The New England Patriots create a green dynasty at Gillette Stadium. In addition to being the home of the New England Patriots, Gillette Stadium is a world class entertainment facility that hosts everything from international soccer matches to concerts by Jay Z, Beyoncé, Taylor Swift and Kenny Chesney. During what they call a full-stadium event Read more
Featured Articles
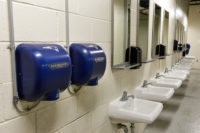
The New England Patriots create a green dynasty at Gillette Stadium. In addition to being the home of the New England Patriots, Gillette Stadium is a world class entertainment facility that hosts everything from international soccer matches to concerts by Jay Z, Beyoncé, Taylor Swift and Kenny Chesney.
During what they call a full-stadium event, nearly 70,000 people crowd the stands—and use the restrooms.
Since 2009, Gillette Stadium has used XLERATOR high-speed, energy efficient hand dryers to cut costs, meet sustainability goals, promote restroom hygiene and improve the guest experience.
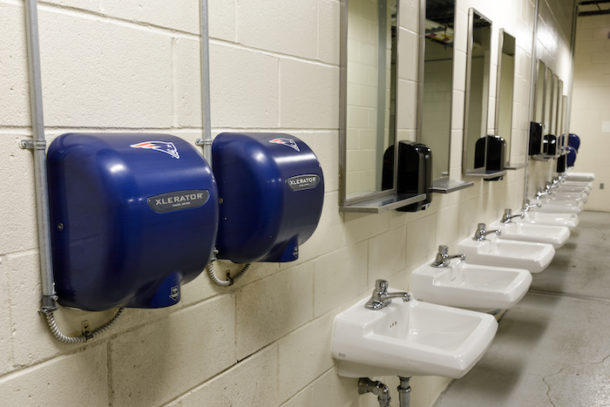
“The XLERATOR is a win-win-win-win for us,” says Jim Nolan, Chief Operating Officer. “First, it’s better for the environment. Second, we are saving money while our staff is spending less time cleaning paper off the floor and refilling dispensers. Third, staff is freed up to respond more quickly to fan issues. Fourth, and most important, fans prefer it to paper, giving them a better experience.”
Big Money Player
Originally equipped with paper towel dispensers, the stadium used an average of 6,264,000 paper towels per year, at a cost of more than $50,000 for paper, maintenance and waste removal. In September 2009, Gillette installed more than 125 XLERATOR dryers featuring exclusive, custom digital imaging cover technology throughout Gillette Stadium.
When you do the math, that means 125 XLERATORs do the work of 6 million paper towels.
“The XLERATOR hand dryers reduce the cost and maintenance associated with paper towels in the stadium’s restrooms,” says Jim Nolan.
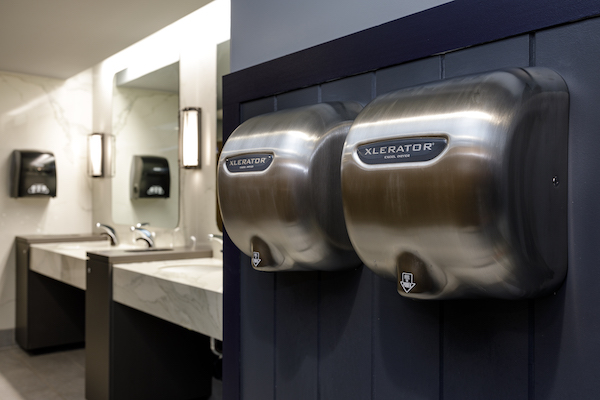
The XLERATOR represents a 95% cost savings when compared to paper towels, eliminating their labor, maintenance and waste. It is the only hand dryer Made USA Certified® with a dry time of 8 seconds* — tested to guidelines from the Global Hand Dryer PCR published by UL Environment — and it uses 80 percent less energy than conventional hand dryers. The XLERATOR is BuildingGreen Approved and helps facilities qualify for the most LEED credits.
“We want to make sure our operations are as efficient as possible,” says Jason Stone, Senior Director of Operations. “Having the XLERATORs, we’re able to be more efficient in the bathrooms and provide our customers with a great experience.”
