Drain cleaning is in full-swing and if you’ve been thinking about ways you can add services to your business – diagnostics, inspection and locating – may be the perfect addition. Not only can it add an additional revenue stream year-round, but it’s a particularly beneficial service this time of year when home buying tends to Read more
Industry Blogs
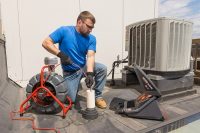
Drain cleaning is in full-swing and if you’ve been thinking about ways you can add services to your business – diagnostics, inspection and locating – may be the perfect addition. Not only can it add an additional revenue stream year-round, but it’s a particularly beneficial service this time of year when home buying tends to pick up across the country.
While most homebuyers opt to have a home inspection completed as part of the home buying process, sewer inspection is not typically included. Many don’t know to ask for it and realtors aren’t always suggesting it as a necessary inspection.
Drain Mob, a camera, jetting and drain cleaning company in San Diego regularly provides camera inspection and drain cleaning services for clients after they’ve purchased a home and are experiencing issues, something they and other professionals think could be avoided if homebuyers and their realtors took the time to inspect the lines as part of the home inspection.
“Every day we see a lot of clients that did not have a realtor that would actually camera their sewer lines, they would always go on the inspection report from the inspector,” said Billy Teeter, Drain Mob Owner in a recent Instagram video talking to realtors. “It’s two to three hundred dollars, it’s worth the money. Hire a professional and you’ll be a hero with your client. Protect your clients investment.”
How to Get Started
To begin offering services to this market, you don’t need to buy equipment all at once. Invest in equipment you’ll initially need most and then add-on as needed once you recoup your initial investment. For example, a RIDGID® SeeSnake® Compact2 Camera System paired with the CS6xPak Digital Recording Monitor is a good initial investment for residential jobs. All RIDGID digital monitors come standard with Wi-Fi allowing for easy capturing and sharing of images and video through the HQx Live App on your phone or tablet. This lets buyers and sellers quickly see any potential issues.
After your initial equipment purchase, marketing your new service becomes a priority. A few ideas as you get started are:
- National Association of Realtors – Connect with your local National Association of Realtors chapter. The association represents 1.3 million members involved in all aspects of the residential and commercial real estate industries and has over 1,200 local associations/boards and 54 state and territory associations.
- American Society of Home Inspectors – Reach out to local home inspectors about partnering to offer drain and sewer inspection as part of their services. The American Society of Home Inspectors, a professional organization for inspectors across the country, offers a searchable database of local inspectors on their website.
Additional Business Benefits
Incorporating diagnostic, inspection and locating services into your business provides additional benefits for a company. These include:
- Expanded Capabilities – Diagnostics is an investment that quickly pays for itself and continues to drive incremental income by letting contractors offer additional plumbing services. It also allows plumbers to take on more complex and difficult projects they previously would have had to decline.
- The Added Value of Certainty – Clearly seeing the problem means being able to offer the right fix, no more and no less. For customers, seeing the problem that backs the estimate increases their trust in a contractor and the necessity of work being completed.
- Find it. Clear it. – Contractors can serve more customers in less time with diagnostics, inspection and locating equipment because they can locate and repair problems faster. Many tools come standard with Wi-Fi capabilities, allowing for findings to be shared immediately with clients and co-workers, which leads to faster decisions and shorter projects.
In closing, regardless of whether you decide to target your diagnostic, inspection and locating services to homebuyers and realtors, these services and type of equipment can be a beneficial addition for your business and clients.
Article by Gina Hartman
Gina is Senior Global Marketing Manager of Underground Technologies, including inspection and diagnostic products, at RIDGID®. The company is a global manufacturer of more than 300 dependable and innovative tools, trusted by professional trades in over 100 countries. Learn more at RIDGID.com.
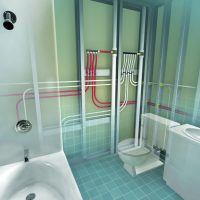
For residential plumbers, there have been two schools of thought for plumbing a house: home run and trunk and branch. Both have their positives and negatives, depending on what you’re trying to accomplish with the plumbing system. However, you may not know there’s a new (and smarter) way to design and install a residential plumbing Read more
For residential plumbers, there have been two schools of thought for plumbing a house: home run and trunk and branch. Both have their positives and negatives, depending on what you’re trying to accomplish with the plumbing system.
