Artificial Intelligence (AI), digital twin, VR & AR, hydrogen fuel—all technologies pointing to the future of the plumbing industry. It’s really no wonder that the circulator industry—with the addition of Bluetooth-enabled technology and accompanying apps, for example, is moving into the 21st century as well. Couple that with US DOE mandates for efficiency, and you Read more
Featured Articles
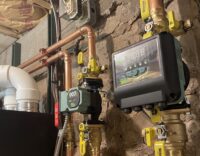
Artificial Intelligence (AI), digital twin, VR & AR, hydrogen fuel—all technologies pointing to the future of the plumbing industry. It’s really no wonder that the circulator industry—with the addition of Bluetooth-enabled technology and accompanying apps, for example, is moving into the 21st century as well. Couple that with US DOE mandates for efficiency, and you have the perfect storm of advancement. According to Taco’s John Barba, Director, Sales, Training, North America, the U.S. Department of Energy is tentatively setting mid-2025 as the date that mandated minimum circulator efficiency standards will be implemented. What that means on the specified date, manufacturers like Taco, Grundfos, Xylem, and others will no longer be able to manufacture and sell circulators that don’t meet a minimum efficiency standard.
“That doesn’t necessarily mean ECM technology, but as of right now Electronically Commutated Motor (ECM) is the only technology we have available that meets those standards; ECM is undoubtedly the direction our industry is going,” says Barba.
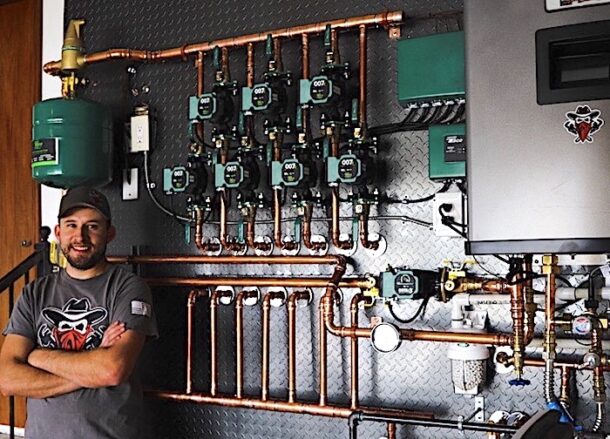
Keefer Rader, Outlaw Mechanical
According to Keefer Rader, owner, Outlaw Mechanical, Albuquerque, ECM will be the future as standard motor technology will no longer meet energy efficiency criteria. “I don’t know if Bluetooth technology will be the future, but it sure is nice to be able to monitor the equipment. I think Bluetooth and Wi-Fi technology will be a must for building management system (BMS) in our state.”
But by moving pumps and circulators into the “digital age,” some would ask, “why bother?” and “if it ain’t broke, why fix it?” “That’s an excellent question,” says Barba. “Part of me thinks back to something Henry Ford said a long, long time ago. ‘If you keep doing what you’ve been doing, you’ll keep getting what you’ve been getting.’ That’s the flipside to ‘If it ain’t broke, don’t fix it.’ The ‘if it ain’t broke’ idea is hard to argue with, but that doesn’t mean things can’t be made better, more efficient and more effective. After all, if good enough was truly good enough, we’d still be dealing with coal boilers and fireplaces. Those weren’t broke, either,” suggests Barba.
According to Barba, the fundamental truth is that building a hydronic system, putting pipe together so the water stays on the inside, connecting it to a boiler and having it make fire so people don’t freeze to death isn’t all that hard to do. A reasonably competent handyman could probably pull it off. But what makes a professional a professional is his or her ability to not only keep people from freezing to death, but to also create a system where the whole is greater than the sum of the parts; where the whole is designed to operate at peak efficiency and provide years of trouble-free operation. Variable-speed ECM circulators, when properly programmed and installed, are great tools to help achieve that goal.
“Of course, Henry Ford also said that he saw no advantage in new clocks” says Barba. “They run no faster than the ones made 100 years ago.” But again, it’s important to remember what we’re trying to accomplish. “Heck, cast iron boilers aren’t ‘broke,’ and they’re certainly less expensive, but modulating condensing boilers are more common now than ever before in residential hydronics. They’ve become ‘standard.’
