In the last several decades, increasing regulations on lead content in drinking water systems have directly impacted the evolution of plumbing materials. For Viega, the transition from leaded bronze to ZL (zero-lead) bronze represented a significant milestone in ensuring compliance and advancing industry standards. This is further exhibited by the Viega MegaPress® Transition Coupling, which Read more
press technology
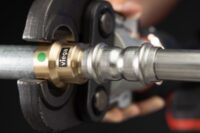
In the last several decades, increasing regulations on lead content in drinking water systems have directly impacted the evolution of plumbing materials. For Viega, the transition from leaded bronze to ZL (zero-lead) bronze represented a significant milestone in ensuring compliance and advancing industry standards. This is further exhibited by the Viega MegaPress® Transition Coupling, which uses press technology to make transitioning between different systems easier than ever before.
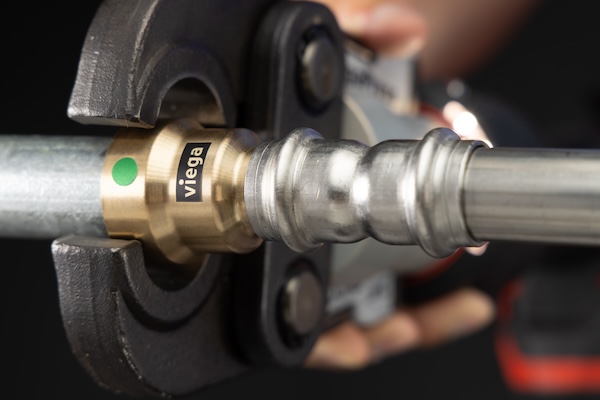
The Shift to Lead-Free Alloys
Regulations on lead content have appeared with respect to gasoline, paint and plumbing systems.
- 1974: The Safe Drinking Water Act (SDWA) was originally created in 1974 and been amended in 1986 and 1996. Allowed the EPA to regulate public water systems and impose limits on contaminants.
- 2008: California and Vermont reduced allowable lead content to 0.25% weighted average across wetted surfaces.
- 2011: The federal Reduction of Lead in Drinking Water Act (RLDWA) mandated a nationwide 8% lead limit.
- 2014: Full enforcement of RLDWA required manufacturers to adopt zero-lead materials for all new potable water systems, further reducing the lead limit for pipes, fittings, and fixtures to less than 0.25%.
These regulatory changes led to the development and adoption of alternative alloys that meet lead content requirements while maintaining performance.
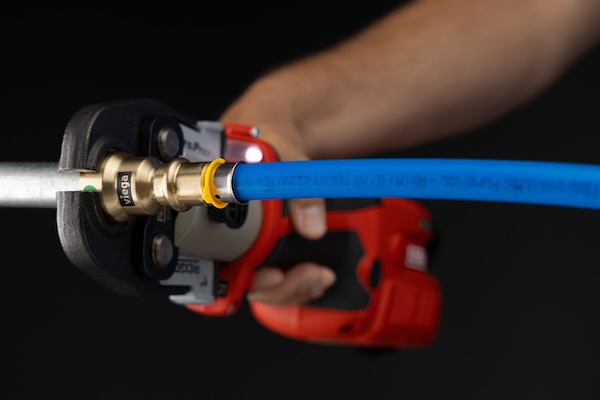
Challenges in Transitioning to Zero-Lead Bronze
The shift from leaded to lead-free components presented significant engineering and manufacturing challenges:
- Material Properties: Traditional leaded bronze offered superior machinability due to lead’s lubricating properties. Lead-free alternatives, such as silicon and phosphorus-bronze alloys, required modifications of machining processes to mitigate tool wear and burr formation.
- Casting and Forming: Lead also contributes to metal fluidity, reducing shrinkage defects. Transitioning to zero-lead alloys necessitated mold redesigns and optimized casting techniques.
- Soldering and Brazing: The wetting behavior of lead-free materials differs from leaded solder, requiring adjustments to flux compositions and brazing temperatures. Installation techniques had to adapt as well due to differential heating between this new bronze and copper tubing.
- Corrosion Resistance: Some zero-lead alloys are more prone to dezincification and stress corrosion cracking, increasing the need for dezincification-resistant (DZR) alloys staying below 15% zinc or adding inhibitors.
- Compliance and Cost: Meeting NSF/ANSI/CAN 61 and 372 standards involved significant investment in new tooling, certification, and material procurement.
