Use these tips to keep customers comfortable this winter Do you know how to ensure your tankless water heater installations perform optimally this winter? Tankless water heaters — known for their on-demand hot water, low energy use, and compact size — are popular among homeowners. Propane-powered systems offer an additional advantage: they can be installed Read more
HVAC
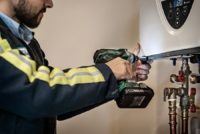
Use these tips to keep customers comfortable this winter
Do you know how to ensure your tankless water heater installations perform optimally this winter?
Tankless water heaters — known for their on-demand hot water, low energy use, and compact size — are popular among homeowners. Propane-powered systems offer an additional advantage: they can be installed virtually anywhere.
For customers located in regions that experience snow and frigid temperatures, there are a few considerations for HVAC professionals to keep in mind to ensure their customers’ comfort year-round.
Here are eight tips for specifying, installing, and maintaining tankless systems in cold climates:
- Size the unit for the cold. As temperatures drop, more time and energy are needed to heat water to the desired level. To ensure customers’ tanks meet demand throughout the year, it’s important to know how they’ll perform in cold weather. For example, in Washington D.C., a unit that can produce 8.5 GPM on a hot summer day will only produce 5 to 6 GPM on a cold winter day.
- Design for the coldest conditions. Be aware of how low ground temperatures can go and how much water a household will need. Also consider the difference between the set unit temperature and the ground temperature, also known as the Delta T. The bigger the gap, the lower the unit’s flow rate will be.
- Bring it inside. Many tankless systems have some degree of built-in freeze protection. Check the product specs, and your region’s historical weather patterns, to determine where to install the tank.
- Vent smart. Proper venting is important. Installations should avoid freezing winds and have sufficiently long vent runs. In cold areas, the minimum vent run recommendation is six feet.
- Keep vents clear of snow. Before a snowstorm, remind customers to keep a few feet around the vent clear of snow. Some tankless models offer air intake from the outer pipe — if that’s blocked, the unit may turn itself off.
- Educate customers with recirculators. For customers whose systems have a recirculating loop, remind them to turn off that function when bad weather is on the way. If the vent termination is snowed under, the unit will eventually power off with an error code.
- Consider condensation. Drain condensate from condensing units into a conditioned space to avoid drain freezes, which will cause the unit to turn off.
- Be ready with backup power. Many tankless systems need electricity for freeze protection and ignition. A propane standby generator can help ensure that customers’ hot water will continue to flow, even during a power outage.
For more information about propane tankless water heaters, visit Propane.com/Water-Heating.
Bryan Cordill is director of residential and commercial business development for the Propane Education & Research Council. He can be reached at bryan.cordill@propane.com.
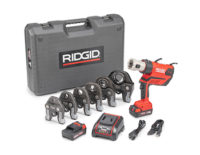
The RP 350 features a brushless motor, no service interval downtime and 360-degree swiveling head. RIDGID®, part of Emerson’s Professional Tool group, is adding even more versatility to its line of trusted press tools with the introduction of the RP 350 – an advanced, long- running press tool that’s built for the most demanding jobsites Read more
The RP 350 features a brushless motor, no service interval downtime and 360-degree swiveling head.
RIDGID®, part of Emerson’s Professional Tool group, is adding even more versatility to its line of trusted press tools with the introduction of the RP 350 – an advanced, long- running press tool that’s built for the most demanding jobsites. Engineered to be five percent lighter and almost three inches shorter than its predecessor, the RP 350 eliminates scheduled service intervals for less downtime and features a brushless motor, 360-degree swivel head and most advanced LED interface and lighting.
“RIDGID has been the leader in press technology for decades, and we’re excited to give tradespeople even more options for connecting pipe quickly, safely and with less fatigue,” said Michael Provenzano, global product manager, press connections, RIDGID. “We’ve already heard from contractors who previewed the RP 350 at the AHR Expo that the tool exceeds their expectations and they are excited to upgrade their pressing capabilities on the jobsite.”
