle, the temperature of the stagnated water and condition of the internal surfaces. This is so bacteria that are resistant to simple purging/draining and have become resident in biofilm can be addressed. Common methods include thermal treatment or treating with chemicals such as chlorine, chlorinated gas and chlorine dioxide.
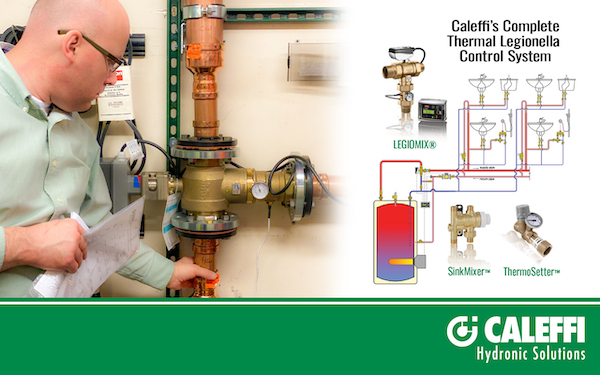
A significant benefit of thermal treatment is that it’s a proven, cost-effective method for bacteria management on an ongoing basis in the hot side of the plumbing system. The cold side doesn’t typically require ongoing treatment unless water remains stagnated for extended periods within the temperature range that Legionella grows which is 68°F to 122°F.
Thermal treatment requires little additional maintenance compared to chemical treatment. Also, common plumbing equipment such as seals, gaskets and polymer components are not exposed to potentially incompatible life-shortening chemicals.
Residual chemicals in the water can also be a human health concern if acceptable concentration values are exceeded. In contrast, most common plumbing materials can withstand, without effect, thermal shock temperatures such as 160°F.
Thermal treatment consists of periodically circulating elevated water temperature such as 160°F through the entire system for a specific and measured period of time, thereby killing harmful bacteria and restoring the water to a safe and usable condition. During this period it is important to ensure all point-of-use fixtures are either disabled for access or equipped with anti-scald devices. An example is the Caleffi scald-protection valve SinkMixerTM — an innovative, easy to install valve for under-sink applications.
Often the most difficult portions of the hot water side to circulate sufficiently through is the recirculation return risers. This because they are sized and balanced to a relatively low flow rate such as 0.5 GPM. The Caleffi ThermoSetterTM thermal balancing valve automatically responds when it senses high temperature water by fully opening an internal by-pass, thereby allowing a sufficient return riser flushing during treatment. It then automatically returns to standard operation state when water temperature decreases to normal.
If a building is equipped with a Caleffi LEGIOMIX digital mixing valve, it will enjoy highly accurate mixed water temperature 24/7. The LEGIOMIX has industry-unique, calendar- based automatic thermal disinfection programs. For thermal monitoring, it has data logging capabilities and can connect to a building automation system for remote monitoring and access.
LEGIOMIX combined with SinkMixer anti-scald valves and ThermoSetter recirculation balancing valves offer an innovative total thermal solution for control of safe and sanitary domestic hot water.
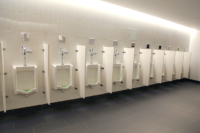
Ron George, CPD Below is a recommended flushing procedure for building owners, property managers, water utilities, health officials, code officials, service contractors, engineers, insurance companies and Interested parties to perform on buildings before re-opening buildings for occupancy after a long shut-down. With the recent coronavirus events causing many stay-at-home orders and extended vacancy of offices Read more
Ron George, CPD
Below is a recommended flushing procedure for building owners, property managers, water utilities, health officials, code officials, service contractors, engineers, insurance companies and Interested parties to perform on buildings before re-opening buildings for occupancy after a long shut-down.
With the recent coronavirus events causing many stay-at-home orders and extended vacancy of offices and workplaces, there is a looming, serious issue associated with stagnant water or aging water in the plumbing tanks, fixtures and pipes of buildings that have not been occupied for long periods of time. Bacteria will grow and flourish in the biofilm of the plumbing tanks, fixtures and pipes that have been sitting stagnant with ambient temperature or warm water where the water treatment chemicals have dissipated to levels that will not control bacterial growth. Studies have shown water treatment chemicals dissipate over time and there are several factors that affect the rate of dissipation such as pipe material, temperature, and organic contaminants in the water.
