The COVID-19 pandemic is causing commercial buildings such as day care facilities, hotels, schools and health clubs to remain closed for abnormally long periods. When the coast is clear to begin reopening, ensuring safe and sanitary plumbing water will be of utmost importance. Plumbing systems left idle can be susceptible to harmful bacteria such as Read more
legionella
The COVID-19 pandemic is causing commercial buildings such as day care facilities, hotels, schools and health clubs to remain closed for abnormally long periods. When the coast is clear to begin reopening, ensuring safe and sanitary plumbing water will be of utmost importance. Plumbing systems left idle can be susceptible to harmful bacteria such as Legionella which can proliferate to dangerous concentrations.
Experienced water maintenance managers know susceptible systems should be flushed before reusing. Important considerations should not be overlooked such as ensuring all service lines are purged and dead legs drained.
Several factors determine if the system equipment requires treatment such as how long a system is left idle, the temperature of the stagnated water and condition of the internal surfaces. This is so bacteria that are resistant to simple purging/draining and have become resident in biofilm can be addressed. Common methods include thermal treatment or treating with chemicals such as chlorine, chlorinated gas and chlorine dioxide.
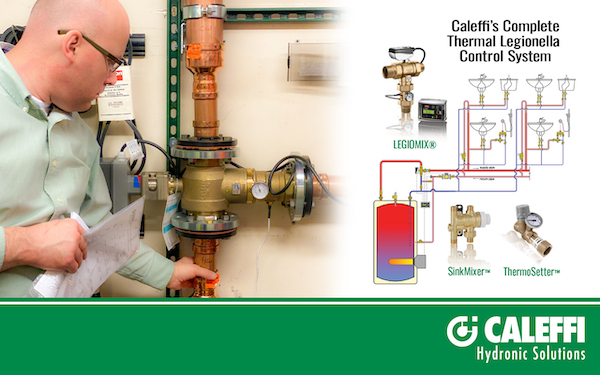
A significant benefit of thermal treatment is that it’s a proven, cost-effective method for bacteria management on an ongoing basis in the hot side of the plumbing system. The cold side doesn’t typically require ongoing treatment unless water remains stagnated for extended periods within the temperature range that Legionella grows which is 68°F to 122°F.
Thermal treatment requires little additional maintenance compared to chemical treatment. Also, common plumbing equipment such as seals, gaskets and polymer components are not exposed to potentially incompatible life-shortening chemicals.
Residual chemicals in the water can also be a human health concern if acceptable concentration values are exceeded. In contrast, most common plumbing materials can withstand, without effect, thermal shock temperatures such as 160°F.
Thermal treatment consists of periodically circulating elevated water temperature such as 160°F through the entire system for a specific and measured period of time, thereby killing harmful bacteria and restoring the water to a safe and usable condition. During this period it is important to ensure all point-of-use fixtures are either disabled for access or equipped with anti-scald devices. An example is the Caleffi scald-protection valve SinkMixerTM — an innovative, easy to install valve for under-sink applications.
Often the most difficult portions of the hot water side to circulate sufficiently through is the recirculation return risers. This because they are sized and balanced to a relatively low flow rate such as 0.5 GPM. The Caleffi ThermoSetterTM thermal balancing valve automatically responds when it senses high temperature water by fully opening an internal by-pass, thereby allowing a sufficient return riser flushing during treatment. It then automatically returns to standard operation state when water temperature decreases to normal.
If a building is equipped with a Caleffi LEGIOMIX digital mixing valve, it will enjoy highly accurate mixed water temperature 24/7. The LEGIOMIX has industry-unique, calendar- based automatic thermal disinfection programs. For thermal monitoring, it has data logging capabilities and can connect to a building automation system for remote monitoring and access.
LEGIOMIX combined with SinkMixer anti-scald valves and ThermoSetter recirculation balancing valves offer an innovative total thermal solution for control of safe and sanitary domestic hot water.
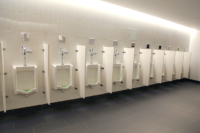
Ron George, CPD Below is a recommended flushing procedure for building owners, property managers, water utilities, health officials, code officials, service contractors, engineers, insurance companies and Interested parties to perform on buildings before re-opening buildings for occupancy after a long shut-down. With the recent coronavirus events causing many stay-at-home orders and extended vacancy of offices Read more
Ron George, CPD
Below is a recommended flushing procedure for building owners, property managers, water utilities, health officials, code officials, service contractors, engineers, insurance companies and Interested parties to perform on buildings before re-opening buildings for occupancy after a long shut-down.
With the recent coronavirus events causing many stay-at-home orders and extended vacancy of offices and workplaces, there is a looming, serious issue associated with stagnant water or aging water in the plumbing tanks, fixtures and pipes of buildings that have not been occupied for long periods of time. Bacteria will grow and flourish in the biofilm of the plumbing tanks, fixtures and pipes that have been sitting stagnant with ambient temperature or warm water where the water treatment chemicals have dissipated to levels that will not control bacterial growth. Studies have shown water treatment chemicals dissipate over time and there are several factors that affect the rate of dissipation such as pipe material, temperature, and organic contaminants in the water.
