Lindon, Utah —Aquatherm, the industry leader in polypropylene piping systems, has released an informative new video that provides an overview of polypropylene pipe applications and benefits, as well as the company’s expertise and capabilities. The “Leading the Way in Polypropylene Piping” video includes information about the advantages of polypropylene pipe over steel pipe for commercial Read more
pipe joining
Lindon, Utah —Aquatherm, the industry leader in polypropylene piping systems, has released an informative new video that provides an overview of polypropylene pipe applications and benefits, as well as the company’s expertise and capabilities.
The “Leading the Way in Polypropylene Piping” video includes information about the advantages of polypropylene pipe over steel pipe for commercial heating and cooling systems, industrial piping, and domestic water systems. The video explains how polypropylene repels water and will never scale or corrode the way metal pipe does, thus ensuring the quality and integrity of mechanical systems and potable water systems.
The video also explains the heat fusion process that joins polypropylene pipe and fittings, and how heat fusion creates a connection that’s as strong or stronger than an as-manufactured section of pipe—with no leak paths.
Also covered are Aquatherm’s Fabrication Services and Scan-to-Fab, both of which can help simplify and compress the timeline of complex projects as well as provide labor savings.
Classes to be held in Colorado and New Hampshire Broomfield, Colo. — Viega, LLC has announced its Winter 2019-20 lineup of courses at its seminar centers in Broomfield, Colo., and Nashua, N.H. The offerings include topics from commercial piping solution to radiant design and LoopCAD. With two fully equipped state- of-the-art seminar centers, Viega is Read more
Classes to be held in Colorado and New Hampshire
Broomfield, Colo. — Viega, LLC has announced its Winter 2019-20 lineup of courses at its seminar centers in Broomfield, Colo., and Nashua, N.H.
The offerings include topics from commercial piping solution to radiant design and LoopCAD. With two fully equipped state- of-the-art seminar centers, Viega is an industry leader in supporting the trades and helping contractors become more versatile, skilled and efficient. To date, more than 40,000 people, from self-employed contractors to employees of large firms, have taken courses at the centers.
The classes are taught by experts with years of experience in the field and offer ample hands-on experience. Attendees leave with skills and knowledge that will show immediate benefits on the job.
Training seminars are listed below:
Radiant Design, Piping and Controls
Jan. 27-29, Nashua, N.H.; March 3-5, Broomfield, Colo.
Covers design theory and practice, piping arrangements and control strategies. Includes hybrid systems, multiple temperature piping arrangements and system component placement.
LoopCAD
Feb. 11-12, Nashua; Jan. 22-23, Broomfield
How to use LoopCAD software for radiant design and layouts. Covers heat loss, drawing layout, material selection and snow melt.
Commercial Piping Solutions
Dec. 3-4 and March 18-19, Nashua; March 3-4, Broomfield
Covers Viega systems and products and their appropriate uses. Includes PureFlow, ProPress and MegaPress; hybrid systems; installation techniques; project savings; hands-on installation and competitive information.
Hydronics 101 & Radiant Systems
March 3-4, Nashua; Jan. 16-17, Broomfield
Provides a basic understanding of how hydronic systems work. Topics include methods of heat transfer, piping materials and components, control strategies and installation methods.
Carbon Steel Press Technology
Jan. 13, Nashua
Covers the use of carbon steel press systems for residential, commercial and industrial piping applications.
Stainless Steel Press Technology
Feb. 20, Nashua
Covers the use of stainless steel press systems for commercial and industrial plumbing, heating and piping applications. Properties and chemical compatibility of 304 and 316 stainless steel will be covered.
Press Technology for Fuel Gas Piping
Feb. 3, Broomfield
Covers the use of carbon steel press systems for fuel gas piping in residential, commercial and industrial applications. Fuel types such as natural gas, LP gas, diesel, fuel oil and kerosene and their implications in NFPA 54 will be covered.
NFPA 13D Fire Sprinkler
Covers NFPA 13D requirements, system design, installation concerns and energy code compliance.
For more information and to register, click here.
