When millions of gallons of water are traveling through your piping system every month, it’s bound to put wear and tear on the system. The folks at Model Linen Service in Ogden, Utah, realized that huge volumes of water were doing a number on their copper; so in a new laundry facility building, they incorporated Read more
pipe connections
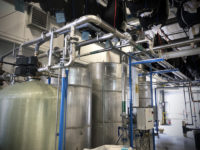
When millions of gallons of water are traveling through your piping system every month, it’s bound to put wear and tear on the system. The folks at Model Linen Service in Ogden, Utah, realized that huge volumes of water were doing a number on their copper; so in a new laundry facility building, they incorporated stainless pipe instead.
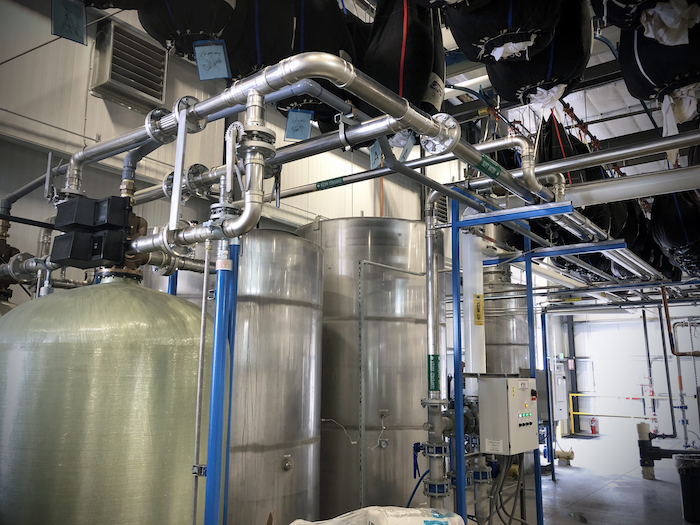
Then, in looking at options for connecting the 3” and 4” pipe, they discovered Viega’s ProPress Stainless fittings and thought it could be a better option than threading.
“ProPress made the day!” said Ryan Thon, Chief Engineer at Model Linen. “I’ve been using copper over the years and just found that I wasn’t getting the life out of it. We get so much water volume through the pipes that it wears out the copper. So we decided to go with the Schedule 40 stainless.”
Model Linen services about 700,000 pounds of linen a week. Their main business in the facility where the ProPress fittings are located is restaurant service items like bar towels and floor mats. Running at capacity, Model Linen needed to expand, so they built a 19,000-square-foot facility bordering the original main plant.
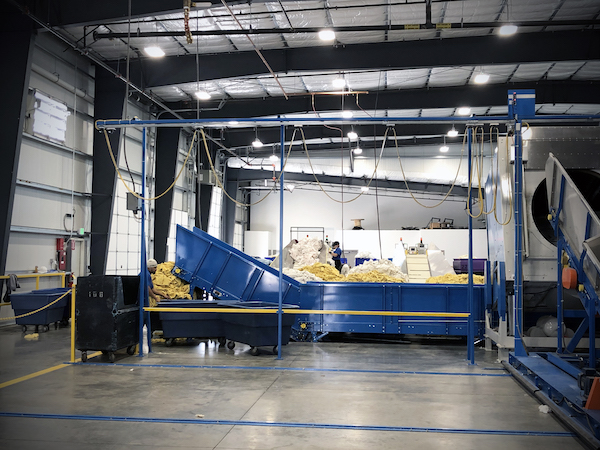
When Thon and his crew started on the building in April 2018, circumstances beyond his control meant they had to start threading instead. He said the first quarter of the building was threaded.
“There’s so much time and effort involved with threading Schedule 40 pipe,” he said. “Then [when circumstances changed], I was able to get the press tool and jaws. And I’d say it probably took me the same amount of time to press the other three-quarters of the building with Viega as it did to thread the first quarter!
“It’s a big facility and it took months of time—but pressing made it so much easier. I’d probably still be threading right now!” Thon said with a laugh.
