The Plastics Pipe Institute, Inc. (PPI) announced today that its Building & Construction Division (BCD) has elected Bill Melvin of Legend Valve (Auburn Hills, MI) as Division Chair and Jim Paschal of Aquatherm (Lindon, UT) as Vice Chair. Melvin, who will also represent the division on the PPI Board of Directors for the next two Read more
Aquatherm
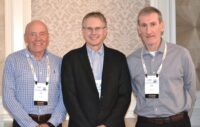
The Plastics Pipe Institute, Inc. (PPI) announced today that its Building & Construction Division (BCD) has elected Bill Melvin of Legend Valve (Auburn Hills, MI) as Division Chair and Jim Paschal of Aquatherm (Lindon, UT) as Vice Chair. Melvin, who will also represent the division on the PPI Board of Directors for the next two years, takes over from Joseph Poniatowski of Asahi/America. The changes took effect June 1, 2024. PPI’s BCD focuses on pressure piping materials for plumbing and mechanical applications.

Jim Paschal (left) of Aquatherm, new Vice Chair and Bill Melvin (right) of Legend Valve new Chair of PPI’s Building & Construction Division with Lance McNevin, the engineering director for the division.
Bill Melvin has served on the Management Committee in several roles, including the Communications Committee Chair and Vice Chair. Jim Paschal also serves as Chair of PPI’s Polypropylene Pressure Pipe Steering Committee and formerly served as R&D Projects Chair. That position will now be filled by Rick Stock of Uponor. Brian Conner of Charlotte Pipe and Foundry joins the committee as Codes & Governments Affairs Committee Liaison.

Rick Stock, Uponor
Adam Grier of iNOEX serves as the Communications Committee Chair, and also as Chair of the PPI Umbrella Marketing Committee. Jason McKinnon of Viega LLC serves as the PPI Education Committee Chair and also as the BCD Education Chair, a position he has held for more than eight years. Forest Hampton III of Lubrizol continues as Advisory Council Liaison & Strategic Planning Chair.
According to Lance MacNevin, P. Eng., director of engineering for PPI’s Building & Construction Division, “PPI’s management committee members provide significant guidance to staff on topics from research, codes and standards to education and advocacy. These new leadership positions solidify their continued commitments to PPI and the piping industry. We are grateful for the volunteer service of these dedicated members.”
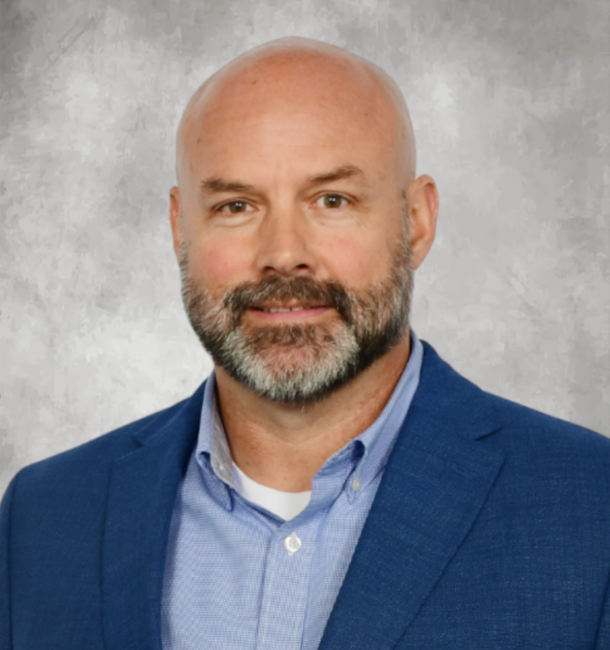
Brian Conner, Charlotte Pipe and Foundry
PPI is the major North American trade association representing the plastic pipe industry. The Building & Construction Division represents plastic pressure piping materials such as CPVC, HDPE, PEX, PE-RT, PP-R, and PP-RCT.
More information can be found at https://plasticpipe.org/buildingconstruction
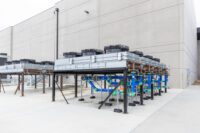
Businesses that entrust their data storage to the state-of-the art Novva data center outside of Salt Lake City will benefit from a location chosen for its many data center-friendly attributes. The area offers outstanding connectivity, low power costs, and a central-western site with easy access to a major international airport. In addition, the site’s climate Read more
Businesses that entrust their data storage to the state-of-the art Novva data center outside of Salt Lake City will benefit from a location chosen for its many data center-friendly attributes. The area offers outstanding connectivity, low power costs, and a central-western site with easy access to a major international airport. In addition, the site’s climate and 5,000-ft. altitude allow for many hours of free cooling annually.
Just as important to Novva’s clients, the new data center has a low disaster risk. The area is not prone to earthquakes, floods, or adverse weather events such as hurricanes.

And finally, for the additional peace-of-mind that makes this data center truly start-of-the-art, the cooling system for the computer servers boasts Aquatherm PP-RCT piping that will provide virtually leak-free service for decades to come. The Aquatherm piping will never scale or corrode, and the cooling water flow will remain unchanged throughout the anticipated 50-year lifespan of the pipe. All of this data adds up to a win for Novva and its clients.
The “hyperscale” data center in Salt Lake City will be Novva’s flagship data center. The 100-acre Utah campus is planned to ultimately include more than 1.5 million square feet of data center space and will accommodate 250kW to 30 MW clients. The construction is taking place in four phases. The first phase, which includes a 300,000-sq.-ft. data center, a 120MW substation and an 80,000-sq.-ft. headquarters office building for Novva, was completed in December 2021.
