The kitchen sink being attendees, that is. PHCC CONNECT, this past October 25-27, was set up for one of those “best-ever” shows. Beautiful downtown Cleveland was the backdrop to very a good week of meetings, connections, site visits and much more. Oh, and the weather didn’t hurt either, with temps lingering in the mid-70s. RIDGID Read more
Featured Articles
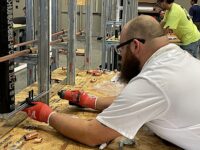
The kitchen sink being attendees, that is. PHCC CONNECT, this past October 25-27, was set up for one of those “best-ever” shows. Beautiful downtown Cleveland was the backdrop to very a good week of meetings, connections, site visits and much more. Oh, and the weather didn’t hurt either, with temps lingering in the mid-70s.
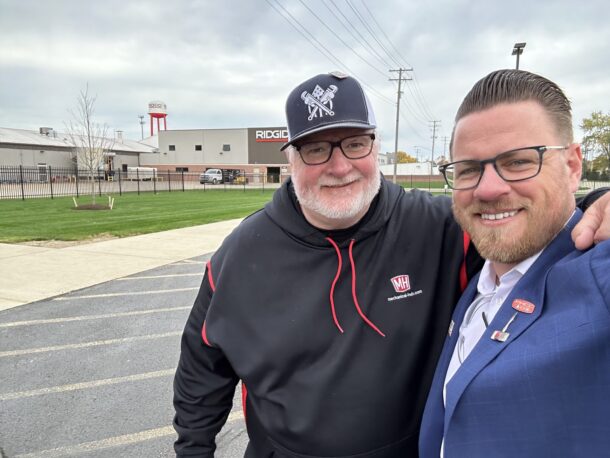
Mechanical Hub’s John Mesenbrink and The Family Plumber owner, Mike Prencavage, Jr. take the RIDGID tour.
RIDGID, Oatey, Moen and Merit Brass all call the “City that Rocks” home, or close to it anyway, and they each offered a bus trip to visit their respective HQs. Contractors visited their location of choice and all benefitted from their site visits.
The opening keynote, “Growth Begins at the End of Your Comfort Zone,” was presented by a compelling Ken Carter whose story blew up on the big screen as “Coach Carter,” played by none other than Samuel L. Jackson. The story of his 1999 season as coach at Richmond High School is the basis for the film. Throughout his life and tenure as a coach, he has inspired and guided numerous lives of young men to reach their highest potential. His “no non-sense” approach to getting things done is the force that has sustained him to have the tremendous positive influence that he currently possesses.

One of the contestants of the Plumbing Apprentice Contest.
One of our favorite annual events at PHCC CONNECT is the Plumbing and HVAC Apprentice Contest. A total of 21 plumbing and 11 HVAC apprentices from across the U.S. competed for top billing. The Plumbing Apprentice Contest winner was Cody McDonald of Van Contracting, Inc. in Columbia City, Ind. He was sponsored by the International Code Council.
The HVAC counterpart apprentice winner was Jacob Lee of P1 Service in Lenexa, Kan. He was sponsored by RIDGID.
The plumbing apprentices were required rough-in a bathroom system. The set-up includes a toilet, sink and shower, complete with supply, waste and vent lines, plus cleanouts and extra features designed to test the contestants’ knowledge and skills. The test set-up includes a variety of pipe materials—cast iron, copper and PVC and corresponding joining methods.
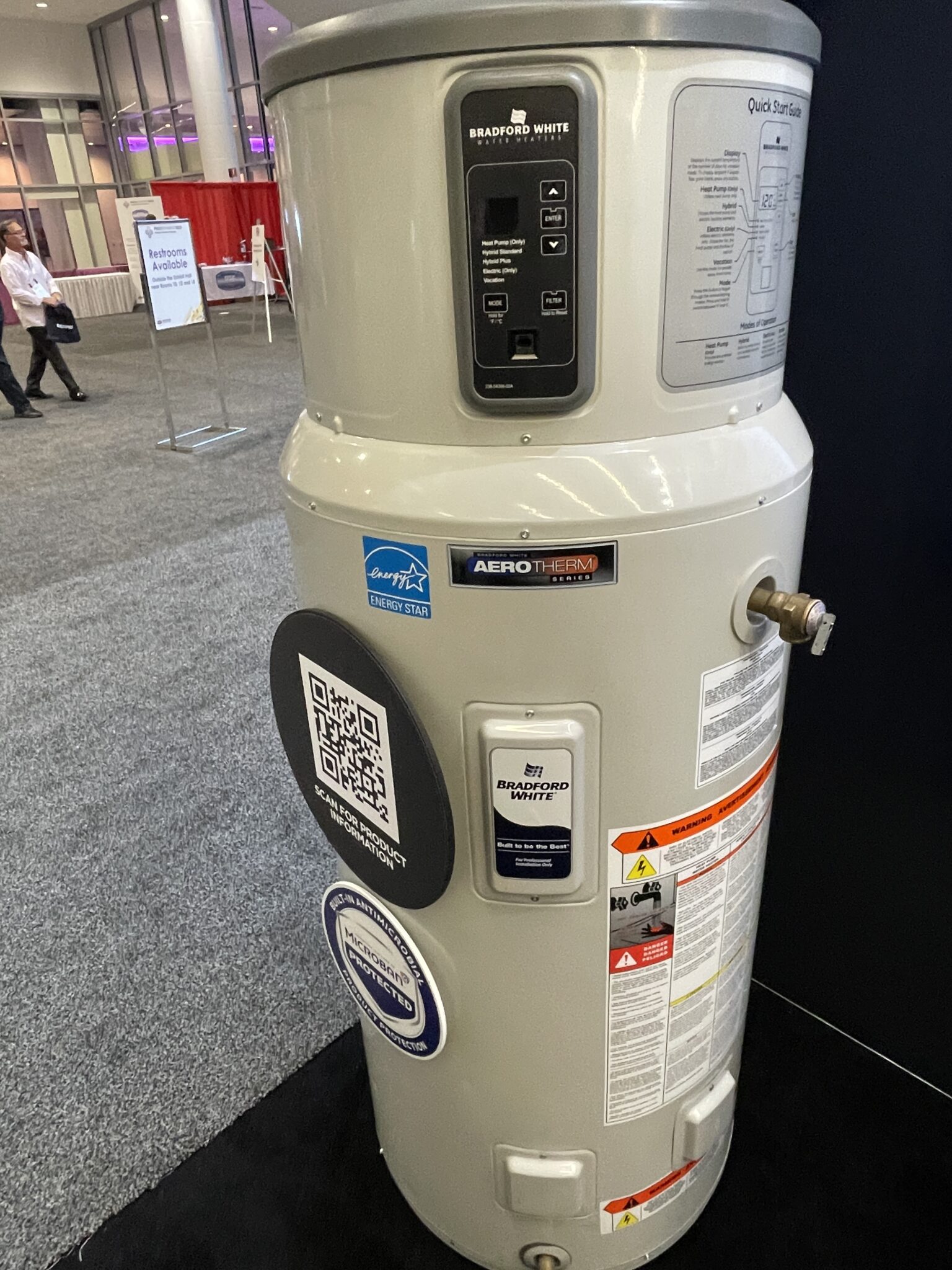
A Bradford White AeroTherm heat pump water heater was on display during the Product & Technology Showcase.