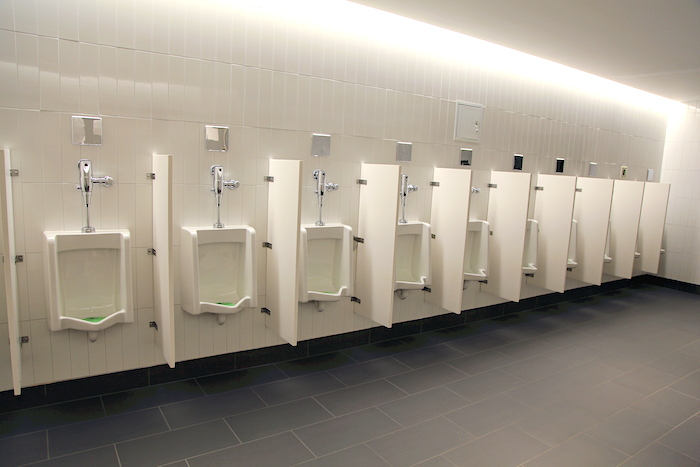
After the chlorine dissipates, bacteria can grow to high numbers. When bacteria and microorganisms are aerosolized in water from showers and other fixtures that can aerosolize the water it can be inhaled into the lungs causing Legionellosis or Legionnaires’ disease. Therefore, it is important to flush these stagnant pipes of bacteria laden water before re-occupying the buildings that have been vacant for long periods of time. I have been involved in developing Legionella standards & guidelines with ASHRAE and ASSE and I have spent over 42 years designing plumbing systems to simultaneously prevent scalding and Legionnaires disease. There are standards for flushing and disinfecting large public water mains but, there is no consensus standard for flushing and disinfecting plumbing systems within buildings.
In early 2020, government officials issued stay at home orders, with guidance from health officials, which has caused many buildings to sit abandoned with little to no water usage for weeks or months. When a building has been empty or unoccupied for an extended period, bacteria like Legionella and various other bacteria, viruses or disease-causing organisms can be found in inadequately treated water or stagnant water after the water treatment chemicals dissipate.
Before re-occupying a building that has been unoccupied for an extended period, it is recommended to flush stagnant water from the piping system before opening the building to occupants. To minimize to chances of transmission of Legionella bacteria and other microorganisms to humans, flushing water from the plumbing fixtures is the easiest, quickest and cheapest way to prepare for occupants to return to the building.
I am encouraging government officials, health officials, water utilities, code officials and other non-profits to implement these simple and inexpensive flushing procedures into national, state and local ordinances or guidelines to help protect the occupants of buildings from bacteria laden water upon return to buildings that have been sitting idle for long periods of time. These entities should use the language in this document and create a local flushing and disinfection ordinance for documentation of flushing procedures before opening and occupying buildings that have been idle for long periods of time. The government entity can decide what length of shut-down justifies flushing based on chlorine or other water treatment dissipation rates in your area. If a building has been idle for more than four weeks, a Legionella test should be conducted on first draw water before flushing to determine if a chemical disinfection procedure is needed to be performed. Chemical disinfection should be performed on the hot water system before heating the water.
Domestic Water Systems Flushing Procedure:
Building Address: ________________________________________ Flushing Date: ______________
Name of Persons Conducting the flush 0peration:_______________________________________________________________________ _______________________________________________________________________
For documenting the flushing operations, follow the tasks outlined below. Building owners or maintenance staff should be advised to perform these flushing operations in all buildings that have been closed for an extended period. This will reduce the risk of illness and death following a building that has been unoccupied for a long period. The objective is to replace all stagnant water in the potable water system with new water containing a disinfectant residual from the municipal distribution system.
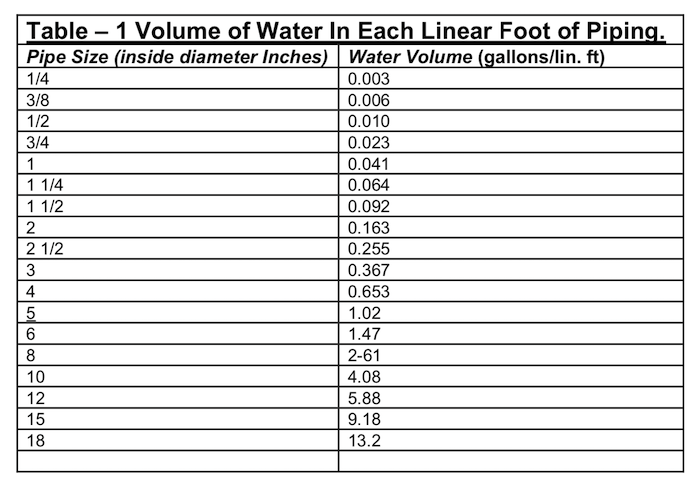
Flushing personnel should wear an “N-95 respirator mask” and Personal Protective Equipment during flushing operations. When performing a flushing operation, complete the following flushing procedure in the following sequence:
1. Collect a water sample of first draw water for testing the water treatment chemical residuals in the building service pipe. Collect the sample from a monitoring point in the service pipe at or near the meter and backflow preventer or where the service pipe enters the building.
Note the Water utilities water treatment chemical type. This pre-flush test should be serve as a baseline to compare pre-flush water quality with post flush water quality.
Locaton ______________________; Free Chlorine Residual: _____ppm; Test By: ______; Time: ______ am/pm
Location ______________________; Legionella Test1: _________ cfu/ml; Test By: ______; Time: ______ am/pm
(Note 1. – Conduct a Legionella test if the building has been significantly unoccupied for more than 14 days.)