Weighing only eight pounds with the battery, the RP 350 features an advanced brushless motor, known for maximizing tool longevity, efficiency and durability. The tool’s 360-degree swivel is an industry-first and comes paired with brightest-in-class LED lights to let users not only access tight spaces – but see them more clearly in low-light applications.
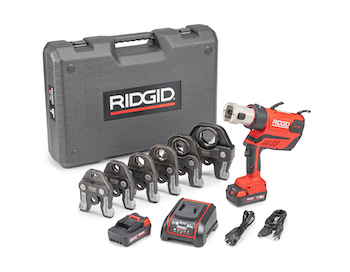
“The RP 350 is designed for contractor ease of use, not only from the standpoint of creating a quality press, but also to minimize contractor fatigue when using the tool,” said Don Embree, manager, industrial design – professional tools, Emerson. “Every feature we built into the tool helps put less impact on the body – for a more productive day and to reduce muscle fatigue.”
Ideal for making connections on residential, commercial and industrial jobs, the RP 350 is compatible with the full line of RIDGID jaws and rings, including: 1⁄2 – 4-inch ProPress® for copper and stainless steel, 1⁄2 – 2-inch PureFlow® for PEX, and 1⁄2 – 2-inch MegaPress® for carbon steel. It also offers maximum versatility, pairing with the RIDGID Press Booster for 2 1⁄2 -inch, 3-inch, and 4-inch carbon steel, StrutSlayrTM Strut Shear Head and the Press SnapTM Soil Pipe Cutter. The tool’s 18V battery platform includes a car charger for on-the-go battery charging; the unit also pairs with the RIDGID Link app to track tool usage, service needs, battery life and last known location. All RIDGID press tools, including the RP 350, come with the RIDGID Full Lifetime Warranty.
To purchase or learn more about the RP 350 and its accessories or other press tool products, visit RIDGID.com, or call toll-free: 1-800-4RIDGID.
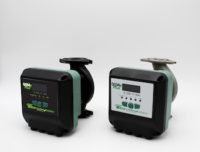
Taco Comfort Solutions® has expanded their family of easy-to-use, ECM high-efficiency circulators with the addition of the 0034e™ and 0034ePlus™ models. With a maximum of 34 feet of head and 50 gpm, the new circulators offer up to 85% energy savings over a conventional circulator. These circulators are available with cast iron or NSF/ANSI 61 Read more
Taco Comfort Solutions® has expanded their family of easy-to-use, ECM high-efficiency circulators with the addition of the 0034e™ and 0034ePlus™ models. With a maximum of 34 feet of head and 50 gpm, the new circulators offer up to 85% energy savings over a conventional circulator.
These circulators are available with cast iron or NSF/ANSI 61 & 372 certified stainless steel volutes, so they are ideal for closed-loop heating systems as well as domestic hot water recirculation systems. Both circulators also offer a convenient, rotatable control box cover for a professional look, no matter the orientation of the installed circulator.
The 0034e features an easy-to-use dial with five operating modes, including constant pressure, fixed speed, Taco’s exclusive activeADAPT™ self-adjusting proportional pressure, and 0-10V capability. The 0034ePlus adds proportional pressure and more constant pressure settings as well as a digital display with real-time feedback, including watts, GPM, feet of head, and RPM. Both circulators are dual-voltage 115V/230V.
Both new circulators come with exclusive features that make Taco’s ECM high-efficiency circulators so easy to use, including SureStart® automatic unblocking and air purging, BIO Barrier® black iron oxide protection, dual electrical knockouts, six-inch stranded leads, recessed flange nut-grabbers and double insulation so no ground wire is needed.
For more information, visit www.TacoComfort.com
Top water heating and storage manufacturer and trade organizations share concerns about aging blue-collar workforce. Ambler, Pa. — As global economic disruption accelerates during the ongoing coronavirus pandemic, leaders in manufacturing, distribution and residential and commercial services are calling attention to overlooked career opportunities in the traditional skilled trades and urging an industry-wide focus on workforce Read more
Top water heating and storage manufacturer and trade organizations share concerns about aging blue-collar workforce.
