No job is too big or too small for trade contractor support. Whether you need help with a quick repair or a complex installation, there are plenty of experts out there who can lend a hand. The key is knowing where to look and how to ask for help. You know when you’re in the Read more
jobsite
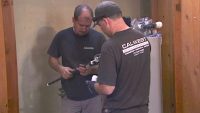
No job is too big or too small for trade contractor support. Whether you need help with a quick repair or a complex installation, there are plenty of experts out there who can lend a hand. The key is knowing where to look and how to ask for help.
You know when you’re in the middle of the job and you realize that there’s more to it than you thought. Or an issue comes up and you need another person in the trades to step in and support you to get it done. In this blog post, we’ll give you some tips on getting expert support when you’re on the job.

Before You Start the Job
The first step is to do your research. If you know what type of help you need, start by looking for businesses or individuals who specialize in that area. For example, if you’re a plumber who needs help with an irrigation project, you’ll want to find an expert in that field. Once you’ve compiled a list of potential options, take some time to read reviews and compare pricing. This will help you narrow down your choices and find the best option for your needs.
Another important consideration is your timeline. If you have a tight deadline, make sure to communicate that to the expert you’re working with. If you need to get out mobile welding services then you’ll want to arrange that ahead of time to support your job. This will help them plan their work accordingly and ensure that they’re available when you need them.
Asking for Help
Once you’ve found the right expert for the job, it’s time to reach out and ask for help. The best way to do this is by being specific about what you need assistance with. When possible, include as much information as possible so the expert can give you an accurate quote.
It’s also important to be clear about your budget. This will help the expert determine whether they’re able to take on your project within your specified price range. If not, they may be able to suggest alternative solutions that fit within your budget.
How to Find the Right Person
No matter how experienced you are, there are always going to be times when you need a little help on the job. Whether it’s a tricky installation or a last-minute change order, it’s important to know where to turn for expert support. Here are four places you can go for help when you’re on the job.
1. The Internet
Whether you’re looking for installation tips or troubleshooting advice, chances are good that you’ll find what you’re looking for online. There are plenty of forums and chat rooms where trade professionals can ask questions and get answers from their peers. In addition, many manufacturers and suppliers offer online support services.
2. Trade Associations
If you’re having trouble finding the information you need online, your next best bet is to contact a trade association. These organizations represent professionals in all sorts of trades, and they can often provide members with access to experts who can offer advice and answer questions.
3. Local Suppliers
When all else fails, your local supplier is always a great resource for expert support. These businesses depend on repeat customers, so they’re usually more than happy to help out with installation issues or other problems you might be having. In addition, many suppliers offer training courses on the products they sell.
4. The Manufacturer
If you’re still struggling to find the answers you need, your last resort is to contact the manufacturer directly. Many manufacturers have customer service representatives who are familiar with their products and can offer helpful advice. You may also be able to find helpful information on the manufacturer’s website.
Calling in the Experts
Getting expert support on your next job doesn’t have to be difficult—just follow these tips! With a little research and planning, you can find the perfect individual or business to lend a hand with even the most complex projects. So don’t wait—get started today and rest easy knowing that you have the support you need to get the job done right.
No matter what kind of problem you’re having on the job, there’s an expert out there who can help you solve it. By turning to the internet, trade associations, local suppliers, or the manufacturer, you should be able to get the answers and information you need to get the job done right.
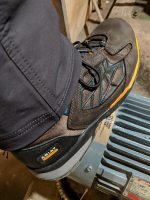
Summer vacations are winding down and the annual ritual for parents buying school supplies for the kids is underway, but maybe it’s high time to kick off the old work boots and find a new pair. Does that sound like a great first step? Recently, Mechanical Hub ProStaff member Andy Mickelson, owner of Mickelson Plumbing and Read more
Summer vacations are winding down and the annual ritual for parents buying school supplies for the kids is underway, but maybe it’s high time to kick off the old work boots and find a new pair. Does that sound like a great first step?
Recently, Mechanical Hub ProStaff member Andy Mickelson, owner of Mickelson Plumbing and HVAC in Montana, tested a pair of Ariat Rebar Flex 6″ Waterproof Composite Toe Work Boots on multiple job sites and in various indoor/outdoor conditions to provide us with the following observations.
