From the 2021 UPC Illustrated Training Manual, Chapter 6, WATER SUPPLY AND DISTRIBUTION 603.3.4 Double Check Valve Backflow Prevention Assembly (DC). A double check valve backflow prevention assembly consists of two independently acting internally loaded check valves, four properly located test cocks, and two isolation valves. The double check valve backflow prevention assembly (DC) is Read more
Featured Articles
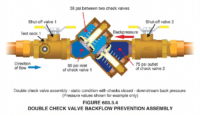
From the 2021 UPC Illustrated Training Manual, Chapter 6, WATER SUPPLY AND DISTRIBUTION
603.3.4 Double Check Valve Backflow Prevention Assembly (DC). A double check valve backflow prevention assembly consists of two independently acting internally loaded check valves, four properly located test cocks, and two isolation valves.
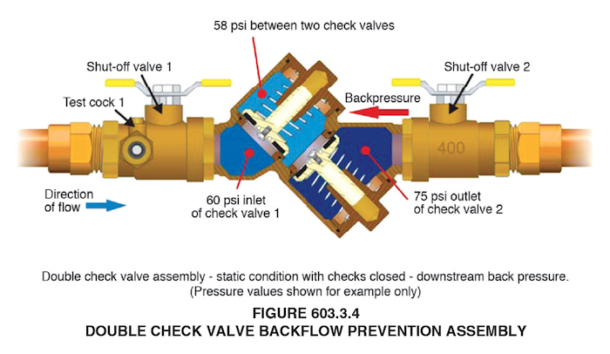
The double check valve backflow prevention assembly (DC) is just what it says – two check valves in series to prevent backflow (see Figure 603.3.4). The first check will close in a backflow condition. Usually one psi of backflow pressure will close the check. The second check is incorporated as a backup if the first check fails; however, there is no way to know if the second check has failed until it is tested. If the device fails, there is no means for removal of the polluted or contaminated water, which may then travel into the potable line. Therefore, the DC may only be used on low-hazard applications. Any liquid connected to the piping downstream of a DC should be a pollutant and not a contaminant.
The DC provides backpressure and backsiphonage protection. A DC may be used as meter-service protection as a containment, or on individual fixtures and appliances as isolation protection. A field test is required on installation, at least annually thereafter, after any repair and when relocated. The device must be installed a minimum of 12 inches above the surrounding ground or floor.
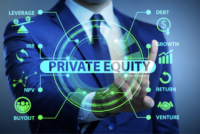
Over the past few years—wink, wink COVID—the industry has seen a rise in purchasing activity between plumbing and HVAC companies and private equity firms and other outside influences—coming in and gobbling up already successful contracting shops with a message of making them better. Sure, it’s a smart exit strategy as well for those looking to Read more
Over the past few years—wink, wink COVID—the industry has seen a rise in purchasing activity between plumbing and HVAC companies and private equity firms and other outside influences—coming in and gobbling up already successful contracting shops with a message of making them better. Sure, it’s a smart exit strategy as well for those looking to hang up the wrenches.
But why the flurry of activity now? “What we’ve seen from COVID is that the trades are pandemic-proof and to some extent recession proof. When money gets tight, consumers may hold off on that new car, going out to eat, but when that water heater goes out, it’s a necessity,” says Dan Foley, Foley Mechanical, Lorton, Va.
Foley continues, “Artificial Intelligence (AI) will never be able to take over this industry. You will always need someone to walk into someone’s home and make a repair, and that’s not easy to do. It’s the technician’s skill that AI cannot replace.”
According to Mike Prencavage Jr., president/owner, The Family Plumber, Los Alamitos, Calif., president, PHCC ORSB, director, PHCC National Business Development, “Working on margins is crucial for any business to succeed; however, in the plumbing industry most companies aren’t struggling with tight margins to turn a profit.”
As an example, Prencavage Jr. says restaurants and bars can stand to lose greatly if more than two ounces of alcohol is poured into any drink or if larger than accounted for portions of food are served on any plate. These private equity firms have seen that plumbing companies have a greater amount of sold labor income per invoice that can offset losses on jobs allowing for much wider margins to run a profitable business.
“Private equity firms are also looking to the future of renewable energy. With the electrification of the nation soon to be at every state’s doorstep, government grant funding has already become available to plumbing companies who are leading the way by installing energy efficient products. These grant programs. combined with the opportunity to capitalize on wider margins, are creating a buzz of interest from private equity groups to get more involved in the plumbing industry sector,” says Prencavage Jr.