The Importance of Dezincification-Resistant (DZR) Bronze
Dezincification occurs when zinc is leached from brass, leaving a porous, weakened structure. Viega’s ZL bronze incorporates DZR properties to ensure:
- Enhanced corrosion resistance in aggressive water environments.
- Longer-lasting performance in high-temperature applications.
- Regulatory compliance without compromising material strength or durability.
Leading the Industry Forward
As part of our commitment to innovation and regulatory compliance, our zero-lead fittings exemplify how advanced material science can support safe drinking water initiatives. Notably, the MegaPress Zero-Lead Bronze Transition Coupling is the first and only press coupling of its kind, setting the standard as a durable, reliable and compliant solution for the plumbing industry.
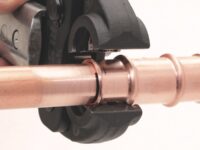
St. Louis — Rapid Locking System (RLS), a leading provider of press-to-connect fittings for the HVAC/R market is proud to announce that its couplings, elbows, reducers, tees, caps, bushings and SAE flares are officially certified A2L-compliant. Attaining A2L compliance required RLS to participate in a thorough testing and screening process, across multiple 3rd party testing Read more
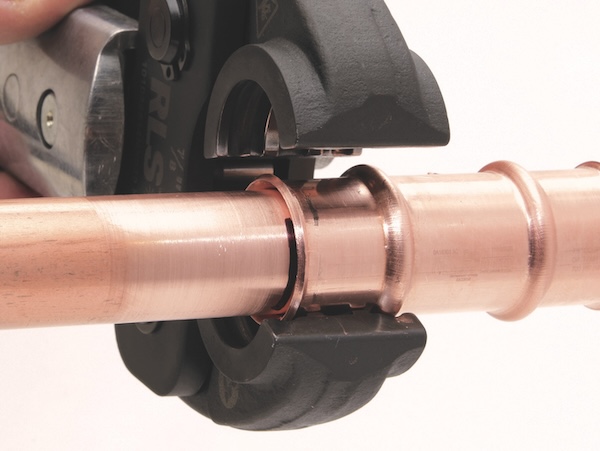
The 180,000-sq.-ft. plant in Shalersville, Ohio, will break ground in November 2023 and is expected to be operational in early 2025. Broomfield, Colo. — Viega recently announced that it will build a new manufacturing facility for its ProPress® and MegaPress® products in Shalersville, Ohio, about 40 miles southeast of Cleveland. Viega LLC President and CEO Read more
The 180,000-sq.-ft. plant in Shalersville, Ohio, will break ground in November 2023 and is expected to be operational in early 2025.
Broomfield, Colo. — Viega recently announced that it will build a new manufacturing facility for its ProPress® and MegaPress® products in Shalersville, Ohio, about 40 miles southeast of Cleveland. Viega LLC President and CEO Markus Brettschneider made the announcement.
“This is an exciting time at Viega, as our growth continues to prompt the expansion of our North American footprint,” said Markus Brettschneider, CEO and President of Viega LLC. “This new facility in Ohio, along with recent investments in our existing Kansas facility, further supports our growing demand and is part of Viega’s plan to increase North American production. We look forward to expanding our presence in this part of the country to further support our customers.”
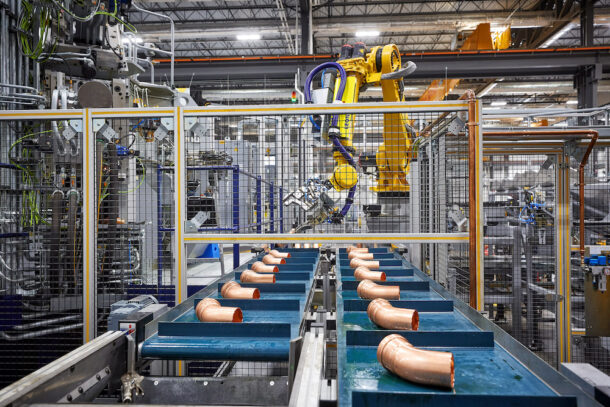
The 80-acre parcel in Shalersville and the construction of the new plant represent an investment of approximately $200 million in Ohio. Viega’s business continues to grow in the U.S., and the additional plant will help support the increased demand for Viega products. It also aligns with the company’s sustainability goals, which include reducing the carbon emissions associated with importing products by manufacturing more items in the U.S. The new facility will be completely carbon neutral from the start, supporting the company’s long-term goal of achieving net-zero carbon emissions for all their plants by 2035.