“However, it makes zero sense to install a high-efficiency modulating condensing boiler and then not installing the outdoor sensor or enabling the outdoor reset. Even if the boiler has to run up to 180 degrees for fin-tube baseboard, it can still modulate and reset the water temperature as it gets warmer outside. Not doing so is basically wasting your customer’s money. “
By the same token, says Barba, all of the components you install with that modulating-condensing boiler—or even a cast-iron boiler, for that matter—should be purpose-chosen, meaning they are specifically selected in order to enhance the overall performance of the system—to make the whole greater than the sum of the parts.
“One thing variable speed technology has taught the industry is that the circulator plays a bigger role in overall system efficiency than we’ve ever given it credit for,” says Barba. “Sure, the boiler makes the heat, and sure, the heat emitters deliver the heat. But it’s the circulator that facilitates the journey. If we are overpumping, and even with ECM technology, we’re almost always overpumping, we’re limiting the overall performance and efficiency of the system, not enhancing it. A typical three-speed, standard efficiency circulator is almost always set to high speed or, as we like to call it, ‘contractor no-callback mode.’
“On the one hand, unless there’s velocity noise, there’s no immediate downside to doing so. However, pumping 5 gallons per minute through a zone that only needs 2 gallons per minute under design conditions means you’re pumping at a rate 2.5 times more than is required. In a perfect world, you’d have a 20-degree Delta-T under design conditions, but in this example, the best Delta-T you’ll ever see in that system is 8 degrees. That would mean with a mod-con boiler sending out 140-degree water on the coldest day of the year, the return water temperature would be about 132. We’re not condensing nearly as much as we could be, and we’re leaving an awful lot of efficiency on the table, but no one will complain about being cold.”
“Cavemen! I don’t understand why people are afraid of new things,” shouts Rader. “I’m a big proponent because I know Taco tests everything stringently so I know when it comes out of the box, I’m not likely to have an issue with it. I love having four circulators on my truck that I can typically adapt to any system and make it more efficient and work better. The double 0015e, 0018e, vt2218—this is my favorite, because people can see data in front of their face and understand the value—and 0026e.”
But Bluetooth?
As for Bluetooth technology and its associated app, it’s simply a way for an installer to make sure the ECM circulator he or she is using is, in fact, doing what he or she wants it to do. The myths and misinformation about ECM and variable speed technology that are common in our industry are astounding, says Barba. No, they do not size themselves and no, they do not always give you the right flow. What ECM and variable speed technology allows us to do is properly program a circulator so that it performs as close to what a system requires as possible. These things aren’t magic and they don’t “do the thinking for you,” or “take the thinking out of it.”
“You can’t just slap one of these things in, push a button and let it do the rest,” says Barba. “This isn’t the Hogwarts School of Hydronic Magic. ECM circulators don’t think and they aren’t magic. But what they are is obedient. They will do what you tell them to do – and the benefit of Bluetooth technology is it allows the installer to make sure a circulator—in Taco’s case the 0018e Delta-P technology circulator—operates as close to the actual system requirements as possible.”
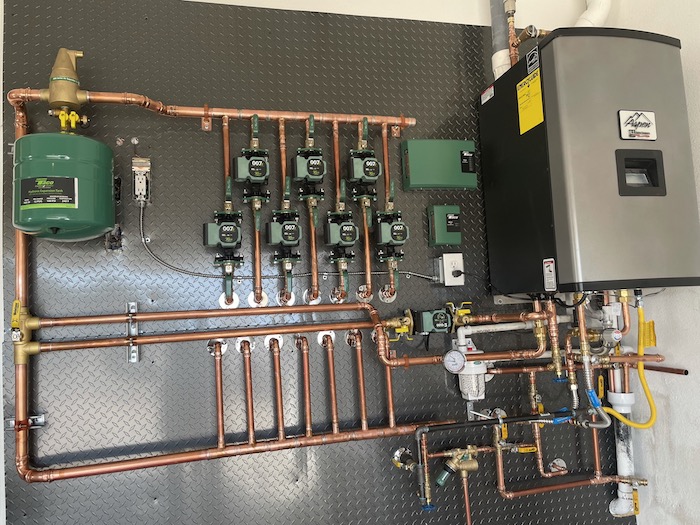
Additionally, residential hydronics has a chronic overpumping problem, continues Barba. Pick any residential hydronic system and chances are it’s WAY overpumped. Overpumping is one of those insidious problems—no one will ever complain about being cold, but over pumping means more GPM is being pumped through a zone or a system than it needs. When that happens, the system Delta-T is small and gets smaller as the outdoor temperature increases.
