Great for a wide range of heavy-duty plumbing, drain cleaning, maintenance, and rental applications, the Typhoon® trailer jet from General Pipe Cleaners blows away blockages in big lines and long runs. The Typhoon delivers 12 gallons a minute at 2500 psi to blast grease, sediment and debris from 4” to 12” drain lines up to 400 Read more
drain cleaning
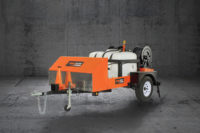
Great for a wide range of heavy-duty plumbing, drain cleaning, maintenance, and rental applications, the Typhoon® trailer jet from General Pipe Cleaners blows away blockages in big lines and long runs.
The Typhoon delivers 12 gallons a minute at 2500 psi to blast grease, sediment and debris from 4” to 12” drain lines up to 400 ft. long. And a 200 gallon holding tank carries enough water to handle remote locations where access to water is limited.
General’s brawny machine also boasts electric brakes, safety strobe light, safety cones, rear fold-down stabilizer jacks, retractable hose guide arm, and antifreeze system as standard equipment.
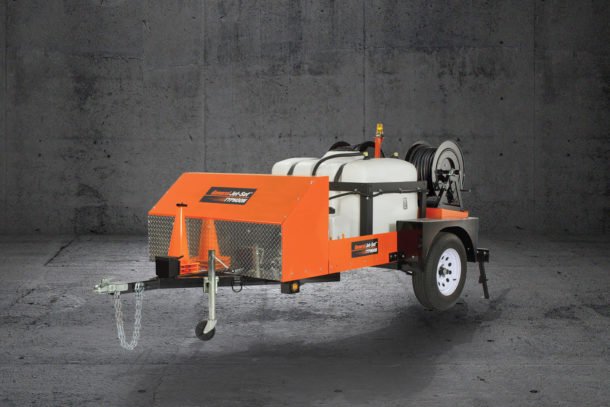
Its reliable 690 cc (24 hp) Honda engine with electric start and 7 gallon fuel tank ensures extended performance on stubborn stoppages. On-demand Vibra-pulse® helps slide the nozzle around tight bends – and propel the hose down long lines.
Two hose reels – a jet hose reel with 400 ft. x 1/2″ capacity featuring variable speed electric rewind, and a water supply hose reel carrying 150 ft. x 3/4″ hose – are mounted at the rear of the unit next to the pressure gauge and output valve. Engine controls, including an hour meter, are located within easy reach in the lockable tool box with slide action doors just below the reels.
General’s Typhoon trailer jet rides on rugged 15″ radial tires with modular wheels and a leaf-spring suspension rated at 3500 lbs per axle. A splash guard at the front helps protect the pump and engine from road debris. And the body is protected by a tough epoxy finish for added weather protection. The Typhoon is also available in a skid mount model.
To see the Typhoon trailer jet in action, visit drainbrain.com/en/products/jm-2512/. For more information, contact the Drain Brains® at General Pipe Cleaners at 800-245-6200 or 412-771-6300.
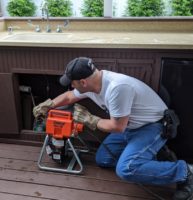
With the versitlity to handle 1-1/4” to 4” drain lines, General Pipe Cleaners’ Root 66® is three machines in one. Designed to clear practically any inside or rooftop drain, the Root 66 sectional cable power drain cleaner uses 5/8″ or 7/8″ sections interchangeably. There’s no need for adapters or tools to switch from one cable Read more
With the versitlity to handle 1-1/4” to 4” drain lines, General Pipe Cleaners’ Root 66® is three machines in one.
Designed to clear practically any inside or rooftop drain, the Root 66 sectional cable power drain cleaner uses 5/8″ or 7/8″ sections interchangeably. There’s no need for adapters or tools to switch from one cable size to the other!
Need to clear sinks and other small drain lines? Get the optional drum with smaller 1/4″, 5/16” or 3/8” Flexicore® cables. Just slide onto the back of Root 66 and you’re ready to go.
