The Vanderbilt University Medical Center (VUMC) is one of the largest academic medical centers in the Southeast, managing more than two million patient visits each year. With its adult and children’s hospitals consistently ranked as one of U.S. News & World Report’s Best Hospitals, VUMC is the primary resource for specialty and primary care in Read more
Featured Articles
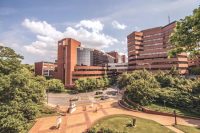
The Vanderbilt University Medical Center (VUMC) is one of the largest academic medical centers in the Southeast, managing more than two million patient visits each year. With its adult and children’s hospitals consistently ranked as one of U.S. News & World Report’s Best Hospitals, VUMC is the primary resource for specialty and primary care in hundreds of adult and pediatric specialties throughout Tennessee and the Mid-South.
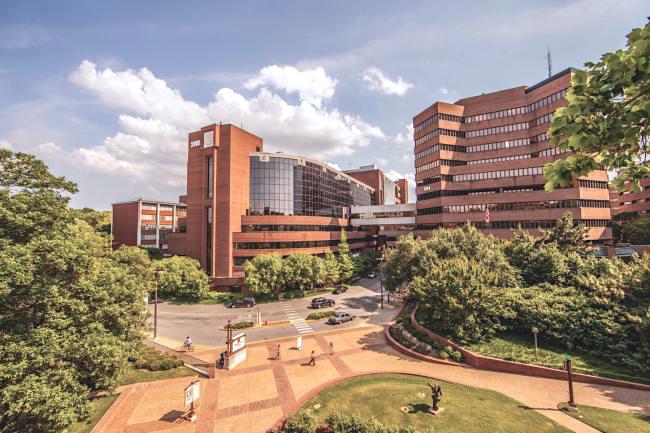
That’s why when it came time for VUMC to install new faucets, it needed a product that would help promote a hygiene-friendly handwashing process while standing up to high-traffic environments. VUMC also wanted a cutting-edge product that was easy to maintain while also enabling the facilities team to become smarter water managers.
Hospitals are a breeding ground for germs and disease, and Sloan’s Optima faucets help to promote proper hygiene with their touch free-application to cut down on cross-contamination. Installed throughout both public restrooms and nurses’ stations, the faucets improve the handwashing process for patients and caregivers alike. With 2 million annual patient visits in addition to on-site medical staff, Sloan’s faucets are subjected to plenty of wear and tear. The Optima faucets are not only durable enough to meet the demands of this high-traffic environment, but also deliver VUMC with sustainable water-saving benefits.
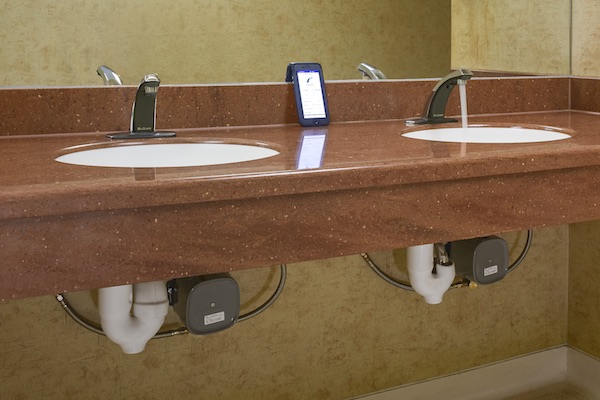
VUMC specified over 500 Sloan ETF-80 Optima® hardwired deck-mounted faucets as the new standard for the entire facility. Not only do Sloan’s redesigned faucets feature an underdeck Optima® Control Box that reduces the service time needed by VUMC’s facilities team, but the maintenance staff is also able to remotely monitor each individual faucet through the Sloan Connect App. Enabling the maintenance staff to adjust faucet settings without getting under the sink, the combination of state-of-the-art below-deck components and a mobile device on-site puts data right at the VUMC team’s fingertips.
The team conducts a weekly check-in to assess flow rates on specific fixtures throughout the facility and the data has allowed them to adjust flow rates accordingly. Thanks to the mobile application, VUMC’s staff is also able to adjust settings wirelessly, set faucet timeouts and measure and report water usage as needed. “Sloan’s faucets have proven to be very effective,” said Randy Howington, Plumbing Shop Manager at Vanderbilt University Medical Center. “They are high performing, and they have the ability to give us an understanding of how our faucets are performing at an exact moment.”
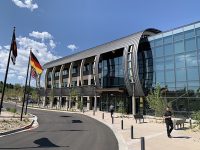
Recently, the Mechanical Hub team took part in a two-phase, two-state trip to visit Viega’s North American manufacturing in McPherson, Kansas, and toured the brand new HQ and Seminar Center in Broomfield, Colo. Impressive is the first thing that comes to mind when describing both facilities. The McPherson manufacturing facility exudes the company’s philosophy of Read more
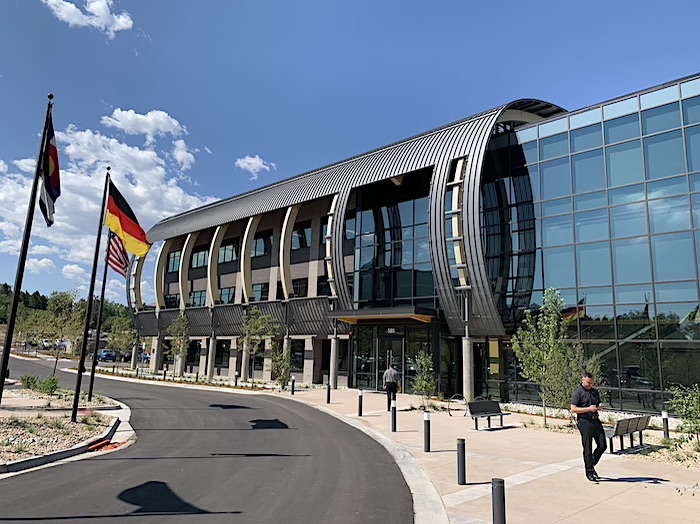
The new Viega North American headquarters in Broomfield, Colo., was designed to look like a fitting.
