The son of an arcade owner, you could say that business ran in his blood. Born into an entrepreneurial family, Terence Chan (@the_impetus), owner, Impetus Plumbing and Heating LTD, Vancouver, British Columbia, Canada, practices networking and customer service daily to grow his business. But it didn’t come easy, at first. With a goal of becoming Read more
Uncategorized
The son of an arcade owner, you could say that business ran in his blood. Born into an entrepreneurial family, Terence Chan (@the_impetus), owner, Impetus Plumbing and Heating LTD, Vancouver, British Columbia, Canada, practices networking and customer service daily to grow his business.
But it didn’t come easy, at first. With a goal of becoming an engineer, Chan found himself in the “slumps,” after dropping out of the local university. “I didn’t know what I wanted to do and my parents told me to try plumbing,” says Chan. “Instead of just playing video games all day and waiting for something to happen, I decided to take on that challenge and try working with my hands,” says Chan.
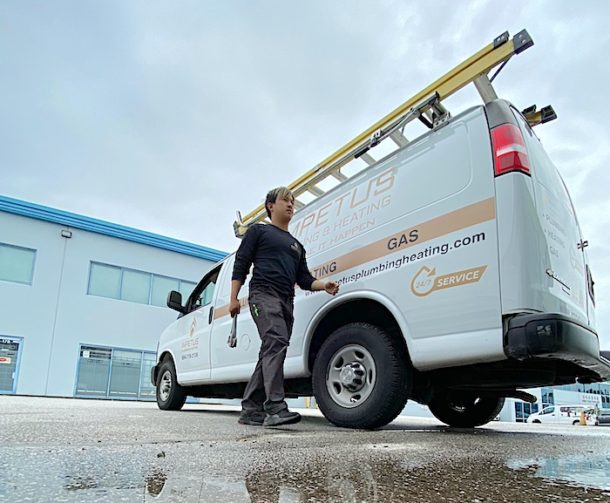
Chan ended up really liking the trade—more so because he found out how plumbing and heating is so important in everyone’s day-to-day lives—and he was adamant about being the best out there, and his sights were set on owning his own business one day. “My goal was to get all types of experience before I start my business; commercial, residential, construction, service and sales,” say Chan.
In fact, Chan worked in commercial construction, working on high rises, schools and low rises. He then moved over to a sales position learning how to sell, diagnose boilers/heating issues, inside/outside sales and customer relations. From there, Chan moved over to a service company that did commercial service for restaurants and multi-complex buildings. After a stint doing residential construction for custom homes, Chan had the final experience of working for a full-service company doing residential/commercial service to finish his plan of starting a business with the experience he had built.
“Basically, I was able to change jobs each year to get the experience that I needed. Fast forward to this day, I have my own business, freedom, and I challenge myself to change the trade daily,” says Chan.
Six years later and Impetus is a leader in Vancouver area, receiving multiple awards for plumbing and customer service. “Even through all the years, the biggest thing I’d say in running a successful business is customer service. I may not know everything, but I sure as hell know what it takes to provide good service. Service goes a long way—learn and master it!” says Chan.
The Next Generation
According to Chan, the industry should invest more in marketing to the next generation. The industry should continue to create scholarships, giveaways, recognition, anything captivating for plumbing so that younger generations can see it as a feasible career path. “It needs to provide more interest to the next generation so that they want to come into the trade. For the longest time, everyone believes the trade to be butt cracks and the uneducated. That was not true back then nor is it true now, especially now,” says Chan. “There is so much technology and so much change that we need younger people to work on the equipment. Everything can be connected to a phone, everything is automated. So much has changed, a plumbing job is almost like an IT job,” says Chan.
As for taking on the role of being a role model? “100%. I try to be the role model to show them that someone young can make the difference—showing everyone that if someone young can do this, so can they. I want to show that trades can be fun and rewards in all aspects,” says Chan.
And how about attracting more diversity to the trades? “Social marketing would be my answer. The more we get everyone on there and flood the world with plumbing content, the more people will eventually see it. Quantity is key in my opinion,” says Chan.
As for social media, “it has opened an unimaginable number of new doors for me,” says Chan. “From new friends, to learning, to connecting, to networking and to sponsorships, all of that came from the power of social media. It has been an amazing ride and I believe it has just started, there is a lot more to come and a lot more to share,” says Chan.