If the pre-flush water quality test indicates any water discoloration, odor or other unusual characteristics note them below:
Notes:_________________________________________________________________________________________________
2. Collect a water sample from first draw water of at least five (5) remote locations within the building to determine the building water chemical residuals in the building. These locations should be documented for to serve as a baseline pre-flush to post flush to compare pre-flush water quality with post flush water quality.
Loc. #1 ______________________; Free Chlorine Residual: _____ppm; Test By: ______; Time: ______ am/pm
Loc. #1 ______________________; Legionella Test1: _________ cfu/ml; Test By: ______; Time: ______ am/pm
Loc. #2 ______________________; Free Chlorine Residual: _____ppm; Test By: ______; Time: ______ am/pm
Loc. #2 ______________________; Legionella Test1: _________ cfu/ml; Test By: ______; Time: ______ am/pm
Loc. #3 ______________________; Free Chlorine Residual: _____ppm; Test By: ______; Time: ______ am/pm
Loc. #3 ______________________; Legionella Test1: _________ cfu/ml; Test By: ______; Time: ______ am/pm
Loc. #4 ______________________; Free Chlorine Residual: _____ppm; Test By: ______; Time: ______ am/pm
Loc. #4 ______________________; Legionella Test1: _________ cfu/ml; Test By: ______; Time: ______ am/pm
Loc. #5 ______________________; Free Chlorine Residual: _____ppm; Test By: ______; Time: ______ am/pm
Loc. #5 ______________________; Legionella Test1: _________ cfu/ml; Test By: ______; Time: ______ am/pm
If the pre-flush water quality test indicates any water discoloration, odor or other unusual characteristics note them below:
Sampling Notes: __________________________________________________________________________________________________________________________________________________________________________________________________
(Note 1. – Conduct a Legionella test if the building has been significantly unoccupied for more than 14 days.)
3. Determine the building service pipe size and length. Service pipe size: _________ , Volume gallons per Linear foot Service pipe length: _________
4. Determine the volume in the building service pipe based upon its size and length in Table 1 below and multiply the volume by 2 for the required volume to be flushed from the service piping.
Service pipe volume from Table 1: _________ (Linear feet of service pipe x volume per foot from #3 above)
Service pipe volume from Table 1 x 2 = _________ Note 2
Note 2 – Volume of water to be flushed through the service pipe at 3 feet per second velocity per Table 2.
5. Determine and document the quantity and location of the fixtures required to be flowed simultaneously to have a velocity of 3 feet per second in the service pipe. (See table X) and hose valves will be flowing from the required number of flushing points in order to have a flushing velocity high enough to scour bio-film and sediment from the service pipe at a flow velocity in excess of 3 feet per second as determined in table 2.
6. Perform and document a pre-flush water quality test at the water service entrance and at 5 remote fixtures to determine water quality and water treatment residual, There should be a minimum 1 part per million (ppm) free chlorine at the building service entrance and 0.5ppm of free chlorine at the most remote fixture. For buildings with other water treatment chemicals in the utility water, consult with a professional for recommended minimum water treatment chemical levels or as directed by the facilities’ water management program team) entering the building. If the test shows the water quality is good, then no service pipe flushing is needed.
7. If the pre-flush water quality test indicates any water discoloration, odor or lack of sufficient free chlorine residual, perform and document a full velocity flush of 3 feet per second for the building water service pipe as follows:
a) Determining the proper number of fixtures to flow to flush the building service pipe at a minimum velocity of 3 feet per second, based on the size of the building service pipe size, (See table 2)b) The flow can be through a combination of fixtures can be flowed through a combination of hose bibbs, hydrants and fixtures near the water service entrance. and test the potable water service connection until a disinfectant residual is detected or a volume equivalent to double the water held in the service connection is cleared, whichever occurs first.
8. If a disinfection residual is not detected, after 30 minutes of flushing the building service pipe, Stop flushing and do not continue with the potable water system flushing operation. Contact the water utility for direction and ask to have them or the fire department flush the water mains through nearby fire hydrants to bring chlorinated water close to the building. If the building is in a cluster of buildings or area with many unoccupied buildings ther may be a logical place to flush a hydrant near the end of the water main.
9. When a disinfectant residual is detected on the building service pipe, open some faucets that are the farthest away from the building water service and on the end of each major branch main of the water distribution piping and let the hot and cold water run continuously until a disinfectant concentration is detected close to or equal to that of the chlorine residuals in the building service connection. A branch main is defined as a main distribution pipe (typically greater than 3⁄4” diameter) which supplies other branch pipes and fixture branch pipes.
10. Flush all remaining fixtures, tanks, and appliances connected to the potable water system (including exterior outlets). Flow water from both the hot and cold water systems. The following flushing procedure should be used based on each fixture type:
- Toilets and urinals shall be flushed 5 times each for 1.6 gpf fixtures.
- All other fixtures shall be flushed for a minimum of 3 minutes each, both hot and cold water with flows of 2 gpm.
- Any water storage or hot water tanks should be flushed at a rate to flow at least 2 times the volume of the tank.
- Hydro-pneumatic and thermal expansion tanks should have the water pressure relieved from them so that they totally discharge all water within the tank.
