Training in 2024 is just as important as ever. How do you integrate training, education and continued learning with today’s busy contractor? Power Points, sales pitches and doughnuts. Tried and true methods of training gone by, that’s for sure. But what does today’s training look like, especially in the purview of the younger generation of Read more
hydronics
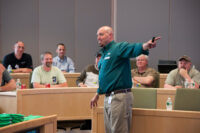
Training in 2024 is just as important as ever. How do you integrate training, education and continued learning with today’s busy contractor?
Power Points, sales pitches and doughnuts. Tried and true methods of training gone by, that’s for sure. But what does today’s training look like, especially in the purview of the younger generation of contractors that digests information in 90 seconds or less?
“What was that? Sorry, I was looking at my phone,” jokes Max Rohr, Director, Education and Technical Marketing, Caleffi. “Five years ago, a three-minute-long video was a good option, now it will seem long if it is over that 90-second threshold. Ideally, you get to the point in the first five seconds and work the explanation back from there. Like showing the cake and then going back to bowls of ingredients.”
According to, Dave Holdorf, Residential Trainer & Rep Training Manager—Eastern Region, Taco Comfort Solutions, it’s a challenge. “We’ve found that it helps to bring different instructors in for specific segments of the training. Each instructor brings their own perspective; even hearing a different voice in the room makes for a more compelling presentation. Every facet of our training is now geared to maintain the attention of participants. We also make sure to schedule breaks so that the attendees can attend to business, or need at home. By creating the curriculum with attendees in mind, their focus remains with the topic in front of them.”
Nevertheless, the training department at Taco has always looked at training not from a product view but from an application perspective, giving attendees the information they need to do their job better, and to give their customers the comfort they deserve. “We use real world experiences to solve real world problems with personal experiences and a bit of humor—as you know, John, it ain’t worth doing if you’re not having fun as well,” says Holdorf.
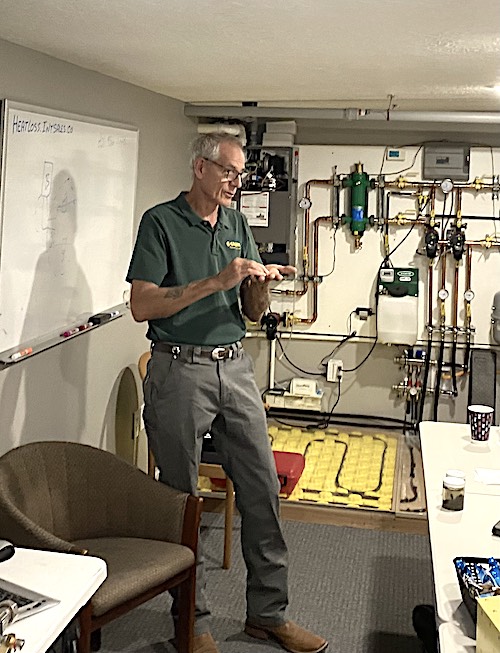
Caleffi’s Bob “Hot Rod” Rohr brings his props and his wealth of experience and knowledge to trainings.
But what about those PowerPoints and doughnuts? “Every learning style is different, so you have to be adaptable. If you see the audience tuning out a PowerPoint, stop and grab a product to bring to an attendee and talk about a case study that is related instead,” says Rohr.
In addition, everything falls apart for a trainer if the audience gets the impression they are overpromising, adds Rohr. For example, “Honesty is something Hot Rod is specifically good at in contractor training sessions. As a former installer, he always has tips for getting the job done and workarounds that are really tangible,” says Rohr.
The New Normal?
The Covid pandemic saw what we thought was going to be a new normal with virtual training, but what we are now seeing is the importance, and return, of in-person training.
This past year Taco saw a huge jump of in-person training, on the road as well as at Taco HQ in Rhode Island. So much so that the company had to dramatically increase the number of sessions back in Rhode Island to accommodate. “However, that does not mean to diminish the virtual training, Taco Tuesday and Taco After Dark webinars are still posting a large number of attendees that are hungry for information in bite size chunks, not as large as when we all locked down at home, but still popular,” says Holdorf.
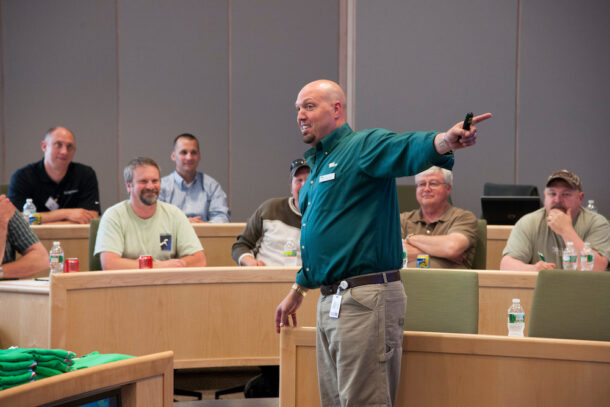
Taco’s Holdorf conducts a training at the Cranston, R.I. HQ.
