Leading hot water solutions manufacturer Bradford White supports top snowboardcross competitor and master plumber as he races to compete in the 2022 Olympic Games in Beijing Bradford White Water Heaters, an industry-leading manufacturer of residential, commercial and industrial water heating and storage products, announces its continued support for master plumber and general contractor Jonathan Cheever Read more
Featured Articles
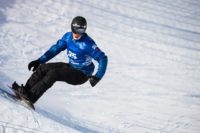
Leading hot water solutions manufacturer Bradford White supports top snowboardcross competitor and master plumber as he races to compete in the 2022 Olympic Games in Beijing
Bradford White Water Heaters, an industry-leading manufacturer of residential, commercial and industrial water heating and storage products, announces its continued support for master plumber and general contractor Jonathan Cheever as he pursues his dream of competing in the 2022 Winter Olympics in Beijing.
The company has renewed its sponsorship agreement with Cheever, a 2018 U.S. Olympian and former national snowboardcross champion who has balanced world-class international competition with plumbing, general contracting and design work throughout his career.
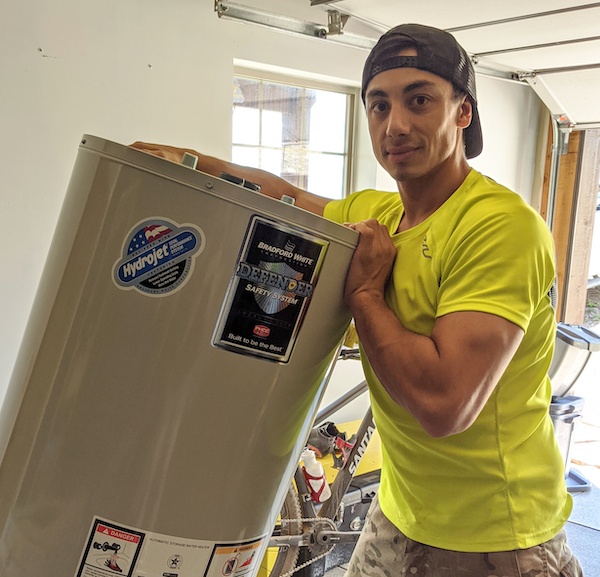
Cheever credits his career in the skilled trades as the key factor allowing him to compete internationally for more than 15 years.
“My experience in the trades has been essential to my snowboarding career,” Cheever said. “Without the flexibility I found in the industry, I wouldn’t have had the freedom to race all over the world, from the U.S. and Canada to New Zealand, Europe and Asia. Plumbing has also taught me lessons in patience and resilience that have been critical to maintaining a professional snowboarding career for almost 20 years. I’m grateful not only for Bradford White’s generous support of my efforts but for their dedication to the entire trades profession.”
Cheever learned the plumbing trade from his father while growing up in Boston and earned his master plumber license in 2004. He currently operates Team Cheever Design Build in Park City, Utah, delivering high-quality residential and commercial plumbing, general contracting and interior design services.
“Jonathan represents peak achievement, not just in his sport but in his career as a hard-working tradesman and entrepreneur,” said Carl Pinto, Jr., senior director of marketing communications for Bradford White Corporation. “The dedication that he has demonstrated on the slopes has also fueled his success as a highly skilled plumber and contractor. While his accomplishments are extraordinary, they also reflect the commitment and discipline that define the trades. We’re proud to be working with him as he continues to chase his dreams.”
Cheever’s outstanding career accomplishments include multiple podium finishes in World Cup competition; a third-place finish in the overall 2010-11 World Cup standings; the 2010-11 U.S. championship in snowboardcross; and a place on the U.S. team at the 2018 Winter Olympics in PyeongChang, South Korea.