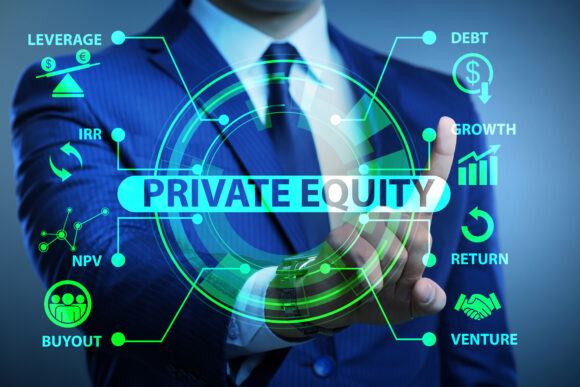
Speaking of grants, on a national level, the Infrastructure Bill and Inflation Reduction Act, are ripe for the taking, if eligible.
On the flipside, private equity firms offer contractors security, not only monetarily, but though the expansion of their reach and service offerings across their respective regions, expand evolving customer bases and refine overall strategic growth initiatives.
Just last month, Grove Mountain Partners—a private equity firm investing in lower, middle market home service companies and specialty business service companies—announced the sale of Unique Indoor Comfort Holdings LLC to Ace Hardware. Nate Kukla, CEO, and the entire management team, including the brand presidents, will continue to lead the company as it embarks on its next growth phase.
Grove Mountain brought together 12 independent service-providing businesses, beginning in June 2021, with the acquisition of three related companies: Moncrief Heating & Air, Unique Indoor Comfort of Philadelphia, and Werley Heating & Air. It added nine other companies in the Eastern region of the U.S., including Clay’s Climate Control, Detmer & Sons, Canella Heating & Air, A-Total Plumbing, All Phase Electrical, Dick Hill & Son, Carolina Custom, Rye Heating and Air, and Jackson Plumbing and Heating & Air.
“We are grateful for our partnership with Grove Mountain and are proud of what we have built and accomplished,” said Nate Kukla, CEO. “Now, we are excited to be part of the Ace team which will allow us to leverage their combined financial and operational capabilities and expertise. Since day one, Unique has been passionately dedicated to an employee-centric, high-integrity, and customer-focused culture. Ace shares in our mission and values and brings a plethora of resources to allow us to continue and grow the business.”
Also, this month, Auctus Capital Partners—a leading financial services and investment banking firm focused exclusively on creating value for the lower middle market, which specialize in merger and acquisition advisory, institutional private placements of debt and equity, financial restructuring, valuation, and strategic consulting—announced its role as exclusive advisor to The Precision Group and its affiliated entities, supporting the environmental and infrastructure services leader in completing a majority recapitalization by PowerVac, a Pillsman Partners LLC and Peninsula Capital Partners, LLC portfolio company.
The Precision Group is comprised of three separate yet complementary companies that serve a diverse array of commercial, industrial, and municipal customers. Founded in 1992, Precision Industrial Maintenance, Inc. provides environmental remediation, industrial cleaning services, hazardous and non-hazardous waste transport and disposal, and other industrial waste services. Martin Environmental Services, Inc. was acquired by Precision Group in 2002, adding new services in asbestos and lead abatement, and disposal services. Precision Trenchless, LLC was formed in 2013 to focus on environmentally-friendly pipe rehabilitation using less disruptive technologies, such as UV-Cured and other Cured-in-Place Pipe Lining (CIPP) methods, potable water line rehab to minimize air, water and soil pollution and support advanced monitoring services.
The group of companies operate as a unified provider of services to several broad regional markets with strong projected growth through 2026 — including the sewer and pipeline rehabilitation market with a compound annual growth rate (CAGR) of 4.6%, as well as trenchless pipe rehabilitation (4.8% CAGR), and liquid waste management (3.7% CAGR).
“Underpinned by significant government support for the repair of aging infrastructure, pipeline rehabilitation and wastewater management services are seeing record investment. In addition, an ever-growing awareness of ESG issues has been driving strong investor demand,” says Muhammed Azfar, CEO and managing partner, Auctus.
More to come on this topic.
