If you buy an ECM circulator later this summer, you’re likely to see something new stuck to it: an Efficiency Rating label courtesy of the Hydraulic Institute. The labeling represents independent, third-party verification of each circulator’s overall electrical efficiency. That sounds pretty cool, but what does it all mean? Well, for starters, it means you Read more
Featured Articles
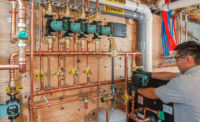
If you buy an ECM circulator later this summer, you’re likely to see something new stuck to it: an Efficiency Rating label courtesy of the Hydraulic Institute. The labeling represents independent, third-party verification of each circulator’s overall electrical efficiency.
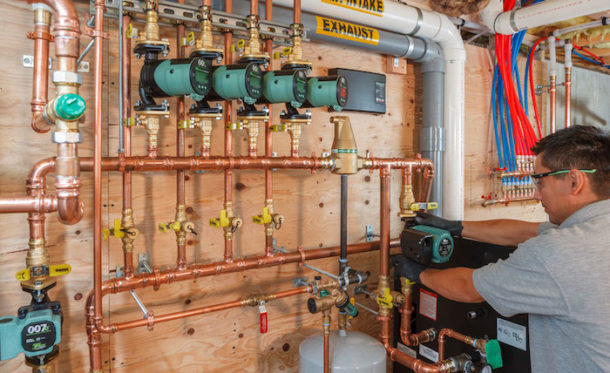
That sounds pretty cool, but what does it all mean?
Well, for starters, it means you don’t have to rely on marketing claims or sales mumbo-jumbo to determine who has the most advanced and efficient circulators. And you don’t have to rely on vague math to determine how much less an ECM circulator will cost to run compared to its standard efficiency counterpart.
In other words, it’s there in black and white.
There’s a lot to unpack here, so let’s get started.
First Off, Just What Is the Hydraulics Institute?
The Hydraulics Institute, or HI for short, touts itself as the global authority on pumps since 1917. It’s an industry association working on behalf of the pump industry and works with the U.S. Department of Energy to establish guidelines and regulations for pumps of all types and sizes. Most recently, its efforts with the DOE led to commercial pump efficiency regulations that went into effect in January of 2020, covering all pumps 1 H.P. and above.
The new labeling on ECM’s under 1 HP can be considered a pre-cursor to DOE regulations that will ultimately phase out standard efficiency circulators. However, don’t expect those regulations to go into effect for at least two, maybe three more years.
While HI is an organization made up of pump and circulator manufacturers, it’s important to note that all of its guidelines and regulations are set in concert with the DOE. In its most basic form, the DOE says, “this is what you have to do.” HI, in turn, develops guidelines, test procedures and processes manufacturers need to follow in order to be rated.
HI also certifies each manufacturer’s test lab, and it fully audits all test results. Yes, manufacturers test their own pumps, but only if their test lab is certified. HI creates all testing procedures and guidelines, including machinery calibration, personnel training and record keeping. Labs are periodically inspected, and all test results are reviewed and audited.
The whole process is set up so there’s no scamming the system. The results are the results.
But What About the Ratings?
You’ve no doubt seen those ubiquitous yellow EnergyGuide stickers on just about every appliance under the sun. They’re not only on fridges, dryers and other everyday items, they’re also on boilers, furnaces, A/C units and heat pumps. The Federal Trade Commission requires those stickers to give consumers an idea of relative energy efficiency compared to similar units.
The new HI Energy Rating stickers on circulators are pretty much the same thing, only different.
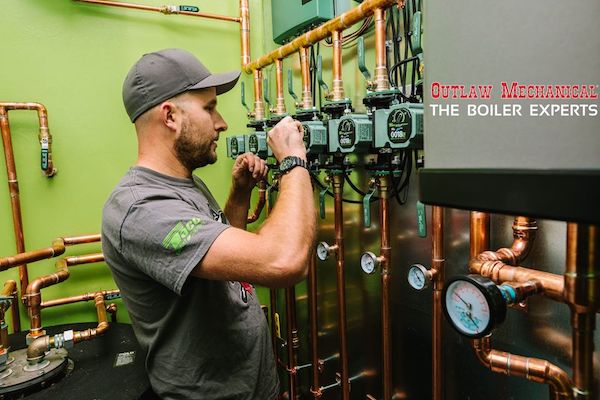
Instead of giving you an estimated yearly energy cost, the new HI Energy Rating stickers give each circulator an Energy Rating score, or an ER. It’s a pretty easy rating to decipher: the higher the number, the more efficient the circulator.
For example, an ECM circulator with an ER of 188 consumes 10 percent less energy than a circulator with an ER of 178.
By comparison, a common standard efficiency circulator, such as a Taco 007 or a Grundfos 1558, would have an ER in the neighborhood of 48 to 50.
The math to calculate the ER is fairly detailed, so it would take someone way smarter than me to walk you through it. The ultimate value of ER, however, is to provide a simple way to show a customer how much less an ECM circulator will cost to operate compared to its standard efficiency counterpart based on independent, third-party testing.
Let’s Do THAT Math!
Let’s look at the ER label for the Taco 0015e3. The 0015e3 is a variable speed Delta-P circulator with three settings, two for constant pressure and one for full-speed, fixed speed. It’s the perfect pump to use for zone valve applications and does a dandy job as a zone circulator as well.
As you can see, the 0015e3 has an ER ranging from 152 in its least efficient mode, which is that full speed, fixed speed setting. In its most efficient operating mode setting – variable speed, constant pressure Delta-P – the ER goes to 188.