Nonetheless, “when we’re online, we know it’s so easy to stray off to the next shiny thing online, so to keep attendees engaged, we encourage two-way communications. If participants have questions, we want them to ask immediately,” continues Holdorf.
In fact, Holdorf says that people who attend Taco’s webinars typically take it to the next level and seek live training. A combination of both virtual and live training can help attendees dial in on what they want to learn—or perhaps didn’t initially develop a full understanding of what it is they most needed to know. “These options allow them to fine-tune their training experience to make them as good as they want to be. And, ideally, we help them raise the bar. We routinely heard from trade pros who came to us for a better understanding of a single application or concept, and through that experience come away with an energized desire for much more,” says Holdorf.
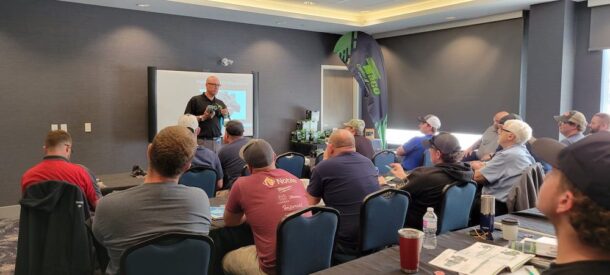
In 2023, Caleffi performed almost a 50/50 mix of in-person and virtual. Contractors like hands-on training, says Rohr, so it is good to be back on job sites for that type of interaction. And, engineers didn’t all go back to the office after COVID. “Many of the engineering sessions we do are virtual because that firm may be scattered all over the region. You might catch 20 people in a virtual training, where only 10 of them are in the office that day,” says Rohr.
Know-It-Alls
What about those who are stubborn enough to think that they don’t need further education and training? “I love this question and see and hear it often in the industry,” says Ken Midgett, L.M.P, Plumbing, Marketing Director, Interplay Learning, and former Teacher and Apprenticeship Instructor, Lehigh Career & Technical Institute.
Those in skilled trades should embrace the concept of being “lifelong learners,” consistently expanding their knowledge in their current specialty and exploring related disciplines. Whether licensed or not, individuals in skilled trades should assess their goals, career paths and professional growth within their field. It’s common for some to reach a point where they feel adequately skilled and think further education is unnecessary. According to Midgett, this assumption is misleading for several reasons:
• For example, a residential plumber could benefit from learning about commercial plumbing, Med Gas, Backflow, Water Well work, Water Conditioning, HVAC, Electrical, etc. Diversifying skills not only enhances one’s expertise but also increases their marketability across various skill sets, intern boosting income and long-term employability.
• Despite advancements in safety measures within the construction industry, the misconception that skilled trades workers are immune to injuries persists. While the overall safety landscape has improved, life-changing injuries can still occur. In such unfortunate instances, if an individual can only rely on skills specific to their trade and lacks versatility, their career may face irreparable damage. Therefore, investing in ongoing training, education, and professional development becomes crucial for ensuring resilience in the workforce and mitigating the impact of unforeseen challenges. Repurposing skillsets may be challenging when there has been no prior skill or professional development planning before the injury event.
• The industry, codes, tools, and methods to do a task are constantly changing. Skilled trades workers need to educate themselves and stay on top of new developments. This is critical to the success of a technician and company.
In the end, it’s what ends up in the ol’ noggin as useful information that translates to the jobsite. “Students only retain a tiny amount of the information that you present to them, but they will remember their feelings about the trainer for a very long time,” says Rohr. “It is hard to know if a bigger win is when customers retain a piece of information you presented or if they remember that you seem like you know what you are talking about. “If they trust that you did a good job, that memory will stay with them for a career, potentially.”
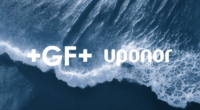
By joining forces with Uponor, GF is set to become a global leader in sustainable water and flow solutions. To support this ambition, complementary businesses will be grouped together under one roof: the new division GF Uponor will focus on Building Technology, whereas the infrastructure and utility business will move to GF Piping Systems. Michael Read more
By joining forces with Uponor, GF is set to become a global leader in sustainable water and flow solutions. To support this ambition, complementary businesses will be grouped together under one roof: the new division GF Uponor will focus on Building Technology, whereas the infrastructure and utility business will move to GF Piping Systems. Michael Rauterkus will join GF’s Executive Committee and will lead the new division together with his Uponor leadership team.