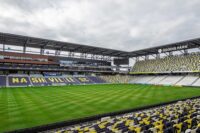
Opened in May 2022, GEODIS Park is one of the premier sports and entertainment destinations in the country. Home to Major League Soccer’s Nashville SC, the 30,000-seat stadium is the largest soccer stadium in the United States and Canada. Sustainability is important to Major League Soccer and its fans, so GEODIS Park set out to Read more
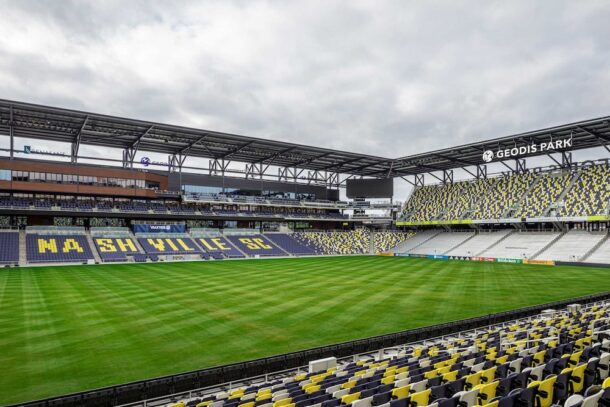
Sustainability is important to Major League Soccer and its fans, so GEODIS Park set out to feature products that not only help the environment, but also look and feel good to fans, patrons, and employees. That’s why the park specified a variety of products from Sloan—a one-stop shop of fixtures that save water, promote hygiene, and offer enhanced aesthetics throughout the restroom.
“The entire process was seamless,” said Dan Farrell, Vice President, Corporate Partnerships, Nashville Soccer Club. “The Sloan products were exactly what we were looking for. It was, from start to finish, a nice, smooth process.”
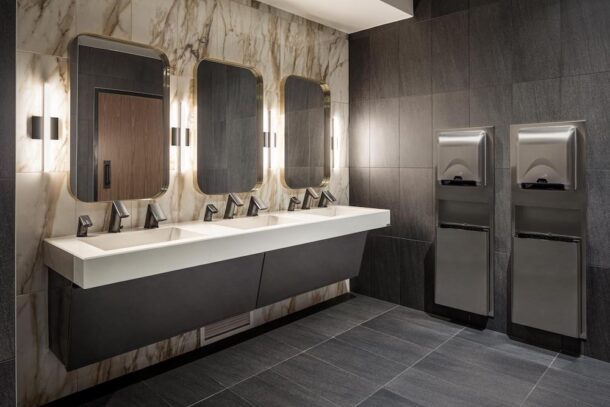
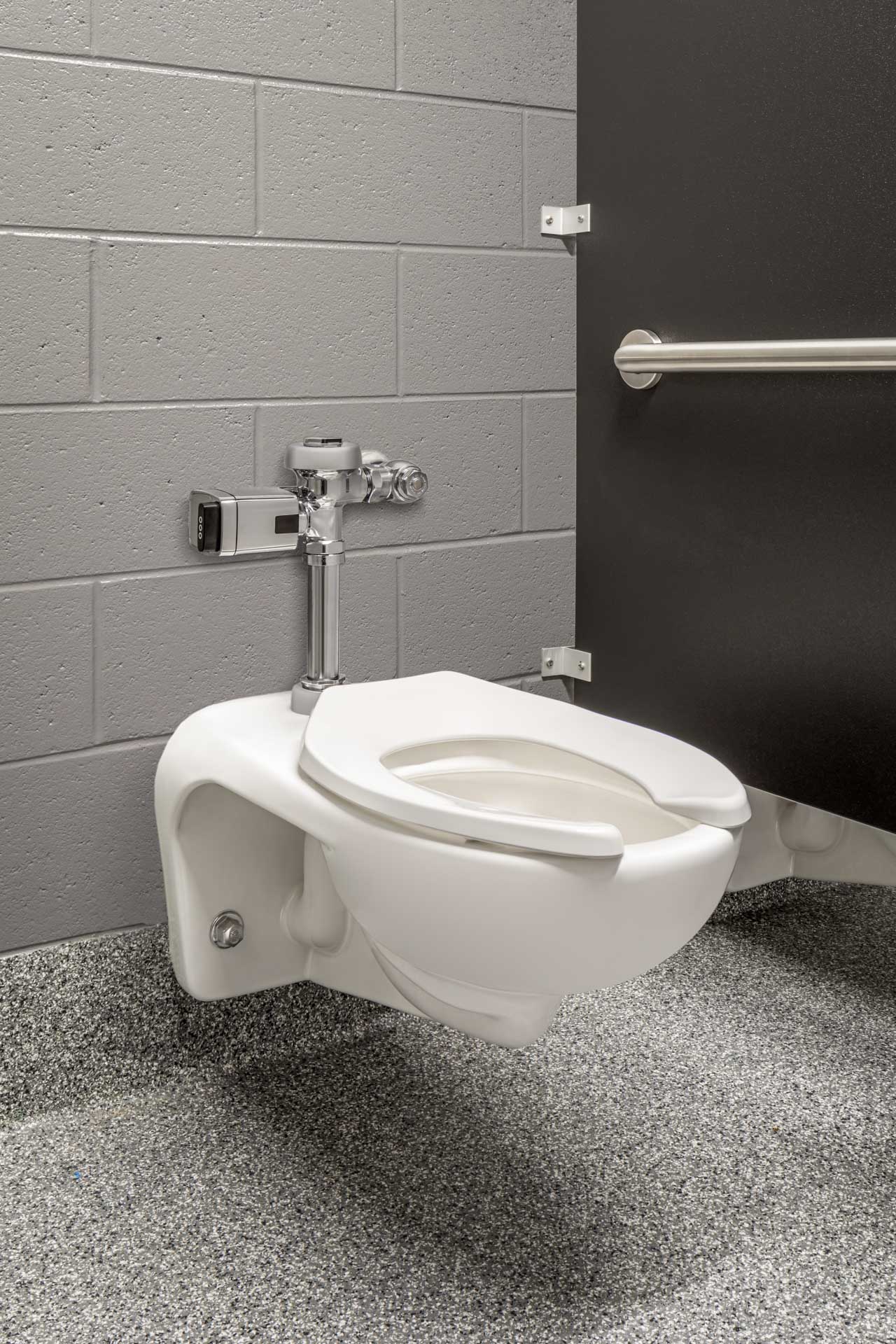
Keeping it Clean
Best of the Best
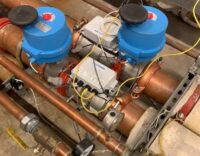
According to the EPA, residential leaks—not including commercial water leakage in this country—wastes nearly 1 trillion gallons of water annually. It’s a widespread problem. Not long ago, Washington Post journalists wrote about a guy, Sam, who went to his rural vacation home south of Chicago. Following a long winter, he found the entire basement flooded with Read more
According to the EPA, residential leaks—not including commercial water leakage in this country—wastes nearly 1 trillion gallons of water annually.