The HVAC competitors were required to complete a written test, demonstrate proper brazing techniques and perform a hands-on diagnostic on an HVAC package unit, with system errors created by the Foundation’s contractor volunteers for the competition. The competitors also had to perform a pressure and leak test, demonstrate proper refrigerant recovery procedures and the ability to accurately take a variety of instrument readings.
Adjacent to these apprentices diligently working on their assignment, a Product & Technology Showcase buzzed with activity surrounding the lates in tool technology, kitchen and bath, and water heating and heat pump tech.
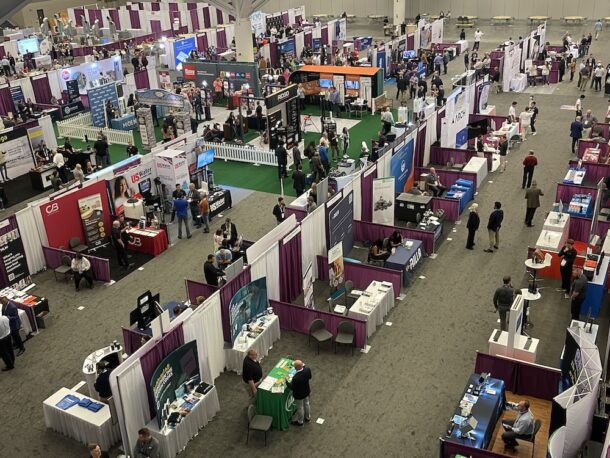
The kitchen sink.
Seminars and breakout sessions included a Government Affairs Update, Private Equity’s Interest in Plumbing Industries, DOE Standards for Water Heating Products and an Open Roundtable with Union Affiliated Contractors.
A strong session on Women in Industry: “Unlocking Potential and Breaking Barriers: Fostering Success for Women in the Trades through Gender-Inclusive Practices in Recruitment, Retention, and Engagement,” featured some of our personal friends, including Linda Hudek, LH Plumbing Services, Fairfield, Ohio; Ashley Martin, Executive Vice President, NIBCO; and Cassie Pound, co-owner of Quality Heating, Cooling & Plumbing in Tulsa, Oklahoma.
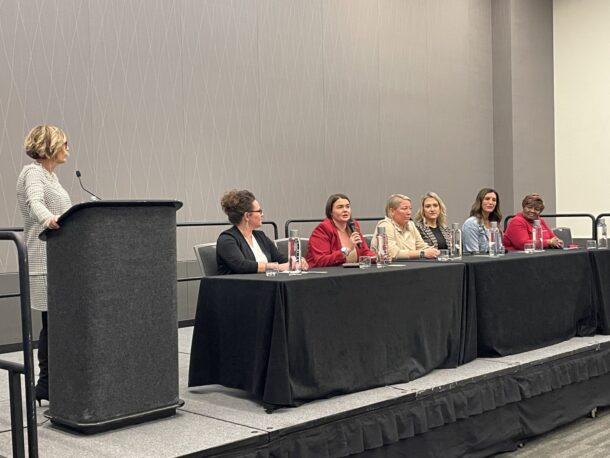
Linda Hudek addresses a question from moderator Susan Frew.
In today’s ever-changing business landscape, strengthening the contractor/wholesaler channel is critical to survival. A recent general session at PHCC CONNECT drilled deep into the conversation. This session, “Collaborative Connections: Strengthening Supplier-Contractor Relationships for Success,” featured RobertGrim, Senior Vice President, Global Sales, InSinkErator, Mount Pleasant, Wis.; Scott Robertson, President, Robertson Heating Supply Co., Alliance, Ohio; Dan Callies, President, Oak Creek Plumbing, Inc., Oak Creek, Wis.; Kathryn Poehling-Seymour, President and CEO, First Supply LLC, Madison, Wis.; and JasonPritchard, Co-Founder, PriCor Technologies, Seattle.
