By joining forces with Uponor, GF is set to become a global leader in sustainable water and flow solutions. To support this ambition, complementary businesses will be grouped together under one roof: the new division GF Uponor will focus on Building Technology, whereas the infrastructure and utility business will move to GF Piping Systems. Michael Read more
PEX piping
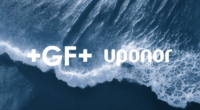
By joining forces with Uponor, GF is set to become a global leader in sustainable water and flow solutions. To support this ambition, complementary businesses will be grouped together under one roof: the new division GF Uponor will focus on Building Technology, whereas the infrastructure and utility business will move to GF Piping Systems. Michael Rauterkus will join GF’s Executive Committee and will lead the new division together with his Uponor leadership team.
After all conditions of the tender offer have been fulfilled, GF closes the transaction as of 13 November 2023.
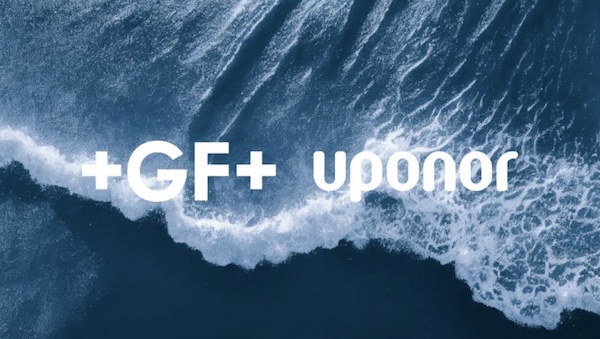
To accelerate the implementation of GF Piping Systems’ Strategy 2025 and to further benefit from global megatrends, GF will start an ambitious value creation program to unleash the full potential of this acquisition. GF Piping Systems will focus on the industrial and utility business, providing its customers with sustainable leak-free piping solutions for numerous end markets such as microelectronics, water treatment, energy, chemical processing, marine, data centers or water & gas utilities. Uponor’s infrastructure business will become part of GF Piping Systems and will further strengthen the division’s portfolio to provide customers with combined solutions.
In the new division, GF Uponor, the building technology businesses will be combined to offer a complementary portfolio for safe and clean water, as well as energy efficient heating and cooling. The consolidation of complementary businesses provides an ideal platform to develop markets with high potential for both divisions. As the brand Uponor stands for high quality and innovation, it will drive growth in intelligent Building Flow Solutions.
These organizational changes will be implemented during the course of 2024 while GF will ensure operational excellence and business continuity to customers.
“We will continue to implement our strategy, and leverage powerful global trends, such as the need for safe and clean water, or more efficient energy use,” GF CEO Andreas Müller said. “On behalf of all my colleagues, I am happy to welcome Uponor employees and start this new chapter together.”
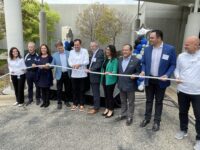
“It’s like Disney World for engineers and contractors,” said one visitor on the tour. The Mechanical Hub team made a quick visit to Apple Valley, Minn., to visit Uponor North America as the company celebrated the grand opening of its newly constructed Uponor Experience Center with a “pipe-cutting” ceremony. The team was treated to a Read more
“It’s like Disney World for engineers and contractors,” said one visitor on the tour. The Mechanical Hub team made a quick visit to Apple Valley, Minn., to visit Uponor North America as the company celebrated the grand opening of its newly constructed Uponor Experience Center with a “pipe-cutting” ceremony.

Andres Caballero (fifth from left) performs the pipe cutting for the new Uponor Experience Center.
The team was treated to a behind-the-scenes tour of the new 4,500-sq.-ft. customer experience center, which features hands-on displays, full-scale residential and commercial training areas, and cutting-edge innovation showcases, and a place to bring MEP students from the area to get a taste of the trades. The new Uponor Experience Center is a flexible education and discovery space designed to advance the technical skills of current and potential customers. In addition, it will help foster innovation within the plumbing and HVAC industry and provide an immersive experience for employees and visitors alike.