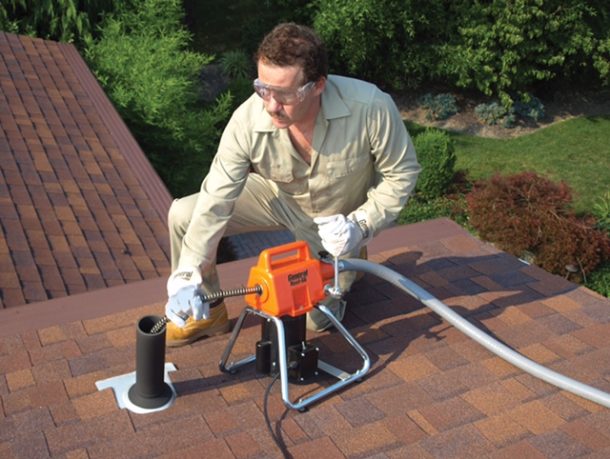
A General exclusive, optional 7/8″ Proflex® sectional cables (15R10-P) sport an inner spring. It gives the cable greater strength to transfer extra torque down the line for additional cutting power.
Operating Root 66 is easy, too. Depress the drive handle for plenty of cable torque from the 1/2 hp capacitor motor. Release the drive handle and the cable immediately stops rotating – for no additional torque build-up. A wide, four-point base adds greater stability, and an optional dolly offers easy transport over long distances.
Other accessories include cable carriers, the optional drum for small drain work, and a toolbox. Standard equipment includes a ground fault circuit interrupter, double palm leather gloves, rear guide hose, and General’s tradition of quality, performance and reliability.
For more information contact the Drain Brains® at General Pipe Cleaners at 800-245-6200 or 412-771-6300, or visit drainbrain.com.
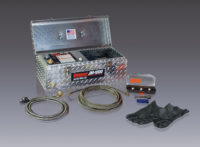
General Pipe Cleaners has enhanced the performance and cleaning power of its popular JM-1000 Mini-Jet™ with stainless steel braid hoses – a new supply hose and optional jetter hoses. The upgraded supply hose now sports a durable, 10’ x 3/8” stainless steel braid design with a compression fitting for attachment directly to angle stops beneath Read more
General Pipe Cleaners has enhanced the performance and cleaning power of its popular JM-1000 Mini-Jet™ with stainless steel braid hoses – a new supply hose and optional jetter hoses.
The upgraded supply hose now sports a durable, 10’ x 3/8” stainless steel braid design with a compression fitting for attachment directly to angle stops beneath sinks.
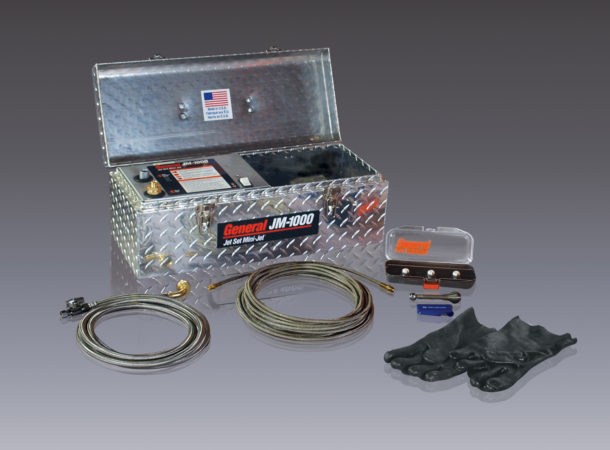
The optional abrasion-resistant, stainless steel braid jetter hoses smoothly traverse 1-1/2” to 3” drain lines – and easily navigate tight bends. Available in 30’ and 50’ lengths, the 3/16” Teflon® core also reduces water flow resistance, improving small-line cleaning power.
The lightweight JM-1000 Mini-Jet clears grease, sand, and ice from small lines, sinks, and laundry drains with high-pressure, wall-to-wall water spray. The compact, powerful unit clears clogs with 1500 psi of cleaning power, yet weighs just 23 lbs. The pump and motor assembly are safely contained in a rugged diamond plate metal case.
See the Mini-Jet in action at www.drainbrain.com/jm1000, or contact the Drain Brains® at General at 800-245-6200 for more information.