It’s a widespread problem. Not long ago, Washington Post journalists wrote about a guy, Sam, who went to his rural vacation home south of Chicago. Following a long winter, he found the entire basement flooded with eight feet of water. It sat there for weeks because of a burst pipe. In such an instance—especially if the leak happened in the summer—the risk of mold, including the toxic Stachybotrys chartarum (black mold), is substantial.
Post reporters also wrote about a woman who lives on the 35th floor of a condo building. While she was out one day, the water to her drinking water filter broke. Half a day and many gallons of water later, she was able to stop the leak, but a lot damage had already been done: the water had cascaded down through several floors of the building, causing significant damage.
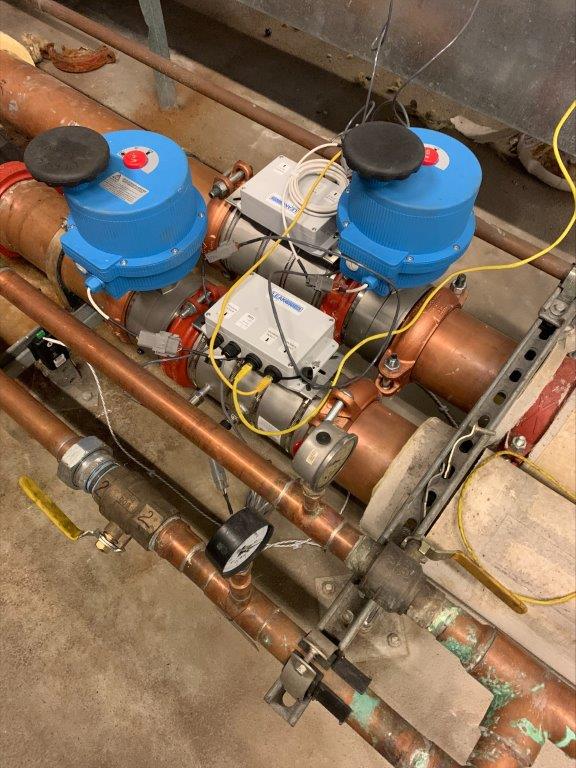
This combination of Sentinel Hydrosolutions Leak Defense System technology guards a penthouse mechanical room in a condo facility, including automatic shutoff valves connected to point-of-leak detectors protecting all water sources, including storage tank, water lines and booster pumps. Two large 6″ valves control all water in the building. Remote control emergency water shutoff is controlled a concierge desk. All images courtesy of Watts.
The ravages of water from hidden leaks can be devastating, expensive. Even permanent.
The good news is that today’s wireless technology can either alert you instantly that there’s a problem, or even shut off the water main automatically or remotely. Some of these devices sense water and send an audible alarm along with a text or email alert so whether you are home or away, you get the alert.
According to Kenneth Fox, VP of Sales and Business Development for Escondido, Calif.-based Leak Defense, a Watts Brand, there are a wide variety of solutions, some being far more durable and effective than others.