Some displays mimicked true applications.
The new Uponor Experience Center occupies the company’s previous customer training area, which was originally built in 2000 and renovated in 2010. It is at the center of the North American headquarters campus, surrounded by corporate offices, an R&D facility, and manufacturing space.
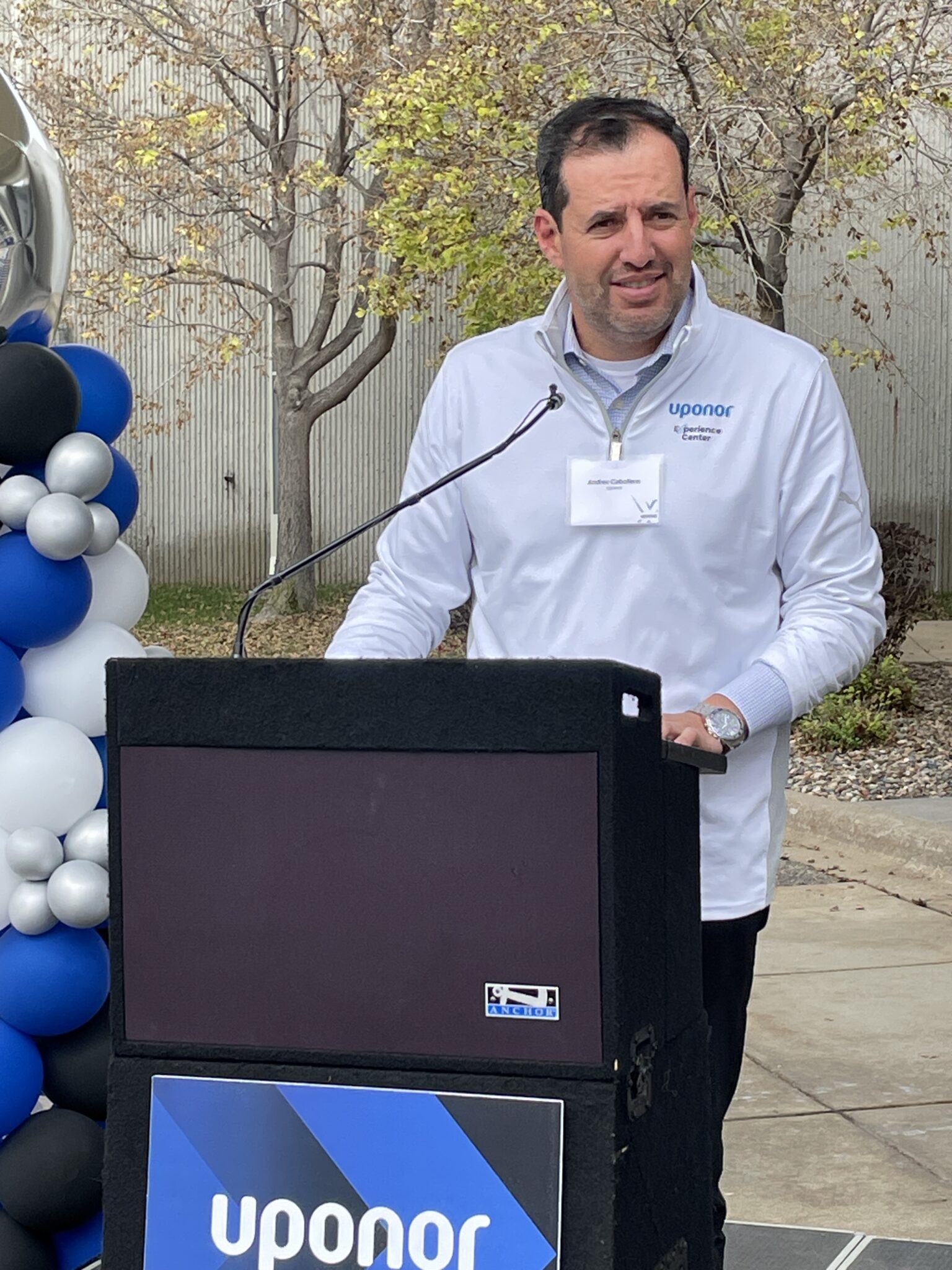
Andres Caballero thanks his staff for all of the hard work and dedication that went into planning and constructing the experience center.