Recently, the Mechanical Hub team took part in a two-phase, two-state trip to visit Viega’s North American manufacturing in McPherson, Kansas, and toured the brand new HQ and Seminar Center in Broomfield, Colo. Impressive is the first thing that comes to mind when describing both facilities.
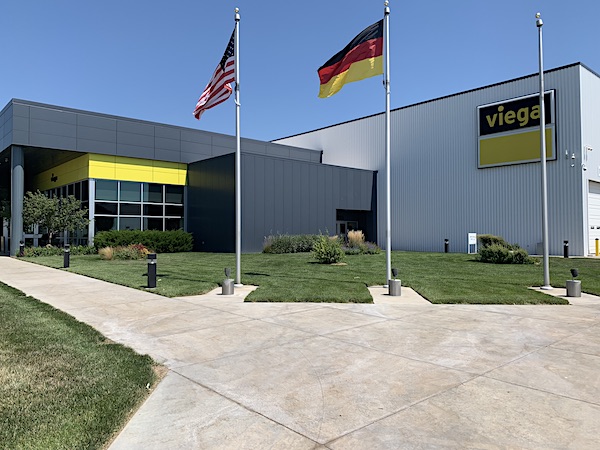
One of the Viega manufacturing facilities in McPherson, Kansas.
The McPherson manufacturing facility exudes the company’s philosophy of both progress and vision for the future. “We are constantly looking past the immediate future and into the distant future,” Eric Wicker, director, manufacturing, Viega.
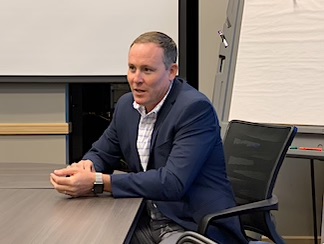
Eric Wicker, director, manufacturing, Viega
This summer, Viega completed a two-year building program in McPherson that included: a 90,000-sq. ft. expansion of a manufacturing plant, completed in Dec. 2017; a new 205,000-sq.-ft. manufacturing plant, completed in June; and a new 25,000-sq.-ft. tool shop and apprentice building, completed in July. And, the company is currently building a 55,000-sq.-ft. logistics expansion—a high-bay storage and retrieval area for inventory.
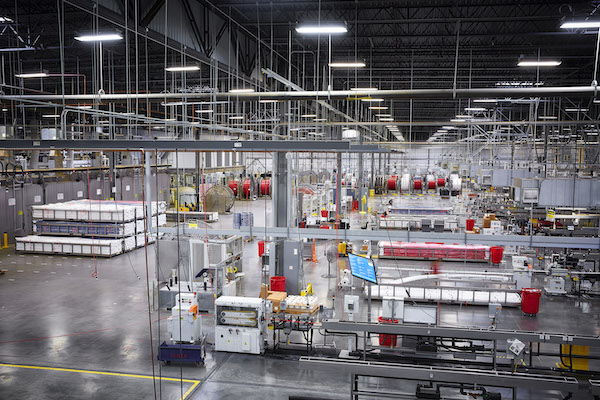
The manufacturing floor at the McPherson facility is as meticulous as it gets.
Mimicking some of the processes from its global HQ in Germany, robotics and machining take center stage throughout the meticulous McPherson plant. Fear not, all of this new-fangled technology is not taking jobs away, rather increasing them. Currently at approximately 300 employees, the company hopes to hit the 500 mark by years ’23-’24.
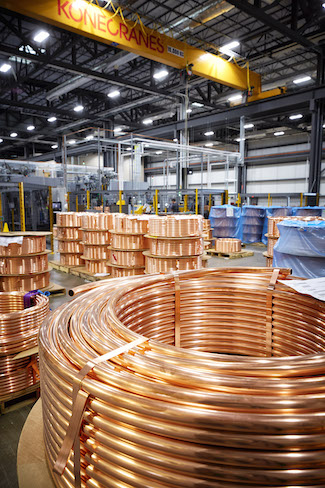
Some of the copper inventory, now produced in the states.
McPherson is where Viega produces its PureFlow line of PEX product, as well as select fittings from the ProPress Copper and 80,000 sq. ft. dedicated to its MegaPress product lines. McPherson is also home to Viega’s master distribution center for North America.
Continued expansion is a testament to the company’s progressive philosophy. For instance, the company has dedicated 270,000 sq. ft. to the copper fitting production. “The goal is to be producing the majority of copper fittings sold in the U.S. right here in the states,” says Wicker.
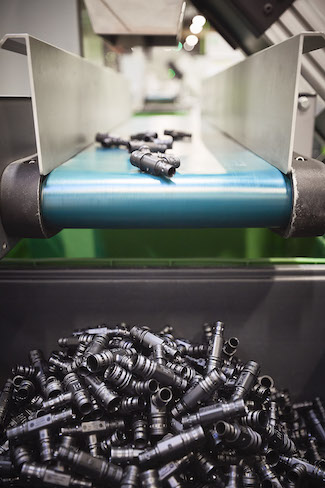
Plastic fittings rolling off the line. Seven million per month made in Kansas.
The state-of-the-art distribution center incorporates the latest technology and automation, as well as an upgraded warehouse management system that provides faster product turnaround. With additional metals products being manufactured in McPherson, a larger distribution center for both metals and PEX products was necessary.
Although media wasn’t allowed to shoot photography inside the plants—understandably—the tour started in the 36,000-sq.-ft. Plastic Injection Molding area which exemplified the company’s high investment in tooling. Twenty machines produce approximately seven million fittings per month. This particular building was well lit and comfortable, due, in part, by the implementation of its own radiant heating and cooling technology.
Quality is never understated at Viega; we strolled through the Quality Assurance Lab where dedicated staff monitor product and equipment through a series of rigorous testing.
