Without proper maintenance, steam and hot-water boilers in hydronic heating systems corrode and become less efficient, leading to additional service calls and a shorter life span. Replacing a heating system can be very expensive, costing home and building owners thousands of dollars. To help prevent this, encourage your customers to spend a little money every Read more
Heating System Cleaner
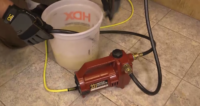
Without proper maintenance, steam and hot-water boilers in hydronic heating systems corrode and become less efficient, leading to additional service calls and a shorter life span. Replacing a heating system can be very expensive, costing home and building owners thousands of dollars.
To help prevent this, encourage your customers to spend a little money every year on services to maximize the life of their heating systems and prolong a significant expenditure.
With that said, there are some best practices when it comes to servicing a boiler not firing up or flushing different types of hydronic heating systems. In such a system, water expands when it is heated and contracts when it is cooled; i.e., enlarges or reduces in volume. Known as thermal expansion, this is the tendency of matter to change its shape, area, volume, and density in response to a change in temperature.
To accommodate thermal expansion, storage is needed within a system. Two types of systems accommodate thermal expansion: a closed loop (sealed) system and an open loop (vented) system.
Before we dive into how and when to flush a heating system, let’s take a closer look at the difference between a closed loop system and an open loop system.
What is a Closed Loop System versus an Open Loop System?
Closed Loop
In short, a closed loop system is closed to the atmosphere. These systems integrate expansion tanks to accommodate the expansion and contraction of water. A closed system also has a built-in, dedicated return line to carry water back to the heating source (usually a boiler), preventing the possibility of warm or cold spots from mixing in the water supply, as happens in an open loop system.
Usually smaller than open loop systems, closed loop systems there take up less space, while assisting with cleanliness, improving water quality, and reducing the entry of oxygen into the system.
As already noted, a closed loop means less potential for water to enter the system, and that decreases the risk of corrosion.
Open Loop
An open loop system is open to the atmosphere and draws water directly from the hot or cold water lines to which it is connected. Open loop systems have an open expansion tank that accommodates expansion and contraction within the system. More evaporation happens with this type of system, leading to more water being introduced and possibly contaminating the system.
While closed loop systems aren’t as common, they are usually older heating systems and often cannot reach higher pressures. As mentioned, these units allow pollutants to enter the system water, so feed and expansion tanks require periodic cleaning. That enables oxygen to enter the system, contributing to corrosion.
The pipework run from the expansion tank location to the mechanical room where the boiler is located can be grueling and will need insulating to protect against freezing. (More on freezing temperatures later.)
When to Flush a System
Flushing A Hot Water System
Newer residential hydronic systems with hot-water boilers are closed-loop. We do not recommend opening and flushing a closed loop system unless you absolutely have to. Why? Because the enemy of such a system is actually oxygenated water.
However, like a car, closed loop hydronic heating systems must be regularly serviced to prevent problems and maintain efficiency. But unlike a car, they don’t cough, stutter, give off smoke or produce a foul odor when something goes wrong. The system just silently continues doing its job, slowly deteriorating in performance and failing much sooner than it should.
However, sometimes the system will provide some clues that it is acting up — like making a rumbling noise as minerals start to collect in the system. After all, a closed system still has a component that feeds water into it if it needs to.
Additionally, your customer might have a system leak that they weren’t aware of, adding oxygenated water to the system for years. That will cause many problems and change the pH level in the system.
For a closed-loop residential boiler to operate properly, the liquid it circulates must maintain the correct pH levels. To truly identify if you have a potential leak or sludge buildup, you must conduct a pH test to determine if the system should be flushed with a cleaner. We recommend conducting a pH test at least once a year.
Start with a visual reading by opening the drain valve and bleeding off some liquid. If it appears clear, proceed with a pH test. To run a pH test, you can buy test strips that provide a color-coded readout. If you need a more precise reading — say, for an aluminum system — use a digital pH meter.