Ambler, Pa. — As global economic disruption accelerates during the ongoing coronavirus pandemic, leaders in manufacturing, distribution and residential and commercial services are calling attention to overlooked career opportunities in the traditional skilled trades and urging an industry-wide focus on workforce development to close the skilled trades labor gap and recruit a new generation of young workers.
“For young people who are seeking a rewarding career but don’t feel like four years of college is the best choice for them, there are some tremendous advantages to seeking a career in the traditional skilled trades, from good starting salaries and job security to a variety of opportunities for advancement,” said Carl Pinto Jr., senior director of marketing communications, Bradford White Corporation.
“Unfortunately, many high school students and recent graduates who would thrive in our industry never consider a career in the trades. This is due in part to the overwhelming message that is being delivered through a variety of channels — college is the only path to success. But recent circumstances have highlighted the fact that manufacturing and residential and commercial service jobs are a critical part of the national economy. Lockdowns and social distancing have created challenges for the industry, but HVAC service and clean hot water have proven to be necessities during a pandemic. An overwhelming number of manufacturers and contractors were quickly identified as essential services and have been operating continuously since the COVID-19 outbreak began.”
Pinto and other experts share a concern about the demographics for manufacturing, distribution and skilled trades jobs.
“Everyone has a sweet spot in life and a unique path toward finding the career that best suits them,” said Rep. Tim Walberg of Michigan. “For some people this might mean pursuing a four-year degree, while for others an apprenticeship might be the answer. Whatever that path may be, it is critical that we look for innovative ways to provide educational opportunities for America’s workers and ensure our workforce is prepared for the good-paying jobs of the 21st century.”
According to the American Supply Association, approximately half of the people in those industries are at or nearing retirement age, but only 4% are under the age of 26.
“That’s our greatest concern, that there just aren’t enough people,” said ASA CEO Mike Adelizzi. “At the same time, we have to recognize that it’s an opportunity, too. With so many people aging out of the industry, a young worker can fast track his or her career.”
The ASA and other organizations are involved in ongoing efforts to combat stereotypes about blue-collar jobs. One of ASA’s key initiatives is the ASA Education Foundation, which provides innovative tools and strategies to support the preparation of the next generation of leaders and continued support for the next generation of the industry’s workforce.
“Our industry offers so much for young workers, but unfortunately there are some persistent stereotypes about manufacturing and trades jobs,” said PHCC Executive Vice President Michael R. Copp. “We feel a major responsibility to help our members reach and recruit the best talent. Connecting with the next generation of skilled trades workers not only helps individual businesses succeed, it elevates the industry as a whole.”
The Plumbing-Heating-Cooling Contractors—National Association (PHCC) has made workforce development a strategic priority and is developing a tool kit for its members and their suppliers. PHCC’s Workforce Development Center currently provides potential employees, manufacturers, contractors and suppliers with a library of online information and training material, with additional assets in the works. In response to needs that arose during the pandemic, the PHCC Educational Foundation is leveraging its online learning platform to provide alternative methods to help contractors attract and train new employees.
To learn more about Bradford White, please visit https://www.bradfordwhitecorporation.com/
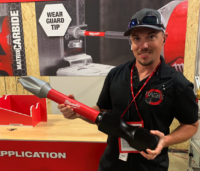
These days have been pretty busy for Bulldog Contractors. “When COVID first appeared, there wasn’t enough hours in the day to get everything accomplished. And once stimulus checks hit, there was a huge spike in work flow. We have been very blessed and fortunate to be working through the pandemic,” says Jeff Keller. A licensed Read more
These days have been pretty busy for Bulldog Contractors. “When COVID first appeared, there wasn’t enough hours in the day to get everything accomplished. And once stimulus checks hit, there was a huge spike in work flow. We have been very blessed and fortunate to be working through the pandemic,” says Jeff Keller.