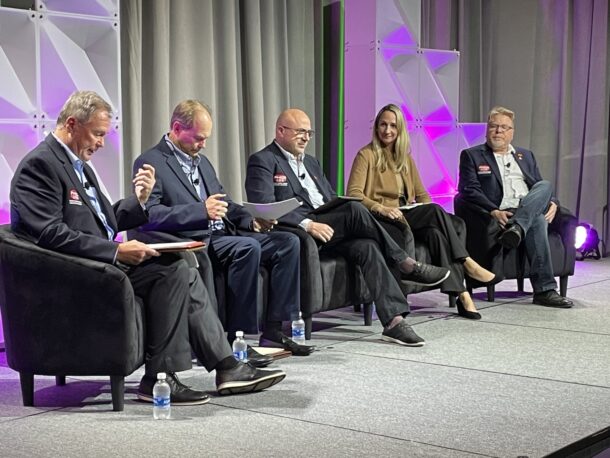
From l to r: Robert Grim, Scott Robertson, Dan Callies, Kathryn Poehling-Seymour, and Scott Pritchard.
And many, many more worthwhile seminars were offered. In fact, PHCCCONNECT2023 education sessions had been approved by OCILB (Ohio Construction Industry Licensing Board) for 19 CEUs.
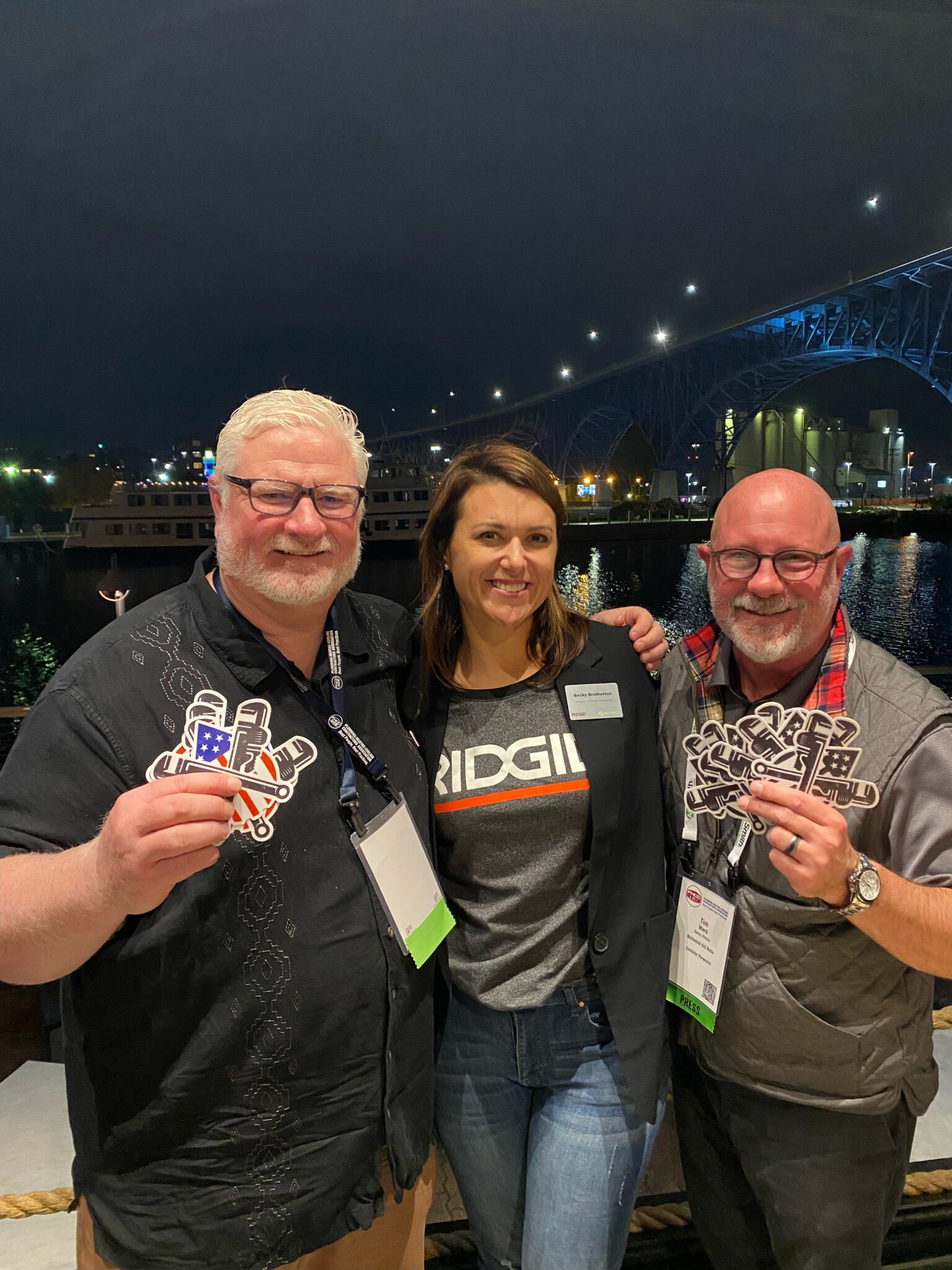
A RIDGID afterparty at a brewery on the river in downtown Cleveland with some American Plumber Story stickers? Yes, Please! Here with RIDGID’s Becky Brotherton, the Hub’s John Mesenbrink (l) and Tim Ward (r) from the Appetite for Construction podcast, recorded a series of podcasts from the event.
So, mix in some fun nights out with Oatey, RIDGID and PHCC’s receptions “Ohio Night House of Blues” and its closing event at the Rock ‘n Roll Hall of Fame, and, of course, connecting with industry peers, and you had the recipe for one kick-ass event.
Next year’s PHCC CONNECT will be held in Birmingham, Ala. Of all places, I sure hope that words gets around about the event. It’s worth the time, but more people need to come experience it, Birmingham or not.