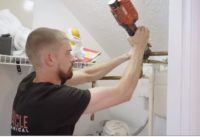
A part of Emerson’s professional tools portfolio, RIDGID is proud to support trade professionals giving back to the community RIDGID®, a part of Emerson’s professional tools portfolio, today announced their sponsorship of the first Miracle Mechanical project, a new initiative that completes plumbing, heating and air conditioning work for those in need at no-cost to Read more
A part of Emerson’s professional tools portfolio, RIDGID is proud to support trade professionals giving back to the community
RIDGID®, a part of Emerson’s professional tools portfolio, today announced their sponsorship of the first Miracle Mechanical project, a new initiative that completes plumbing, heating and air conditioning work for those in need at no-cost to the homeowner. The non-profit, headquartered in Georgia, is spearheaded by plumbing and mechanical contractor Brent Ridley.
“I have been doing tool reviews for many years, but I wanted to do more with my platform and really try to help some folks,” said Ridley, who along with working as a contractor is also a tool reviewer and co-host of the Tool Pros podcast.
The Miracle Mechanical team recently completed its first project for homeowner Nick Hendricks and his family in Monroe, Georgia. Hendricks had been seriously injured in a car accident. While he was recovering, the family’s home began experiencing septic system issues.
“The repairs mean everything to us at a time like this,” Hendricks said. “It had come to a point that we were afraid when it rained that the toilet downstairs would overflow due to groundwater getting in the septic and backing up through the toilet! Any time it rained the toilet would bubble and gargle and it was very unsettling.”
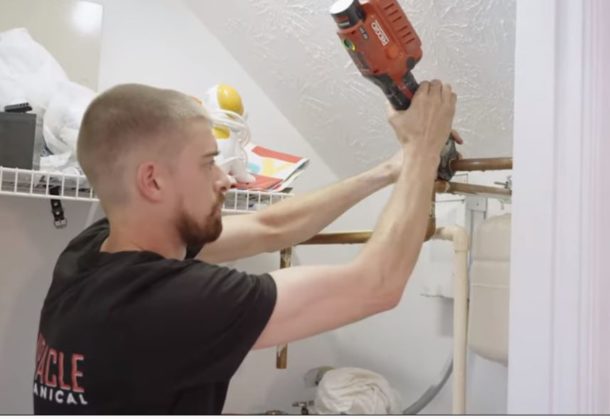
The Miracle Mechanical team repaired the septic system issues to prevent sewage from backing up in the house. They also installed three new toilets, repaired kitchen sink piping and installed a new electric water heater.
“At RIDGID we’re committed to not only supporting the trades, but also giving back to the community,” said Becky Brotherton, Senior Marketing Communications Manager, RIDGID for Emerson. “It’s a privilege for our team to be a financial supporter of the work Miracle Mechanical is doing to help others.”
https://youtu.be/0FL3hvxn2sY
Emerson’s professional tools business, which includes RIDGID as well as the Greenlee® and Klauke® brands, provides the industry’s broadest portfolio of advanced, reliable tools and technologies for the mechanical, electrical and plumbing trades globally.
Visit emerson.com/professionaltools for more information.
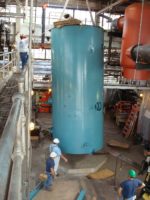
With zero emissions, economical electric steam and hot water boilers deliver maximum heat and hot water in minimum spatial footprint Due to the threat of global warming as well as international commitments to the Paris Accord on Climate Change, municipalities and regions using district heating in Europe and North America are tasked with significantly reducing Read more
With zero emissions, economical electric steam and hot water boilers deliver maximum heat and hot water in minimum spatial footprint
Due to the threat of global warming as well as international commitments to the Paris Accord on Climate Change, municipalities and regions using district heating in Europe and North America are tasked with significantly reducing their environmental footprint in record time. With district heating, towns or large areas typically receive heat and hot water, distributed to commercial, residential, or public buildings at greater economies of scale than individual heating systems.
