Homeowner’s Mid-January Crisis Resolved by New Jersey Contractor Surprisingly warm temperatures greeted residents of Mid-Atlantic states In the middle of January. For people living in the area who typically face freezing temperatures, severe nor’easter snowstorms, and perilous ice storms, temperatures ranging from the mid-30s to low-40s without precipitation was almost a best-case scenario for the Read more
Featured
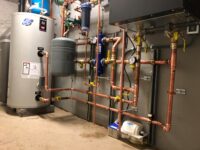
Homeowner’s Mid-January Crisis Resolved by New Jersey Contractor
Surprisingly warm temperatures greeted residents of Mid-Atlantic states In the middle of January. For people living in the area who typically face freezing temperatures, severe nor’easter snowstorms, and perilous ice storms, temperatures ranging from the mid-30s to low-40s without precipitation was almost a best-case scenario for the residents’ safety – and thermal comfort.
Despite the mild atmospheric conditions that occurred last January, homeowners who have a malfunctioning boiler, even in tranquil weather, may unexpectedly find themselves in a catastrophe at home. This was the situation a homeowner from New Jersey faced when the heating unit of a century-old home stopped working, causing the residents to shiver as evening temperatures approached the freezing point.
Ezzy Travis, a plumbing and heating contractor and solo proprietor of E. Travis Mechanical installed a HTP ELU 150K BTU boiler to substitute the feeble and inefficient one. Four days without heat or water might not seem like a lot, but can seem like an eternity for people living in the house.
“The boiler was only about 12 years old, but was not properly serviced,’’ Travis said. “With the amount of time it would’ve required to repair the boiler, it didn’t make sense. It also wasn’t piped 100 percent correctly.”
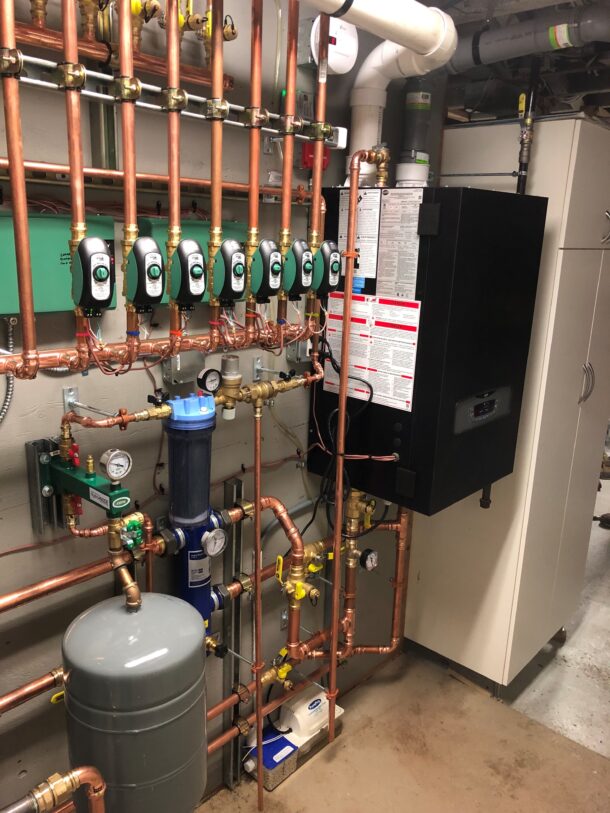
Workers from E. Travis Mechanical replaced the heating system in a century-old New Jersey home when the existing system failed during January, one of the coldest months of the year in the Garden State.
A Fresh Start
Prior to arriving at the home in the New Jersey neighborhood of Glen Rock, Travis had already fixed other home heating emergencies. Upon assessing the situation, he recognized the project required extensive repairs, rather than a short-term solution.
“A wholesaler referred this project to me,’’ Travis said. “I knew right away we’d have to replace the boiler and all the piping. Things weren’t done 100 percent correctly, and I have a standard way of doing things. All the piping in the mechanical room and the boiler had to be ripped out. The only thing that was salvageable was the indirect tank. It had been installed in August, so there was no reason to rip it out.”
Constructed in 1916, the traditional house features four bedrooms and three baths, in a 3,200 square feet area. Despite the house being quite expansive, the mechanical room’s workspace did not have the same luxury.
“That was probably the biggest challenge we faced,’’ he said. “It wasn’t a deep mechanical room. There just wasn’t a lot of room for two of us. I needed another set of hands for this one. We had to ask each other to move out of the way when we had to move within the room. It was a pretty tight squeeze with some significant space constraints.”
Contractors often encounter working areas that are cramped like a sardine can. “It’s weird because many times when you need space, you don’t have it,’’ Travis said. “Other times we’ll install something that is relatively small, and we have all the space in the world. A lot of my jobs are in areas where everybody wants to utilize every square inch of the basement. I’ll have to spend time putting down protective material for the carpet and wall, which makes it take longer. I don’t want to do any damage to the house.”
Navigating tight staircases with burdensome boilers is a risk that contractors frequently experience. When setting up the new boiler to replace the faulty one, Travis and his helper maneuvered carefully as they removed the old unit and installed the new one.
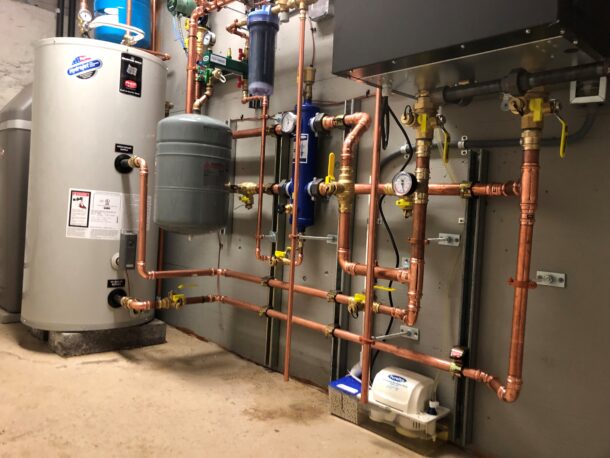
The project included the installation of an HTP ELU 150K boiler, which was selected for its durability and 11:1 turndown ratio.