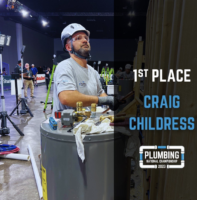
In a savvy move that would pay off more than he could have predicted, Craig Childress, a tradesman from Boston University, made the strategic decision to check extra luggage before jetting off to Tampa for the Elite Trades Championship Series (ETCS) Plumbing National Championship sponsored by SharkBite Plumbing Solutions —a rigorous showdown between the crème de Read more
In a savvy move that would pay off more than he could have predicted, Craig Childress, a tradesman from Boston University, made the strategic decision to check extra luggage before jetting off to Tampa for the Elite Trades Championship Series (ETCS) Plumbing National Championship sponsored by SharkBite Plumbing Solutions —a rigorous showdown between the crème de la crème of American tradespeople, including plumbers, competing for the first time for their share of cash and prizes.
Childress’s foresight was spot on. Not only did he clinch the title in the Plumbing National Championship, but he also emerged as the groundbreaking crossover victor in the HVAC National Championship’s pro division—a first in the event’s history.
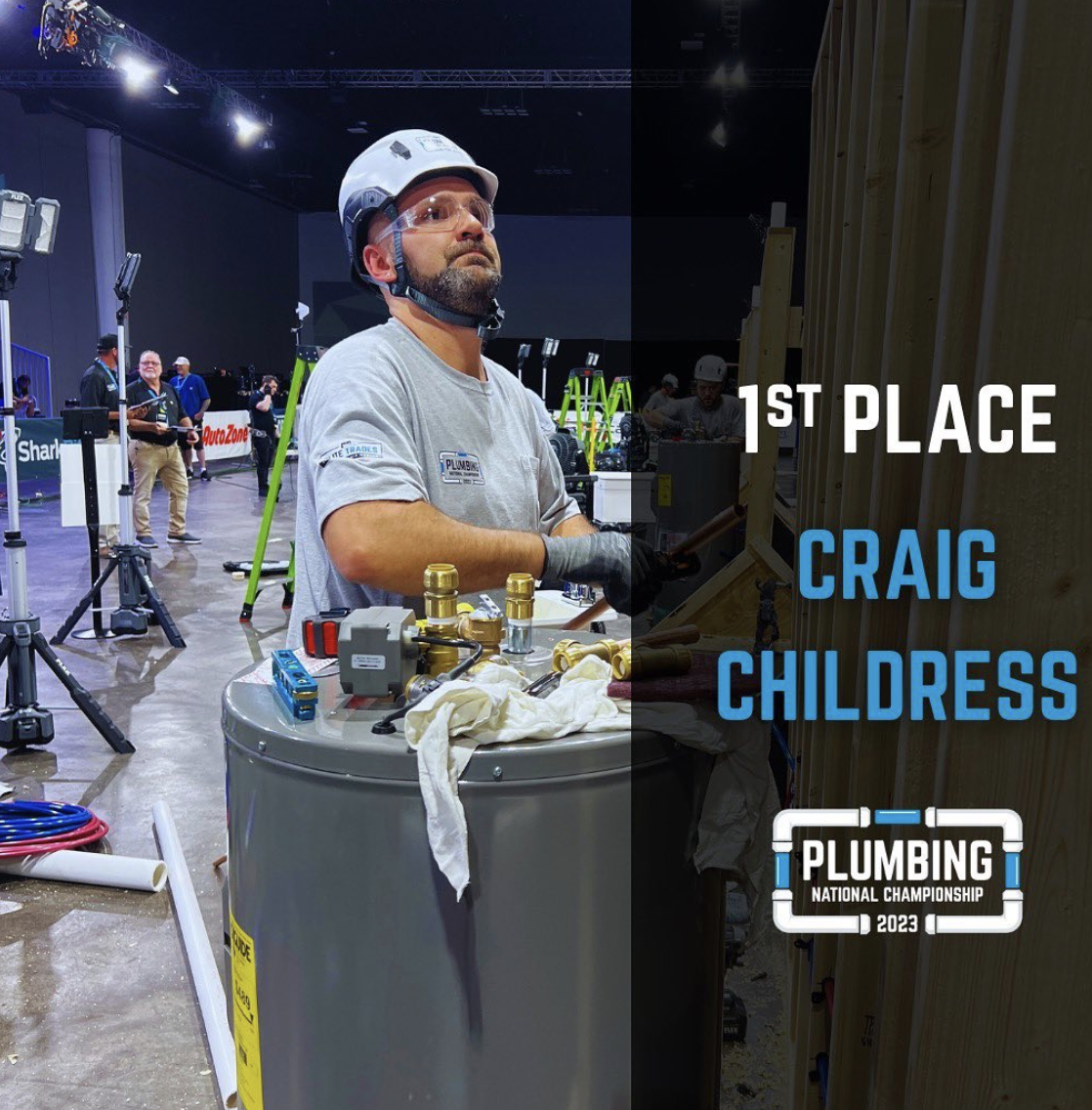
The spoils of his double triumph? A hefty $50,000 in prize money, complemented by a pair of weighty trophies. In the aftermath of his double win, with his wife Rachel by his side, an elated Childress reflected on the magnitude of his achievements: “Professionally, this is the most absurdly wonderful thing that’s ever happened to me,” he remarked, still processing the whirlwind of success. “It’s been an unbelievable journey. I’m incredibly grateful.”
The ETCS is more than just a trades competition. It’s a showcase of finesse, knowledge and dedication among the nation’s elite apprentices and seasoned pros, all vying for a slice of the $300,000 prize pool, bolstered by various sponsor contributions, including SharkBite’s support of the trade.
The ETCS Plumbing Championship is a mission to elevate the profile of plumbing. By framing pipework as a competitive sport, the championship aims to flush away old stereotypes and draw a new generation into the fold. It’s a call to action for young craftsmen and craftswomen: plumbing is not just a job—it’s a vocation that pays well but demands smarts, skill and a steady hand. In showcasing the sheer expertise these challenges demand, the championship underscores the critical role plumbers play in keeping our modern world running. The city of Tampa Bay became the stage where these virtues were on full display.