In response, last year the 27-nation European Union (EU) agreed to cut greenhouse gas carbon emissions by 55% by 2030 compared to 1990 levels. According to a recent report that has tracked the EU’s power sector since 2015, renewables surpassed fossil fuels last year (38% to 37%), indicating that municipalities relying on district heating are already pivoting away from often inefficient, outdated equipment that produces excess carbon emissions.

Even the U.S., which recently rejoined the Paris Agreement, has targets for American businesses to achieve a carbon pollution-free power sector by 2035 and a net-zero economy by 2050.
While the interest of regions using district heating in electric boilers has waxed and waned in the last century, suddenly it is in vogue again. Whether to honor Environmental Social and Governance (ESG) goals, meet regulatory commitments, or take advantage of government credits and incentives, a growing number of municipalities are installing new or retrofit high-voltage electrode boilers that are compact, economical, and produce no emissions.
This is, in part, due to technological advances in electric boiler design that increase the output to a level that rivals even large gas or oil-fired boilers. When utilized for district heating, electric-powered alternatives are sure to be a critical piece of the puzzle to meet future emission reduction goals.
Transitioning from High-Emission Gas and Oil-Fired Boilers
With district heating, besides the notorious greenhouse gasses carbon dioxide (CO2) and methane (CH4), natural gas-fired boilers and furnaces emit dangerous nitrogen oxides (NOx), carbon monoxide (CO), and nitrous oxide (N2O), as well as volatile organic compounds (VOCs), sulfur dioxide (SO2), and particulate matter (PM).
However, many facility engineers familiar with gas-fired boilers mistakenly believe that electric boilers cannot match the output of the traditional, fossil fuel burning units. Due to considerable advances in electric boiler technology, that is far from the case. Today, such technology can match the capacity of large gas or oil-fired boilers in a much smaller footprint.

Electric boilers utilize the conductive and resistive properties of water to carry electric current and generate steam. An A.C. current flows from an electrode of one phase to ground using the water as a conductor. Since chemicals in the water provide conductivity, the current flow generates heat directly in the water itself. The more current (amps) that flows, the more heat (BTUs) is generated, and the more steam produced. Crucially, almost 100% of the electrical energy is converted into heat with no stack or heat transfer losses.
As an example, the electrodes of the CEJS High Voltage Electrode Steam Boiler by Acme, a Canada-based manufacturer of industrial and commercial boilers, are vertically mounted around the inside of the pressure vessel. This enables the unit to produce maximum amounts of steam in a minimum amount of floor space, with boiler capacity from 6MW to 52MW.
The boiler operates at existing distribution voltages, 4.16 to 25 KV with up to 99.9% efficiency, and can produce up to 170,000 pounds of steam per hour. With pressure ratings from 105 psig to 500 psig, the boilers are designed to ASME Section 1, and are certified, registered pressure vessels at the location of the boiler.
“There is an entire generation of district heating facility engineers that grew up with oil and gas-fired boilers almost exclusively,” says Robert Presser, Vice President of Acme Engineering, which, along with North American facilities, builds in Europe to European standards and has a network of CE-compliant fabricators for the pressure vessel, as well as partners in France and the UK for local equipment assembly.
“As a result of preconceived notions, most view electric boilers as small underpowered units, like a hot water heater,” adds Presser. “So, we frequently have to educate engineers that there is electric boiler technology that can match the capacity of large gas or oil-fired boilers available.”
According to Presser, the electric boiler technology is used for residential and commercial district heating, which is increasing in demand, particularly within urban centers. With district heating, distributed heat is generated in a central location through an insulated pipe system, and utilized for high-efficiency, low-pollution, space and water heating. For central heating applications, electric boiler technology quietly supplies ample power for its compact size. This approach is currently being considered to install several 50MW steam boilers in the center of Manhattan, replacing gas-fired boilers to provide centralized steam to a number of buildings.
Typically, district heating upgrades are initiated due to high heating costs that customers find unaffordable, often due to expensive fossil fuels or an aging system that needs to be replaced. Increasingly, such upgrades are pursued to minimize environmental impact.