Turning Up the Heat
Finding the appropriate boiler is key for a project in an old home with many rooms and floors. Contractors must consider that houses with compromised insulation and large square feet make the selection even more important.
“I had to factor in the heat loss of the house,’’ Travis said. “In this part of New Jersey, we see a lot of houses like that. In a hydronic system, you need to do thorough heat loss analysis. I wanted to make sure that the unit we installed was able to overcome any heat loss within the house.”
The high BTU output the HTP boiler provides was the deciding factor in Travis’ choice. “I also liked the fact that it had a 11:1 turndown ratio,’’ Travis said. “I like the simplicity of it. It’s not a complicated boiler. Because of the age of the house, I was also concerned about heat loss. I wanted to make sure we had enough BTUs to heat the entire house.”
In nearly all residential heating systems, the 11:1 ratio is a significant factor to consider. Whenever a boiler or burner finishes a cycle, it uses a substantial amount of energy. Reducing the amount of complete on and off cycles by utilizing a higher turndown ratio can minimize inefficiencies, resulting in lower maintenance costs. Additionally, high turndown burners are capable of responding more rapidly to changes in demand.
The HTP units – offered in sizes from 85K BTU input and all the way up to 199K BTU input – feature high-quality stainless-steel heat exchangers that guarantees the highest quality at the boiler’s core with corrosion resistance. The amplification in water flow provided by the heat exchanger results in increased turbulence that helps scrub the internal walls, thus reducing the accumulation of hazardous deposits.
“I liked the simplicity of this boiler,’’ Travis said. “There are not a lot of moving parts and it’s pretty uncomplicated.”
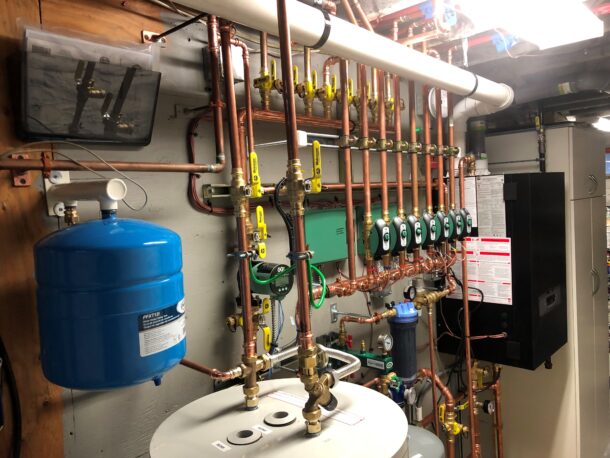
The HTP ELU boiler includes a Wi-Fi solution that enables remote monitoring and notifies personnel when faults occur in the system.
Linked Together
With the help of HTP link technology, the HTP ELU boiler offers a Wi-Fi solution for remote observation and alerts staff in the instance of a system fault. The boiler’s settings can also be conveniently adjusted on location without getting up from the chair.
During his 20-plus years in the industry, Travis has suggested HTP units for several projects. “I like their efficiency, durability and simplicity,’’ he said. “I get a lot of support when I’m installing them. They’ve been a good product for me over the years.”
Despite primarily being a one-man team, Travis takes pride in resolving significant or minor issues for all his clients. “I don’t feel like I’m doing anything special,’’ he said. “I’m just doing what I do. Fortunately, we were able to come up with a good solution for this rather quickly. It’s never a good thing for a homeowner to be without heat in the middle of winter.”
Brian Giardina writes on building, construction, engineering and other trade industry topics for publications throughout the United States.
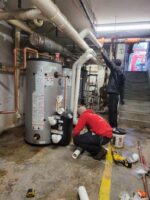
Peak Season Plumbing Problem During winter, not having hot water can be an aggravating experience for any homeowner. But if a hotel owner must deal with hot water interruption during the holiday season, the issue becomes much more disruptive and severe. A hotel in the Philadelphia area with 88 rooms faced this problem just before Read more
Peak Season Plumbing Problem
During winter, not having hot water can be an aggravating experience for any homeowner. But if a hotel owner must deal with hot water interruption during the holiday season, the issue becomes much more disruptive and severe.
A hotel in the Philadelphia area with 88 rooms faced this problem just before Christmas when its water heating system failed. Normally, plumbing contractors are used to emergency service requests, but with a snowstorm on the way, an increased number of guests and the holidays arriving, this situation required particularly quick action.
The team at Affordable Fixes Heating Cooling Plumbing completed the task by installing two HTP Phoenix tanks, with each holding a capacity of 119 gallons and 199K BTU respectively. Tackling this task required the team to remove four faulty water heaters that were leaking and generating carbon monoxide in the building.
“There are always challenges but replacing four and putting in two meant we had to put in a new exhaust, re-pipe the system, and re-do the electric units,’’ said Val Savkin, owner of Affordable Fixes Heating Cooling Plumbing. “It was supposed to be a one-day job. It took three, which was very efficient given the scope of the project.”
Due to prior communication with the building owner, Savkin knew the condition of the system. When he received a call shortly preceding he holiday season, he knew his help would be needed.
“This was an emergency project,’’ Savkin said. “The water heaters that had been in place had deteriorated. They couldn’t be repaired any longer. It was just wear and tear, they were outdated. Just two days before Christmas we were out there in the snow getting the project finalized.”