However, you may not know there’s a new (and smarter) way to design and install a residential plumbing system that installs faster, uses less materials, requires fewer connections, minimizes your liability and operates more efficiently.
It’s called Logic plumbing.
A Logic plumbing design can only be used with PEX piping, but since PEX is now used in more new-home construction than copper and CPVC combined, you’re most likely already using it. (And if you’re not, you need to check it out. PEX is highly durable, flexible and more cost-effective compared to copper and CPVC.)
The Logic approach leverages the flexibility of PEX pipe to minimize connections and reduce potential leak points while also incorporating multiport tees located near fixture groupings to both limit the amount of pipe and connections needed while also improving installation efficiencies and system performance.
What’s a multiport tee?
I’m sure right now you’re wondering, “What’s a multiport tee?” It’s essentially a bunch of tees all molded together to create one long tee with multiple outlets. This innovative product minimizes connections and is the heart and soul of a Logic design.
For example, six regular tees will have 18 connections, but a flow-through multiport tee with six outlets will only have eight connections (six connections for the ports, a main flow-through inlet and a main flow-through outlet). Think about how much faster you could install a system when you’re making half the number of connections.
And get this — while multiport tees may resemble a manifold, they have the benefit of being hidden behind walls without the need for an access panel. Yes, you heard that right. No need for an access panel, minimizing costs and labor to help keep your projects on schedule and on budget.
Multiport tees are made of engineered polymer (EP), a thermoplastic material that has been used in plumbing applications for more than 20 years. EP has superior mechanical, chemical and thermal properties that provide dimensional stability in demanding applications, including areas of high stress, heat and moisture.
And, like PEX, the EP material in multiport tees resists corrosion, pitting and scaling, so it creates a highly durable system that’s engineered to last. Best of all, multiport tees (as well as all EP fittings) are approved for direct burial in the soil or concrete slab, so they are ideal for in-slab plumbing applications.
The Logic layout
So what exactly is a Logic plumbing layout? It’s quite simple: a main line connects to a multiport tee with distribution lines going out from the tee. These individual lines extending from the single multiport tee provide water to all fixtures in a single or adjacent grouping.
This design uses significantly less pipe than a home-run layout, with just a few more connections. Plus, it requires considerably fewer connections compared to a trunk-and-branch installation.
For example, a 2,300-square-foot, two-story home using a Logic design requires only 637 feet of pipe while a home-run system uses 1,515 feet of pipe. That’s more than twice the amount of piping necessary.
In addition to the added costs required to install all that extra pipe, the system performance is also greatly reduced due to added pressure loss and longer wait times for hot water. Plus, all the extra pipe can lead to issues isolating hot and cold water lines. This increases heat transfer and energy inefficiencies within the plumbing system.
And, while it’s true a Logic installation uses slightly more connections than a home-run layout (59 vs. 48 in the 2,300-square-foot, two-story home example above), the amount of pipe savings is significantly more beneficial with the labor and material savings you get with less pipe to install (not to mention the efficiency of the system).
A Logic layout also installs much faster compared to a trunk-and-branch system due to the vast reduction in connections. With the two-story home example above, a Logic layout uses a mere 16 fittings and 59 connections compared to a whopping 96 fittings and 165 connections for trunk and branch. That’s six times the number of fittings and nearly three times the amount of connections!
All those added connections greatly increase your liability with more potential for leaks, plus it also limits the performance of the system with increased pressure loss.
So there you have it! Just a few “logical” reasons why you should consider a smarter approach to plumbing a home that will improve your installation times, limit your liability and offer an all-around better-performing system for the end user.
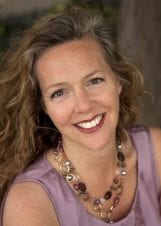
Kim Bliss is the content development manager at Uponor. She can be reached at kim.bliss@uponor.com.
