Watts offers “Industrial Pipe Solutions: The Science Behind Making the Right Choice,” an ASPE-accredited webinar worth 0.1 CEUs. Many types of industrial facilities have specific drainage requirements for sanitation, contamination, chemical resistance, temperature, mechanical stress, and fire safety. The right choice of drainage materials, methods, and attention to proper engineering practices can help to mitigate Read more
fire safety
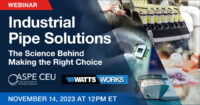
Watts offers “Industrial Pipe Solutions: The Science Behind Making the Right Choice,” an ASPE-accredited webinar worth 0.1 CEUs.
Many types of industrial facilities have specific drainage requirements for sanitation, contamination, chemical resistance, temperature, mechanical stress, and fire safety. The right choice of drainage materials, methods, and attention to proper engineering practices can help to mitigate contamination and corrosion that can affect drainage systems while providing installation and operational benefits.
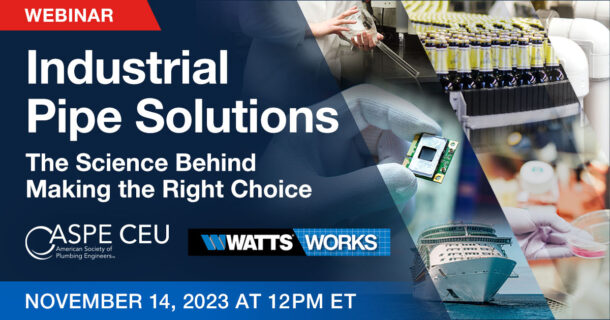
On Tuesday November 14th, 2023, from 12:00 p.m. – 1:00 p.m. ET, participants will learn how to:
- Identify the risks associated from improperly specified drainage materials
- Identify the primary considerations when selecting drainage materials for specific applications
- Analyze and evaluate the performance of various drainage materials
- Describe the unique advantages and benefits of various drainage systems
- Compare the cost ramifications of different drainage solutions
To register, visit Watts.com/PipeSolutionsWebinar.
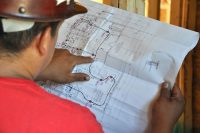
Increasing mandates to include fire sprinkler systems in new residential construction are naturally affecting bottom-line costs. Fortunately, several steps in the design process, if undertaken early enough, can minimize the financial sacrifice. By Melisa Rodriguez, P.E., NICET IV Residential fire sprinkler systems can save lives as well as prevent financial, physical and emotional damage. Yet Read more
Increasing mandates to include fire sprinkler systems in new residential construction are naturally affecting bottom-line costs. Fortunately, several steps in the design process, if undertaken early enough, can minimize the financial sacrifice.
By Melisa Rodriguez, P.E., NICET IV
Residential fire sprinkler systems can save lives as well as prevent financial, physical and emotional damage. Yet, historically, fewer than two percent of new homes include them. This hesitance to incorporate fire sprinklers largely results from the cost, which ranges between one and two dollars per square foot for residential systems.
In recent years, however, state and local governments have increasingly come to recognize fire sprinkler systems’ value. As a result, they are gradually adopting National Fire Protection Association (NFPA) standards that govern fire sprinkler installation. NFPA Standard 13R, developed in 1989, governs detection and control of fires in multifamily residential buildings and residential occupancies up through four stories in height. NFPA Standard 13D, developed in 1973, affects one- and two-family dwellings, manufactured homes and townhomes and aims to prevent flashover, or the explosive ignition of flammable gases released by burning materials in the home.
With states like California and Maryland, along with other municipalities nationwide, officially adopting these standards and requiring fire sprinkler systems in all new one- and two-family homes, builders have no choice but to face the costs head on.
Fire sprinkler system costs have three main determinants:
- Pressure losses: Depending on how much pressure is lost in a home’s supply pipes, this problem can mean increased meter sizes or supply-pipe diameters, or even costly storage tanks and pumps.
- Number of sprinkler heads: The more sprinkler heads required in a home, the higher the material costs.
- Installation time: Labor can add considerable cost to a fire sprinkler system. The more complicated the system, the more labor will be required to install it.
Fortunately, the above determinants, and thus the costs, can be limited during the design process by considering underground water supplies, builder techniques and design techniques.
Water Supplies
According to NFPA 13D, the minimum pressure requirement for a standard residential fire sprinkler head is 7 psi (pounds per square inch). The flow required to meet this pressure will change depending on the size of the sprinkler orifice, but for a typical residential sprinkler that flow will be 13 gpm (gallons per minute). Verifying the size and distance of the water supply line to the home is thus indispensable to appropriately planning a system. The supply line determines how much money any given sprinkler system will cost the sprinkler installer, builder and homeowner. Large underground supply lines to houses allow for smaller and less complicated sprinkler lines, which reduce material and labor costs.
Ideally, a sprinkler system design will be completed before supply lines are in place. This way, the builder can give the designer the specifics regarding the underground distances and allow the technician or engineer to determine the most appropriate pipe size.