The upgrades often entail retrofitting or replacing boilers (the heat source) with cleaner, more efficient electric alternatives, along with the heat distribution network (pipes/ heat exchanger stations).
In addition, electric boilers have several advantages compared to oil or gas-fired boilers, including superior safety, ease of installation, faster start-up and shut down time, and quiet operation. Electric boilers do not have a high minimum operating level to make them immediately available.
“Electric boilers do not need an operator because if anything goes wrong, the breaker trips, preventing further escalation of the issue,” says Presser. “With gas burning boilers, however, any gas leak can increase the risk of an explosion. So, gas units must usually be continually monitored or periodically inspected.” He notes that state and municipal safety guidelines vary depending on boiler type and the expected frequency of inspection.
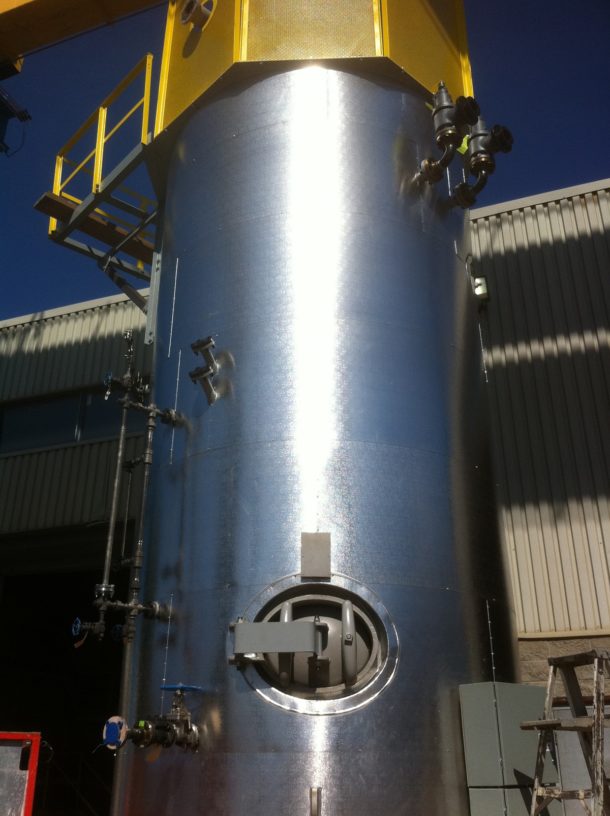
With electric boilers, the energy input as well as adjustment is also precise and virtually immediate. In contrast, increasing or decreasing the temperature in a gas fired boiler is a slower process because it takes time for the heat in the boiler to rise or dissipate before reaching the targeted output.
The electric units are also exceptionally quiet compared to fuel fired boilers. “Unlike gas-powered burners that throttle like turbine engines almost continually, electric boilers keep operational noise levels down,” says Presser. “Because the loudest boiler component is a circulating pump motor, it is easy to have a conversation next to one without having to raise your voice.”
As the EU and U.S. resolve to dramatically cut their greenhouse gases to combat climate change, the urgency for areas using district heating to similarly reduce their carbon emissions will only grow. In this battle to protect the environment before the global climate hits an irreversible tipping point, municipalities along with state and federal government, and the commercial sector must do their part. Fortunately, advanced, zero-emission electric boiler technology can be a readily implementable part of the solution.
For more info, contact Robert Presser at Acme Engineering rpresser@acmeprod.com; phone: 888 880-5323; or visit our website.
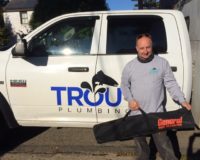
All closet augers are created equal. Right? “Wrong” says Alan Trout of Trout Plumbing LLC in Pittsburgh, PA. “Most off-the-shelf closet augers lack the durability, spring action, and special features professionals need,” he argues. “You can’t just waltz into Wal-Mart for one.” That’s why Trout counts on a pair of popular, innovative Teletube® Flexicore® closet Read more
All closet augers are created equal. Right?