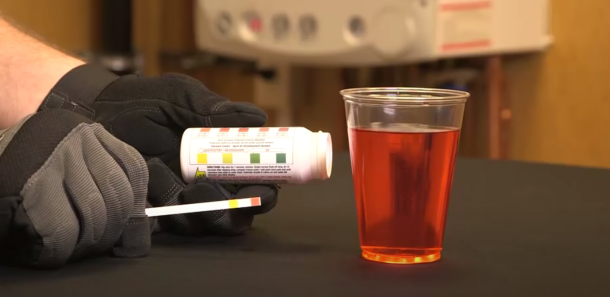
The correct pH level depends on the composition of the heat exchanger. Systems with a cast iron, stainless steel, or copper exchanger are resilient and usually have a wide range of acceptable levels. Aluminum is more prone to corrosion and may require a specific pH number. Read the system’s installation and operating manual to determine the acceptable pH range. We recommend using a corrosion inhibitor to balance out the pH — a seamless fix. However, if the buildup or corrosion has been going on for several years, the system will probably not recover with this treatment. Instead, you’ll have to use a cleaner to flush the system to maximize boiler efficiency.
Check out this blog that covers the impact of pH in hydronic heating systems and how to test and balance levels.
Flushing A Steam Heating System
Larger steam boilers are usually used in multifamily or commercial applications. Years ago, these large steam boilers held thousands of gallons of water. But, as time went by, steam boilers became more efficient. Today, more compact units are available.
As a steam boiler heats up, water turns into steam and eventually flows through the system. When that steam condensates, it all returns to the boiler. But newer, more compact boilers don’t have nearly the capacity of their older, larger counterparts, so the former run out of water quickly.
Over the years, the industry has developed components to sense when the boiler is low on or out of water. They will shut the boiler down, giving the system time to fill up. So these safety components essentially prevent the unit from firing if it’s low on or out of water.
Some components are electronic. Others involve a ball sitting inside the unit that floats up and down as the water level of the boiler changes.
Timers on these systems will indicate a shutoff for, say, one to three minutes, providing time for all the condensate and water to return to the boiler. Then, if the return water is not sufficient, electronic and solenoid valves will open to let more water in.
That, of course, permits corrosion-causing, oxygenated water into the system. Which is why these safety components must be flushed from time to time, because of the likelihood of mineral buildup.
Which is why steam boilers require regular maintenance and should be flushed with a cleaner or corrosion inhibitor at least twice a year — typically at the beginning and at the end of the heating season.
Preventative Maintenance and How to Flush a Heating System
Depending on how dirty the system is and if you don’t want to take it out of operation to completely flush it, we recommend using a cleaner like Hercules® Boiler and Heating System Cleaner. That’s because it can stay in the system and doesn’t require flushing the system.
Hercules Boiler and Heating System Cleaner is formulated to clean and condition all steam and hot-water boilers in hydronic heating systems. The cleaner contains silicone to protect pumps by lubricating seals, maximizing efficiency and preventing valve clogging and corrosion.
Still, be sure to check the pH levels in the system. If the first liquid sample in your visual pH reading contains a lot of rust or sludge, you must take a more aggressive approach by flushing the system with a system restorer. Sludge indicates corrosion in the heat exchanger, fittings or piping.
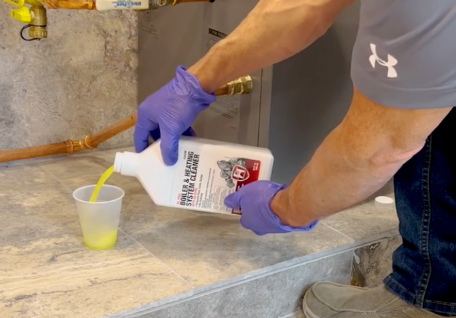
Here’s how to remove sludge:
- Drain off about a gallon of liquid and replace it with three quarts of water and one quart of a system restorer like Hercules® Sludgehammer™ System Restorer & Noise Reducer, which removes scaling and sludge deposits.