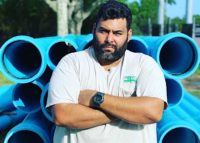
When I asked Conrado Ensenat Jr.—aka @conradtheplumber—if he ever considered himself a role model to young people thinking of entering the trades, he unequivocally answered, “No, absolutely not.” Yet his answer wasn’t completely without, perhaps, an internal epiphany. You see, according to Conrad, the way he does things may not be the way others do Read more
When I asked Conrado Ensenat Jr.—aka @conradtheplumber—if he ever considered himself a role model to young people thinking of entering the trades, he unequivocally answered, “No, absolutely not.” Yet his answer wasn’t completely without, perhaps, an internal epiphany. You see, according to Conrad, the way he does things may not be the way others do things. And that’s okay. But in reality, unbeknownst to Conrad, he may just be moving into that role model role as we speak. “What I am is a plumber that has no problem taking the time to answer any kind of question an apprentice or a student in school may have about our trade,” says Ensenat. “I believe we are more approachable today more than ever; communication is so much easier with social media. So, for me, a role model I am not. But a plumber with the love for the trade and wanting to see young people succeed if they want to pursue a career, then I most certainly am.”
His Calling
Early on, Conrad was working for a restaurant and just starting at a local community college, yet he wanted something more. Working with his hands always appealed to Conrad so he quit the restaurant and started working as a carpenter’s helper. “It was okay, but saw what the plumbers were doing with the soldering and PVC, and I was intrigued,” Conrad says.
Conrad was hired as a helper cutting and removing cast iron pipe in a building in downtown Miami and loved it right away. “Sure, I was dirty and smelled bad but learning about the pipe and how it works was just really cool. Seventeen years later and I’ve never looked back; plumbing was my calling.”
Conrad’s journey into the plumbing trades technically began full time in 2002 where he started on “snake patrol,” as he was given a van full of all types of machines for drain cleaning—RIDGID, Electric Eel, General Pipe Cleaner, etc. “I learned quickly how to use these machines—I got slapped in the face by a cable, had my shoelaces ripped off after the cable got tangled on them and got splashed with sewer and grease—and all of this happened within my first two days.”
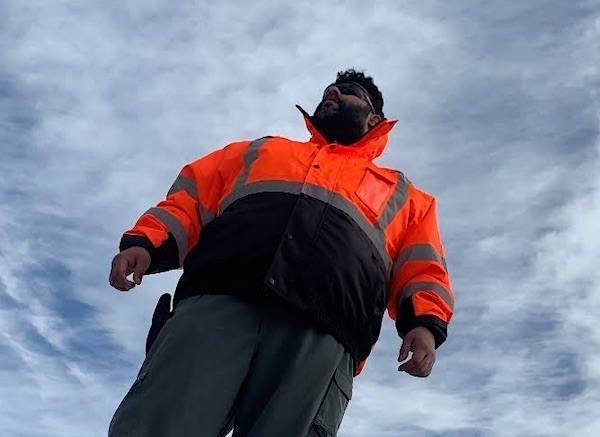
After one year, Conrad begged his boss for an upgrade and was moved over to camera inspections. Here, Conrad learned the insurance side of things for residential and commercial applications—how it all works and the importance of video and the location of problems. At this time, Conrad also was installing temporary sinks and water heaters, and doing leak detection as well. After about six months, Conrad went into new construction, completing multiple high-end buildings and renovations in multiple hotels. After about a year, Conrad took over as lead plumber on two high-end homes in Sunset Island and Hibiscus Island, Miami Beach. “One project took seven years to complete while the other took four, and that meant a lot of money and a lot of change orders,” says Ensenat.
At this time, Conrad bounced from lead plumber to supervisor—in charge of about 17 plumbers and 10 helpers—ordering material, pricing out jobs, and meeting with contractors and owners. “I didn’t carry a tool or do any labor for about four years; it was mostly delegating and office work. It was a bit boring at times and the days were long and sometimes stressful, but you go on,” says Ensenat.
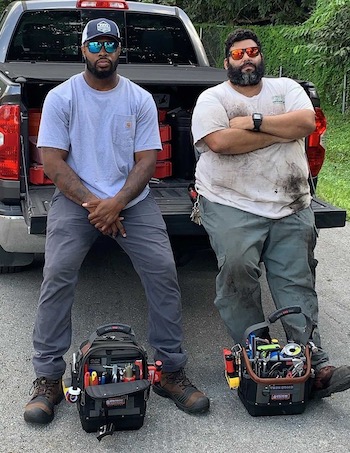
Conrad with Omar Harris (left).