Beating the Heat
Reliable cooling systems are an essential component of modern data centers. Computer servers are notorious for generating heat—and heat is notorious for being an enemy of computer servers.
The decision to install Aquatherm pipe as part of the new data center’s cooling system was driven by Steven Boyce, vice-president of infrastructure and design at Novva Data Centers. Boyce has been involved in the IT and data center space for more than 20 years, and has worked on multiple successful startups during that time.
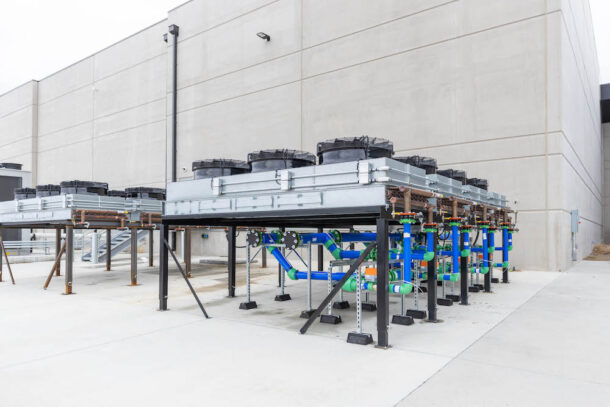
When I first learned about Aquatherm, it was a no-brainer,” Boyce said. “I had been using steel pipes in my builds, which would corrode and rust, and in turn, fill my equipment with sediment and pieces of rust. Efficiencies would be diminished, and the pipes would eventually have to be replaced. Aquatherm’s total installed costs are lower, and their warranty is something that no steel vendor could match.”
Once the decision was made to trust the cooling system’s performance to Aquatherm pipe, Novva turned to the Salt Lake City branch of Harris Mechanical for the installation.
Harris had experience installing Aquatherm pipe, although the Novva data center represented the company’s largest data center Aquatherm installation to date. To handle the first phase of the Novva system, Harris installed a BASX custom chiller package (which included the pumps and controls), the Aquatherm pipe for computer system cooling, and the comfort system piping and plumbing. The piping work for phase 1 began in mid-May 2021 and was completed in October 2021. The system was commissioned and turned over to the owner in December 2021.
Fast and Furious
Jeff Reading, operations manager, construction, Harris Mechanical, explained that the Novva data center started out as a core and shell project, with the office built first and the data hall scheduled to be built out later. However, as anyone in construction work knows, it’s always best to expect the unexpected.
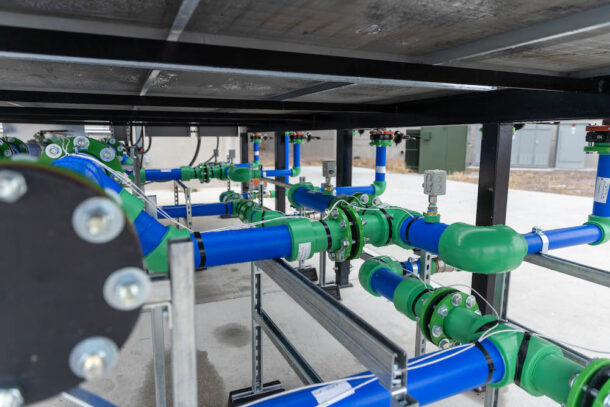
“We finished the core and shell construction in May 2021, and the data hall was right on its heels as a change order to the original project. So it came at us fast and furious,” Reading said. “The original plan was to complete the entire chilled water loop, which runs underneath the floor on both sides of the building. However, it was decided to install the piping in stages as the facility is built out. So far we have installed about half of the piping that will ultimately go in there.”
The installation to date has included 4,418 ft of Aquatherm Blue Pipe SDR 17.6. The main system piping is 10-in., and the takeoffs are 4-in.
Training Professionals
To handle such a large project. Harris Mechanical sent several installers to Aquatherm’s U.S. headquarters in nearby Lindon, UT, for training.
Having Aquatherm-trained technicians opens up new opportunities for HVAC and plumbing companies. The company gains differentiation in the market, and enjoys the time- and labor-savings associated with installing polypropylene pipe.
Aquatherm training is the most intensive, comprehensive training in the polypropylene piping industry. Attendees receive both classroom training and hands-on training with multiple fusion machines, and must pass a rigorous test using all the fusion tools correctly.
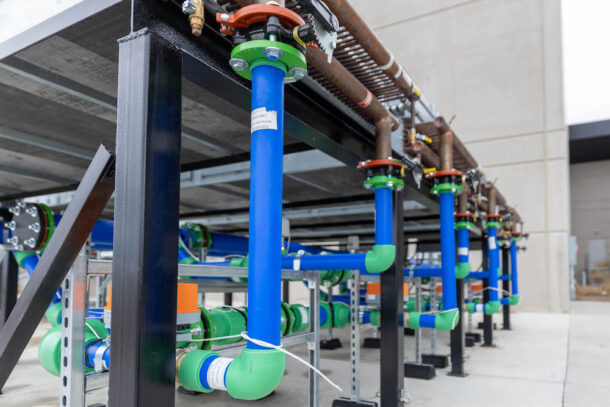
After the training, Harris completed the installation using McElroy fusion tools and a combination of socket fusion for the 4-in. pipe and butt fusion for the 10-in. pipe. The system runs at a low pressure (35 to 45 psi); the cooling system supply water runs at 55°F and returns to the chiller at about 60°F.
According to Reading, Harris Mechanical had a good experience with Aquatherm piping at the Novva data center, and the ease of installation compared to steel pipe helped Harris stay ahead of the project’s tight schedule.
