Whether installing a new boiler or maintaining an existing one, it’s important to consider the inherent issues that can befall a hydronic system and impact the performance of its components. Anticipating these pitfalls and planning accordingly will result in a smarter installation. By choosing your boiler accessories wisely, you can extend the life of your Read more
hydronic systems
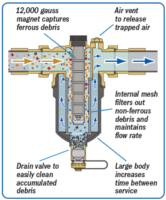
Whether installing a new boiler or maintaining an existing one, it’s important to consider the inherent issues that can befall a hydronic system and impact the performance of its components. Anticipating these pitfalls and planning accordingly will result in a smarter installation. By choosing your boiler accessories wisely, you can extend the life of your boiler and maintain its efficiency while guarding against potential problems down the road.
One of the most common issues comes in the form of ferrous debris, a result of normal metal pipe wear that, when left unchecked, can cause major problems. Over time, rust particles and other debris in the heating loop build up, creating an iron sludge that reduces boiler efficiency or even stops it altogether from working. The resulting damage can require expensive repairs, increase heating costs, and reduce the overall lifespan of the boiler.
To combat the accumulated sludge in the pipes, a system flush may be required. Depending on the severity of the issue, this could be a costly and time-consuming process. Moreover, doing so will not reverse any damage that’s already been done to the boiler. By the same token, boiler manufacturers are becoming more stringent about their warranty claim requirements. Installing a boiler accessory as a precautionary measure is the most consistent way to ensure due diligence is being done. The best protection from iron sludge is to prevent it from ever reaching the appliance.
To protect the boiler, consider the Magnetic Boiler Filter (MBF) from Webstone®, a brand of NIBCO. It captures ferrous and non-ferrous debris before it can reach the boiler using a high-powered 12,000 Gauss magnet. Its internal filter knocks out sediment as it enters the unit, breaking down the sludge and maintaining optimal flow rate. The build-up is captured in the body, which has a large storage capacity to increase time between service. The strapped cap is also used to actuate the integrated drain valve, making it simple to remove accumulation when needed, and a service tool is included to help remove the filter housing with ease.
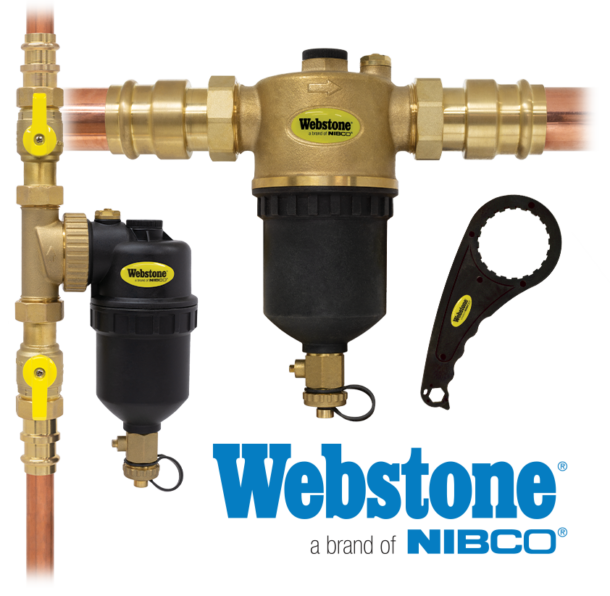
The MBF bodies feature G-thread ends for connection to your choice of MIP, FIP, sweat, or press union fittings. Unions and bodies can be purchased as an installation kit or as separate components depending on the installer’s preference. Optional lead-free dezincification-resistant brass isolation valves are also available to simplify future service. When installed in conjunction with a circulator pump, the flanged ball valve saves space, labor, and leak paths compared to the off-the-shelf assemblies that would normally be required to connect the two appliances. It also mitigates the risk of electrolysis and galvanic corrosion, while allowing virtually no air into the system upon pump replacement. For more simple isolation needs, Webstone offers straight and angled G-union ball valves with reversible handles.
For smaller systems, the ¾” and 1” models feature a universal diverter that allows the MBF to be used in both horizontal and vertical piping orientations on the system return line. For horizontal installations on the system run, the Magnetic Boiler Filter XL model is now available in sizes 1¼” or 1½”. Introduced in 2021, the patent-pending MBF XL is ideal for larger residential and light commercial boiler applications, with a robust 2-layer metal mesh filter and manual air vent.
Webstone offers a wide array of system performance products designed to support efficient operations and protect components. To learn more about how you can work smarter, visit Webstone Valves.