After the company closed its doors and went into new ownership, Conrad decided it was time to go on his own. He opened a company with a partner and ran it for four years.
“I tip my hat to all the business owners, but there’s another side to that coin. The long days and nights—being held accountable for what your plumbers and helpers do, calling contractors for payment, supply houses, bills, gas, insurance, marketing, etc. It was great for a while but I was working a lot, and when you’re on your own, you want every call and every job as the stress of business falls on you. You need to bring in the money for your plumbers and office staff. They depend on you.”
But in the end, family was most important to Conrad. There was a time Conrad was working 6-7 day a week, 15-20 hours per day. “So, I closed shop and went and worked for a commission company, which was not the best decision, but I did see another side of plumbing I hadn’t seen, which I am not too fond of. But I did meet my best friend Omar Harris there, and met some great plumbers like Hiram Martinez and Joey Neal. These are great guys with vast knowledge of the trade.”
After leaving that company, Conrad joined the Broward County Parks and Recreation Division, where he has been for the past three years. “I couldn’t have made a better choice for me and my family.”
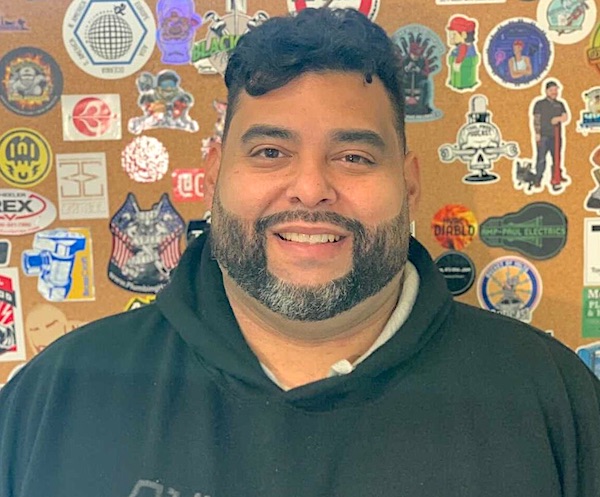
Looking back to when he started, Conrad says he didn’t know what he was doing but always enjoyed learning. And, as he was putting systems together and turning on/off the water, gas, or testing a drainage system, there was a sense of accomplishment. “We all have that story where we figured out a leak when five other plumbing companies could not. Where we worked all night, were dead tired, and when they asked, you said ‘you had to be there.’ The journey is different but the end result is the same,” says Ensenat. “The customer is coming to you with a problem and needs you to solve it. Putting that trust in you is a great feeling and honor; they could’ve picked anyone but they picked you.”
Learning from the Past
Conrad owes a lot of what he knows in the trades to William Gonzalez. “That man taught me a lot and would become my future father-in-law. He was an old-school plumber since the ’70s and he did not take it easy on me—probably because I was dating his daughter, lol. But he showed the business side of plumbing. He pushed me in new directions and always challenged me, whether it was reading plans delegating or a simple stoppage. His passion became my passion and my drive to learn all new methods of plumbing. I will be forever grateful to him, leaving me with the knowledge to make it in this trade; he may be gone, but never forgotten.”
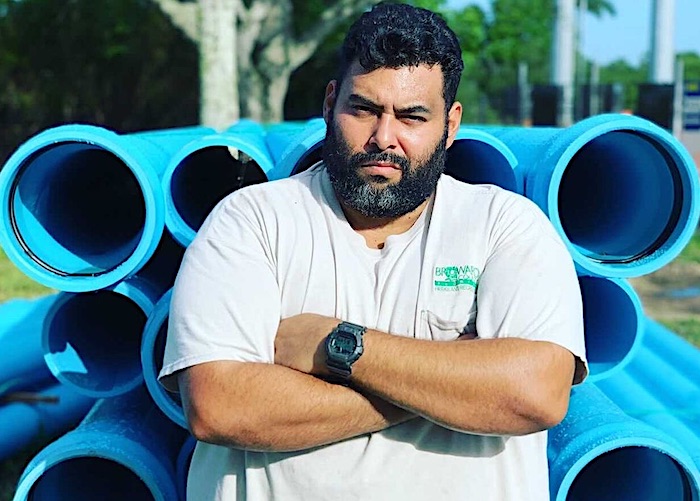
Conrad’s brother-in-law, Guillermo Gonzalez, also taught him a lot about gas, and working with tankless water heaters. “Like his dad, he is a great person, and I was very lucky to be welcomed into the family—not only have they shown me love but they showed me a trade and a skill that will never be taken away. I have taken what they taught me and I have taught others as well,” says Ensenat.