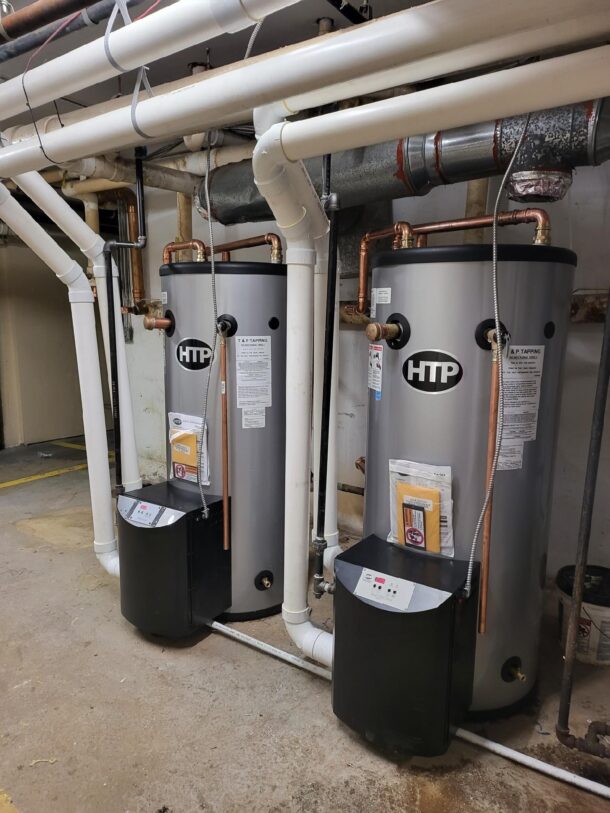
Photos by Affordable Fixes Heating Cooling Plumbing
Before Savkin chose the HTP Phoenix units, he explored other possibilities. “These HTP units were new to us, but we wanted a high efficiency, fast recovery water heater. If we had used another system, we would have to put in at least 3 units,’’ Savkin said. “We saved the customer about $12,000 by selecting this system.”
To complete the in-depth project, Savkin deployed a team of four plumbers and a debris scrapper. The initial phase involved the deconstruction and removal of the current units.
The second step proved to be just as demanding as the first step. Electrical wiring, new exhaust and gas lines were all components required for the second phase, due to the new system requiring fewer heating units.
John Monaghan, a HTP National Training Manager assisted the project by evaluating the building’s heat requirements and proposed installing two Phoenix 119-gallon tanks. “That not only saved the building owner a lot of money, but it also allowed us make the installation a little bit quicker,” Monaghan said.
Placing the tanks in the hotel’s basement was no easy task throughout the setup process. “It was a very tight fit. We were fortunate to have an elevator handy,’’ Savkin said. “We had to disassemble the new units, put them in a box, put them in the elevator and then re-assemble them. If there had not been an elevator, we would’ve gone old school and roped them down.”
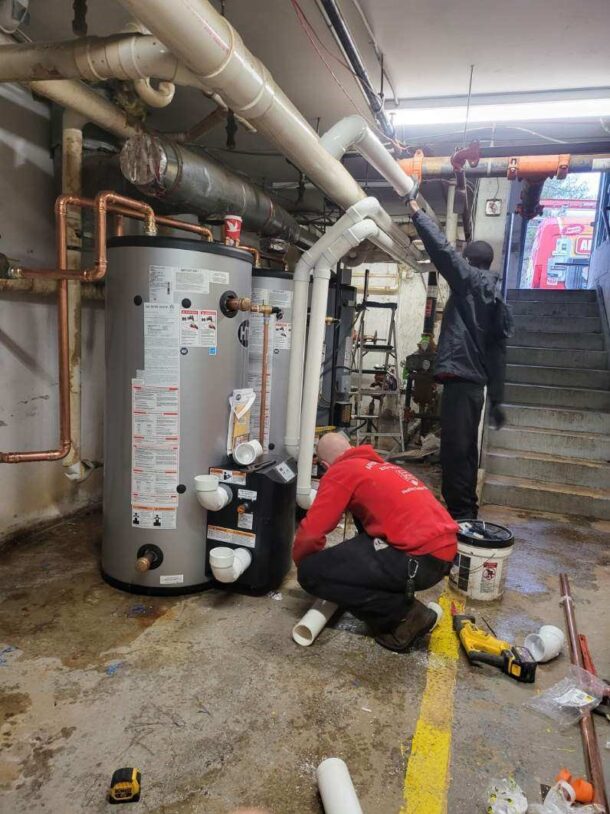
Workers from Affordable Fixes Heating Cooling Plumbing removed four water heaters and installed two HTP Phoenix 119 gallon tanks. Efficiency, durability and fast recovery factored into the decision to install the HTP products.
The selection of the HTP Phoenix water heaters was influenced by several reasons. The water heaters feature energy efficiency, durability and fast recovery that provides thermal comfort for hotel guests in a cost-effective way for the hotel owner.
“We didn’t know much about them, but we recently had training with them and I really liked their efficiency,’’ said Savkin, who has been in business in the Philadelphia area for more than three decades. “They were a great fit with a nice integrated control and easy to replace.”
Boasting a thermal efficiency rating of 96, the HTP Phoenix effectively uses 96 cents of every dollar towards heating purposes. On the other hand, a standard efficiency unit has a maximum capacity of a 60 percent efficiency rating, making the HTP Phoenix a significant upgrade. Operating at a 5:1 turndown ratio, the HTP Phoenix’s modulating burner delivers productive system efficiency even when the load is low.
To prevent corrosion, the HTP Phoenix comes with a 316L stainless steel tank. Furthermore, the unit includes a 7-year warranty for residential use and a 3-5-year warranty for commercial purposes.
“Most times you’ll get 8-12 years out of units, but like anything else it depends how much you take care of it,’’ Savkin said. “I could see these lasting 12-20 years. It’s all about the maintenance of the equipment, but it’s important to look at the water quality, too. The hardness and chemicals of the water has a lot to do with the longevity of the system.”
Receiving emergency service requests is typical for many plumbers, including Savkin. Having no access to heat or cold water will irritate any hospitality owner or homeowner, particularly during peak season.
“When we first looked at this project, we gave the owner a price and he didn’t get back to us right away,’’ Savkin said. “Then he called back and said he needed to have it done immediately. It’s an occupied hotel, and we are right around the corner. With the snow, the holidays and people traveling, this could have been a bad situation for him. We were glad to help him out and fix it quickly.”
Brian Giardina writes on a wide range of trade industry topics for publications throughout the United States.
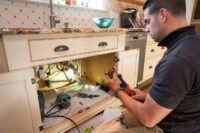
Domestic Water’s Creepy Challenge It’s a, well, creepy sort of problem. That is, when hot water recircs lose their ability to govern themselves. So, there’s the problem. But, let’s back up just a bit. Let’s start with an explanation. Then we’ll talk to the experts. There’s little debate that residential or light commercial domestic hot Read more
Domestic Water’s Creepy Challenge
It’s a, well, creepy sort of problem. That is, when hot water recircs lose their ability to govern themselves. So, there’s the problem.