A Strong Defense Against Dirty Restrooms
In addition to cost savings, the XLERATOR has helped increase restroom cleanliness and hygiene—while freeing maintenance staff to focus on other areas.
“With the XLERATOR hand dryers, we’re not finding paper towels all over the floors, toilets, urinals and sinks,” says Stone. “We had to have staff continually monitor the bathrooms. Now, if we have a spill out in the concourse area or in a seating section, they’re able to get to those issues a lot quicker and enhance the experience of our guests.”
While the XLERATOR hand dryers make the restroom experience faster, cleaner and more efficient for fans, they also hold up like workhorses against high traffic and usage.
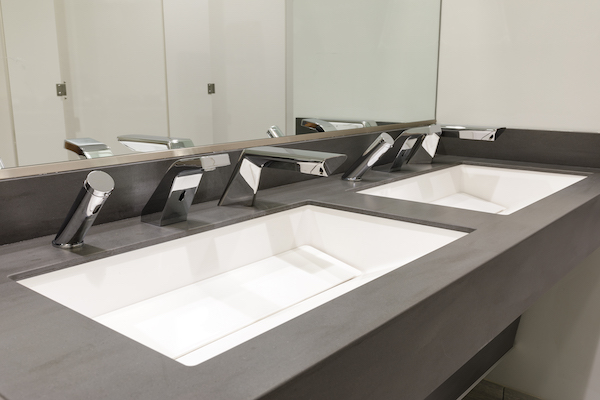
“One thing we really like about the XLERATOR hand dryers is that they’re very reliable,” says Stone. “With the millions of people who have come through the facility, we really haven’t had to change any of the units out since they were first installed. We’ve just changed the covers on them, from a branding perspective, but the main components have not been switched out.”
Gillette makes great use of Excel Dryer’s custom cover option—keeping the branding fresh with updated designs and communicating their sustainability mission to fans. Excel Dryer’s cover finish options are the most diverse in the industry, including custom cover options for corporate branding or environmental messaging. Exclusive patented Kolorfusion digital image technology is used to customize covers with graphics, team colors, corporate logos, green messaging or any other high-resolution image.
Championing Sustainability
From the stadium’s inception, the designers and contractors focused on long-term sustainability, energy efficiency and ecosystem management. In 2002, they won the U.S. Environmental Protection Agency’s New England Environmental Merit Award for the stadium’s design.
“When we built Gillette Stadium, we used a lot of recycled materials, from concrete to steel. We daylighted a portion of the Neponset River that was going through the horse track that was here,” says Jason Stone. “Sustainability and green initiatives are a big part of our operation.”
Gillette Stadium employs several cutting-edge sustainability practices, including:
• Timing devices installed on the electrical distribution system that enable all nonessential lighting after hours to be automatically shut down, minimizing energy use.
• An on-site wastewater treatment facility that treats the stadium’s sanitary drainage such as wastewater generated from hand washing, laundry and bathing. This water is then reused in thousands of toilets throughout the facility, saving millions of gallons of water annually.
• During the construction of the stadium, more than 130,000 cubic yards of blasted open rock was processed through on-site crushers and reused on site. This process resulted in more than 90% of the residual product being reused as opposed to being added to the region’s diminishing landfill capacity.
• A photovoltaic power system that generates approximately 525 kilowatts of clean, renewable solar power at Patriot Place, the 1.3-million-square-foot entertainment, retail and dining destination adjacent to the stadium. The system supplies approximately 30% of Patriot Place’s power and approximately 2,800 crystalline photovoltaic panels span seven building rooftops at the complex.
The facility management team at Gillette Stadium continues to search for new ways to expand its conservation efforts. “Some of our latest sustainability initiatives include our food waste diversion program where we recycle approximately 200 tons of food waste per year,” Stone says. “We send that off-site where it gets converted to electricity. We’ve also incorporated LED lighting throughout the facility, including converting the lights that illuminate the game field to LED.”