“It was a smooth process,” he said. “We definitely gained experience and confidence with the pipe throughout the project, and our installers became accustomed to ‘leapfrogging’ and working with more than one [fusion] machine at a time.”
A Smooth Path
The underfloor piping system presented one of the major installation challenges at this project. The floor is raised 5-ft., and all of the facility’s piping, wiring, HVAC ducting, and utilities run through the raised space.
Aquatherm’s building information modeling (BIM) capabilities and Scan-to-Fab service helped ensure that the installation went smoothly by preventing underfloor conflicts and collisions.
“Using 3D BIM and Revit really helped with coordinating this installation,” said Autumn Turner, a fabrication drafter at Aquatherm. “Not only was all the HVAC and plumbing under the floor, there were floor stands every square foot. It took a lot of coordination to avoid all those potential obstacles.”
Turner noted that careful coordination enhanced the already-fast heat-fusion installation of Aquatherm pipe, and that less time and money spent on welders is a major benefit of choosing Aquatherm.
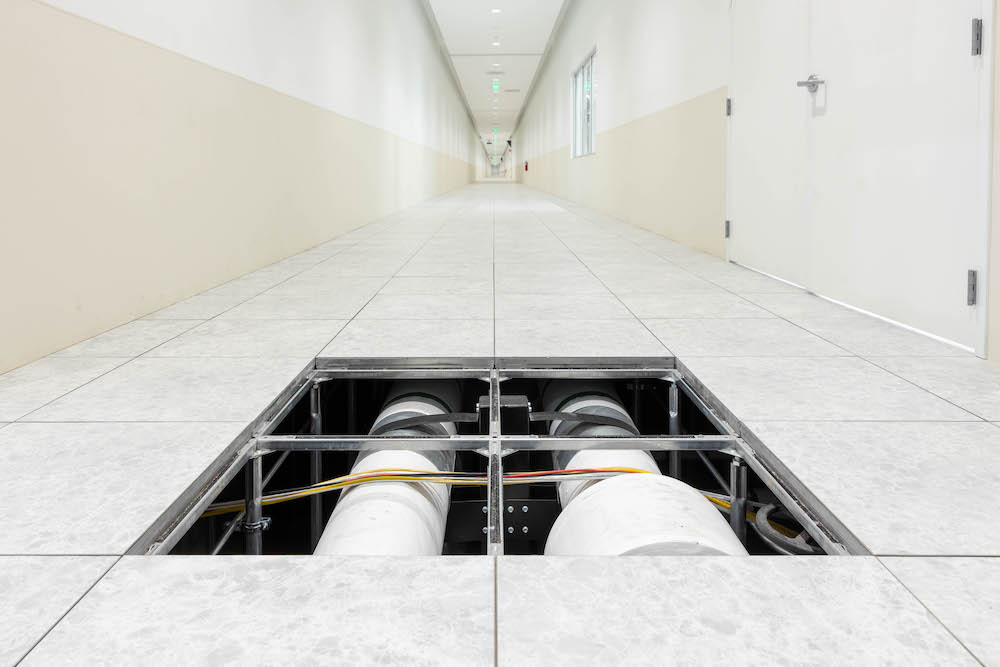
“Aquatherm is just easier work with than steel pipe,” she said. “It takes a lot less time to weld, and when you add in the BIM support and drafting it was easier for the installers to get situated into the floor and navigate the space.”
Turner added that Aquatherm’s BIM and Revit capabilities will ensure the future installation phases of the massive project also go smoothly.
Rhett Coles, Aquatherm’s fabrication drafting/scan-to-fab manager, said that Aquatherm’s Scan-to-Fab service and in-house fabrication makes any piping installation easier and smoother. Spools can be custom made in any size or configuration and shipped to the jobsite ready to install. In addition, any pieces fabricated by Aquatherm are covered by a comprehensive 10-year warranty.
“In the case of the Novva data center, we were in constant communication with Steven Boyce and the owner’s group,” Coles said. “We were not providing a cookie cutter system to them. They would tell us whatever they wanted or needed and we would work directly with them to help them fully accomplish their goals.”
A reliable, leak-free piping system with a long life span, and a smooth installation in any space, including challenging underfloor designs? The data are in: Aquatherm is the right choice for data centers.
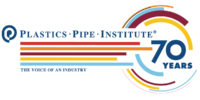
The Plastics Pipe Institute, Inc. (PPI) is celebrating its 70th year. Formed in 1950 as the Thermoplastic Pipe Division of the Society of the Plastics Industry (SPI), PPI is now the leading North American trade association representing all segments of the plastic pipe industry, and is known for its research, its work to develop industry Read more
The Plastics Pipe Institute, Inc. (PPI) is celebrating its 70th year. Formed in 1950 as the Thermoplastic Pipe Division of the Society of the Plastics Industry (SPI), PPI is now the leading North American trade association representing all segments of the plastic pipe industry, and is known for its research, its work to develop industry standards and codes, advocacy and education.
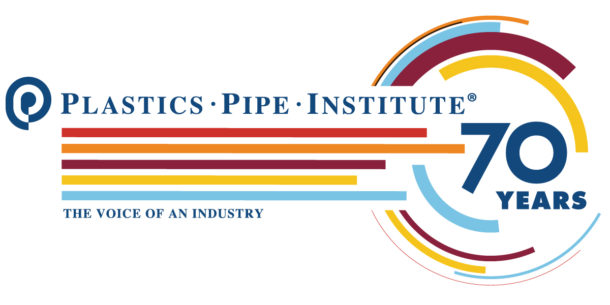
“Since the very beginning, PPI has provided the vision and the leadership that has produced the establishment of uniform test and design criteria that became the foundation for all current applications of plastics piping,” stated PPI President David Fink.