After all conditions of the tender offer have been fulfilled, GF closes the transaction as of 13 November 2023.
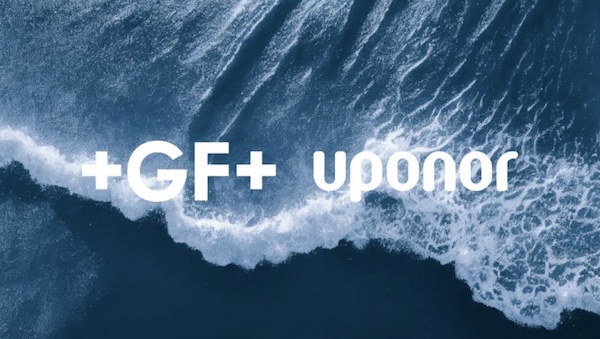
To accelerate the implementation of GF Piping Systems’ Strategy 2025 and to further benefit from global megatrends, GF will start an ambitious value creation program to unleash the full potential of this acquisition. GF Piping Systems will focus on the industrial and utility business, providing its customers with sustainable leak-free piping solutions for numerous end markets such as microelectronics, water treatment, energy, chemical processing, marine, data centers or water & gas utilities. Uponor’s infrastructure business will become part of GF Piping Systems and will further strengthen the division’s portfolio to provide customers with combined solutions.
In the new division, GF Uponor, the building technology businesses will be combined to offer a complementary portfolio for safe and clean water, as well as energy efficient heating and cooling. The consolidation of complementary businesses provides an ideal platform to develop markets with high potential for both divisions. As the brand Uponor stands for high quality and innovation, it will drive growth in intelligent Building Flow Solutions.
These organizational changes will be implemented during the course of 2024 while GF will ensure operational excellence and business continuity to customers.
“We will continue to implement our strategy, and leverage powerful global trends, such as the need for safe and clean water, or more efficient energy use,” GF CEO Andreas Müller said. “On behalf of all my colleagues, I am happy to welcome Uponor employees and start this new chapter together.”
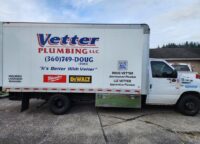
Vetter Plumbing, that is. If you’re ever in the Pacific Northwest, look up Doug Vetter, owner of Vetter Plumbing, Longview, Wash., and successful plumbing and heating contractor who has worked with the tools almost nonstop since graduating from high school in 1990. We recently rain into Doug at the pipe-cutting ceremony for Uponor’s Experience Center Read more
Vetter Plumbing, that is. If you’re ever in the Pacific Northwest, look up Doug Vetter, owner of Vetter Plumbing, Longview, Wash., and successful plumbing and heating contractor who has worked with the tools almost nonstop since graduating from high school in 1990. We recently rain into Doug at the pipe-cutting ceremony for Uponor’s Experience Center, and his passion for the trades is palpable.

Doug Vetter, right, has an infectious attitude, and enjoys living life like no one else.
In fact, you might say that young people searching for their true passion won’t likely encounter a more inspiring ambassador than Doug to a life in plumbing and heating.
There are, of course, a great many proud, highly accomplished professionals in this industry. But you’d be hard-pressed to find a tradesperson with a more robust and, at times, fearless outlook on life than Doug. He readily insists that much of this bring-it-on attitude derives from the sheer thrill of working as a service technician. “I just love my job,” he says over and over again.
For a small sampling of the sunny-side-up attitude Vetter brings to work each day, consider his morning routine of delivering doughnuts to the counter and warehouse staff at his favorite local supply house. Whoever heard of a plumber bringing free food to a wholesaler? “They have done lots of special stuff for me,” he cheerily reasons, “and, besides, it doesn’t cost that much.”
“My customers are always asking me, ‘Why are you in such a good mood today?’” he continues. “Well, when you contact me, we both know it’s not a social call. You have problems and fixing them may not be a ‘fun’ time for either of us. Why dump more stress on your situation by carrying a chip on my shoulder because I need to, let’s say, squeeze into your crawl space? Believe me, I hate crawl spaces. But being a plumber was my choice, and squeezing into crawl spaces is my job. That’s why you pay me.”
Doug willingly, happily, eagerly does his job 10 hours a day, seven days a week. But these are mere average—the actual totals could be much more in any given week. He would not have it any other way in a business that seldom lets him even slow down, let alone rest.
