The 708-unit military community saves more than one million gallons of water in one month. INSTALLATION AT LA MESA VILLAGE COMMUNITY In October 2014, Monterey Bay Military Housing upgraded La Mesa Village Community with all new Ultra-High-Efficiency-Technology (UHET™) Water- Saving Kits from Niagara Conservation with no upfront costs. Niagara’s UHET Kits provided La Mesa Read more
Uncategorized
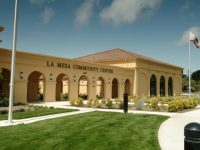
The 708-unit military community saves more than one million gallons of water in one month.
INSTALLATION AT LA MESA VILLAGE COMMUNITY
In October 2014, Monterey Bay Military Housing upgraded La Mesa Village Community with all new Ultra-High-Efficiency-Technology (UHET™) Water- Saving Kits from Niagara Conservation with no upfront costs. Niagara’s UHET Kits provided La Mesa Village residents with drastically lowered utility bills and reduced maintenance issues.
THE PRODUCTS
La Mesa Village installed Niagara’s UHET Kits throughout the 708-unit property. Each UHET Kit consists of five high-efficiency products that drastically reduce water and energy usage. Each kit included Niagara’s EPA WaterSense® certified Original Stealth 0.8 GPF toilet, Earth Massage 1.5 GPM showerhead, and 1.0 GPM kitchen and bathroom aerators.
The Original Stealth boasts the lowest gallons per flush on the market; flushing at just 0.8 gallons each time thanks to Stealth Technology – a patented, re-engineered flush that works better and wastes nothing. The showerhead and aerators have Niagara’s Equiforce™ Technology, a pressure-compensating technology that guarantees a powerful, consistent flow rate regardless of available water pressure.
The 0.8 GPF toilets were installed to replace the older 1.6 GPF toilets previously found on the property. Monterey Peninsula Water Management District helped fund the retrofit by providing property managers rebates for every toilet installation.
RESULTS
The retrofit began in October 2014 and was completed in less than 30 days. According to Adrian Jimenez, Operations Manager for Monterey Bay Military Housing, La Mesa Village saved 1,113,500 gallons of water when compared to the previous year.
“The installation of Niagara’s high-efficiency plumbing fixtures have been nothing but well received by our residents in the La Mesa Village,” stated Jimenez. “Each retrofit was completed with the utmost professionalism and ease. And since the project’s completion last November, we have not only seen remarkable reductions in water usage within each unit of the community, but also we have received zero complaints from our residents.”
Mokena, Ill. (June 7, 2019) — ASSE 1053-2019, Performance Requirements for Dual Check Backflow Preventer Wall Hydrants—Freeze Resistant Type, has been designated as an American National Standard by the American National Standards Institute (ANSI) and is now available for purchase. ASSE 1053 establishes design and performance requirements for Freeze Resistant Dual Check Backflow Preventer Wall Read more
Mokena, Ill. (June 7, 2019) — ASSE 1053-2019, Performance Requirements for Dual Check Backflow Preventer Wall Hydrants—Freeze Resistant Type, has been designated as an American National Standard by the American National Standards Institute (ANSI) and is now available for purchase.
ASSE 1053 establishes design and performance requirements for Freeze Resistant Dual Check Backflow Preventer Wall Hydrants, which protect the potable water supply against backsiphonage and backpressure without damage to the device due to freezing. To verify protection under the high hazard conditions present at threaded hose outlets, these devices must be field-testable.
ASSE 1053 devices are classified as Type A or Type B. Type A devices automatically drain water when the hydrant valve is closed and the hose is removed to prevent damage from freezing, and Type B devices automatically drain water with a hose removed or attached, end nozzle closed, and the hydrant valve closed.
“ASSE Standard 1011, Performance Requirements for Hose Connection Vacuum Breakers, was issued for hose bib vacuum breakers, which provide excellent backsiphonage protection with a single check valve and an atmospheric vent valve,” said Herb Hoeptner, Chairperson of the ASSE 1053 Working Group and owner of Hoeptner Preferred Products. “This standard, ASSE 1053, focuses on devices containing two check valves — dual check backflow preventer wall hydrants. These devices provide both backsiphonage and low-head backpressure protection and are suitable for high hazard applications.”
Performance requirements in ASSE 1053 include compliance testing for hydrostatic pressure, water flow capacity and pressure loss, deterioration at maximum rated temperature and pressure, resistance to bending, self-draining capabilities, backflow, backsiphonage, and backpressure, among other testing requirements.
To purchase ASSE 1053-2019, please visit the ASSE International Webstore at www.assewebstore.com.