Infra-red faucets shall be operated for a consecutive period of time equal to 20 cycles for every 10 feet of 3⁄4 inch branch piping.11. The person performing the flushing operation should record the room number, the fixture type & ID, flow rate in gpm, start time and temperature, end time & temperature, chlorine residual near end of flushing operation, and notes or observations for each fixture like: ambient temperature of the room, when the water temperature starts to change indicating fresh water is arriving at fixture, chlorine residuals in the first draw and at completion. thereafter until a minimum chlorine residual of 0.5 ppm is achieved at each fixture. Take a water sample in the first draw and upon completion of the flushing and Note any water discoloration, odor, etc) for first draw and test the chlorine residual in the final draw at the completion of the flushing operation. If the measured chemical residual is insufficient to control bacteria growth, perform and record the flushing operation as shown on the following “Fixture Flushing Record Sheet.”
12. The water utility has a duty to deliver safe drinking water to the building service meter according to the safe drinking water act. Note: the utilities are allowed fall below the level of quality in the safe drinking water act for three, consecutive 6-month reporting periods before they must notify the public. The responsibility for building water safety is the responsibility of the building owner. The drinking water provider has no responsibility for water quality on the building side of the water meter. A water utility should strive to deliver quality water, but we know that the water utilities cannot guarantee safe drinking water because there are often water main breaks, construction, fire events and other disruptions of water main flows that cause turbid water and high bacteria events. For this reason, the building owner has a duty and responsibility to monitor the water quality coming into their building and have a water management plan in place to address water quality issues. In this day of water conservation, water flows have been reduced to levels that are less than 20 percent of flows prior to 1992. The flow in water mains have been reduced to the point where water treatment chemical residuals dissipate to levels that will not control bacteria growth in the water mains. Building owners must monitor the incoming water and adjust the water quality if needed by using supplementary water treatment systems. When a building owner is considering a supplementary treatment system, they should consult with a professional to determine if they need licensing, certification and any filters.
13. When a building is unoccupied for more than 7 days or a period of time agreed to by the building’s water management Program team, flushing should be performed immediately prior to re-occupancy. When a building is unoccupied for more than four weeks (28 days), or a period of time agreed to by the building’s water management Program team, flushing and disinfection should be done immediately prior to the building being reoccupied.
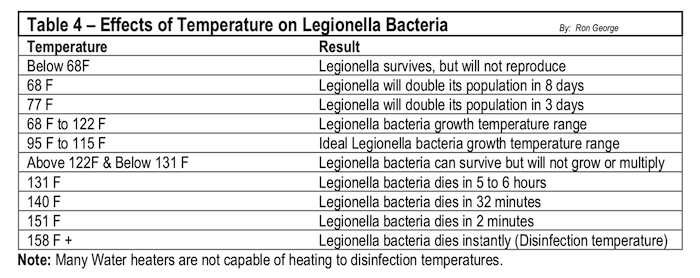
Note: Flush all sinks first, then flush showers, then flush water closets & urinals. Fixtures with flush valves can become clogged with debris and not flush properly if they are flushed first. If flush valves do not perform properly and run-on, shut off water and remove diaphragm and clean the orifice. When done flushing, remove faucet strainers and shower heads and clean or replace them.
Storage Water heaters should be maintained at a minimum temperature of 140F or higher in the tank as needed to offset heat loss and maintain a minimum hot water temperature at the lowest temperature in the system a couple of degrees above the Legionella Growth temperature of 122 F. (124 F) on the hot water return pipe connection to the water heater. The hot water return pipe just before the cold water connection to the water heater is the lowest temperature point in the hot water system. See the “Temperature Effects on Legionella Bacteria Table” Below. To prevent Sclading, all shower valve maximum temperature limit-stops should be adjusted to a maximum temperature of 115 F at showers & bathtubs to prevent scalding. (Consider a maximum temperature limit stop setting for showers and tub/showers of 110 F at hospitals, nursing homes and similar facilities where there is additional risk of scalding.)
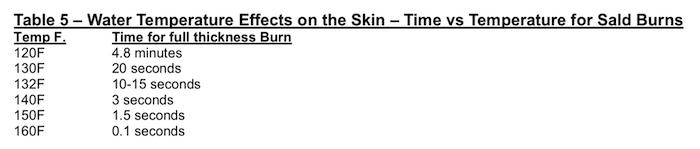
Hot water temperatures can be higher in the storage and distribution piping and should be reduced or limited at or near the fixtures by code compliant temperature limit-stops that are properly adjusted on tub/shower valves or by temperature limiting valves that are properly set to limit temperatures at the point of use.
Every fixture in the building should be flushed in accordance with these guidelines or until the water treatment chemical residuals reach an acceptable level. Following these procedures should prevent thousands of workers from getting sick and dying from Legionnaires disease and other types of waterborne illnesses associated with stagnant water.