Says Fox, the best technologies, including the Leak Defense system, continuously monitor properties for hidden leaks and—if one is detected—automatically shuts off the water and alerts homeowners, property managers or plumbing professionals.
“We’ve found that an on-site control, or mobile app, are the best, easiest way to control water flow,” he added. “With multiple ways to monitor, you’ll always feel protected against potential loss, expense and hassle from water damage. Our full line of accessories allows Leak Defense to work with any type of residential or commercial plumbing system.”
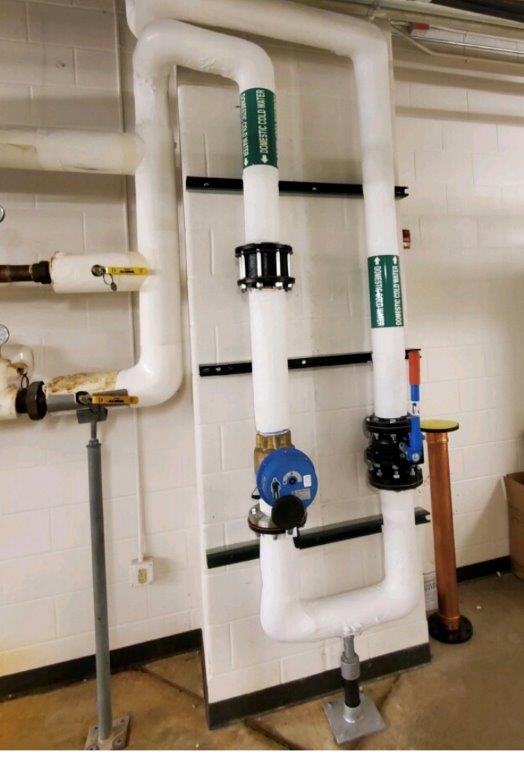
In Atlanta, a facility’s entire water service piping is leak-protected.
For commercial systems, leaks can very easily cause frustration among tenants and legal liabilities and lead to remediation hassles and great expense.
At the very least, not being protected from the risk of water damage from hidden leaks can be stressful. According to Fox, Leak Defense has helped thousands of commercial and multi-family building owners and facility managers easily monitor and protect their properties.
“With modern systems, the status of all leak detection components—from smart controls to sensors—should populate information on a convenient, user-friendly dashboard,” said Fox. “The technology should be capable of catching all types of leaks, including those hidden in under slabs, behind walls and in ceilings.”
Like a security system with ability to shut the door!
Contemporary leak detection and prevention systems should also be effective at turning off water automatically if flow settings are exceeded, or shut off water to selected zones or the entire building. They should also allow manual stopping of water via control or app, and provide round-the-clock monitoring and alarming of all devices—much like contemporary security systems, but with the added capability of shutting the shut the door to deny entry.
To have this remarkable capability, a Leak Defense valve must be installed on the main water line and downstream of the primary shut-off valve, pressure regulator, irrigation line and fire sprinkler line. All components “talk to each other,” with set parameters that allow total system shutoff if conditions warrant it.
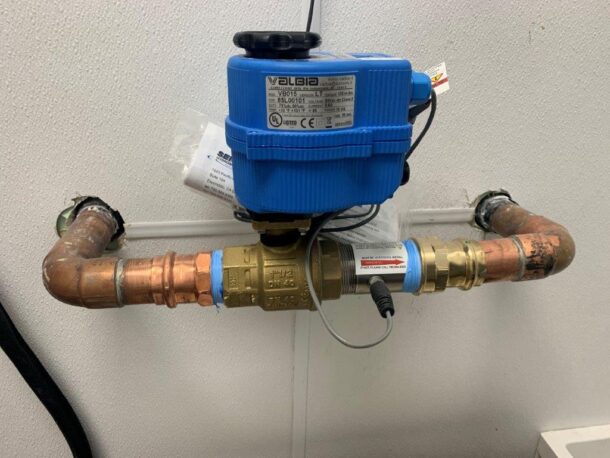
Protective measures taken at a national salon franchise with a Sentinel Hydrosolutions Leak Defense System shutoff valve.
According to Fox, the Leak Defense Point of Leak Detector (POLD) is an excellent solution, when coupled with Leak Defense flow sensors, for residential homes or commercial locations to simply and easily protect a property from catastrophic water damage. These multi-point electronic leak detectors can be placed anywhere there’s a high risk for plumbing leaks, typically near appliances and fixtures; they will close the water supply valve and send an alarm if moisture is detected.
“Leak Defense products are available through our over 2,000 nationwide installers, wholesalers and rep firms,” said Fox. “Installer and facility manager training is conducted nationwide.”