In fact, Chan says that the closest thing to a mentor would be Instagram. “On the platform, I’ve met so many awesome people and learned so much from others just by watching and observing—accounts like Mechanical Hub, my BC plumbers, people from overseas, there are just so many to mention,” says Chan.
Getting Personal
If you’ve followed Chan on Instagram lately (@the_impetus), you’ll know that a lot of his work gets done in the bathroom—not just plumbing. “Don’t ask for more information than that,” says Chan.
A lot of that has to do with work on the phone. “I carry two phones with me, one company and one personal. But both of them impact my day to day hugely. People would think, ‘well isn’t he a plumber: what about wrenches and other things?’ Of course, I have all that stuff and use that from day to day, but I’m more of a business guy,” says Chan.
Chan’s personal phone is for taking videos, answering emails, answering calls from his guys to troubleshoot and editing videos. His other work phone is for taking calls, forwarding calls, taking videos, tracking jobs through his Jobber app, and also acts as an extra battery, in case the other phone dies.
“Without my phones, I wouldn’t be able to operate my business at all, as I start moving up and doing less plumbing work, managing a business becomes crucial. Communication becomes key,” says Chan.
And let’s not forget about his computer. That’s where the quotes happen, that’s where the approvals happen, that’s where the networking happens and that’s where the learning comes from.”
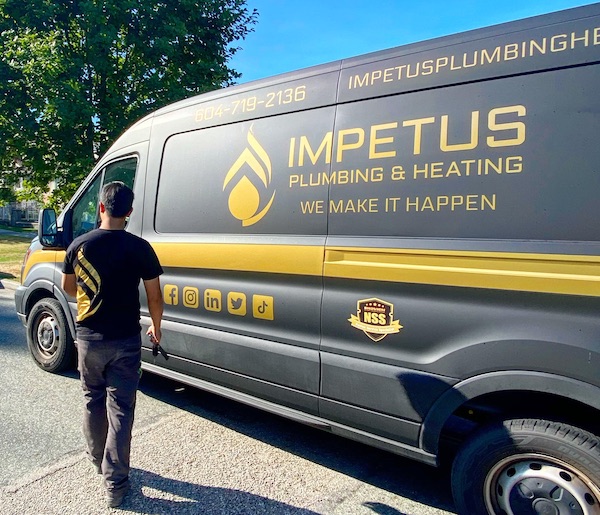
As far as balancing his work with leisure? “I don’t. I let them balance out themselves. I do what makes me happy on a daily basis. It sounds greedy and selfish but my true belief is that you can only make people around you happy by being happy yourself,” says Chan.
But there is some personal time mixed in, and that includes golf, lots of golf. In addition, Chan enjoys hanging out with his friends and his team, going out to eat new food at new places he’s never been before, and shopping for tools or golf stuff. “But all of it revolves around work,” says Chan.
Full Circle
It always comes back to customer service, however. “The most rewarding thing about my job is being able to help a customer with their issue. It always feels like I’m a hero and that I actually made a difference in someone’s life. It’s so rewarding to have a happy customer knowing that you solved something essential in their life while getting paid. It doesn’t get any better!” says Chan.
In the end it’s about being satisfied with yourself and your work. “If I were to enter a business or a job that I don’t like. I wouldn’t be doing it. I’m all about being happy with everything I do. Unluckily, having my own business, I have to do everything so I don’t bother hating or not liking anything because I love what I do every day,” says Chan.
AHR Expo Announces Open Call for the 2022 Innovation Awards; Entries Accepted through August 3, 2021
The AHR Expo (International Air-Conditioning, Heating, Refrigerating Exposition) 2022 Innovation Awards call for entries is now open. The annual competition, held in conjunction with the Show, honors the most innovative and original products, systems and technologies in HVACR. Exhibitors are encouraged to submit new or upgraded products to compete. Entries will be accepted through August Read more
The AHR Expo (International Air-Conditioning, Heating, Refrigerating Exposition) 2022 Innovation Awards call for entries is now open. The annual competition, held in conjunction with the Show, honors the most innovative and original products, systems and technologies in HVACR. Exhibitors are encouraged to submit new or upgraded products to compete. Entries will be accepted through August 3, 2021. The 2022 AHR Expo will be hosted at the Las Vegas Convention Center in Las Vegas, NV January 31 through February 2, 2022. To request more information about the Innovation Awards, or to receive forms for entry, please email Kim Pires at kpires@iecshows.com.