“While our primary focus remains on creating the ultimate fan experience, we’re continually looking for new areas to make environmental improvements,” says Jim Nolan. “Updating the restrooms with XLERATOR hand dryers represented another large step in reducing our carbon footprint.”
A Bright Future in the NFL
“The NFL currently has XLERATOR hand dryers installed at its New York headquarters, NFL Network Studios in Los Angeles and is encouraging the use of high-speed, energy-efficient hand dryers at stadiums as part of the league’s ‘Green Initiative’,” says David Krichavsky, Director of Community Affairs, National Football League.
“We are proud of our relationship with one of the most respected organizations in professional sports,” says William Gagnon, Vice President of Marketing and Sales, Excel Dryer. “The Kraft Group has created the model franchise in the NFL. Its team, operations, business and green initiatives are a proven blueprint for success.”
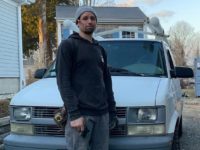
“If pipes are involved, it’s my specialty,” says Matt Benevides, owner of Benevides Plumbing & Mechanical Inc., New Bedford, Mass. A self-proclaimed workhorse, Matt’s journey didn’t quite start off working with pipes. Benevides went to a vocational school for welding and sheet metal, got a job hanging duct work in schools for about three years Read more
“If pipes are involved, it’s my specialty,” says Matt Benevides, owner of Benevides Plumbing & Mechanical Inc., New Bedford, Mass. A self-proclaimed workhorse, Matt’s journey didn’t quite start off working with pipes. Benevides went to a vocational school for welding and sheet metal, got a job hanging duct work in schools for about three years until he eventually got laid off. “My grandmother kept telling me to be a plumber like her father; that way I’d never get laid off. I took her word and jumped,” says Benevides.
Benevides started his apprenticeship for a large outfit just outside of Boston in 2006. “They hired me with no experience, no apprenticeship card—probably hired me because I broke out my funeral suit for the interview,” says Benevides.
When Benevides thinks back, he realizes that the opportunity doesn’t happen very often where a company takes a chance on someone and provides them with in-house schooling for three years—as long as you passed. “Once I received the ticket, my next goal was to work my way to foreman,” says Benevides.
Benevides worked his way to become the lead guy on projects until the company had the confidence in him to run small projects. They then gave him a van and he ran small commercial projects and commercial service. “Once I grew out of that spot, I knew I wanted to run larger projects so I switched companies to run larger projects like schools and a marine biology center, for example.”
Once Benevides figured out he could do the work, he was looking for something else and started doing residential side work at night and weekends. “After a year, I was able to take off on my own, and now I’m on year two.”
Leading the Way
Benevides owes a lot of his work ethic and drive from watching his dad his entire life. “My dad owned and operated his own landscaping business, and seeing that made me want more.” As far as the trades are concerned, Benevides had a foreman named Steve Lima who started with him as a 2nd year apprentice and followed him around. “He showed me the ins and outs of plumbing and running commercial jobs. I called him my ‘plumbing father,’” says Benevides.
Benevides says that he wants to pay it forward through his Instagram page (@boston_plumbing_monstahs_). “I would hope that I’m making the trade more enjoyable so visitors to my page can see the ins and outs of plumbing rather than a plumber equals a plunger,” says Benevides. “Social media is the way to kids these days so I’d say we are on the right road.”
Moreover, the Instagram page has recently led to some local jobs and the opportunities are endless, says Benevides. “You never know who will see something you post.”
Balancing work with leisure time is not always that easy. Beneivdes’ spare time is dedicated to his family, if I’m not working, I’m trying to be there for my wife and four kids. “I do my best to be there when my family needs me, and I take at least one day off a week. When the weather gets warm again, I make sure to bring the kids outside as much as possible. Other than that, I plumb.”
