Boiler pressure gauges are critical in maintaining safe and efficient residential and commercial heating systems operations. These gauges are designed to measure the pressure inside the boiler, providing valuable data that helps operators monitor and control the boiler’s performance. This article explores the significance of pressure gauges, their types, installation, calibration, and maintenance to ensure Read more
Residential & Commercial Boiler Pressure Gauges
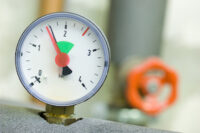
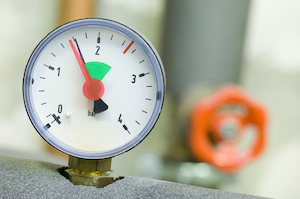
An illustration of a hot water boiler pressure gauge
Boiler pressure gauges are critical in maintaining safe and efficient residential and commercial heating systems operations. These gauges are designed to measure the pressure inside the boiler, providing valuable data that helps operators monitor and control the boiler’s performance. This article explores the significance of pressure gauges, their types, installation, calibration, and maintenance to ensure optimal and reliable functioning of boiler systems.
Importance of boiler pressure gauges
Boiler pressure gauges are indispensable components that enable operators to keep track of the pressure levels within the boiler. Maintaining the correct pressure is crucial for several reasons:
- Low-pressure indicator: One of the primary functions of the boiler pressure gauge is to indicate when the pressure in the system is too low. Low pressure often occurs due to insufficient water levels, resulting from excessive bleeding from radiators, leakages, or incomplete water filling during installation.
- High-pressure indicator: The boiler gauge also alerts users when the system pressure is too high. Radiators can be carefully bled to reduce pressure in space heating applications while monitoring the pressure gauge when the boiler is operational. In other applications, a pressure relief valve can regulate the boiler’s high pressure.
- Maintenance indication: Inconsistent pressure readings during boiler operation may indicate the need for maintenance. These irregularities could be caused by leaks, pipe blockages, or faults in the burner or electrical heating coils. When such inconsistencies are observed, it is important to conduct proper boiler maintenance to address and rectify any underlying issues.
Types of boiler pressure gauges
There are two primary types of pressure gauges used in residential and commercial boilers:
- Bourdon tube gauges: Bourdon tube gauges are the most common type in boiler applications. They consist of a coiled tube connected to the boiler system. As pressure increases, the tube straightens, and the movement is converted into a reading on the gauge. These gauges are reliable, accurate, and suitable for various pressures.
- Digital gauges: With technological advances, digital pressure gauges have become popular due to their ability to provide precise and easy-to-read pressure values. They often come with additional features like alarms and data logging, making them useful for advanced monitoring and control systems.
Selection criteria
Consider the following factors when selecting a boiler pressure gauge:
- Connection size and type: Pressure gauges come with different connections, such as BSP, NPT, and DIN.
- Connection material: Boiler pressure gauges can be made from various materials, like copper alloy and brass. It’s crucial to choose a material that is compatible with the holding socket and process. Always check the material compatibility chart before making a decision.
- Connection location: The gauge’s connection point can be located above, below, or at the rear portion of the gauge. Consider the available space in the system to make an informed decision.
- Unit of measurement: Boiler pressure gauges commonly provide readings in both bar and psi for gauge pressure measurement.
- IP protection: Considering the IP rating is important, especially if the gauge will be exposed to dust or water splashes in its environment. Higher IP ratings will increase the cost of the gauge.
- Digital reading: There are options for digital display pressure gauges, some of which can transmit readings to a remote controller. Most boiler pressure gauges have a dial indicator.
Installation of boiler pressure gauges
Proper installation is vital for the accurate functioning of pressure gauges. Key considerations include:
- Location: Install the pressure gauge on the boiler or on a nearby panel where it is easily visible to operators.
- Piping: Quality piping and fittings ensure a secure connection between the gauge and the boiler system.
- Isolation valves: Incorporate isolation valves on both sides of the pressure gauge to facilitate easy removal and maintenance without affecting the boiler’s operation.
- Calibration: Calibrate the gauge according to the boiler’s pressure range and system requirements.
Calibration and maintenance
Regular calibration and maintenance are essential to keep pressure gauges accurate and reliable:
- Calibration: Perform periodic calibration to verify the gauge’s accuracy against a standard reference. This ensures precise readings and adherence to safety standards.
- Inspection: Regularly inspect the gauge for signs of damage, wear, or leaks. Replace damaged gauges immediately to prevent inaccuracies and ensure safety.
- Cleaning: Keep the gauge lens clean and free from debris to maintain clear visibility. Replacement: Replace pressure gauges that consistently fail calibration tests or exhibit signs of malfunction.
Conclusion
Boiler pressure gauges are vital instruments that enable operators to monitor and regulate boiler pressure, ensuring safety, energy efficiency, and optimal performance. Choosing the right gauge type, proper installation, calibration, and regular maintenance are all crucial steps in maximizing the longevity and effectiveness of pressure gauges in residential and commercial boiler systems. By following these guidelines, operators can ensure safe and efficient heating operations while extending the life of their boiler systems.