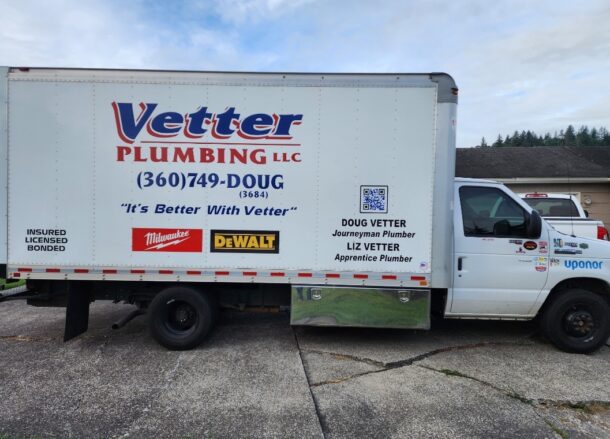
“I’ve never had a down time, even during the recent recession,” he says. “I just can’t say ‘no’ to people. That’s one of my downfalls and an issue with my significant other. But I love working.”
Back to the Uponor visit, Doug tells us that he is particularly proud of his tattoos, even the jaw-droppingly large U-P-O-N-O-R logo. Its six block letters span the full width of his back, left shoulder to right. Just as amazing: Every last ink mark strictly adhered to corporate style guidelines, right down to the correct shade of blue.
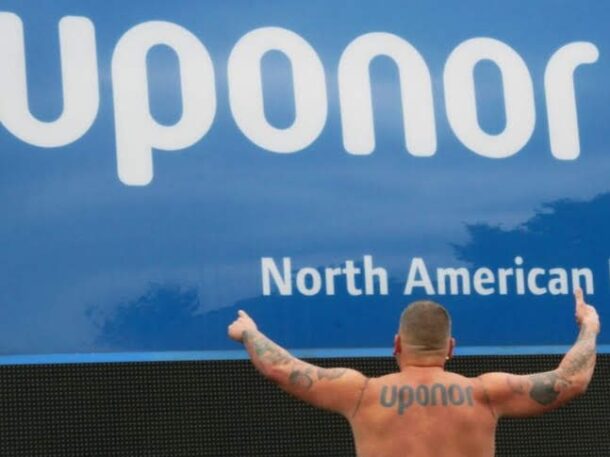
“I had a large blue Uponor sticker of the sort I put on my two trucks. I told my tattoo guy to put this exact thing on my back. He said, ‘Really?’ and I said, ‘Absolutely!’” Three grueling sessions over eight hours later, the tattoo was exquisitely in place and ready for show time whenever Doug decides to remove his shirt.
Why would he do something so “out there”? Why not? he shrugs. How better to express his unwavering loyalty to a brand he has supported nearly his entire career? “Uponor is the only brand I will put on my skin,” insists Doug, offering what is for him the ultimate compliment.
He fondly remembers his very first encounter with PEX more than 20 years ago, working for a Seattle plumbing wholesaler in the mid-1990s. Mark Walther — then a sales agent for the Portland-, Ore.-based Hollabaugh Brothers & Associates (still Uponor’s rep in the Pacific Northwest); and later a mentor for Doug when both worked at Merit Mechanical in Seattle—demonstrated the thermal memory of PEX with the familiar heat-gun demonstration that thousands have witnessed at countless trade shows over the decades.
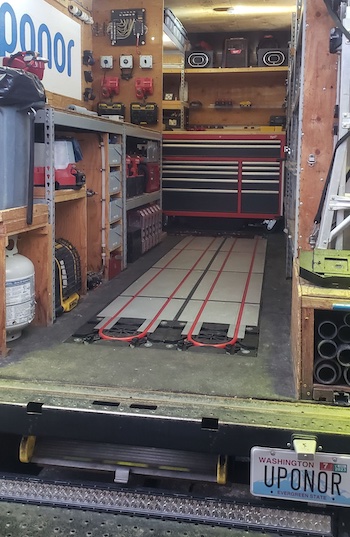
Vetter’s work truck is radiantly heated.
“Mark said to me, ‘Watch this, Doug!’ After kinking the pipe in his hand, he used a simple heat gun to make that kink vanish in minutes. I will never forget that moment—it was the coolest thing, just incredible. Every chance I get, I love showing people the same demo with the heat gun.”
Doug readily embraces the problem-solving aspect of service work: “I love going into someone’s house, learning what’s wrong, explaining the situation in ways the customer can understand and appreciate, and then fixing the problem—and fixing it in the right way.
“I can’t just throw something together for a customer. I do my plumbing a certain way—the way I was taught all those years ago at Merit Mechanical, where I earned my journeyman’s license.”
As noted earlier, those young people you’re trying to steer toward a trade career won’t likely snag a first job with Doug, who has happily—defiantly even—worked solo for the vast majority of his professional life since starting his own business. Although, his wife, Liz, is going through her apprenticeship to join him as a licensed plumber in the business.