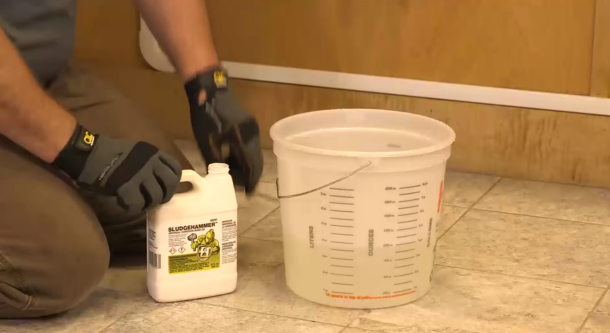
- Let the solution circulate for two hours.
- After 2 hours of cycling, dump the system. Leaving the chemical in for too long can damage metal pipes and fittings and ruin the heat exchanger.
- Refill the system with a blend of water and inhibited virgin propylene glycol to prevent corrosion and scale buildup inside the heat exchanger and piping system. Always reference the system manufacturer’s installation and operating manual to ensure you use the proper blend.
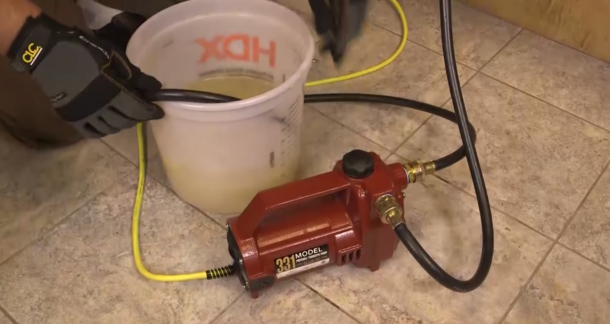
Watch this video to learn how to remove sludge and corrosion in hydronic heating systems with Sludgehammer.
While Flushing the System, add Antifreeze
Many contractors use only water in indoor hydronic heating systems. However, water freezes at 32° Fahrenheit; so if there is a power outage, pipes could freeze and burst. In addition, as we’ve learned, water also promotes corrosion and mineral buildup.
Adding an inhibited virgin propylene glycol antifreeze to a boiler corrects both of those problems. Installing inhibited virgin propylene glycol into hydronic heating systems is also a requirement to maintain warranty by leading boiler manufacturers.
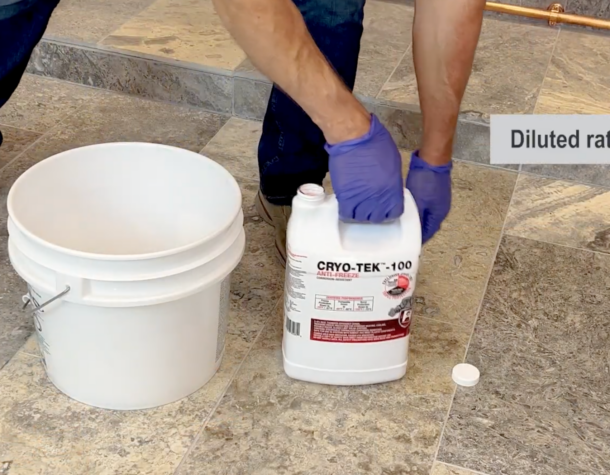
The type of antifreeze you’ll need depends on the climate and the metal content of the system.
- For cast iron, stainless steel, or copper systems, choose an antifreeze solution like Hercules® CryoTek™ AG, -100, Original or Universal.
- For systems with aluminum heat exchangers, the best choice is an antifreeze that works with any type of metal, such as Hercules® Cryo-Tek™
- Depending on the level of freeze protection required to have an effective and efficient operating system, you can choose blends like Cryo-Tek™ AG or Universal and blend them with distilled water to arrive at the proper freeze protection. Or you can purchase pre-blended formulas like -100 or Original.
The active ingredient of antifreeze is propylene glycol. Avoid antifreeze products that contain “used” propylene glycol, which may introduce minerals and other foreign particles to the boiler. Look for a label that reads “inhibited virgin propylene glycol.”
Author’s biography: Sean Comerford is a Technical Applications Manager at Oatey Co. He is a third-generation tradesman with nearly 20 years of plumbing experience, including serving as the lead plumber for commercial/residential new-construction, service and fire protection jobs. He holds a State of Ohio Fire Protection License for Sprinkler and Standpipe.