This isn’t supposed to happen and it’s not needed to make a system work, although you’ll hear people mistakenly make that claim. What a shrinking Delta-T does do is it sends warmer and warmer water back to the boiler. We don’t want that to happen at all with a modulating-condensing boiler, and we really don’t want it to happen with a cast iron boiler, either (as long as we’re above the condensing point). When that return water temperature is higher than necessary, boilers tend to short cycle and, in the case of a mod-con, it won’t “con” as much as it could. It’s almost impossible to quantify mathematically, but it’s reasonable and logical to presume that overall system efficiency (and fuel consumption) will suffer.
“And short-cycling doesn’t do any of the moving parts in a system any favors. It won’t take long for any key—and expensive—component in a mod-con boiler to fail prematurely. At that point, someone is left with some ’splaining to do,” says Barba.
Bluetooth technology has to be useful and hold value to the contractor, and that we’ll see about, says Barba. “What we’ve found in the five years we’ve had Bluetooth technology in the market is there are contractors who get the value right away, and others who question the value. That’s to be expected. When we show all of the capabilities of the circulator, show them how easy it is to set up the circulator to optimize system performance and—most importantly— what that optimization is important, we see more who see the value and fewer who question it,” says Barba.
“That said, we do see contractors who roll their eyes at the word ‘app’ and don’t want anything to do with it, and that’s fine. We have the VR 1816, which we’ve had since 2014, the 007e, which we’ve had since 2015, the 0015e3—which we’ve had since 2017 and the VT-2218, a Delta-T variable speed circulator that we’ve had since 2011. Different strokes, meet different folks.”
“I’ll tell you what I wish they put a small screen on the 0018. I really love this circulator because I can get real time data on my iPad and set a circulator to pretty much exactly what that zone needs,” says Rader. “I prefer to use them on zone pump systems. I also like to use them on the head scratcher systems so I can try to compile as much data as possible. A lot of times it becomes more of a tool than product.”
And beyond initial setup? “Initial setup isn’t just a throw-away item; it’s the most important element of using, and maximizing, variable speed circulators. And Bluetooth connectivity gives you stark visuals and really numbers of what it is you’re doing. As my co-trainer Dave Holdorf says, Bluetooth for the first time lets you see what’s actually happening inside the pipe. It’s real and it’s now knowable and quantifiable,” says Barba.
Added Costs?
Let’s face it, with new technology inevitably there’s going to be added costs. “There are added costs, but I have found when selling a new circulator—when I explain to the customer, the benefits of a properly sized circulator—that their buyback should be within a year. For instance, if I have a circulator that speeding up and slowing down based upon how many zones are opened or closed at that time, we are not wasting fuel. We are directing the heat at the proper speed to hit maximum efficiency,” says Rader.
People do ask all the time, “How do it sell this to my customer?” says Barba. There are two answers to that. The short one is if it’s a simple swap out—a new circulator for a dead one—it can simply be a matter of explaining these new circulators are much more electrically efficient than the standard models, use about half the electric and can make the system work better and more efficiently for the long haul. Often, that’s enough of an explanation.
If someone wants particular, the Hydraulics Institute has created labeling for ECM circulators that all of the major manufacturers have adopted, indicating relative efficiency ratings (the higher the number, the more efficient the circulator—although once you reach a certain point, the practical differences are minimal). By using a formula provided by the Hydraulics Institute, one can show how quickly the more efficient circulator will offset the higher purchase price— it’s usually within two, maybe three heating seasons.