“Wrong” says Alan Trout of Trout Plumbing LLC in Pittsburgh, PA.
“Most off-the-shelf closet augers lack the durability, spring action, and special features professionals need,” he argues. “You can’t just waltz into Wal-Mart for one.”
That’s why Trout counts on a pair of popular, innovative Teletube® Flexicore® closet augers from General Pipe Cleaners.
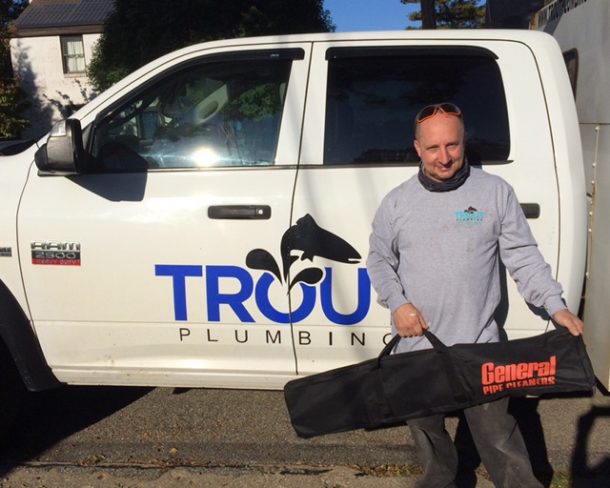
Versatility And Reliability Count
The heavy-duty Teletube Flexicore closet auger remains the industry’s most durable auger – and excels at clearing stoppages just beyond the bowl.
That’s because General’s rugged tool carries three extra feet of Flexicore® cable telescoped inside the guide tube.
“I just push the button for extra cable length when I need it,” Trout says. “And with a total reach of six feet, there’s usually no need to pull the bowl!”
General’s Flexicore closet augers are the ideal for quickly clearing clogged toilets. The strength and durability of Flexicore cable make the difference.
Flexicore comprises two layers of tempered spring steel coiled tightly over a core of 49-strand wire rope – for remarkable resistance to kinking.
The design is so tough, it’s guaranteed against breakage for a full year – including damage to the cable, as well as to the closet auger’s other components.
Performance – Inside And Out
On one recent job, a homeowner unsuccessfully tried unclogging a three-inch cast-iron stack – after feeding 25 feet of cable into the line.
“The customer must’ve missed the stoppage – or his cable was too small,” Trout recalls, “because I extended Teletube to six feet upon arrival – and quickly cleared the clog!”
Teletube’s extra reach even lets Alan Trout clear outside stoppages.
On another job, the powder room toilet in a two-room home office suite suddenly backed up.
After unsuccessfully snaking the drop head Teletube through the bowl, Trout went in through the outside fresh-air vent – and immediately got things flowing.
“That extra three feet made all the difference,” he smiles.
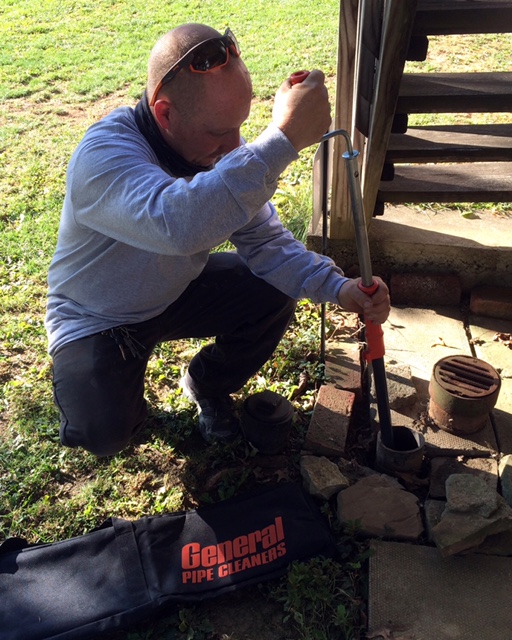
Special Features Enhance Appeal
He likes General’s down head option, too.