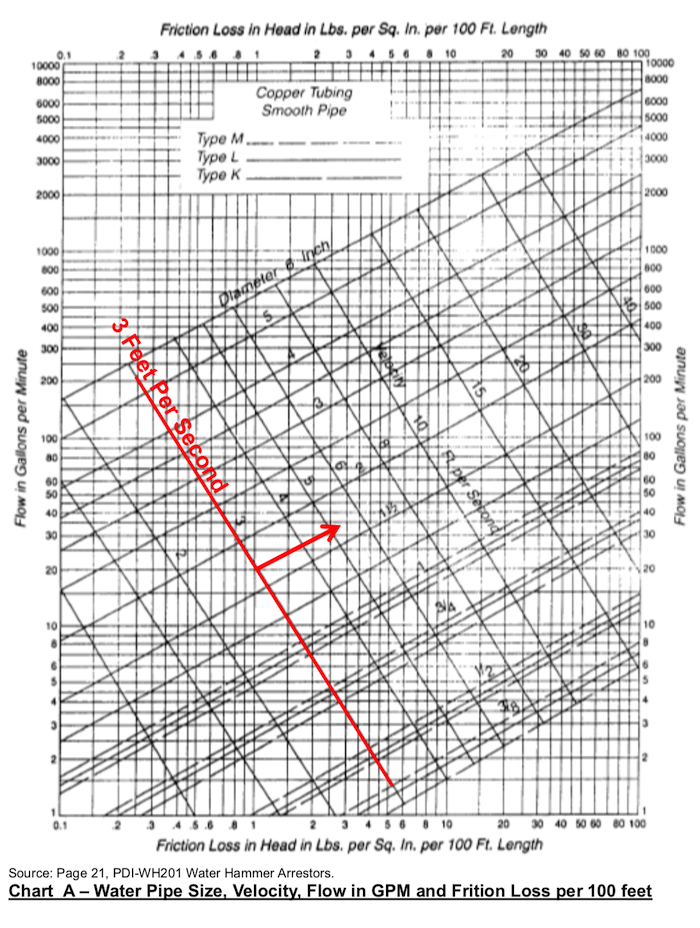
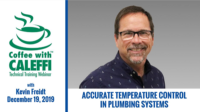
The importance of proper domestic hot water (DHW) temperature control in providing comfort, safety and convenience cannot be overstated. Delivering it remains one of the most important responsibilities of plumbing system designers. Kevin Freidt, Caleffi director of product management and technical support, will discuss temperature control at the hot water source, at the point-of-use, in the Read more
The importance of proper domestic hot water (DHW) temperature control in providing comfort, safety and convenience cannot be overstated. Delivering it remains one of the most important responsibilities of plumbing system designers. Kevin Freidt, Caleffi director of product management and technical support, will discuss temperature control at the hot water source, at the point-of-use, in the balanced secondary circuits and in the system as a whole.
You’ll learn:
→ What methods are used to control temperature at the DHW source?
→ What is different about controlling hot water temperature at the source vs. at the point-of-use?
→ Mixing valve standards ASSE 1017, ASSE 1070 and other related ASSE standards.
→ Can an instantaneous heater take the place of a mixing valve?
→ Are electronic mixing valves more accurate than thermostatic mixing valves?
→ How do I properly size and install a mixing valve to assure accuracy?
→ What are some causes of the loss of accuracy in a mixing valve?
→ What about temperature control and balancing of secondary piping circuits when I have recirculation?
→ What does accurate temperature control have to do with preventing Legionella bacteria issues?
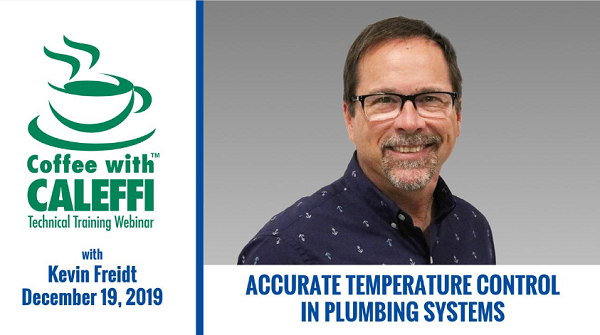
Freidt is the intellect behind sizing up the best product offerings in a moving target market and manages an exceptional technical support team. He has a B.S. in Mechanical Engineering Technology, 35+ years’ of experience in the commercial HVAC industry and is a LEED AP. Our audience will thoroughly appreciate his academic passion and concise content delivery.
Coffee with Caleffi technical training webinars are free and intended for contractors, designers and wholesalers. By submitting your webinar registration, you are consenting to email communications to keep you up-to-date on industry news. A Certificate of Attendance is emailed to attendees following the webinar.
Missed a webinar? No problem, our webinar archive is available 24/7 for your convenience.
If you have questions on webinar content, please direct them to bob.rohr@caleffi.com.
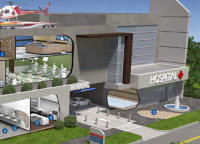
“They always put up the stop sign at the dangerous intersection after a horrible accident, right?” said an editorial colleague in response to a side conversation regarding a Legionella presentation at the 2nd Healthcare Symposium hosted by Watts Water Technologies. The symposium featured four high-level executives whose expertise centered around a comprehensive approach to mitigating Read more
“They always put up the stop sign at the dangerous intersection after a horrible accident, right?” said an editorial colleague in response to a side conversation regarding a Legionella presentation at the 2nd Healthcare Symposium hosted by Watts Water Technologies. The symposium featured four high-level executives whose expertise centered around a comprehensive approach to mitigating opportunistic waterborne pathogens, especially Legionella.