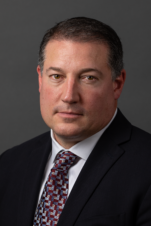
PPI President David Fink
“PPI created the methodology for rating the long-term strength of pipe materials plus the concepts of pipe pressure rating, the establishment of standard dimensional ratios and the adoption of numbers to state those properties. Our association staff and members also engineered the first code acceptances for plumbing, industrial, commercial and gas distribution applications for plastics piping, and provided the first industry-wide statistics. Today, that work continues and includes telecommunications conduit, corrugated drainage pipe, along with pipe used in potable water, forced main sanitary sewer systems and building and construction projects.”
In 1950, when the group was first formed as the Plastic Pipe Manufacturers Association, plastic pipe was still in its infancy, having been developed during World War II as a way to insulate radar cables. Solid-wall high-density polyethylene (HDPE) pipe began replacing metal pipe in oil- and gas-gathering systems in the late 1950s. In the early 1960s, gas utilities started replacing failing iron pipe with polyethylene (PE) pipe, and because of its successful performance history, 95 percent of all new gas distribution systems installed today use PE pipe. A few years later, corrugated HDPE pipe started to replace clay pipe in agricultural drainage systems. In the late 1980s, large-diameter corrugated HDPE pipe began to replace metal and concrete in storm water culverts. The material has continued to evolve into what is now its third and fourth generation of development, each with improved performance capabilities.
“PPI has always been ‘member-run, member-led,” Fink stated. “The continuing success and growth of our association is a direct result of the enthusiastic work by those members. One indication of how our members view their association can be determined by the many people who have participated for several decades.”
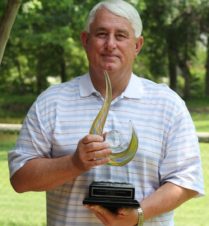
Jim Craig, PPI Lifetime Achievement Award Recipient
Frequently, PPI presents its Lifetime Achievement Award to a member who provided exceptional devotion and dedication to the industry. Jim Craig was honored in 2013 for his 40 years of service to the industry and said, “I am proud to be a lifetime member of PPI. It is a great organization with a super staff to help the members accomplish great gains in the plastic pipe markets. I joined PPI in the 1980s, while working for McElroy Manufacturing in Tulsa, OK. I quickly learned that this organization was great at getting people and organizations together to grow the PE industry in general. We had pipe manufacturers, resin manufacturers, fitting manufacturers, joining manufacturers and distribution organizations take on projects, do testing, and develop technical notes and reports with everyone working together to accomplish our goals.”
“Unfortunately, Jim passed away soon after providing his thoughts about PPI,” explained Fink. “His contributions and devotion to PPI and the industry is his legacy that will always benefit others.”
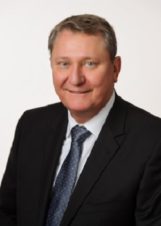
George Zagorski, PPI Lifetime Member
Another Lifetime Member, George Zagorski, now retired from Blue Diamond Industries (Lexington, KY), offered, “I was a somewhat “reluctant” young volunteer when Blue Diamond first joined PPI some 15 years ago. What I discovered was like-minded professionals, who would debate and cooperate for the betterment of the overall plastic piping industry. Along the way, my voice was always heard and considered. In the end, I’ve developed not only professional relationships, but lifelong friendships.” Zagorski also served on the PPI Board of Directors from 2011 to 2017 as vice chair, chair and past chair plus numerous other committees and task groups.
In 1963, Phillips Petroleum, the company that brought a new manufacturing process to the industry for making HDPE and discovered how to make polypropylene 1951, now another popular pipe resin, and in 1963 established its pipe division, Driscopipe, which is now known as Performance Pipe. Harvey Svetlik, another long-time PPI member who started his career with Phillips Driscopipe and recently retired from PPI-member company Georg Fischer Central Plastics LLC, said, “PPI is the leader in the polyolefin pipe industry specifically and in the plastic pipe industry generally. PPI is not so much about what it has accomplished in the past, as it is about our polyethylene brotherhood and our commitment to future accomplishment.
“We have watched the industry grow from using 80 million pounds in 1980 to almost a couple of billion pounds annually for all its applications and all its pipe types. The next 40 years will witness a doubling yet again, as polyethylene pipes and fittings take their place as a dominant leak-free system in the drinking water sector. The North American population will double in this timeframe, creating the demand, along with the need to replace half of existing water distribution pipes due to their deterioration. PPI has led and will lead the market in plastic pipe technology, standards, and associations.” Svetlik received his PPI Lifetime Membership in 2019.
In 1975 the Corrugated Polyethylene Tubing Association was created. Later known as the Corrugated Polyethylene Pipe Association it became the Drainage Division of PPI in 2019. It focuses on the use of corrugated pipe that can be found up to 60 inches in diameter for stormwater and gravity sewer systems. “The members of this division are some of the largest users in the United States of recycled plastic,” Fink said. “One company processes more than 550 million pounds of post-consumer recycled plastics for its pipe products. Keeping this large amount of material out of landfills is possible because of the growing demand for this type of pipe.”
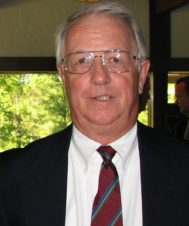
PPI bestowed an Honorary Lifetime Membership to James Goddard, P.E.
In 2011, PPI bestowed an Honorary Lifetime Membership on Drainage Division member James Goddard, P.E. recognizing his more than 30 years of contributions and industry innovations. Goddard retired from Advanced Drainage Systems, Inc. (ADS) as the company’s Chief Engineer.