Plumbing may not spark viral hashtags or trend on TikTok, but the Plumbing National Championship is changing the conversation around this foundational trade. Think of it as the Olympics of U-bends and pipe wrenches: a high-stakes arena where plumbing pros from across the nation lock horns, armed with nothing but their tools and talent. Each plumber dives into a gauntlet of real-world challenges, turning the spotlight on the unsung skills that keep our faucets flowing and toilets flushing.
The competitive but fun event also celebrated other top-tier talents, with David Shanor and Joe Jaspers nabbing the second and third spots respectively in plumbing, and Dagner Espinoza and Lee Morris Jr. rounding out the HVAC podium.
However, for Childress, his moment of victory was as personal as it was professional. After both championship wins, he shared the moment with his 12-year-old daughter via video chat. Her pride in her dad was the cherry on top of an already sweet victory, moving Childress to the brink of tears.
The gripping tale of the ETCS SharkBite Plumbing National Championship will hit the airwaves soon. According to the Plumbing Nationals Instagram feed, CBS Sports Network will broadcast the 2023 Plumbing National Championship on December 29, 2023, at 8:00 PM ET, allowing viewers nationwide to witness the drama of Childress’s remarkable pipe dream come true. The HVAC National Championship will be televised Friday, December 15 at 8 PM ET, also on CBS Sports Network.
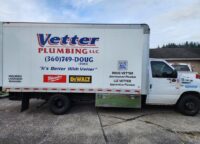
Vetter Plumbing, that is. If you’re ever in the Pacific Northwest, look up Doug Vetter, owner of Vetter Plumbing, Longview, Wash., and successful plumbing and heating contractor who has worked with the tools almost nonstop since graduating from high school in 1990. We recently rain into Doug at the pipe-cutting ceremony for Uponor’s Experience Center Read more
Vetter Plumbing, that is. If you’re ever in the Pacific Northwest, look up Doug Vetter, owner of Vetter Plumbing, Longview, Wash., and successful plumbing and heating contractor who has worked with the tools almost nonstop since graduating from high school in 1990. We recently rain into Doug at the pipe-cutting ceremony for Uponor’s Experience Center, and his passion for the trades is palpable.

Doug Vetter, right, has an infectious attitude, and enjoys living life like no one else.
In fact, you might say that young people searching for their true passion won’t likely encounter a more inspiring ambassador than Doug to a life in plumbing and heating.
There are, of course, a great many proud, highly accomplished professionals in this industry. But you’d be hard-pressed to find a tradesperson with a more robust and, at times, fearless outlook on life than Doug. He readily insists that much of this bring-it-on attitude derives from the sheer thrill of working as a service technician. “I just love my job,” he says over and over again.
For a small sampling of the sunny-side-up attitude Vetter brings to work each day, consider his morning routine of delivering doughnuts to the counter and warehouse staff at his favorite local supply house. Whoever heard of a plumber bringing free food to a wholesaler? “They have done lots of special stuff for me,” he cheerily reasons, “and, besides, it doesn’t cost that much.”
“My customers are always asking me, ‘Why are you in such a good mood today?’” he continues. “Well, when you contact me, we both know it’s not a social call. You have problems and fixing them may not be a ‘fun’ time for either of us. Why dump more stress on your situation by carrying a chip on my shoulder because I need to, let’s say, squeeze into your crawl space? Believe me, I hate crawl spaces. But being a plumber was my choice, and squeezing into crawl spaces is my job. That’s why you pay me.”
Doug willingly, happily, eagerly does his job 10 hours a day, seven days a week. But these are mere average—the actual totals could be much more in any given week. He would not have it any other way in a business that seldom lets him even slow down, let alone rest.
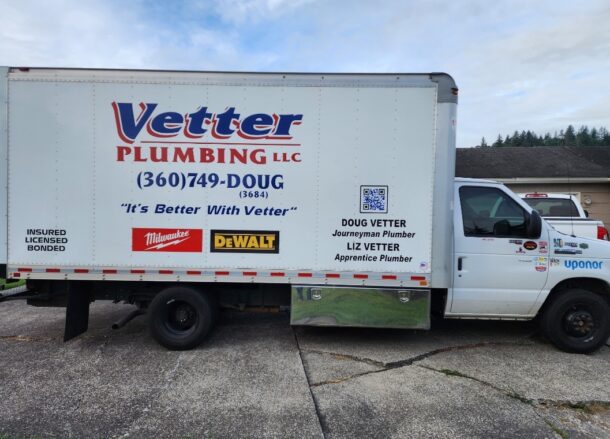
“I’ve never had a down time, even during the recent recession,” he says. “I just can’t say ‘no’ to people. That’s one of my downfalls and an issue with my significant other. But I love working.”
Back to the Uponor visit, Doug tells us that he is particularly proud of his tattoos, even the jaw-droppingly large U-P-O-N-O-R logo. Its six block letters span the full width of his back, left shoulder to right. Just as amazing: Every last ink mark strictly adhered to corporate style guidelines, right down to the correct shade of blue.
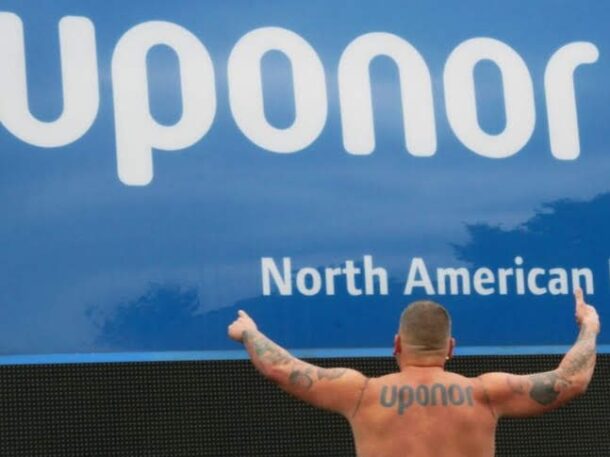
“I had a large blue Uponor sticker of the sort I put on my two trucks. I told my tattoo guy to put this exact thing on my back. He said, ‘Really?’ and I said, ‘Absolutely!’” Three grueling sessions over eight hours later, the tattoo was exquisitely in place and ready for show time whenever Doug decides to remove his shirt.