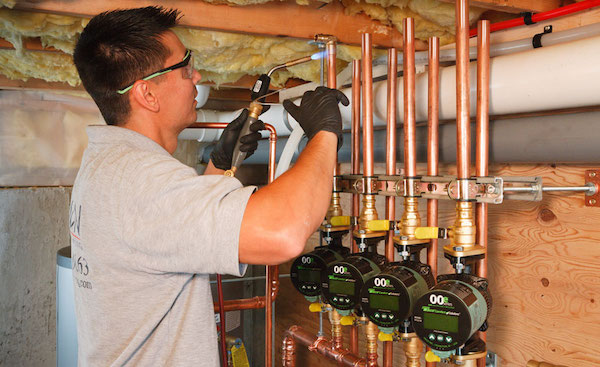
And not for nothing, Taco has four circulators with 188 ratings (and a fifth rated at 187). Those are the highest rated circulators on the HI database (Armstrong also has a circulator rated at 188. No one else is within six ER points). You can access the HI database here.
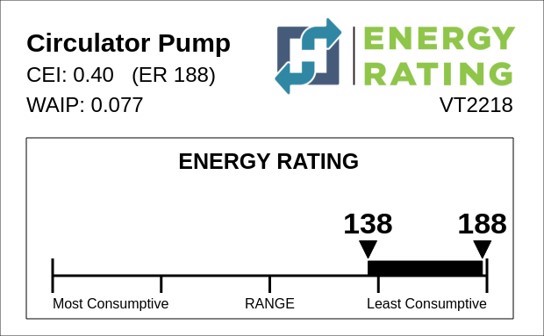
The full ratings label provides you with the math to determine how much a particular circulator will save. You first multiply ER by something called WAIP, which stands for Weighted Average Input Power. WAIP represents the average input power in horsepower for an ECM circulator without controls:
188 x 0.071 = 13.348
Next, to convert horsepower to watts, you’d multiply by 7.46:
13.348 x 7.46 = 99.58 watts
From here on it, it’s a simple kWh/cost calculation. To convert watts to kilowatts, you divide by 1000, and then multiply by the estimated number of run hours over a heating season. For this example, we’ll use 2500.
99.58 ÷ 1000 = 0.09958 kilowatts
0.09958 kW x 2500 hours = 248.95 kWh
Last, multiply kWh by your cost per kilowatt hour. That will tell you how much less the 0015e3 would cost to operate compared to a 007 or 1558:
248.95 kWh x 0.15 per kWh = $37.34
Is that a Lot?
Well, it depends. If you’re trying to justify replacing four perfectly good and not terribly old circulators with four ECMs, you’ll save just under $150 per heating season. Depending on how much you charge for the swap out, it might be a hard sell. And there’s nothing “green” about dumping four perfectly good circulators before their time.
However, if you’re trying to show a customer (or yourself, for that matter) that replacing a dead circulator with a more expensive ECM is worth it, you now have something to sink your teeth into.
Say a standard efficiency 007 or 1558 dies and you want to replace it with a 0015e3. Yes, the 0015e3 costs more. But just channel your inner Cosmo Castorini from Moonstruck and tell them, “it costs money, because it saves money.”
Without getting into wholesale costs, profit margins and selling prices (those are your business), it’s fair to say that based on a $37.34 annual savings, the 0015e3’s higher selling price will be offset in less than two heating seasons. After that, the homeowner pockets the rest.
And if you want to talk about how a properly programmed ECM, particularly one that operates on a fixed Delta-T, will help the overall system work better, let’s make an Outlook appointment. There’s a LOT more to discuss.
What’s the Point?
So, why HI is doing this labeling thing in the first place? Simple: to give the industry an easy—and independent—way to show the value of converting from standard efficiency to ECM.
In markets where local utilities do not offer incentive rebates to drive conversion, ECM conversion has been snail’s pace slow. Some of it is a little of the “if it ain’t broke, don’t fix it,” mindset. Some of it has been ridiculous claims of “magic” and the misguided promise that these circulators somehow mean you don’t have to know how to size a pump. No one with half a mind believes that nonsense.
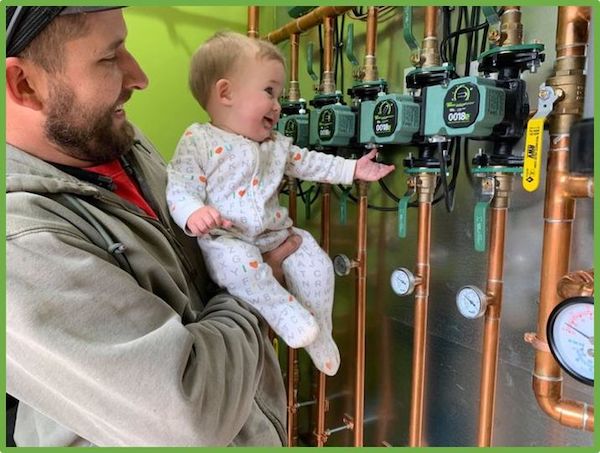
And some of it is, to put it gently, giving new technology a healthy—and distant —respect.
But for the most part, it’s been price resistance.
What the ER label does is give you an easy way to show a customer a fundamental truth: they’re going to be paying for the ECM circulator one way or another. The only question is whether they actually get it or not.
Remember Cosmo’s words.
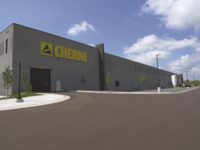
Cherne Industries, part of the Oatey Co. family of brands, recently completed a historic move of its headquarters and manufacturing operations — its first in more than 60 years — to a newly constructed, 130,000-square-foot facility located in Shakopee, MN, situated 25 miles southwest of downtown Minneapolis. Opened in March, the manufacturing portion of the Read more
Cherne Industries, part of the Oatey Co. family of brands, recently completed a historic move of its headquarters and manufacturing operations — its first in more than 60 years — to a newly constructed, 130,000-square-foot facility located in Shakopee, MN, situated 25 miles southwest of downtown Minneapolis.