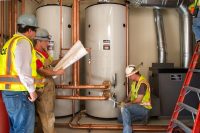
Four pro tips on how to cope with ever-growing consumer demands and better serve today’s digitally fluent customers You don’t have to be a fan of HGTV’s hit show Fixer Upper to be familiar with hosts Chip and Joanna Gaines. These days, the husband-wife duo has become the face of the American DIY Dream to Read more
Four pro tips on how to cope with ever-growing consumer demands and better serve today’s digitally fluent customers
You don’t have to be a fan of HGTV’s hit show Fixer Upper to be familiar with hosts Chip and Joanna Gaines. These days, the husband-wife duo has become the face of the American DIY Dream to transform an unsightly space into something chic and beautiful. And while the experienced contractor might understand the projects featured in each 30-minute episode actually take eight weeks or more to complete, home makeover shows make it look fun, easy—and unrealistically quick.
Considering the huge popularity of HGTV and DIY networks, there’s a good chance your customers are familiar with – and have been inspired by – the Gaineses and other home makeover stars.
In addition to HGTV and DIY network, your customers are likely fans of services like Amazon Prime two-day delivery, on-demand ride-hailing apps Uber and Lyft, and any number of other apps, websites and virtual services that have conditioned the average American to expect what they want when they want it.
This is the world in which we live and paint. In-person visits to a prospective customer’s house or business to spec out a project are being replaced by a growing number of mobile apps and web services like Paintzen, Houzz and Angie’s List that provide instant access to contractors, reviews, project estimates and design inspiration. This trend presents new challenges for the painting pro, but also new opportunities.
“Any time you can get people interested in what we do, we can add value by providing that service to them,” says Kevin Nolan, President and CEO of Nolan Painting in Havertown, PA. Nolan, who has nearly 40 years in the industry, says customers that look to platforms like Houzz and programs like Fixer Upper for design ideas are likely to have a more adventurous approach to their project and a clearer idea of what they’re after, not to mention a photo or video clip to help share their vision.
Tom VanDerkolk, 25-plus-year industry veteran and owner of VanDerkolk + Kooi Painting in Grand Rapids, MI, agrees, specifically citing how communication technology advancements have made his team more efficient. “Most projects are going to have questions, concerns or misunderstandings. We work to plan around those as much as possible, but simply knowing if our customer prefers a text, call or email allows us to solve an issue quickly.”
Here are four takeaways to help you stay relevant in the digital era and manage ever-growing customer expectations.
Get Social
If your business doesn’t have a Facebook or Instagram page, start there. Both platforms offer a free and easy way to showcase your handiwork. There’s a good chance your customers will share those project photos with their networks, which could lead to additional business. Or, you could pay to boost one or more of your posts to reach a larger network of potential customers. Both Facebook and Instagram allow you to choose your budget and target your posts to specific geographic regions and user interests; for even as little as $20, you can increase the probability of getting your craftsmanship in front of people most likely to need your services.
If you specialize in commercial work, sharing with photos, videos or behind-the-scenes tidbits about your work processes on LinkedIn might help you catch the eye of other local businesses.
Many of your prospective customers look to Pinterest for inspiration specifically for home painting projects. Having a Pinterest presence will show your customers that you are up to date with current trends and can be useful in helping your customer pinpoint the paint color or design scheme they are after.
Learn to Use a New Tool: Technology
While there are plenty of ways you can spend money to get noticed online, there are also a variety of free tools. For example, VanDerkolk says his team often uses Google Maps’ Streetview and Google Earth imagery to view a new job site – a simple practice that helps them prepare for the job. You can also review your business’ Facebook page insights (they’re free) to get a better understanding of your audience’s age, gender and location demographics – information that can be of use when designing a seasonal sales push, tailoring the tone of your social media content or deciding where to target an advertising campaign. And storing frequently used sales and marketing materials on cloud storage services like Google Drive or Dropbox allows for quick and easy access out in the field. Some painting contractors take their use of technology one step further — Google AdWords campaigns (an inexpensive form of online advertising) can help generate new leads, for example.