“Now with a uniform, consistent voice, PPI and specifically the Drainage Division, can go out to federal agencies such as the U. S. Department of Transportation, EPA, Army Corps of Engineers, and others plus state agencies, such as Departments of Transportation, as well as significant organizations such as AASHTO with a common voice technically and that has helped the industry to grow and prosper and has significantly benefited our nation.”
Fink and his organization foresee increased use for plastic pipe. “The trend to create more applications along with enhanced grades of resin and even new resins continues to accelerate at a rapid rate,” he stated. “And we fully expect this continue for the next 70 years. PPI’s first 70 years has been an exciting journey.”
Additional information can be found at www.plasticpipe.org.
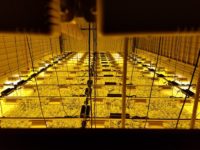
This paper refers to legal professional cannabis growers complying with state/provincial laws. Professional cannabis growers are well aware that environmental conditions play a critical role in plant quality and overall yield. Most can recite the ideal temperature and humidity for their crops without missing a beat. But ask most growers which type of pipe is Read more
This paper refers to legal professional cannabis growers complying with state/provincial laws.
Professional cannabis growers are well aware that environmental conditions play a critical role in plant quality and overall yield. Most can recite the ideal temperature and humidity for their crops without missing a beat. But ask most growers which type of pipe is best and they’ll likely to refer you to the closest head shop. The fact is professional growers (of cannabis or otherwise) are generally unaware of the piping options they have or the extent to which these options impact structural costs, energy efficiency and overall sustainability. When these matters are given proper consideration, polypropylene emerges as a great choice for this burgeoning industry.
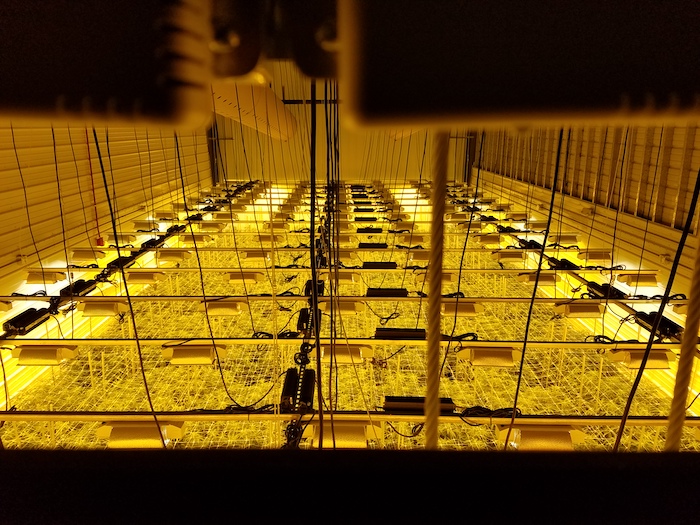
Cannabis growing facilities use a lot of energy and generate a lot of heat, making a reli- able cooling system essential.
Polypropylene pipe has been widely used for plumbing and hydronic heating in Europe since the 1970s. However, it was not introduced to North America until 2005. Since then, it has become increasingly popular for a wide range of applications, from radiant heating of sports fields to process applications in craft breweries. It is a lightweight yet highly durable thermoplastic pipe with pressure and temperature tolerances that make it suitable for hydronic heating and cooling, potable water, and industrial and food-grade applications.
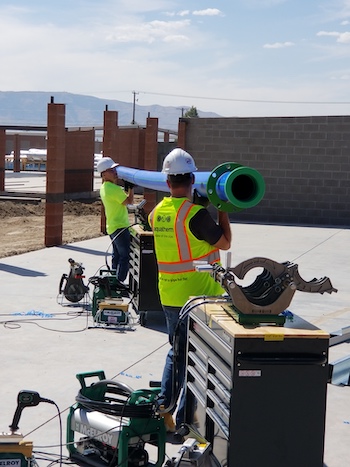
Depending on size and wall thickness, polypropylene pipe can weigh up to 70% less than carbon steel pipe.
Unlike metal pipe, the installation of polypropylene pipe does not involve traditional torch welding. Instead it relies on a flameless heat-fusion method that’s easy to learn and highly reliable at creating virtually leak-free connections. When contractors become adept at heat fusion, they can typically install polypropylene piping much faster than welding copper, carbon steel and stainless-steel pipe.
An appealing characteristic of polypropylene is its chemical purity and inertness. It does not rust, scale or leach any impurities into to the fluids it transports, nor does it react with most chemicals. This not only improves its longevity over other piping materials, it also makes it suitable for a wide range of applications. Furthermore, unlike PVC or CPVC piping, polypropylene pipe does not become brittle or susceptible to cracking when exposed to cold temperatures. A full list of the physical/performance characteristics of polypropylene and associated benefits is shown in Table 1.
Where does polypropylene fit into the day-to-day operation of a grow facility? The answer is pretty much any application that requires the transport of fluids. But to truly understand the potential roles that polypropylene can play in the growing cannabis industry, one must first look at the special needs, challenges and values of the industry.