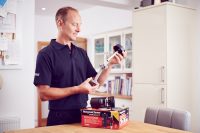
We are approaching the end of the 2018-2019 heating season in North America, although homeowners in the colder northern sections of the United States and throughout Canada will likely need their heating systems for another two, maybe even three months. As you know, our long cold seasons can take a heavy toll on hydronic heating Read more
We are approaching the end of the 2018-2019 heating season in North America, although homeowners in the colder northern sections of the United States and throughout Canada will likely need their heating systems for another two, maybe even three months. As you know, our long cold seasons can take a heavy toll on hydronic heating systems. Here’s a rundown on some of the more common boiler and component problems facing home and business owners and what can be done to remedy them.
Radiator cold spots
If your home’s or business’s radiators are not uniformly hot throughout, the following could be the culprit:
- air in the piping and components;
- a malfunctioning component or part, such as a circulator or a valve; and, finally, our “favorite” villain —
- rusty or corroding system pipes that ultimately fill the radiators with magnetite.
What is magnetite? As air and water mix inside the pipes of an untreated hydronic heating system, an iron oxide sludge, called magnetite, forms. As these small (.0003-micron) particles circulate and accumulate inside the system, they begin to adversely affect heat-transfer rates and boiler efficiency. Eventually, iron oxide buildup can lead to equipment damage and/or failure, resulting in costly repairs. Just how extensive is this problem? A recent study analyzing returns to European pump manufacturers found that nearly 70 percent of circulator returns consisted of failures triggered by iron-oxide buildup. The study also showed that more than 95 percent of the debris in hydronic heating systems consists of iron oxide*.
The fix? To eliminate air in the system, first try bleeding your radiators. But if the cold-spot problems persist, bring in a professional plumbing and heating contractor to:
- conduct a full system inspection;
- upgrade failing parts;
- fully cleanse the system with a magnetic dirt filter, as well as a chemical cleaner, such. This maintenance should remove not only the rust, but also all the other debris.
Noisy system
Maybe your boiler rattles every time it rolls into action. Maybe you are routinely treated to a chorus of bangs, gurgles, whistles and rumbles from elsewhere in the system. Regardless, such noise goes beyond mere annoyance; it might indicate more serious problems. Once again, air as well as a buildup of limescale are the most common culprits.
The fix? To eliminate the pipe noise, get rid of any trapped air by bleeding your radiators. If that doesn’t work, call a professional to flush the entire system of limescale and air. If the noise originates in your boiler, your service technician will work to remove limescale in the heat exchanger.
Leaks and drips
Water leakage from your boiler is never a good sign. Leakage usually means a breakdown is imminent. It’s a simple problem to spot. Is there any water beneath the boiler or around its pipes and tank? Causes can range from broken parts to corroded pipes.
The fix? Whether the problem stems from a damaged component or simple wear and tear, there’s only one answer for leaks and drips: Call a professional to check your boiler.
On the subject of leaks, it is often questioned whether cleaning chemicals cause leaks within hydronic systems. The answer to this is — no, if, of course, you are using correctly formulated chemicals, which includes surfactants, dispersants, and inhibitors that make it pH neutral. The surfactants and dispersants help dislodge, lift and move the corrosion, while the inhibitors protect the vulnerable metals during cleaning.
Complete protection
The rising popularity of high-efficiency boilers and the increased use of high-efficiency ECN (electronically commutated motors) pumps with these boilers, have helped lower fuel bills. That’s the good news. The downside: both of these positive trends can also create system-performance headaches for home and business owners. We will explore the why behind these problems in a future blog. For now, understand that both trends can lead to premature system and component failure because of the buildup of iron oxide sludge (magnetite) and other nonmagnetic debris. Both can rob hydronic heating systems of their high efficiency and superior performance.
The solution is magnetic dirt filtration, along with regular and proper system cleansing and protection. This is the only way to prevent the buildup of magnetite and the costly problems it can cause.
GUEST BLOGGER: Brian Salem, ADEY Western/Central North America area sales manager.
Growing up in his Dad’s plumbing company, Brian has a wealth of experience within the HVAC/P industry. Professionally, Brian has been in the industry since 2004 and joined ADEY in 2017 – his role began as OEM Manager for North America but due to ADEY’s growing network of North American Reps, Brian has now taken the reigns as ADEY’s Western/Central North America Area Sales Manager. Brian Salem: brian.salem@adey.com, (847) 440-6665