“The expansion of our operations into Ohio shows our commitment to creating highly skilled jobs in the U.S.,” said Marki Huston, Head of Manufacturing for Viega LLC. “Our goal is to build more sustainable manufacturing processes and continue developing tomorrow’s workforce. With production scheduled to begin in early 2025, we expect to start hiring for positions as soon as January 2024, bringing more than 68 new jobs to the area over the next few years.”
Viega recently announced investments in new equipment for its McPherson, Kansas, manufacturing and distribution facility. In addition, Viega supports its customers and partners through distribution centers in Reno, Nev. and Carlisle, Penn., with more North American expansion planned for 2024 and 2025.
Viega worked with local, regional, and state organizations, including Team NEO, JobsOhio, Portage Development Board and the Shalersville-Streetsboro Joint Economic Development District on tax credit assistance and to select the 80-acre site. “We have a great manufacturing legacy, dedicated talent pool, and future-oriented industry resources to support Viega’s new operations,” said Team NEO Chief Executive Bill Koehler. “Along with JobsOhio and our local partners, we welcome Viega to the Northeast Ohio Region. We are confident they will thrive here.”
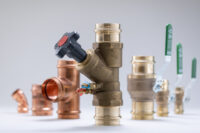
Viega adds MegaPress® 316 Spring Check Valves in 1⁄2” to 2” sizes, MegaPress® Ball Valves in 1⁄2”-4” sizes and ProPress ECO Tubing 316 and Manual Balancing Valves for Potable Water Broomfield, Colo. — Viega announces the availability of new products in its MegaPress® and ProPress® product lines. The expanded line of ball valves completes the Read more
Viega adds MegaPress® 316 Spring Check Valves in 1⁄2” to 2” sizes, MegaPress® Ball Valves in 1⁄2”-4” sizes and ProPress ECO Tubing 316 and Manual Balancing Valves for Potable Water
Broomfield, Colo. — Viega announces the availability of new products in its MegaPress® and ProPress® product lines. The expanded line of ball valves completes the MegaPress system and is ideal for commercial and industrial applications, including gas applications. All the valves have Viega’s SmartConnect® technology, which helps installers easily identify unpressed connections during a pressure test. The new products being added to the line of MegaPress ball valves are:
- – MegaPress Ball Valve 1⁄2” to 2” (EPDM Sealing Element) – a full port valve featuring a carbon steel body, double-stem seal, stainless steel ball, and a lockable handle.
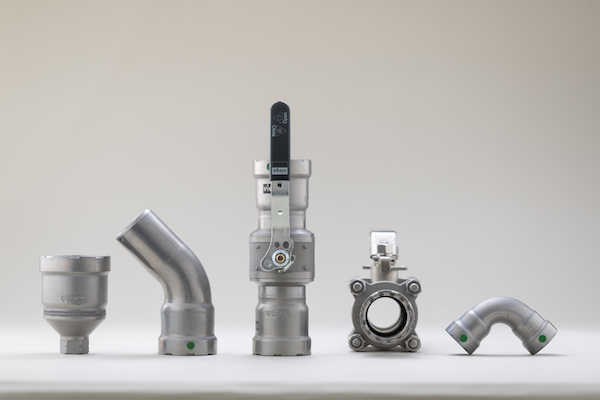
- – MegaPress FKM Ball Valve 1⁄2” to 2” (FKM Sealing Element) – this valve has the same carbon steel body, double-stem seal, stainless steel ball, and lockable handle, yet features an FKM sealing element which is designed for use in higher-temperature applications. The 2-1⁄2” to 4” valves feature a carbon steel body, chrome-plated ball and an SST lockable handle.
- – MegaPress 304 FKM Ball Valve 1⁄2” to 4” (FKM Sealing Element) – this valve features a 304 stainless steel body, double-stem seal, stainless steel ball, and lockable handle. The combination of the FKM sealing element and the 304 stainless steel makes this option ideal for harsh environments that require higher operating temperatures.
- – MegaPress 316 Ball Valve 1⁄2” to 4” (EPDM Sealing Element) – this valve works in a variety of harsh environments, including cleaning agents, acid, and potable water. It is made of a 316 stainless steel body featuring a double-stem seal, a stainless steel ball, and lockable handle.