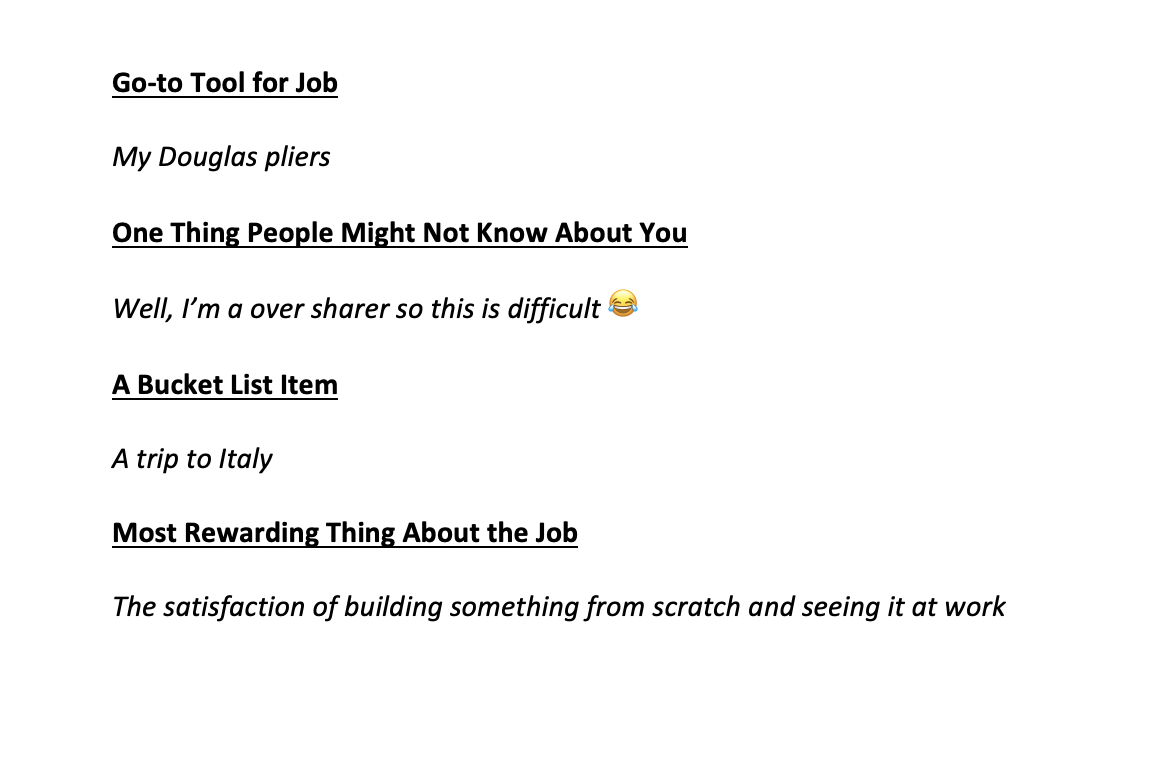
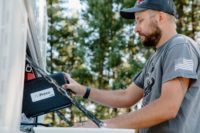
The importance of inventorying the right tools + supplies Last year, Keefer Rader, owner of Albuquerque-based Outlaw Mechanical, a shop that specializes in light commercial work, including kitchens, had one of those experiences that confirmed the value of an investment he’d made just weeks earlier. Well, he didn’t buy cryptocurrency or Spotify stock at just Read more
The importance of inventorying the right tools + supplies
Last year, Keefer Rader, owner of Albuquerque-based Outlaw Mechanical, a shop that specializes in light commercial work, including kitchens, had one of those experiences that confirmed the value of an investment he’d made just weeks earlier.
Well, he didn’t buy cryptocurrency or Spotify stock at just the right time if that’s where your imagination was going with it.
The event that triggered confirmation of a diagnostic tool’s purchase was a visit to a popular wedding venue in Colorado, a full day’s drive (or night, in this caser) from his shop.