If it’s a full boiler change out, the difference in price between a standard circulator or circulators compared to ECM circulators—in the overall picture of the job—isn’t huge and gives the contractor talking points as to why he or she has chosen specific circulators, and why it’s best for the system to do the job right. “I’ve had customers tell me that their customers aren’t asking for ECM technology, so there’s no market for them and besides, they’re too expensive. I’ll go with another Henry Ford quote: ‘If I’d asked people what they wanted, they’d have said ‘faster horses,’” says Barba.
Depending on where you live and work, Barba says, ECM circulators may actually be less expensive than standard efficiency circulators. Many states offer instant, at-the-counter rebates from utility companies to incentivize ECM adoption. It makes sense—if wider adoption of lower-wattage circulators takes place, that’s less of a load on the power grid. The utilities are simply buying efficiency—it’s no different than with light bulbs or other low-consumption appliances.
In non-rebate states, the comparative purchase cost is higher—anywhere from a little bit to a lot, depending on what you want for a particular job. We’ve had great success with the 007e and 0015e3—both variable speed Delta-P ECM circulators—that only have the features and operating parameters that people might need for a particular job. If you like 007s and want similar performance in an ECM circulator, the 007e is virtually identical in performance. The 0015e3 is a seamless transition from your typical 3-speed circulator and works great with zone valves or as a zone pump. The multi-feature, multi-function circulators offer more features, but that comes at a higher purchase price.
Ultimately, ECM, variable speed and Bluetooth technology isn’t a matter of making the water go round-and-round the pipes better, says Barba. It’s simply a matter of using the latest technology to make sure a key part of the system is doing its job to ensure that system is working as efficiently and effectively as possible, ensuring the system itself remains as trouble-free as possible for as long as possible, and that the customer is getting the most out of what they’re paying for. “We’re all consumers in one way or another, and none of us want to pay top dollar and then get only 80 percent of what we’re paying for.”
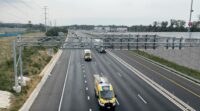
From MyPlumber.com A remarkable sight unfolded on June 16, 2023 as a multitude of My Plumber Plus trucks lined Route 66 forming a powerful symbol of homage and respect to pioneering local businessman, R. Wendell Presgrave. The convoy, driven by My Plumber Plus plumbers, HVAC service experts and electricians, was a display of admiration and Read more
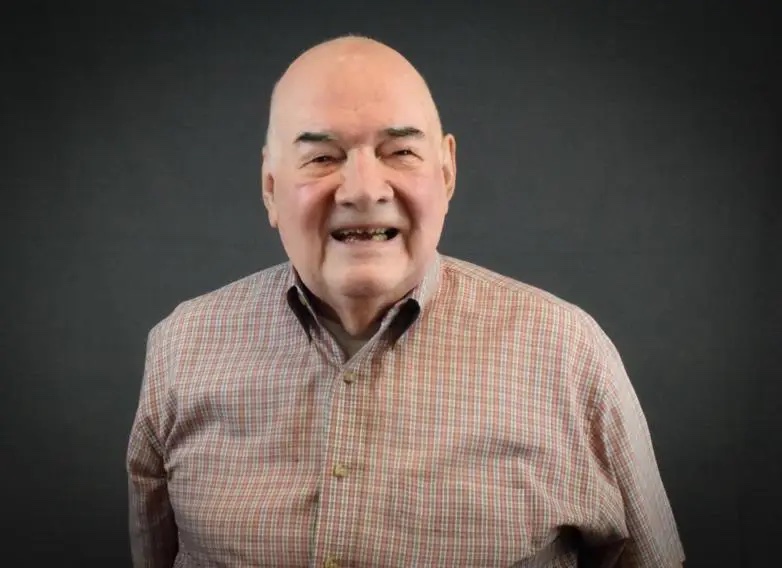
Wendell Presgrave
From MyPlumber.com
A remarkable sight unfolded on June 16, 2023 as a multitude of My Plumber Plus trucks lined Route 66 forming a powerful symbol of homage and respect to pioneering local businessman, R. Wendell Presgrave. The convoy, driven by My Plumber Plus plumbers, HVAC service experts and electricians, was a display of admiration and appreciation for their company Founder.