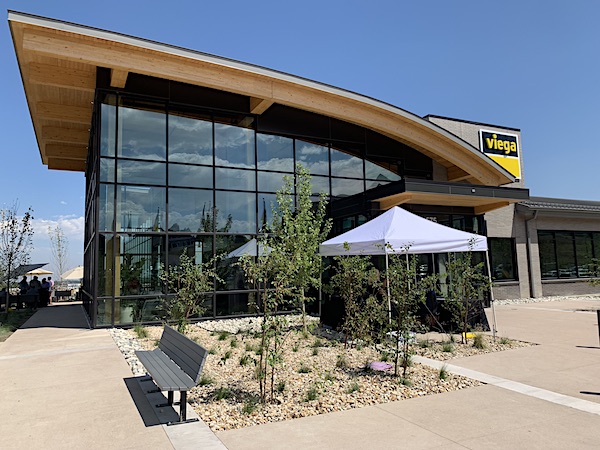
The Broomfield Seminar Center
Next, we toured the 200,000-sq.-ft. Extrusion Area where the plastic piping is made. Once made and exported from Georgia, Viega now produces its own resin—which is transformed into pellets—onsite. The rejected pellets are not repurposed, yet recycled and sold.
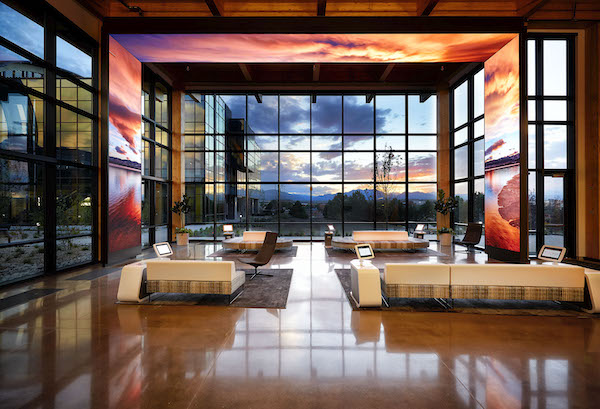
Whoa! Check out the beautiful seminar center, and the frickin’ view!
There is a Special Extrusion Area where plastic metal plastic tubing extrusion is performed. The only company in America making this, the plastic piping is integrated with aluminum so it can better hold its shape rather than returning back to its original form. (Nearby is a 40,000-sq.-ft. dedicated machine shop.)

Another angle of the entrance to the seminar center with the HQ in the background.
We then toured the 270,000 sq. ft. of ProPress copper fittings production area and 80,000 sq. ft. of the MegaPress/Metals production area. Strategically, it makes sense for Viega to start producing here in the states. With press technology introduced here in 1999, education and awareness of the process and technology have helped contractors nationwide run a more efficient business. Viega system solutions are designed to work together in plumbing, heating, cooling and pipe joining applications, making the contractor’s work fast, easy and safe.
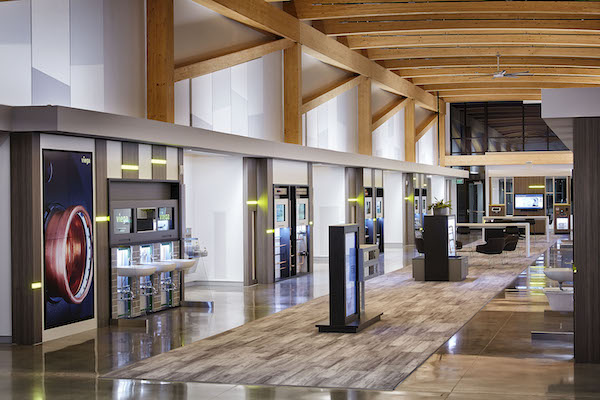
The seminar center features an interactive display area chock full of Viega products.
The following day we were flown to Denver to tour the recently opened Viega North American headquarters and Seminar Center in Broomfield, Colo. The 55,000-sq.-ft. headquarters resembles a pipe fitting, and its interior is the real testament to Viega innovation. I can’t express enough how beautiful these two buildings are, and, of course, amid the breathtaking backdrop of the Rocky Mountains. The HQ building opened in January and the first official training took place April 8, and weekly training is booking fast. “Viega is absolutely committed to its customers and their success in the field,” says Bo DeAngelo, manager, technical training at the center.
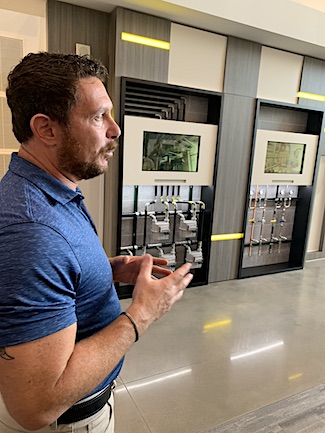
Like a proud new papa, Bo DeAngelo gives the tour of the new seminar center.
Yet, I am always interested: when a new facility is built, does it incorporate its own products? While the cross-laminated timber beams are imported from Austria, the exposed ceilings give employees and visitors a clear view of the many uses of Viega’s innovative technology.
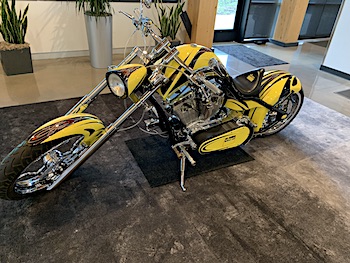
We’ve located the custom Viega chopper! It was taken in the middle of the night from the McPherson facility and relocated to Broomfield where it sits proudly on display. Who has the keys?
Potable water is carried through copper pipes connected with ProPress fittings. The carbon steel fire sprinkler system is joined with MegaPress fittings. Radiant heating and cooling keeps the building comfortable, while a snowmelt system keeps the courtyard free of ice and snow. Manifolds ensure the systems operate smoothly and efficiently. The restrooms feature wall-hung bowls and no exposed tanks, thanks to in-wall carrier systems and Visign style flush plates.
The new 23,000-sq.-ft. Broomfield Seminar Center next door supplements Viega’s Nashua, New Hampshire Seminar Center, which has trained thousands of people since opening in 2006. The new center is an innovative training experience and is equipped with four classrooms, two hands-on labs, and interactive displays throughout, which allows attendees to see, touch and experience Viega products. “Demand for training has been increasing steadily. This facility will allow us to continue to provide and expand on the training that our industry deserves,” says CEO Dave Garlow.
Viega experts lead single- and multi-day classes in everything from radiant system design and fire protection to hydronics and pathogen prevention. Despite being open only since April, it is on track to host more than 2,100 students this year, says DeAngelo.