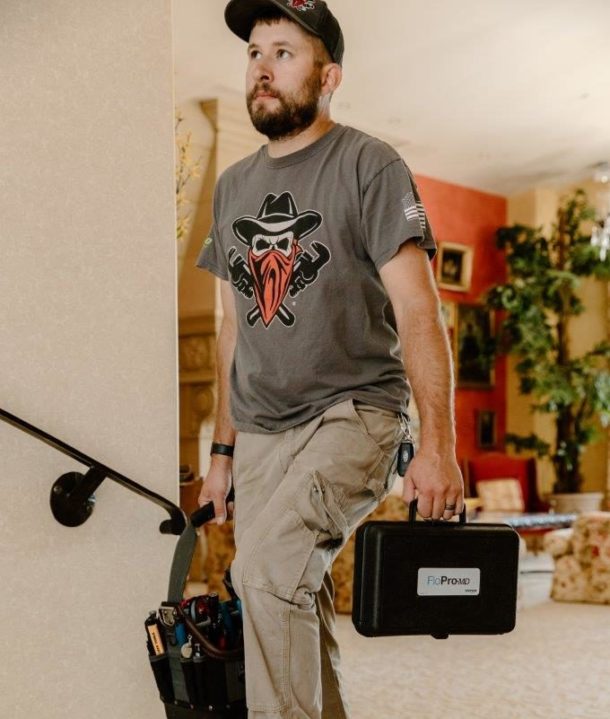
Keefer Rader, owner of Outlaw Mechanical.
350 miles from home base
Several years before he founded Outlaw Mechanical at the age of 21, Rader worked in remote Colorado, maintaining the property and mechanical systems on a private ranch – a destination that’s won recognition as a luxurious wedding/events venue. Though his firm – now 15 years old – has won recognition as the “Number Two-rated” mechanical firm in Albuquerque, he’s maintained ties in Colorado.
“My family and I love the area, and there are still folks in Colorado who insist that I serve as their mechanical systems pro – even at a distance of 350 miles,” he said. So it wasn’t a complete surprise to hear from a man who manages a mountaintop wedding venue outside of Durango, CO – just several days before a large gathering was to lease the facility for a ceremony.
Apparently, a large kitchen broiler – “absolutely needed by the caterer,” he said – wasn’t performing well. The new manager was instructed to get Rader out to fix it.
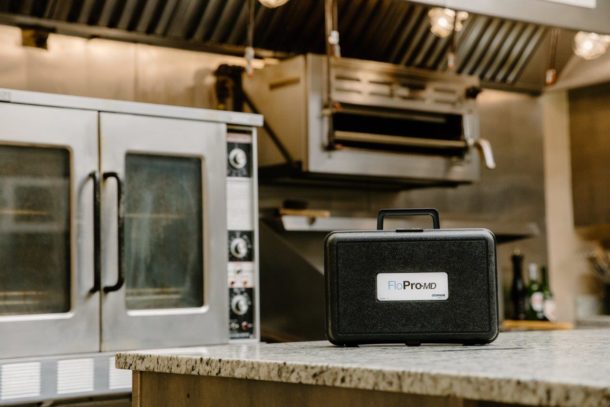
The Watts/Dormont Flo0Pro-MD is protected by its own hard case, and is easily portable.
“I tried to help him diagnose and trouble-shoot the problem, but I quickly learned that they’d already attempted to solve the problem [to no avail],” said Rader. “So, with less than a week before the large group arrived for the wedding – and with plenty of work to do in Albuquerque – Rader swept his schedule to allow time for a Friday night drive to Durango, hoping to have the problem solved for a drive home the next day.
“The challenge with remote site work is the need to pre-think everything,” he added. “Would I have the right materials and supplies and spare parts with me, and anything else I might need to complete the job in one trip?”
By Friday afternoon, Rader visited a local supplier, buying some spare parts for the large, commercial kitchen broiler. He ran between the truck and his shop’s well-stocked shelves a dozen times before his departure and was soon on his way, driving most of the distance that evening.
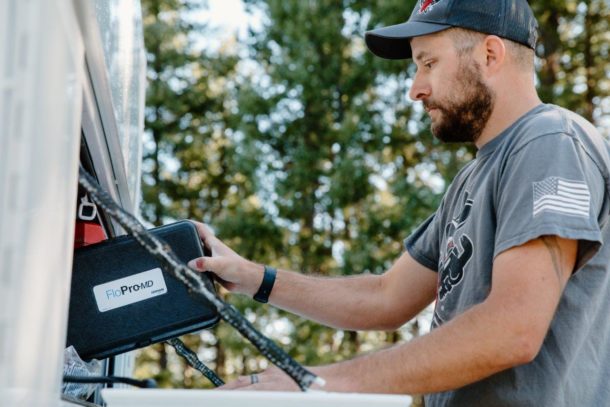
Keefer Rader, owner of Outlaw Mechanical, retrieves the FloPro-MD from his truck.
