Advanced sensors deliver better in-pipe images while reporting the pitch of the camera in-pipe Experience the first true data-enabled plumbing diagnostic cameras with the new line of RIDGID SeeSnake cameras powered by TruSense technology. TruSense establishes a two-way datalink path between the camera head and a connected RIDGID SeeSnake CSx series Wi-Fi enabled monitor. With Read more
Uncategorized
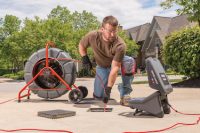
Advanced sensors deliver better in-pipe images while reporting the pitch of the camera in-pipe
Experience the first true data-enabled plumbing diagnostic cameras with the new line of RIDGID SeeSnake cameras powered by TruSense technology. TruSense establishes a two-way datalink path between the camera head and a connected RIDGID SeeSnake CSx series Wi-Fi enabled monitor. With TruSense, advanced sensors on the camera head convey valuable information about the in- pipe environment.
SeeSnake cameras with TruSense technology include a high dynamic range (HDR) image sensor that takes the next leap forward in diagnostic imaging. A common challenge faced by diagnostic professionals is being able to see far down the pipe as well as the image just in front of the camera’s lights. An HDR image sensor expands the camera’s dynamic range, allowing a greater ratio of bright and dark areas to be displayed in the same image at the same time without reducing visibility. This means fewer blown-out areas and sections of the pipe that are too dark to see, offering superior clarity and detail.
TiltSense is an on-camera inclinometer that is included on SeeSnake cameras with TruSense technology. The inclinometer measures the camera’s angle. When connected to a SeeSnake CSx series monitor, the camera can convey the camera’s degree of tilt on the monitor display—giving you a useful indicator of the pitch of the camera in-pipe.
“RIDGID SeeSnake cameras are trusted for having the clearest in-pipe picture along with features that help our customers work smarter and faster,” said Tim Dunphy, RIDGID Marketing Director of Underground Technologies. “With TruSense technology, HDR sensors and TiltSense deliver the image quality and information contractors need to see.”
SeeSnake cameras with TruSense technology are available in self-leveling models, which keeps the image upright, and non self-leveling models. All RIDGID SeeSnake cameras come with the RIDGID Full Lifetime Warranty.
To purchase or learn more about SeeSnake cameras with TruSense contact your local distributor, visit RIDGID.com, or call toll-free: 1-800-769-7743.
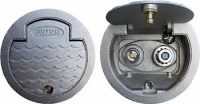
The new C-634RB1 heavy duty commercial hydrant round box is the answer to long and arduous hydrant box installations. This product was designed to simplify the process for plumbers, while maintaining the durability and finish of a traditional PRIER hydrant box. “A plumbers’ time is valuable, and they have always praised how easy it is to install our Read more
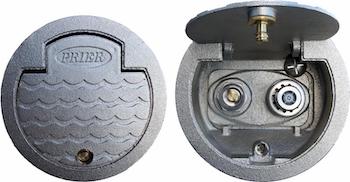
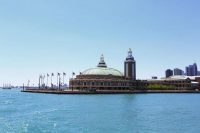
Navy Pier opened its People’s Energy Welcome Pavilion in 2017, designed to greet people as they get set to enjoy one of the Pier’s various amenities and provide them with information as they arrive. For the more-than-9 million guests that visit the Pier annually, the Welcome Pavilion needs to make a good first impression on Read more
Navy Pier opened its People’s Energy Welcome Pavilion in 2017, designed to greet people as they get set to enjoy one of the Pier’s various amenities and provide them with information as they arrive. For the more-than-9 million guests that visit the Pier annually, the Welcome Pavilion needs to make a good first impression on visitors, while setting the tone for what they’re to expect throughout the rest of the facility.
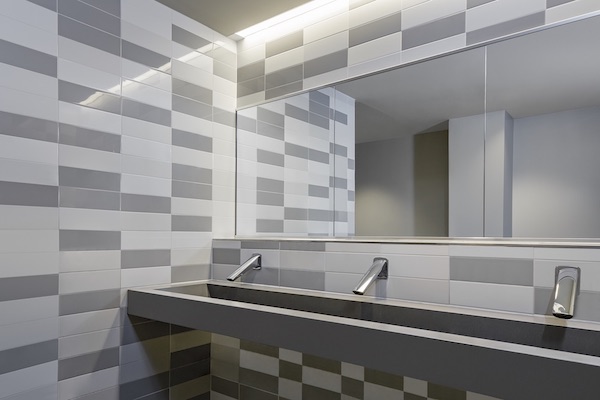
When it came time to specify commercial restroom products at the Welcome Center, not only did Sloan’s products present the elegant aesthetic that greets guests in a pleasant environment, but they also provide the durability to stand up to the millions of users each year. The Pier also needed products that would match its commitment to sustainability, and along with the facility’s energy-saving green roof and LED lighting, Sloan’s products help to make the building over 20 percent more efficient than traditional structures.
With Lake Michigan in its backyard, the Pier strives to protect and conserve water and the life around it. That’s why Navy Pier wanted water-saving flushometers that would contribute to its sustainability efforts in maximizing the guest experience while minimizing the environmental impact. Sloan SU-7009 small washdown urinal fixtures were paired with Sloan Royal® Sensor Flushometers (Royal 186 SFSM) to deliver an efficient 0.125 gallons per flush (gpf). Additionally, Sloan ST-2459 Elongated Wall-Mounted Water Closets were installed with Sloan Royal 111 SFSM Sensor Flushometers. With a static load rating of 750 pounds, the water closets can withstand the Welcome Center’s high-traffic environment, while the flushometer’s 1.28 gpf contribute to water savings across the facility.