Opened in March, the manufacturing portion of the new, state-of-the-art headquarters was built to Cherne’s exacting specifications by the OPUS Group, as management sought to more fully integrate all its operations under one roof. Shakopee combines automated robotic manufacturing pneumatic pipe plugs, mechanical pipe plugs and testing equipment with a new research and development laboratory for product testing, extensive customer training facilities, and an in-house machine shop for making all the needed tooling on premises, rather than depending upon outside sources.
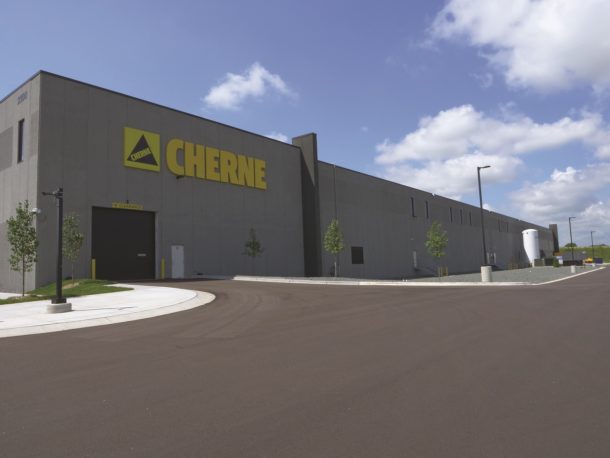
In addition, the new building contains ample storage space for raw materials and finished product, so that Cherne no longer relies on outside warehousing for storage and shipping. The resulting, more efficient material flows have already cut lead times and increased operating efficiencies since the move.
“Cherne has been growing at a double-digit pace for the past seven years,” says General Manager and seven-year company veteran David Biron, explaining why the former, 66,000-square-foot facility in nearby Edina was no longer suitable. “We had acquired some robotic equipment and other automation components in recent years, but as the business grew, we simply ran out of space.
“The R&D and testing operations demonstrate Cherne’s newly fortified capabilities as we maintain world class, industry-leading new-product development that provide the safest, most productive value-added solutions for our end users,” Biron continues. Cherne can now test its entire production on premises, instead of relying on outside facilities, as had sometimes been the case in the past.
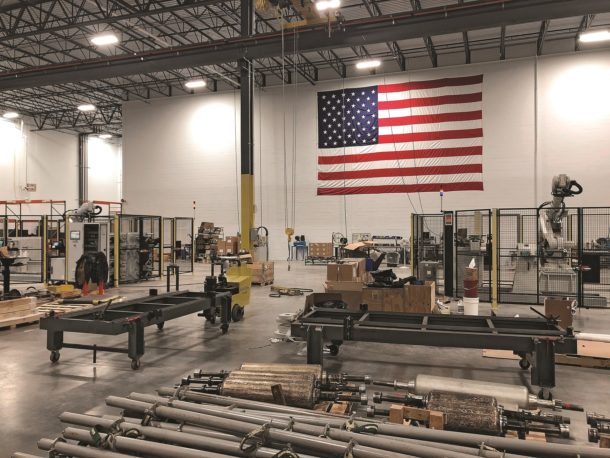
“The old building did not offer a setting large enough — and therefore safe enough — to test larger plugs and testing equipment, which expand up to 120 inches,” says Biron. “No other plug maker can offer as comprehensive or as safe a testing facility as what we’ve built in Shakopee.”
Robotics = safer, longer-lasting plugs: The most impactful upgrade with the new Shakopee operation is the inclusion of a pair of automated robots for producing Cherne’s industry-first and industry-leading offering of pneumatic plugs. The robotic technology creates a mechanical bond to more securely join the plug’s aluminum end plate to its premium natural-rubber core.
The result is more precise and consistent fabrication, from plug to plug, minimizing field failures sometimes found with the manual, chemical-bonding connection process long used by other manufacturers. Cherne’s robotic-made plugs are a significant industry advancement, offering best-in-class safety, durability, and premium performance.
“No other North American manufacturer is building plugs with one robot, let alone two,” says Biron. “Other producers still assemble them by hand, as they have been for decades. This entire facility demonstrates the enduring strength of the Cherne brand and why a customer can be comfortable buying and installing plugs and related piping products from us.”
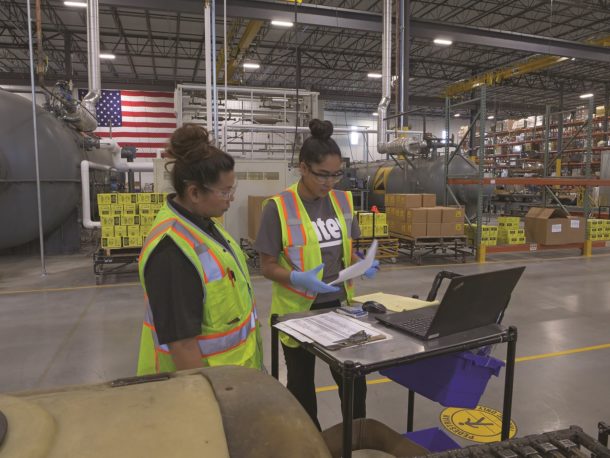
Rapid turnaround: Until this past March, every plug sold by Cherne over the past five decades and more had been made in the company’s former Edina facility, erected by founder Lloyd Cherne in 1970. (Oatey Co. bought Cherne in 1990.) So, it may seem surprising that the relocation to Shakopee required only seven days, as Biron reports, with the new plant successfully running 70 percent of the company’s catalog by the end of that first week.
Biron expects to employ 130 personnel, a gain of approximately 20 over Edina. Among the reasons Cherne chose to move to Shakopee was to tap its “wide cross-section of qualified workers” to fill the diversified roster of skilled technical positions needed to operate and maintain Cherne’s large, automated equipment at a high level.