“The opening of our new Uponor Experience Center signifies the importance we place on keeping the needs of our customers, employees, and key stakeholders top of mind as we continue our mission of becoming the global leader in sustainable water and energy solutions,” says Uponor North America President Andres Caballero. “The ‘X’, as our employees have begun to call it, is a culmination of our rich history and decades of innovation coming together to generate awareness and create enthusiasm for moving water more efficiently, effectively, and sustainably.”
With original concepts beginning back in 2020, the Uponor Experience Center was several years in the making. The thoughtful design, which takes into consideration the company’s rich Finnish roots, resulted from many months of internal team collaboration, as well as feedback from customers, partners, and industry influencers.

Mechanical Hub took the opportunity to record parts of the Appetite for Construction podcast with Des Clancy, director of training, Uponor, and the “architect” for the new center.
As guests move through the front doors toward the back of the space, they first experience displays depicting who Uponor is as a company along with the customers served and the unique value provided to key audiences and the industry.

Experience center visitors will get the full hands-on treatment as seen here with one of its gracious partners Milwaukee Tool and its PEX Expander.
Then, there are product showcases and interactive displays for plumbing, fire safety, radiant heating/cooling, hydronic piping, and pre-insulated piping system solutions for residential and commercial markets. Finally, there is an oversized training area, featuring both wood and steel structures, where professionals will learn proper hands-on installation techniques as well as how Uponor’s emphasis on problem-solving and productivity delivers results for their businesses.
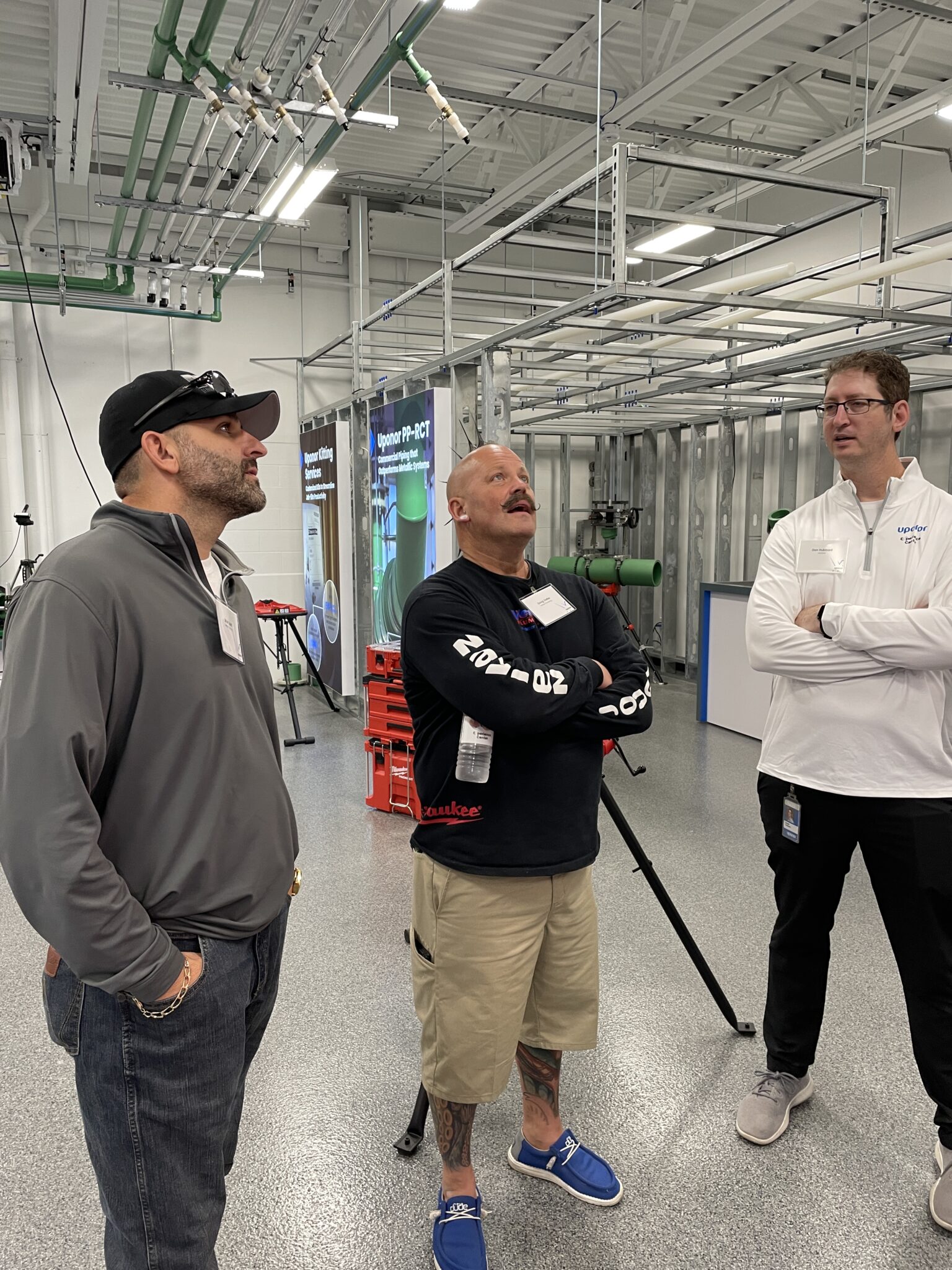
Doug Vetter, center, and Brian Spjut, left, from Vetter Plumbing, came all the way from Seattle to get a first glimpse of the space. (Pictured right is Uponor’s Dan Hubbard.)