Why would he do something so “out there”? Why not? he shrugs. How better to express his unwavering loyalty to a brand he has supported nearly his entire career? “Uponor is the only brand I will put on my skin,” insists Doug, offering what is for him the ultimate compliment.
He fondly remembers his very first encounter with PEX more than 20 years ago, working for a Seattle plumbing wholesaler in the mid-1990s. Mark Walther — then a sales agent for the Portland-, Ore.-based Hollabaugh Brothers & Associates (still Uponor’s rep in the Pacific Northwest); and later a mentor for Doug when both worked at Merit Mechanical in Seattle—demonstrated the thermal memory of PEX with the familiar heat-gun demonstration that thousands have witnessed at countless trade shows over the decades.
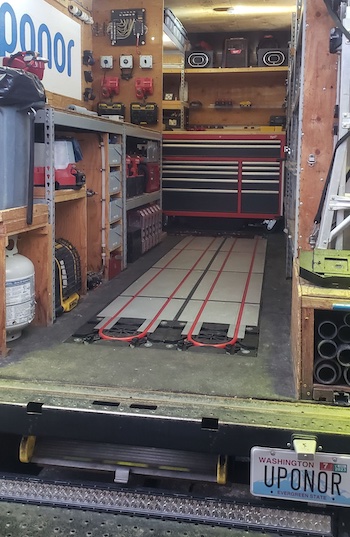
Vetter’s work truck is radiantly heated.
“Mark said to me, ‘Watch this, Doug!’ After kinking the pipe in his hand, he used a simple heat gun to make that kink vanish in minutes. I will never forget that moment—it was the coolest thing, just incredible. Every chance I get, I love showing people the same demo with the heat gun.”
Doug readily embraces the problem-solving aspect of service work: “I love going into someone’s house, learning what’s wrong, explaining the situation in ways the customer can understand and appreciate, and then fixing the problem—and fixing it in the right way.
“I can’t just throw something together for a customer. I do my plumbing a certain way—the way I was taught all those years ago at Merit Mechanical, where I earned my journeyman’s license.”
As noted earlier, those young people you’re trying to steer toward a trade career won’t likely snag a first job with Doug, who has happily—defiantly even—worked solo for the vast majority of his professional life since starting his own business. Although, his wife, Liz, is going through her apprenticeship to join him as a licensed plumber in the business.
Vetter has a certain way of running his business. “I want my cords wrapped in a one-foot circle and put away in a particular spot. My truck, a big-box van, is spotless and organized a certain way, and I want to keep it that way. That one employee I had just couldn’t do it.”

Same thing for working with the tools, if not more so: “I’m not a hard ass, but my No. 1 job is to protect the health of my customers. If I fail to create a sewer-line joint properly, the customer will have a disaster. If I expand a pipe incorrectly, I’m flooding someone’s house. I do it right because my reputation depends on it, and my reputation is all I have.”
Another, equally critical facet of “Doug’s Way” is treating every customer the same—fairly and nicely. “Nobody, it seems at times, does customer service any more. For example: promptly calling someone back who has called you. I feel badly if a day goes by before my returning a call. Many don’t do it at all and think nothing of it.
“I was taught to treat people with the utmost respect, regardless of what they look like, where they’re from, or how much money’s in their pockets. I want to fix their plumbing, of course, but I also want to give them the best service they can get anywhere.”
Currently in his 50s now, Doug plans to work “until I just can’t do it any more”—before retiring to Puerto Rico, where he says the people are warm, the weather’s warmer, and the water’s warmest of all. Until then, he will stick to his 70-hour work week as a highly motivated service plumber who gladly shoulders more work than any one man should handle, despite doing no advertising or promotion other than word-of-mouth.
“I thrive on service work. I love the instant gratification of solving problems. I get up in the morning, hit the road to meet new people, and figure out how to help. Every job is different, and the days just fly by.”
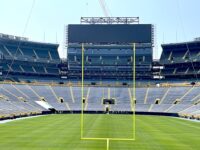
https://youtu.be/MhqypPXJtxM?si=h-FhMaoiuUVe3c4w Frozen Tundra no longer. Mechanical Hub’s Hub on the Road series takes us to Lambeau Field. Lambeau’s mechanical contracting partner, Tweet/Garot, gives us a behind-the-scenes look at Lambeau’s mechanical room, which serves as the epicenter for snowmelt, field heat, and HVAC, as well as its prefabrication facility in Wrightstown, Wis Read more
Frozen Tundra no longer. Mechanical Hub’s Hub on the Road series takes us to Lambeau Field. Lambeau’s mechanical contracting partner, Tweet/Garot, gives us a behind-the-scenes look at Lambeau’s mechanical room, which serves as the epicenter for snowmelt, field heat, and HVAC, as well as its prefabrication facility in Wrightstown, Wis.
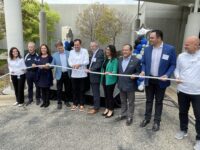
“It’s like Disney World for engineers and contractors,” said one visitor on the tour. The Mechanical Hub team made a quick visit to Apple Valley, Minn., to visit Uponor North America as the company celebrated the grand opening of its newly constructed Uponor Experience Center with a “pipe-cutting” ceremony. The team was treated to a Read more
“It’s like Disney World for engineers and contractors,” said one visitor on the tour. The Mechanical Hub team made a quick visit to Apple Valley, Minn., to visit Uponor North America as the company celebrated the grand opening of its newly constructed Uponor Experience Center with a “pipe-cutting” ceremony.