Wendell’s passion for plumbing, customer centric focus, and strong work ethic can be traced back to 1968 when he began as a parts runner for Griffin Plumbing. After earning his Masters in Plumbing license, he started his first company in 1975, Courthouse Plumbing, which he sold in 1982 and begin My Plumber, later named My Plumber Plus due to the addition of HVAC and electrical services. His innovative “Same Day Service Guaranteed” promise became a trendsetter.
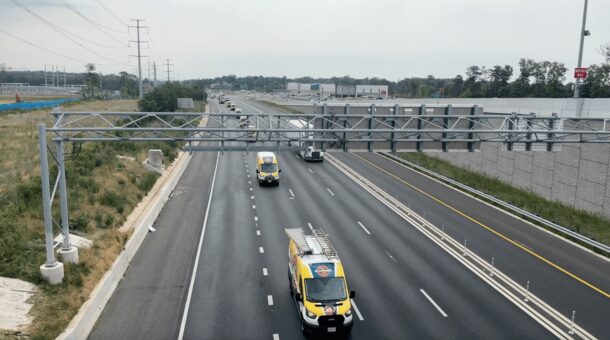
Wendell went on to be a 4 times past President of the Virginia PHCC (Plumbing Heating Cooling Contractors Association), and to earn many awards alongside his son and business partner, Mark Presgrave, including PHC News Magazine Top 100 Contractors of the year, Washington Business Journal Top Contractor, Prince William County Business Excellence Award, PM Plumbing & Mechanical Best Contractor to Work For, and Leader of Nexstar‘s Top 10 Overall Selective Service Companies, to name a few.
My Plumber Plus has employed over 2000 people and served hundreds of thousands of customers in Virginia, Maryland and even San Diego, CA where a West Coast office was opened in 1999. While Wendell’s business accolades are well-deserved, those who worked with him say he was quick to give the credit to his My Plumber Plus team. Wendell had an abundance mentality, believing that there was an abundance of opportunity out there for his company and others. He openly shared his insights and actively helped others in the business community succeed.
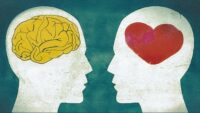
Keep your technical knowledge close in the tool bag; emotional intelligence is a highly valued personal trait that can help you run a more successful business. We’ve all heard the expression before, “You’re thinking with you heart and not your head.” But what if both were true? On a recent Thursday night Plumbing Perspective (@plumbing_perspective) Instagram Read more
Keep your technical knowledge close in the tool bag; emotional intelligence is a highly valued personal trait that can help you run a more successful business.
We’ve all heard the expression before, “You’re thinking with you heart and not your head.” But what if both were true? On a recent Thursday night Plumbing Perspective (@plumbing_perspective) Instagram Live, guest Shreya Nagwani (@_shreymvp), sales/service expert and coach for Service MVP, discussed an interesting aspect of Service MVP’s training that translates to running a successful business. It’s called Emotional Intelligence or EQ. Almost counterintuitive—because of the opposite nature of how people can think one way and act another—the term actually makes an abundant amount of sense.
According to Harvard Business School, Emotional intelligence is defined as the ability to understand and manage your own emotions, as well as recognize and influence the emotions of those around you. The term was first coined in 1990 by researchers John Mayer and Peter Salovey, but was later popularized by psychologist Daniel Goleman. (Goleman lists five components of EQ below.)
In the realm of home service sales, emotional intelligence (EQ) often takes a backseat to technical expertise. However, it is a critical component that should not be overlooked. EQ refers to the ability to understand and manage emotions effectively, enabling individuals to relieve stress, communicate well, empathize, overcome challenges, and defuse conflicts. In the sales process, where emotions heavily influence buying decisions, focusing on logical reasoning alone can leave clients hesitant.
But how does it translate into plumbing and HVAC business? While plumbing and HVAC techs have a high IQ, and what they communicate is overly technical, a non-technician, i.e., customer, doesn’t understand what that means, says Nagwani. “All they want is safety, comfort and health for their family and their home.”