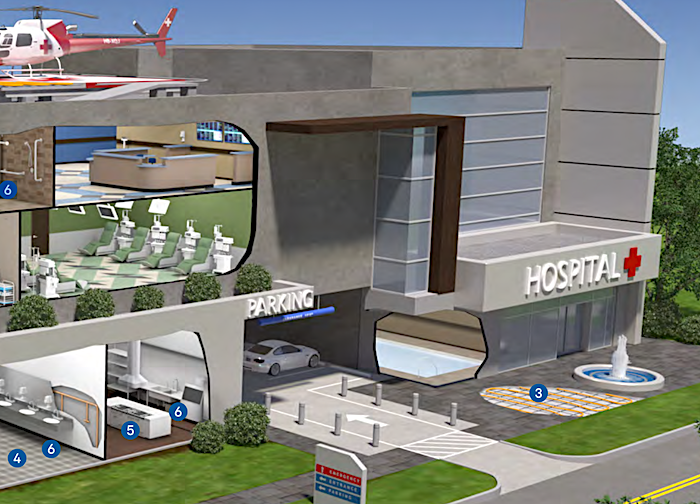
Image courtesy of Watts Water Technologies
When it comes to Legionella assessment, for example, there is continued debate throughout the industry on cost justification vs. actual risk. What is the cost of not putting a water safety plan in place? Injury, death, lawsuits, negative publicity, etc. Is this not enough to be acting now toward a more proactive approach to mitigation? Although Legionella can’t be completely “eradicated” in plumbing systems, implementing safeguards and following through with proper processes to keep a healthcare facility relatively “safe” from opportunistic pathogens—while it does incur a cost—should be the proper approach, and it is fiscally responsible.
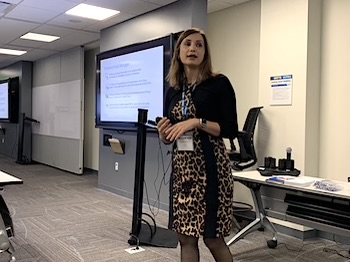
Shatha Salah
The proactive vs. reactive conversation stemmed as a response to the presentation by Shatha Salah, Environmental Manager, UAB Medicine, the first of four speakers at the symposium. Following a Legionella outbreak at the University Hospital, Salah is now responsible for directing and managing the UAB Medicine Water Safety Plan and serves as a member on the UAB Medicine water safety team. “It’s important to create a team for a water safety plan, which includes plumbers who are the front-line soldiers in the fight against Legionella,” says Salah. “The plumber’s role is important in protecting patients from waterborne illnesses.”
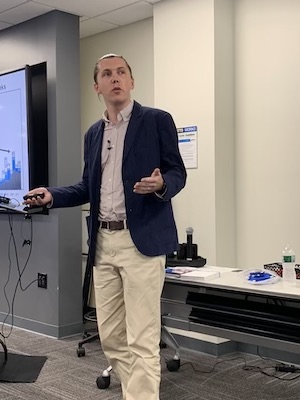
William Rhoads
Through a combination of a supplemental water treatment system and point-of-use filters, UAB gained control of Legionella growth in the building and began developing a comprehensive water safety plan, engaging team members that can take action and influence process change to conduct risk assessments to help mitigate the growth and distribution of waterborne pathogens.
Dr. William Rhoads, EIT, PhD, postdoctoral researcher, Virginia Tech, focused on the importance of proper assessment of engineering controls and understanding water quality with his “Controlling Opportunistic Pathogen Growth in Building Plumbing” presentation.
Rhoads suggests some Engineering Control Strategies:
- Control Water Age—flow conditions
• Limit Nutrients
• Pipe Material Selection
• Secondary Residual Type and Dose—including in-building treatment - Water Heater Set Point— including thermal shock
- Probiotic/Prebiotic
• Upgrade Water Mains
• System Design—hot water recirc, piping strategy
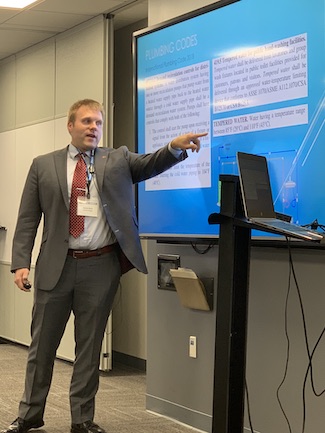
Aaron Bock, Cannon Design
Why the increased incidence of Legionella? Rhoads suggests a few reasons: improved detection and diagnosis; people are spending more time indoors; changing demographics and immunodeficiency status; and the unintended consequences of more sustainable buildings and cities. “Sustainability in buildings may increase water age—the Distribution System Water Age + Precise Plumbing System Water Age—which can lead to more opportunistic pathogens,” says Rhoads.
Piggybacking Rhoads’ points, Aaron Bock, PE, CPD, Plumbing and Fire Protection Discipline Leader, Cannon Design, suggests that some challenges include building codes, standards and guideline; equipment and fixtures; and building piping and design. Items such as low flow and seldomly used fixtures can lead to stagnant water, which encourages bacterial growth, says Bock. Programmable sensor faucets, for instance, should be chosen carefully and limited to high-traffic areas. Other concerns include water system size and age, building location, equipment and appliances and uncirculated piping can all lead to problems.
