Is your plumbing business experiencing a drought? Things drying up a little bit? Jokes aside, it can be disheartening for things to slow down for your business, especially when you work for yourself. But while things might seem a little quiet right now, it doesn’t have to be this way for long. With some simple Read more
HVAC
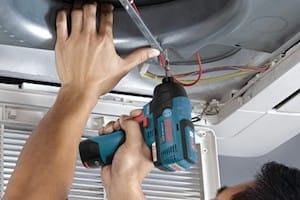
Is your plumbing business experiencing a drought? Things drying up a little bit? Jokes aside, it can be disheartening for things to slow down for your business, especially when you work for yourself. But while things might seem a little quiet right now, it doesn’t have to be this way for long. With some simple steps you can help pick yourself back up, ready for a busy summer.
Take a look at some things you can do to give your plumbing services a boost this summer.
Reconnect with existing clients
If your clients aren’t coming to you, perhaps it’s time to go to them! While you might be looking for ways to get more repeat customers, it doesn’t hurt to focus on the ones you already have. A courtesy call or email to see if there’s anything they need could be a good way to book in some work. You might even be able to offer a discount on your typical rates as an incentive.
Push summer-related services
While a lot of people need plumbing services in the winter, you could be surprised at how busy the summer months can get. Outdoor plumbing can face all kinds of issues, which isn’t ideal for your customers who need to maintain their lawns and keep their flowers healthy. It’s also a great time for people to create water features, maintain their pools, etc. Do some promotion around your summer-related services to see if you can bring some new customers on board.
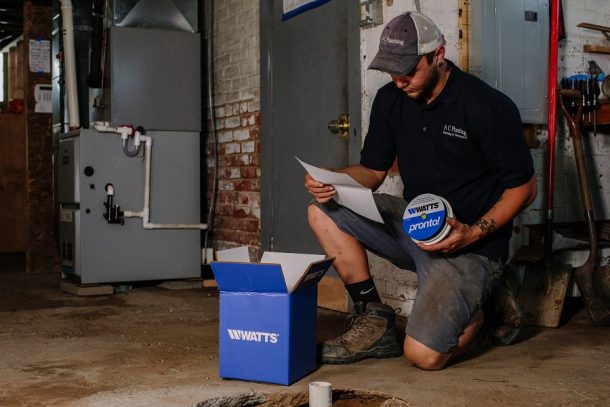
Give your customers what they want
Do your plumbing services cater to your customers’ needs? Different developments in the industry could mean that you’re behind your competition in terms of what you offer. One simple and fast way of upgrading your business is to get a chip reader so that you can accept card payments from your customers – it’s a little thing, but it can make a big difference to customers who can’t pay in cash. You should also ask about the kinds of services they’d like to see and work out if this is something you can offer your clients.
Use social media to build up recognition
Social media isn’t just for big companies with big budgets to make a splash, it’s perfect for small, local businesses like yours too. There are some effective ways of using social media for your small business, including some paid-for ads using local targeting. Even showing off your latest work can be a good way to get people interested – start following some people local to your area and start pushing your services.
It’s normal for businesses to experience quiet periods, but that doesn’t mean you have to stay idle during this time. You can use this time to market your services, but it can also be a chance to do some additional training so that you can offer even more services to your clients. It could also be an excuse to take a much-needed vacation, so that you’re nice and refreshed ready for the next busy period!
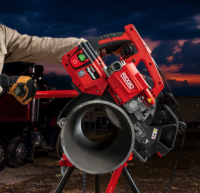
Cut 10-inch schedule 40 pipe in just over a minute with this purpose-built pipe saw from RIDGID, a part of Emerson’s professional tools portfolio. RIDGID®, a part of Emerson’s professional tools portfolio, introduces a new tool for cutting pipe quickly and efficiently: the Pipe Saw. Whether in the fab shop or in the field, the Read more
Cut 10-inch schedule 40 pipe in just over a minute with this purpose-built pipe saw from RIDGID, a part of Emerson’s professional tools portfolio.
RIDGID®, a part of Emerson’s professional tools portfolio, introduces a new tool for cutting pipe quickly and efficiently: the Pipe Saw. Whether in the fab shop or in the field, the fully transportable Pipe Saw cuts 1-inch to 12-inch pipe up to a 1⁄2-inch wall thickness.