The optional down head follows bowl contours – and springs through sharply angled passages while protecting inner walls from chipping or breaking.
Alan Trout also has an optional Closet Auger Bag. General’s convenient carrying case puts an end to dragging dripping closet augers though homes, hospitals, and offices.
It keeps a closet auger contained and out-of-sight between jobs. Three vent holes let the auger dry between tasks. And thick shoulder strap keeps hands free to carry other tools.
“Until I got the bag, I’d carry a bucket with the Teletube,” Trout chuckles. “General’s Closet Auger Bag enhances ‘professional’ appearance – and keeps customer property clean.”
Building Trust – Job After Job
From installations and repairs to leaks and stoppages, Trout Plumbing handles a wide range of problems for Pittsburgh-area customers – both commercial and residential.
“On every job, we aim to build a level of professional trust that turns new customers into lifetime customers,” Trout says.
Proper equipment operation helps makes the difference, he quickly adds. But he isn’t afraid to push his Teletube closet augers to the limit – inside and out.
Part Of The Drain Cleaning Arsenal
For most inside drain cleaning jobs, Trout favors General’s classic Super-Vee® hand-held machine.
“I use it at least once a week – if not more – on 1-1/4” to 2” lines,” he notes.
In fact, Super-Vee easily unclogs sink, tub, and laundry drain lines up to 3” in diameter. With a dependable motor, durable aluminum drum, and tough Flexicore cable, Super-Vee withstands the most demanding small line tasks, and keeps working.
Convenient, quick-change cable cartridges also make Flexicore cable switching clean and easy.
“With 3/8” cable, my Super-Vee was actually able to snag – and remove – a broken cable in one customer’s slow-draining line,” Trout recalls. “And that solved the problem!”
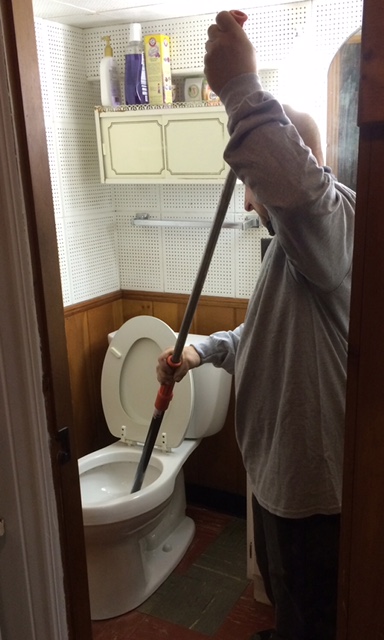
The Bottom Line
Like Teletube closet augers, Super-Vee carries an almost legendary reputation for rugged reliability – and longevity.
“I actually bought my Super-Vee from a plumber with excess equipment when I first went into business,” he continues. “So I’d say it’s nearly 15 years old – and still works great!”
His Teletube closet augers work great, too.
“As a plumbing service contractor, I use Teletube toilet augers from General,” Trout concludes. “The Teletube can almost do it all!”
For more information, contact the Drain Brains at 800-245-6200, or visit https://drainbrain.com/en/products/closet-augers-2/
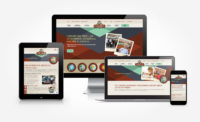
When Dana Spears assumed full ownership of Cornerstone Pros in 2009, it was a very different company than it is today. She credits much of her Tampa Bay, FL business’ increased success to her relationship with KickCharge Creative, a New Jersey-based marketing agency that serves small businesses across the country. The partnership began in 2013 Read more
When Dana Spears assumed full ownership of Cornerstone Pros in 2009, it was a very different company than it is today. She credits much of her Tampa Bay, FL business’ increased success to her relationship with KickCharge Creative, a New Jersey-based marketing agency that serves small businesses across the country.