Bock’s solutions include:
- Plumbing System Design
Selection of Fixtures & Materials
– Laminar Flow or Open Faucet Spouts
– Placement of Fixtures
– Sanitizable Fixtures & Piping Materials
– Hands-Free Faucet Operation
– Sensors in Public Areas Only
Temperature & Flow Maintenance
– Limiting uncirculated water piping accomplishes both
– Recognize devices/piping that create stagnation
– Don’t ignore cold water systems
– Isolation of System Sections
- Chemical/Ion Injection
– Chlorine
– Chlorine Dioxide
– Monochloromine
– Copper-Silver Ionization
- Supplemental Measures
– Elevated Water Temperatures
– Ultrafiltration—Total Building, Hot Water, Point-of-Use
Moreover, Bock suggests implementing Design, Construction and Occupancy Phases, which include fixture selection and future provisions during the design, flushing and disinfecting water lines during construction, and water management plans, monitoring control points and maintenance during occupancy. “It’s important to education building owners during the design phase,” says Bock.
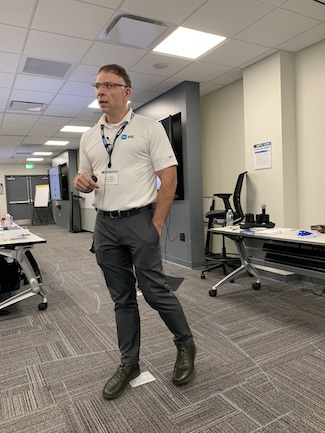
Frank Sidari, Special Pathogens Laboratory
Frank Sidari, Technical Director, Special Pathogens Laboratory, an encore speaker from the Watts’ inaugural Healthcare Symposium, placed continued emphasis on the importance of a water management plan. Sidari focused on a closer inspection on how engineers, facility managers and infection control can work to manage building water systems to reduce the risk associated with opportunistic waterborne pathogens and coordinate efforts with their water safety and management program. Interestingly, he cited a National Academies of Sciences, Engineering, and Medicine (NASEM) report that states, “Stronger policies are needed to protect the public against Legionnaires’ Disease.”
Perhaps building codes and standards can take a more focused look in mandating more stringent building compliance when it comes to mitigation and a tangible action plan. In the meantime the bottom line is this: it is better to be proactive than reactive when considering water safety and pathogen mitigation in healthcare facilities.
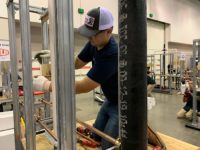
The Week in Review is a recap of the week — what’s trending, what’s breaking the internet on social, and what we’ve been up to. We’ll try our best to keep you up to date with the industry, social media and our travels. It’s been a pretty busy couple of weeks for the Mechanical Hub team Read more
The Week in Review is a recap of the week — what’s trending, what’s breaking the internet on social, and what we’ve been up to. We’ll try our best to keep you up to date with the industry, social media and our travels.

Jed Christner during the Plumbing Apprentice Contest at PHCC CONNECT.
It’s been a pretty busy couple of weeks for the Mechanical Hub team. The boys headed down to Indianapolis last week (Oct. 1-3) for the PHCC CONNECT Show. I have to say there was a nice buzz to the show, and every trade show booth we visited, we heard the same positive feedback. It’s always nice to see our friend from PHCC and other industry reps. We were also there to support our plumbing apprentice contestant, Jed Christener, from JRC Mechanical, Chesapeake, Va. This is something we are very passionate about—supporting the skilled trades push!
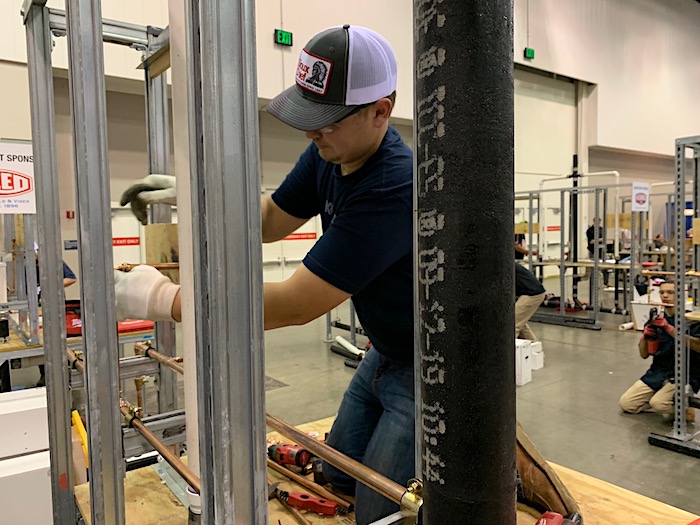
A plumbing apprentice contestant.
• To start the week, the Hub’s John Mesenbrink was in Boston for the 2nd Healthcare Symposium, hosted by Watts Water Technologies. The day was packed with critical information on the topic of opportunistic pathogens in water, especially Legionella. Shatha Salah, Environmental Manager at UAB Medicine, talked about the journey from recovering from a Legionella outbreak to developing a Water Safety Plan. Her experience includes four years of managing and implementing the ASHRAE 188 compliant water safety program that covers 19 healthcare buildings. “It’s important to get plumbers involved in a water safety plan since they are on the “front lines.” “The plumber’s role is important in protecting patients from water borne illnesses,” said Salah.
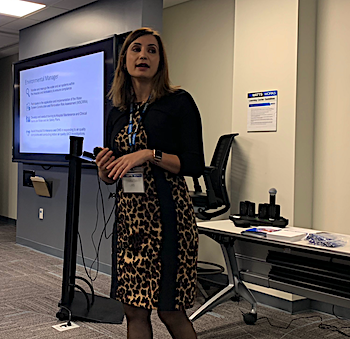
Shatha Salah
Other keynotes highlighted were Frank Sidari, Chief Consulting Engineer, Special Pathogens Lab, who cited a NASEM report that states, “Stronger policies are needed to protect the public against Legionnaires’ Disease.” Why the heck do cases continue to rise?