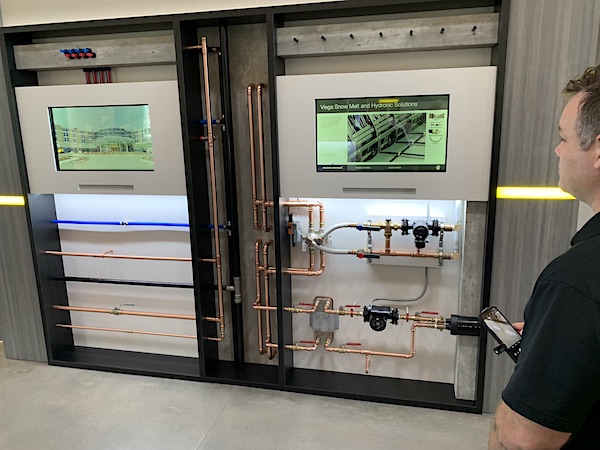
The Hub’s Eric Aune checks out the hydronics and snowmelt display.
I walked away very impressed, telling DeAngelo I—and I’m sure the clients that visit—can’t help but feel energized the minute I walk in this facility. Shaking his head in agreement, “That’s what Dave Garlow tells me every day he walks in here,” responded DeAngelo.
Make no mistake, there is a lot of money, time and resources invested in Viega North America. But it’s a huge testament to the dedication the company believes is its biggest investment: its customers and its employees.
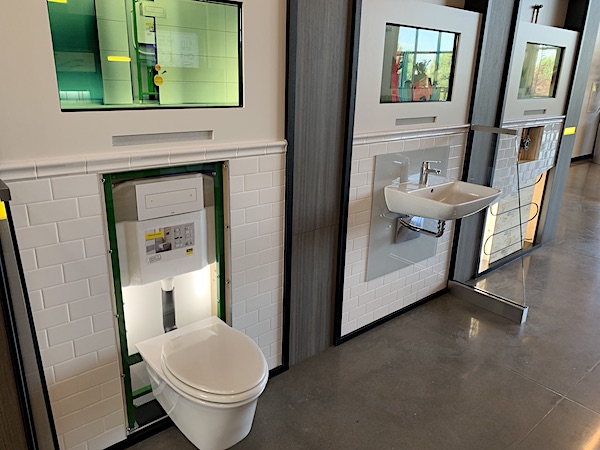
The interactive display at the Broomfield Seminar Center features a breadth of innovative Viega products.
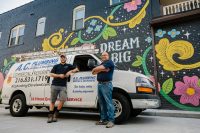
Family businesses work when everyone is invested in a common goal. Half-hearted efforts and attitudes, jealousy or near-sightedness are the kiss of death when parents, siblings and in-laws are involved. But when all are engaged and aligned fruitfully, the result can be an uncommonly strong enterprise with long-term potential. AC Plumbing, Heating & Mechanical in Read more
Family businesses work when everyone is invested in a common goal. Half-hearted efforts and attitudes, jealousy or near-sightedness are the kiss of death when parents, siblings and in-laws are involved.
But when all are engaged and aligned fruitfully, the result can be an uncommonly strong enterprise with long-term potential.
AC Plumbing, Heating & Mechanical in Cleveland, OH, seems to have written the handbook for success in family business, though that wasn’t initially the plan. Tony Caruso started the firm with his wife LuAnn, in 1980, while also serving as a professional fireman.
Today, their children operate the 14-person company in Bedford Heights, OH.
Daughter Monica runs the office and her husband, Kelly Miller, is head of the HVAC shop. Anthony, like his father, is a professional fireman and paramedic, working 24 hours on, 48 off. When he’s not on duty at the firehouse, he’s the lead hydronic technician. Michael, who has a construction management degree, is the company’s lead plumber.
Under their direction and Tony’s mentorship and guidance, the business has flourished.
“I never envisioned all of this with my children,” said Tony Caruso. “I didn’t plan for them to join the company, let alone see the potential for them to propel us forward. But I’ve always believed this profession was something special. Having them join me has been a tremendous source of pride.”
Today, the company’s reputation for outstanding craftsmanship is validated by long-standing customer relationships, both commercial and residential. Some of those clients haven’t changed since the early years, when LuAnn was still writing invoices from notes that Tony scratched in the firehouse breakroom.
As Tony takes a back seat to day-to-day operations, it has given him time for volunteer work, and to tackle personal projects.
Restoring antiquity
“I’m drawn to old things, especially mechanical in nature,” said Tony. “Volunteering at a historic railway has been rewarding, especially when I can involve my grandchildren. I love to bring things back to their proper vintage and grace; cabooses, automobiles, buildings, etc.”
In part to scratch an itch and partly as a long-term investment, Tony and LuAnn purchased a 100-year-old building near downtown Cleveland in 2017. The Detroit Avenue area is slowly experiencing a renaissance of sorts. Young people are moving back in, small businesses are cropping up, and property values are plodding patiently upward.
Caruso bought the old building as a rundown residence. Police were frequently called to the address for one sort of disturbance or another. But with plenty of vision and know how – not to mention the involvement of a team of mechanical technicians – Tony and LuAnn had other plans.
They’re just now finishing the details on the 5,000 square-foot building. An upscale salon and spa occupies the ground level, with floor-to-ceiling windows along the sidewalk. The upstairs is divided into two apartments, with a third being added behind the salon.
Half of the basement slab received a pebble finish called Natural Stone. No sooner had the top coat cured before water backed up into the basement.
“We thought we’d need to hammer out a part of the new floor to access a clog in the old porcelain plumbing, and install a drain at that spot,” said Caruso. “So we purchased a Watts Pronto!™ floor drain because of the ability to do post-pour adjustment between the concrete and finished floor.”
Then Michael and Zac Wood, one of the company’s plumbers, scoped the pipe. It became apparent that the clog could be remedied without digging up the floor. Jagged edges on the old cast iron pipe within a fitting were catching sewer debris. By snaking the pipe with a heavy cutter tip, the issue was remedied.
In an adjacent basement room without finished flooring, the building had a plumbing stack coming down from the first floor. It was no longer in use, and just in the way.