Intergas joins Rheem’s Global Water Division, expanding its water heating and boiler portfolio for both residential and commercial applications to meet demands in Europe and additional markets worldwide Atlanta and Coevorden, The Netherlands—On May 31, 2019, Rheem acquired Intergas of Coevorden, the Netherlands, through its group entity, Paloma Rheem Global, Inc. Intergas is a leading Read more
Intergas joins Rheem’s Global Water Division, expanding its water heating and boiler portfolio for both residential and commercial applications to meet demands in Europe and additional markets worldwide
Atlanta and Coevorden, The Netherlands—On May 31, 2019, Rheem acquired Intergas of Coevorden, the Netherlands, through its group entity, Paloma Rheem Global, Inc. Intergas is a leading manufacturer of high-efficiency, residential gas boilers and water heaters. Renowned for its state-of-the-art boiler technology, Intergas leads the Dutch market for gas-fired condensing boilers and has fast-growing subsidiaries in the United Kingdom, as well as Canada and the United States via its IBC® brand.
Rheem is the only manufacturer in North America that produces heating, cooling, water heating, pool/spa heating, commercial boilers and commercial refrigeration products. Today, Rheem is America’s #1 water heating brand, and its products are available in more than 50 countries. Headquartered in Atlanta, the company’s portfolio of premium water brands include Rheem®, Raypak® Ruud®, Eemax®, EcoSmart®, Richmond®, Splendid®, Solahart® and EverHot™.
With the acquisition of Intergas, Rheem will obtain a first-class platform in the European heating and hot water market, which is the second largest in the world.
“We are very pleased to welcome Intergas as an important part of our Global Water Division,” said Chris Peel, President and CEO of Paloma Rheem Global, Inc. “The addition of Intergas into the Rheem family of brands increases the breadth of our boiler and water heating offerings, while also providing Rheem with competitive solutions to meet consumer demands in Europe. Both Rheem and Intergas also proudly foster cultures of inclusion, and our organizations have a shared commitment to innovating all-new products that create a meaningful and positive environmental impact.”
Janno de Haas, CEO of Intergas, added, “We are very excited to join the Rheem family of brands. Rheem understands our core business and its leadership is committed to long‐term growth plans for Intergas. We look forward to accelerating product innovations together with Rheem, and expanding into new markets and regions in the future.”
Intergas will join Rheem’s Global Water Division and operate as a wholly owned subsidiary of Paloma Rheem Global, Inc. Its headquarters will remain in Coevorden.
“The strong synergies in product offerings and complementary cultures make the joining of Rheem and Intergas a truly exciting—and monumental—collaboration,” said Rich Bendure, President of Rheem’s Global Water Division. “Combined, we now offer an extremely compelling and comprehensive water heating and boiler portfolio for both residential and commercial applications.”
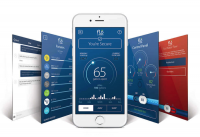
Since its formation in 1926, IAPMO has been known for its progressive focus on the future. One might believe sanitation and the use of resources have reached a peak; this sort of thinking, however, is not within the realm of IAPMO’s culture. IAPMO Codes and Standards excels in recognizing technology that improve the lives of Read more
Since its formation in 1926, IAPMO has been known for its progressive focus on the future. One might believe sanitation and the use of resources have reached a peak; this sort of thinking, however, is not within the realm of IAPMO’s culture. IAPMO Codes and Standards excels in recognizing technology that improve the lives of Americans and elsewhere. Over time, IAPMO has proven to be the leader in bringing innovation to the industry while, at the same time, protecting the public health and welfare.
Non-Sewered Sanitation Systems
Since the early 1900s, technologies from flight to telephones have advanced with tremendous progress. We have gone from a simple 12 horsepower engine propelling an aircraft to jets that can break the sound barrier. Telephones have gone from rotary dial and cords to smart phones that have far more computing power than all the computers used to send the first man to the moon in 1969.
But what about wastewater management? It has not really advanced much. Yes, the sanitation is far safer than it was in the early 1900s, but the concept is the same. Not to mentioned that more than 2.3 billion people across the world lack access to basic sanitation services.
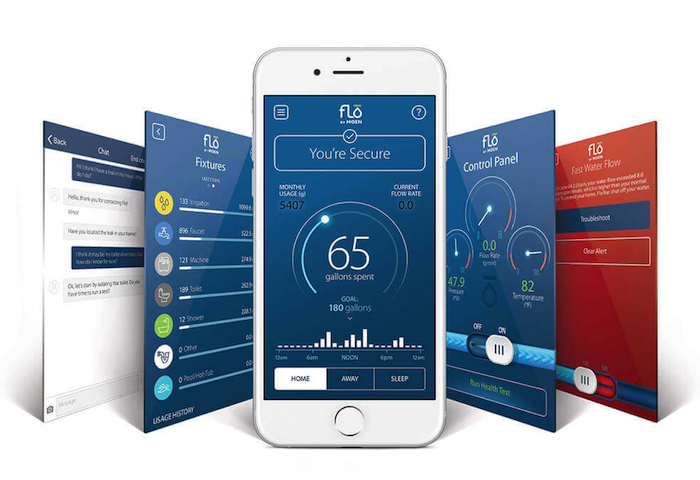
Water-leak-detection technology listed to the IAPMO standards has the capability of letting the homeowner know if there is a water leak with the use of a smartphone.