Home service technicians, typically analytical and left-brained, tend to prioritize the logical aspects of their work, inadvertently neglecting the emotional side of the sales process. The gap lies in the lack of training on communicating solutions in an emotionally intelligent manner. To successfully bridge this gap, technicians must be equipped with the skills to connect with customers on a deeper level, understand their unique needs, and present solutions that resonate emotionally.
“It’s a very emotional job,” says Nagwani, but there is a gap. “To bridge the gap would be learning emotional intelligence. How do I communicate this job, which is just a plumbing job, to something like, ‘What is the effect of this system for their family? If they have chlorine in their water and their son has eczema.’ That’s how you connect emotional intelligence to a plumbing job,” says Nagwani.
And, not only that, people buy things when they have high self-esteem, when they feel like they deserve it. “People who have a high self-esteem buy premium,” says Nagwani.
How do to techs learn how to communicate that? “What we teach—in part—in our Service MVP offerings is, how do you raise someone’s self-esteem during a visit that by the end of the appointment the client feels better about themselves as a person? What happens is they’ll pick an option,” says Nagwani. “‘I deserve endless hot water,’ for example, connecting a technician’s job over to emotional intelligence.”
Moreover, sometimes it can be difficult exude confidence, stability, empathy on a tremendously busy schedule. “It’s confidence. Even if it’s not a lack of confidence, it comes off that way. This also goes to managers and owners. If your’re giving your guys six or seven calls on the board, they would see all of the calls stacked up and it would really affect the way they ran those calls and they would burn through all of them. They are just thinking of getting in and out. That is going to affect the service to the client, the job, the revenue and the happiness of the technician.
“We have a rule where a technician can see only one call at a time and they get a long time on that call. They have all the time they need; it’s quality over quanitity. What starts to happen is, there are less upset clients, there are more 5-star reviews, they triple their revenue, literally. The confidence of the technician is really important. How is somebody going to be confident when they don’t have communications training?” says Nagwani.
By incorporating emotionally intelligent communication techniques, technicians can establish a stronger connection with customers. Understanding and addressing customers’ emotions not only builds rapport but also allows for customized solutions that meet their specific needs. Training programs, such as those offered by Service MVP, specialize in teaching teams to utilize emotionally intelligent approaches. Implementing these techniques can lead to a significant increase in revenue per technician, averaging at 297%. This approach enhances customer satisfaction, improves conversion rates, and fosters long-term customer loyalty.
Goleman’s 5 Components of EQ
- Self-Awareness: Recognizing and understanding your own strengths and weaknesses, your emotions and moods, and the effects these things have on other people. A self-aware person is not easily offended by criticism, but rather learns and adapts.
- Self-Regulation: To think before doing and to express your feelings maturely with restraint. Rather than being controlled by emotions and impulses, an emotionally intelligent person can control impulses and emotional responses.
- Internal Motivation: High EQ people are self-motivated, pursuing personal goals for reasons of self-development and self-gratification, rather than money, titles, external praise or esteem.
- Empathy: Empathy involves recognizing, understanding and feeling the emotions of others. Unlike sympathy, empathy involves actually sharing the emotional experience another person is having. Empathetic people genuinely understand and respond to the needs of others.
- People Skills: Emotionally intelligent people easily build trust and respect with others. They are good at managing relationships and building networks, and they avoid power struggles and deceitfulness. Their high levels of the first four components of EQ make for deep bonds and genuine, non-competitive friendships.
Source: Forbes.com
Service MVP is an e-learning website featuring video-based micro-learning content designed to revolutionize your office, service, sales and install teams. It is the ultimate service sales training resource, where high performers increase the value of their solutions to create higher revenue and profit.