“We wanted the Uponor Experience Center to extend beyond simply training customers on our products and systems,” says Vice President of Sales Matt Bahr. “As a result, we’ve created a holistic experience that spans a broad spectrum of who we are as a company, showcasing the depth and breadth of our product portfolio and sustainable solutions as well as providing access to the best trainers in the industry.”
With the focus not only on customers but also employees and those in the community, Director of Training Des Clancy says the planning team was very thoughtful about creating an elevated experience for everyone.
“At any given time, we will have contractors, builders, engineers, owners, students, employees, civic leaders, and other guests coming through the doors,” he says. “From tours and training, to onboarding and education sessions, the Uponor Experience Center offers something for everyone, and we are proud to showcase all we are offering to the industry and our community.”

Mechanical Hub’s John Mesenbrink (l) and Tim Ward (r) complete the “Uponor sandwich” as they also toured Uponor’s Distribution Center in Lakeville, Minn., with tour guide and director of logistics and warehousing, Nate McIntosh.
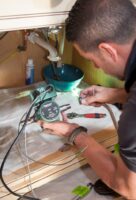
Advancements in technology, sustainability, and accessibility have been driving constant change in various industries, and plumbing is no different. What previously seemed to be a norm, plumbing experts are now substituting it with more efficient and advanced technology, especially in regard to plumbing appliances and fixtures. Let’s look at some trends that are already shaping Read more
Advancements in technology, sustainability, and accessibility have been driving constant change in various industries, and plumbing is no different. What previously seemed to be a norm, plumbing experts are now substituting it with more efficient and advanced technology, especially in regard to plumbing appliances and fixtures. Let’s look at some trends that are already shaping the plumbing industry and what to expect in the future.
