The Drain, Waste and Vent (DWV) piping system in a building is a crucial component of the overall plumbing infrastructure. In a building, the Drain, Waste and Vent (DWV) system is an often overlooked, yet it is an essential component of the plumbing infrastructure. The majority of DWV piping systems are hidden below floors, behind Read more
Piping Systems
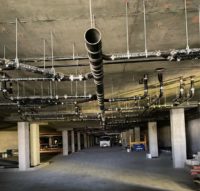
The Drain, Waste and Vent (DWV) piping system in a building is a crucial component of the overall plumbing infrastructure.
In a building, the Drain, Waste and Vent (DWV) system is an often overlooked, yet it is an essential component of the plumbing infrastructure. The majority of DWV piping systems are hidden below floors, behind walls, and in ceilings. Out of sight, out of mind. That is until your previously fully functional plumbing system has a problem.
Plumbing may be out of sight, but just like any other mechanical system, your DWV piping should be properly and regularly maintained, regardless of the material. Developing a DWV maintenance plan will keep your plumbing system top of mind. This will help facility management to budget effectively for your system maintenance and diminish the likelihood of plumbing emergencies that could send your building occupants reeling.
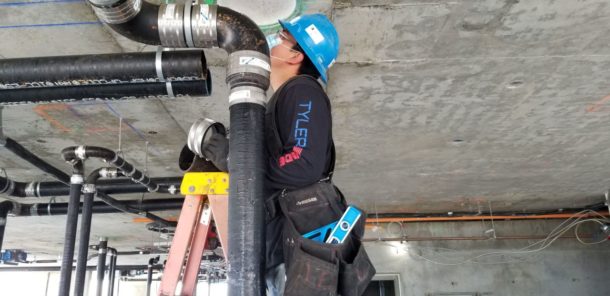
DWV System Evaluation
There is no one-size-fits-all maintenance program for DWV systems. Building occupancy type and usage, piping material, and other special conditions that are unique to your building requires evaluating your DWV systems as a first step.
Facility management can start by performing a regularly scheduled visual examination of the DWV system. You are looking for proper slope, appropriate support of the piping system and components, suitable venting and clear vents, and of course, any visible leaks in the piping system, among other things. Regular visual inspection is just one step in a larger effort to maintain your DWV system.
If your visual inspection reveals no obvious signs of wear and tear, do not assume that you are in the clear. Many factors outside of the DWV system can have negative effects on it and its long-term functionality. These factors are what are at the heart of the maintenance program. As conditions change, the frequency and the way you maintain your system should change with it.
Once you have completed your visual inspection, consider the risk factors that make your building unique. What are some of the considerations when determining the factors and frequency of your maintenance program?
- Cleaning chemicals Harsh cleaning chemicals having a pH range outside the normal range of expected sanitary effluents could be harmful to the DWV system, unless properly flushed.
- Grease Interceptors These should be serviced in accordance with manufacturer’s recommendations so as not to allow its contents to go septic. Proper disposal of food particles is key to the health of an interceptor.
- Gases from the municipal sewer Some municipalities depend on the building’s vent system to vent gases from the sewer, which can be harmful to the building vent piping because this is not the intended application. When these gases are in the system, regular flushing should be performed to minimize the impacts.
- Building usage Is the buildings occupancy year-round or seasonal? If usage is low, more frequent maintenance of the DWV system may be required.
- Low flow or no flow fixtures The proliferation of low flow and waterless fixtures for conservation have unintended consequences. Not enough water in the lines to self-scour or to float the proverbial boat leaves behind microbes that are potentially harmful to your piping system.
- Soda fountains Sodas are typically low pH fluids. In high concentrations, they can be detrimental to pipe and fittings, especially if they are not properly flushed through the system.
- Commercial kitchens High temperature fluids from pasta stations or commercial dishwashers can exceed the working temperatures of certain piping systems and lead to system failures.
- Special waste Any waste outside the scope of normal sanitary effluents should be treated as such, with piping approved for the materials that they are conveying. Any special chemicals must be properly diluted before being allowed in the city sewer.
- De-icing Agents De-Icing agents (road salts, sand and the like) used on roadways can accumulate in the DWV system in parking garages. This accumulation needs to be assessed and a maintenance schedule developed to flush and clean the system to the municipal sewer.