“We wanted to remove the stack for more storage space,” said Michael. “But in a building like this, where the use of occupied space can easily change in the future, we try not to eliminate sewer connections. We already had the Pronto! drain in the van. It’s a little overkill for an unfinished slab, but it definitely served the purpose.”
Zac hammered-out the floor, installed a new trap, then poured new concrete and installed the drain.
“The real benefit of the Pronto! floor drain is that the drain can be adjusted twice,” said Zac. “The basin can be raised or lowered to match the initial concrete pour, and then the strainer can be adjusted to match the finished floor grade. It comes with a set of shims to get a perfect level. On this installation, though, we only needed to make one adjustment. Using the drain’s integral bubble level, I was able to plumb-in the drain perfectly just by adjusting it after making my PVC connection.”
The Watts Pronto! floor drain is available in either cast iron or PVC, and comes in grate sizes of 5”, 6” or 8”.
“We’ve used a variety of Watts products since I started the company,” said Tony. “Our hydronic installations are covered in Watts valves, and we often use tekmar controls. We also like their backflow assemblies. We picked the Pronto! drain, despite it being a completely new product, based on the quality of products we’ve come to expect from the brand.”
With the plumbing issues resolved at the investment property, the Carusos can focus on finishing the final rental unit. The building is now an integral part of the Detroit Avenue urban revitalization effort, inside and out. Two walls on the building feature giant murals, a theme throughout the area. It’s another source of pride.
Doing right
“Not everyone at AC Plumbing is family, but they may as well be,” said Tony. “Every member of our team is vital. We hire people that want to provide service. That is, in my judgement, the finest pursuit. The responsibility to our team is never to do less than the right thing. That may include engineering the correct system, performing the proper replacement or repair, or taking responsibility for mistakes. Good business ethics.”
Tony’s quick to note that the industry and market is changing rapidly, and is thankful that his children are proactively keeping pace with it. Clients have become much more astute in regard to what they want in their homes. Systems are now “on demand,” “green” or otherwise designed primarily for comfort.
“The daily challenge we now face is installing a system that never compromises safety, comfort or efficiency,” Tony continued. “In years’ past, things were simpler, and efficiency wasn’t as critical. These factors have truly raised the bar on what it means to be a plumbing or HVAC professional. Fortunately, manufacturers and reps are providing more support than ever before.”
“I feel that being trusted in a customer’s home is the greatest responsibility,” Tony said. “As my career winds down, I feel that my family has that same passion. At the end of the day we can all rest knowing we’ve done what is dutifully right.”
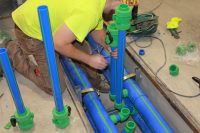
New process cooling system showcases flexibility, advantages of Aquatherm pipe It is often said that adversity builds character. But in some cases, it also helps build a better piping system. During a cold and snowy snap in the winter of 2017-2018, a combination of a heavy snowpack and high winds caused a portion of the Read more
New process cooling system showcases flexibility, advantages of Aquatherm pipe
It is often said that adversity builds character. But in some cases, it also helps build a better piping system.
During a cold and snowy snap in the winter of 2017-2018, a combination of a heavy snowpack and high winds caused a portion of the roof to collapse at the headquarters of IVP Plastics in Washington, Ill. Fortunately, no one was injured (the collapse took place on a Saturday), and the damage was somewhat mitigated by the presence of a crane rail running the length of the ceiling.
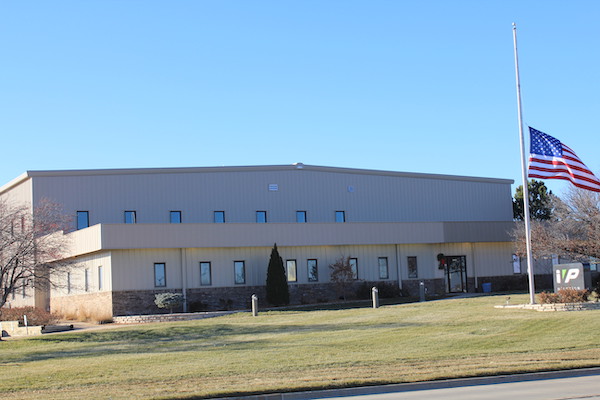
In the bigger picture, this bit of adversity wrought by Mother Nature served to introduce IVP Plastics to Aquatherm polypropylene pipe—and who better than a plastics manufacturing company to benefit from the advantages offered by Aquatherm piping?
Fateful Day Leads to New Conversations
IVP Plastics was founded in 1953 and today is a leading provider of customized plastic parts for the agricultural, heavy equipment, and automotive industries. The company’s services include consultation, design, prototyping, and material management, and its manufacturing capabilities include thermoplastic molding, injection molding, insert molding, in-mold labeling, and sonic welding. The company’s mission is to provide outstanding customer service based on three core values: innovation, value, and performance.
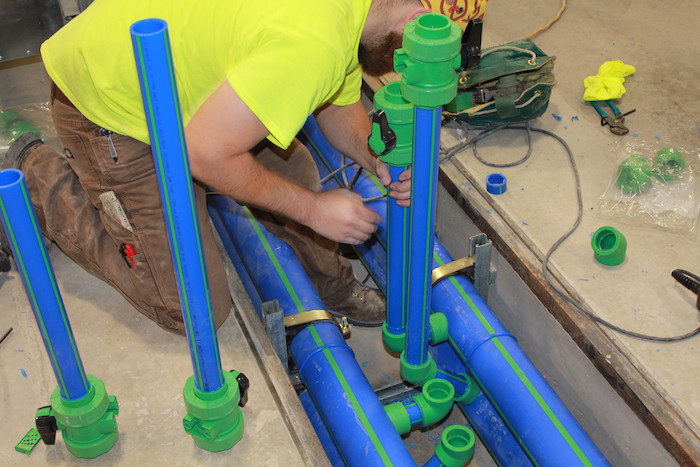
Aquatherm pipe being installed at IVP Plastics. The plant’s manufacturing machines may be moved into place and hooked up to the process cooling system as necessary.
Fate reared its head at IVP Plastics on the afternoon of March 24, 2018. Central Illinois’ winter weather can be notoriously brutal, and a late-season storm took its toll on the 20,000-sq-ft clear-span building. Although damage to the building itself was significant, the crane rail spared much of the manufacturing equipment from serious damage.