Luxury Condo Puts a Stop to Leakage
Sunset Pointe near St. Petersburg, Florida, is a luxury condominium complex on a barrier island off the Florida coast. Since 2017, three of four six-story buildings have been built and occupied, with a fourth one now under construction.
Today, all 130 occupied units, each exceeding $1 million in value, contain a Leak Defense system. Their technologies were installed after three leakage incidents—all within a six- month period in 2018—created more than $150,000 in damage to many individual units, common areas and an elevator system.
“We haven’t had a single loss or insurance claim after completion of the [Leak Defense] products,” said Vince Pusateri, board president of the Sunset Pointe Condo Association.
Three separate incidents
Pusateri, an early resident of Building 1, was the building president at the time the incidents occurred. The first was in a laundry room, when a hose connecting to a washer sprung a leak.
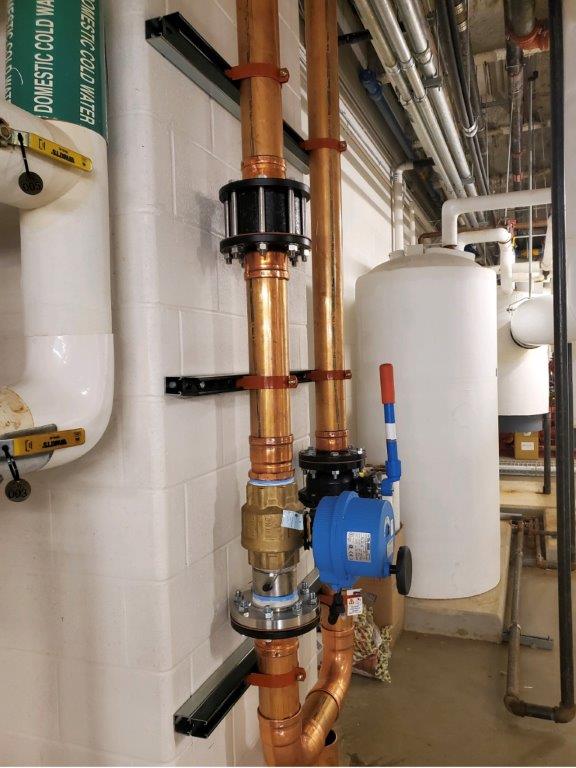
Emergency water shutoff with set schedules protect a facility in Atlanta, Ga.
The second occurred in the middle of the night. A water softener system in a utility closet sprung a leak, and the condo owners awoke to find themselves wading in six inches of water. The water also spread to the two units next door, into the walls of units below, and into the elevator area.
“In a condo complex where there are common walls and floors, a leak in one unit affects not only the people there, but also the people around them,” said Pusateri. “In addition to structural problems, there can be damage to rugs and furnishings—and, potentially, black mold if things aren’t taken care of quickly.”
Installing leak defense
Following a third incident when a hot water tank line sprung a leak in a pantry, a building maintenance engineer suggested several leak detection solutions to the Building Governance Committee. Ultimately, the committee (chaired by Pusateri) chose to install Leak Defense.
The system is comprised of several components. The first is a proprietary valve installed on the incoming waterline to each condo unit; once installed, the automatic water shut-off control valve monitors water flow 24/7/365.
The second is a wireless touchscreen control in each living unit, allowing residents to set the system to fit their family’s lifestyle needs. For example, if high-volume overnight water use would be unusual, the control can send an audible alert; it can also shut off the water intake. The control could also be connected to a third-party monitoring company to make sure an alert is attended to even if the owners are away.
Point-of-leak detectors can be placed at any potential trouble spots to detect leaks, such as in the laundry room or under a bathroom or kitchen sink. Finally, a mobile app allows easy, remote monitoring.
“We liked the sturdy unit [control panel] and the company’s good track record,” Pusateri said. He also pointed to other features, such as being able to set the system for how long water could run before activating an audible alarm, and ease of operation.
Condo owners in Building 1 agreed to the installations, as did the owners later in Buildings 2 and 3. Pusateri said that most condo owners have 6-10 sensors in their home; locations are up to each owner.
“What I also liked is that sensors can detect a change in water pressure, even behind a wall,” said Pusateri.
He added that for reliability in a storm, the system is backed up with an uninterruptible power supply (UPS), which plugs into a wall. “In Florida, we have a lot of lightning strikes and power surges,” Pusateri noted, “but with UPS battery backups, we’re covered.”
When Building 4 is completed in 2023, Leak Defense systems will be installed to protect those units in the condo complex. “We’re happy with Leak Defense,” Pusateri said. “It has the best track record; it’s rugged, and we don’t want any further damage.”
