By Aaron Stotko
When a century-old Dallas railroad company headquarters required major renovations to transform into a Homewood Suites by Hilton, initial cost estimates for the hydronic heating system came in too high.
That’s when City Wide Mechanical of Dallas looked to alternative piping systems for a solution. They found PEX-a pipe with F1960 expansion connections to be the ideal system, due to its durability and ease of installation in addition to the job-site productivity, safety and, best of all, profitability potential it provided.
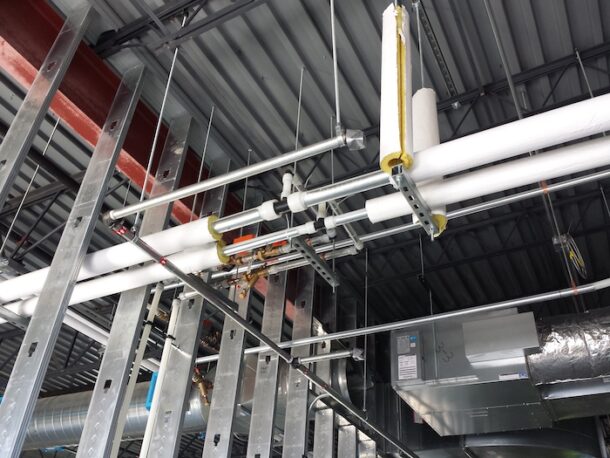
And City Wide Mechanical isn’t alone in their findings. Many mechanical contractors are discovering the benefits of PEX-a pipe and F1960 connections as the preferred alternative to copper, iron, and steel, which have dominated the mechanical piping industry for decades.
Benefits of PEX-a
PEX is an acronym for crosslinked polyethylene. It has been used in North America since the mid-1980s, starting with radiant floor heating systems, then moving into plumbing and, eventually, to hydronic hot-water heating and chilled-water applications.
PEX can be manufactured via three different processes, which create products with varying crosslinking percentages that allow for different characteristics. PEX-a is the most durable, flexible, and resilient with crosslinking around 85%. PEX-b is a stiffer piping product with crosslinking around 65% to 70%, and PEX-c features crosslinking around 70% to 75%.
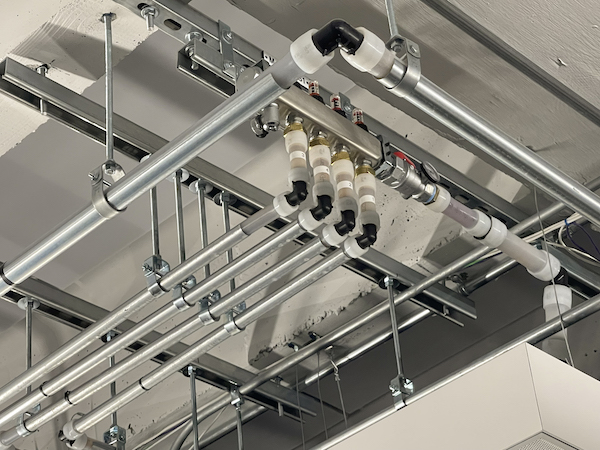
ASHRAE Headquarters Grand Opening Fall 2021, photos by Devin Abellon
One major benefit of the higher crosslinking in PEX-a is its extreme flexibility along with its thermal and shape memory. The flexibility of PEX-a eliminates most connections in smaller-diameter piping, saving time and money with up to half the connections required in rigid metal piping systems. To make a change in direction, the installer simply bends the pipe instead of having to stop and make a fitting. There are also bend supports available that help hold a bend securely in place.
The thermal memory of PEX-a provides kink repairability with a simple shot of heat from a heat gun. This eliminates the need to add in a coupling if a kink ever occurs in the pipe. (It is important to note that kink repairability is not possible with PEX-b or PEX-c pipe.)
The shape memory of PEX-a allows the pipe to expand and contract back down to its original shape. This makes it extremely resilient in freezing conditions and also provides for the fastest, easiest, most reliable PEX-a fitting system — F1960 expansions.