But, let’s back up just a bit. Let’s start with an explanation. Then we’ll talk to the experts.
There’s little debate that residential or light commercial domestic hot water recirculation (DHWR) technology has proven its value in the world of plumbing and mechanical systems. The devices guard our safety, comfort and health. Hot water recirc systems move potable hot water to fixtures quickly, without waiting for the water to get hot, so there’s less wasted water, and time.
The key challenge to these simple systems is the problem of “hot water creep.” Let’s take a closer look, beginning with an examination of the components that have a role in the recirculation of a home’s domestic hot water.
Let’s first define the “system” After all, the various components, if not connected intelligently and working in concert, would accomplish nothing:
- Water heater without a tempering/mixing valve. Essentially, an unprotected, full-on arrangement that places anyone at risk.
- Water heater with a distribution tempering/mixing valve (typically, and ASSE 1017, or ASSE 1070 valve). This is most common, and became the point of introduction for DHWR systems.
- Water heater with distribution tempering/mixing valve with a DHW recirculation pump and a bypass valve or pump located at the domestic water system’s most remote fixture – with use of the cold water line as a means of returning water to the water heater.
- Water heater with distribution tempering/mixing valve with a DHW recirculation pump and a dedicated return line from the most remote fixture on that particular hot water zone. Ideally, this is how a DHWR system is installed.
- Finally, all of the above, to include a control of some means; aquastat, timer or combination control with some kind of logic.
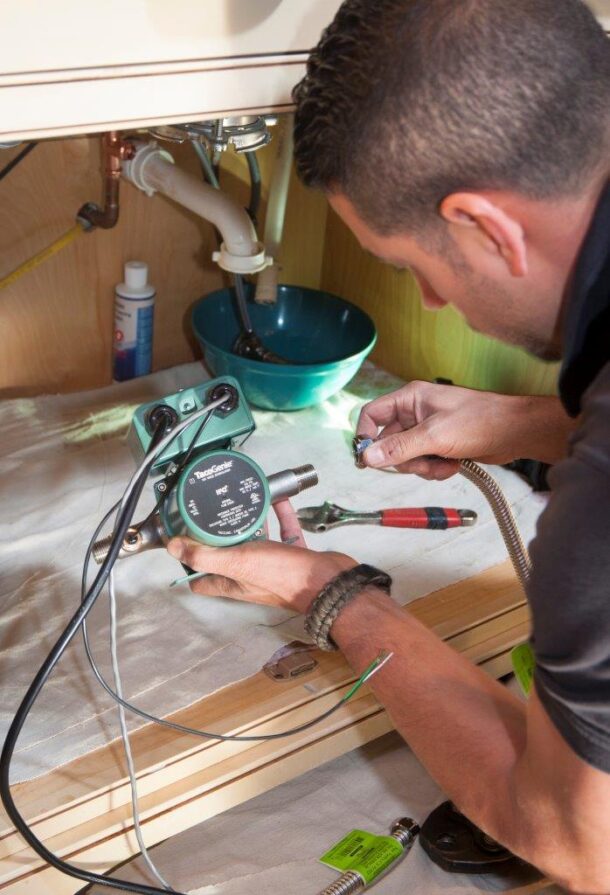
“It takes some, or several of the components above, to make a DHWR system,” explained Rick Mayo, product and applications instructor, Western region, Taco Comfort Solutions.
Most recirc systems, by design, have a tempering valve that continuously adjusts its temperature when water flows through it – while tempering (that is, mixing) it with cold water – to maintain proper outlet water temperature for rapid release at points of use.
The challenge is to maintain the mixed water temp during periods of no demand. The reason for this: the recirc’s pump enables flow through the valve, even when there’s no demand, or draw, from points of use – such as faucets and other fixtures. For this reason, recirc pumps must be piped so that the recirc’s returning flow can reach both the cold connection of the valve as well as the cold connection of the heat source. Some balancing may be required.
Smart, by design
Typically, a water heater’s storage temperature is set for about 140°F for legionella mitigation, and the DHWR’s hot water temperature is reduced to under 120°F at the mixed outlet connection of the valve (with the reduced temp made possible by mixing with cold water, by design).
This cause the valve assembly to adjust temperature; that is, until it reaches the hot water’s set-temp. The internal thermostat adjusts the piston to open the cold port and close the hot port, allowing hot water to recirculate. Unfortunately, there can be challenges to the intended function of these systems.
- Creepy situation #1: If the hot water distribution system isn’t insulated, this can cause the distribution loop temperature to creep down during periods of no demand.
- Creepy situation #2: Domestic water systems installed with a domestic hot water recirculation pump may cause downstream water to overheat if it’s not piped properly or is running longer than required. This overheating of temps within the piped system may go unnoticed for quite a while and could cause risk of scalding at points of use.
Mayo offers this insight: The ASSE 1070 valve does a better job of restricting flow of the hot water than the ASSE 1017 and is more effective at preventing “creep.” He clarifies: “Don’t get me wrong. Those ASSE 1017 valves work as intended in non-recirc systems. If the temperature is set for 115°F, they regulate the temperature to that point, almost assuredly. But as soon as you match ‘em up with a (DHW) recirc, problems can begin.”
- Creepy situation #3: Make sure there’s always sufficient flow to meet the DHWR valve’s minimum flow requirement. All DHWR control valves need a certain amount of flow to function properly. A properly sized, recirc pump will usually assure sufficient flow.
- Creepy situation #4: A point-of-distribution, ASSE 1017 mixing valve (or, for that matter, even the ASSE 1070 valve) that does not have a full or completely closed function for its hot inlet port can cause thermal creep if not properly piped and controlled; many mixing valves with an electronic actuator have a fully-closed position so that this doesn’t occur.