Own Your Reviews
Nolan and VanDerkolk’s combined 67 years of experience hasn’t yielded a sure-fire way to avoid negative customer feedback, but it sure has taught them a thing or two in how best to deal with it. Both owners recommend taking the time to respond to any negative reviews that show up on Google, Facebook, and Yelp, an effort that at minimum demonstrates to anyone who may encounter the negative review that you are genuinely concerned about your customers’ satisfaction, and in the best-case scenario may even result in the dissatisfied customer amending the negative review (or removing it altogether) or giving you another shot at the business. Additionally, don’t be afraid to ask your satisfied customers to leave a positive review of your business online – having a high volume of good reviews on Google, for example, will help your business show up in search results.
Maintain Your Humanity
No amount of technology will replace the value of a human connection with your customer. So while some homeowners may opt for the ease of a website or app to get a project estimate, the reality is that many more will seek your business out because of your reputation or as the result of a recommendation from a friend or family member. VanDerkolk recommends going the extra mile with customers whenever possible; he’s been known to surprise families who are without use of their kitchen for a few days due to a renovation project with a gift card to a local restaurant or tickets to a sporting event. Similarly, Nolan recommends finding ways to give back to the community around you. Whether you are sponsoring a community event or doing pro bono work for a community organization, you are demonstrating your business’s character and culture in a way that no digital service can ever replace.
Diane Walsh is Vice President of Market Development and Sales Operations for ShurTech Brands, LLC, maker of FrogTape® brand painter’s tape. Diane also serves as director of the ShurTech Brands Professional Paint Advisory Board, working with leading contractors from across the country to explore industry trends and share innovations for the benefit of the entire trade. Diane was awarded 2018 PDCA Associate Member of the Year.
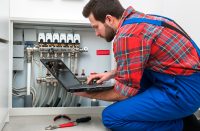
Callbacks are often preventable—if you understand the common causes. Learn how to reduce callbacks, maintain your reputation and boost productivity with a few best practices. “I’m not happy with the work.” They are the words no contractor ever wants to hear. They mean less attention to other jobs, a smaller profit margin and the potential loss Read more
Callbacks are often preventable—if you understand the common causes. Learn how to reduce callbacks, maintain your reputation and boost productivity with a few best practices.
“I’m not happy with the work.” They are the words no contractor ever wants to hear. They mean less attention to other jobs, a smaller profit margin and the potential loss of future business.
Callbacks can hurt a business’ reputation in several ways. First, referrals are adversely affected when homeowners talk with one another and share their unpleasant experiences. And when those same homeowners take their displeasure online and leave negative reviews online and on social media, the impact can be much more permanent. Finally, callbacks can also hurt a company’s productivity by inhibiting the ability of the team to move on to other projects.
The good news? Many callbacks are preventable. Here’s a rundown of three key strategies for avoiding them.
Educate the Customer
Very often, customer satisfaction comes down to one very important factor: A contractor’s ability to manage customer expectations.
“We get fewer callbacks when we educate the client about things like materials and warranties,” says Cal Phillips, who has owned and operated the Denver-based Eco Paint since 1990 and has been painting homes since 1977. “We’re the professionals, so it’s up to us to educate the client so they can care for their home.”
Education should start as early as the initial onsite visit. Managing a customer’s expectations is essential, especially when it comes to color variations, service parameters and ongoing maintenance.
And consumer education doesn’t stop after the last coat is applied. Phillips makes sure his clients understand their responsibilities for continued care after the job is completed.
“On an exterior project, we’ll let a client know that the paint needs to be maintained by making sure sprinklers are properly adjusted, with gutters and downspouts in good operation so that water is adequately removed from painted surfaces,” he says. “We also inform them to keep vegetation pruned back away from the substrate.”
This kind of dialog does more than help prevent callbacks. It can also instill a trust factor with your customers that tells them you care about the lasting quality of your work, even after the job is complete. And that can have the fringe benefit of turning first-time customers into repeat clients.
Maintain Clear Communication — Inside the Office and Out
Rarely is poor work the reason painters get called back to a job site. The most common reason is poor communication. Communication breakdowns between estimators and painters or between painters and customers can result in mistakes. Like applying an accent color to the wrong wall or painting trim the customer had wanted untouched. That can often mean lost productivity and bad customer reviews.
At Two Dudes Painting, a leading commercial and residential painting company in Lancaster, PA, painters receive a copy of the client’s paperwork to ensure everyone understands what the client has signed off on.