The partnership began in 2013 when Cornerstone sought KickCharge’s expertise to rebrand the heating and cooling company. As the company expanded its services to include plumbing and electrical, its name changed from Cornerstone Air to Cornerstone Pros. The team at KickCharge created a dapper, friendly retro technician mascot to communicate Cornerstone’s differentiator—old-fashioned quality service in today’s fast-paced world. KickCharge Creative wove the retro brand into all of Cornerstone’s marketing efforts, including its service vehicles, initial brand announcement, brochures, blogs, print ads, billboards and stationery.
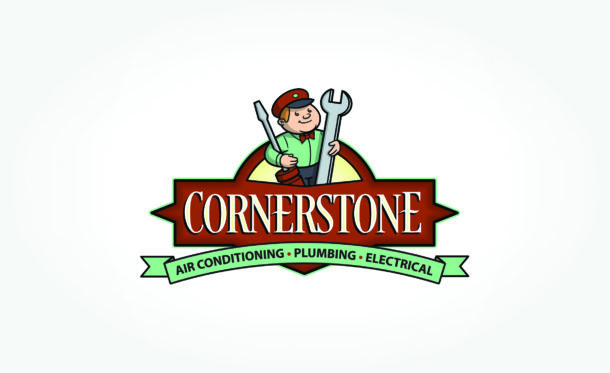
Cornerstone Pros had five service vehicles when its rebranded fleet first hit the streets in 2014. But Spears said the visibility and power of the new brand made customers feel like there were many more vehicles out there. Today, Cornerstone has roughly 56 vehicles in its fleet. Spears said the increased visibility has helped with employee recruitment efforts, too.
During the eight years since this partnership began, the new brand continues to pay dividends, including a 300% boost in revenue. Spears said annual revenue was $3 million before the rebrand and it jumped quickly to $5 million within the first year after introducing the retro brand and new services.
Since 2016, KickCharge has been managing Cornerstone’s highly successful digital marketing campaigns, which include search engine optimization, email marketing and pay-per-click advertising. KickCharge also launched a retro-themed, custom-designed website for this brand.
THE STATS:
- 300% growth in annual revenue since rebrand\
- Increase from 5 to 35 service vehicles
Spears’ goal is slow-based growth. As of 2020, the company had more than $12 million in annual revenue and roughly 78 employees. Cornerstone has nearly 2,000 reviews on Google with a 4.8/5 average rating. Its closing ratio is 87 percent even when the team has too much work to tackle same-day appointments.
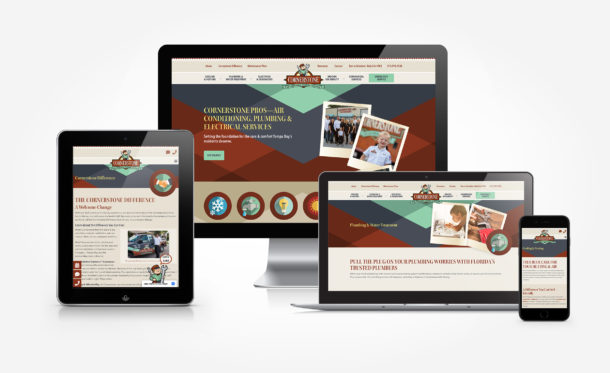
For Cornerstone, newspaper ads were once a primary driver of leads and Spears relied heavily on print, billboards and home-based advertising as well as some radio spots. These days, digital marketing is the dominant force. Google is the leading source of call volume (80 percent of leads), followed by repeat and referral customers.
“I am now dominating online so I don’t need to spend as much in other marketing areas,” she said.
Digital marketing campaigns offer more control over lead volume because they can be targeted specifically and adjusted instantly based on demand and seasonality. Those are factors Spears likes. It’s also easier to track these campaigns and to evaluate results.
“Although I was reluctant to turn my marketing over to an agency,” Spears said. “I’m glad that I did.”