An Energy Intensive Industry
The electrical demand of cannabis grow facilities is staggering. According to the 2018 Cannabis Energy Report, legal cannabis cultivation in the U.S. consumes an estimated 1.1 terawatt-hours of electricity a year, enough to power all of Newark, New Jersey or Anaheim, California.[1] In indoor grow facilities — very often repurposed warehouses or other types of vacant buildings —this massive energy consumption is caused by the artificial light required to grow cannabis. Heat from these lights imposes another energy burden: cooling. Year-round cooling loads are unavoidable in indoor facilities since carefully controlled space temperatures are essential for growers to achieve maximum yields. Greenhouse facilities may avoid most of the need for artificial light, but still need heating, cooling and dehumidification. In either case, large facilities benefit from the long-term efficiency of centralized hydronic heating and/or cooling systems, which are typically about 15 percent to 20 percent more efficient than other HVAC options.[2] These systems utilize piping to transport the heating water to and from a central boiler system and to transport cooling water to and from a chiller and/or evaporative cooling equipment.
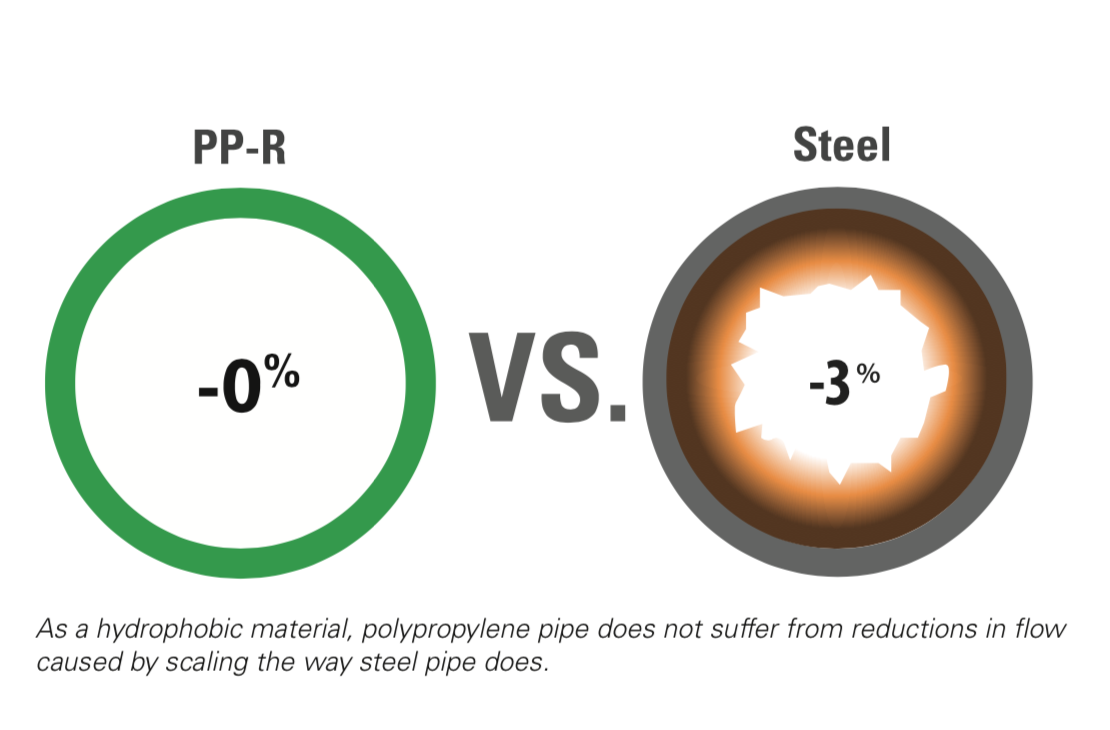
Polypropylene piping is ideal for these applications for reasons that directly impact the efficiency and longevity of a grow facility. First, the inner walls of polypropylene pipe are uniquely smooth, resulting in reduced friction losses, reducing pump energy consumption. The friction losses of polypropylene start out low and remain low for the life of the system because the pipe is not susceptible to rust or scale. Steel, copper and other metals do rust and corrode over time, increasing friction losses and the pump energy required to overcome those losses.
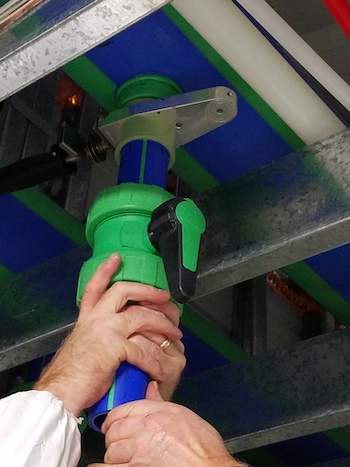
Socket fusion (shown here) is one method of heat-fusing polypropylene pipe and fittings.
Polypropylene pipe also can be used in conjunction with geothermal heat pump systems which are frequently applied in agriculture. Geothermal systems rely on the earth or a body of water as a heatsink and/or heat source for highly efficient transfer of heat to and from the growing spaces for space conditioning and agricultural processes. In these applications, polypropylene pipe transports the heating and/or cooling fluid from the central energy source to forced-air equipment or a radiant distribution loop. The pipe can be buried in the ground and/or concrete floors without the need for any protective sleeves or wrap.
Another strategy that grow facilities often use to reduce their energy consumption is heat reclaim. In these applications, polypropylene pipe can be used to transfer energy to or from process water, wastewater, or any other source that can be used to pre-heat or pre-cool water for other heating, cooling or process needs. This gives growers the opportunity to fully optimize whatever resources are available to them – whether it be the sun, a nearby lake, or even a nearby wastewater treatment plant. It’s all been done with polypropylene.
Specialized Growing Strategies
Not all commercial cannabis is grown in soil. Some is grown hydroponically with plant roots submerged in a nutrient-rich solution of water and fertilizers while others are grown aeroponically with roots suspended in air, drawing nutrients from a sprayed mist. These grow strategies very often rely on high purity water (typically reverse osmosis or deionized water) when existing water sources are determined unsuitable.
