Winter’s strangle hold of frigid sub-zero temperatures has finally taken hold here in Minnesota. I’m sure many of you too have been blasted with arctic air and the storms that come with it. I think we’re in for a good old-fashioned winter and to be honest, it’s a welcome event. Last year’s winter weather was Read more
Uncategorized
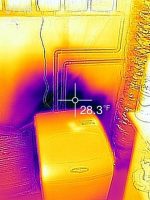
Winter’s strangle hold of frigid sub-zero temperatures has finally taken hold here in Minnesota. I’m sure many of you too have been blasted with arctic air and the storms that come with it. I think we’re in for a good old-fashioned winter and to be honest, it’s a welcome event.
Last year’s winter weather was terrible for business here in my area and I am very much in need and looking forward to the late night emergency no-heat calls or the many frozen/burst pipe repairs a typical winter inevitably ushers in. I never wish these situations on any of my customers; however, it is how we make our money so it’s good for the bottom line.
This past week our temps began to drop leading into the weekend; with lows bottoming out near -30F air temp and windchill reaching as low as -55F the calls have been coming in fairly regularly now. No heat, frozen pipes, a couple broken water pipe and even a frozen stock tank are some of the issues I’ve personally dealt with so far.
Just this last Sunday you might have seen a Facebook or Instagram post from an early morning emergency call I received from a new customer without water at any of their faucets. With overnight lows reaching well below -25F I was curious whether they had a frozen pipe inside their home or if the well supply line to the house has actually froze underground. I quickly found the problem upon arrival with the help of my infrared thermal imager, a tool I cannot imagine being without.
As mentioned in my post I have a few thermal imagers, two by Flir, one from Milwaukee and another from SEEK Thermal. Each is a little different from the others but all have proven extremely useful when diagnosing problems with both plumbing and heating systems. I should also mention how valuable these tools are to verify the proper operation of radiant heating systems as well. On a more than one occasion I have used an imager to show my customers where embedded heating lines are installed and that they are in fact operating as designed; something nearly impossible to do with any other tool.
Back to the frozen plumbing call.
When I arrived to the house with no water I immediately turned on all the faucets, walked downstairs into the mechanical room and attached my thermal imager to my iPhone. Within a minute I was able to identify the likely problem, a fresh air supply duct spilling -13F cold air directly onto the inlet copper tubing to the whole house water softener. As you can see in the photo the area around the softener is only 28F, something I would have eventually figured out but there was a lot of piping near the rim joists and strapped in front of an outside wall so I have no doubt it would’ve taken more than one minute.
Thankfully none of the copper had burst or even expanded so once I had thawed the ice plug in the softener piping it let loose and water was flowing to each faucet. Problem solved. Quickly thanks to a tool I will never be without and continue to find new uses for everyday.
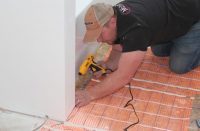
Residential construction is definitely on the upswing here in Missoula, MT. We’re quickly approaching the levels we saw before 2008, and I hope we don’t quite hit that peak again. I say this because the quality of work suffered in ’08. I was strictly doing service at the time, but pressure on all the trades Read more
Residential construction is definitely on the upswing here in Missoula, MT. We’re quickly approaching the levels we saw before 2008, and I hope we don’t quite hit that peak again.
I say this because the quality of work suffered in ’08. I was strictly doing service at the time, but pressure on all the trades was so high that shortcuts were taken on construction and installation, and it didn’t do any good for the collective tradesmen’s reputation around town. I think everyone breathed a sigh of relief when things slowed down. At least initially.
In the years leading up to the “crash,” I was able to establish a local reputation as someone who could figure out a solution for most plumbing and hydronic problems related to poor workmanship and improper installation. This served me well when I started my own company in 2011.
So, everyone here is getting busy again, but things are a bit different for me this time around. I now own a three-person company, and we do plenty of installation work. As we’ve grown, we’ve been mindful to use the best practices and products for the each application, instead of using a broad-brush approach on everything we encounter. We’ve expanded our comfort zone to better serve our customer base and it’s proven worthwhile.
Warm floors without water
About 60% of our heating work is hydronic. It’s our opinion that there’s no system more comfortable than in-floor radiant, but there are applications where it’s just not feasible.
This spring we were working on a new, 3,500-square-foot residence where heat and AC was being supplied by a heat pump. An additional hydronic system wasn’t in the budget, but the homeowner really wanted floor warming in the master and guest bathrooms. With a total of about 55 square feet, installing a boiler wouldn’t have been cost effective, even an electric boiler.