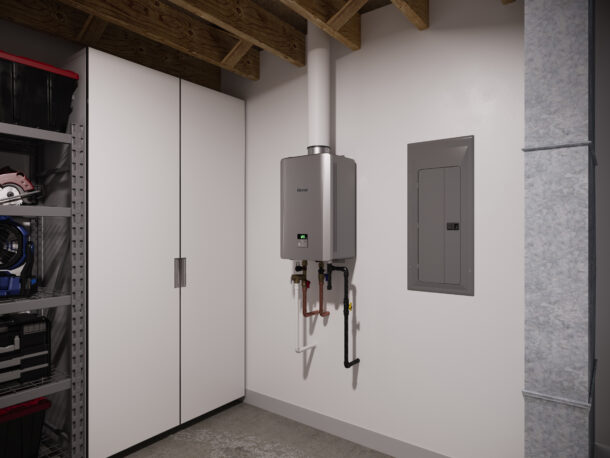
Increase in Online Subcontractor Scheduling
Most reputable plumbing companies like Grable Plumbing Services are catching up with technology by enabling potential clients to request free estimates and schedule consultations effortlessly on a website.
Plumbing experts are increasingly adopting the use of project management software, which enables them to monitor their plumbers’ productivity and performance while reducing downtime. There is also the use of digital apps that enhance effective communication and collaboration in real-time among plumbers, especially when not physically present at the site.
Adoption of Tankless Water Heaters
There is a rising number of commercial and residential property owners installing tankless water heaters. The water heaters only work on demand, enabling you to save a notable amount of money and energy. Besides that, tankless water heaters occupy less space compared to traditional water heaters and feature an extended lifespan than the conventional counterparts.
Use of Better Materials
Manufacturers are now using better materials to develop plumbing pipes and fixtures. PEX piping is a newer plumbing material that continues to gain popularity due to its flexibility, durability, and affordability compared to traditional copper piping.
In addition, PEX piping has the ability to resist corrosion and scale buildup, which mostly happens with copper pipes. It also withstands freezing temperatures and higher pressures, improving its lifespan. If you are a cautious property owner, you can add better insulation to your plumbing pipes to protect them from freezing during winter. It is also a perfect way to maintain hot water temperatures for longer periods.
The Rise in Automation and Sensors
The plumbing landscape is immensely changing, thanks to the increased adoption of smart automation and sensors. This has become more popular in residential homes. For instance, homeowners are installing sensor-activated toilets to enable automatic flushing and faucets that automatically turn on and off.
There are also showerheads capable of tracking your water usage and leak-detecting sensors. All these go a long way in helping you to save water and energy. Currently, you can find automatic toilets and faucets even in commercial applications.
Increased Awareness About Greywater Plumbing
Like many property owners who have become more environmentally conscious, you might be looking for ways to lower your environmental footprint and conserve water. The best way to do this is through setting up a greywater plumbing system.
The average American family consumes more than 300 gallons of water each day at home, with the largest share being consumed by toilets, showers, and faucets. By establishing proper greywater systems, you can recycle greywater from sinks and showers and use it to water plants or flush toilets.
Superior Water Filtration Systems
Filtration systems enable the cleansing of potable water to remove subtle elements like chlorine and magnesium. Many water filtration systems have been using reverse osmosis as a major component of the process.
Ultraviolet light and activated carbon stand out as the future of water filtration. While the former focuses on filtering smaller particles, the latter effectively gets rid of viruses, bacteria, and parasites.
Technology plays a crucial role in what you should expect in plumbing moving forward. Nothing is set in stone, and all these trends will keep changing as new discoveries are made. The best thing to do is to stay informed and keep track of the latest trends to make the best plumbing decisions for your business or home.
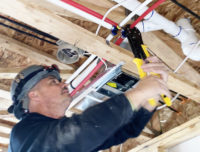
Shamrock Plumbing in North Salt Lake, Utah, is currently finishing up a large apartment complex, Soleil apartments, in Bluffdale. It’s a 100 percent solar complex with no gas. There are about 600 units in the entire complex, broken into buildings of 24 to 48 apartments. Sanders said there is a 2″ PEX line into each building to Read more
Shamrock Plumbing in North Salt Lake, Utah, is currently finishing up a large apartment complex, Soleil apartments, in Bluffdale. It’s a 100 percent solar complex with no gas. There are about 600 units in the entire complex, broken into buildings of 24 to 48 apartments.