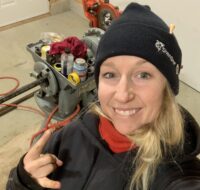
Name: Lesley Joan McGlenen Title: Owner/Operator Company: Pipe Wench Plumbing & Heating ltd. Location: Scotch Creek, British Columbia, Canada Specialty: Plumbing and Heating When asked if she’d be on a scooter anytime soon, Lesley McGlenen (@thepipewench) says she’ll take a HARD PASS! “My favorite smoothie is a spinach, protein (double protein) yogurt, frozen Read more
Name: Lesley Joan McGlenen
Title: Owner/Operator
Company: Pipe Wench Plumbing & Heating ltd.
Location: Scotch Creek, British Columbia, Canada
Specialty: Plumbing and Heating
When asked if she’d be on a scooter anytime soon, Lesley McGlenen (@thepipewench) says she’ll take a HARD PASS! “My favorite smoothie is a spinach, protein (double protein) yogurt, frozen blueberries and pineapple, and orange juice, and most definitely will not be having any more burger shakes,” says McGlenen.
Unless you’ve been living under an Instagram or social media rock, you probably have heard of that ill-fated scooter ride by now. McGlenen was heading back to the hotel from an evening’s festivities during the WWETT Show, and decided that jumping on a scooter was the fastest way to get back. Did I mention it was raining? “Unfortunately, I hit a bump in the alley as I was approaching a sidewalk and fell chin to curb,” says McGlenen.
Friend and fellow contractor friend Alan Carlson @alan_calrson was riding ahead and quickly doubled back, making the 911 call. The paramedics took Lesley by ambulance to the hospital. As Lesley went into emergency surgery, Alan was able to gather her things, and the next day take her back to the hotel post operation. Alan and Mary @theladyplumber stayed with Lesley that night and the next morning, and helped with rescheduling her flight home. “Alan was able to drive me to the airport and see me off. It was very comforting as I was traveling solo,” says McGlenen.
Lesley says she has come a long way since that rainy night in March; however, she still has quite a bit left to go. “The jaw is on the mend and getting more functional, wires are out, and I am able to chew soft foods and still on the smoothie train. Next appointment is June 1 where i’ll get another assessment of progress and then be able to get a better time line on dental reconstruction in the fall, or early of 2024,” says McGlenen.
The Start
Lesley started working as a laborer for her dad’s construction/development company, and worked there for about a year and half. “We were in-between projects and they had to lay me off, and the plumber offered me a job. I was on site for about 2-3 weeks and the apprentice officer came on site and suggested that I get indentured. I approached my employer with the paperwork and signed up as an apprentice, and scheduled my in-class portion for the following January,” says McGlenen.
Lesley continued to work for the same employer for nearly 11 years, then turned subcontractor after she passed her apprenticeship and received her Red Seal Journeyman Plumbing and Gasfitter B tickets. It was a smaller company that ran about 3-6 guys, and they did mostly commercial/residential developments. “With it being a small, tight crew with big projects, I had to learn quick and learn to be efficient,” says McGlenen.
How did Lesley know it was time to try to make the jump on her own? “I didn’t, lol, but I knew it was time to make the next move as I felt I was stagnant in pay and opportunity with the company I currently worked for,” says McGlenen.
“I had been working for my employer for quite a few years as an employee, and when we started the next big complex/development, I wanted to be able to make more money and have more of a challenge so I started subcontracting,” continues McGlenen.
From there, Lesley was able to take on small renos and service calls on her own in addition to those projects, and when they slowed down, she had set up a decent network to be able to pick up projects on her own, and from other plumbers in town from which to subcontract. “By doing so, I was not putting all my eggs in one basket.” Lesley has been on her own since September 2012.
Labor of Love
McGlenen says she loves the freedom and variety that the trades offer daily, weekly, monthly, and year by year. “Everything is changing and innovating within the industry. At the same time, you are using old school practices that you will carry throughout, in addition to all the new technologies and advancements.”
Over these past 2 1/2 years, McGlenen has been primarily building Bob’s (her dad’s) and her mom’s retirement home. The skills Lesley has learned from her father—from building this house starting from the foundation all the way up to doing the metal standing seam roofing—has been immeasurable. “I will carry these lessons, along with the memories of building a house with my 72-year-old father, long into my future endeavors,” says McGlenen.
Yet, with any job, there are some drawbacks. For Lesley, it is very mentally and physically demanding, “so what I have learned during this current injury is that there will always be work in the future. Learning my limits and staying within it so I do not over work/overrun myself is key. This can happen unexpectedly, considering I find myself being a ‘yes’ person; it is ok to step back and say ‘no.’”