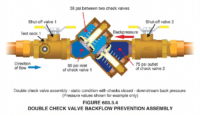
From the 2021 UPC Illustrated Training Manual, Chapter 6, WATER SUPPLY AND DISTRIBUTION 603.3.4 Double Check Valve Backflow Prevention Assembly (DC). A double check valve backflow prevention assembly consists of two independently acting internally loaded check valves, four properly located test cocks, and two isolation valves. The double check valve backflow prevention assembly (DC) is Read more
From the 2021 UPC Illustrated Training Manual, Chapter 6, WATER SUPPLY AND DISTRIBUTION
603.3.4 Double Check Valve Backflow Prevention Assembly (DC). A double check valve backflow prevention assembly consists of two independently acting internally loaded check valves, four properly located test cocks, and two isolation valves.
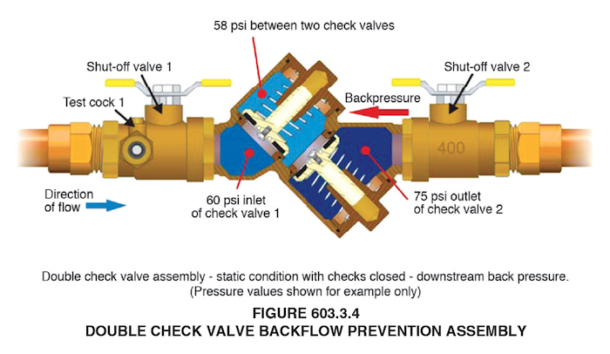
The double check valve backflow prevention assembly (DC) is just what it says – two check valves in series to prevent backflow (see Figure 603.3.4). The first check will close in a backflow condition. Usually one psi of backflow pressure will close the check. The second check is incorporated as a backup if the first check fails; however, there is no way to know if the second check has failed until it is tested. If the device fails, there is no means for removal of the polluted or contaminated water, which may then travel into the potable line. Therefore, the DC may only be used on low-hazard applications. Any liquid connected to the piping downstream of a DC should be a pollutant and not a contaminant.
The DC provides backpressure and backsiphonage protection. A DC may be used as meter-service protection as a containment, or on individual fixtures and appliances as isolation protection. A field test is required on installation, at least annually thereafter, after any repair and when relocated. The device must be installed a minimum of 12 inches above the surrounding ground or floor.
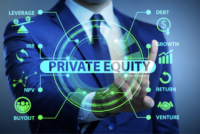
Over the past few years—wink, wink COVID—the industry has seen a rise in purchasing activity between plumbing and HVAC companies and private equity firms and other outside influences—coming in and gobbling up already successful contracting shops with a message of making them better. Sure, it’s a smart exit strategy as well for those looking to Read more
Over the past few years—wink, wink COVID—the industry has seen a rise in purchasing activity between plumbing and HVAC companies and private equity firms and other outside influences—coming in and gobbling up already successful contracting shops with a message of making them better. Sure, it’s a smart exit strategy as well for those looking to hang up the wrenches.
But why the flurry of activity now? “What we’ve seen from COVID is that the trades are pandemic-proof and to some extent recession proof. When money gets tight, consumers may hold off on that new car, going out to eat, but when that water heater goes out, it’s a necessity,” says Dan Foley, Foley Mechanical, Lorton, Va.
Foley continues, “Artificial Intelligence (AI) will never be able to take over this industry. You will always need someone to walk into someone’s home and make a repair, and that’s not easy to do. It’s the technician’s skill that AI cannot replace.”
According to Mike Prencavage Jr., president/owner, The Family Plumber, Los Alamitos, Calif., president, PHCC ORSB, director, PHCC National Business Development, “Working on margins is crucial for any business to succeed; however, in the plumbing industry most companies aren’t struggling with tight margins to turn a profit.”
As an example, Prencavage Jr. says restaurants and bars can stand to lose greatly if more than two ounces of alcohol is poured into any drink or if larger than accounted for portions of food are served on any plate. These private equity firms have seen that plumbing companies have a greater amount of sold labor income per invoice that can offset losses on jobs allowing for much wider margins to run a profitable business.
“Private equity firms are also looking to the future of renewable energy. With the electrification of the nation soon to be at every state’s doorstep, government grant funding has already become available to plumbing companies who are leading the way by installing energy efficient products. These grant programs. combined with the opportunity to capitalize on wider margins, are creating a buzz of interest from private equity groups to get more involved in the plumbing industry sector,” says Prencavage Jr.