Now there is technology that is attempting to take sanitation to another level. It is technology that has already benefited areas where resources are scarce. Any country that adopts this technology has taken a leap into the future of sanitation. This technology is the Non-Sewered Sanitation System (NSSS) and it is covered by the ISO 30500 standard.
ISO 30500, Non-sewered sanitation systems—Prefabricated integrated treatment units—General safety and performance requirements for design and testing, seeks to provide general safety and performance requirements for the product design and performance testing of these non-sewered sanitation systems. It applies to integrated sanitation systems that are not attached to a sewer.
The ISO 30500 standard helps develop new toilet technology that will save millions of lives
Imagine using a toilet where the drainage system has the capability of preserving energy for use in other applications, such as powering lights, and with a recirculation loop for fluid reuse. Imagine a remote location where there is no water supply or a drainage system, yet you can have a fully functional toilet or urinal. The possibilities are endless with the use of the NSSS technology.
IAPMO is leading this effort to bring the NSSS technology to countries such as the United States and Canada. A committee with both U.S and Canadian stakeholders is preparing to bring the ISO 30500 standard to these respective countries as an American National Standard (ANS) and National Standard of Canada (NSC).
States like Hawaii or other areas where the use of cesspools is of concern, or California where droughts are common, can benefit from this technology. Likewise, provinces in Canada can also derive benefit.
Safe sanitation is something that IAPMO takes seriously and IAPMO feels privileged to be selected as the Accredited Standards Developer (ASD) by ANSI to introduce this technology to the U.S. and Canada.
Leak-Detection Systems
As stated, there are areas where resources are scarce. Such scarcity does not only apply to underdeveloped nations but well-established, developed nations, as well. There are areas in the United States where safe and sanitary water is not a basic commodity. From California to New York, and around the globe, water is a resource that must be cherished and protected. A drop of water the size of grain of rice can be easily ignored or overlooked due to its local minimal effect. This miniscule drop multiplied numerous times around the globe now becomes a large body of water. This now becomes something that cannot be overlooked.
IAPMO Codes and Standards is once again at the forefront tackling this issue. IAPMO has long published standards that address water-leaking detection products. Those standards are the IAPMO IGC 115 and IAPMO IGC 349, which are expected to become national standards soon (IAPMO Z1115 and Z1349). These standards are being used for the listing and certification of products designed to detect water leaks. Jurisdictions nationwide are already looking for the IGC 115 and IGC 349 mark for these products.
The water-leak-detection technology listed to the IAPMO standards has the capability of letting the homeowner know if there is a water leak with the use of a smartphone. Aside from preserving resources, a homeowner will save money on their water bill and insurance companies can have peace of mind that water leaks will be detected prior to causing major damage to the structure. Aside from damage to the structure, leaks that are not properly fixed can cause mold to grow.
IAPMO Codes and Standards prides itself as being the go-to-source for new and novel products. There are many plumbing technologies that began as an IAPMO standard and slowly became a normal part of our lives. Many innovators and manufactures have taken advantage of IAPMO’s services to ensure that their novel products find their way into the industry. As technology rapidly improves, IAPMO Codes and Standards is ready to meet the needs of the industry.
Code Development
The IAPMO codes provide consumers with safe and sanitary systems while, at the same time, allowing latitude for innovation and new technologies. The industry looks to IAPMO codes to address innovations or novel products.
The Uniform Plumbing Code (UPC) introduced an appendix that provides a modern way of sizing water supply piping. The newly developed Water Demand Calculator (WDC) recognizes that the world is now utilizing lower flowrate fixtures. In many states, it is law to use low-flow fixtures. Due to the lower water demand, the existing water pipe sizing method used will typically lead to oversizing, which means more volume of water in the piping. The larger volume of water equates to longer waits for the hot water to come out of the shower. This also leads to more water waste. The UPC is the only code that takes all this into account with the Water Demand Calculator (WDC) in Appendix M. The WDC is the first update since Hunter’s 1940 Curves to estimate peak water demand for single and multi-family dwellings using efficient fixtures. It reduces meter and pipe sizes and increases cost savings.
The Uniform Mechanical Code (UMC) was the first national mechanical code to address A2L refrigerants. A major milestone that introduced lower flammability refrigerants such as A2L and B2L. The industry’s concerns to address lower Global Warming Potential (GWP) refrigerants led to the development of these lower flammability refrigerants.