Designed for versatility, the Pipe Saw is configured to cut steel and stainless steel and with a quick switch to one of the optional blades it can cut plastic and cast steel. Eliminating the need to struggle with gas tanks, open flames, or handle loose tools, the Pipe Saw secures to the pipe with a rugged 3-point roller system that sets up and cuts up to 12-inch pipe in minutes.
Conveniently placed handlebars and feed rate speed monitoring with LED interface enable easily controlled rotation from a comfortable, ergonomic position. Built-in handles and dedicated cord wrap provide easy portability.
“Since introducing the RIDGID B-500 Transportable Pipe Beveller a few years ago, RIDGID saw a need for a portable cutting solution. Our new Pipe Saw is the answer and ideal complement,” said Larry Feskanich, senior global marketing manager, pipe fabrication, RIDGID for Emerson. “The speed and efficiency in making quality cuts, paired with its ergonomic and easily transportable design, make the RIDGID Pipe Saw an ideal cutting solution.”
The Pipe Saw comes backed by the RIDGID full lifetime warranty.
To purchase or learn more about the Pipe Saw, contact your local distributor, visit RIDGID.com,
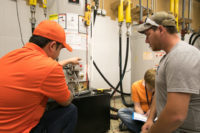
Top water heating manufacturer joins non-profit service organization for shared focus on education and workforce development Bradford White Corporation announces a partnership with Plumbers Without Borders, a grassroots non-profit organization working to increase global access to safe water and sanitation. The partnership affirms Bradford White’s commitment to impactful engagement within the industry and supports Plumbers Without Read more
Top water heating manufacturer joins non-profit service organization for shared focus on education and workforce development
Bradford White Corporation announces a partnership with Plumbers Without Borders, a grassroots non-profit organization working to increase global access to safe water and sanitation.
The partnership affirms Bradford White’s commitment to impactful engagement within the industry and supports Plumbers Without Borders’ ongoing contributions to professional training, promoting careers in the trades and maintaining the industry’s commitment to the highest standards of quality for products and services.

“Plumbers Without Borders is a unique organization that demonstrates the generosity and goodwill of the hard-working men and women in our industry,” said Carl Pinto, Jr., senior director of marketing communications for Bradford White. “Our company has always been dedicated to social leadership and to strengthening the plumbing and water heater industry. Helping uplift the work of Plumbers Without Borders not only supports their noble work around the world, it’s an investment in showcasing the essential nature of the work we do every day.”
Plumbers Without Borders was founded in 2010. The organization connects volunteer plumbers and other skilled tradespeople with projects around the world that are establishing safe plumbing and sanitary systems and promoting related health and safety education. Plumbers Without Borders selects partners based on quality, service, craftsmanship and training.
“It’s an honor to partner with Bradford White Corporation,” said Domenico DiGregorio, president and co-founder of Plumbers Without Borders. “Our mutual respect for quality, craftsmanship, professional training and workforce development creates a great platform for advancing our collective work toward improving lives and health around the world by increasing access to safe water and sanitation.”
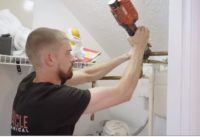
A part of Emerson’s professional tools portfolio, RIDGID is proud to support trade professionals giving back to the community RIDGID®, a part of Emerson’s professional tools portfolio, today announced their sponsorship of the first Miracle Mechanical project, a new initiative that completes plumbing, heating and air conditioning work for those in need at no-cost to Read more
A part of Emerson’s professional tools portfolio, RIDGID is proud to support trade professionals giving back to the community
RIDGID®, a part of Emerson’s professional tools portfolio, today announced their sponsorship of the first Miracle Mechanical project, a new initiative that completes plumbing, heating and air conditioning work for those in need at no-cost to the homeowner. The non-profit, headquartered in Georgia, is spearheaded by plumbing and mechanical contractor Brent Ridley.
“I have been doing tool reviews for many years, but I wanted to do more with my platform and really try to help some folks,” said Ridley, who along with working as a contractor is also a tool reviewer and co-host of the Tool Pros podcast.