“First and foremost, we are thrilled to gather again in Las Vegas for the 2022 AHR Expo. Despite not coming together in 2021, we celebrated ten outstanding category winners and the Product of the Year, Infinitum Electric’s IEq,” said Mark Stevens, Manager of AHR Expo. “This competition celebrates the HVACR industry’s most innovative solutions through leadership in design, construction and execution. Each year we look forward to seeing the advancements in HVACR through the snapshot that the Innovation Awards provides. It is an excellent indicator of the exciting Show ahead.”
In 2003 the AHR Expo debuted the Innovation Awards as a means to highlight those in the HVACR industry creating innovative solutions for new and existing challenges and new avenues for growth. They aim to honor the most inventive, useful and original products, systems and technologies pushing boundaries and disrupting the market today.
Entries are evaluated by a panel of third-party ASHRAE members with over 20 years of professional engineering experience. The review process includes points tallied based on application, innovation, value and market impact. Winners are selected from ten industry categories, including: building automation; cooling; heating; indoor air quality; plumbing; refrigeration; software; sustainable solutions (formerly green building); tools and instruments; and ventilation. Winners and finalists demonstrating superior innovative design, creativity, application and performance will be recognized at the 2022 Show, on the AHR Expo website and social media channels, as well as in industry media coverage leading up to the Show.
An overall Product of the Year will be selected from the pool of category winners and will be announced at the Show. This prestigious honor is awarded based on exceptional leadership in HVACR innovation.
Eligibility and general information about the 2022 Innovation Awards
- The competition is open to exhibitors with a confirmed space contract, as well as a deposit payment on file for the 2022 AHR Expo.
- Eligible products include those that will be exhibited at the 2022 AHR Expo in Las Vegas and must be available for sale by January 2022.
- Exhibitors are permitted to submit one product per category.
- Product entries are limited to one product category.
- Products that have previously won an AHR Expo Innovation Award are not eligible, however, those products that have previously been named a category finalist may be re-entered.
- Completed entry forms, along with a non-refundable $100 entry fee, must be submitted by Tuesday, August, 3, 2021.
- One winner from each category will be selected. An overall Product of the Year award is selected from all category winners and announced at the 2022 Show.
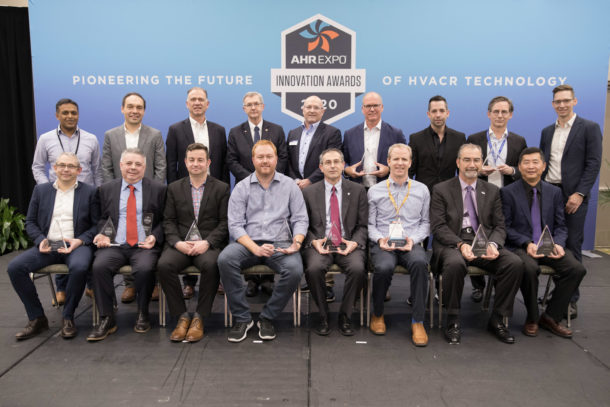
Entry fees for the 2022 Innovation Awards (approximately $20,000) will be donated to a charitable organization serving the local Las Vegas area community. The donation is generally used to provide HVACR repairs or upgrades. Each year, the AHR Expo works to select a charitable organization within the area where the Show is held.
“This past year has been a catalyst for new ways of thinking and adapting,” continued Stevens. “Our industry has risen to the challenge and provided critical solutions to help us move forward. HVACR is an area of exciting innovation on the global stage and we can’t wait to see what awaits us on the Show floor in Las Vegas.”
Registration for the 2022 AHR Expo is expected to open in July of 2021. Visit the AHR Expo website for updates and to sign up for the Show newsletter.