“We drew it all up on a napkin two years ago,” recalls Biron, “and spent another 18 months meticulously planning the move down to the smallest detail. It was unbelievable how our team came together, and it could not have gone any more smoothly — even with all of our large pieces of equipment and despite the pandemic. In a year when everything seemed to go wrong, this move and its aftermath have gone exceptionally right.”
Some key partners that were critical to making the move go as well as it did were Cullinan Rigging and Erecting, OlympiaTech Electric, Voson Plumbing and Allen Mechanical. “Without their attention to detail and customer focus,” says Biron, “this move wouldn’t have been successful.”
To learn more about careers and opportunities available at Cherne Industries, visit oatey.com/careers.

Robust forecast is expected to beat pre-COVID-19 estimates by a significant margin. Hackettstown, N.J. — In its July update to the Kitchen & Bath Market Outlook, the National Kitchen & Bath Association (NKBA) revised its 2021 industry sales projection upward to $170.9 billion, up by a substantial 21.4% from 2020’s $140.8 billion in kitchen and Read more
Robust forecast is expected to beat pre-COVID-19 estimates by a significant margin.
Hackettstown, N.J. — In its July update to the Kitchen & Bath Market Outlook, the National Kitchen & Bath Association (NKBA) revised its 2021 industry sales projection upward to $170.9 billion, up by a substantial 21.4% from 2020’s $140.8 billion in kitchen and bath spending and nearly 8% higher than the initial estimate for the year.
New construction K&B spending is now expected to exceed 2020 by an impressive 28.5%, as builders attempt to keep pace with substantial demand. Meanwhile, K&B remodeling is expected to climb by 12.5%.
The update provides a comprehensive review of current industry conditions as well as macroeconomic factors — such as consumers opening their homes to workers post-pandemic and stimulus checks — likely to impact business.
“This update is very encouraging and confirms the ongoing robust performance of the design and remodeling industry,” said Bill Darcy, NKBA CEO. “This very strong sales forecast is attributable to pent-up demand for new home construction, easing COVID disruptions and a sea change in consumer behavior. People will continue to work from home in some capacity, fostering renovation of their space to meet their evolving needs. A tight inventory of homes for sale is also encouraging homeowners to stay put and renovate. That’s all good news for our industry.”
Darcy cautioned, however, that there are a few bumps in the road: Home prices continue to rise, and the cost of building materials is still high — a combination that’s excluding some potential buyers from the market; the employment picture still hasn’t fully recovered to pre-pandemic peaks, and supply-chain disruptions continue to delay jobs and make product sourcing a challenge. “But most indicators suggest the thriving K&B market will continue,” he added.
The industry should see double-digit increases in both kitchen and bath spending. This is a reversal from the industry’s 3.8% decline in 2020, which was driven by an 8.6% loss for remodeling and stagnant growth of just 0.5% for new construction during the pandemic.
Bathroom spending will rise by 22.3% in 2021 and will be sparked mainly by gains in new construction, while kitchen spending will increase by 20.4%, led by stronger gains in remodeling.
Among the report’s other key findings:
High-End Soars Even Higher: Although forecasts for low and mid-range project spending have each been revised upward, it’s the high-end that will shine. It’s now expected to surge by over 28% compared to 2020 (beating the initial 19.8% projection), as pent-up demand, robust savings and impressive house appreciation encourage homeowners to go the extra mile.
Job Recovery Lags: Not everyone is in a position to act. Although 14 million jobs have been recovered since the pandemic lows, total U.S. employment is still more than 8 million jobs below peak levels. At the current rate of job creation, it would take more than a year to fully recover. The unemployment rate, however, is receding to traditional levels, as some have left the job market entirely and are no longer counted.
Tailwinds for Housing Starts: Starts are expected to grow by 18% in 2021, a sharp upward revision over the initial forecast for the year. The spike in starts is partially owing to a plunge in available resale inventory. This portends a continued hot market for at least the short term, but relentless home inflation is beginning to flash warning signals, as more consumers are being priced out of the market.
Home Improvement Tops Discretionary Spending: Nearly 1 in 3 homeowners plan to boost their home-improvement discretionary spending this year, well above the 1 in 5 (or fewer) who plan such increases for eating out, entertaining, travel or health. In fact, the average home-improvement project price point is 25% higher than last year.
Kitchen & Bath Are Top Choices: For those planning home improvements this year, kitchens and primary baths rank #1 and #2, respectively, among a dozen home areas offered. More than half (55%) said they planned to remodel their kitchen, while 40% cited their primary bathroom. Exterior (37%), patio/deck (29%) and primary bedroom (29%) round out the top five.
Methodology:
The data presented in this report is compiled from a variety of sources: U.S. Census American Housing Microdata, National Apartment Association (NAA) Spending, the National Association of Realtors, Moody’s Analytics, Home Innovation Research Labs (HIRL) data, and John Burns Real Estate Consulting’s home improvement estimates and forecasts. In addition, a survey was conducted among 530 consumers to better understand spending behaviors as the COVID-19 pandemic subsides. The homeowners were over age 24, and only projects of $1,000 or more were included.
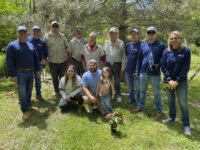
Clean, running water gifted to Illert family of Eureka, Missouri, through Hometown H2O Former St. Louis Rams star Chris Long and partners Xylem and Water Well Trust provided a local family of four in Eureka, Missouri, access to clean water with a donated water well system, equipment, well drilling and pump installation. The Illert family Read more
Clean, running water gifted to Illert family of Eureka, Missouri, through Hometown H2O
Former St. Louis Rams star Chris Long and partners Xylem and Water Well Trust provided a local family of four in Eureka, Missouri, access to clean water with a donated water well system, equipment, well drilling and pump installation. The Illert family – Justin Illert, veteran, age 30 yrs old, Sarah age 27, Lilah, age 5, and Austin, age 1 – was previously living without clean, running water in their home and relied on bottled water and rainwater for cooking and cleaning. The family now has reliable access to clean, potable water for the first time.