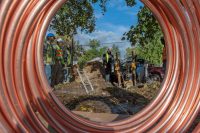
A recent Gallup poll found that 63% of Americans are worried about the safety of their drinking water. Except in extreme cases, these concerns are mostly unfounded as America’s drinking water is among the safest in the World. However, these concerns are understandable considering that the quality of our water is subject to threats old Read more
A recent Gallup poll found that 63% of Americans are worried about the safety of their drinking water. Except in extreme cases, these concerns are mostly unfounded as America’s drinking water is among the safest in the World. However, these concerns are understandable considering that the quality of our water is subject to threats old, like millions of lead pipes, and new chemical contamination from things like PFAS.
Protecting North America’s water safety requires a three-step approach: understanding and recognizing modern water quality threats, specifying safe materials, and following correct installation procedure.
Water Quality Threats
Water quality threats are still abundant. A 2018 study identified 163 different substances that have the potential to leach from common piping materials. These substances range from alcohols to hydrocarbons, ketones, esters, metals, peroxides, phthalates, alkyl phenols, organotins, halogenated compounds and vinyl compounds, including some known or suspected as environmental contaminants or carcinogens. Of these, water quality standards only exist for 89 of them. The other 74 are not currently regulated or understood, leaving a gray area on what effects they may have on our water quality and health.
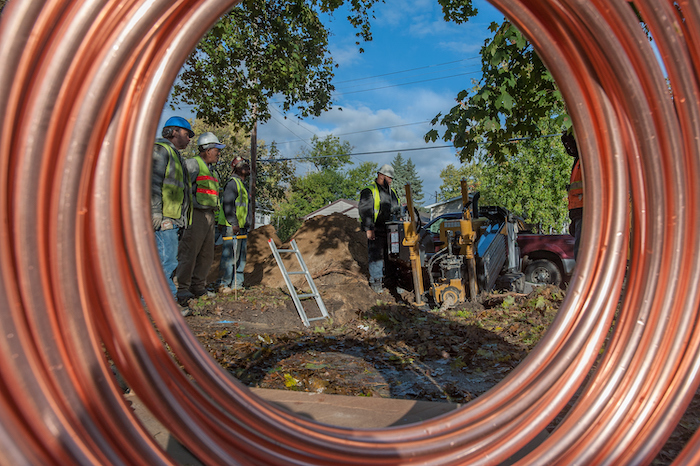
Replacing lead water pipes with copper piping between the street and homes in Flint, Michigan October 28, 2016. (John M. Galloway)
While additional research may help determine the total effect on water quality and health, these substances are a concern and should be taken into consideration when selecting a piping material.
Specifying with Copper
A reliable way to avoid these threats is to select copper, a time-tested, durable, proven piping material. Copper is safe; it won’t release potentially harmful chemicals into the water, it won’t give off toxic fumes in a fire, and it won’t allow harmful chemicals to permeate through the pipe wall. It is natural—made of 99.9% pure copper—and is accepted by all plumbing codes.
Below, is a brief, step-by-step guide for strong, leak-free solder joints—one of the most common joining methods for copper drinking water systems, provided by the Copper Development Association (CDA). CDA has been instrumental in developing the soldering procedures that are now standard in the copper and plumbing industry, and has since taught these procedures to hundreds of thousands of installers across the country and throughout the world.

Proper soldering technique when working with copper pipe.
To assist contractors and installers, CDA has produced several do-it-yourself videos to its “Do it Proper with Copper” YouTube video series. Additionally, the Copper Tube Handbook, available on www.copper.org, provides additional step-by-step installation guides for all copper joining methods. CDA recommends the following four steps for properly soldering joints:
Step One: Preheat the Tube
First, heat the interior surfaces of the fitting/component with heat from the tube surface. The preheating of the tube should be undertaken with the appropriately sized torch tip directing the flame perpendicular to the tube, about the same distance from the fitting cup as the length of tube that is inserted into the solder cup (i.e. if the fitting cup is 1-inch deep, preheat the tube approximately 1-inch beyond the face of the joint). While there is no definitive time limit on preheating, the tube should be preheated until the flux at the face of the joint begins to become active (begin showing signs of cleaning the tube/fitting surfaces).