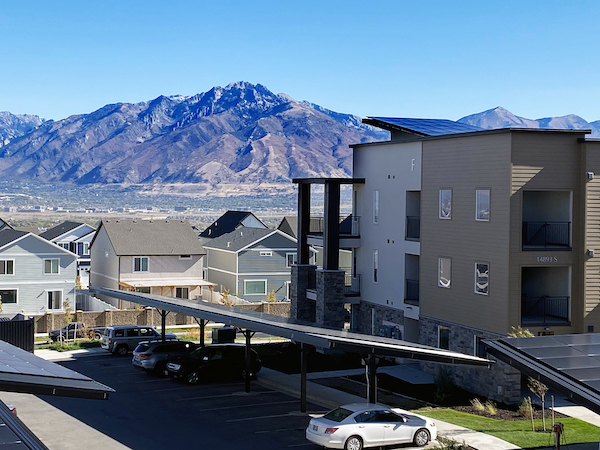
Sanders said there is a 2″ PEX line into each building to feed the water supply, and from there the lines drop down to 1″ from the water supply to the fixtures.
There are several reasons Shamrock Plumbing in North Salt Lake, Utah, uses Viega PureFlow PEX and press fittings in its multifamily new builds.
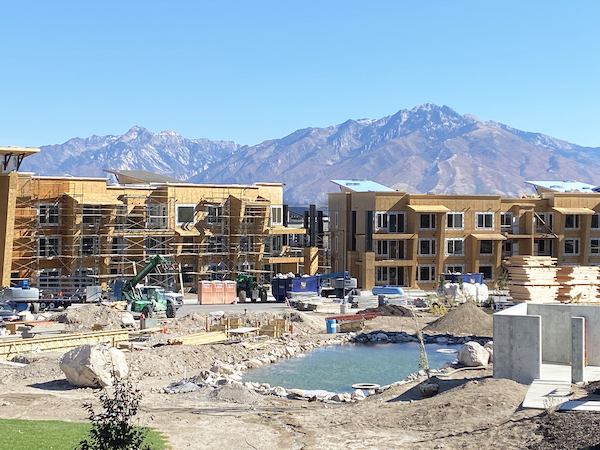
“It’s the flexibility. It’s the cost. It’s a 25-year warranty as opposed to zero warranty when you sweat copper. It’s the ease of installation,” said Bob Sanders, manager and partial owner of Shamrock. “You can also train a guy to install it fairly quickly, as opposed to the skillsets needed with copper pipe and all of that.”
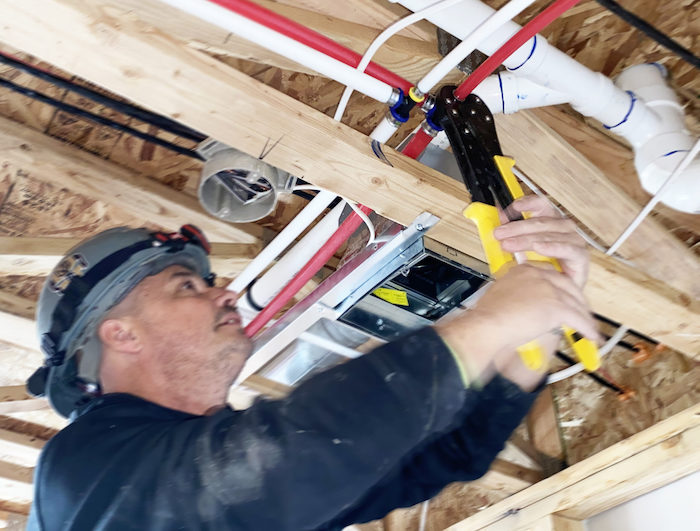
Thanks to the flexibility of PEX, fewer fittings are needed throughout the buildings to plumb the waterlines to each fixture, which in turn makes the installation quicker. Sanders estimated that one installer can get about four units done per day using PureFlow.