And with the years of experience in the trades and the experience owning and operating her own business, McGlenen has had her fair share of learning opportunities. By sharing her experiences with up-and-coming apprentices and other colleagues, which can be used as a tool to be emulated in their practices to become better, more efficient, successful human beings, McGlenen definitely considers herself a mentor.
The Personal
What’s so interesting about Lesley is, well, anything she puts her mind to. She is creative, funny, smart, and has the ability to laugh at herself when the chips are down. See scooter story above. She has said about that moment was that she could have sulked and felt sorry about herself and asked “why me?” or realized what’s done is done and plan for the future.
Back in the early stages of COVID, the “Sharpie Doodles” came about. “I was stuck at home, along with the rest of the world, and over-consuming some beverages one night, and a friend sent a meme about not drinking alone,” explains McGlenen. “It was on someone’s legs with the worst drawing of a smiley faces showing ‘it’s not drinking alone if you have your buddies with you.’ So, I proceeded to grab my sharpies, threw on some Rolling Stones and got to drawing. Then it just became a thing every-so-often, grab a few ‘pops’ and the sharpies as a way to cut loose to decompress from stress while doing something fun an creative.
“I have been told by my aunt Sheelagh that I should really try an just stick to paper, but what fun is that?! I have done a few others since—Alan Carlson, Bob Baker, Bob Boilercrew, Plumb Bob Rob and my main man FRED. “Next up ….. TBD,” says McGlenen.
When it comes to free time, “I love to golf and spend with friends/family. In the summer, I love to grab a cold bevy and a book, some tunes and float on the lake.
“In the winter I love to do puzzles, listen to podcasts, go on odd snowboard trips, and travel to warmer destinations to golf,” says McGlenen.
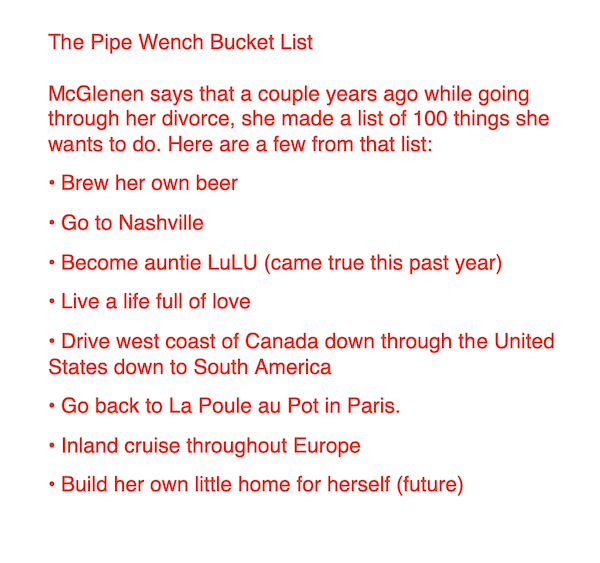
Golf has been one constant free-time activity. Lesley grew up with her my mom, dad and grandparents as avid golfers. “I golfed when I was little and I am pretty sure my dad wanted me to be on the LPGA, but I was not interested as a pre-teen,” says McGlenen.
“However, as I grew out of my teenage years and moved out of town, I found golf was a good way to meet other women and make connections for business. I joined the local ladies’ leagues and started golfing regularly and made a good crew of friends.”
Since moving three years ago, Lesley had planned a weekend for her friends to come down to see the house, golf and tour the new area, so she figured she should plan a golf tournament—the G-Dammnn Golf Tournament (GDGT) for the babes. “It’s vibe is a fun interactive atmosphere for all skill levels where women can feel confident to come out to a tournament with their friends, make new friends and have a great time while supporting other women. A portion of the proceeds are being donated this year to the Women in Trades program at the Okanagan College, for which I mentor,” says McGlenen.
Lesley feels it’s important to encourage women and to show them that they have plenty of opportunities within the trades to provide a financially secure future for themselves and their families. She is still accepting registrations for the event up until June 1 or until it sells out. The event is being held June 10th at Talking Rock Golf Course, Little Shuswap Lake, British Columbia, Canada. You can find more details at www.babesgdgt.ca, and she is also actively accepting sponsorships and donations toward the event and the Women in Trades program.
What’s one thing people may not know about McGlenen? “I like to sew,” she says. “I was in a textiles class in high school, a fancy word for sewing class, and originally wanted to be a home economics teacher. My grandma sewed and I got into sewing as a child and loved making my own clothes, even made a pair of my own golf capris. I would make pajama pants and sell them to the neighborhood kids. The most recent items I have sewed for myself are bathing suits.”