https://vimeo.com/1074098129 On this Weekly Update—April 11, 2025, we talk tariffs, a visit with American Plumber Stories while some plumbers prepare for a turkey hunt and we visit with our friends at InSinkErator Read more
Featured Articles
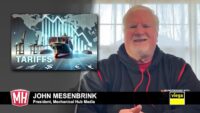
On this Weekly Update—April 11, 2025, we talk tariffs, a visit with American Plumber Stories while some plumbers prepare for a turkey hunt and we visit with our friends at InSinkErator.
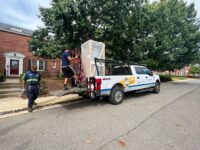
For nearly 20 years, the State Water Heaters Ultra Force (SUF) commercial water heater served an Arlington, Virginia apartment complex well. When it came time to replace the unit, the building owners turned back to State for a brand-new SUF unit. The previous unit provided ample hot water for bathrooms, kitchens, laundry facilities and more to Read more
For nearly 20 years, the State Water Heaters Ultra Force (SUF) commercial water heater served an Arlington, Virginia apartment complex well. When it came time to replace the unit, the building owners turned back to State for a brand-new SUF unit. The previous unit provided ample hot water for bathrooms, kitchens, laundry facilities and more to 28 units over the last 18 years, so it was an easy decision to stick with the State Ultra Force unit.
“This unit is warrantied for three years, so to see this unit last for close to 20 years is truly astonishing,” said Matt Baranuk, A. O. Smith commercial segment development leader. “The longevity of this unit is a testament to State’s legacy of lasting durability and the high quality of our water heating technology. We’re thrilled that the unit performed so well that they decided to do a like-for-like replacement. We’re confident that the new unit will meet their needs for many years to come.”
It is anticipated that by 2026, the U.S. Department of Energy (DOE) will require all commercial water heating units to have condensing technology. Users can install the SUF commercial water heater knowing it will not only possess high-level performance thanks to cutting-edge features designed for optimal performance but also will meet local and national regulations as they continue to evolve.
Beyond this, new features offer numerous benefits for contractors and users alike. The components inside the units are durable and made to last. With a corrosion-resistant tank, the unit will withstand the test of time. The iCOMM™ Connectivity Platform also provides users with detailed diagnostic fault notifications, allowing building managers to quickly schedule maintenance as needed. The platform allows for control of the set point and differential directly from a smartphone.
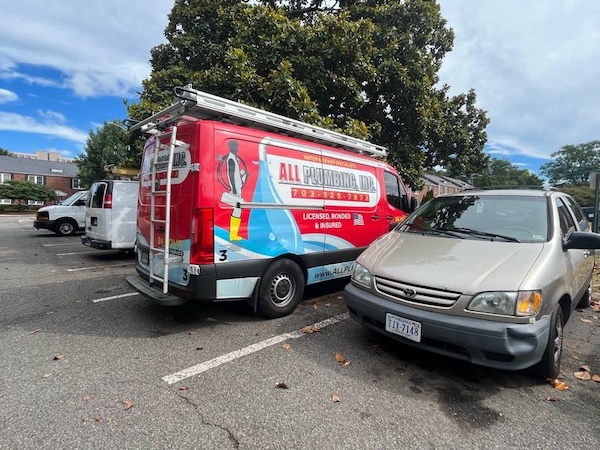
“When there is only one unit powering the entire complex, it’s essential that the unit performs well consistently, which is why we recommended sticking with the State Ultra Force water heater for this installation,” said Patrick Fulford, Ferguson manager.“Our unique 24/7 Commercial Water Heater Express Response service empowered us to replace the unit with minimal disruptions to the hot water supply. Through this service, customers in select cities can contact Ferguson for a last-minute replacement and we deliver the water heater within two hours, day or night. Along with delivery, we haul away the old unit and place the new water heater where it will be installed.”