“It feels like we won the lottery,” said Sarah Illert, Water Well Trust beneficiary. “It means the world. It really is life changing for us. We are so grateful to have clean water to cook with, do our laundry, clean the dishes, and take clean showers and baths.”
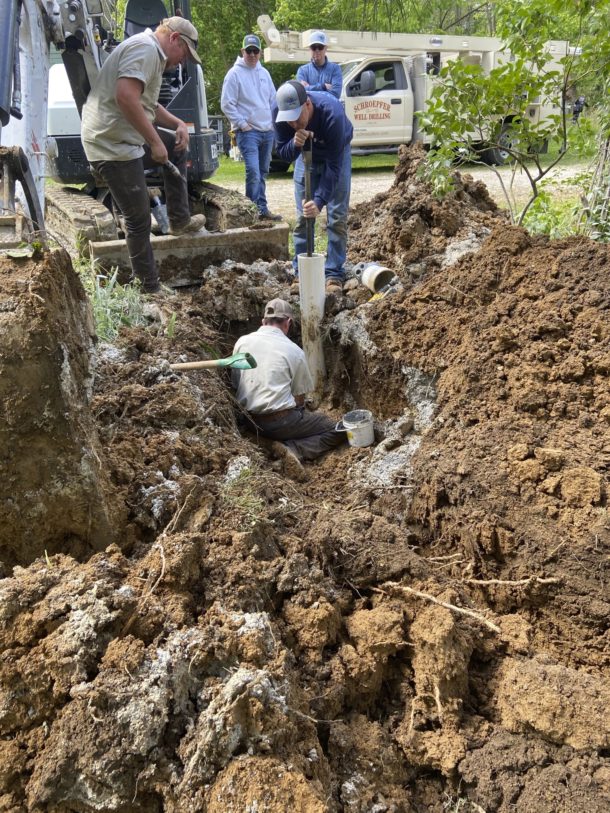
The donation marked the fourth project between Xylem Inc., Water Well Trust and Hometown H2O, which is a domestic water program dedicated to bringing clean, sustainable water to people and communities in need across the United States. Hometown H2O – a program launched in early 2020 – is a united effort between retired NFL player Chris Long and his Foundation’s Waterboys initiative and water technology company Xylem Inc. to address domestic water scarcity issues, which currently leave more than 2 million Americans without access to clean water. Hometown H2O and Xylem work alongside the Water Well Trust, a national nonprofit that helps qualify low-income families. This project was also supported by beverage company Talking Rain, who donated water to project staff and made a financial contribution to the family.
“Nobody should have to live without access to clean water– especially the brave and honorable men and women that have served our nation,” said Chris Long, two-time Super Bowl champion and founder of the Chris Long Foundation. “Clean water access for many Americans is an increasingly serious problem. Since Hometown H2O launched in 2020, we have raised awareness for water equality that affects policy at the state and federal levels. We will continue to prioritize this mission in our future projects. The organizations we work with, including Xylem and Water Well Trust, bring industry expertise to the table, and passionately do what it takes to make these projects successful. Thank you to our supporting partners for helping us to change lives and ensure that clean, running water is a basic human need that no American lacks.”
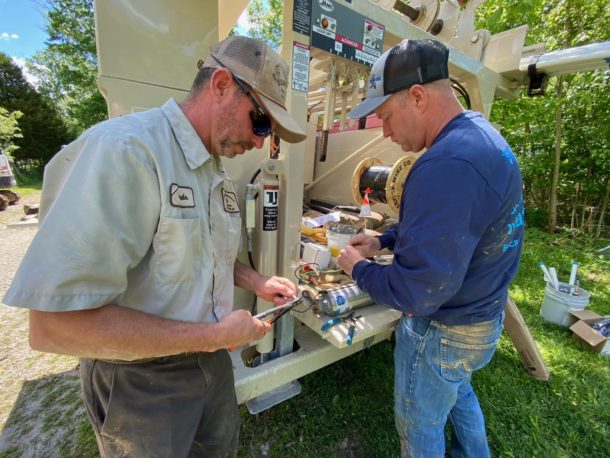
Xylem donated Goulds Water Technology brand equipment while local distributor partner Water Works of Springfield, Missouri, coordinated the discounted installation through pump installer Schroepfer Well Drilling, Inc. of Franklin County, Missouri. A team of volunteers – from Water Works and Xylem employees – also donated time to clean up the property’s yard.
“The unacceptable reality is that many Americans do not have access to potable, running water,” said Susan O’Grady, Director of Marketing, Building Services and Agriculture, Xylem. “For Xylem and its partners, we are honored to be able to use our expertise and passion for the cause to bring this vital service to people who deserve to have clean water.”