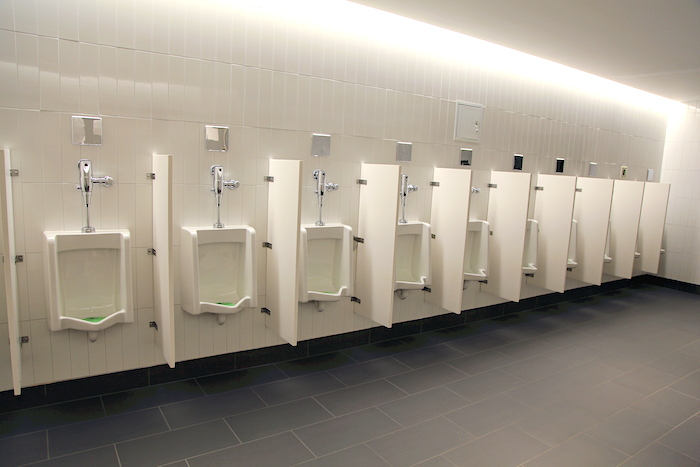
After the chlorine dissipates, bacteria can grow to high numbers. When bacteria and microorganisms are aerosolized in water from showers and other fixtures that can aerosolize the water it can be inhaled into the lungs causing Legionellosis or Legionnaires’ disease. Therefore, it is important to flush these stagnant pipes of bacteria laden water before re-occupying the buildings that have been vacant for long periods of time. I have been involved in developing Legionella standards & guidelines with ASHRAE and ASSE and I have spent over 42 years designing plumbing systems to simultaneously prevent scalding and Legionnaires disease. There are standards for flushing and disinfecting large public water mains but, there is no consensus standard for flushing and disinfecting plumbing systems within buildings.
In early 2020, government officials issued stay at home orders, with guidance from health officials, which has caused many buildings to sit abandoned with little to no water usage for weeks or months. When a building has been empty or unoccupied for an extended period, bacteria like Legionella and various other bacteria, viruses or disease-causing organisms can be found in inadequately treated water or stagnant water after the water treatment chemicals dissipate.
Before re-occupying a building that has been unoccupied for an extended period, it is recommended to flush stagnant water from the piping system before opening the building to occupants. To minimize to chances of transmission of Legionella bacteria and other microorganisms to humans, flushing water from the plumbing fixtures is the easiest, quickest and cheapest way to prepare for occupants to return to the building.
I am encouraging government officials, health officials, water utilities, code officials and other non-profits to implement these simple and inexpensive flushing procedures into national, state and local ordinances or guidelines to help protect the occupants of buildings from bacteria laden water upon return to buildings that have been sitting idle for long periods of time. These entities should use the language in this document and create a local flushing and disinfection ordinance for documentation of flushing procedures before opening and occupying buildings that have been idle for long periods of time. The government entity can decide what length of shut-down justifies flushing based on chlorine or other water treatment dissipation rates in your area. If a building has been idle for more than four weeks, a Legionella test should be conducted on first draw water before flushing to determine if a chemical disinfection procedure is needed to be performed. Chemical disinfection should be performed on the hot water system before heating the water.
Domestic Water Systems Flushing Procedure:
Building Address: ________________________________________ Flushing Date: ______________
Name of Persons Conducting the flush 0peration:_______________________________________________________________________ _______________________________________________________________________
For documenting the flushing operations, follow the tasks outlined below. Building owners or maintenance staff should be advised to perform these flushing operations in all buildings that have been closed for an extended period. This will reduce the risk of illness and death following a building that has been unoccupied for a long period. The objective is to replace all stagnant water in the potable water system with new water containing a disinfectant residual from the municipal distribution system.