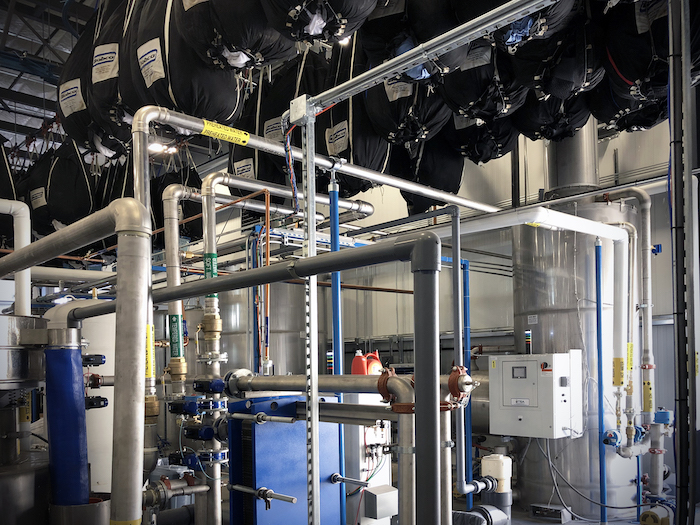
In the building, there is a 4” water main that brings in the cold water. It’s softened and goes into an exchanger. Thon explained that old, dirty water coming from the washers is recycled and feeds through the exchanger to work as a heater. It raises the city water up to about 95 degrees without any heating elements.
“It’s hot water. Why let it go straight into the sewer?” Thon said. “All we’re using is the radiator and pumps to pump it, but we re-water to get our tempered water.”
From there, half of the tempered water goes into the washers and the other half goes through a heater to make hotter, 165-degree-water.
Model Linen does a good job in saving as much water and energy as possible. In addition to using the reclaimed hot water to heat the incoming water supply, the washer’s final-rinse hot water is also reused.
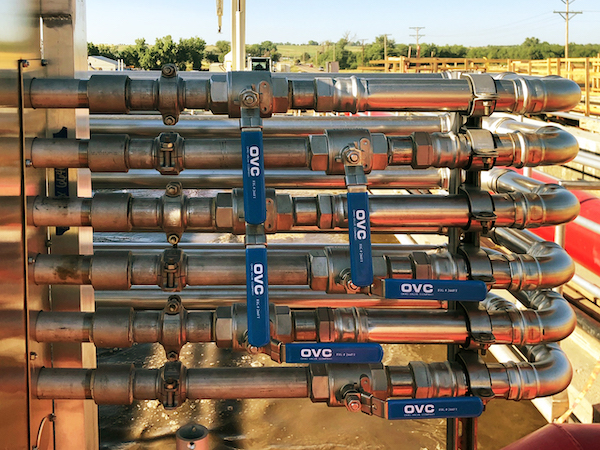
“At that point with the last rinse, the soap is out and it’s clean, so that water drops into its own trench and recirculates to be used in the first part of the wash cycle with the detergent,” he explained. “It’s a pretty cool process instead of using more clean city water.”
In total, nearly 100 Viega fittings were used in Model Linen’s new building, ranging in size from 1¼ ” adapters to 4” fittings in various configurations.
Thon said he’s confident the ProPress Stainless fittings will hold up well to the demands of Model Linen’s system. He said there are not many chemicals that run through the pipes, just a mild softener.
One of the concerns in piping a laundry facility are issues with water hammer, Thon said.
“If the washer has a 3” valve open, that’s a lot of water going in quickly; and if it shuts off too quickly, then it shakes the whole system,” he said. “Luckily we have good equipment dialed in well so that they close slowly. There has been no movement with the pipes at all—I was impressed.”
Thon was so pleased with Viega fittings that they’ll be appearing in Model Linen’s other building a few miles down the road, where all of their hotel linens are serviced. He said he purchased a “whole stack of 3” ProPress Stainless” and was getting ready to tear out all the old copper and put in stainless piping at that facility, too.
“Pressing these fittings down saved the day,” he said simply. “I’ve been pretty impressed with the whole thing.”