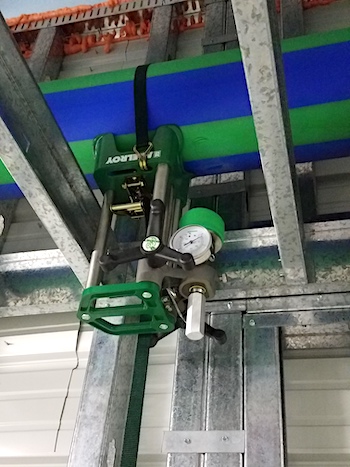
Versatile fusion tools allow polypropylene pipe to be heat- fused in spaces in which welding metal pipe would be difficult or impossible.
High purity water automatically limits piping options. Copper should never be used with deionized water because if the fluid’s pH levels fall below 6.5, corrosion may occur and copper molecules can leach into the supply. Although stainless steel piping is an option for these applications, it is often cost-prohibitive and it, too, will leach over time if the water should become too acidic or too alkaline. Polypropylene is ideal for these applications because it does not leach, and its installation never requires the use of any potential contaminants such as solder, flux or glue. It can even be used for potable water and food processing since it is available in formulations that meet both NSF 51 and NSF 61.
Facilitating Construction and Expansion
Growers and owners are typically under a lot of pressure to quickly get grow facilities operational so they can begin the journey from seed to profit as soon as possible. Construction schedules are always a challenge, particularly when it comes to mechanical components like piping. Installing metal pipe requires licensed welders (expensive and increasingly scarce) as well as special permitting for the use of open flames on a jobsite. In addition, maneuvering heavy sections of metal pipe into existing structures and then supporting it so it can be welded into place is both logistically and physically challenging. Under these circumstances, a seemingly trivial error like a miscalculation in metal pipe length can put a project several days (if not weeks) behind schedule.
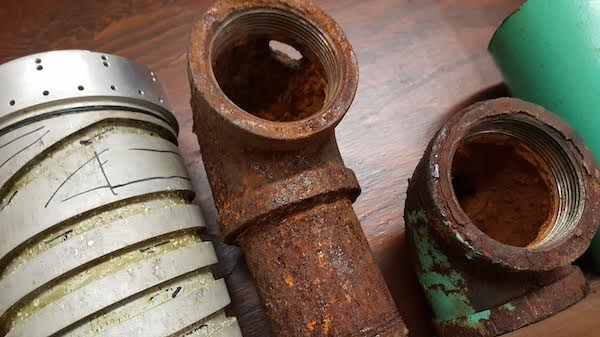
Polypropylene pipe is hydrophobic and will never scale and corrode the way metal pipe does.
Opting for polypropylene pipe keeps these jobsite nightmares at bay for the following reasons:
- Polypropylene is lightweight – especially helpful in greenhouses where structural support is limited
- Polypropylene fittings can be prefabricated offsite in controlled areas so that jobsite fabrications are minimized – some manufacturers even offer fabrication services
- Improper lengths can usually be amended at the jobsite with little disruption to work schedules
- The pipe’s maneuverability compared to metal means it can be better negotiated in tight spaces
If an owner has hopes to expand the facility in the future (as many do), polypropylene piping systems are much easier to build out than metal pipe. Strategically located shut-off valves make it easy to isolate flow and cut into existing pipe to create new connections with minimal disruption to current operations. Fusion outlets allow for easy and relatively inexpensive expansions and one manufacturer offers a hot tap solution. Again, no flames or permits are required.
Beer There, Done That
If cannabis entrepreneurs need relevant examples of all that polypropylene can do, they need only look as far as the craft brewing industry. Craft brewers, an intensely collaborative group, have solidly embraced polypropylene for all that it has to offer, most notably its purity, sustainability, and fast and flexible installation – interests that closely parallel those of the cannabis industry.
“The word of mouth in the craft brewing industry is amazing, so we’ve had tremendous growth from breweries using it, not just for the glycol lines but in their heating and cooling applications, their geothermal applications, their domestic water supply, CO2, compressed air applications and beyond,” said Barry Campbell, VP of Marketing at Aquatherm, a leading manufacturer of polypropylene pressure piping systems.
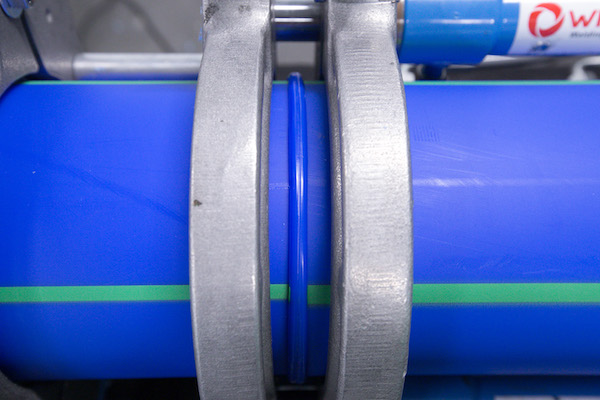
A properly executed heat-fusion on polypropylene pipe creates a single piece with no leak paths.
According to Campbell, the fact that polypropylene is among the most environmentally friendly piping systems available has helped Aquatherm gain favor among craft brewers. One polypropylene pipe manufacturer has also done the certification work to allow the product to contribute to LEED v4 credits in the U.S. Green Building Council’s (USGBC) program.
An interest in sustainability is just one of the many commonalities that exist between the cannabis and brewing industries. Like so many newly incorporated cannabis growers, many craft brewers begin their entrepreneurial journey in the shell of a vacated building where existing infrastructure can challenge piping installations. The building or parking lot next door is “Phase II” of their venture. Finally, owners are often the same people brewing the beer or growing the cannabis, so they tend to be more hands-on in the selection of mechanical equipment. They do their own research and tend to look outside the box for ways to conserve energy.