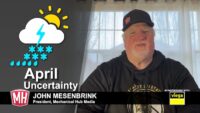
https://vimeo.com/1071965170 On this week’s Mechanical Hub weekly update, we talk about the unpredictability of the weather, Utah’s Fluoride ban in drinking water, April Fool’s jokes, a visit with our friends from Viega and the Appetite for Construction podcast, which features Jorge Arias, vocational plumbing instructor at the Correctional Training Facility (CTF) Soledad State Prison in Read more
On this week’s Mechanical Hub weekly update, we talk about the unpredictability of the weather, Utah’s Fluoride ban in drinking water, April Fool’s jokes, a visit with our friends from Viega and the Appetite for Construction podcast, which features Jorge Arias, vocational plumbing instructor at the Correctional Training Facility (CTF) Soledad State Prison in California.

https://vimeo.com/1070103550 Did you know that on this date in 1979, the infamous Three Mile Island accident occurred, which was a partial meltdown of the Unit 2 reactor of the Three Mile Island Nuclear Generating Station, located on the Susquehanna River near Harrisburg, Pennsylvania. It is the worst accident in U.S. commercial nuclear power plant history Read more
Did you know that on this date in 1979, the infamous Three Mile Island accident occurred, which was a partial meltdown of the Unit 2 reactor of the Three Mile Island Nuclear Generating Station, located on the Susquehanna River near Harrisburg, Pennsylvania. It is the worst accident in U.S. commercial nuclear power plant history? |
Illinois’ Top Apprentices Showcase Elite Skills at Statewide Competition
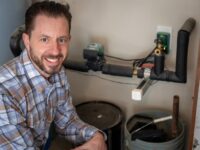
“I’m paying attention to the specifications of the planet,” said Bryan Uhler, second-generation builder, YouTuber and Instagram influencer. Long-term quality and conservation within the building trade are calling cards for Pioneer Builders Inc., which Bryan’s father, Tim Sr., founded in Port Orchard, Wash., nearly 50 years ago. Today, Bryan serves as vice president of the Read more
“I’m paying attention to the specifications of the planet,” said Bryan Uhler, second-generation builder, YouTuber and Instagram influencer.
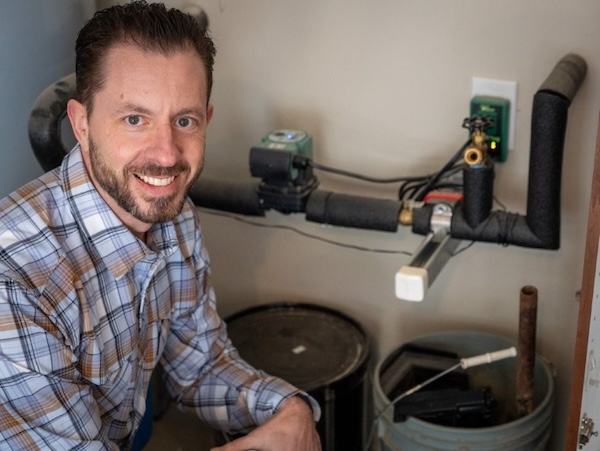
Long-term quality and conservation within the building trade are calling cards for Pioneer Builders Inc., which Bryan’s father, Tim Sr., founded in Port Orchard, Wash., nearly 50 years ago. Today, Bryan serves as vice president of the company. His brother, Tim Jr., is lead carpenter.
Their father remains involved as an advisor, and the third generation is beginning to take shape. Bryan’s son, Ethan, helps with digital content production.
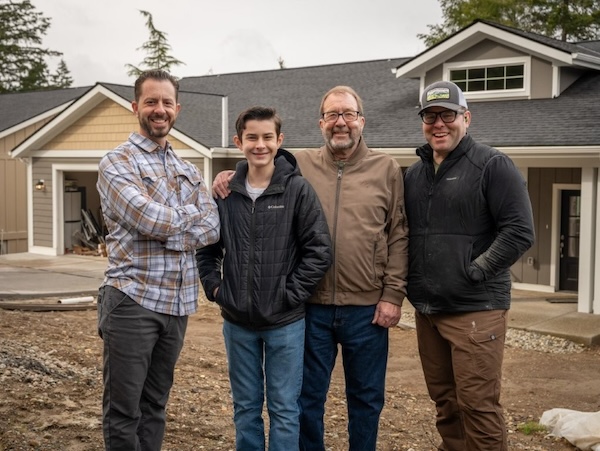
From l to r: Bryan, Ethan, Tim Sr. and Tim Jr.