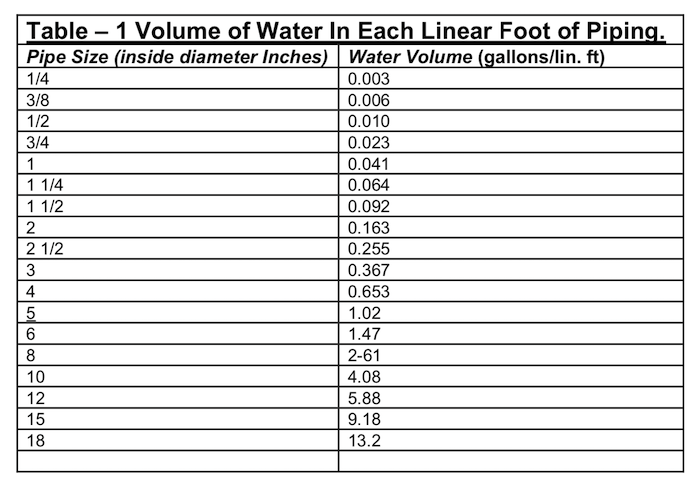
Flushing personnel should wear an “N-95 respirator mask” and Personal Protective Equipment during flushing operations. When performing a flushing operation, complete the following flushing procedure in the following sequence:
1. Collect a water sample of first draw water for testing the water treatment chemical residuals in the building service pipe. Collect the sample from a monitoring point in the service pipe at or near the meter and backflow preventer or where the service pipe enters the building.
Note the Water utilities water treatment chemical type. This pre-flush test should be serve as a baseline to compare pre-flush water quality with post flush water quality.
Locaton ______________________; Free Chlorine Residual: _____ppm; Test By: ______; Time: ______ am/pm
Location ______________________; Legionella Test1: _________ cfu/ml; Test By: ______; Time: ______ am/pm
(Note 1. – Conduct a Legionella test if the building has been significantly unoccupied for more than 14 days.)
If the pre-flush water quality test indicates any water discoloration, odor or other unusual characteristics note them below:
Notes:_________________________________________________________________________________________________
2. Collect a water sample from first draw water of at least five (5) remote locations within the building to determine the building water chemical residuals in the building. These locations should be documented for to serve as a baseline pre-flush to post flush to compare pre-flush water quality with post flush water quality.
Loc. #1 ______________________; Free Chlorine Residual: _____ppm; Test By: ______; Time: ______ am/pm
Loc. #1 ______________________; Legionella Test1: _________ cfu/ml; Test By: ______; Time: ______ am/pm
Loc. #2 ______________________; Free Chlorine Residual: _____ppm; Test By: ______; Time: ______ am/pm
Loc. #2 ______________________; Legionella Test1: _________ cfu/ml; Test By: ______; Time: ______ am/pm
Loc. #3 ______________________; Free Chlorine Residual: _____ppm; Test By: ______; Time: ______ am/pm
Loc. #3 ______________________; Legionella Test1: _________ cfu/ml; Test By: ______; Time: ______ am/pm
Loc. #4 ______________________; Free Chlorine Residual: _____ppm; Test By: ______; Time: ______ am/pm
Loc. #4 ______________________; Legionella Test1: _________ cfu/ml; Test By: ______; Time: ______ am/pm
Loc. #5 ______________________; Free Chlorine Residual: _____ppm; Test By: ______; Time: ______ am/pm
Loc. #5 ______________________; Legionella Test1: _________ cfu/ml; Test By: ______; Time: ______ am/pm
If the pre-flush water quality test indicates any water discoloration, odor or other unusual characteristics note them below:
Sampling Notes: __________________________________________________________________________________________________________________________________________________________________________________________________
(Note 1. – Conduct a Legionella test if the building has been significantly unoccupied for more than 14 days.)
3. Determine the building service pipe size and length. Service pipe size: _________ , Volume gallons per Linear foot Service pipe length: _________
4. Determine the volume in the building service pipe based upon its size and length in Table 1 below and multiply the volume by 2 for the required volume to be flushed from the service piping.
Service pipe volume from Table 1: _________ (Linear feet of service pipe x volume per foot from #3 above)
Service pipe volume from Table 1 x 2 = _________ Note 2
Note 2 – Volume of water to be flushed through the service pipe at 3 feet per second velocity per Table 2.
5. Determine and document the quantity and location of the fixtures required to be flowed simultaneously to have a velocity of 3 feet per second in the service pipe. (See table X) and hose valves will be flowing from the required number of flushing points in order to have a flushing velocity high enough to scour bio-film and sediment from the service pipe at a flow velocity in excess of 3 feet per second as determined in table 2.
