The new patent-pending Boiler Vent Valve is a space-saving valve that expands the utility of a boiler’s existing ¾” pressure relief valve (PRV) port, capitalizing on its location at the top of the unit as the ideal placement for an air vent and other accessories. Its automatic air vent can be isolated for service, allowing Read more
NIBCO
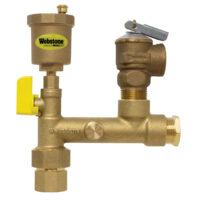
The new patent-pending Boiler Vent Valve is a space-saving valve that expands the utility of a boiler’s existing ¾” pressure relief valve (PRV) port, capitalizing on its location at the top of the unit as the ideal placement for an air vent and other accessories. Its automatic air vent can be isolated for service, allowing the PRV (included with the boiler or sold separately) to operate unobstructed. Plugged FIP ports accommodate the installation of a low-water cut-off device and/or pressure gauge if so desired.
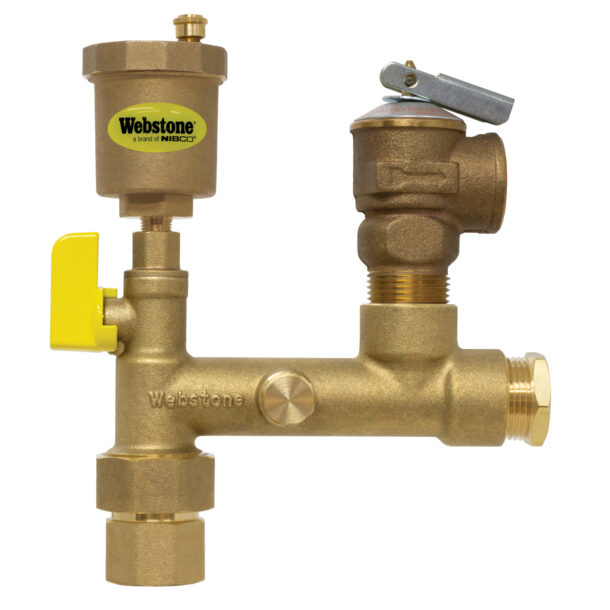
Learn more: www.webstonevalves.com/propal
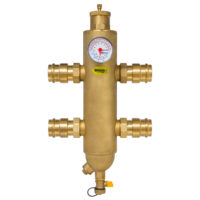
Webstone®, a brand of NIBCO, releases a new Hydraulic Separator to ensure ongoing system performance and efficiency. The Webstone Hydraulic Separator combines multiple components to balance flow between primary and secondary piping, protects systems from debris, and eliminates accumulated trapped air. Its unique, patent-pending design includes a 12,000 gauss magnet, an air separator, a dual-scale Read more
Webstone®, a brand of NIBCO, releases a new Hydraulic Separator to ensure ongoing system performance and efficiency.
The Webstone Hydraulic Separator combines multiple components to balance flow between primary and secondary piping, protects systems from debris, and eliminates accumulated trapped air. Its unique, patent-pending design includes a 12,000 gauss magnet, an air separator, a dual-scale temperature/pressure gauge, mounting brackets, and hardware. Available in Press, SWT, FIP, and MIP G-union connections, in sizes 1″ to 1 ½”.
Learn more: www.webstonevalves.com
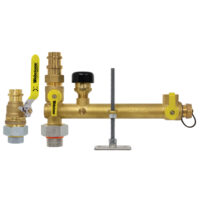
Webstone®, a brand of NIBCO, announces new Water Heater Service Valve Kits. These kits simplify the installation of water heaters and isolate the water supply and other peripheral devices for service. Hot and cold connection solutions are available with options for your unique installation needs, including isolation valves, vacuum relief valves, and expansion tank service Read more
Webstone®, a brand of NIBCO, announces new Water Heater Service Valve Kits. These kits simplify the installation of water heaters and isolate the water supply and other peripheral devices for service. Hot and cold connection solutions are available with options for your unique installation needs, including isolation valves, vacuum relief valves, and expansion tank service valves.
All kits feature FIP dielectric unions for connection to the water heater and press or sweat options for connection to system piping. All products are forged from lead-free dezincification-resistant brass.
Learn more: www.webstonevalves.com/pro-pal
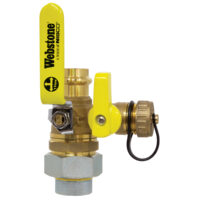
Webstone®, a brand of NIBCO, announces an array of new dielectric products. Pro-Pal® Dielectric Union Ball™ and Dielectric Union Ball Drain simplify installations with integrated FIP dielectric unions that mitigate the risk of galvanic corrosion and satisfy code requirements. The Webstone press dielectric union is also now available in new 1¼” to 2” sizes. All Read more
Webstone®, a brand of NIBCO, announces an array of new dielectric products. Pro-Pal® Dielectric Union Ball™ and Dielectric Union Ball Drain simplify installations with integrated FIP dielectric unions that mitigate the risk of galvanic corrosion and satisfy code requirements. The Webstone press dielectric union is also now available in new 1¼” to 2” sizes. All products feature lead-free dezincification-resistant brass and press products are compatible with popular press tools.
Learn more: www.webstonevalves.com/propal
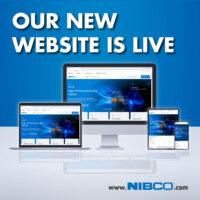
NIBCO has launched a new and improved website, which includes a new design, better search functionality and easier and faster navigation, along with expanded features. The new platform integrates three NIBCO family brands, Webstone®, Sure Seal® and Chemtrol®, for a one-stop, seamless experience for users to quickly find exactly what they are looking for. It also provides Read more
NIBCO has launched a new and improved website, which includes a new design, better search functionality and easier and faster navigation, along with expanded features.
The new platform integrates three NIBCO family brands, Webstone®, Sure Seal® and Chemtrol®, for a one-stop, seamless experience for users to quickly find exactly what they are looking for. It also provides international customers with more access to NIBCO’s full line of products.
NIBCO’s standalone sites have been eliminated, including the NIBCO Poland site, enabling all users to have the same experience.
“We want our new website to better serve our customers and enable them to quickly and easily find the information they need,” said Ashley Martin, executive vice president of NIBCO. “Combining all of our NIBCO brands’ sites into a single platform will create efficiencies for our customers.”

The redesigned site features include:
- Better and faster search functionality across all 36,000 flow control products and NIBCO family brands, including Webstone, Chemtrol and Sure Seal products.
- Improved product “Where to Buy” feature that directs visitors to stocked distributors in their area.
- Build-A-Submittal function that allows users to create an account and organize, store and revise submittal documents.
- Download library with improved filters that permits users to access marketing and technical documents from one location on the site.
- CAD/BIM product database that includes more than 1,200 product families and over 11,000 SKUs with complete product details, performance characteristics and high-fidelity images.
“Our website is our most public marketing vehicle,” added Martin. “If our customers have a positive user experience, then it will positively impact our brand.”
NIBCO encourages users to check out the new website, explore the exciting new features and view the latest products NIBCO has to offer. To view NIBCO’s new website, visit NIBCO.com.