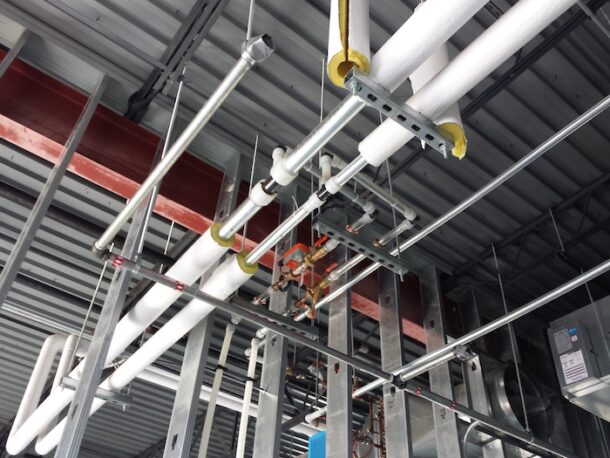
Expansion fittings require one simple tool to expand the pipe and an expansion ring before inserting a fitting. As the pipe and expansion ring naturally shrink back to their original shape, it creates a strong, durable connection that holds tight and can never be dry-fit. (Note: It is not recommended to expand PEX-b or PEX-c pipe due to microcracking that can occur.)
The innovative expansion fitting method eliminates torches, glues, and solder from a job site for greater worker safety. Plus, the system is extremely easy for installers to learn, helping get new crews up to speed quickly.
Speaking of job-site safety, PEX is also much lighter in weight compared with metal systems. For example, a 300-foot coil of 1/2-inch PEX weighs about 18 pounds, whereas the same amount of copper pipe weighs around 85 pounds. The lighter weight of PEX makes it safer and easier for installers to move around a job site and also eliminates the need for heavy-lifting equipment.
PEX-a also has a long-term advantage over copper when it comes to performance longevity. It is a static system, meaning its internal surfaces — which are three times smoother than copper — will not pit, scale, or corrode. That means its performance will remain the same from day one through decades of use.
Finally, because it is not a traded commodity, PEX-a holds a relatively stable material cost. This makes bidding a project much more consistent and reliable.
Application Details and Installation Tips
PEX-a is regulated by the ASTM F876 standard, which denotes temperature and pressure ratings of 200°F at 80 psi (pounds per square inch), 180°F at 100 psi, and 73.4°F at 160 psi. These values are well within the range of operation for most hydronic systems, including chilled beams, fan coil units, baseboards, radiators, hydronic VAV (variable-air volume) reheat coils, and radiant manifolds.
Because PEX is oxygen-permeable, it is important to use a pipe with an oxygen barrier that limits oxygen diffusion to levels below DIN 4726. This will protect the metallic components in the mechanical piping system, such as valves, strainers, and pump volutes, from corrosion.
The pipe is manufactured in sizes from 5/16 inch up to 4 inches and features a copper tube size (CTS) outside diameter. This means all the off-the-shelf components used in a copper hydronic piping system — hangers, supports, and insulation — can be the same.
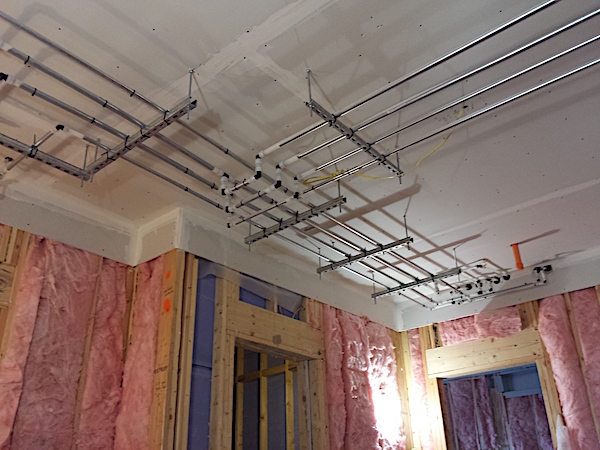
For horizontal piping, the industry offers PEX-a Pipe Support — a galvanized-steel channel that is 9 feet in length and available in PEX pipe sizes from ½ inch to 3½ inches. This solution enables hanger spacing similar to copper pipe and helps control the natural expansion and contraction of the pipe as it heats and cools.
Because PEX-a expands at 1.1 inches per 100 feet per 10°F Delta T (which is 10 times that of copper), installing anchors every 65 feet and using PEX-a Pipe Supports allows PEX-a to function much like a copper system. In fact, different installation methods have a different effect on the overall net expansion rate.
With a strut-and-clamp system, using PEX-a Pipe Supports and anchoring with fixed points reduces the expansion rate of PEX-a to 0.08 inches per 100 feet per 10°F Delta T (a rate less than copper). And a loop-and-clevis system can reduce the rate to 0.12 inches per 100 feet per 10°F Delta T.
If you’d like to learn more about PEX-a piping systems, visit the Plastics Pipe Institute at plasticpipe.org or the Plastic Pipe and Fittings Association at ppfahome.org.
Aaron Stotko is the director of Segment Marketing at Uponor. He can be reached at aaron.stotko@uponor.com.