Social Media All-In
According to Conrad, social media has been a great tool from talking to people all over the world to seeing the different methods of plumbing that are used—from the equipment to the way others approach the work. “We are a community here to help each other answer questions: we are at a time with social media where you can ask a question to a professional and get a real answer from the people that do it and live the trade,” says Ensenat.
Speaking of helping others, Conrad and his best friend Omar Harris (@omartheplumber) are in the initial stages of their PipeTalk “Instacasts”on Instagram. “We want a show where we can talk about anything in the trade, not a show about showcasing tools or doing giveaways. Real talk about experiences in the trade. How we can truly help apprentices understand what they are getting into,” says Ensenat.
In the end, for Conrad, it’s important to show new apprentices that the plumbing trade is not just about labor-intensive work; there is a future beyond just being a plumber. For instance, you can become lead plumber or foreman, says Conrad, or you can get your license and become an inspector or a plans processor. “There are so many great paying jobs with opportunities revolving around plumbing than just installing pipe, tubs and toilets all day. And this goes for any man or woman and every color and race—you have the opportunity to go far as you want.”
And with that hard work comes a little down time. Before the pandemic, Conrad would take multiple vacations a year to spend time with his family. “When I’m off work, I’m off. The two days a week I’m off, it’s all about either what I’m doing or spending time with the kids or the wife,” says Ensenat.
During football season, it’s all about the Miami Dolphins—Conrad would enjoy tailgating and going to games, including road games. Oh, and the last time Conrad said today is a great day? “I opened a cleanout at the front of a house holding water. Stuck the cable in 3 feet and it cleared without turning the machine on. Winner, winner, chicken dinner.”
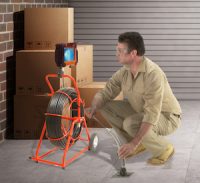
Save BIG with General’s GEN–EYE SUPER REBATE! Getting your rebate is easy! Just purchase an eligible Gen–Eye® sewer camera system through March 31, 2021: Buy any complete Gen-Eye USB or SD system, and get a US $1000 Rebate Buy any complete Gen-Eye X-POD system, and get a US $1000 Rebate Buy any complete Gen-EYE POD system, and get Read more
Save BIG with General’s GEN–EYE SUPER REBATE!
Getting your rebate is easy! Just purchase an eligible Gen–Eye® sewer camera system through March 31, 2021:
- Buy any complete Gen-Eye USB or SD system, and get a US $1000 Rebate
- Buy any complete Gen-Eye X-POD system, and get a US $1000 Rebate
- Buy any complete Gen-EYE POD system, and get a US $500 Rebate
- Buy a GM-G2 Gen-Eye Micro-Scope system and get a $250 Rebate
Just submit a rebate form, a copy of your invoice/receipt, and warranty registration card for each purchase. It’s that easy to put money back in your pocket. A picture could be worth a thousand dollars!
Gen–Eye sewer cameras precisely pinpoint what the problem is, where it is, and how deep to dig.
Always easy on your back and your budget, General’s lightweight, compact Gen–Eye POD® pipe inspection cameras now feature Wi-Fi inside that lets you use your own tablet or smartphone to record the inspection and send it to your customers.
The Gen–Eye X-POD® features a powerful Command Module with USB port to record video inspections on a flash drive. It’s packed with features like a big 7” LCD color monitor, one-touch recording, digital zoom, voice-over recording, and more.
The Gen–Eye USB® Premium packs a lot of features into a compact package, including a USB port, 10.4” sunlight readable screen, waterproof keyboard, rechargeable battery that lasts up to 4 hours, and Wi-Fi, all protected by a heavy-duty Pelican case.
For details, download the rebate form at www.drainbrain.com/CameraRebate today! Or, for more information, call the Drain Brains® at 800-245-6200.