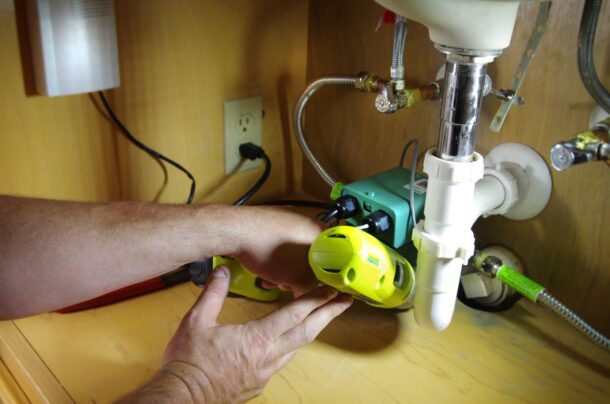
Piped conundrum
“It’s often a piping challenge,” said tekmar’s General Manager, Greg Leupin. “For many hot water recirc ‘creep’ challenges, the challenge has to do with incorrect piping. When the recirc is off or at rest, thermal ‘ghost flow’ can affect the amount of hot water that makes its way into the [distribution] piping.
Leupin added that many recirc loops lack a mixing valve, causing excessive – sometimes unsafe – temperature in the recirc loop, increasing the risk of scalding. This can also lead to inefficiency from heat loss, especially when the domestic water lines aren’t insulated.
Smart technology
Manufacturers have stepped in to help negate the risk of domestic water creep when recirc systems are installed. “Installation instructions are more explicit and the technology’s improved,” said Mayo.
“The problem begins when there’s an inability to dissipate the heat during periods of no demand,” added Mayo. “As referenced earlier Some [DHWR] devices close the hot side better than others, so both the built-in control strategy may help, as does the installation piping. Of course, the recirc shouldn’t be running when the distribution system’s already sufficiently full of hot water, readily accessible at taps and other points of use.”
- Taco SmartPlug (which won AHR Expo’s Product of the Year Award in 2017) was developed to eliminate the hassle of a “timer;” because of their design they only allow water to be circulated for short periods of time, this can help fight the challenge of thermal creep. The small device instantly changes any corded hot water recirc – for instance, those with just timer and on/off function – into a “smart” device by giving it the intelligence it needs to learn a household’s usage patterns to improve and regulate hot water distribution, increasing comfort and efficiency. It can also be set into a ‘pulse only’ mode for light commercial applications, or for homeowners who don’t have a predictable schedule.
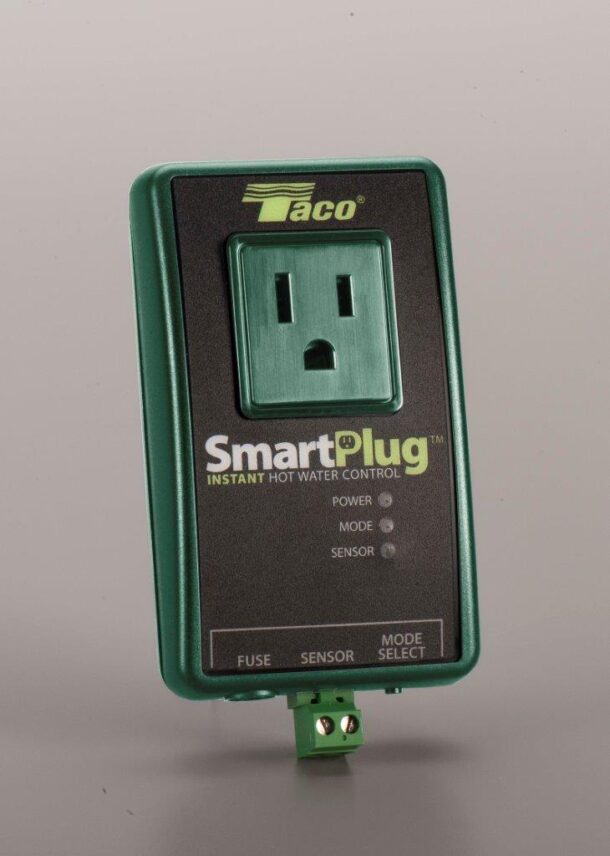
Other hot water recirc solutions include:
- TacoGenie allows homeowners to simply push a button when hot water is desired at a tap, on demand.
- Watts/Premier 500800 – an ideal solution for retrofitting existing domestic water systems with hot water recirc. The device uses the pump at the water heater (though not tankless systems) and an under-sink sensor valve to create a pressure differential – allowing the cold and cool water in the hot water supply line to bypass into the cold water supply line at a low volume through the thermostatically-controlled sensor valve, keeping the water in the hot water supply line at a “no-wait” temperature throughout the home.
ASSE 1070 valve
As Mayo stated earlier, ASSE 1017 thermostatic valves installed at the water heater or heat source may not close off sufficiently in some instances (while the circulator is running) to stop the outward flow of heat. If this happens, and a recirc pump continues to run, temperatures within the distribution piping can creep upward – creating the potential for unexpectedly hot water at taps.
In a situation like that one, the need for hot water [in the distribution piping] is satisfied, but if the [DHWR] pump’s running, ‘creep’ can occur,” concluded Mayo. “Yet another solution protects users from unexpectedly high temps at the tap with or without replacement of the distribution safety valve – and that is the installation of 1016 or 1070 point-of-use valves. They’re most often used for commercial installations, though there are many residential uses of the valves.”
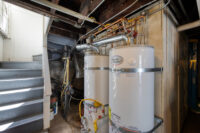
Decoupling Boiler and Installing Water Heaters in Century-Old San Francisco Apartment House Brings Relief to Residents Nothing lasts forever. That is especially true with mechanical fixtures, where the corrosive nature of water, the environment in which units are located and frequent use all work against fixture longevity. Nearly a century of service isn’t forever, but Read more
Decoupling Boiler and Installing Water Heaters in Century-Old San Francisco Apartment House Brings Relief to Residents
Nothing lasts forever. That is especially true with mechanical fixtures, where the corrosive nature of water, the environment in which units are located and frequent use all work against fixture longevity.
Nearly a century of service isn’t forever, but it’s a pretty good run. Some steam boilers, especially in inner-city buildings, that were installed in the 1920s and ‘30s are still in service. The reliance on steam-heated buildings in that era was a “direct result of theories of infection control” to help fight the global pandemic of 1918 and 1919, according to a Bloomberg article in 2020. Masks, shots and forced isolation fought against the most recent pandemic, but a century earlier the solution was far simpler – open the windows.
