Navien’s combi-boiler is possibly the most common combi- in the US market but working on or replacing parts for the combi can be a real challenge. I’ve serviced and installed quite a few in the last 3-5 years and the flow sensor is definitely one part that seems to fail more than others. If you Read more
Uncategorized
Navien’s combi-boiler is possibly the most common combi- in the US market but working on or replacing parts for the combi can be a real challenge. I’ve serviced and installed quite a few in the last 3-5 years and the flow sensor is definitely one part that seems to fail more than others. If you find yourself looking at this part replacement you may benefit from a couple tips I’ve shared in this video.
Please forgive the video quality, I decided to make this last minute and only had my iPhone (hand held without a tripod). If you find this useful please share with your friends or post to your favorite FB group.
If you’re interested in purchasing the tools I use in the video just click the links or pics below for the best pricing I have found.
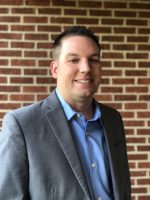
Brewster, N.Y. — Matco-Norca has announced the appointment of Brian Jennings to its Industrial sales team. Jennings comes aboard as Assistant Vice President of Sales, reporting to Vice President of Sales & Marketing Scott Bardreau. He will focus on Matco-Norca’s growing industrial products business. A graduate of the University of Kentucky, Jennings brings solid industrial Read more
Brewster, N.Y. — Matco-Norca has announced the appointment of Brian Jennings to its Industrial sales team. Jennings comes aboard as Assistant Vice President of Sales, reporting to Vice President of Sales & Marketing Scott Bardreau. He will focus on Matco-Norca’s growing industrial products business.
A graduate of the University of Kentucky, Jennings brings solid industrial B2B sales experience to his new position, having worked previously for Apollo Valve and NIBCO.
Huntington Beach, Calif. — California Faucets celebrates 30 years as a manufacturer of artisan-crafted bath and kitchen fixtures. Over the course of three decades, California Faucets has helped shape the direction of the industry, offering a versatile mix of game-changing products that look and function better. At the same time, the manufacturer has remained true Read more
Huntington Beach, Calif. — California Faucets celebrates 30 years as a manufacturer of artisan-crafted bath and kitchen fixtures. Over the course of three decades, California Faucets has helped shape the direction of the industry, offering a versatile mix of game-changing products that look and function better. At the same time, the manufacturer has remained true to its roots by focusing on old-fashioned customer service and efficient turnaround on custom orders of its premium-quality products.
California Faucets’ history of innovation has resulted in products and technologies that have shifted the industry’s approaches to both design and performance. Most notable among those is StyleDrain®, the first decorative shower drain with fast-flow efficiency. StyleDrain transformed a category that was once restricted to lackluster, industrial-like drains into a sleek focal point. The industry took notice of California Faucets’ innovations, recognizing StyleDrain and line extensions StyleDrain® Tile and CeraLine® with numerous awards, including three prestigious Best of Year (BoY) Awards from Interior Design (ID) magazine.
A fourth ID award was bestowed upon ZeroDrain®, the world’s first “pop-down” lavatory drain that turns a utilitarian product into a sleek design statement; the drain sits flush with the sink instead of awkwardly protruding. A one-finger touch opens and closes ZeroDrain, which makes installing and cleaning it fast and easy. Another breakthrough was California Faucets’ StyleTherm®, which brought advanced thermostatic technology, previously limited to the luxury market, into an affordable price point suitable for every bathroom in the home. Thanks to creative engineering and years of development, StyleTherm offers a range of features unavailable with pressure balance systems, including dialing-in to exact temperatures, no diverter valve required to toggle between shower applications, independent volume operation for each application, anti-scald protection, and a higher water flow rate.
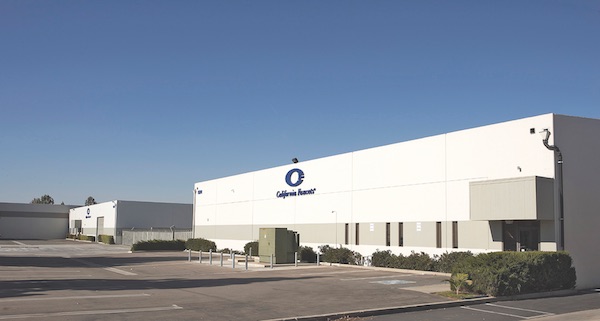
Along with its reputation for innovation, California Faucets prides itself on its culture rooted in old-fashioned values and fine craftsmanship. With the mantra, “artisan hands, not mass produced,” the manufacturer continues to deliver custom-built, handcrafted solid-brass fixtures in 30-plus hand-produced finishes, even as it has gradually expanded in size and industry footprint.