In addition to handling land acquisitions, project development, permitting, sales, job costing, and payroll, Bryan emphasizes constructing homes with a strong emphasis on conservation.
While the company constructs spec homes almost exclusively, it has also built all variety of custom and pre-sale homes. Over the years, Pioneer’s emphasis on efficiency and green building technologies has outpaced Washington state’s stringent energy code, which is one of the strictest in the nation.
Taking the Next Step
“In 2024, we made a commitment to construct Zero Energy Ready homes,” said Uhler. “This is a certification through the Department of Energy (DOE) for homes built to a rigorous set of requirements, providing high levels of energy conservation, comfort, health and durability. Through the Inflation Reduction Act, homes built to this standard can qualify for the 45L tax credit worth $5,000.”
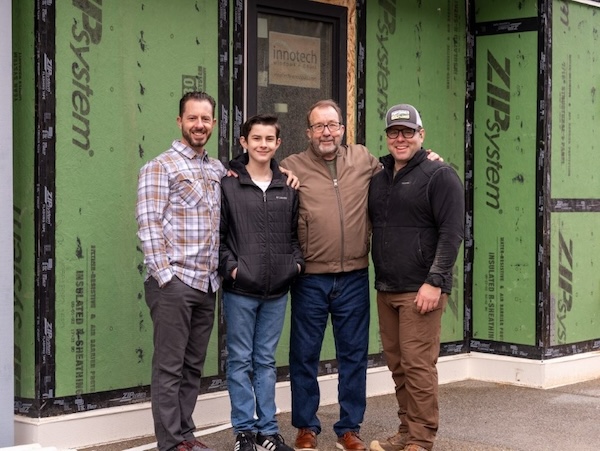
The goal behind Zero Energy Ready homes is to provide residences that are so efficient, a renewable energy source could offset the home’s power consumption. All of Pioneer’s spec homes are also ENERGY STAR certified.
As important as energy conservation is, the recent fires in southern California are the latest reminder that water conservation may soon be the nation’s greatest challenges.
Concentrating on Water Conservation
“Conserving water is as big an environmental concern as reducing energy consumption,” said Bryan. “If you curb domestic hot water use, you achieve both.”
For years, Pioneer Builders has specified water-conserving fixtures. They use Gerber’s line of faucets, toilets and shower heads.
“With properly designed equipment, the homeowner can reduce household water consumption without sacrificing comfort or even being aware of the fact that they’ve reduced water use,” said Bryan.
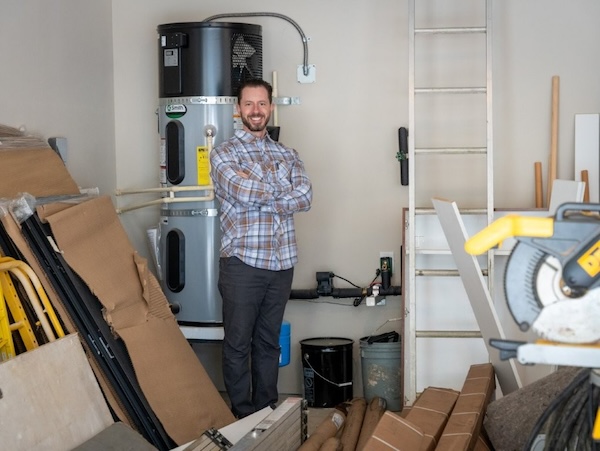
Bryan Uhler displays how Pioneer Builders pairs a heat pump water heater with Taco’s SmartPlus-e recirculation system.
This principle is carried into the mechanical room, where Pioneer Builders partners with Herdman Plumbing. Heat pump water heaters are used in all Pioneer’s homes. While this provides energy savings and eliminates on-site fossil fuel consumption, it does present one challenge.
“Our homes feature domestic hot water circulation, which saves a great deal of potable water, not to mention increasing the comfort level,” said Bryan. “The issue is that heat pump water heaters and conventional DHW recirculation systems don’t play well together. I’m willing to admit that we’ve done everything wrong at least once, and this is no exception.”