The Miracle Mechanical team recently completed its first project for homeowner Nick Hendricks and his family in Monroe, Georgia. Hendricks had been seriously injured in a car accident. While he was recovering, the family’s home began experiencing septic system issues.
“The repairs mean everything to us at a time like this,” Hendricks said. “It had come to a point that we were afraid when it rained that the toilet downstairs would overflow due to groundwater getting in the septic and backing up through the toilet! Any time it rained the toilet would bubble and gargle and it was very unsettling.”
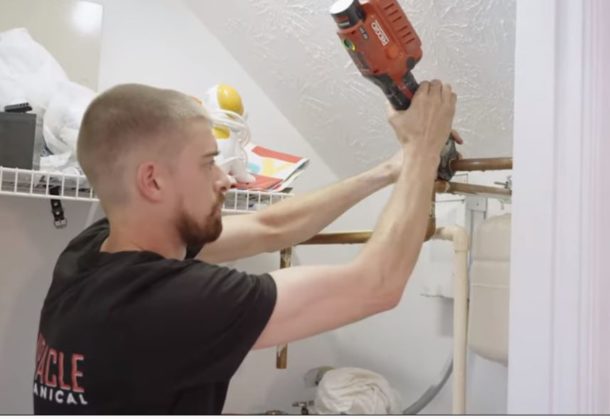
The Miracle Mechanical team repaired the septic system issues to prevent sewage from backing up in the house. They also installed three new toilets, repaired kitchen sink piping and installed a new electric water heater.
“At RIDGID we’re committed to not only supporting the trades, but also giving back to the community,” said Becky Brotherton, Senior Marketing Communications Manager, RIDGID for Emerson. “It’s a privilege for our team to be a financial supporter of the work Miracle Mechanical is doing to help others.”
https://youtu.be/0FL3hvxn2sY
Emerson’s professional tools business, which includes RIDGID as well as the Greenlee® and Klauke® brands, provides the industry’s broadest portfolio of advanced, reliable tools and technologies for the mechanical, electrical and plumbing trades globally.
Visit emerson.com/professionaltools for more information.
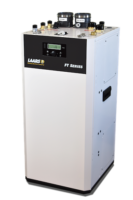
The new floor-standing FT Series Combination Boiler and Water Heater is the only residential combi boiler that delivers uninterrupted home heat and on-demand hot water simultaneously. Laars Heating Systemsannounces the launch of its powerful, ultra-high efficiency floor-standing FT Series Combination Boiler and Water Heater, the only residential combi boiler that simultaneously supplies abundant home heat Read more
The new floor-standing FT Series Combination Boiler and Water Heater is the only residential combi boiler that delivers uninterrupted home heat and on-demand hot water simultaneously.
Laars Heating Systemsannounces the launch of its powerful, ultra-high efficiency floor-standing FT Series Combination Boiler and Water Heater, the only residential combi boiler that simultaneously supplies abundant home heat and endless hot water without interruption.
“Home heat and hot water are critical to health and comfort in our daily lives,” said Chuck O’Donnell, director of marketing for Laars Heating Systems. “The Laars floor-standing FT Series Combination Boiler and Water Heater, like the rest of the FT Series of products, is built to meet the needs for space heating and domestic hot water reliably, efficiently and economically.”
The FT Series Combination Boiler and Water Heater includes a unique, integrated domestic hot water mini-indirect tank that delivers stable hot water on demand. Advanced smart technology coordinates uninterrupted space heating with domestic hot water demand and ensures continuing hot water supply for multiple heating events.
With industry-leading capacity, the FT Series Combination Boiler and Water Heater can deliver six gallons per minute of hot water in the first minute and 5.2 gallons per minute continuous delivery at a 70°F temperature rise. Other features include domestic hot water recirculation compatible; built-in low loss header for ease of installation; robust stainless-steel fire-tube heat exchanger; top piping connections for flexible installation; and large front access for service and maintenance.
“The Laars floor-standing FT Series Combination Boiler and Water Heater offers a unique combination of performance, efficiency and convenience,” O’Donnell said. “Based on extensive feedback from heating professionals, multiple features have been incorporated that make installation and service straightforward and accessible, and also provide options for homeowners.”
For more information, visit http://www.laars.com.