The theory followed the correct premise that fresh air would help fight off airborne diseases. In New York City, for instance, the Board of Health ordered windows to remain open to provide ventilation – even in winter. Steam heating and radiators thus packed plenty of punch. They provided heat for building residents on the coldest days and with windows open. Efficiency, obviously, was not top of mind when the boilers were installed.
In San Francisco, Excalibur Water Heaters solved a heating issue for an 8-bedroom apartment house that relied on a steam boiler that been in place since the building opened in the 1930s. The steam boiler provided hot water and radiant heat. “Because of the age of the boiler, the hot water was never reliable,’’ said Anthony Achermann, one of the owners of Excalibur.
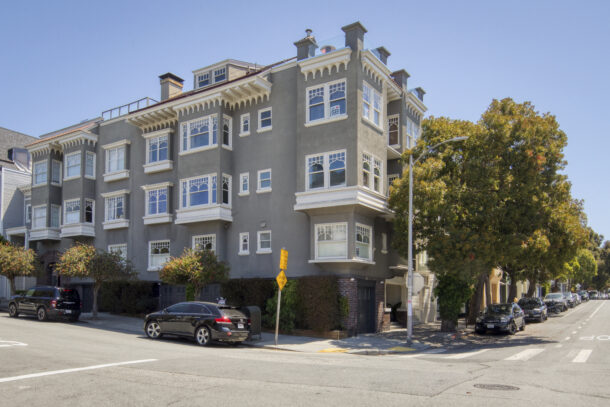
An 8-unit apartment house in San Francisco solved a problem with hot water delivery by installing two American Standard Water Heaters to replace an aging and faltering boiler.
Excalibur designed a solution that solved the problem in just one workday. The company installed two American Standard Water Heaters to provide hot water to the building. Due to space limitations, Achermann’s team used two 50-gallon tanks instead of one 100-gallon tank. Even more interesting, the ancient boiler remained in place and will remain the heating source for the apartment house.
A Hot Mess
The simple solution would have been to repair the ancient boiler – again – or install a new one. Achermann knew neither would be terrific options.
Replacing the steam boiler would have required a lengthy wait due to supply chain issues. The boiler had been repaired and serviced frequently, but few products that are nearly 100 years old work like they did when they came out of the box. In addition, many repair technicians avoid a challenging boiler replacement project.
“Most plumbers in this industry when they see a boiler, they run,’’ Achermann said. “Boiler service people are few and far between these days. Retrofitting any building with a boiler is hard.”
The boiler – “about the size of MINI Cooper,” Achermann said — operated on a timer, so hot water availability differed throughout the day. “Sometimes hot water was readily available,’’ Achermann said. “Other times it was lukewarm or no hot water.”
Steam boilers undergo significant stress and age over time. Poor water chemistry, corrosion, extreme temperature shifts and even the environment where the boiler is installed can contribute to the degradation of a unit.
Caustic embrittlement due to corrosion is a serious form of boiler metal failure. Even worse, chemical attack of the metal is usually undetectable. Failure occurs suddenly, often with catastrophic results. While aging, the apartment house boiler still has enough juice to provide heat. Perhaps it will need to be replaced at some point, but for now it serves the building. Certainly, the building owner can hardly quibble after receiving a lengthy amount of service from the heating beast.
The project was part of a remodeling of the apartment house. “The steam boiler was as old as the building,’’ Achermann said. “If they wanted to replace the boiler, they would have had to wait weeks, if not months. It was a common problem, but I’m seeing it less and less. When I come into a situation like this, I try to identify an out-of-the-box solution that can solve the problem.”
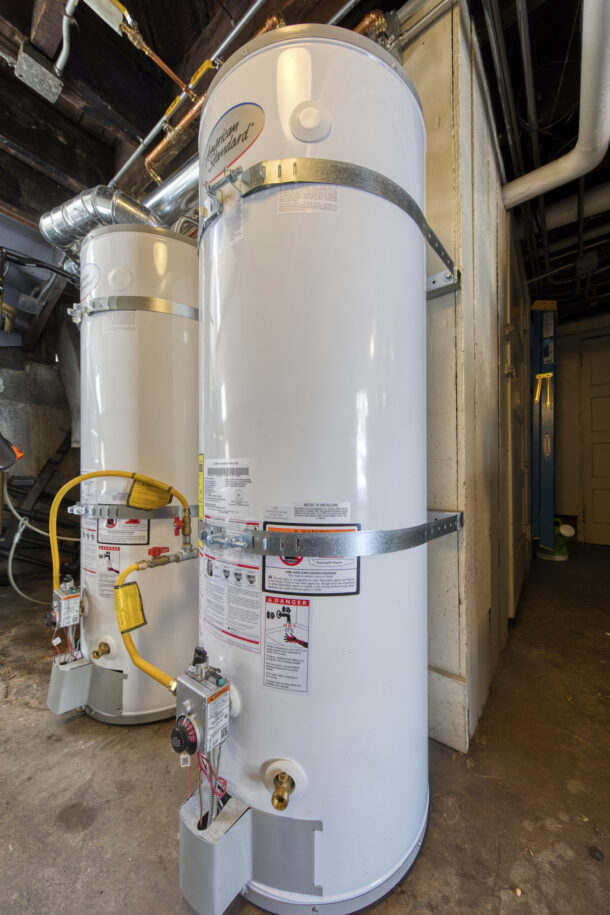
Due to the tight footprint of the mechanical room, Excalibur Water Heaters installed two 50-gallon tanks instead of one 100-gallon tank.
Splitting Service
Achermann solved the issue by decoupling the boiler from providing hot water. The in-place boiler still runs the heating system for the apartment house, but his team installed two American Standard Water Heaters for the building’s hot water service.
Because of space issues, Excalibur installed two 50-gallon tanks. “We didn’t have the space or the height clearance to install a 100-gallon tank,’’ Achermann said. “It was a pretty tight fit.”
The durability of the American Standard Water Heater brand was important to their inclusion in the project. “Over the years, water heaters have been getting lighter, they are making the walls on many brands thinner,’’ Achermann said. “Over time, water will try to corrode the tank. Anode rods are supposed to prevent that, but eventually they’ll leak and fall apart. The water doesn’t have anywhere to go, and it leads to leaks. By having a heavier tank, it’s buying more time.”