The wide array of finishes, including 15 decorative PVD finishes with a lifetime guarantee against tarnishing, establish the brand as a world leader in PVD while playing an important role in the manufacturer’s ability to satisfy most any design vision. In essence, by offering the ability to customize any spout in any handle in any finish, California Faucets presents users with nearly limitless design freedom.
“Thanks to my father, Fred Silverstein, California Faucets was founded in 1988 with core values of delivering high-quality decorative faucets in a timely fashion supported by superior customer service. Thirty years later, these principles remain the core of our company culture,” says Jeff Silverstein, President & CEO. “Of course, while the DNA of our company hasn’t changed, we’ve evolved immensely in terms of innovation, technology, and design,” he says, noting that three family members are by his side in their dedication to ensuring the handmade faucet company his father built continues to evolve and thrive. In order of seniority, they include Jeff’s cousin Noah Taft, Senior Vice President of Marketing and Sales; his sisters, Tina Silverstein, who handles the company’s digital marketing and Sue Cuthbert, who recently joined as the new product launch coordinator. “Overall, we’ve created a formula that has gratifyingly resulted in stellar growth and an ability to continue delivering our luxury designer fittings on a grander scale. I’m proud that we’ve accomplished this growth and continue to be a leader in innovation all while sticking true to the roots my father established three decades ago.”
Fred Silverstein’s cultural vision also is reflected in the company’s devotion to its Huntington Beach home base, where it employs 180 people and has earned the coveted, “Made in California” designation. “We’re extremely proud to do all of our own design, engineering, finishing, and assembly right here in Huntington Beach,” says Noah Taft, Senior Vice President of Marketing and Sales. “In fact, California Faucets employs more American labor per faucet sold than almost any other faucet manufacturer, a detail that is just as important to the company’s legacy as our reputation for innovation and craftsmanship.”
To see more innovations and artisanship from California Faucets’ storied history, visit www.californiafaucets.com.
After months of use, varied from thawing frozen AC coils to straightening PEX-a kinks on radiant tubing installs I think its time to set the record straight on cordless heat guns. Of, the only cordless heat gun, Milwaukee’s M18 #2688-20. Its legit. First let me say its not a complete replacement for a corded, multiple Read more
After months of use, varied from thawing frozen AC coils to straightening PEX-a kinks on radiant tubing installs I think its time to set the record straight on cordless heat guns. Of, the only cordless heat gun, Milwaukee’s M18 #2688-20.
Its legit.
First let me say its not a complete replacement for a corded, multiple temperature heat gun. The M18 is a single temp (listed at 875F on acmetoosl.com) but that is enough for typical tasks like heat shrink for wiring, simple thawing of small diameter piping and even PEX repair.
The 2688 Heat Gun has a well designed hook for carrying or storage. The hook fits well onto a belt or pants pocket but wont hang on a ladder rung or anything larger than about an inch in thickness.
Available accessories kit (49-80-0300) includes four different heat gun nozzles for a variety of specialty tasks. Each nozzle is fully compatible with any of Milwaukee’s heat guns. The deflector nozzle directs hot air to specific points, which is most useful when you want to strip a window of sealants without cracking the glass under heat. Air reduction nozzles further refine the blast of hot air to a small, circular point for spot melting. A hook nozzle moves the air flow in a circular pattern, which seals shrink wrap around cables or other similarly-shaped pieces instantly. The air spreader nozzle increases the width of the air blast and is useful for a variety of heat gun applications, including drying paint, putty, concrete filler and other construction materials.
The 2688 is not a full power heat gun and likely never will be, battery tech has come a long way but there are certain limits that we may always be up against with tools like this. Its a very useful tool and has earned a spot in my daily PACKOUT case for sure.
https://www.instagram.com/p/BmIwN1CH13w/?taken-by=mechanicalhub
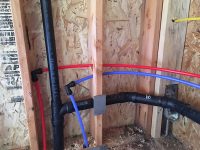
John Guest has continued to be a manufacturer of choice for the most innovative and high-quality plumbing materials on the market. JG ProLock and JG Speedfit feature the most advanced plumbing technology currently available, allowing them to be both efficient and easy to install. It is precisely these qualities that first piqued the interest of Read more
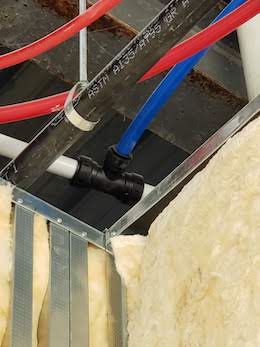
JG ProLock
John Guest has continued to be a manufacturer of choice for the most innovative and high-quality plumbing materials on the market. JG ProLock and JG Speedfit feature the most advanced plumbing technology currently available, allowing them to be both efficient and easy to install.