Step Two: Preheat the Fitting/Component
Once the appropriate preheat has been applied to the tube, the flame should be moved back onto the fitting/component surface to the base of the fitting cup. Preheating of the fitting is most effective if the torch is directed from the back of the fitting cup to the face of the solder cup. This torch position directs the greatest amount of heat from the back of the fitting cup towards the face, where the solder will be applied. This allows for the primary flame of the torch to concentrate heat into the fitting/component while allowing the secondary flame to keep the tube surface at temperature.
Step Three: Apply Heat and Solder
The copper tube has excellent thermal conductivity so as it is heated, it will conduct heat throughout the tube length inside the fitting space. In addition, as the tube expands into the fitting cup, it will maintain a small capillary space between the two and help to heat the fitting cup from the inside. On horizontal joints, preheating should focus on the bottom two-thirds of the tube. Heat it until the tube is very close to soldering temperature, as indicated by the soldering flux beginning to bubble and clean the surface.
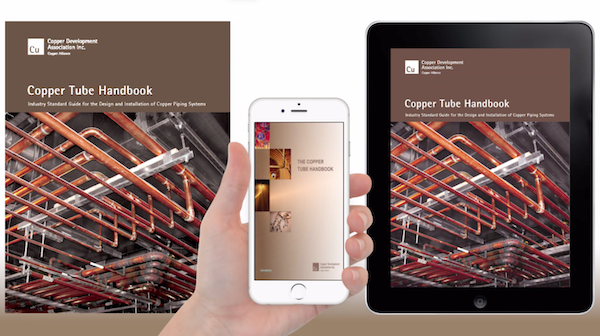
Copper Tube Handbook
Next, move the heat to the base of the fitting cup to bring it up to soldering temperature. Point the torch tip from the face of the fitting cup out towards the tube so the cooler part of the flame continues to keep the tube at soldering temperature. Then apply the heat to the base of the fitting cup. On horizontal joints, that should be somewhere off center near the bottom of the joint, before solder is added. If the solder doesn’t begin to melt, continue to preheat. Once the solder begins to melt, the torch should be moved along with the solder, keeping the heat only slightly ahead of where solder is being applied.
Step Four: Cooling and Cleaning
The completed soldered joint should be allowed to cool slowly and naturally. The new, no-lead alloys may not reject heat as quickly as their predecessors due to their lower thermal conductivity. By controlling the amount of heat applied, an individual can ensure the bare minimum required to facilitate full solder melting and flow is used. This allows the solder to solidify and cool to the joint quickly after the heat is removed.
If the proper soldering procedures are followed, particularly in the preheating and heating process, consistent, high-quality solder joints can be achieved between copper tube and fittings/components.
Durable, Reliable Piping Systems
Compared to copper pipes, no other material has the long history of reliable, leak-free installation in a wide variety of systems and settings, protects the water system from contamination, and does so with proven value. Plus, when copper’s long life cycle finally comes to an end, its high recyclability allows it to be reformed into new products with zero loss of performance. The choice is obvious, the choice is copper.
To learn more about copper piping and installation best practices, visit www.copper.org.
Andrew G. Kireta Jr. is vice president of the Copper Development Association Inc. (CDA). Kireta is responsible for the use of copper and copper alloy systems and products in building construction applications, including plumbing, mechanical and architectural systems.
Milestones Include One Billion Solution Installations Worldwide, Contributions to Eiffel Tower, Hoover Dam and Other Iconic Projects Victaulic celebrates a century of innovation—100 years since it was granted its first industry patent for mechanical pipe joining solutions. On its Centennial “Innoversary,” the company continues to develop and patent groundbreaking technologies, with a current portfolio of Read more
Milestones Include One Billion Solution Installations Worldwide, Contributions to Eiffel Tower, Hoover Dam and Other Iconic Projects
Victaulic celebrates a century of innovation—100 years since it was granted its first industry patent for mechanical pipe joining solutions. On its Centennial “Innoversary,” the company continues to develop and patent groundbreaking technologies, with a current portfolio of more than 2,000 patented solutions that transform the building and industrial construction industries, while driving new industry standards in performance and safety.