6. Perform and document a pre-flush water quality test at the water service entrance and at 5 remote fixtures to determine water quality and water treatment residual, There should be a minimum 1 part per million (ppm) free chlorine at the building service entrance and 0.5ppm of free chlorine at the most remote fixture. For buildings with other water treatment chemicals in the utility water, consult with a professional for recommended minimum water treatment chemical levels or as directed by the facilities’ water management program team) entering the building. If the test shows the water quality is good, then no service pipe flushing is needed.
7. If the pre-flush water quality test indicates any water discoloration, odor or lack of sufficient free chlorine residual, perform and document a full velocity flush of 3 feet per second for the building water service pipe as follows:
a) Determining the proper number of fixtures to flow to flush the building service pipe at a minimum velocity of 3 feet per second, based on the size of the building service pipe size, (See table 2)b) The flow can be through a combination of fixtures can be flowed through a combination of hose bibbs, hydrants and fixtures near the water service entrance. and test the potable water service connection until a disinfectant residual is detected or a volume equivalent to double the water held in the service connection is cleared, whichever occurs first.
8. If a disinfection residual is not detected, after 30 minutes of flushing the building service pipe, Stop flushing and do not continue with the potable water system flushing operation. Contact the water utility for direction and ask to have them or the fire department flush the water mains through nearby fire hydrants to bring chlorinated water close to the building. If the building is in a cluster of buildings or area with many unoccupied buildings ther may be a logical place to flush a hydrant near the end of the water main.
9. When a disinfectant residual is detected on the building service pipe, open some faucets that are the farthest away from the building water service and on the end of each major branch main of the water distribution piping and let the hot and cold water run continuously until a disinfectant concentration is detected close to or equal to that of the chlorine residuals in the building service connection. A branch main is defined as a main distribution pipe (typically greater than 3⁄4” diameter) which supplies other branch pipes and fixture branch pipes.
10. Flush all remaining fixtures, tanks, and appliances connected to the potable water system (including exterior outlets). Flow water from both the hot and cold water systems. The following flushing procedure should be used based on each fixture type:
- Toilets and urinals shall be flushed 5 times each for 1.6 gpf fixtures.
- All other fixtures shall be flushed for a minimum of 3 minutes each, both hot and cold water with flows of 2 gpm.
- Any water storage or hot water tanks should be flushed at a rate to flow at least 2 times the volume of the tank.
- Hydro-pneumatic and thermal expansion tanks should have the water pressure relieved from them so that they totally discharge all water within the tank.
Infra-red faucets shall be operated for a consecutive period of time equal to 20 cycles for every 10 feet of 3⁄4 inch branch piping.11. The person performing the flushing operation should record the room number, the fixture type & ID, flow rate in gpm, start time and temperature, end time & temperature, chlorine residual near end of flushing operation, and notes or observations for each fixture like: ambient temperature of the room, when the water temperature starts to change indicating fresh water is arriving at fixture, chlorine residuals in the first draw and at completion. thereafter until a minimum chlorine residual of 0.5 ppm is achieved at each fixture. Take a water sample in the first draw and upon completion of the flushing and Note any water discoloration, odor, etc) for first draw and test the chlorine residual in the final draw at the completion of the flushing operation. If the measured chemical residual is insufficient to control bacteria growth, perform and record the flushing operation as shown on the following “Fixture Flushing Record Sheet.”
12. The water utility has a duty to deliver safe drinking water to the building service meter according to the safe drinking water act. Note: the utilities are allowed fall below the level of quality in the safe drinking water act for three, consecutive 6-month reporting periods before they must notify the public. The responsibility for building water safety is the responsibility of the building owner. The drinking water provider has no responsibility for water quality on the building side of the water meter. A water utility should strive to deliver quality water, but we know that the water utilities cannot guarantee safe drinking water because there are often water main breaks, construction, fire events and other disruptions of water main flows that cause turbid water and high bacteria events. For this reason, the building owner has a duty and responsibility to monitor the water quality coming into their building and have a water management plan in place to address water quality issues. In this day of water conservation, water flows have been reduced to levels that are less than 20 percent of flows prior to 1992. The flow in water mains have been reduced to the point where water treatment chemical residuals dissipate to levels that will not control bacteria growth in the water mains. Building owners must monitor the incoming water and adjust the water quality if needed by using supplementary water treatment systems. When a building owner is considering a supplementary treatment system, they should consult with a professional to determine if they need licensing, certification and any filters.