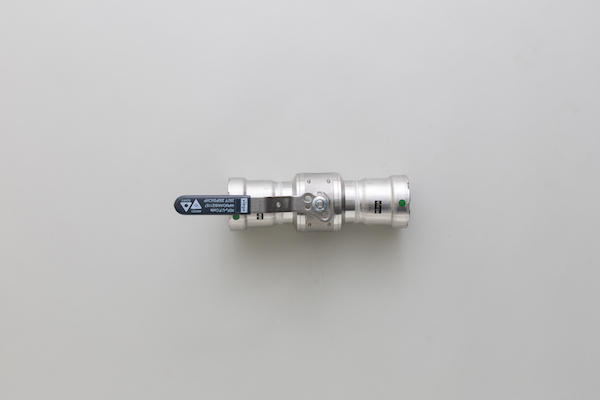
- – MegaPressG Ball Valve 2 1⁄2” to 4” (HNBR Sealing Element) – now available in large diameters, the valves feature an HNBR sealing element at the press-ends which is compatible with fuel and gas applications.
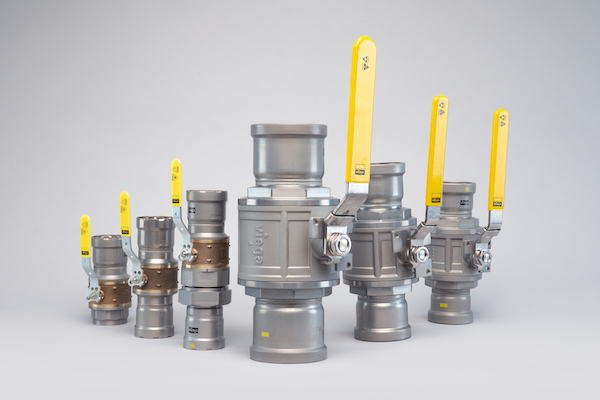
- – MegaPress 316 Check Valve (EPDM Sealing Element) – the check valve helps create directional flow of fluid in one direction while preventing fluid from flowing back. It is ideal for industrial applications, including potable water, rainwater, chilled and hydronic water.
“After 10 years of success, it’s exciting to have the MegaPress portfolio grow with maintenance-free MegaPress ball valves that enable fast, safe and efficient installation from 1⁄2” to 4″. MegaPress 316 spring check valves are a useful addition to the MegaPress 316 portfolio and carry an NSF®-61-372 listing,” said Christian Becker, Product Manager, Valves, of Viega LLC.
Viega also released two new products for the ProPress system – the ProPress Manual Balancing Valve and ProPress 316 ECO Tubing. The ProPress 316 ECO Tubing is a stainless-steel alternative to copper. It’s engineered for commercial potable systems where the piping may come into contact with corrosive cleaning liquids. It is compatible with ProPress 316 fittings and is a great option for potable water, air, acidic and cleaning solution applications.
The Viega ProPress Manual Balancing Valve features an adjustable handle with an integral scale visible on the side used to increase or decrease the flow rate. The two pressure-test ports are used to measure the differential pressure across the seat of the valve, which can be used to calculate the flow rate. The ProPress Manual Balancing Valve is suitable for commercial applications, including potable and hydronic systems.
“Our customers now have more options to use press technology for a larger number of applications,” said Luke Paulo, Manager, Product Portfolio Development of Viega LLC. “The new ProPress 316 ECO tubing is a natural extension to our existing ProPress 316 line. It carries an NSF®-61-372 listing, which means our ProPress 316 system can be used in potable water systems.”
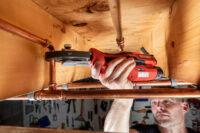
RIDGID, part of Emerson’s professional tools portfolio, introduces the smallest and lightest press tool on the market, the RP 115 Mini Press Tool. Designed for residential and lightweight commercial plumbing use, it completes the majority of press connections installed in the market with ease, while getting professionals to their next job faster. Engineered with the Read more
RIDGID, part of Emerson’s professional tools portfolio, introduces the smallest and lightest press tool on the market, the RP 115 Mini Press Tool. Designed for residential and lightweight commercial plumbing use, it completes the majority of press connections installed in the market with ease, while getting professionals to their next job faster.
Engineered with the quality and technology that have kept RIDGID first in pressing for decades, the RP 115 can press 1/2-inch to 3/4-inch copper and stainless steel fittings. It is 14.6 inches long, 2.5 inches wide and weighs only 5.5 pounds with battery and jaws. The RP 115 has a SlimGrip handle and optimized trigger for balance and control; one-handed jaw opening and operation for reach and ease of use; and 210-degree head swivel for access to tight spaces.
Visit RIDGID.com for more info.