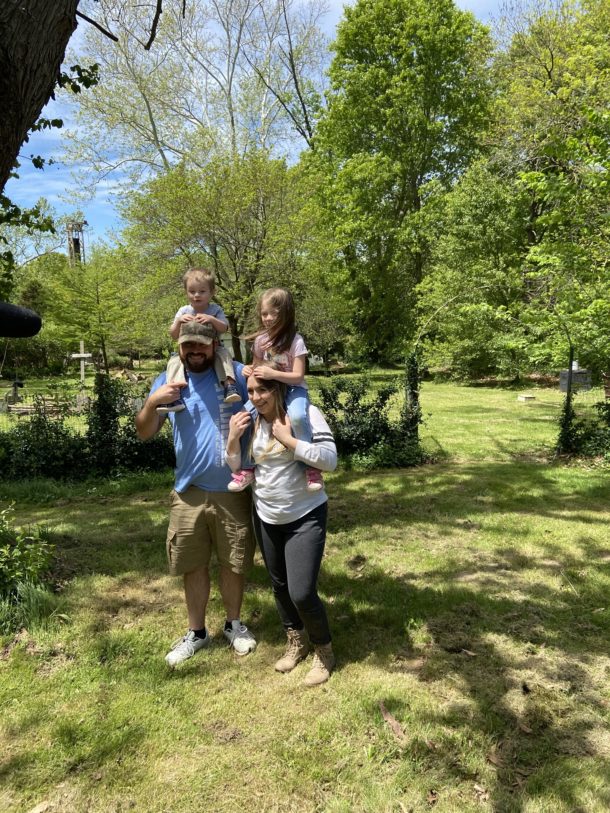
Xylem and Waterboys, along with nonprofit partner Water Well Trust, seek to raise awareness about domestic water issues, including that more 2 million people in the U.S. lack access to clean, safe drinking water at home. Working in coordination with Watermark and the company’s Goulds Water Technology brand, this partnership delivers ongoing water well projects to provide rural communities with reliable, safe water access, which can lead to better overall health and improved quality of life.
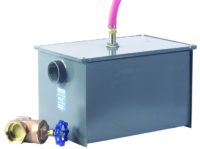
Restaurant grease traps are the devices design to intercept fats, oils and grease (FOG) from leaving a kitchen facility and entering a sewer system. Slimy FOG compounds that, by design, are trapped and held in place are chiefly byproducts of cooking that leach out of meats and dairy products. The idea is that wastewater flows Read more
Restaurant grease traps are the devices design to intercept fats, oils and grease (FOG) from leaving a kitchen facility and entering a sewer system.
Slimy FOG compounds that, by design, are trapped and held in place are chiefly byproducts of cooking that leach out of meats and dairy products. The idea is that wastewater flows from sink, wash area and cleaning table drains into tanks that are designed specifically to trap the crap that shouldn’t enter sewage systems. In a grease trap, solids settle while oils, fats and grease—usually lighter that water—float to the top where they’re arrested, keeping them from flowing out with the wastewater discharge.
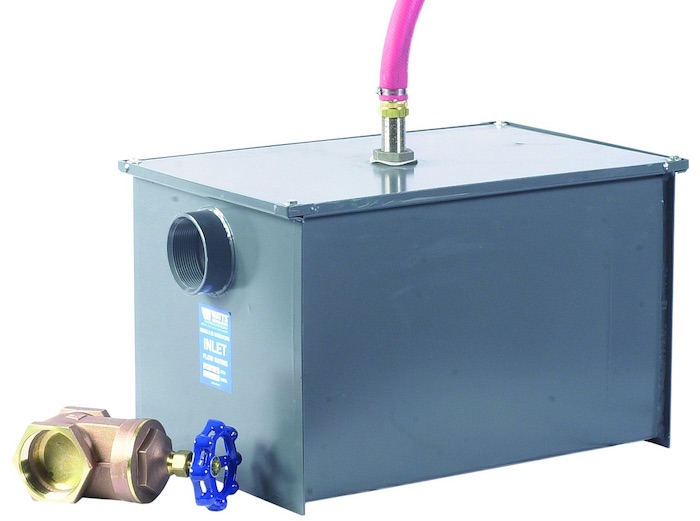
Typically, a grease interceptor works the same way as a grease trap, but on a much larger scale. They’re actually pretty simple devices, and their basic design hasn’t changed since the 1880s.
It’s flow rate that defines the difference between a grease trap and a grease interceptor. A grease trap is intended for use with flow measuring less than 50 gallons/minute. Larger operations—such as a poultry process plant—require the installation of a larger-scale “grease interceptor.”
Ask anyone in the municipal wastewater treatment business: one of the biggest environmental problems grease can have, outside of clogging pipes, is the disruption caused in the “digestive” process of water treatment plants. Bacterial processes are used to break down and clean sewage but FOGs can destroy these bacteria, causing all sorts of problems.
Design
Grease interceptors are designed with a high inlet/outlet, direction flow plate, vertical baffle and flow control device—all of which play a key role in the proper separation of grease.
High inlet/outlet layouts prevent the clogging of the inlet line, commonly seen in systems that have a lower inlet. This clogging, like that of the wastewater piping system, can result in a blockage or backup in the system or a reduction in separation percentage (grease to water) unsuitable for municipal wastewater systems.
Vertical baffle plates cause immediate disruption in the flow, forcing fluids directly to the bottom of the separation chamber where it is then met by the direction flow plate, initiating the separation process. From there, freshly separated water is reintroduced to the main water system and the grease is cleaned out by removing the cover and skimming it off the top.
Flow controls play a key role in the proper functionally of a grease interceptor because they’re designed to work properly under certain flow conditions.
Sizing is important. Prior to installing an interceptor, check with local authorities for sizing requirements. They may differ according to specific locations.
The following will outline the most common method for grease trap/interceptor sizing along with a few variables, with solutions that may affect overall system performance.