Widely used in Utah and in newer builds overall, Sanders said PEX is always specified when Shamrock takes on a new project like this, because of all of its pluses. He said most contractors they work with rely on Shamrock to pick the best products, and PEX is “far superior as far as a cost breakout compared to copper—plus the longevity and ease of use.”
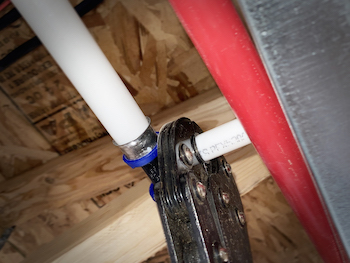
Shamrock uses Viega PureFlow products exclusively. The company used them in the past and was impressed, then they tried another company but eventually came back to Viega for its superiority.
“We weren’t satisfied with the other’s inconsistencies in the product, problems with leaks, etc., so we came back to Viega,” Sanders said. “It’s good, with good name recognition, and the reps and everyone we work with are a great support. You just can’t beat it.”
Uponor is committed to using 100 percent renewable resources to power its facilities globally by 2025. Apple Valley, Minn. — In conjunction with Earth Day 2020, Uponor North America is pleased to announce that its Lakeville, Minn., distribution center now receives 100 percent of its electrical power from wind energy, and is the first major Read more
Uponor is committed to using 100 percent renewable resources to power its facilities globally by 2025.
Apple Valley, Minn. — In conjunction with Earth Day 2020, Uponor North America is pleased to announce that its Lakeville, Minn., distribution center now receives 100 percent of its electrical power from wind energy, and is the first major manufacturing customer to participate in Dakota Electric Association’s Wellspring Renewable Energy program.
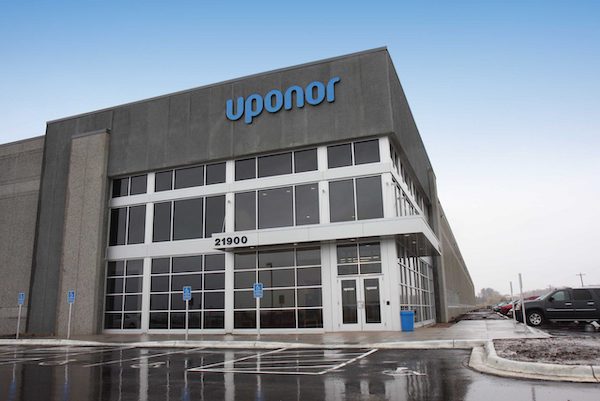
Wellspring Renewable Energy subscribers pay a slight premium to purchase wind energy sold in 100 kilowatt-hour blocks. As a partner in the program since Jan. 1, 2020, Uponor will annually purchase approximately 2.2 million kilowatt-hours of wind-generated electricity, which is equivalent to powering 263 homes’ electricity use for one year.
“Wellspring provides a way for businesses to receive all their power from renewable sources without having to build infrastructure or get in the energy business,” said Dakota Electric Association President and CEO Greg Miller. “Uponor has demonstrated its environmental commitment in a tangible way, and we are happy to assist the company in achieving its environmental goals.”
Since 2017, Uponor has worked with local utilities to purchase renewable energy blocks, increasing its renewable energy consumption in North America to 36 percent of its total energy use. Globally, Uponor continues to work towards its commitment of achieving 100 percent renewable resources to power its facilities by 2025.
“Globally, Uponor’s sustainability platform is centered on four key areas: conserve water, reduce waste, improve energy efficiency and empower labor,” said Bill Gray, president of Uponor North America. “The milestone reached at our Lakeville facility is a leap toward achieving not only our goals for improving energy efficiency in North America, but also on a global scale.”