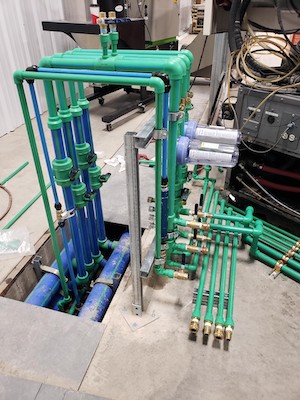
An underfloor trench system with above-floor fittings offers IVP Plastics the versatility they needed for their manufacturing processes.
About two weeks after the collapse, while a general contractor was still shoring up the building, Jeff Frieden, president of Warner Mechanical LLC, Edwards, IL, had an opportunity to visit the damaged manufacturing facility.
“We sat down with the IVP Plastics team, the general contractor, and the insurance company, and the bottom line was that time was of the essence,” Frieden said. “Another contractor had put together a temporary chiller system to keep them in production, but the long-term solution was to take the building down.”
Once the decision was made replace the damaged building with a new one, IVP Plastics requested that Warner Mechanical design the process piping system for the 16 machines that would be moving into the new building. The old process cooling system had used 6-in PVC pipe running overhead at the ceiling, and the company said it preferred a system that would place the pipe in mechanical trenches behind each run of machines.
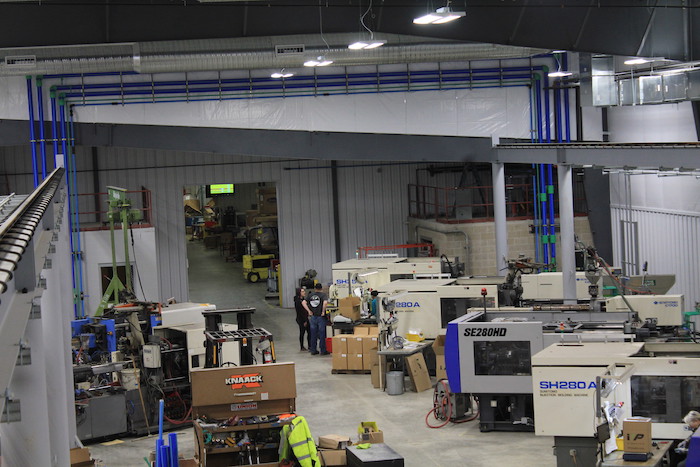
IVP Plastics provides customized plastic parts for the agricultural, heavy equipment, and automotive industries.
Frieden immediately knew Aquatherm would be a good choice for such a piping application, and IVP Plastics’ management agreed—not surprising for a company with a mission statement built on innovation, value, and performance.
Frieden turned to Warner Mechanical’s partner, Columbia Pipe and Supply Co., Peoria, Ill. Columbia supplied 1,575-ft of 4-in., 247-ft of 3-in., and 156-ft of 1 1/2-in. Aquatherm SDR-11 MF Blue Pipe for the process chiller piping, as well as 507-ft of 1-in. Aquatherm Green Pipe for clean-up water. Columbia also supplied the necessary fittings, flanges, fusion outlets, and transitions. Warner Mechanical owns the McElroy ½-in. to 4-in. fusion irons that were used on this project, but Columbia provides butt fusion tools for projects that require larger sizes.
“Columbia Pipe is very supportive of having all the tooling we need for projects,” Frieden noted. “We’ve never had to wait on tools.”
The joys of Leak-Free Performance
The system designed by Warner Mechanical, with support from Keith Engineering Design Inc., Peoria, Ill., calls for most of the pipe to be located in trenches under the equipment in the concrete floor of IVP Plastics’ new manufacturing facility. Fittings emerging from the trench covers allow the manufacturing machines to be easily hooked up whenever the process line is reconfigured. The company’s Budzar chiller provides 40°F cooling water to the machines, with return water flowing through the Aquatherm pipe at up to 100°F.
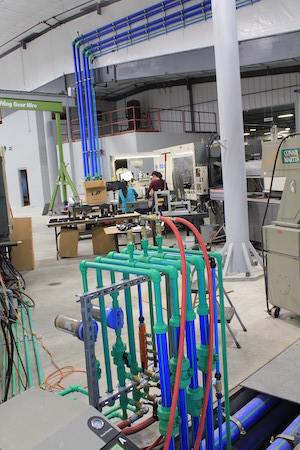
This project incorporated nearly 2,000 ft of Aquatherm Blue Pipe® for the process chiller piping, and 500 ft of Aquatherm Green Pipe.
“We decided to do things differently at the new facility,” explained Joe Camp, engineering manager, IVP Plastics. “We wanted to put the process plumbing in the floor and it was Jeff’s recommendation to use the Aquatherm pipe for that. It will be nice to not have pipes sweating and dripping, which was a problem when we had the PVC overhead.
“Another nice feature of the Aquatherm pipe was that we could get longer continuous lengths of pipe, so we had fewer joints to deal with,” Camp added.
The clincher for IVP Plastics, according to Camp, was Aquatherm’s virtually leak-fee performance that — because it was installed by Aquatherm-trained technicians—is backed by an extensive and comprehensive 10-year warranty.
“There is definitely peace of mind that comes from investing in a product with a warranty like that,” Camp said.
Colorful Pipe Draws Attention at Plastics Manufacturer
For Warner Mechanical, an undeniably interesting aspect of this project was installing Aquatherm pipe in a plastics manufacturing facility.
“As we discussed this project with IVP Plastics, the owners were very pleased to see the range of temperatures and pressure ratings that were available to them,” Frieden said. “After our initial conversations the owners researched it themselves and were very impressed by what they saw. When you’re working with a plastics company and they’re researching plastics, you’re playing with experts.”
Once the project began, the installation of the Aquatherm pipe attracted a great deal of attention from the IVP Plastics personnel.