ABOUT THE AHR EXPO
The AHR Expo is the world’s premier HVACR event, attracting the most comprehensive gathering of industry professionals from around the globe each year. The Show provides a unique forum where manufacturers of all sizes and specialties, whether a major industry brand or innovative start-up, can come together to share ideas and showcase the future of HVACR technology under one roof. Since 1930, the AHR Expo has remained the industry’s best place for OEMs, engineers, contractors, facility operators, architects, educators and other industry professionals to explore the latest trends and applications and to cultivate mutually beneficial business relationships. The next Show, co-sponsored by ASHRAE and AHRI, will be held Jan. 31 – Feb. 2, 2022 in Las Vegas, and is held concurrently with ASHRAE’s Winter Conference.
For more information, visit ahrexpo.com and follow @ahrexpo on Twitter and Instagram.
When I asked Sean Debnath, VP of Sales and Marketing, Viega, about the short-term economy earlier this year, he said, “The uptick in business that we all experienced gradually through Q3 and Q4 of 2020, seems to be continuing in to Q1 2021. But we choose not to take that trend for granted with all Read more
When I asked Sean Debnath, VP of Sales and Marketing, Viega, about the short-term economy earlier this year, he said, “The uptick in business that we all experienced gradually through Q3 and Q4 of 2020, seems to be continuing in to Q1 2021. But we choose not to take that trend for granted with all that is happening around us, and deal with it a month and a quarter at a time. Viega has taken steps with frequent testing and tracing to ensure we keep our factories and distribution centers running.”
Through all of this uncertainty and one month-at-a-time mentality, making the transition to new a new CEO can be difficult enough. But through a pandemic? Mechanical Hub recently talked with Viega’s new CEO, Markus Brettschneider, about his vision for the company, and navigating through these uncertain times.
MH: How has Viega navigated through the pandemic and what does the path moving forward look like as we start to normalize?
Brettschneider: Since the beginning of the pandemic, the health and safety of our people has come first. We put into place regular testing and safety measures at the facilities where in-person work was required. Moving forward, health and safety will continue to be our focus. Our other big focus is our customers, and we have done all we can to keep production and distribution as normal as possible. With all of the challenges in the logistical side, it’s a tense period. But we haven’t shied away from spending money to keep things running smoothly. We hope in the coming months to get colleagues back to the office and find new ways of working in various setups. We very much look forward to meeting our customers once again face-to-face, while at the same time being very careful and keeping everyone safe. So far this year, the outlook is positive.
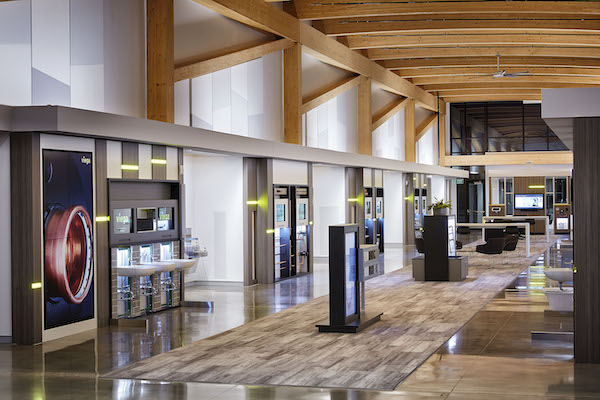
Viega’s interactive displays in Broomfield, Colo.
MH: Has the company learned anything during the pandemic that will be implemented more into the business plan (virtual trainings, less travel, etc.)
Brettschneider: I think we have learned that virtually, a lot is possible. There are even certain benefits when it comes to training as well as new ways of engaging with customers. It will be interesting to see how things like trade shows and other events evolve in the future, but in 2020 we reallocated most of those funds into other channels to make the most of what we could. We didn’t cut any funding. Instead, we trained our own people to be capable in this digital environment, and have excelled with virtual education and customer events. We know there have been changes in buying behavior in the past year, and we remain open to this ever-changing business landscape.
MH: What are some of your top initiatives for the company?
Brettschneider: Our biggest priorities right now are safety and supply to the customers. We’re looking at things like raw materials, logistics and the availability of workforce. We are continuously investing in our company footprint through automation, digitization and robotization. This is all important to help drive growth with our customers. We also know how important it is to invest in virtual and online marketing, as well as launch additional customer training activities.