The Pier paired Sloan DSG Designer Series sinks with its BASYS EFX800 wall-mounted faucets to present an aesthetically pleasing, yet sustainable handwashing experience. Featuring a cool Silestone Spa Suede finish, the ADA-compliant sinks complement the faucets’ sleek polished chrome appearance. The faucets’ infrared sensors enable a hygienic-friendly and touch-free handwashing process, with a flow rate of just 1.5 gpm and a line purge feature to eliminate stagnant water.
A totally new venture for the pump making giant: Air to Water Heat Pump System Taco’s new prototype heat pump was front and center. Imagine our surprise when first learning of Taco’s venture into the home heating appliance market through partnership with GlenDimplex. Taco has been a leader in the hydronic system component and pump Read more
A totally new venture for the pump making giant: Air to Water Heat Pump System
Taco’s new prototype heat pump was front and center. Imagine our surprise when first learning of Taco’s venture into the home heating appliance market through partnership with GlenDimplex.
Taco has been a leader in the hydronic system component and pump manufacturing industry since 1920. To our knowledge this is a first for the US pump giant. According to Wikipedia, GlenDimplex is an Irish based consumer electrical goods firm headquartered in Dublin, Ireland. The company is privately held. Has manufacturing and development centers in the Republic of Ireland, the United Kingdom, China and many other locations around the world.
We had no previous knowledge of this system prior to the show. Our interview with Taco Canada’s Mike Miller is below. All the technical details we know are included in the video.
Our thoughts on the new Heat Pump system
First, I’m told Taco had the new heat pump on display in their booth as sort of a “soft” reveal for their affiliated reps and interested vendors. This seems about right. Next, even the deepest Google searches and requests for official technical info from our contacts at Taco have come up short. Nonetheless it looks like a very exciting prospect for contractors, especially plumbing contractors not equipped to install refrigeration piping. In short, this is a hydronic system making it very attractive to a much larger crowd of potential installers.
AHR Expo 2019
First, we realize you may have missed attending AHR this year. However you can get a recap of the show from The Hub’s John Mesenbrink.
John’s latest blog touches on the city of Atlanta, some things that impressed him most [and some things that were a little less than impressive]. To clarify, please don’t get us started on our Uber/Lyft experiences while staying in the city. Check out John’s blog here.
Overall, if you found this and John’s blog useful please let us know! You can send us an email or post a comment below. In addition, you can see more of our coverage from the show by following us on Facebook or Instagram. Furthermore, you can watch the many videos we have on our Facebook page under the “AHR Expo 2019” playlist -OR- follow the #ahrhub tag on Instagram to see existing posts with more to come.
RIDGID® Press-In Branch Connector Tool Kit for 3/4-Inch Branches Eliminates the Need to Weld Ideal for chilled water, compressed air, industrial gas and low-pressure steam systems https://www.youtube.com/watch?v=9MuUwpBFQ4Q&t=23s Press Release: ELYRIA, OHIO – January 14, 2019 – Quickly make 3⁄4-inch branch connections on black steel pipe with the new RIDGID® Press-In Branch Connector Tool Kit being Read more
RIDGID® Press-In Branch Connector Tool Kit for 3/4-Inch Branches Eliminates the Need to Weld
Ideal for chilled water, compressed air, industrial gas and low-pressure steam systems
Press Release:
ELYRIA, OHIO – January 14, 2019 – Quickly make 3⁄4-inch branch connections on black steel pipe with the new RIDGID® Press-In Branch Connector Tool Kit being introduced at AHR Expo today. Significantly faster when compared to traditional welding, it is ideal for adding gauges or 3⁄4-inch pipe in chilled water, compressed air, industrial gas and low-pressure steam system applications.
Plumbers, pipe fabricators and maintenance professionals working on 11⁄2-inch to 6-inch black steel pipe will not only save time but also eliminate fire risk and avoid the additional expense of a fire safety watch.
The Connector Tool Kit includes an expander that fits all RIDGID standard press tools, including the RP 340, RP 330, RP 320 and CT-400, and works with Viega Press-In Branch Adapter Fittings. The kit also contains fitting positioning guides, an arbor shaft assembly, drill guide, and vacuum adapters.
The hole saw arbor attaches to standard drills, includes an M27 hole saw, and is designed to prevent the saw from penetrating both sides of the pipe; while the vacuum adapters allow for connection to standard size vacuum hoses to help reduce steel chips falling into the pipe while making the branch. Both the positioning and drill guides ensure proper placement against the pipe.
“The RIDGID Press-In Branch Connector Tool Kit takes our standard press tools up a notch. This accessory kit not only reduces complexity, but more importantly, it speeds up the process when creating branches,” said Rob Trefz, RIDGID Director of Business Development and Marketing. “Particularly in industrial gas settings, when you can eliminate flames and a fire watch, it provides significant project cost savings.”
The Connector Tool Kit comes with the RIDGID Full Lifetime Warranty. Contact your local distributor, visit RIDGID.com, or call toll-free: 1-800-769-7743 to learn more.