13. When a building is unoccupied for more than 7 days or a period of time agreed to by the building’s water management Program team, flushing should be performed immediately prior to re-occupancy. When a building is unoccupied for more than four weeks (28 days), or a period of time agreed to by the building’s water management Program team, flushing and disinfection should be done immediately prior to the building being reoccupied.
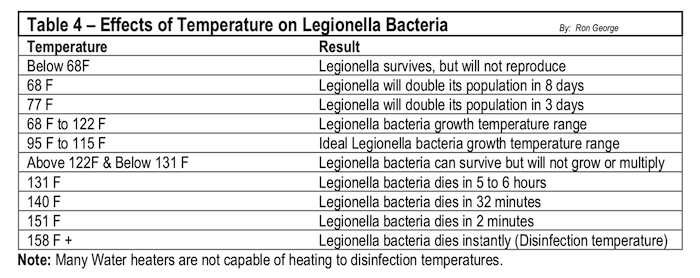
Note: Flush all sinks first, then flush showers, then flush water closets & urinals. Fixtures with flush valves can become clogged with debris and not flush properly if they are flushed first. If flush valves do not perform properly and run-on, shut off water and remove diaphragm and clean the orifice. When done flushing, remove faucet strainers and shower heads and clean or replace them.
Storage Water heaters should be maintained at a minimum temperature of 140F or higher in the tank as needed to offset heat loss and maintain a minimum hot water temperature at the lowest temperature in the system a couple of degrees above the Legionella Growth temperature of 122 F. (124 F) on the hot water return pipe connection to the water heater. The hot water return pipe just before the cold water connection to the water heater is the lowest temperature point in the hot water system. See the “Temperature Effects on Legionella Bacteria Table” Below. To prevent Sclading, all shower valve maximum temperature limit-stops should be adjusted to a maximum temperature of 115 F at showers & bathtubs to prevent scalding. (Consider a maximum temperature limit stop setting for showers and tub/showers of 110 F at hospitals, nursing homes and similar facilities where there is additional risk of scalding.)
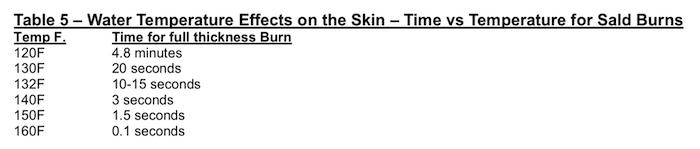
Hot water temperatures can be higher in the storage and distribution piping and should be reduced or limited at or near the fixtures by code compliant temperature limit-stops that are properly adjusted on tub/shower valves or by temperature limiting valves that are properly set to limit temperatures at the point of use.
Every fixture in the building should be flushed in accordance with these guidelines or until the water treatment chemical residuals reach an acceptable level. Following these procedures should prevent thousands of workers from getting sick and dying from Legionnaires disease and other types of waterborne illnesses associated with stagnant water.