The next day, Keefer drove the last 20 miles to the wedding venue. “Just after sunrise, the site was open just as the manager promised,” said Keefer. He quickly found the griddle and set to work.
“I found that the broiler worked, but not well enough. It needed more [LP] gas for more heat,” he explained. Rader was unable to use a conventional manometer as the broiler didn’t have the test ports that he typically used for diagnosing hydronic boiler problems.
He went to the truck for the FloPro-MD diagnostic tool. “It’s now one of my go-to tools for gas appliance work,” he said. “The FloPro showed that the pre-regulator gas flow and pressure were good, but on the regulator’s other [outgoing/supply] side, I began to see my problem.”
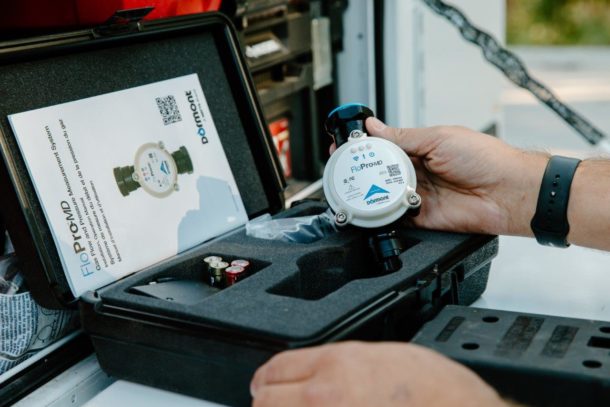
The Watts/Dormont FloPro-MD is a portable 3-in-1 gas flow meter, digital manometer, and calculator that helps service technicians and installers perform equipment start-ups, commissioning, and quickly diagnose gas flow or gas pressure issues with gas-burning appliances.
Among the supplies Rader learned long ago to keep in his truck: several gas regulators. “The FloPro made it perfectly clear that the broiler’s regulator had failed. Once connected, the new regulator provided greater gas pressure to the broiler which worked as intended, with plenty of heat for the caterer set to arrive that afternoon.”
Rader explained that, as the tool is connected to the gas line, and is out of the way, he especially likes the [FloPro-MD’s] ability to diagnose problems while the appliance is operating. “Managers at most commercial kitchens refuse to allow trouble-shooting or maintenance work during hours of operation because of the need to shut the appliance down – or, even worse – to cut gas service at a manifold to several gas appliances. Not with this tool – it’s designed to work while the appliance is in use.”
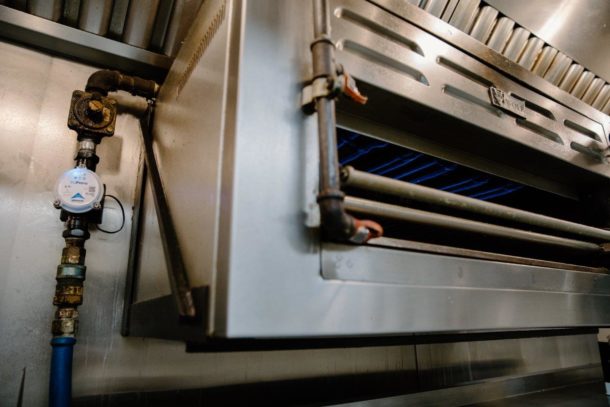
The FloPro-MD performs its diagnostic tasks, and provides useful data, while in-line (as gas courses through it). Here’s the device, in place, while flames heat the griddle following Keefer’s successful fix.
“The FloPro does the work of a variety of other tools,” added Rader. “It offers the function and intelligence of a manometer, and a gas flow meter, too. It offers precise diagnostics, with plain English on the screen. My hat’s off to the [tool’s] designer. The FloPro now has a permanent place in my truck.”