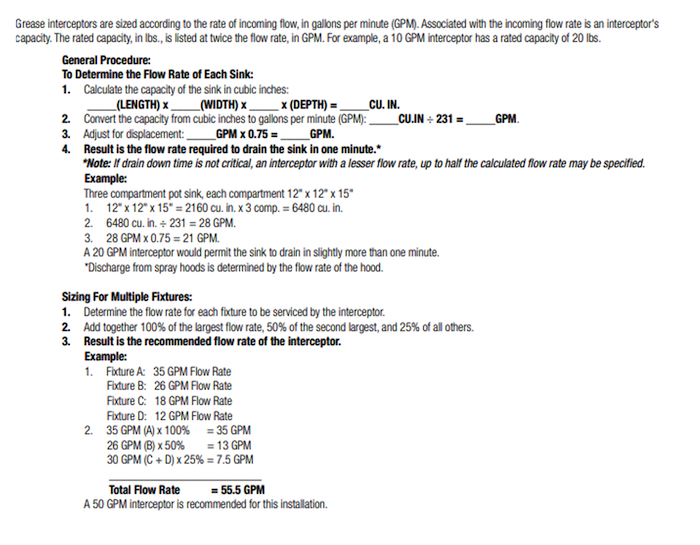
Performance affecting variables:
In the scenario described above (with a flow rate of 55 GPM), additional flow control devices may be needed if the incoming velocity/flow exceeds the recommended velocity. A high velocity incoming flow results in a more turbulence, which reduces the systems efficiency and increases the separation time.
Interceptor size needs increase if . . .
- the incoming ratio of grease to water increases. If the ratio of grease to water is higher, the separation process will not work.
- there’s a possibility of detergents in the system (soap/cleaning products, etc.). Detergents break down the grease particulars into smaller particles that will not separate properly and can pass through a grease interceptor – polluting the flow of water released into municipal treatment systems.
By increasing the size of an interceptor unit, both the flow path and separation time are increased, allowing the system to capture the particles more effectively.
Install a solids interceptor in series (prior to the grease Interceptor) if . . .
- the system contains solid particles (such as food). Because grease has a lower specific gravity than water, it floats to the top with ease. But when a solid (such as a French fry) is introduced it sinks to the bottom and overtime can pass through the system. By introducing a solids interceptor prior to the grease intercepting process this French fry or any other solids are caught and will not be at risk of re-entering the cities drainage system.
Installation
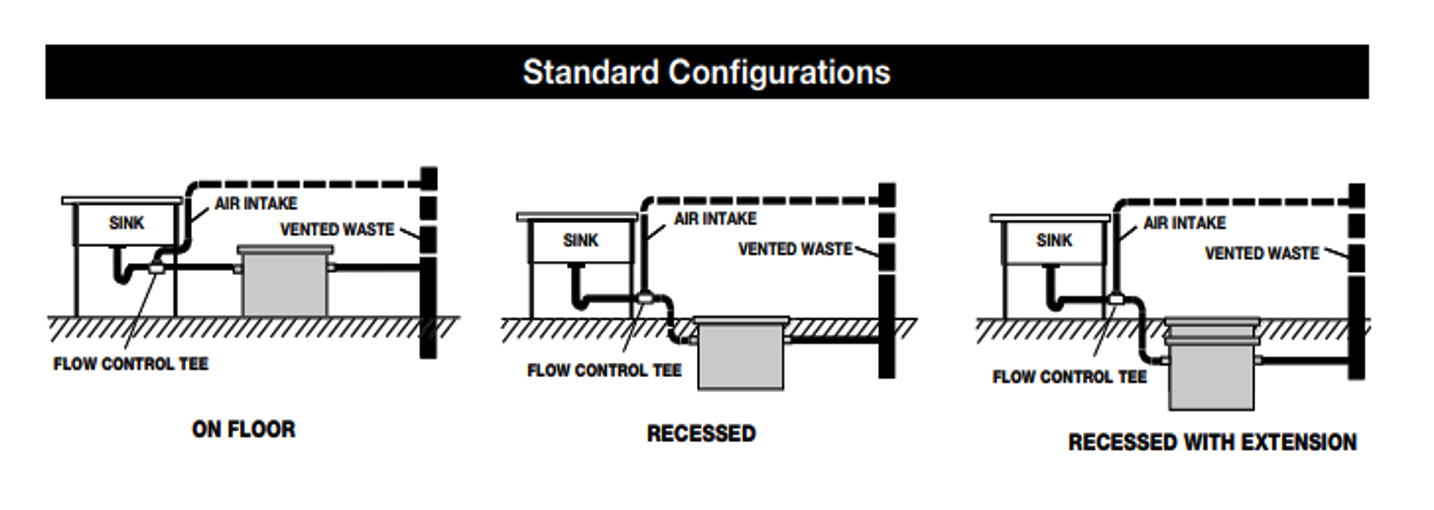
The installation of a grease interceptor is just as important in the operation of the system’s performance. First and foremost, the location of a grease interceptor should be as close as possible to the source of grease due to the cooling and solidification potential of grease over longer plumbing runs. For best results, the grease interceptor can be installed in any of the three orientations illustrated above.
Be sure—prior to finalizing the install location—to consider the clearance necessary to accommodate any connective piping and provide sufficient space for proper removal of the cover for cleaning purposes.
Key considerations
Grease interceptors are not designed to handle solid debris. In an application where solids are present, such as all sinks where garbage disposals are used, a solids interceptor is required to be used in conjunction with the grease interceptor. Due to the nature of greases—which have a natural attraction to solid particles—the presence of solids dramatically reduces a grease interceptor’s effectiveness. This can result in everything from unpleasant odors caused by the decay of solids, to the clogging of pipes or even the grease interceptor.
If an interceptor is installed outside, which is a common practice, it’s important to ensure all piping is installed below the frost line. In these applications, a single or series of extensions are common, allowing the interceptor to be buried low enough to avoid freezing.
Because proper flow through a grease interceptor plays an important role in its function, it’s important to regulate incoming velocities for proper separation to occur.
A flow control device is typically designed with an integral orifice (opening) to assure that an interceptor has optimal flow rate, and air intake. The following chart indicates the appropriate orifice size for gravity flow conditions (where no pressure or “head” is present).