Andres Caballero (fifth from left) performs the pipe cutting for the new Uponor Experience Center.
The team was treated to a behind-the-scenes tour of the new 4,500-sq.-ft. customer experience center, which features hands-on displays, full-scale residential and commercial training areas, and cutting-edge innovation showcases, and a place to bring MEP students from the area to get a taste of the trades. The new Uponor Experience Center is a flexible education and discovery space designed to advance the technical skills of current and potential customers. In addition, it will help foster innovation within the plumbing and HVAC industry and provide an immersive experience for employees and visitors alike.

Some displays mimicked true applications.
The new Uponor Experience Center occupies the company’s previous customer training area, which was originally built in 2000 and renovated in 2010. It is at the center of the North American headquarters campus, surrounded by corporate offices, an R&D facility, and manufacturing space.
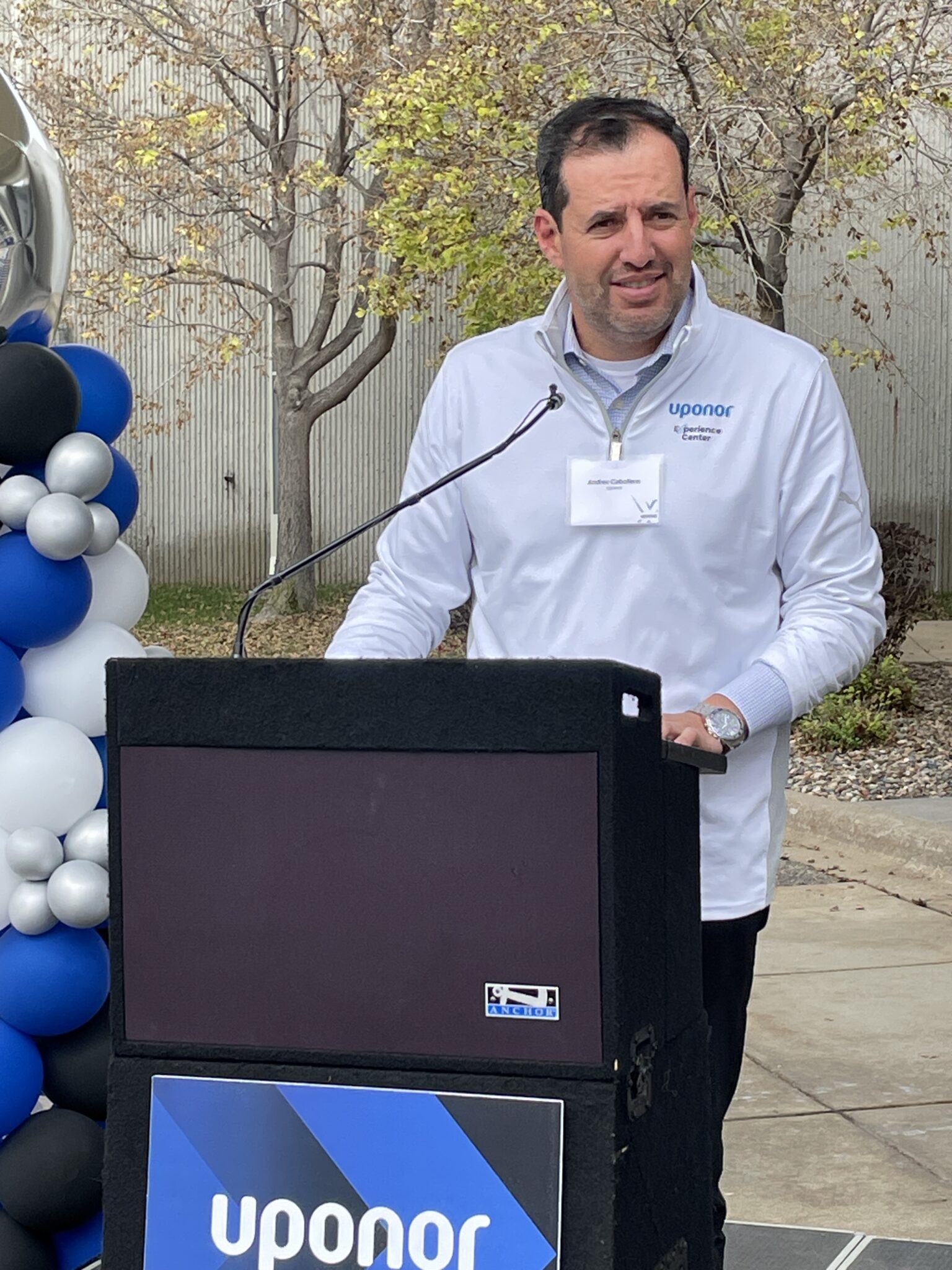
Andres Caballero thanks his staff for all of the hard work and dedication that went into planning and constructing the experience center.
“The opening of our new Uponor Experience Center signifies the importance we place on keeping the needs of our customers, employees, and key stakeholders top of mind as we continue our mission of becoming the global leader in sustainable water and energy solutions,” says Uponor North America President Andres Caballero. “The ‘X’, as our employees have begun to call it, is a culmination of our rich history and decades of innovation coming together to generate awareness and create enthusiasm for moving water more efficiently, effectively, and sustainably.”
With original concepts beginning back in 2020, the Uponor Experience Center was several years in the making. The thoughtful design, which takes into consideration the company’s rich Finnish roots, resulted from many months of internal team collaboration, as well as feedback from customers, partners, and industry influencers.

Mechanical Hub took the opportunity to record parts of the Appetite for Construction podcast with Des Clancy, director of training, Uponor, and the “architect” for the new center.