Vetter has a certain way of running his business. “I want my cords wrapped in a one-foot circle and put away in a particular spot. My truck, a big-box van, is spotless and organized a certain way, and I want to keep it that way. That one employee I had just couldn’t do it.”

Same thing for working with the tools, if not more so: “I’m not a hard ass, but my No. 1 job is to protect the health of my customers. If I fail to create a sewer-line joint properly, the customer will have a disaster. If I expand a pipe incorrectly, I’m flooding someone’s house. I do it right because my reputation depends on it, and my reputation is all I have.”
Another, equally critical facet of “Doug’s Way” is treating every customer the same—fairly and nicely. “Nobody, it seems at times, does customer service any more. For example: promptly calling someone back who has called you. I feel badly if a day goes by before my returning a call. Many don’t do it at all and think nothing of it.
“I was taught to treat people with the utmost respect, regardless of what they look like, where they’re from, or how much money’s in their pockets. I want to fix their plumbing, of course, but I also want to give them the best service they can get anywhere.”
Currently in his 50s now, Doug plans to work “until I just can’t do it any more”—before retiring to Puerto Rico, where he says the people are warm, the weather’s warmer, and the water’s warmest of all. Until then, he will stick to his 70-hour work week as a highly motivated service plumber who gladly shoulders more work than any one man should handle, despite doing no advertising or promotion other than word-of-mouth.
“I thrive on service work. I love the instant gratification of solving problems. I get up in the morning, hit the road to meet new people, and figure out how to help. Every job is different, and the days just fly by.”
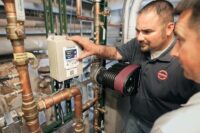
Way back in 1987, ASHRAE experts developed the BACnet protocol as a communications standard for Building Automation Systems (BAS). BACnet has since earned the respect of specifying engineers, facility managers, controls experts and service technicians worldwide as it’s now the leading technology in building automation. BACnet offers an open architecture and the ability to control Read more
Way back in 1987, ASHRAE experts developed the BACnet protocol as a communications standard for Building Automation Systems (BAS). BACnet has since earned the respect of specifying engineers, facility managers, controls experts and service technicians worldwide as it’s now the leading technology in building automation.
BACnet offers an open architecture and the ability to control and monitor any building automation process—from water sourced heat pumps and chillers to boilers and volume water heaters.
At North Andover, Mass.-based Watts, one of the largest and most diverse manufacturers in the plumbing and mechanical and HVAC market, BACnet has been incorporated into several of its brands’ technologies, most notably through its HVAC and snow-melting controls brand, tekmar; “IntelliStation” digital mixing stations for commercial domestic water control and tempering by their brand, Powers; and for Benchmark boilers and Innovation water heaters (via their “EDGE” controller), offered by the company’s brand, AERCO.
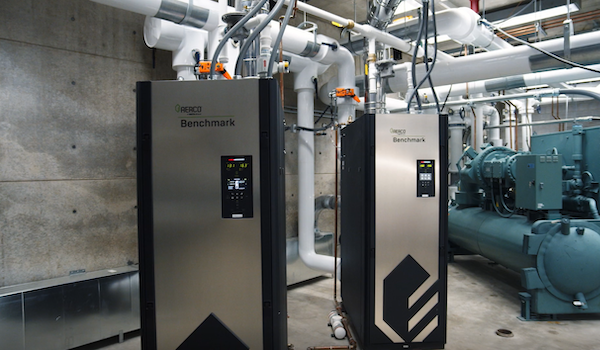
“For us, BACnet is so useful because it’s a standardized communication protocol that interconnects and ‘talks to’ all other BAS-connected technologies throughout an entire facility, and also facilitates remote monitoring and control,” said Amar Dhore, AERCO Software Engineering Supervisor. “When fully integrated, all communications can work through one BACnet device. That’s the advantage of standardization, and what it enables.”
New York-based AERCO is one of the nation’s leading suppliers of commercial condensing boilers and water heaters for a variety of industries. Several years ago two of AERCO’s brands—Benchmark boilers, andInnovation water heaters—adopted the use of BACnet to offer sophisticated communications through their EDGE controller and ProtoNode gateway, the key interfaces to BAS for legacy system communications.
AERCO offers a multi-protocol, communications gateway to support integration with customers’ building automation (BAS) and energy management systems (EMS). The plug-n-play package supports build in integration with BACnet/IP, BACnet MS/TP, Modbus RTU, Modbus MSTP. AERCO also has a ProtoNode Gateway to support legacy products like Benchmark standard, Modulex EXT boilers; Innovation and SmartPlate water heaters.