Samantha Seifried, who holds the role of Client Advocate at Two Dudes, says for longer projects, the company encourages clients to communicate with painting crews.
“When a project lasts more than a couple of days, we strongly encourage homeowners to review the work daily and let us know if they see errors or details they’re not happy with,” says Seifried. Regular dialog with the customer makes the company more efficient—and clients are more satisfied—because if errors crop up, painting crews can make corrections while they’re still on site, rather than having to come back after they’ve committed to another job.
Re-scope the Job When Needed
When customers fail to understand the process or timeline, or ask their painting contractor to perform work outside their area of expertise — carpentry or electrical work, for example — professional painters can sometimes find themselves tasked with a job in which they’re less-than-comfortable. Painters may not have experience in carpentry, drywall finishing or electrical work, and therefore trying to perform work in these areas could end up worsening jobsite problems. Knowing when to call in a specialist, as well as rescope the job with the customer, is crucial to ensuring your work and reputation remain intact.
For companies that offer a variety of service lines, it makes sense for crew members to request assistance from others who specialize in that line of work when needed. Trusting your field staff and giving them the authority to call and ask for help if they feel uncomfortable taking on certain aspects of a project can reduce callbacks significantly, since certain contractors have more experience in certain areas than others.
For smaller companies or one-to two-person crews, it makes sense in such cases to simply recommend an outside contractor to tackle repairs that fall outside the scope of the painting job. This is especially true with exterior paint projects, where it’s not uncommon to run into damage like rotted wood. It may be the last thing small painting companies (or homeowners, for that matter) want to hear, but in the end, the customer will appreciate your honesty and have a better overall experience because of it.
In the end, callbacks can cost a painting company dearly, both in reputation and production. It’s essential to take proactive steps to prevent them if you want to build a more profitable business.
“We don’t want callbacks,” Seifried says. “But, more than that, we want great reviews and ratings. That’s why we work so hard to deliver a whole project experience.”
Diane Walsh is Vice President of Market Development and Sales Operations for ShurTech Brands, LLC, maker of FrogTape® brand painter’s tape. Diane also serves as director of the ShurTech Brands Professional Paint Advisory Board, working with leading contractors from across the country to explore industry trends and share innovations for the benefit of the entire trade. Diane was awarded 2018 PDCA Associate Member of the Year.
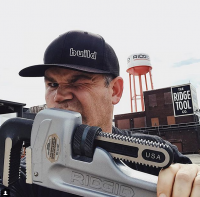
Just a couple days ago I returned from an event that has me so excited about working in the trades and what it means to be “Made in the USA”. The RIDGID Experience is only in it’s second year of existence but its clear to me that this will be an amazing annual event for Read more
Just a couple days ago I returned from an event that has me so excited about working in the trades and what it means to be “Made in the USA”. The RIDGID Experience is only in it’s second year of existence but its clear to me that this will be an amazing annual event for years to come. Here’s how it works: All across their social media channels RIDGID invites anyone who uses their tools, any and all of the RIDGID tools to show off their pride in the work they do with those tools. There’s an official entry process and some hashtagging involved but its super simple and fun. Once entered RIDGID picks the winners of the contest and those winners are treated to a total first-class experience with factory & hands-on training center tours, an inside look at new upcoming products and tools, meals, lodging, airfare, limo, professional photo shoots, a box suite at the Indians ball game and even a fishing trip on Lake Erie! Oh man, I gotta tell you it was a blast!
Of course factory tours are exciting, getting to see how our favorite tool is made and even meeting the people who make them daily leaves me with a higher level of respect for the brand and excitement for my work. That was definitely the case for me after the #RIDGIDExperience.
Unfortunately we don’t always get to take the camera’s along for every step of the tour but I’ve posted a few cool shots on our Facebook and Instagram along with some comments along the way. I’ve included a video of the final steps in the assembly of the iconic 300 below; its hard to believe that machine was ever so clean and shiny!
I’d like to thank the entire team at RIDGID and those involved who organized and pulled off a truly memorable experience for all of us “winners”. It’s clear the entire company knows and cares about who their customer is. Thank you, Eric Aune.
https://www.instagram.com/p/BlLwrqWhEO3/?taken-by=mechanicalhub