As guests move through the front doors toward the back of the space, they first experience displays depicting who Uponor is as a company along with the customers served and the unique value provided to key audiences and the industry.

Experience center visitors will get the full hands-on treatment as seen here with one of its gracious partners Milwaukee Tool and its PEX Expander.
Then, there are product showcases and interactive displays for plumbing, fire safety, radiant heating/cooling, hydronic piping, and pre-insulated piping system solutions for residential and commercial markets. Finally, there is an oversized training area, featuring both wood and steel structures, where professionals will learn proper hands-on installation techniques as well as how Uponor’s emphasis on problem-solving and productivity delivers results for their businesses.
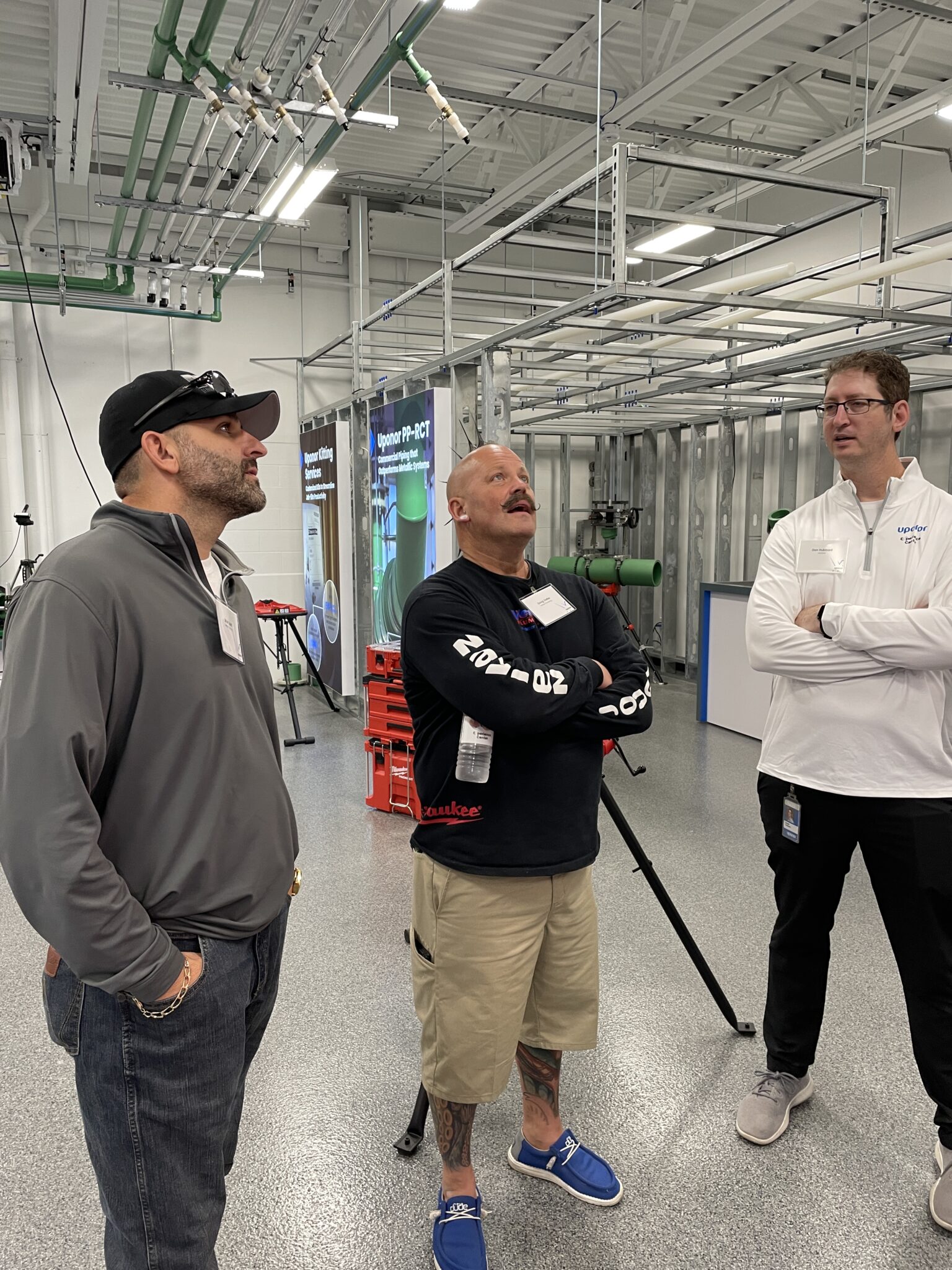
Doug Vetter, center, and Brian Spjut, left, from Vetter Plumbing, came all the way from Seattle to get a first glimpse of the space. (Pictured right is Uponor’s Dan Hubbard.)
“We wanted the Uponor Experience Center to extend beyond simply training customers on our products and systems,” says Vice President of Sales Matt Bahr. “As a result, we’ve created a holistic experience that spans a broad spectrum of who we are as a company, showcasing the depth and breadth of our product portfolio and sustainable solutions as well as providing access to the best trainers in the industry.”
With the focus not only on customers but also employees and those in the community, Director of Training Des Clancy says the planning team was very thoughtful about creating an elevated experience for everyone.
“At any given time, we will have contractors, builders, engineers, owners, students, employees, civic leaders, and other guests coming through the doors,” he says. “From tours and training, to onboarding and education sessions, the Uponor Experience Center offers something for everyone, and we are proud to showcase all we are offering to the industry and our community.”

Mechanical Hub’s John Mesenbrink (l) and Tim Ward (r) complete the “Uponor sandwich” as they also toured Uponor’s Distribution Center in Lakeville, Minn., with tour guide and director of logistics and warehousing, Nate McIntosh.