AERCO’s EDGE features built-in translation for BACnet/IP, BACnet MS/ TP, Modbus RTU and Modbus TCP protocols; these communications are selectable and configurable via touch screen (No DIP switch needed). With this easy access to data, customers have ready access to more data. They can also choose and map BAS points of his interest to access, control and monitor devices.
In fact, the company’s Benchmark Platinum boilers can be managed effectively with an app that connects with the EDGE controller. With the app, a service technician or facility manager can monitor or balance hydronic system flow, perform a wide variety of system diagnostics, or combustion analysis and calibration.
For building owners, the EDGE permits trouble-free management of all boiler/water heaters functions—whether one unit or up to 16 units, connected in a cascade.
The EDGE controller also permits flow balancing—a function that allows elimination of balancing valves and also reduces commissioning costs, one of many operations enabled through the built-in communications via BACnet IP, BACnet MS/TP, Modbus IP or Modbus RTU.
Start-up and maintenance functions are also simplified. Boilers +/or water heaters can be calibrated through assisted or manual operations, a big time-savings advantage. The assisted options offers guided steps that automatically adjust precise air/fuel ratios for optimal performance.
AERCO access and control security:
AERCO managers understand the importance of security and have taken steps to make BAS communication secure. EDGE offers built in security using IP and MAC address. Once the security is enabled, user needs to enter front end BAS MAC and IP address. Once done, Edge will only accept the communication from the BAS with specified MAC and IP address.
tekmar’s 680, 681 + 284
Vernon, BC-based tekmar Control Systems, a Watts brand, is a world class integrated engineering and manufacturing company that provides solutions for the HVAC industry. For the past 38 years, tekmar has earned a reputation as the leader in complete control solutions for hydronic radiant floor and baseboard heating systems, multi-stage boilers plants, and automatic snow melting controls.
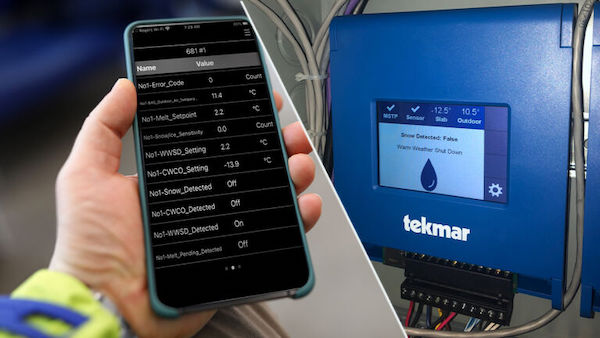
tekmar provides energy-saving control solutions for a broad range of hydronic systems—whether within a building, or outside (for snowmelt or turf-warming)—while assuring no-compromise comfort control, system efficiency and durability.
The company’s technologies provide:
- Setpoint controls—offering precise temperature control for domestic water storage tanks, pools and hot tubs.
- Boiler + domestic water controls—These technologies are designed to control temperature and operation of multiple boilers or volume water heaters. Multi-staging controls provide significant energy savings while also enhancing system reliability.
- Heating controls—Here, tekmar offers controls to provide zoning solutions for heating systems; specific models are designed for use in hydronic heating, radiant heating, HVAC systems, and baseboard or “hydro-air” applications.
- tekmarNet 4 zoning controls—These technologies connect to thermostats to control operation of heating system zone valves or heat pumps for precise delivery of heat.
- Snowmelt control and sensors—Snowmelt control systems measure and control road, driveway or walkway surface temperatures to provide safe, snow- and ice-free surfaces, and at the lowest operating cost. Controls may connect to electric or hydronic systems as the source of warmth. Fully automatic controls, or manual controls can be chosen.
“Our specialties are boiler and snowmelt system controls,” explained tekmar’s Cleber Alves. “One of our unique products is the new BACnet snow/ice sensor interface 681—designed to measure the presence of snow or ice and interfaces with the BAS to activate or deactivate electric or hydronic snow melting systems.”
According to Alves, the 681 uses tekmar sensor technology to automatically detect precipitation, then communicates with the BAS through BACnet MS/TP. This operation allows the BAS to automatically turn the heat source and distribution system on, or off, and provide operational status for all snow-melt functions. The 681 is ideally suited for commercial applications such as hospitals, schools, airports, ski resorts, business entrances, driveways, loading docks, and shopping malls.
The 681’s features include slab target temperature, automatic snow and ice detection, error codes, warm weather shut-down, melt pending function, cold weather shutdown, and supports both in-slab and retrofit aerial sensors—all with BACnet MS/TP communication.
IntelliStation digital water control
Public safety relies chiefly on the availability of clean water. As it can affect water quality, the condition of premise (building-specific) plumbing systems have a direct impact on the safety of those within the facility. The ability to remotely monitor and control water temperature, flow, and other parameters in a quick and precise way is vital to delivering healthy, safe water in an efficient manner.