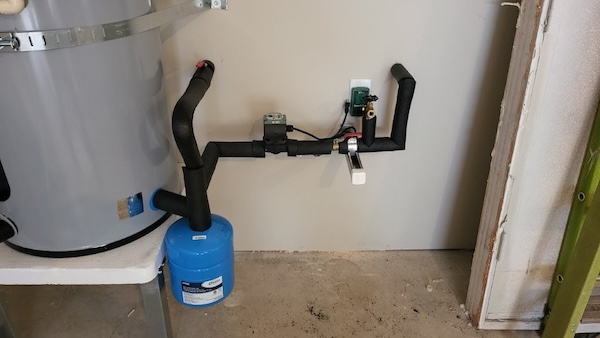
By using the Taco SmartPlus-e, Pioneer Builders avoids the pitfalls caused by pairing a heat pump water heater with a DHW recirculation pump.
The number one issue when pairing these two technologies is that a DHW recirculation system that runs continuously tends to disrupt stratification within the water heater. Recirculation lines, even when properly insulated, also shed heat while circulating, causing the heater to recover when the cooler water returns to the tank.
This often causes the heater to operate when there isn’t a call for DHW or switch the unit from heat pump mode to electric resistance backup. Not all recirculation pumps are created equally. Some pumps – specifically those that don’t feature ECM motors – are inefficient, and this raises the HERS rating. That’s a bad thing for an energy conscious contractor.
“I didn’t know there was a solution until Eric Aune from Mechanical-Hub suggested I look at Taco’s SmartPlus-e recirculation system,” said Bryan. “He explained that the system paired a small ECM circulator with a smart control, eliminating the problems caused by constant circulation. That’s a winning combination.”
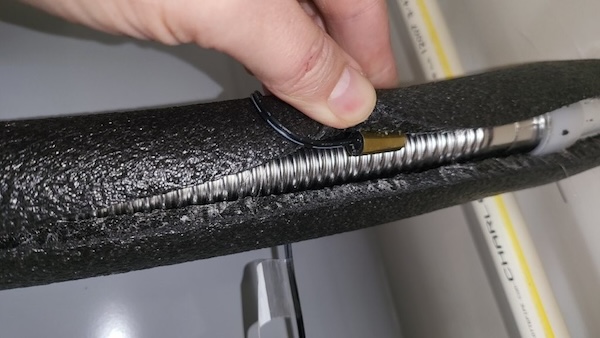
The recirculation system’s temperature sensor is installed under pipe insulation on the hot water supply line.
The SmartPlus-e includes two components, a 006e3 circulator and a SmartPlug control, which can be paired with any recirculation pump. The SmartPlug can operate in Pulse mode, which continuously cycles the pump on and off, or Smart mode. In Smart mode, the control records hot water use patterns in the home and only operates the pump according to those patterns.
“We’ve found that the SmartPlus-e system helps us hit some of the benchmarks needed to achieve ENERGY STAR certification,” Bryan shared. “Our projects range from around 2,500-4,000 square feet with about the bathrooms. With the water heater in the garage, the potential to save water and energy with a recirculation system is considerable.”
A Holistic Approach
Bryan makes it evident that creating a durable, healthy, energy efficient home can’t be achieved by selecting one or two energy-efficient products and adding a bit more insulation. It’s a holistic approach that begins in the design phase and continues through to educating the homeowner during the final walk-through.
One of the biggest changes Pioneer has made over the past decade, especially with the use of air-to-air heat pumps, is to bring the ductwork into the conditioned space. This saves a great deal of energy being lost to the attic.
Another improvement is the careful selection of building materials in the interest of indoor air quality. Natural materials like hardwood flooring and rockwool insulation reduce the VOCs in newly constructed homes.
“We insist that each of our homes provides comfort while actively contributing to the health of its occupants and the preservation of our environment,” said Bryan. “That typically means making a lot of little improvements to the built environment, rather than one big change.”
Check out Pioneer Builders at pioneerbuildersonline.com.