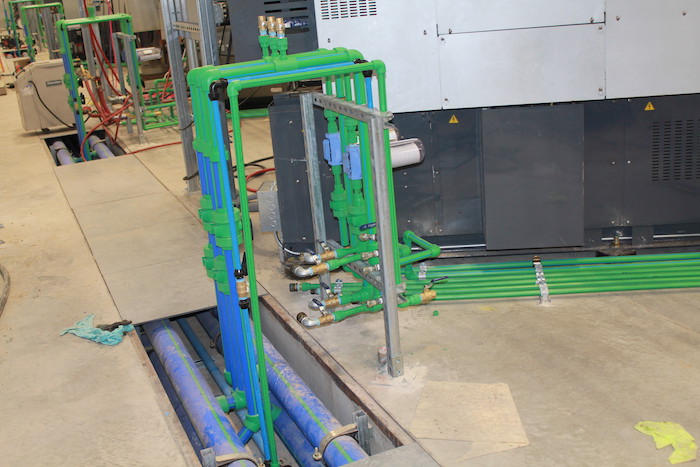
Aquatherm Blue Pipe® placed in a trench beneath the floor offers flexibility for this facility’s process cooling needs.
“The engineers were watching us put this in, and it really intrigued them—being a plastics company—that we were putting this thermoplastic piping in their building,” Frieden said. “The engineers liked the heat fusion process, and they all came out of their offices and took a peek. Some were familiar with solvent-weld types of plastic, but once they saw the benefits of the heat-fusion welding process they had total confidence in the durability of the product. They can understand when it’s properly heat-fused there will be no leakage problems.”
Camp agreed and noted one other benefit of the new piping system: it just flat-out looks good.
“Most of it is buried, but there are sections where it runs up a wall or transitions from one trench to another, and it’s got that nice pop of blue,” he said. “When we bring a guest or customer through they’re pretty impressed with it.”
Frieden added that Aquatherm was much easier to heat-fuse and place in the trenches than metal pipe would have been.
“I think any time you’re in a process where you would typically turn to welded piping, you should look at the time savings and durability of Aquatherm pipe,” he said. “For this customer, using Aquatherm enabled us to reduce the time it took to complete the system and allow the owner to start production.
“I also really think it’s a great choice any time you’re in a buried or constrained space,” he concluded. “It’s easier to work with than metal pipe and it offers a big advantage in peace of mind. You know you can walk away from it when the job’s complete and not worry about leaks.”
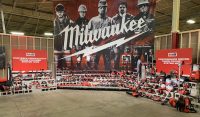
Milwaukee Tool is committed to providing end user solutions to the core trades—mechanical, electrical and plumbing (MEP)—and it was never more evident than at its latest #NPS19 event last month. Milwaukee’s commitment to the trades, and its company-wide goal to provide innovative solutions to the end user, is commendable. For example, the company has stressed Read more
Milwaukee Tool is committed to providing end user solutions to the core trades—mechanical, electrical and plumbing (MEP)—and it was never more evident than at its latest #NPS19 event last month. Milwaukee’s commitment to the trades, and its company-wide goal to provide innovative solutions to the end user, is commendable. For example, the company has stressed that you won’t see their logo on cars during NASCAR races or on outfield walls at professional baseball parks. “Our focus clearly is the trades. How do we develop products, how do we understand what the user does and how do we leverage the technology? We want to combine those points to deliver disruptive innovation by investing in people,” says Steve Richman, president, Milwaukee Tool.
And just wait: later this year the company plans huge announcements that will blow your mind.
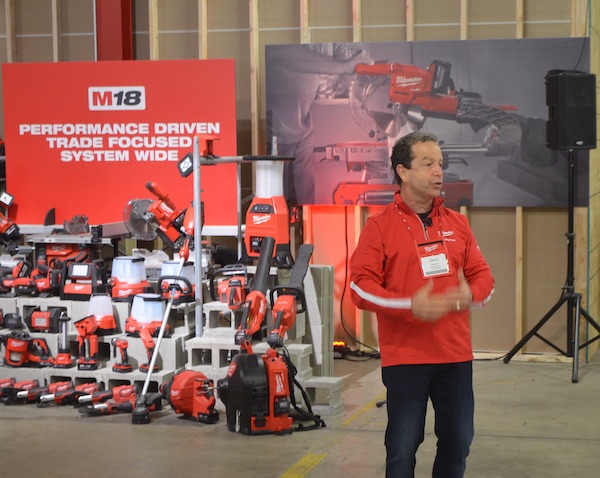
Steve Richman addresses the crowd at the #NPS19 event.
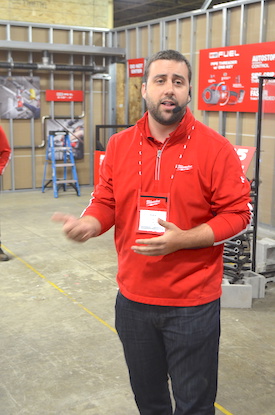
Alex Boll says that we are seeing the depth of Milwaukee Tool’s commitment to the plumbing and mechanical contractor.
During #NPS19—held at a former retail department store warehouse nearby—Milwaukee employees were ready for the “onslaught” of coverage from the more than 100 media and social media influencer attendees. The new tools stretched from the utility, carpentry, electrical fields, and, of course, “You are seeing the depth of Milwaukee Tool’s commitment to the plumbing and mechanical contractor,” said Alex Boll, senior product manager for Milwaukee Tool.
From the very first NPS event, Milwaukee has gone from 200+ people in its R&D headquarters to more than 1,500 today, and is quickly running out of space. Nonetheless, with double-digit growth over that past 10+ years, there is a palpable excitement throughout the company. “We are seeing 100 new products this year, experiencing another year of unbelievable growth, introducing more new products than any of our competitors in this space, and delivering the message that we are a solutions company,” said Richman.
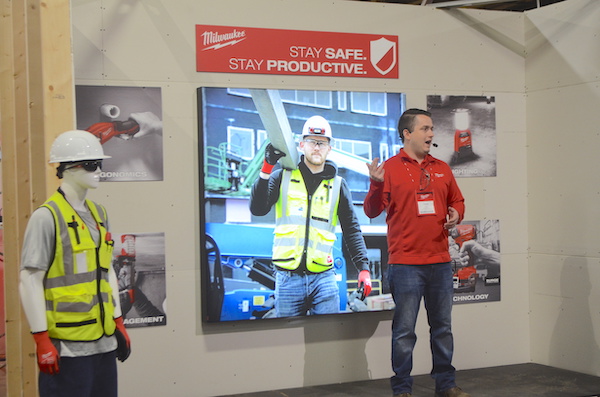
Milwaukee’s Derek Rose stresses the importance of user safety at this year’s #NPS19.