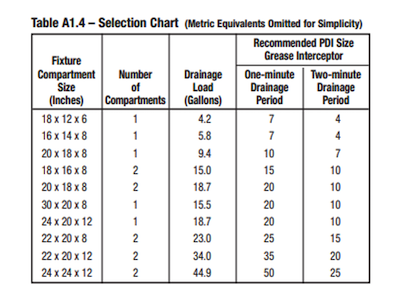
Frequently specified options:
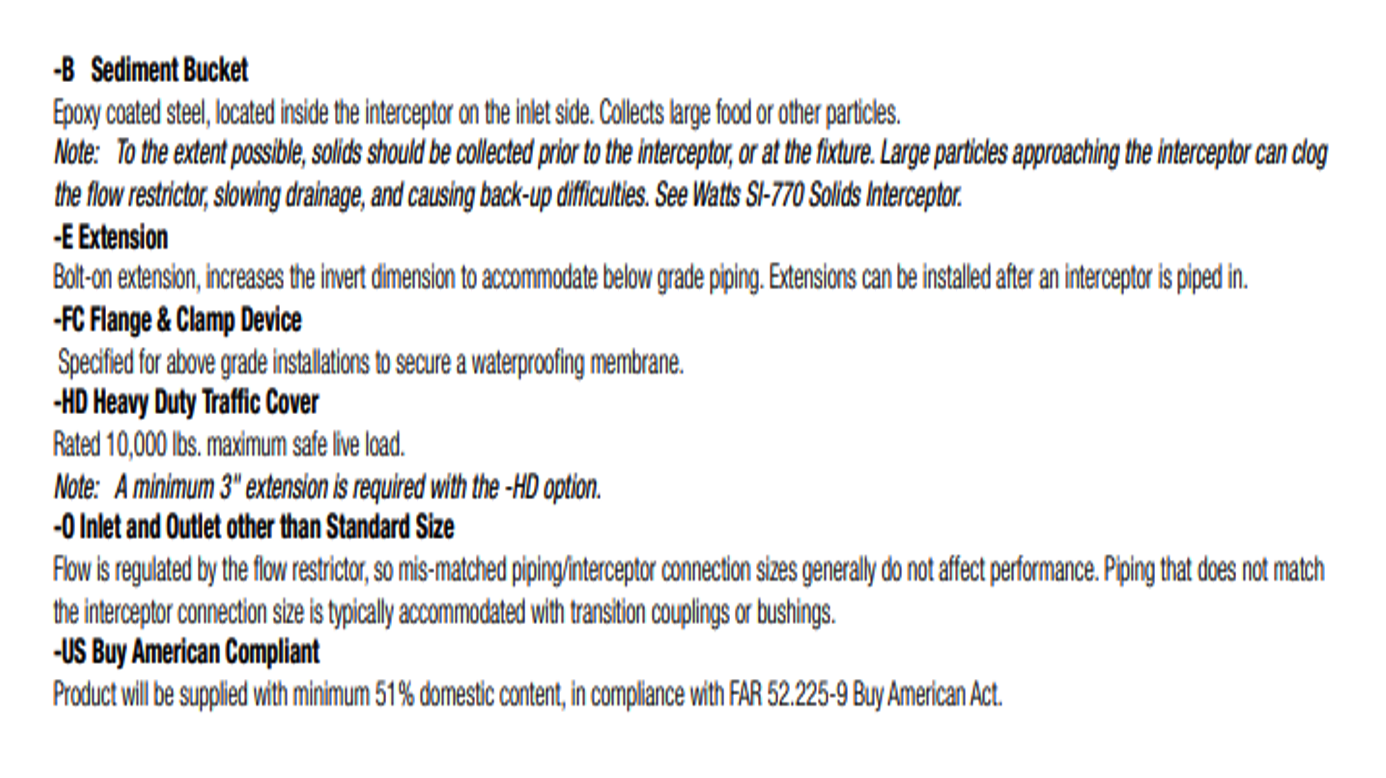
Maintenance + cleaning:
The cleaning frequency of a grease interceptor system is determined by the a.) capacity of an interceptor (measured in pounds of grease that can be trapped within it) and b.) the amount of incoming grease.
Because of this, grease removal intervals may vary from once a week to once every several weeks. When the necessary cleaning schedule has been determined based on a unit’s specific application and size, regular cleaning is necessary to maintain systems function and efficiency.
After the removal of accumulated grease and waste material, the interceptor should be thoroughly checked for any clogs or blockages in the inlet, outlet and air relief.
The following steps should be followed during the grease removal and cleaning process:
- Loosen and remove any fasteners used to secure the cover
- Remove the cover
- Clean out any grease.
- If applicable, use a scoop or shovel to remove any remaining solidified grease in unit
- If present, remove the sediment bucket; empty and clean thoroughly
- Using a clean water supply, hose down and wipe out the inside of the body
- Check integrity of cover sealing gasket (replace if needed)
- Reinstall cover and lock down hardware
If there is a semi-automatic interceptor in place, use the following steps for cleaning:
- With the outlet valve open, run a full stream of clean hot water (140°F min) through the interceptor for at least 2 minutes
- Allow unit to cool for approximately 3 minutes
- Close the valve on the outlet side of the interceptor
- Remove cap from top of interceptor and attach draw-off hose; position hose to drain into waste receptacle
- Run hot water through the interceptor at rate of 1.5 to 2.5 GPM
- Once filled, force the liquified grease out through the top draw-off hose
- When clear water begins to discharge through the draw-off hose, the interceptor is clean
- Disconnect the draw-off hose and replace the pipe cap
- Re-open the valve on the outlet and your interceptor is ready for normal use.
Robert DiPlacido, Mechanical Engineer, Watts, has eight years of experience in the plumbing market. The majority of his time was has been focused on commercial construction, chiefly with storm and wastewater management drainage systems, though also includes experience with roof and floor drainage systems, cleanouts, lavatory and urinal carriers, water separation systems (grease, oil and solids), trench drains, chemical waste and cross-linked polyethylene (PEX) tubing.