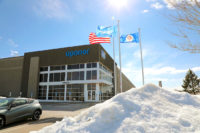
In our continuing Industry Forecast series, we talk with John Reutter, Interim President, Vice President, Finance, Uponor North America, on topics such as the short-term economy, supply chain issues, and lessons learned over the course of the pandemic. Here is our exclusive Q & A with MH: Do you project a turnaround soon or Read more

In our continuing Industry Forecast series, we talk with John Reutter, Interim President, Vice President, Finance, Uponor North America, on topics such as the short-term economy, supply chain issues, and lessons learned over the course of the pandemic. Here is our exclusive Q & A with
MH: Do you project a turnaround soon or within the next 6-12 months for certain materials that relate to your specific company?
Reutter: Signs are pointing towards some positive change with the supply chain, but there’s far too much unknown to say for certain that these constraints will improve in the next year. What we are focused on is securing secondary supply routes for our most important resources to help meet demand—and being a good partner for our customers by ensuring open and transparent communications.
MH: We are in the midst of some of the highest inflation rates since the early ‘80s. Do you think that higher inflation becomes a “newer normal”? Explain.
Reutter: No one ever wants to settle on higher inflation as a normal means of doing business. That said, I do believe we are near a peak inflationary environment with relief on its way. Unfortunately, Russia’s invasion of Ukraine will put a strain on the energy sector which will most likely cause the descent of inflation at a slower pace than we saw the ramp up. The best we can do is focus on what we can control and make sure our teams have the tools and resources they need to be successful move through the new year.
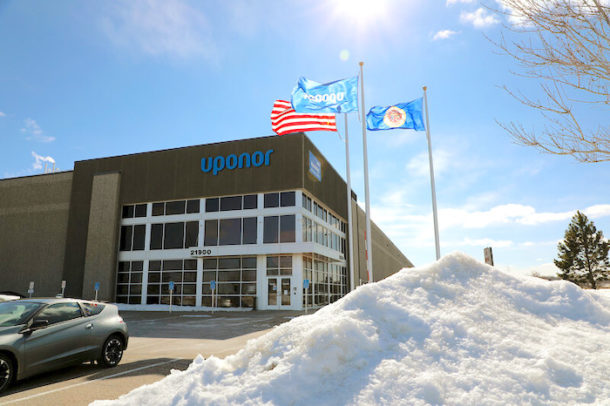
MH: In general, how do you see the economy short-term? Give a few examples of how you draw that conclusion.
Reutter: While there are certainly inflationary challenges, retail spending is up, and employment recovery continues along with wage growth. Couple that with declining COVID-19 cases and a general desire to move to an endemic environment, I believe we will see an uptick in the hospitality and travel sectors along with small business growth. These segments generally fuel short term economic recovery.
MH: Where are you seeing signs of positivity, if any?
Reutter: Residential and commercial demand for polymer piping is stronger than it has ever been. Contractors, builders, and designers continue to explore ways to integrate a complete polymer solution into their projects. We are working to deliver premium products that enrich the lives of our customers around the world, while conserving the scarce resources we are given.
MH: How do you as manufacturers work with customers who are dealing with longer lead times and/or higher prices? Is it a matter of open lines of communication?
Reutter: Everything starts with transparent communication. We are constantly maintaining open lines of communication with our customers through our factory sales team, rep agents, and distributors to ensure they have the most up-to-date information about Uponor. While we have had to make several price adjustments during the pandemic, it has been our open and transparent messaging that has maintained good standing with our customers.
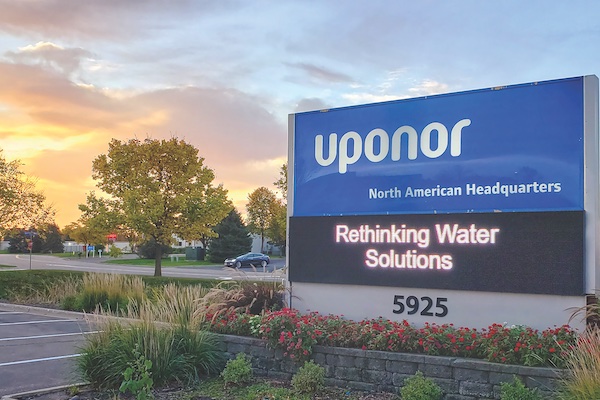
MH: It seems that in today’s employment landscape, it’s hard to find good labor, whether it’s truck drivers, waiters at restaurants, etc. In our industry, how do we continue the fight to highlight the trades as a great career choice?