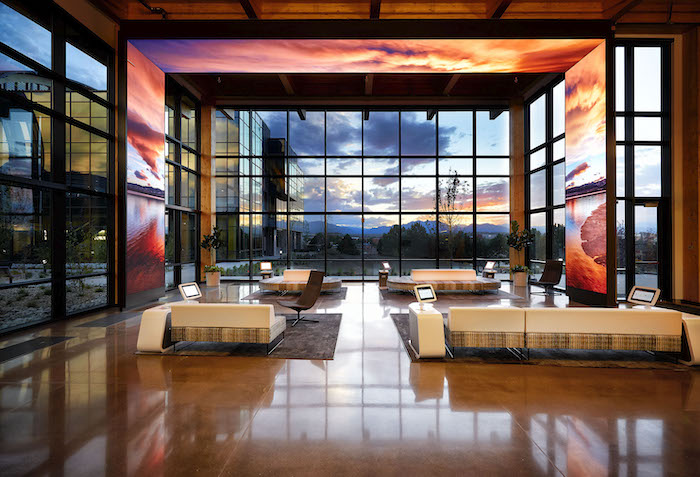
Viega’s Seminar Center in Broomfield, Colo., comes with a view.
MH: What has impressed you the most since joining the company? Brettschneider: The people—our colleagues, the customers and the Viega family ownership. I’m extremely impressed with the products as well as the relationship we have with our customers and the opportunity to grow in our space. I’m also impressed with the commitment of the Viegener family to the company globally as well as its strong commitment to Viega LLC (the North American market) specifically. I’ve found the company is willing to constantly invest in order to grow the business, and the ownership’s passion and commitment is impressive.
MH: Explain Viega’s commitment to the supply chain and wholesale channels.
Brettschneider: We have proven our commitment to the supply chain, especially over the last few years . During that time, we grew the manufacturing and distribution presence in McPherson, Kansas, and we invested heavily in the workforce within the supply chain. We hired additional people to ensure our commitment in the U.S. is as strong as it always has been, and will continue. It’s important for us to invest for continual growth, and we know that our distribution and logistical centers are a key part of the business.
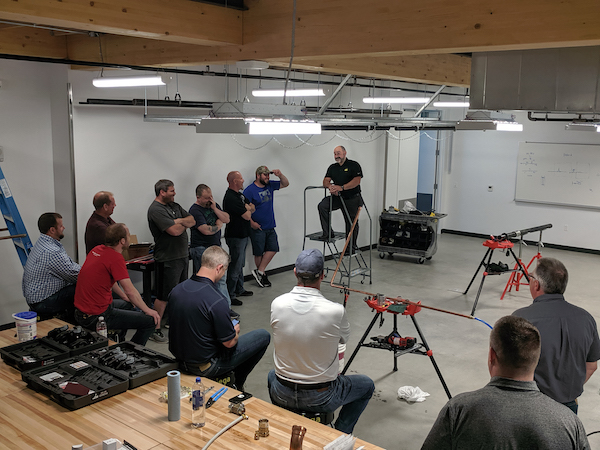
Training is paramount with Viega, and getting contractors back into the facilities, safely, is the goal.
A good example of our commitment was after the record cold snap in Texas and other southern states. We prioritized shipments and looked at unique ways to get products to the area that was so desperately in need of help. We are eager to work with our partners to drive growth, and are currently adding points of distribution throughout the U.S. We are a strong believer in wholesaler business and remain absolutely committed to our wholesaler distribution setup.
MH: What are some things you’ve learned throughout your career that will help you in your new position?
Brettschneider: Simply put, there is nothing more important than your own people and building great relationships with customers. Those ideas are central to a successful business.
MH: How do you see the short-term economy?
Brettschneider: Between the Covid relief package, some of the American population having more disposable income than ever, lower fixed-interest rates and potential infrastructure packages, we’re optimistic. We’ll see bumps here and there, I’m sure, because of the uncertainty of a global pandemic, but the fast-pace rollout of the Covid vaccination is giving us all a more positive outlook for the short-term U.S. economy.
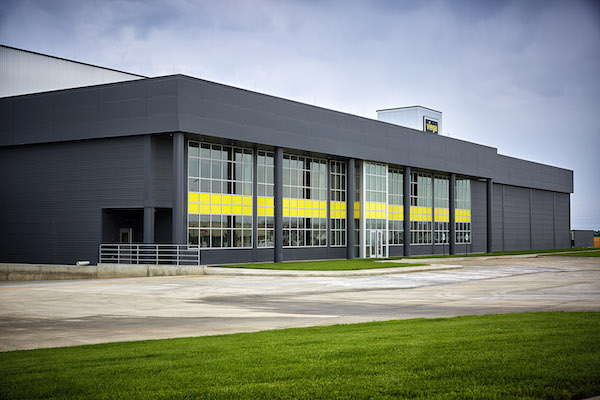
A McPherson, Kansas, facility.