For those not familiar with the Ariat Work Boot Brand (most recognize the brand for its western boots), they have unique and tasteful designs while at the same time delivering high-quality performance and comfort in a stylish and fashionable boot.
Ariat work boots are designed and engineered with the contractor and jobsite person in mind. Constructed from premium sturdy and durable leather with the most advanced footwear technologies they offer superior performance and on the job critical protection in any work field or the environment. Ariat boots offer a safety platform to match every environment, such as the Grip Strip Platform, the Work Ride Platform, the Expert Safety Clog Platform and the Safety Clog Platform.
Ariat also offers ATS and 4LR technology for comfort, stability, and traction as well as waterproof technology with the impermeable waterproof barrier. Insulated boots featuring Thinsulate Ultra insulation will help to give your feet the highest level of cold weather protection and while remaining a lightweight shoe. Ariat also offers a steel toe range for added safety. Ariat boots come with an oil, slip, heat, and abrasion resistant sole that will perform with the best grip and traction on any floor surface.
MICKELSON: It’s the first safety toe boot that I have comfortably worn throughout an entire work day in many years. For the past few months, I’ve worn them almost daily, sunrise to sundown, and in many cases hours into the night, on various surfaces without issue.
The Ariat Rebar work boots come out of the box ready to wear, with relatively little break in needed. The boots have a stylish design with a combination leather and mesh upper. The insole of the boot is comfortable with decent arch support. The soles are listed as a slip & oil resisting, debris release design. I’d support that statement having worn the boots through the better part of winter. Snow and parking lot slop stomps off easily. The tread pattern seems to grip well on most surfaces even when the temperatures drop well below zero.
Many soles will begin to harden and become hazardous well before that, not the case with the Rebar. The debris release design comes in nice while constantly transitioning from snow covered ground onto finished concrete or similar smooth finishes. The uppers of the boot are leather and man-made materials, which lend to the boot breathing very well. Generally breathing well and waterproof aren’t generally both strong traits in a work boot, again, not the case with the Ariat Rebar.
As a Professional Plumber and Pipefitter, these boots have been nearly submerged numerous times and thoroughly soaked on the exterior with no leakage regularly. The leather is holding up fairly well with normal daily abuse, resulting in small cuts and scrapes. The hardware on the boots consist of a single plastic rivet and webbing attachments below, holding a quality paracord like lace. Double row stitching has the components locked together.
Overall I look forward to wearing these boots for as long as they’ll last and very much looking towards to fulfill my work boot needs with Ariat in the future.
Work Boot Specs:
- Waterproof leather in key protection and support areas combined with rugged mesh panels
- 100% non-metallic
- Anatomical last for true fit
- Injected lateral support cage
- Forefoot flex notch
- Mesh lining
- EVA cushioning midsole
- ESS midsole in heel for extra protection and support
- Oil-and slip-resistant Duratread™ outsole with debris-release tread design
- Defined heel
- Safety toe is ASTM F2413-11 M/I/75 C/75 EH rated
- 4LR™ footbed for support and cushioning
For more on Ariat work boots and other work gear, visit Ariat Work.
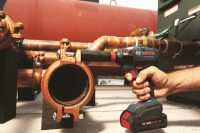
Program is in beta test with industrial users both on the jobsite and off When Bosch introduced its Bluehound asset tracking solution to select customers, the focus was on builders on the jobsite. That’s still the case. But a great beta test site has turned out to be a rental equipment and supply house that Read more
Program is in beta test with industrial users both on the jobsite and off
When Bosch introduced its Bluehound asset tracking solution to select customers, the focus was on builders on the jobsite. That’s still the case. But a great beta test site has turned out to be a rental equipment and supply house that works with its customers.
Cole Breese, inventory warehouse manager, 365 Equipment and Supply, Barrington, Ill., knows an advantage when he sees one. “We’re always looking to get better,” said Breese of the company’s decision to test Bluehound. “We’ve been testing this out on a big project for about seven months. We need to see where equipment has been so that we can optimize asset availability, verify quantity access and monitor records tied to individual assets.”
Getting the Jobsite Running
365 rents everything from power tools and work platforms to cranes and front loaders, in a market area that stretches from Chicagoland to Milwaukee. The company is a one-stop shop for contractors, sub-contractors and municipalities. 365 also sells power tool accessories to support its rentals.
