General Pipe Cleaners Power-Vee® drain cleaner with automatic feed makes clearing small drain lines faster and easier. The power cable feeding system is like having an extra hand in tight and awkward places. Just squeeze the lever and the cable feeds at a rate of up to 16 feet per minute. The Power-Vee easily unclogs sinks Read more
Flexicore Cables
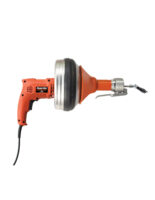
General Pipe Cleaners Power-Vee® drain cleaner with automatic feed makes clearing small drain lines faster and easier. The power cable feeding system is like having an extra hand in tight and awkward places. Just squeeze the lever and the cable feeds at a rate of up to 16 feet per minute.
The Power-Vee easily unclogs sinks, tubs, toilets, and laundry drains ranging from 1-1/4″ to 3″ diameter and at a distance of up to 50 ft. The automatic feed instantly adjusts to take any cable from 1/4″ to 3/8″ without requiring the use of tools or additional parts.
The Power-Vee also features quick-change cable cartridges for fast cable changing or cleaning, a Dyna-Thrust™ bearing system to reduce bearing wear and extend the life of the tool, and an ergonomically designed aluminum drum that resists corrosion.
The optional Handy-Stand™ turns the Power-Vee into a practical countertop or floor machine. The ergonomically balanced Handy-Stand enhances the drain cleaner’s versatility, safety and stability. The optional Uni-Stand makes it easier to access clogged drains under sink cabinets.
Flexicore® cables are made of heavy gauge wire that is coiled tightly around 49-strand aircraft-type wire rope and heat treated. It has unequalled strength and the right amount of flexibility. Flexicore is so tough it carries a one-year warranty against defects or breakage.
For more information contact the Drain Brains® at General Pipe Cleaners at 412-771-6300 or visit www.drainbrain.com/pv to watch the Power-Vee in action.
General Pipe Cleaners, a division of General Wire Spring Co., is a leading manufacturer of high-quality American-made drain cleaning equipment. In business since 1930, the fourth-generation family-owned company is celebrating nearly a century of service to drain cleaning professionals and plumbing contractors, as well as facilities managers, the rental industry and the hardware/home center market. The Toughest Tools Down The Line.
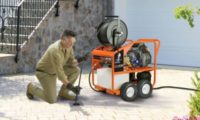
Misconception #1 – You should always wear rubber gloves when operating a snake style drain cleaning machine to protect yourself from the health risks of sewage. While it is true that plumbers and drain cleaners should always be aware that they and their equipment are potentially in contact with human waste and take appropriate actions Read more
Misconception #1 – You should always wear rubber gloves when operating a snake style drain cleaning machine to protect yourself from the health risks of sewage. While it is true that plumbers and drain cleaners should always be aware that they and their equipment are potentially in contact with human waste and take appropriate actions, operating a cable style drain cleaning machine wearing only rubber gloves is not one of them. The problem with rubber gloves is that they can become pinched and caught in the rotating coils of a drain cleaning cable, causing great harm to the operator. We always recommend that operators wear heavy-duty two-ply leather gloves or something similar whenever their hands are anywhere near a drain cleaning machine. Thick leather gloves will not get caught between the coils of a snake or cable and can protect your hands from unexpected kinks or loops that sometimes form in the blink of an eye. If you want to wear rubber gloves to take appropriate sanitary precautions against sewage, then wear them under the leather gloves. This strategy gives you two levels of protection!
Misconception #2 — You should put a drain cleaning machine in reverse when retracting cable using a power feed device. Most modern drum style cable drain cleaning machines have a power feed and guide tube. This equipment makes it much easier to feed and retract the cable and serves to protect the operator. Every floor model brand of drain cleaning machine has a power cable feed that allows the operator to easily switch from forward to neutral to reverse while the drum and cable continues to spin in the forward direction. This feature is essential for smooth and effective operation of the machine. If the operator puts the electric motor in reverse and spins the drum and cable in the opposite direction, bad things tend to happen! Most drain cleaning companies coil their drum style cable in a ‘left hand wound’ direction. These cables are simply long, thin springs. Sometimes, like General’s Flexicore Cables, they have a solid inner core, and sometimes they don’t. However, all of them have a ‘direction’ to the outer coil that affects their performance and capabilities when under torque or in motion, and the drums, distributor tubes and power feeds that house and feed these cables are engineered with these capabilities in mind. When you reverse the motor while retracting the cable, you drastically increase the likelihood of kinking, tangling, or weakening the cable. The only time an operator should put the motor and drum of a machine in reverse is when they get a cutter wrapped up in an obstruction, and even then the duration should only be for a few seconds. Save yourself future complications and keep the machine in forward when the power feed is in reverse!