MH: Provide an update of the McPherson locations — expansions, new innovations, etc.
Brettschneider: We have invested heavily in that location over the past few years, in both infrastructure and people. This year we are focused mostly on hiring people. It’s important to recognize we are investing not to just maintain, but to grow. Our plan has been to build for significant growth so that we are ready when there are sudden spikes in demand (such as the Texas cold snap). In terms of infrastructure, the expansion in logistics was completed early in 2020 and is fully operational. The new ProPress building is completed, with some machines in operation, while others will be arriving later this year (delayed due to Covid).
And now, starting for the Los Angeles Lakers, a 5’ 10” forward from South Pasadena, Krikor Chiranian! [cheers and a loud applause ring throughout the Forum.] “Hey, as a young boy I loved basketball and my dream was to play professionally in the NBA,” says Krikor. But with most young kids dreaming of becoming a Read more
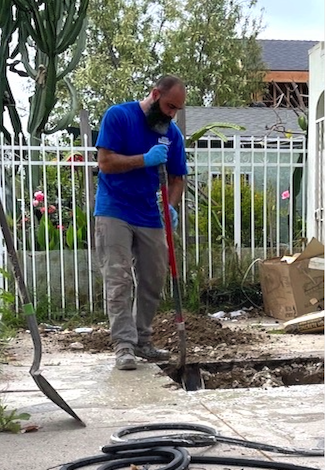
Koko working hard on the jobsite.
And now, starting for the Los Angeles Lakers, a 5’ 10” forward from South Pasadena, Krikor Chiranian! [cheers and a loud applause ring throughout the Forum.] “Hey, as a young boy I loved basketball and my dream was to play professionally in the NBA,” says Krikor.
But with most young kids dreaming of becoming a professional athlete, reality sets in at some point, and fortunately for Koko, he got a taste of the trades early on, and there was no looking back.
Fun Fact: How do most of you know Krikor as Koko? Koko Drains (@koko.drains) was named after Krikor’s nickname. “My given name is Krikor, and since I can remember, my family would only call me Koko. In my career in drain cleaning, everyone has always known me as, and called me by, Koko. So, it really stuck with me,” says Koko.
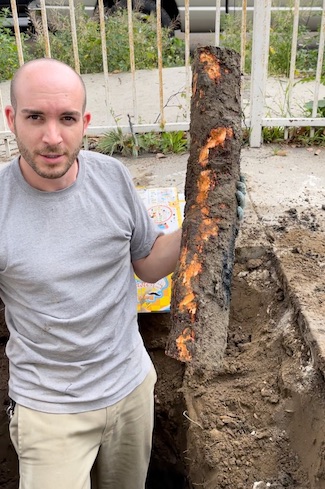
One of Koko’s techs finds a treasure.
Starting in the trades at the age of 20, Koko went on a call for a kitchen sink drain stoppage with his father, a veteran of the plumbing trade for nearly 50 years. “My father had to call on a man named Ole Bugarin to clear the drain stoppage. Ole came out with his Gorlitz Go 50 1/2” cable and cleaned the kitchen drain from the clean out, and I looked at my dad and said, ‘That’s what I want to do.’ There was just something about that moment while watching Ole clear the drain. It opened my eyes to a new part of plumbing that I found appealing and satisfying. I asked Ole if he would hire and teach me, and he did,” says Koko.
Koko worked for a single company for 11 years specializing in drain and sewer cleaning, and became adept to the work very quickly. “With the experience gained my confidence grew.” Says Koko. “One thing led to another, and I was eventually able to go on my own at age 31. As time passed, we became busier, leading to the hiring of my wife and two technicians. I’ve been self-employed for eight years now with plans for continued growth.”