The message is clear: Milwaukee Tool wants to be known as a solutions provider first and foremost. “This is not about products, this is about solutions, and how we make the job safer and more productive every day,” said Richman. As a result, Milwaukee’s new tool lineup includes and increased emphasis on user safety, which includes equipment such as hard hats, safety glasses, safety vests, respirators, hearing protection and headlamps. “How do we partner users to be able to deliver solutions that drive productivity and safety on the job?” asks Richman.
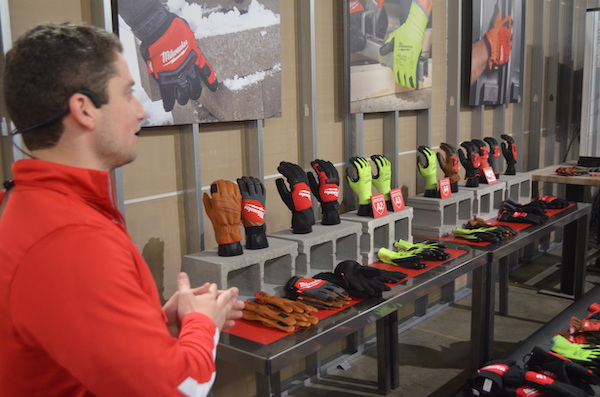
Milwaukee expands its line of gloves to now include more cut-resistant and winter gloves, as well as new lines of leather and impact-rated gloves. With these additions, they will offer a full line of hand protection that provides best-in-class comfort, dexterity, and durability for a variety of jobsite applications. September 2019
Here are some of the tool highlights from this year’s #NPS19 event:
• M18 FUEL Pipe Threader w/One-Key—Harnessing the power, performance and run-time delivered by M18 FUEL technology, the M18 FUEL Pipe Threader w/ONE-KEY revolutionizes the pipe threading process by delivering unprecedented control for the user. With AUTOSTOP technology, which senses severe kickback and automatically shuts the tool off, a dedicated support arm to hold the tool stationary during threading, and an integrated die head lock that enables side-grip thread starts, this new tool provides.
“The introduction of the first cordless pipe threader is a monumental achievement for the M18 System and a huge step forward in productivity for tradesmen,” said Boll. “Through our advanced M18 FUEL cordless technology, we’re able to deliver a cordless pipe threader that not only surpasses the speed of corded but does so while being lighter than the leading corded solution and offering unmatched control, simplifying the entire experience from start to finish.” Available on the market—July 2019.
• M18 FUEL 9″ Cut Off Saw w/ONE-KEY—The M18 FUEL 9″ Cut Off Saw continues to showcase the power of Milwaukee’s M18 system. With the power to cut reinforced concrete as well as all common metals, this saw is extremely versatile. At half the weight of most gas cut off saws it offers no gas headaches like dangerous emissions, difficult pull start, constantly mixing gas and oil, engine maintenance, and paying for fuel. Overall, this saw gives users a much better experience on the job. October 2019
• M18 Radio + Charger w/PACKOUT Compatibility—The extremely popular PACKOUT Modular Storage System has some added wrinkles. The new M18 Radio + Charger w/PACKOUT compatibility delivers the quality sound quality and functionality. A 10-speaker system provides users with 360° sound with the loudest volume and deepest bass that the jobsite has seen. Full compatibility with the PACKOUT system assures that users can easily transport their tools and audio on and off the jobsite. This new radio/charger accepts and charges all M18TM batteries and stores mobile devices. November 2019
• PACKOUT Dolly—Constructed with impact resistant polymer, the PACKOUT Dolly provides users with a convenient way to transport their tools and equipment throughout the jobsite. Its smooth roll wheels allow the Dolly to easily roll with a heavy load up to 250 lbs, while a QUICKSTOP Loading Lever enables users to hold the Dolly in place when loading and unloading. July 2019
• M18 FUEL Sewer Sectional Machine w/Cable Drive—Expanding the offering within the drain cleaning category, Milwaukee launches the M18 FUEL Sewer Sectional Machine w/ CABLE DRIVE. The tool’s CABLE DRIVE technology provides the first Automatic Feed and Retract solution within sectional machines designed to reduce user strain when pulling back the cable from the pipe. The power to clear roots at 200 ft. with a cordless solution provides users the power they need to clear tough clogs with the easiest set up and transport allowing users to work with less hassles. Available on the Market—November 2019.
• IPS XL Rings & PEX Jaw Expansion—The 2-1/2”–4” IPS XL Ring Kit fits directly in the M18TM FORCE LOGIC Long Throw Press Tools and gives it the ability to press Viega MegaPress XL Fittings without the use of cumbersome tool extensions, while vastly expanding the range of applications the tool can accomplish. “With the addition of these jaws mechanical contractors can now make controlled, flameless connections on 2-1/2”– 4” Schedule 10 to Schedule 40 Black Iron Pipe with the very same tool they use for pressing copper, PEX, and stainless-steel. We’ve just reset the standard for productivity in large steel pipe installation,” said Boll. May 2019
• M18 FUEL SUPER HAWG—Milwaukee Tool delivers the industry’s first right-angle drill with the power to fully replace corded. Designed from the ground-up with an upgraded POWERSTATE Brushless Motor and optimized REDLINK PLUS electronics, the new M18 FUEL SUPER HAWG has the power to drill 6-1/4” holes through 6” beam at corded speed, as well as the run-time to complete single home rough-ins. July 2019
• M18 Utility Remote Control Search Light—The M18 Utility Remote Control Search Light’s magnetic base allows it to be used in alleys, backyards, or mounted directly to the vehicle. With 5,000 lumens of TRUEVIEW High Output light, it boasts a spot distance of more than 1250 yards for more visibility during night work. An easy-to-use joystick remote control provides users with more control. Rated for outdoor use with impact and vibration resistance. October 2019