A licensed master plumber, Keller works for his father in running Bulldog Contractors in northeast Texas. Bulldog Contractors is a well-rounded company that strives to provide a one-stop shop for its customers, and that’s why Keller specializes in service work for plumbing, electrical and septic, and carries multiple licenses in electrical and septic as well.
Yet, the career path for Keller wasn’t always defined early on. When Keller was in high school, he wanted to be a veterinarian based on his love for pets and animals. “I honestly didn’t have the grades for it, so if I had to guess, I would be in the oil field chasing that dollar,” says Keller.
But watching his father succeed in business—and life—was huge for Keller. “I honestly never thought of following in his footsteps growing up. But as I got older, and needed a summer job, I fell in love with the overall variation of different types of jobs and people I encountered on a day-to-day basis,” says Keller.
To Keller, his father was his biggest motivator. “He put me on a higher pedestal than I would have liked growing up as a kid, but in the end, it turned out very well and it kept my mindset on track. Also, some very deep guidance was from my grandfather—on my mother’s side—as well. The advice, stories, and memories that I have retained has been priceless. If I could be half the man my grandfather was …. they just don’t make them like they used to!” says Keller.
Keller has never looked back as his love for the trades has grown over the years. “In the service industry, you just never know what you are getting yourself into that day,” he says. “I like the uncertainty. The jobs are never identical. It keeps you on your toes and the mind busy,” says Keller. Oh, and as for Keller’s love for animals? “With my current career, I get to see multiple houses a day and their pets; I bond with them and that’s a cool small aspect of my day.”
Moving the Trades Forward
Concerning to Keller about the trades, though, is the quality of work and labor. “With the trades dying, so does the manpower to get projects completed. So, it’s a rat race to get in and out and onto the next one. Years or even sometimes months down the road we are fixing issues that could have been resolved if some time and quality was put into a job,” says Keller.
One of the biggest concerns for the trades overall is to infuse young, skilled labor into the trades. “It’s all about advertising and education; they go hand-in-hand. We really need to be getting into the school systems and reaching out to the youngsters. With the way this world is going at this moment, this will be a never-ending battle and a hard one to tackle. ANYTHING is possible, though!”
And when those recruits are ready, Keller suggests not going to school—unless required—to learn the trades, especially if you are going into the service industry. “What a service technician knows and understands isn’t taught in a book. Get into the trade, get your eyes and ears in the field, and become a sponge. Learn everything you can,” says Keller.
Work/Life Tilt & Spare Time
Balancing family time and work is often tough to navigate. Keller’s family understands that sometimes the phone rings and he has to take the call, yet he will always make time for them. There will be work and money to be made, regardless, says Keller and his family is the most important thing that he has and cherishes.
“Some days I make a lighter work load to pick the kids up from school and take them on a field trip, or doctor appointments. I took my middle girl, Elyse, out to ice cream the other day, just us. The little things are what they will hold onto and remember for years to come. My father did the same for me and I plan to pass that onto my family, as well. You must make time for your family because the kids will be grown and gone before you know it,” says Keller.
For Keller, though, it’s hard for him to sit still so you’ll normally find him in the shop tinkering around mostly cleaning and keeping it organized, and playing with the kids. “The same with my yard, I’ll go mow dirt if I have time! It’s my quiet place if you know what I mean. On the weekends, I enjoy my main hobby, which is fishing—mainly night fishing so the wife and kids sleep through most of it while I’m gone,” says Keller.
Social media has opened many doors for Keller that he would have never imagined. “If someone told me 10 years ago, I would be traveling all over the country—anything from factory tours to trade shows to attending early tool/product releases, I wouldn’t have believed them. I appreciate all the new friends and connections I have made. It’s a true honor.”
What people may not know about Keller is, “I’m a nerd when it comes to numbers and efficiency of my house. During a day I might check the water pressure of my house 2-3 times. Same goes for my current water heater temp—digital display on heat pump unit. And my solar input and output. I keep a close eye on efficiency.”
The last time Jeff Keller said “today is a great day”? “I took off work super early, surprised my wife and we went out and about for the day, no schedule at all.”