One of the most dangerous tasks for the project involved separating the boiler and installing the water heaters. With the gas and water lines coming into the building, the team took extreme care to complete a smooth transition.
“It’s important to understand the severity of what could happen if something goes awry,’’ Achermann said. “If something goes wrong, it could create a pressurized vessel that can cause an explosion. We had to make sure the steam radiators work appropriately, and that the boiler only has to make the steam.”
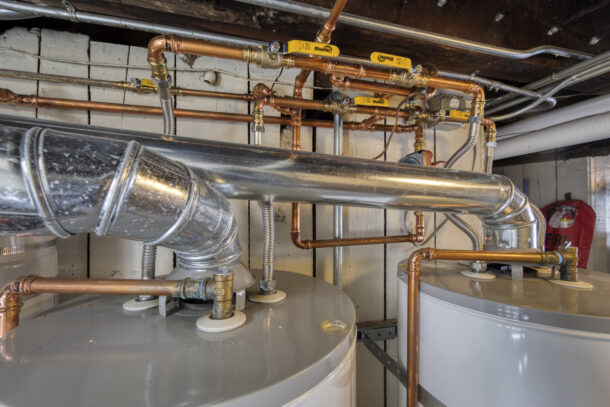
Additional Benefits
The warranty and burner assembly on the American Standard Water Heaters also factored into the selection for the project, Achermann said.
“With many manufacturers, the water heaters just make it past the warranty,’’ Achermann said. “The American Standard Water Heaters last well past their warranty date. They are also the only manufacturer in the San Francisco area that uses a mechanical gas control valve.”
The gas control valve is a traditional assembly that has served the industry well for decades. Many newer models have electronic assemblies that break down far earlier. “The electronic ones are harder to repair, while the mechanical heaters are much more robust overall,’’ he said. “I was getting tired of explaining why a unit we installed two years ago was failing.”
Workers completed the 10-hour project safely, and tenants celebrated that consistent hot water would flow to their apartments without interruption. “They’re excited because they now have consistent hot water,’’ Achermann added. “Sometimes it would take 3-4 minutes. We installed a recirculation pump and now the water gets hot within seconds.”
Overall, the project married Excalibur’s ingenuity, durable products and working with mechanicals already in place. Sometimes plumbers don’t have to re-invent the wheel. Making a few subtle tweaks saves time, money and energy, even if the units were around during the Hoover administration.
“It was a project that required some creativity as to how we could solve the problem,’’ Achermann said. “We came up with a good concept and the owner and the tenants are happy.”
Thomas Renner writes on trade industry topics for publications throughout the United States.
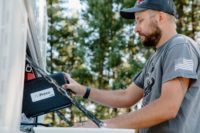
The importance of inventorying the right tools + supplies Last year, Keefer Rader, owner of Albuquerque-based Outlaw Mechanical, a shop that specializes in light commercial work, including kitchens, had one of those experiences that confirmed the value of an investment he’d made just weeks earlier. Well, he didn’t buy cryptocurrency or Spotify stock at just Read more
The importance of inventorying the right tools + supplies
Last year, Keefer Rader, owner of Albuquerque-based Outlaw Mechanical, a shop that specializes in light commercial work, including kitchens, had one of those experiences that confirmed the value of an investment he’d made just weeks earlier.
Well, he didn’t buy cryptocurrency or Spotify stock at just the right time if that’s where your imagination was going with it.
The event that triggered confirmation of a diagnostic tool’s purchase was a visit to a popular wedding venue in Colorado, a full day’s drive (or night, in this caser) from his shop.
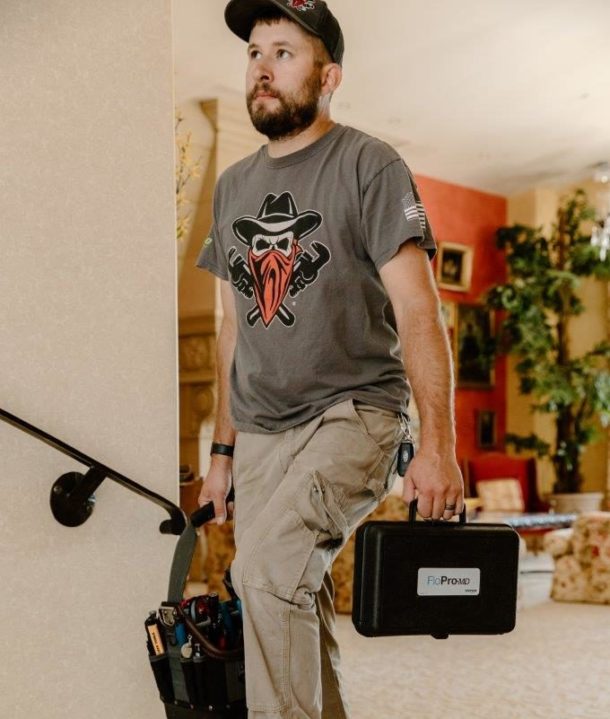
Keefer Rader, owner of Outlaw Mechanical.
350 miles from home base
Several years before he founded Outlaw Mechanical at the age of 21, Rader worked in remote Colorado, maintaining the property and mechanical systems on a private ranch – a destination that’s won recognition as a luxurious wedding/events venue. Though his firm – now 15 years old – has won recognition as the “Number Two-rated” mechanical firm in Albuquerque, he’s maintained ties in Colorado.
“My family and I love the area, and there are still folks in Colorado who insist that I serve as their mechanical systems pro – even at a distance of 350 miles,” he said. So it wasn’t a complete surprise to hear from a man who manages a mountaintop wedding venue outside of Durango, CO – just several days before a large gathering was to lease the facility for a ceremony.
Apparently, a large kitchen broiler – “absolutely needed by the caterer,” he said – wasn’t performing well. The new manager was instructed to get Rader out to fix it.