Now, owner of Koko Drains, South Pasadena, Calif., Krikor Chiranian has been self-employed for the past eight years running a successful drain and sewer cleaning business with a side of waste drainage repair and replacement. In addition, Koko also provides camera inspections with marked pipe location, repairs and cleans of drains or sewer pipes by way of cabling and hydro jetting, as well as toilet and garbage disposal installations. As mentioned, Koko also repairs or replaces waste drainage piping, clean-out installation, pipe descaling, as well as trenchless rehabilitation services, and more. His go-to tool is his sewer inspection camera. “The camera tells all within an underground drain pipe, allowing proper diagnosis,” says Koko. Another daily go-to tool is Koko’s hydro jetter, which allows Koko to move a blockage out of a pipe, and, at the same time, cleans the drain or sewer pipe.”
While Ole was instrumental in mentoring Koko early in his career in drain cleaning and other plumbing essentials “teaching him everything he knows,” does Koko himself consider himself a role model for the younger generation entering the trades?
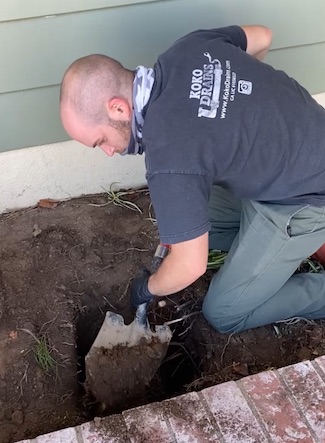
Diggin’ in the dirt, working hard and gettin’ it done.
“Absolutely,” says Koko. “We pave the way for future generations. People are influenced mostly by not only what they see, but also by what they hear. To have a successful plan, it’s very important to stop and think before we act—teaching the younger generations the way to honestly and properly accomplish tasks is critical.”
According to Koko, the industry could do a better job promoting more women or minority contractors in the trades, “allowing for the attraction and eventual growth of a more diversified workforce, especially in leadership positions,” says Koko.
Being self-employed and the owner of a business makes it a bit easier to balance work/family time. “My wife schedules our work and personal life events; therefore, my wife schedules time off for me to spend with my family,” says Koko.
The free time is spending time with family, listening to and reading self-development audiobooks/books, and thinking of new ways to improve and grow the business. And, there’s social media. “Social media has allowed us to share our knowledge with others, and we can learn new ways of doing a job through other tradespeople’s perspective,” says Koko. “With social media, the new tools and equipment that are available to contractors are displayed, and they have brought new ideas for our company to utilize and grow. Also, we have made many new friends and customers through social media, building a network of reliable and respectable people.”
In the end, what does Koko love most about his job? “The gratitude our customers show us for getting the job done is the most rewarding. Also, the ability to be in the field, seeing new faces and places. In the trade, we are always seeing and learning something new.”
Lindon, Utah — Aquatherm announced that it has added Southern Pipe & Supply as a distribution partner. Founded in 1901, Southern Pipe & Supply is one of the largest privately held, independent distributors of brand-name plumbing, HVAC, industrial, mechanical, and water works supplies in the Southeast, with more than 100 locations in Mississippi, Alabama, Louisiana, Georgia Read more
Lindon, Utah — Aquatherm announced that it has added Southern Pipe & Supply as a distribution partner.
Founded in 1901, Southern Pipe & Supply is one of the largest privately held, independent distributors of brand-name plumbing, HVAC, industrial, mechanical, and water works supplies in the Southeast, with more than 100 locations in Mississippi, Alabama, Louisiana, Georgia, Arkansas, Florida, and Tennessee.
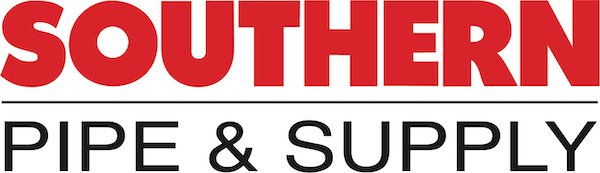
“Southern Pipe has always aligned themselves with the brand leaders in the marketplace,” said William Jolly, Director of Purchasing – Southern Pipe & Supply. “We are honored to partner with Aquatherm, the leader in polypropylene piping systems.”
Glen Miller, Vice President of Sales, Aquatherm North America, said the company has been strategically adding distribution to support its contractor customers.
“Southern Pipe & Supply is a perfect fit with Aquatherm’s Culture of Excellence,” Miller said. “We are excited to have them as a distributor partner.”