It is precisely these qualities that first piqued the interest of Trilogy Plumbing. Trilogy Plumbing Inc., headquartered in Anaheim, Calif., is among the preeminent plumbing contractors in the region. They specialize in the installation of first-class plumbing systems for new commercial and residential properties.
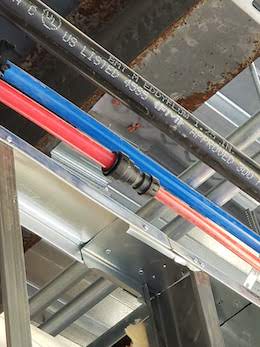
JG ProLock
Like John Guest, Trilogy possesses an unwavering commitment to the delivery of only the highest-quality services and results for their customers. In adhering to this goal, they work closely with constructors to assure that their systems will meet their desired standards.
Having familiarized himself with the benefits of John Guest’s JG Prolock and JG Speedfit, Trilogy Plumbing Vice President Rich Langenwalter recognized that John Guest products would be a perfect fit for his company and would uphold their commitment to providing excellent services for their clients. Langenwalter was particularly enamored with the fact that neither JG ProLock nor JG Speed fit require any tools to make lead-proof connections, drastically decreasing the installation times for plumbing systems. These benefits led Mr. Langenwalter to use John Guest fittings in the construction of Trilogy Plumbing’s first multi-million-dollar custom home.
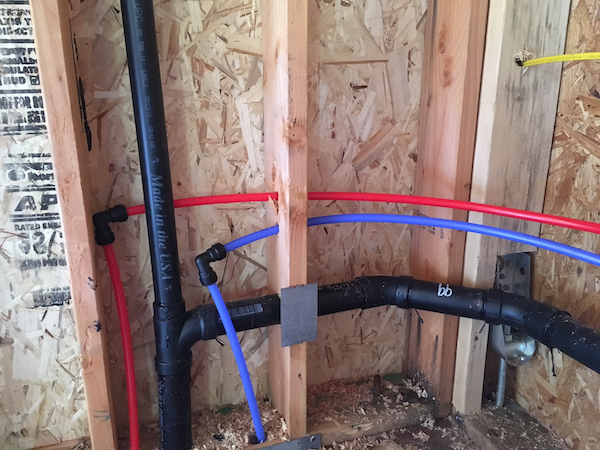
Impressed with ability of the JG ProLock to facilitate a swift and premium installation process on the home, Mr. Langenwalter said, “This is a high-end fitting which I want to use for our high-end custom homes.” The project manager and technicians both spoke highly of John Guest’s products and credited them with making the installation process easier and more efficient. The quality of John Guest fittings was verified through the installation process, after which over 200 ProLock couplers, elbows, tees, reducing tees, reducers, and brass fittings all passed inspection immediately following construction. Langenwalter has since requested the incorporation of John Guest fittings in future Trilogy Plumbing projects.
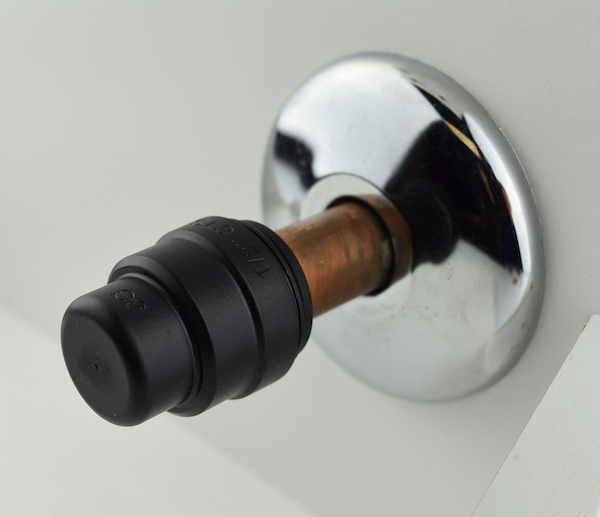
ProLock End Cap
Trilogy’s projects range from a 200-fitting custom house to a 35-fitting one-bedroom apartment. Their experience with John Guest products has led them to conclude that no matter what the size of the project, John Guest fittings are the premier product for the execution of a swift, high-quality installation. John Guest is pleased that Trilogy Plumbing had such an enjoyable and satisfactory experience with JG ProLock and Speedfit, and looks forward to providing the necessary fittings for future Trilogy projects.