We decided to try an electric radiant mat product for the first time. After pricing the few systems on the market, we settled on the Watts Radiant HeatWeave. Despite having a one-ton pickup full of tools, we never used anything other than a multi-meter, glue gun and a pair of scissors.
Watts provided everything else need for installation. It came with a “LoudMouth” alarm that sounds if you nick a wire. The kit also included a slab sensor and a thermostat, so that you can program the system to maintain a specific floor surface temperature, or opt for room temperature.
With adhesive strips on both sides of the mat, there’s no specific orientation or direction you need to run. It simply sticks to the subfloor. While reading the directions, the first bathroom took about an hour-and-a-half. The second room took less than an hour.
In the past, electric radiant has always been something I’ve left for an electrician or a tile guy to install. From here on out, it’ll be a source of revenue for us.
Comfort is Queen
While comfort was king in ‘08, efficiency is just as important on new construction projects these days, as I’m sure you know. Homeowners are looking to shrink utility bills, and they’re asking for hi-efficiency equipment.
In the past year we’ve started using heat pump water heaters when a boiler isn’t present. After trying two different brands, we’ve gravitated toward the Bradford White.
The customer who asked us to put in the electric radiant also got an 80-gallon Bradford White AeroTherm™ Series heat pump water heater. Unlike most of the heat-pump water heaters on the market, you’re able to lay the unit on its side during transportation. That’s a plus, because the heat pump unit adds substantially to the tank’s height.
On that note, we’ve also found that the AeroTherm is significantly shorter than many other models, making installation and service a lot easier. The other brand we tried was probably a full foot taller, and about four inches narrower in diameter. Since you’re not supposed to stuff a heat pump water heater in a closet anyway, the diameter is of little concern.

These types of water heaters are more expensive than their standard electric counterparts, but they often qualify for state and local utility rebates and tax credits.
I don’t know about other brands, but the AeroTherm comes standard with a 10-year limited warranty. For an efficiency-minded customer, it makes a lot of sense.
Convenience and conservation
There’s one more product that has cemented its roll on nearly every new construction job we handle now; domestic hot water recirculation systems. When the AeroTherm was installed in the home, so was a Taco SmartPlus domestic hot water recirculation system.
In the mid-2000s, we installed very few DHW recirculation devices, but times have changed. California’s water shortage has raised awareness to the topic in recent years, and people have grown more impatient. Generally speaking, everyone wants hot water ten minutes ago, whether they’re of a conservation mindset or not.
Knowing your demographic helps here. If it’s a job in town, we lead with water conservation. Missoula is an environmentally-savvy place, so mentioning that a DHW recirc system can save up to 12,000 gallons of fresh water each year generally grabs attention.
Outside of town, where bigger, gaudier homes are pretty common, it’s all about convenience. Very rarely, in either of these situations, are customers completely uninterested. In most cases, recirculation systems aren’t cost prohibitive.
The vast majority of the residential new construction we do is custom, in which case we don’t even list DHW recirculation as an option. It’s simply in the bid. If the builder comes back later looking to cut costs, I tell him to put laminate countertops in the guest bathrooms instead of granite, and keep the recirc.
In 90% of our residential projects, and on every commercial job we do, we’re installing dedicated hot water return lines with a SmartPlus circulator. The system’s “smart” mode records each time hot water is called for during a seven day period and then duplicates the pattern for the following week. It can also be set to “pulse” mode, operating for 150 seconds every ten minutes, maintaining hot water at all fixtures.
For new construction or retrofits where there’s crawlspace access, we can typically run dedicated return lines and install the system for under $1,000. If dedicated lines aren’t a possibility, we’ll go to a system like Taco’s HotLink, with a crossover valve that allows hot water to return to the water heater via the cold water line. This approach has an even smaller price tag.
As I said, the new construction game has changed since the last economic upswing. Competition is arguably even stiffer, but the quality of work has much improved by all the trades. We’ve evolved with the market by providing the best service we know how, and finding new sources of revenue.
By Andy Mickelson, owner, Mickelson P&H. Andy has built a solid foundation for his business through hard work and perseverance. His performance on high profile jobs in the Missoula, Montana area have placed him at the top of the list for area customers seeking a knowledgeable contractor in the plumbing, hydronic and HVAC field. Andy has served as a United Association Instructor at the Missoula Joint Apprentice Training Center for the Local 459. His passion for industry education, advancement and professionalism make him a well-respected local businessman.