Patents held by Powers, a Watts brand, function as the backbone for many products in commercial and industrial water temperature control markets. The company develops and manufactures thermostatic and digital mixing solutions to bring safety and comfort to modern plumbing systems.
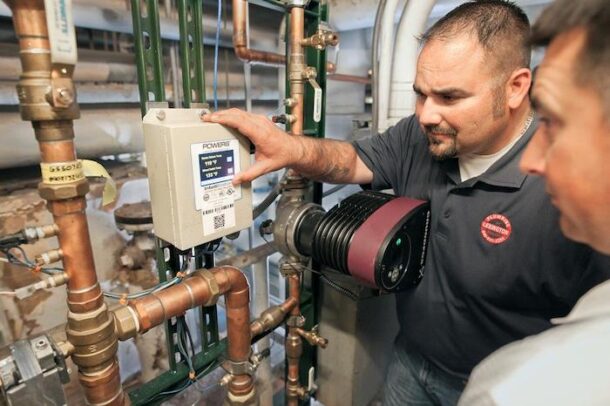
“IntelliStation and IntelliStation Jr. [a smaller version] digital water mixing systems are designed to deliver tempered hot water throughout a recirculation loop in commercial and institutional facilities,” explains Sr. Product Manager Bruce Fathers. “Our digital solutions can be integrated into a BAS to allow facilities managers to remotely monitor and control water temperatures.
“We offer most of the common protocols, with gateways to others if need be,” added Fathers. “Modbus and BACnet are native to our controller, so it’s integrated into our IntelliStation products with no additional cost. Most of our competitors do require an additional module at an added cost to facilitate BACnet. So, it’s become a competitive edge for us, one our customers have come to appreciate.”
According to Fathers, BAS is used to seamlessly monitor and control important facets of system operation—such as mixed outlet temperature, pressure, flow, and inlet temperature. The sensors all require connection/input points.
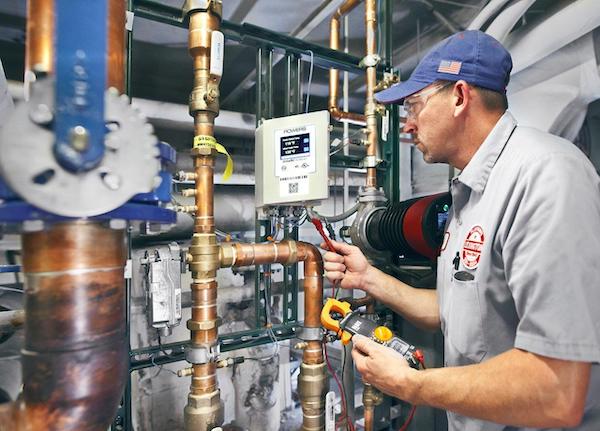
“For commercial domestic water systems, mixed outlet temperature is most important,” explained Fathers. “It’s typically set at 120°F, or 140°F—to either render [biogens/pathogens] unable to reproduce, or to outright kill them [point-of-use mixing valves are then used at showers and faucets to protect users. Facility managers have remote visibility to all critical datapoints.
Fast, responsive digital technology enables the collection of a large amount of data which can be stored and communicated through a building automation system (BAS) or locally at the controller, providing intelligence at the foundation of the entire plumbing system.
Internet of Water
Control of the water recirculation loop ensures safe, precise, and consistent water temperatures (+/- 2oF), supports energy conservation, and reduces energy costs. BACnet IP, BACnet MSTP, and Modbus protocols are supported.
Technology helps to fulfill these needs with digital mixing and connected components like sensors and cloud-based monitoring.
The extent to which COVID-19 has impacted public health and the increased prevalence of Legionella bacteria have highlighted the need for:
- Visibility of water temperature, flow, and quality even when off-site
- A way to remotely control water temperatures
- Automated monitoring and reporting of premise plumbing water parameters and facility management activity
- Connected products that help increase safety and efficiency
- Reliable ways to reduce the risk of Legionella and other harmful bacteria
BAS empowers facility managers and engineers to proactively prevent issues before they arise, rather than having to react to or attempt to mitigate issues once they’ve occurred,” added Fathers.