Dr. William Rhoads, Research Scientist, Va. Tech, touched on the idea of unintended consequences, when he said that sustainability in buildings may increase water age, which is the Distribution System Water Age + Premise Plumbing System Water Age, which can lead to more waterborne pathogens.
Finally, the Symposium featured Aaron Bock, PE, Plumbing & Fire Protection Discipline Leader Cannon Design, who says it is imperative to “educate building owners during the design phase.”
What’s interesting in all of this is why not be proactive and create the water safety plan instead of reactive when the damage is already done? Lives are at stake, potential lawsuits loom, and the overall negative press your facility might endure after the fact. It’s worth the proper investment to help mitigate against potential harmful water borne pathogens.
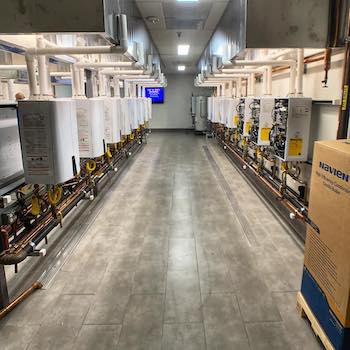
A look inside Navien’s live fire training lab at their headquarters in Irvine, Calif.
• Mid-week, the Hub’s Eric Aune headed out to SoCal to visit our friends at Navien. The attendees had a great time learning about a couple new products coming soon from Navien and touring their headquarters training center. “Navien had us out this week to their North American headquarters in Irvine, Calif., for the unveiling of two new products. We can’t say much more than that yet but watch our site and social channels on Monday for what’s new in tankless,” says Aune.
They have some interesting new things up their sleeves, but we can’t tell you until next week. Evidently, tankless will never be the same. What a tease!
• From the awesome department, Friday, October 4 through Sunday, October 6, North America’s Building Trades Unions (NABTU) successfully convened its ninth international Tradeswomen Build Nations Conference, the largest gathering of its kind in the world. More than 2800 tradeswomen representing 48 states and 10 provinces gathered in Minnesota to share experiences and best practices with fellow tradeswomen, to learn about new programs and opportunities in the industry, and to engage with top leaders from government, industry and the biggest fifteen international building trades unions.
The three-day conference, held over the weekend, featured a day of service with Haven House Ascension Place and Second Harvest Heartland, formal plenary sessions and over 25 workshops on a range of topics addressing unique and critical issues of tradeswomen.
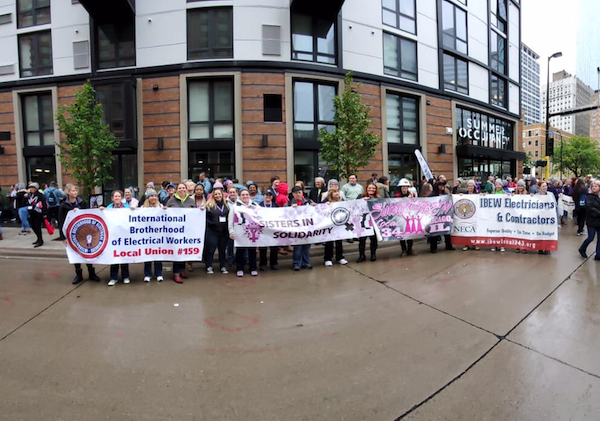
Photo Credit: @UnitedSparkies
“This conference grows exponentially every year, and the impact is phenomenal,” said NABTU President Sean McGarvey. “NABTU is committed to empowering current and future tradeswomen as we increase opportunities for and retention rates of women in fulfilling union trade careers. Every day, we recruit more women into great union construction apprenticeships and careers, and these trailblazing tradeswomen are moving up in the top ranks of leadership. This conference is a celebration of these trailblazers and a testament to the growth of tradeswomen among our ranks.
Last Saturday afternoon, participants took to the streets of downtown Minneapolis for a parade and rally. The conference concluded on Sunday with a keynote speech by UA union International President Mark McManus and a panel on pathways to apprenticeship led by Arlene Dunn, Canada’s Building Trades Unions’ Director. For info, www.nabtu.org
• This week, AHR Expo announced its 2020 Innovation Award Winners. Danfoss, LG, Fresh-Aire IV were among some of the big winners. Check here for more, https://mechanical-hub.com/ahr-expo-announces-2020-innovation-award-winners/
• Finally, I’ve noticed a story shared on social media that is making headway. PBS shared a story titled, “After decades of pushing bachelor’s degrees, U.S. needs more tradespeople. (https://www.pbs.org/newshour/education/decades-pushing-bachelors-degrees-u-s-needs-tradespeople?fbclid=IwAR3NVI0nFrF4hdrc0EItmmeqj7YcAur1eF4Ia9hxE9uv70LaPT9PviVLyjI).
We are delighted to see that more “mainstream” media types are giving this important issue the coverage it deserves. Good on them. But it also reminds me that we at Mechanical Hub have been preaching this for the past 10 years!
Here is something I wrote five years ago, which, I think, still holds water.
https://mechanical-hub.com/path-to-the-trades-starts-in-the-living-room/
So … continue to preach the good word of the trades!