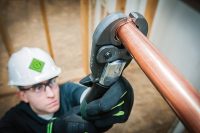
Greenlee Textron Inc. has launched a new line of Gorilla™ pressing tools designed for joining pipe safely by eliminating the need for an open flame and a hot work permit on the jobsite. The new Gorilla™ pressing tool line features two separate tool platforms: the inline battery pressing tool (INLNPRESS-TOOL19kN) and the pistol grip Read more
Greenlee Textron Inc. has launched a new line of Gorilla™ pressing tools designed for joining pipe safely by eliminating the need for an open flame and a hot work permit on the jobsite.

The new Gorilla™ pressing tool line features two separate tool platforms: the inline battery pressing tool (INLNPRESS-TOOL19kN) and the pistol grip battery powered pressing tool (PSTLPRESS-TOOL32KN). Both tools quickly press watertight connections in three to four seconds. The tools can be used while a system is still wet, unlike with soldering, so the contractor does not have to drain the system and wait for it to dry before pressing. The inline pressing tool has a fitting capacity of 1-1/2” (38.1mm) on PEX and 1-1/4” (31.8mm) on copper and stainless steel, and the pistol grip pressing tool has a fitting capacity of 2” (50.8mm) on PEX and 4” (101.6mm) on copper and stainless steel. The tools have a patented twist and release pin, making jaw exchange even easier. The kits come with four jaws for the inline and six for the pistol grip.
These new pressing tools utilize intelligence for accurate pressing and are designed with autostop technology, which automatically stops the piston when the optimal force is reached, sealing the fitting properly. Precise pressure monitoring and diagnostics ensure appropriate specifications for each fitting. The quickstop feature built into both tools elicits an immediate stop to the piston once the trigger is released safeguarding the user’s hands from pinch points. The lightweight design, 350-degree rotating head, and LED work light allow for both products to be used in dark tight spaces.
The Gorilla pressing tool line is a high quality solution for Faster, Safer & Easier® fitting installations from Greenlee. For more information, visit www.greenlee.com or call 1-800-435-0786.

With more than 47 years as a plumber—including three years US Navy service—the Bronx-based professional offers a full range of plumbing, drain cleaning, fire suppression and emergency services for the commercial, residential and institutional markets—to the New York City area. When he talks drain cleaning tools, he can’t help but boast about how much they Read more
With more than 47 years as a plumber—including three years US Navy service—the Bronx-based professional offers a full range of plumbing, drain cleaning, fire suppression and emergency services for the commercial, residential and institutional markets—to the New York City area.
When he talks drain cleaning tools, he can’t help but boast about how much they help him on the job. “There’s nothing like it. It’s fantastic for clearing scale from inside lines. It flies around pipe bends!”
That’s Sylvan Tieger on the unique and revolutionary ClogChopper® cutting tools from General Pipe Cleaners.
“A registered master plumber like me can find lots of work in a city of eight million,” Tieger smiles. “My mechanic sometimes wonders why I put so little mileage on my truck; most of the time, I just travel a couple miles to jobs!”
Much of that work is new construction. “That’s where ClogChopper really shines,” he says.
Raw Cutting Power
Tieger notes that lots of construction debris—like plaster and cement powder—is often carelessly deposited in drains lines.
“You quickly get a build-up of hardened material inside pipe walls,” he points out. “ClogChopper makes short work of problems like those.”
With six self-sharpening blades, ClogChopper digs into encrusted debris and root masses, easily grinding up stoppages, scale and crystallized urine—without risking pipe damage. It works in both directions, into and out of lines—all in one operation.
The spherical design also maneuvers around tight bends and traps, thoroughly and safely cleaning metal, plastic and clay pipes. Available in 1”, 1-1/2”, 2”, 2-1/2”, 3”, and 4” sizes, it’s also excellent for clearing stacks, downspouts and mains – as well as for pipe lining jobs.
“ClogChopper is an amazing tool,” Tieger says. “I love how it slices through roots – and is self sharpening!”
Right Equipment Mix Tackles Tasks
Tieger routinely teams ClogChopper cutters with his Speedrooter 92® power drain cleaner—also from General.
“The combination of ClogChopper and Speedrooter 92 especially lets me tackle long-run jobs—even longer than I expected,” he claims.

Superb for long, tough jobs, Speedrooter 92 blends rugged reliability with optimal control and ease-of-use. Great on tree roots, the field-proven machine features a braced frame at key stress points, a metal drum design for durability and longevity, and Flexicore® cable – the industry standard for toughness.
To assist on long, tough jobs, Variable Speed Power Cable Feed makes feeding and retrieving the cable easier. It drives 3/4” and 5/8” cables with no adapters needed when switching between cable sizes.
Speedrooter 92’s durable design also offers easy handling. One person can easily load it onto a truck. The machine’s frame slides smoothly from the loading wheel to the handle to the stair climbers and finally to the wheels. And the adjustable height, swept-back handle provides maximum maneuvering leverage.