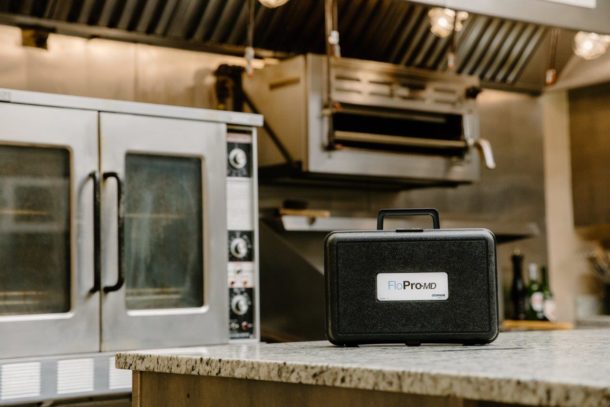
The Watts/Dormont Flo0Pro-MD is protected by its own hard case, and is easily portable.
“I tried to help him diagnose and trouble-shoot the problem, but I quickly learned that they’d already attempted to solve the problem [to no avail],” said Rader. “So, with less than a week before the large group arrived for the wedding – and with plenty of work to do in Albuquerque – Rader swept his schedule to allow time for a Friday night drive to Durango, hoping to have the problem solved for a drive home the next day.
“The challenge with remote site work is the need to pre-think everything,” he added. “Would I have the right materials and supplies and spare parts with me, and anything else I might need to complete the job in one trip?”
By Friday afternoon, Rader visited a local supplier, buying some spare parts for the large, commercial kitchen broiler. He ran between the truck and his shop’s well-stocked shelves a dozen times before his departure and was soon on his way, driving most of the distance that evening.
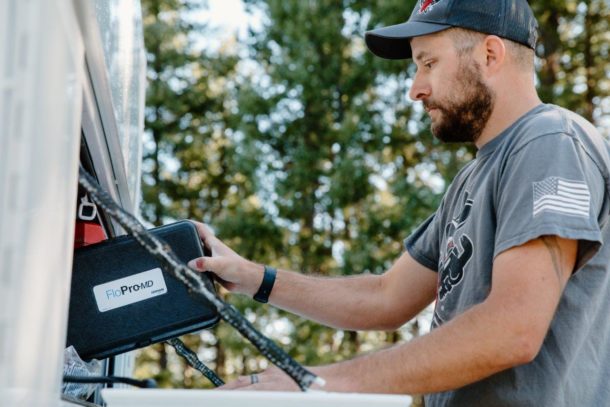
Keefer Rader, owner of Outlaw Mechanical, retrieves the FloPro-MD from his truck.
The next day, Keefer drove the last 20 miles to the wedding venue. “Just after sunrise, the site was open just as the manager promised,” said Keefer. He quickly found the griddle and set to work.
“I found that the broiler worked, but not well enough. It needed more [LP] gas for more heat,” he explained. Rader was unable to use a conventional manometer as the broiler didn’t have the test ports that he typically used for diagnosing hydronic boiler problems.
He went to the truck for the FloPro-MD diagnostic tool. “It’s now one of my go-to tools for gas appliance work,” he said. “The FloPro showed that the pre-regulator gas flow and pressure were good, but on the regulator’s other [outgoing/supply] side, I began to see my problem.”
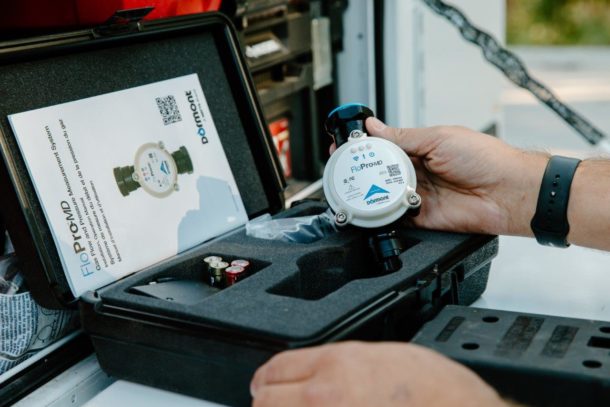
The Watts/Dormont FloPro-MD is a portable 3-in-1 gas flow meter, digital manometer, and calculator that helps service technicians and installers perform equipment start-ups, commissioning, and quickly diagnose gas flow or gas pressure issues with gas-burning appliances.
Among the supplies Rader learned long ago to keep in his truck: several gas regulators. “The FloPro made it perfectly clear that the broiler’s regulator had failed. Once connected, the new regulator provided greater gas pressure to the broiler which worked as intended, with plenty of heat for the caterer set to arrive that afternoon.”
Rader explained that, as the tool is connected to the gas line, and is out of the way, he especially likes the [FloPro-MD’s] ability to diagnose problems while the appliance is operating. “Managers at most commercial kitchens refuse to allow trouble-shooting or maintenance work during hours of operation because of the need to shut the appliance down – or, even worse – to cut gas service at a manifold to several gas appliances. Not with this tool – it’s designed to work while the appliance is in use.”
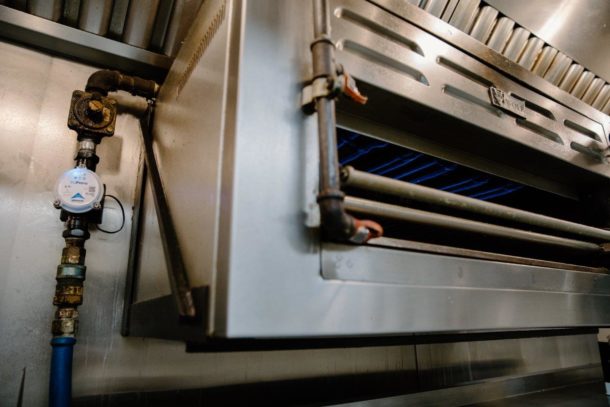
The FloPro-MD performs its diagnostic tasks, and provides useful data, while in-line (as gas courses through it). Here’s the device, in place, while flames heat the griddle following Keefer’s successful fix.
“The FloPro does the work of a variety of other tools,” added Rader. “It offers the function and intelligence of a manometer, and a gas flow meter, too. It offers precise diagnostics, with plain English on the screen. My hat’s off to the [tool’s] designer. The FloPro now has a permanent place in my truck.”