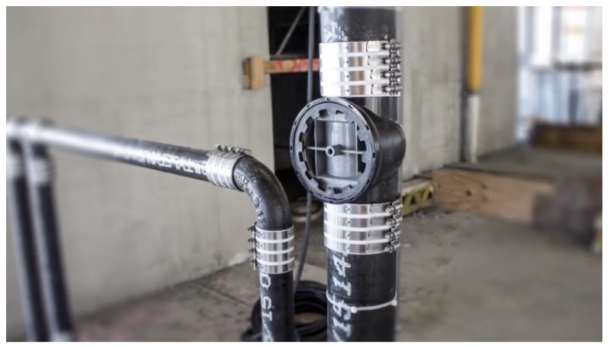
How To Maintain Your DWV System
There are countless tools available for you to incorporate into a facility maintenance program. Here are just a few:
- Camera inspection allows you to see inside your piping system and identify issues that would otherwise remain hidden until it is too late.
- Jetting, drain cleaning, cabling, or rodding to the municipal sewer are also effective methods for cleaning and clearing your DWV system.
- Solenoid may be installed to introduce water to dilute, wash or clean the DWV system where needed.
- Installing vented running traps to isolate the building’s DWV system from the city sewer will prevent your municipality from relying on your building to vent gases into the city sewer system.
- Follow the manufacturer maintenance recommendations of any dilution tanks the building may have.
- Identify and replace any aggressive cleaners that the building cleaning or maintenance personnel may be using with a neutral pH cleaning alternative.
- Consider installing upstream flush valves on soda fountain lines for proper dilution.
Many factors outside of the DWV system itself can have long-term effects on the system’s performance and functionality. Slope, system design, fixtures, frequency of use, chemicals and cleaners, maintenance, materials, and water levels and quality are just some of the factors that can affect a DWV system. All of these influences and more need to be examined and properly assessed by facility management when creating an effective plastic or cast iron DWV system maintenance program.
The information above is not meant to be a complete list of all factors that need to be considered and are merely suggestions for formulating a maintenance program. Proper flushing of your DWV system on a regular time schedule is crucial to a long service life. It may be necessary to consult a plumbing professional when designing an effective DWV preventative maintenance program to keep your plumbing system from being top-of-mind for all the wrong reasons.
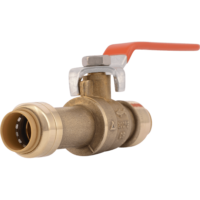
As the deep winter freeze arrives, frozen or burst pipes can become prevalent. Dealing with an unexpected leak is the last thing anyone wants to tackle in the middle of a busy season; but if it happens, there’s a quick solution to restoring ruptured pipes with no specialty tools, soldering, crimping or glue required: SharkBite push-to-connect Read more
As the deep winter freeze arrives, frozen or burst pipes can become prevalent. Dealing with an unexpected leak is the last thing anyone wants to tackle in the middle of a busy season; but if it happens, there’s a quick solution to restoring ruptured pipes with no specialty tools, soldering, crimping or glue required: SharkBite push-to-connect slip and transition fittings.
“SharkBite gives you a wide range of slip fittings and valves to repair burst copper or CPVC pipes quickly,” said Michael Kornegay, SharkBite Product Manager. “Up to two inches of damaged pipe can be removed using a single fitting, even in wet lines, and a drain valve can be easily added to prevent future freezing.”
Ideal for working with multiple pipe types and in tight spaces, SharkBite’s Brass Push transition fittings can be installed in wet lines and can transition between pipe types, including PEX, copper, CPVC, PVC, polybutylene, HDPE and PE-RT pipes, making them one of the most versatile solutions.
“SharkBite’s push-to-connect transition fittings come with color-coordinated collars for each specific pipe material,” Kornegay continued. “The tool-free transition fittings allow for quick and easy repair of copper pinhole leaks and replacement of brittle polybutylene pipe or broken CPVC.”
Since pipes are at a higher risk of freezing and bursting in the winter, it pays to have a solution like SharkBite’s push-to-connect slip and transition fittings handy for a quick fix. Follow these steps to get the job done fast:
- Cut the pipe cleanly – Be sure the pipe is clean of scratches or debris. If working with copper pipe, use a deburr tool or sandpaper to remove any sharp edges or burrs.
- Measure and mark the insertion depth – Use SharkBite’s Deburr & Gauge Tool to mark the insertion depth on the damaged pipe.
- Make the connection – Push the fitting to the insertion marks. Then, turn on the water and check the connection.
When it comes to repairing a burst, frozen pipe, SharkBite push-to-connect slip and transition fittings save time. Pipe transitions make working with PEX, copper, CPVC, PVC, polybutylene, HDPE and PE-RT pipes hassle free, and SharkBite offers the flexibility of repairing the damaged pipe in wet lines under full flow.
“Just cut, push and done,” Kornegay said. “These SharkBite products allow you to quickly repair those frozen, burst pipes in a short amount of time, so you can finish a job with ease and move on to the next.”
Learn more about SharkBite’s repair options at SharkBite.com.