“Pulling the handle down lets me get into small spaces,” Tieger says. “And the big wheels make it easy to maneuver on tight jobs.”
Heavy duty Flexicore cable combines superior strength and kinking resistance with just the right flexibility. It carries the best warranty in the business—one-year protection against breakage.
General’s new Speedrooter XL blends long distance clog-busting power with easier drum changes. A powerful 3/4 hp motor drives the cable up to 200 ft. down the line to clear tough clogs in lines 3” to 10” lines.
Change drums to add cable lengths or swap cable sizes with ease. Just loosen three knobs and remove the drum. Switch between 3/4” or 5/8” cables in the large drum design, or substitute the small drum with 100 feet of 1/2” cable for smaller lines.
Sylvan Tieger’s equipment array also includes General standards like the Mini-Rooter XP® and Super-Vee® cable drain cleaners.
Easy to transport and maintain, Mini-Rooter XP unclogs drains from rooftop to basement – including kitchen, bath and laundry lines. It carries 75 ft. of 3/8” or 1/2” Flexicore® cable – yet weighs about 60 lbs.
The hand-held Super-Vee® easily unclogs sink, shower, toilet, and laundry drain lines up to 3” in diameter. With a dependable motor, durable aluminum drum, and tough Flexicore cable, it withstands the most demanding small line jobs – and keeps working year after year.
“The reason I stuck with General for the last 47 years is the quality,” Sylvan Tieger concludes. “I can’t find anything better than General equipment on the market!”
Natale Builders’ newest development — Rivera Greens — in Clarence, N.Y., includes 35 single-family homes built to an energy efficiency standard unparalleled in the Buffalo/Niagara region. In fact, Rivera Greens is the first certified National Association of Home Builders (NAHB) Green Standards Eco-Friendly Development in New York State. All home designs in the development are Read more
Natale Builders’ newest development — Rivera Greens — in Clarence, N.Y., includes 35 single-family homes built to an energy efficiency standard unparalleled in the Buffalo/Niagara region.
In fact, Rivera Greens is the first certified National Association of Home Builders (NAHB) Green Standards Eco-Friendly Development in New York State. All home designs in the development are ENERGY STAR® rated and are expected to save homeowners 60 to 100 percent of their utility bills. What’s more, the builder is committed to offering these homes at no extra cost to its customers, demonstrating a new standard in home building and leading the way by applying cutting-edge energy-efficient technology, including geothermal heating and cooling systems.

Located in Clarence, 40-year-old Natale Builders was first introduced to geothermal by a customer who requested it in the $500,000-home he was building. As Larry LaDuca, general manager of the company, researched the technology, he realized, “In our market, geothermal is a no-brainer. It’s particularly attractive when you’re building a new home and can incorporate the cost of the system into your mortgage.”
A geothermal system takes advantage of free solar energy stored just below the surface of the earth. Using a series of pipes (an earth loop) buried in the ground and a geothermal (sometimes referred to as a ground source) heat pump, the geothermal heating and cooling system extracts heat from the earth and carries it to a building in the winter. An indoor unit compresses the heat to a higher temperature and distributes it throughout the structure. In the summer, the process reverses and the system extracts heat from the building and rejects it to the earth. In both cases, the geothermal system delivers consistent temperatures and efficiencies that exceed those of conventional HVAC systems, offering savings as high as 70 percent for heating, cooling and hot water.

In addition to consistent temperatures, a geothermal system ensures good indoor air quality (IAQ). That’s because the system doesn’t require combustion and therefore produces none of the byproducts associated with combustion, including carbon monoxide, which can be dangerous if not vented properly. And, the average geothermal system lifespan exceeds 24 years — compared to 15 years for a more traditional heating and cooling system.
Armed with this information, LaDuca set about first convincing owner Angelo Natale that geothermal was the way to go at Rivera Greens and then searching for a contractor with the capability and experience to install the systems in the development. Three to four months of searching for the right company led LaDuca to Jens Ponikau, part owner of Buffalo GeoThermal Heating.
“Jens can talk circles around anybody when it comes to geothermal,” said LaDuca. “It was his grasp of the subject and his passion for the technology that instilled confidence in us that he was the contractor who could provide us with the best installation and service.”

Ponikau is an International Ground Source Heat Pump Association certified geoexchange designer (CGD) who brought more than 20 years of experience to the Rivera Greens project. The challenge for him was two-fold: to reduce his installation costs to meet the builder’s commitment to provide energy-efficient homes at no extra cost and to provide a geothermal design that could be applied to all six model homes offered in the development.