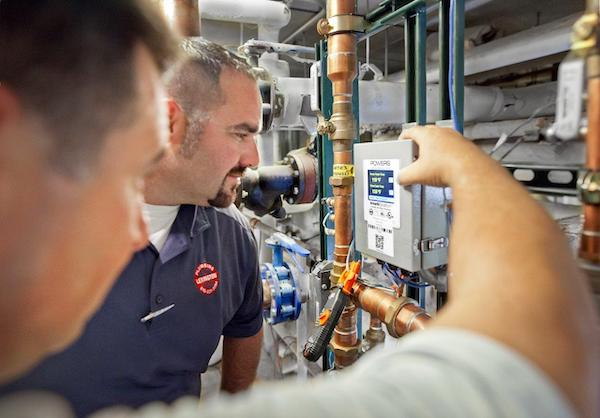
There are three main technology-driven components in a digital mixing solution:
- Sensors, serving as eyes and ears
- The controller’s algorithm (the “mind”)
- Electronic, high-speed actuated valve, continually responds to sensor inputs, to maintain set point
“Our digital mixing controller algorithm processes data from the mixed temperature outlet sensor and signals the actuator to make adjustments to maintain set-points in real time,” continued Fathers. “Sensors relay key system data for pressure, temperature and flow for troubleshooting and optimization.”
Building automation systems give facility managers the ability to see vital data, quickly make informed decisions, and act, even remotely. Digital water mixing controls hot water delivery through a programmable valve or system that processes temperature, flow, and pressure data.
Serious risks, such as Legionella growth, scalding, and thermal shock are associated with mismanaged water temperature. Legionella bacteria are destroyed almost instantly at water temperatures above 160°F, but at temperatures between 70°F and 115°F, their growth is abundant. The Catch 22 is that uncontrolled and unmonitored water distribution systems can create high-temperature scalding hazards in bathtubs, sinks, and showers.
A proactive monitoring program can help reduce risks, predict trends, and improve operational efficiency. Proactive monitoring enables three key control measures that help address modern-day public safety risks:
- Allows for quick decisions based on real data
- Allows facility managers to more easily manager their systems
- Generates automatic reports showing trends and performance
Fortunately, there’s no Catch 22 to the use of BACnet technology. It facilitates fast, reliable communications between all facets of the network it operates in. Watts and its brands rely on BACnet for many operational uses, successfully, and with no compromise.
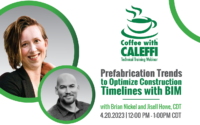
Skilled labor shortages and time-consuming on-site logistics can wreak havoc on construction schedules. Prefabrication is an effective option to expedite projects while maintaining favorable labor investments. BIM (Building Information Modeling) technology can boost the prefabrication advantages even further. Jisell Howe, CDT and Brian Nickel will present to the audience an overview of the current status and future of 3D Read more
Skilled labor shortages and time-consuming on-site logistics can wreak havoc on construction schedules. Prefabrication is an effective option to expedite projects while maintaining favorable labor investments. BIM (Building Information Modeling) technology can boost the prefabrication advantages even further. Jisell Howe, CDT and Brian Nickel will present to the audience an overview of the current status and future of 3D modeling, fabrication, and execution within the plumbing and heating sectors.
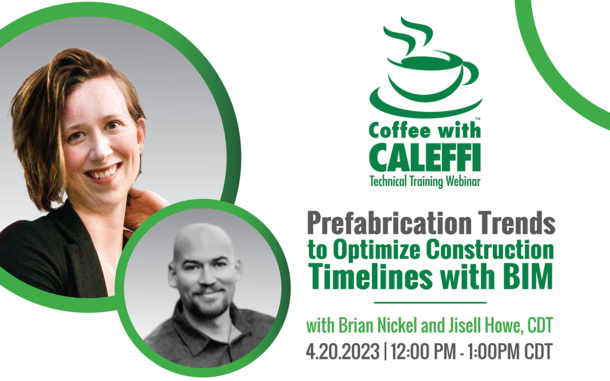
You’ll learn:
→ Best practices in BIM design
→ Prefabrication project success stories
→ Avoiding the software technology / real world disconnect
→ Revit design benefits for installers
→ What’s next in BIM?
Howe is the Senior BPM Platform Integration Manager for ENGworks Global. Her background in manufacturing is pivotal for managing BIM content creation projects for clients. She pushes the AEC Industry (Architecture, Engineering and Construction) forward by bridging gaps between construction design technology and manufactured products.
Nickel is the CEO/Founder of Allied BIM. He is a Virtual Design and Construction Manager with expertise in managing the use of building information models for architecture, engineering, and construction projects. He is also Adjunct Faculty (Revit) for Gallatin College and Montana State University College of Engineering – Construction Engineering Technology.
Coffee with Caleffi technical training webinars are free and intended for contractors, engineers, designers and wholesalers. By submitting your webinar registration, you are consenting to email communications to keep you up-to-date on industry news.
It’s easy to join us! Simply register today.
A Certificate of Attendance is emailed to attendees following the webinar equivalent to 1.0 PDH for continuing education. Please verify with your state/province for fulfillment compliance.