But why stop there? The Uniform Codes also have up-to-date provisions for geothermal, solar thermal energy systems and hydronic energy systems.
IAPMO’s codes based on principle and on a proven consensus process, the ANSI process. It is the only process that has been proven time and time again to employ true consensus. It is a development process that is used internationally for a reason. It is a process that has an oversight from a third-party to assure true consensus.
Whether it is codes or standards, IAPMO is the Standards Development Organization that is bringing innovation to the industry. Jurisdictions everywhere are taking advantage of IAPMO’s proven process because IAPMO codes and standards are developed by the industry for the industry. The Uniform Codes don’t only claim to be ahead of the curve, they are.
Please visit http://www.iapmo.org/standards-development/american-national-standards for more information.
Hugo Aguilar, P.E., is Senior Vice President of Codes and Standards for IAPMO.
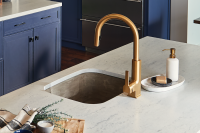
When it comes to style trends and technology, kitchen and bath products have kept up in today’s marketplace. In terms of finishes, designers and homeowners alike are looking for statement pieces that will stand out in a space and get noticed. “With a wider array of finishes becoming more popular in the marketplace, and the Read more
When it comes to style trends and technology, kitchen and bath products have kept up in today’s marketplace. In terms of finishes, designers and homeowners alike are looking for statement pieces that will stand out in a space and get noticed. “With a wider array of finishes becoming more popular in the marketplace, and the rising trend of combining different finishes and textures, Moen, for example, has thoughtfully crafted a sophisticated Brushed Gold finish,” says Danielle Radic, product manager, Moen.
Historically, gold fixtures were often associated with traditional design, but now, homeowners are also using this finish as part of a modern aesthetic, says Radic. Moen’s Brushed Gold finish, available on select kitchen and bathroom faucets, allows consumers to add elegance to their space and blends seamlessly with a variety of décor styles. “It also mixes well with other gold accents they may have throughout their space and has been designed to stand the test of time,” says Radic.
Additionally, homeowners continue to incorporate dark finishes into their homes. Moen’s on-trend Matte Black finish, available on a selection of kitchen and bath fixtures, offers a contemporary look that complements a variety of décor choices, while providing consumers with a unique finish that makes a statement.
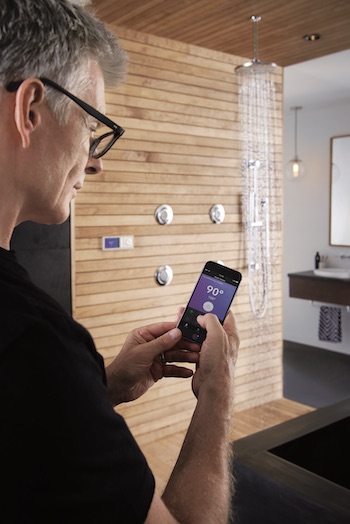
In regards to technology, consumers also are continuing to gravitate towards innovations that make their lives easier, including products that offer the benefit of smart technology. “In 2019, we’re showcasing some updates to the U by Moen shower, which is a cloud-based, app-driven digital shower that offers Wi-Fi mobile connectivity and unmatched personalization, delivering on consumers’ desire to create their perfect shower experience with up to 12 customizable presets,” says Michael Poloha, group manager, IoT, Moen. Consumers can control their shower anyway they like: with their voice, the smartphone app or the in-shower controller.
The product now features enhanced functionality with Amazon Alexa—including compatibility with groups and routines—as well as compatibility with Apple HomeKit™ and Google Assistant™. There’s also a new Matte Black controller finish for additional design customization.
“We’re also excited to introduce Flo by Moen, a game-changing smart home water monitoring and leak detection system that enables homeowners to control their home’s water from their smartphones,” says Poloha. It calculates water pressure, flow rate and temperature within the home’s water supply system while using AI to differentiate normal water use from abnormal use. This enables the device to monitor and help detect water leaks and other vulnerabilities, says Poloha.
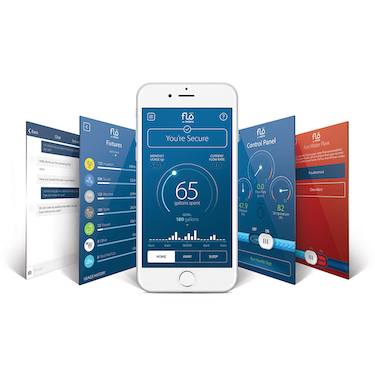
The Flo by Moen app provides users with real-time information about their home’s water consumption habits and alerts to any abnormalities. Within the app, users can control how the system provides alerts and respond to potential issues. Alerts may be sent to users through push notifications, via email, or by text or phone call. The user also can turn off their water directly from the app.