For the residents of Gloucester, Mass., the name Gorton’s Seafood means more than the fish the company is famous for. Gorton’s promotes a feeling of life, love and trust. Founded in 1623, Gloucester is America’s oldest seaport and the birthplace of the U.S. fishing industry. Gorton’s originated as a father and son duo in 1849 Read more
Gorton’s Seafood
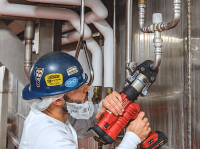
For the residents of Gloucester, Mass., the name Gorton’s Seafood means more than the fish the company is famous for. Gorton’s promotes a feeling of life, love and trust.
Founded in 1623, Gloucester is America’s oldest seaport and the birthplace of the U.S. fishing industry. Gorton’s originated as a father and son duo in 1849 under the name John Pew & Sons, and has evolved into the most recognizable and best selling seafood brand in the U.S. Operating out of the original 1906 building, Gorton’s prides itself on its heritage and quality products.
The third floor of the Gorton’s Seafood Center had been out of commission for the last decade but was remodeled to make room for a new fry line. Eric Sweet, President of Northeast Process Systems Inc. (NEPSI), has worked in Gorton’s facilities for the last 15 years and was tasked with remodeling the 20,000-square-foot facility.
“We specialize in FDA-regulated manufacturing facilities, including food and beverage, pharmaceutical and cosmetics,” Sweet said. “Gorton’s is one of our very good customers. They’re actually our closest customer, located in the same town as our shop. It’s also where we got our first exposure to Viega ProPress and that was more than 10 years ago. It was Gorton’s that actually specified it for their project the first time around.”
Rob Sinico, Senior Innovation Project Engineer for Gorton’s, has chosen NEPSI for nearly every mechanical repair the company has had. So when it came to the remodel, Sinico trusted Sweet at NEPSI when he suggested using Viega ProPress for stainless.
“We look at NEPSI as a supplier and installer to recommend the latest and greatest to us,” Sinico said. “We use their expertise in the field to tell us what’s new and what products are out there.”
NEPSI installed 10,000 feet of Viega ProPress for 304 stainless fittings with piping in sizes ½” to 3″ for applications including compressed air, hot and cold water, and a water/glycol mix. NEPSI chose stainless knowing it would stand up to the chemicals used for cleaning the Seafood Center. Everything that can be – even the floor drains – are stainless steel. They also used Viega’s 3-piece ball valves for shutoffs throughout the Center.
“Almost all of our machines and equipment are stainless steel,” Sinico said. “Because we are in food production, it has to be highly sanitary and easy to wash and clean. We use corrosive chemicals to do that, and the stainless holds up. When they wash, they wash floor to ceiling, so wherever the pipes are, they’re going to get hit.”
According to Sinico, NEPSI also chose stainless because it was better suited to the application. “Once you go stainless,” Sinico said, “you should never have to repair or replace that again. So it might cost more upfront, but in the long run we knew we’d never have to touch it again.”
While Sweet at NEPSI appreciates the fact that it saves him time and labor, it’s the end user’s confidence that makes him glad he chose Viega.
“A lot of the factories we’re in like the Viega system too, because if there is a problem, they can do repairs on site with their own personnel,” Sweet said. “Gorton’s, among others, have actually purchased the products and tools to do small jobs. Personally, the Viega ProPress system has added to our versatility. It was something our customers welcomed.”
Sinico agrees, also noting that the quality is more valuable than the upfront cost of the fittings. Knowing that the connections are secure is more important, and, with Viega press technology, he gets the security he needs.
“With solder, you don’t know how well it held up until you put it under pressure, but with Viega press technology you have a better feeling that it was secured properly,” Sinico said.
“You’d be hard pressed to find any soldered fittings around here.”
The time was also a consideration for Sweet, who was concerned about how much time it would take to get the new system in place and not interrupt Gorton’s production schedule.

“I think the two biggest benefits are time savings and that there’s no requirement for hot work. Sometimes in a working facility that would mean that you probably couldn’t do it during business hours. You’d have to do it on an off shift or on a weekend,” Sweet said.
“With Viega ProPress, we can work while the production line is running.”
Gorton’s went the extra mile and even installed a fire protection system utilizing Viega ProPress for stainless steel, which exceeds the company’s Current Good Manufacturing Practice standards. Along with exceeding the requirements, the project was completed in four months and was worth the upgrade for America’s best seafood brand.
“It’s pretty impressive when you go out and look at that floor,” Sinico said. “Everything is neat. Our entire electrical conduit is also stainless, so aesthetically it looks nice. And it’s all durable, and that was the main driver for going with stainless. I can certainly say, big or small, we use Viega systems. That’s our standard.”
For more information, call 800-976-9819 or visit www.viega.us.