Robert Millspaugh, operations supervisor at Flathead Lake Brewing Company in Bigfork, Montana, did extensive research on what piping to use for the process side of the brewery before ultimately choosing polypropylene. Flathead Lake, born from the ruins of an old bowling alley, installed several thousand feet of polypropylene to transport both heating water and glycol for heating, cooling, and process applications. Part of the system even uses clean effluent from a nearby water treatment plant to indirectly pre-temper process water for better efficiency.
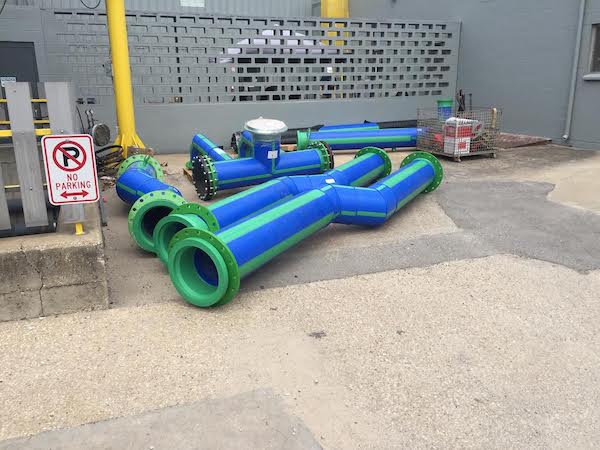
“We were looking for products that would help us achieve a LEED certification and [polypropylene] had a lot to offer. I also came across an article on Epic [Brewing Company in Salt Lake City] and how they used [polypropylene] in a renovation and discussed the product with the brewer there,” said Millspaugh.
Polypropylene also has been used successfully in brewing applications that require piping for food-grade and potable water.
Avondale Brewing Co., in Birmingham, AL was the first North American brewery to use Aquatherm’s food-grade (NSF-51) polypropylene pipe to transport beer from vessels in the main brewery to its packaging building where it is kegged, canned and bottled. The piping, which also is NSF-listed for potable water, is cleaned and sanitized between uses. Of course, like all of the manufacturer’s polypropylene systems, the piping is guaranteed to be free of heavy metals and toxic chemicals.
Cleanliness is a high priority in breweries and is one of the main reasons Founders Brewing Co. in Grand Rapids, MI, decided to use polypropylene in a heat reclaim process that taps heat from the brewing process to pre-heat outdoor air before it enters the building’s HVAC system. The piping is wash-down rated, so the brewer can keep the brew facility sparkling clean.
Examples like these demonstrate the potential for polypropylene piping in the cannabis industry.
“The craft brewing industry and everything it has been able to do with our pipe has created an unexpected blueprint for cannabis growers and how they can use polypropylene to facilitate construction, save energy and be more sustainable,” said Campbell.
[1] New Frontier Data, 2018 Cannabis Energy Report. Scale Microgrid Solutions and Resource Innovation Institute, co-authors. https://newfrontierdata.com/product/2018-cannabis-energy-report/
[2] Surna, Sustainability for Your Indoor Garden (blog) https://surna.com/sustainability-for-your-indoor-garden/
Sixth video in the Tech TV series presents pros and cons of various control strategies. Lindon, UT — Preventing Legionnaires’ disease by controlling the growth of Legionella bacteria in water systems is the topic of the latest Tech TV video from Aquatherm. The video is available at https://aquatherm.com/videos/legionella. Legionnaires’ disease is transmitted through inhalation of Read more
Sixth video in the Tech TV series presents pros and cons of various control strategies.
Lindon, UT — Preventing Legionnaires’ disease by controlling the growth of Legionella bacteria in water systems is the topic of the latest Tech TV video from Aquatherm. The video is available at https://aquatherm.com/videos/legionella.
Legionnaires’ disease is transmitted through inhalation of water vapor in which the Legionella bacterium is present. It can present a very serious health risk to susceptible populations. Sources in a building can include misters, humidifiers, whirlpools and spas, evaporative coolers, and open- and closed-loop cooling towers. The best means of controlling Legionnaires’ Disease is by eradicating Legionella from a building’s water supply.
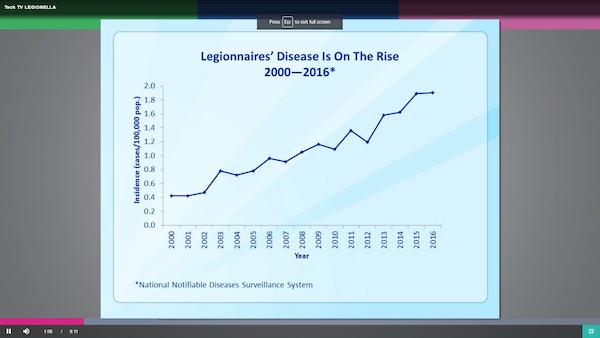
In this Tech TV video, Jim Paschal, P.E., Chief Technology Officer, Aquatherm North America, evaluates the pros and cons of various chemical and non-chemical Legionella control strategies, including hyper chlorination, chlorine dioxide, monochloramine, copper-silver ion generation, heat, and ultraviolet light.
The Legionella video is the sixth in the series of Aquatherm Tech TV videos. Other topics have been mixed systems, temperature, pressure, flow rate, and support considerations. All Tech TV videos can be found here: https://aquatherm.com/video-library. All of the videos in the series are free and available 24/7.