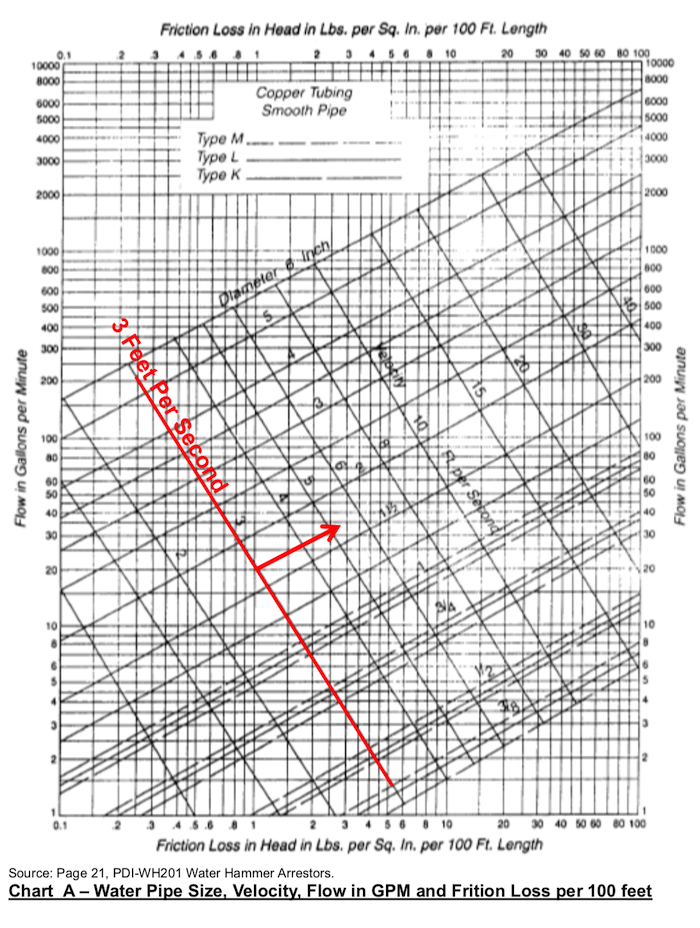
Indianapolis—Williams Comfort Air, a leading provider of heating, cooling and plumbing services, is providing free delivery of grocery pick up orders to healthcare professionals working with COVID-19 patients and people considered to be at high risk for severe illness from the coronavirus. The company, which operates Williams Comfort Air and Mr. Plumber in Indiana, Thomas Read more
Indianapolis—Williams Comfort Air, a leading provider of heating, cooling and plumbing services, is providing free delivery of grocery pick up orders to healthcare professionals working with COVID-19 patients and people considered to be at high risk for severe illness from the coronavirus. The company, which operates Williams Comfort Air and Mr. Plumber in Indiana, Thomas Galbraith Heating, Cooling and Plumbing in Ohio, and Jarboe’s Plumbing, Heating and Cooling in Kentucky, is converting its preventative maintenance teams into grocery delivery drivers – picking up and dropping off online grocery orders made through Kroger, Meijer, Walmart, Target and Market District.
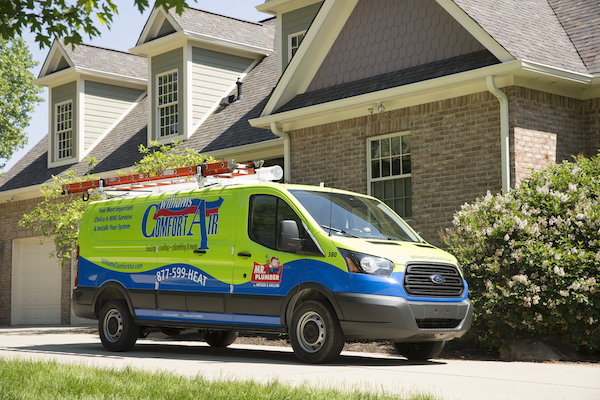
“Our services are considered to be essential, and many of them – like HVAC and plumbing repairs and replacements – absolutely are,” said Jacob Huck, president of Williams Comfort Air. “But we don’t need to be completing preventive maintenance work right now. Still, we wanted our field teams to be getting 35-40 hours of work per week, so we came up with a meaningful, new way to serve the people in our community. We’re proud to offer free delivery of grocery pick up orders to those who need it right now, while still keeping employee and client safety top-of-mind.”
Free delivery of grocery pick-up orders is available now. Company leaders say they’ll continue to provide deliveries throughout the stay-at-home orders.
“As a company, we talked about how thankful we were for people on the front-lines of the pandemic, and discussed how we could help in an authentic, human way,” said Matt Tyner, Williams Comfort Air director of marketing. “Offering free grocery delivery was a way we could give thanks to people treating those who have the virus, help protect those most vulnerable to the virus and prioritize the health and livelihood of our own employees at the same time.”
To receive a grocery delivery from Williams Comfort Air, qualified individuals can place online orders scheduled for pickup between 8 – 5 p.m. EST, Monday through Friday, then call the client care team in their area to confirm the delivery.
- Williams Comfort Air (Indiana) customers can call 317-663-9125.
- Thomas Galbraith Heating, Cooling and Plumbing (Ohio) customers can call 513-342-0460
- Jarboe’s Plumbing, Heating and Cooling (Kentucky) customers can call 502-442-7500.
For more information about Williams Comfort Air, visit https://williamscomfortair.com/.