Various components between the street’s water main and a sprinkler head inside the home can affect pressure loss and thus a fire sprinkler system’s sizing.
- Pressure-reducing valves (PRVs) are necessary to keep incoming pressures below fixture ratings. Depending on which type of PRV is chosen, a builder can expect to lose more or less water pressure.
- Water meters can potentially have a significant impact on available flow and pressure to the fire sprinkler system. Identifying the meter’s make and model to your sprinkler design technician can allow for appropriate sizing.
- Meter setters can greatly restrict water flow and should be avoided whenever possible.
- Elevation significantly impacts pressure changes. A loss or gain of 0.433 psi per foot of elevation will occur in water traveling through pipes along the elevation. This must be taken into consideration during the calculations.
Overall, it is important to involve the local water department and fire sprinkler design professional as early in the design process as possible. The more information you have about pressure loss and flow rates in the water supply system, the more effectively you can plan your fire sprinkler system.

Builder Techniques
Builders can take advantage of various techniques to reduce the number of fire sprinklers required in a residence. Fewer sprinkler heads mean less cost. NFPA 13D allows for sprinkler omissions in certain areas of the home:
- Garages, open attached porches, carports and similar structures do not require sprinklers. However, it’s important to check local and state codes that may exceed NFPA standards for such requirements.
- Closets in which the area does not exceed 24 square feet and whose shortest dimension does not exceed 3 feet do not require sprinklers. Builders can design closets to meet these specifications and save money on sprinklers. The walls and ceilings must, however, be surfaced with noncombustible or limited-combustible materials, as defined in NFPA 220.
- Bathrooms that measure 55 square feet or less do not require sprinklers. A bathroom is defined as a compartment with a plumbing fixture, and breaking up a large bathroom into compartments that are each smaller than 55 square feet will mean you aren’t required to put sprinklers in any compartment.
- Ceiling pockets that are less than 100 cubic feet in volume do not require sprinklers. Still, the entire floor under the unprotected ceiling pocket must be protected by the sprinklers at the lower ceiling elevation. Furthermore, the interior finish of the unprotected ceiling pocket must be noncombustible or limited-combustible.
- Sprinklers are also not required in attics with or without storage, penthouse equipment rooms, elevator machine rooms, concealed spaces dedicated exclusively to and containing only dwelling unit ventilation equipment, floor/ceiling spaces, elevator shafts, crawl spaces, and other concealed spaces that are not used or intended for living purposes.
Design Techniques
Certain steps taken during the design process can keep the pressure requirements low and reduce the total number of sprinklers required. The following factors can impact costs:
- Material Types: It is important to take into account the pros and cons of the piping material for the system. Depending on which material is chosen, the system may require more or fewer fittings and piping materials. See chart.
Pros | Cons | |
CPVC | • Inexpensive materials• Large internal diameters
• 175 psi rating • Can be installed in limited-exposed applications • Typically covered by a manufacturer’s warranty |
• Affected by rain and high-humidity conditions• Can be dry-fit which can cause blow-offs from uncemented connections
• Susceptible to freeze damage |
Copper | • Large internal diameters• Can be installed in exposed applications | • Expensive• Prone to pitting, scaling and corroding
• Can be dry-fit which can cause blow-offs from unsoldered connections • Susceptible to freeze damage • No warranty |
Steel | • Large internal diameters• Can be installed in exposed applications | • Expensive• Prone to corrosion, compatibility issues
• No warranty |
PEX-a | • Flexible for fewer fittings,• Fast, easy connections
• Not affected by rain or high-humidity conditions • Greater impact strength • Expands up to 3X its diameter, minimizing potential freeze damage • Certain manufacturers approved for installation in exposed applications • Covered by a manufacturer’s warranty
|
• Smaller internal diameters
|
- Piping Configuration: Depending on whether the piping system is configured in a tree or loop style can affect pipe size, pressure loss and, as a result, cost. Again, the pros and cons of each type of configuration should be considered. See chart.
Pros | Cons | |||
Loop Configuration |
|
|
||
Tree Configuration |
|
|
- System Type: The two most common types of fire sprinkler systems available are: standalone, mostly used with a tree configuration; and multipurpose, mostly used with a loop configuration.
In a standalone system, the aboveground piping serves only fire sprinklers, with a completely separate set of pipes directly connected to them. This system usually requires not only a backflow prevention device, but also additional drain and test connections.
A multipurpose system requires the fewest fittings and connections. Integrated into a home’s domestic cold-water plumbing, the sprinklers essentially become additional fixtures. This type of system reduces stagnant water in the sprinkler lines and also eliminates the need for costly check valves, antifreeze and backflow preventers (along with the maintenance that accompanies them).
A competent fire sprinkler designer will consider water supply, building and design factors before installing the most cost-effective system in a residence. It’s a planning process that must begin at a building project’s earliest stages. Appropriately designed, a fire sprinkler system can help save lives without breaking your budget.
Melisa Rodriguez, P.E. is the Design Services Supervisor for Fire Safety at Uponor in Apple Valley, Minn. She can be reached at Melisa.Rodriguez@uponor.com.