To reduce installation costs, Ponikau ruled out a vertical loop and a traditional horizontal loop, opting instead for a stacked slinky loop field. This system uses slinky coils rather than straight pipe, which are stacked in a horizontal trench, one at a depth of eight feet and a second directly above it at five feet. This system saves space, fitting approximately 18 feet of coils in each linear foot of trench, and significantly reduces the amount of time required to complete an installation.
And according to Ponikau, the same basic design can be applied to all models, making it cost effective. “We don’t have to re-engineer or re-market everything with each house we build,” he said. “Natale sells a house, gives us the purchase order and we get to work. It’s really that simple, and by reducing our costs and adding in tax credits for the installation of a geothermal system, the homeowner ends up with a home heating and cooling system that is very close in cost to a gas-fired system and far more efficient.”
Sizing the geothermal equipment to meet the requirements of homeowners at Rivera Greens was another challenge for Ponikau. “We decided to install the WaterFurnace 3-ton 5 Series, which provides great performance and the versatility to meet everyone’s unique needs.”
Rivera Greens homeowner Duane Pusch would agree. The new fan of geothermal technology freely admits he was unfamiliar with and even a bit skeptical of geothermal before building his home. But, he read the literature provided to him, and like LaDuca, realized that geothermal technology seemed to make good sense. Eventually Pusch made the decision to install a geothermal system and became the first homeowner in the development to do so.
Pusch heated his prior home with gas, so he was well-positioned to make a comparison of that system to the new geothermal system. “First of all, the geothermal system is far more comfortable,” he said. “I don’t feel any of the hot and cold spots that were common in my former house. The geothermal system provides a much more consistent level of heating and cooling.
“It’s also cleaner,” he noted. “Seven months after the system was installed, I looked at my air filter, and it still looked clear. And you can’t mention geothermal without talking about the energy savings,” said Pusch. “My average electricity bill last July through January was $85, and that was for all the electricity in my house – lights, cooking, hot water and running the heat pump. It was great not to have a gas bill on top of that.
“Of course, it’s also better for the environment,” he added. That’s because geothermal systems do not emit any carbon dioxide, carbon monoxide or other greenhouse gasses, which are considered to be major contributors to environmental air pollution. As a result, the Department of Energy and the Environmental Protection Agency identify a geothermal system as the most environmentally friendly way to heat and cool a home.
Rivera Greens features a number of other environmentally friendly features. Homes are less than a half mile from shopping centers, recreation facilities and religious centers. A freshwater well and pond are home to natural vegetation and protected wildlife. Walking paths, composting areas and protected lands lie within 100 feet of homes. Ten acres, or 50 percent of the development, are dedicated to green space. Streetlights, the pond pump and the Rivera Greens sign are powered by a windmill. A community greenhouse is available to all residents to grow plants and vegetables. Recycling is located at the rear of the development and encouraged. Special grass in the common area has low watering needs. A public gazebo was constructed using 150-year-old wood taken from a barn that once stood on the property.
The homes, themselves, boast their own brand of environmental compatibility. Beyond the geothermal systems, the list of green features includes cradle-to-grave products like bamboo and cork flooring, low VOC paint, precast basements, LED lighting, solar panels, ENERGY STAR® rated appliances, recycled tile and low-flow plumbing.
“People are responding positively to all of these offerings. Even the geothermal system is definitely becoming more and more of a selling point, with more people asking for it,” said LaDuca. “They want to see the bills for the model we built, and when we show them an electric bill with no gas bills and lower air conditioning costs, they are impressed. Then, when you explain how to offset the electric bill with solar power, well that’s a homerun!”
The success of the geothermal installations at Rivera Greens is being repeated in other Natale homes. In fact, today, 90 percent of the builder’s clients – including homes ranging from $200,000 to $2 million — are opting for green built, geothermal supplied homes, and geothermal is rapidly becoming the standard for Natale.
According to Ponikau, the Rivera Greens model home is set between 68 and 70 degrees F, so the house is never too cold or too warm for a showing. “It’s a great demonstration of just how comfortable a geothermal heating and cooling system is,” he said. “And by combining the efficiency of the geothermal system with a solar roof, the house runs at completely net zero, sending excess power to the grid.”
To help potential customers better understand the operating cost and the performance of a geothermal system, Ponikau streams live data from a Rivera Greens home on his company’s website.
“Seeing is believing,” he said. “We’re getting positive feedback from homeowners in the development, from the people at Natale Builders and now from potential customers who can see the system perform live online. It’s hard to argue with data that regularly reinforces what we already know and the message that we want to share – that geothermal is an efficient, economical and environmentally friendly way to heat and cool a home.”