Ryan Braschko, warehouse manager at 365 Equipment and Supply, says there are 7,800 pieces of equipment in the company’s fleet. Up to this point, the company has relied on traditional methods to track when products were rented, when they left a site and when they were returned. If a product stays in the field, the 365 team has limited information as it moves from jobsite to jobsite.
With Bosch Bluehound, Braschko can accurately track every job an item has served, as well as duration and status. While 365 hasn’t implemented the entire Bosch solution, the pair notes that Bluehound has been able to complement and enhance their current system. Bosch tracking tags can be placed on every piece of equipment so it’s easier to see where an item is in real time. The 365 goal is to replace the manual tracking/static bar code-following computer software system that captures tool serial number, jobsite name and contact information for the foreman at a single jobsite.
Efficiency of Asset Flow
Bluehound development has pushed the Bosch research team to consult with everyone from jobsite managers to company owners, from site owners and general contractors to developers and sub-contractors. Bosch has also talked to distributors about how sales representatives find products when they’re in the field.
Even with the diverse feedback Bosch has gathered, there’s no test site quite like 365 Equipment and Supply. “Most of the adjustments we’ve made to Bluehound were influenced by our experience at 365,” said Eli Share, mobile and IoT lead, Bosch Power Tools. “We’re working to be the software link between the tool crib and the jobsite. We’ve seen the influence this technology can have here.”
Share notes that one of the biggest challenges for their customers is that tools and equipment walk from jobsite to jobsite. Nothing has been stolen, but no one in the organization knows which site has what products and equipment. There’s no clear reporting, yet some companies generate thousands of pages of paperwork. He observed that many man-hours of manually checking and verifying records doesn’t prevent lost and stolen items.
What’s clear is that companies want to know where tools and equipment are located all the time, including small tools. One of the things that makes Bluehound attractive is that users can immediately tell if a product is lost or stolen due to manual status updates in the system. And that’s related to the tag.
“On the jobsite, people see the tag – that’s a theft deterrent to start,” said Braschko. “But the real value is that it saves time by showing equipment location on a map.” And any discrepancy about tool location can potentially be cleared up with a single phone call.
The Service Angle
In the case of 365, it’s less expensive to repair serviceable tools rather than having to replace them on a regular basis. With Bosch Bluehound, users know what the maintenance history is so repairs can be completed in a proactive manner. The system also reduces the reliance on manual maintenance administration.
“Everything we need is there in Bluehound,” said Breese. “The system was raw when it first came in, but the team has built up a hierarchy of asset tracking, locations and other details. Initially, we didn’t know what to expect, but we knew this was an opportunity to improve our business.”
The lifecycle for products at 365 is remarkably consistent: small tools, three-to-five years; larger tools, five years; laser measuring tools, seven to eight years. Efficiency and cost savings come when Breese and Braschko know where tools are located all the time rather than having to purchase replacements.
Today, 365 Equipment and Supply buys more tools than it takes in return, but that’s now a product of growth. Throughout the course of its short history, 365 has seen its business grow and become balanced season to season. With Bluehound, the company has been able to optimize asset availability, quantity access and records tied to individual assets. And these functions can be done from anywhere.
“This is the first time we’ve used a live tracker,” said Braschko. “It’s been good.”
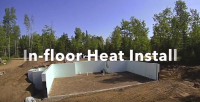
Sometimes its fun to step back and see the whole process from start to finish. Here’s a time lapse video of the prep and install for the radiant in-floor heating at the #duluthbuild project in Northern Minnesota. I’ve been trying to document each step along the way for this project we are building for my Read more
Sometimes its fun to step back and see the whole process from start to finish. Here’s a time lapse video of the prep and install for the radiant in-floor heating at the #duluthbuild project in Northern Minnesota.
I’ve been trying to document each step along the way for this project we are building for my little sister and brother-in-law and I’m starting with the over 7K sq ft of radiant. If you’d like to follow along you can search the hashtag #duluthbuild on either Facebook or Instagram, doing so will show you all the posts from the project.
If social media isn’t your thing or you’d just rather stay put here on The Hub check out these recent videos:
What is permanent? What will be there in 100 years?
Uponor Ecoflex pre-insulated job site install