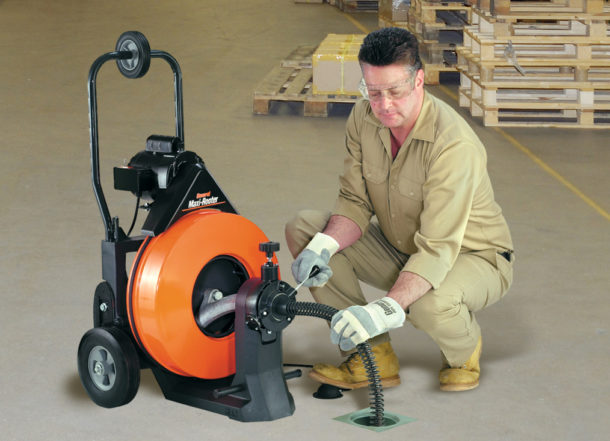
Misconception #3 – Hot water is better than cold water in cleaning drains with a high-pressure water jetter. While it is true that hot water can dissolve grease faster than cold water, the effect at high pressure is marginal. Generally speaking, in real world situations, it is not worth the additional cost and effort. Adding hot water pumps and heating tanks to your jetter protocol makes for a more expensive unit as well as doubling your work at the jobsite. High pressure cold water can do the job almost as fast, without the additional expense and time expenditure. For that reason, in a world where time is money, cold water is the way to go!
Misconception #4– High pressure water drain cleaning jetters with 4000 psi perform better than jetters with 3000 psi. In the past several years, we have seen more and more drain cleaning jetters with 4000 psi come on to the market, claiming that they have more power and effectiveness. However, according to our research, these claims are unfounded. When cleaning a drain, both pressure and flow rate are important factors. The psi, or pounds per square inch is necessary to dislodge foreign material in the pipe like grease and sludge. The jetting process is analogous to spray washing, and a certain amount of pressure, or psi is necessary to scour the inside of the pipe. However, after about 2,500 psi, further increases in pressure fail to deliver significant improvements in cleaning action. From that point on, the gallons per minute flow rate, or gpm grows in importance. For example, increasing a jetter’s flow rate from 4 gpm to 5.5 gpm almost doubles the machine’s drain cleaning speed, regardless of whether the psi is 3000 or 4000. So, look closely at the flow rate of high pressure water jetters before you buy, and don’t be fooled by marketing programs masquerading as science!
Misconception #5 — One of the biggest misconceptions that we hear from first-time General Pipe Cleaners customers is misjudging the ‘initial feel’ of our Flexicore Cable. If the customer is used to another brand of drain cleaner and then purchases a General machine or cable for the first time, they often complain to us that they received a defective cable. To them, compared to the cables that they are used to, it feels limp, weak and not stiff enough to fight its way through tough obstructions down the drain. Although their fears are unfounded, Flexicore does have a looser feel from other cables on the market because of the way it is engineered. However, we reassure our new customers is that the Flexicore will stiffen and strengthen when under torque, giving them clog busting power exactly when they need it the most. According to one customer, “it goes from a noodle to a steel rod in the blink of an eye when you hit the obstruction!” When it comes to General’s patented Flexicore Cable, first impressions can be misleading!
David Dunbar is the National Sales Manager for General Pipe Cleaners, a leader in the drain cleaning/pipe inspection industry. He has been with General since 1996, starting as Customer Service Manager, then Assistant Sales Manager, and National Sales Manager since 2017. He earned a BS degree in Psychology from the University of Pittsburgh and has graduate credits in Human Resource Development and Organizational Theory. David enjoys using his extensive public speaking, video, and writing experience within the industry. He can be contacted at daved@generalpipecleaners.com