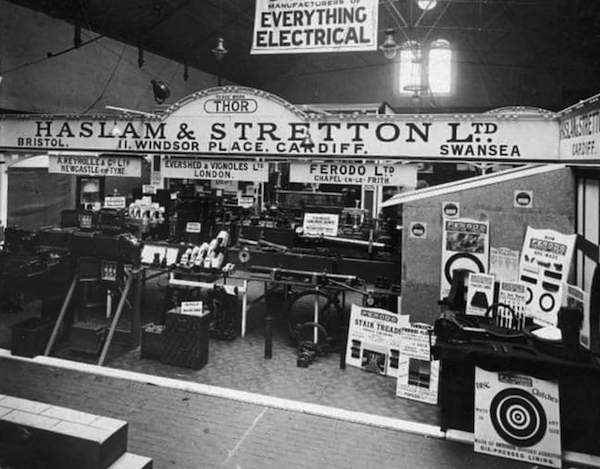
From the very beginning, Victaulic recognized the importance of hands-on demonstrations and building customer relations.
In 1919, Lieutenant Ernest Tribe filed the first patent for The Victory Joint, the first mechanical bolted coupling to join grooved pipe ends. Now known as the Victaulic coupling, the invention enabled critical piping infrastructure to be installed more quickly, safely and cost effectively than traditional methods. While first devised for military applications, the coupling went on to revolutionize the construction industry.
“For 100 years, Victaulic’s reputation has been built on customer collaboration, delivering new technologies that enable productivity, and reducing risk across the construction lifecycle,” said Victaulic’s Chairman, President & CEO John F. Malloy. “Our Centennial ‘Innoversary’ is not only an opportunity to look back on our achievements, it’s also great motivation to make our next century even more valuable for our customers and rewarding for our employees.”
Today, one billion Victaulic solutions have been installed worldwide in some of the world’s most important, iconic and ground-breaking construction projects, including the Hoover Dam, Eiffel Tower, Beijing Olympic Stadium, Petronas Towers and Hudson Yards. The company’s 4,000 employees are spread among 37 branches, 13 manufacturing facilities and five foundries around the world. They proudly serve customers in 120 countries with a variety of application solutions across diverse industries, such as commercial buildings, oil, gas and chemical facilities, power generation facilities, mining operations, and municipal and clean water operations.
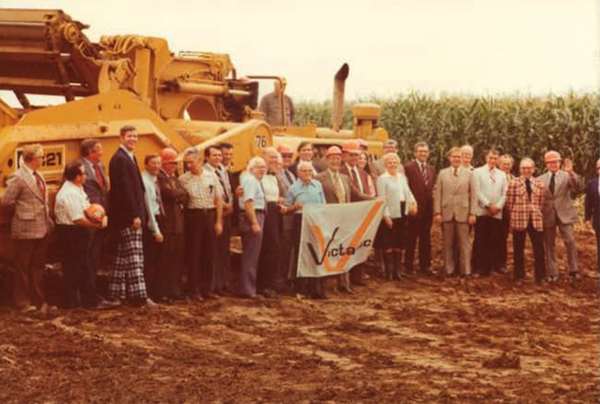
Victaulic broke ground in 1976 to construct its foundry and world headquarters office, on 84 acres of farmland in Easton, Pennsylvania.
Victaulic has been part of Pennsylvania’s Lehigh Valley business community for almost 40 years, having first been headquartered in New York City. Victaulic’s “Innoversary” coincides with current global expansions and investments that will add close to one million square feet to Victaulic’s manufacturing operations, expanding manufacturing capacity to serve customers around the globe. Set to open in 2020, the new, state-of-the-art manufacturing center in Lehigh Valley, Pennsylvania, a 400,000 square-foot facility, is the result of increased domestic demand for the company’s products and the company’s desire to manufacture its products in close proximity to its customers. Additional global expansions include the company’s facilities in Dalian, China; Drezdenko, Poland; and Ontario, Canada.
“Our next 100 years will include more customer-centric innovation as technology grows more rapidly than ever before and we continue to make strategic R&D investments,” said John Malloy. “Our company is an exceptional place to work because of the dedication of our employees and a shared passion for customer excellence across the entire global Victaulic family.”
Victaulic will celebrate its centennial throughout 2019. For more information about Victaulic’s 100 Years of Innovation visit https://www.victaulic.com/100-years-innovation/.