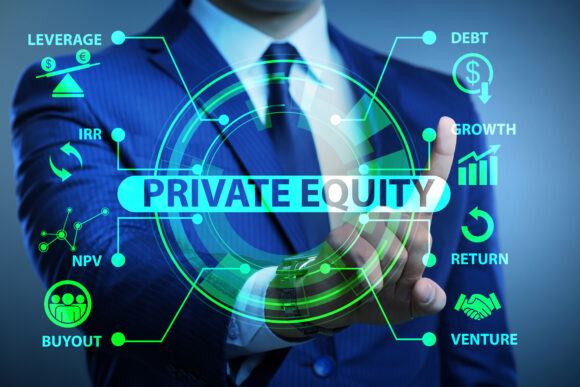
Speaking of grants, on a national level, the Infrastructure Bill and Inflation Reduction Act, are ripe for the taking, if eligible.
On the flipside, private equity firms offer contractors security, not only monetarily, but though the expansion of their reach and service offerings across their respective regions, expand evolving customer bases and refine overall strategic growth initiatives.
Just last month, Grove Mountain Partners—a private equity firm investing in lower, middle market home service companies and specialty business service companies—announced the sale of Unique Indoor Comfort Holdings LLC to Ace Hardware. Nate Kukla, CEO, and the entire management team, including the brand presidents, will continue to lead the company as it embarks on its next growth phase.
Grove Mountain brought together 12 independent service-providing businesses, beginning in June 2021, with the acquisition of three related companies: Moncrief Heating & Air, Unique Indoor Comfort of Philadelphia, and Werley Heating & Air. It added nine other companies in the Eastern region of the U.S., including Clay’s Climate Control, Detmer & Sons, Canella Heating & Air, A-Total Plumbing, All Phase Electrical, Dick Hill & Son, Carolina Custom, Rye Heating and Air, and Jackson Plumbing and Heating & Air.
“We are grateful for our partnership with Grove Mountain and are proud of what we have built and accomplished,” said Nate Kukla, CEO. “Now, we are excited to be part of the Ace team which will allow us to leverage their combined financial and operational capabilities and expertise. Since day one, Unique has been passionately dedicated to an employee-centric, high-integrity, and customer-focused culture. Ace shares in our mission and values and brings a plethora of resources to allow us to continue and grow the business.”
Also, this month, Auctus Capital Partners—a leading financial services and investment banking firm focused exclusively on creating value for the lower middle market, which specialize in merger and acquisition advisory, institutional private placements of debt and equity, financial restructuring, valuation, and strategic consulting—announced its role as exclusive advisor to The Precision Group and its affiliated entities, supporting the environmental and infrastructure services leader in completing a majority recapitalization by PowerVac, a Pillsman Partners LLC and Peninsula Capital Partners, LLC portfolio company.
The Precision Group is comprised of three separate yet complementary companies that serve a diverse array of commercial, industrial, and municipal customers. Founded in 1992, Precision Industrial Maintenance, Inc. provides environmental remediation, industrial cleaning services, hazardous and non-hazardous waste transport and disposal, and other industrial waste services. Martin Environmental Services, Inc. was acquired by Precision Group in 2002, adding new services in asbestos and lead abatement, and disposal services. Precision Trenchless, LLC was formed in 2013 to focus on environmentally-friendly pipe rehabilitation using less disruptive technologies, such as UV-Cured and other Cured-in-Place Pipe Lining (CIPP) methods, potable water line rehab to minimize air, water and soil pollution and support advanced monitoring services.
The group of companies operate as a unified provider of services to several broad regional markets with strong projected growth through 2026 — including the sewer and pipeline rehabilitation market with a compound annual growth rate (CAGR) of 4.6%, as well as trenchless pipe rehabilitation (4.8% CAGR), and liquid waste management (3.7% CAGR).
“Underpinned by significant government support for the repair of aging infrastructure, pipeline rehabilitation and wastewater management services are seeing record investment. In addition, an ever-growing awareness of ESG issues has been driving strong investor demand,” says Muhammed Azfar, CEO and managing partner, Auctus.
More to come on this topic.