Reutter: The need for skilled labor continues to grow. Increased wages and expanded career opportunities are a direct reflection of that demand. Uponor partners with several schools and universities to celebrate the opportunities available to students and workers looking to make a career change.
The fight to find talent starts with meeting the candidates on their terms – whether that’s through social media posts, job fairs, school visits, or community partnerships. We offer great wages, competitive benefits packages, and an award-winning culture that has been recognized as a top workplace for nearly a decade.
MH: In spite of COVID, people must move on. How has your company evolved—or continued to march forward—over the past two years, and talk about any new initiatives, expansions, etc.
Reutter: While our production team has been going strong throughout the pandemic, our office workforce has taken on the challenges in a productive, efficient way. We recently introduced our Flexible First program, a reimagined take on the traditional office space. With three unique employee personas – Resident, Hybrid, and Remote – our employees can perform in an environment that works best for them. We’re in the process of redesigning our corporate offices and will hold Flexible First as our standard moving forward.
You can learn more about Flexible First by reading this release from earlier in the year.
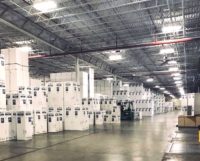
We recently asked some of the major players in the phvac markets to give us their feel of how the economy, supply chain, etc. plays out for 2022. We caught up with Bradford White’s Bruce Carnevale, president and CEO, and here are his thoughts on the rest of the year and beyond. MH: We’ve all experienced Read more
We recently asked some of the major players in the phvac markets to give us their feel of how the economy, supply chain, etc. plays out for 2022. We caught up with Bradford White’s Bruce Carnevale, president and CEO, and here are his thoughts on the rest of the year and beyond.
MH: We’ve all experienced supply chain shortages, whether it’s industry related or things such as computer chips, plastics, bacon, etc., for example. Do you project a turnaround soon or within the next 6-12 months for certain materials that relate to your specific company?
Carnevale: While the supply chain issues for some materials and components is improving, for others it’s actually getting worse. In the aggregate, I think that supply chain issues will continue to impact our business for most of 2022, and for some components, into 2023.
MH: We are in the midst of some of the highest inflation rates since the early ‘80s. Do you think that higher inflation becomes a “newer normal”? Explain.
Carnevale: No. Inflation is somewhat of a self-correcting problem. One of the many economic indicators we follow is the consumer savings rate, which was at an all-time high during the peak of COVID. It is now back to normal levels, so at some point, prices increase to the point where consumers are no longer willing or able to pay the higher prices. Demand then falls, and that puts downward pressure on prices. This will go back through the supply chain from the consumer to commodities suppliers, and I expect we will see deflation on some products driven by lower material costs. There will, however, be a “new normal” for prices because of increased labor costs. Those costs are very unlikely to adjust downward, and therefore even when commodities adjust, the total costs will still be higher than pre-COVID.
MH: In general, how do you see the economy short-term? Give a few examples of how you draw that conclusion (housing starts, commercial construction, etc.).
Carnevale: I have concerns about the macro-economy for 2022 and 2023 and have had concerns since the beginning of 2021. I don’t see how we can’t have a significant slowdown in the economy with all of the headwinds we are facing: Inflation, rising interest rates, energy prices, labor shortages, global instability, the politics of a mid-term election year, etc. I see the slowdown taking hold going into the second half of 2022.
MH: Where are you seeing signs of positivity, if any?
Carnevale: Clearly COVID cases are falling, and hospitalizations and deaths are significantly lower with Omicron vs. previous variants. There is hope that we are nearing the end of the pandemic phase and entering the endemic phase.
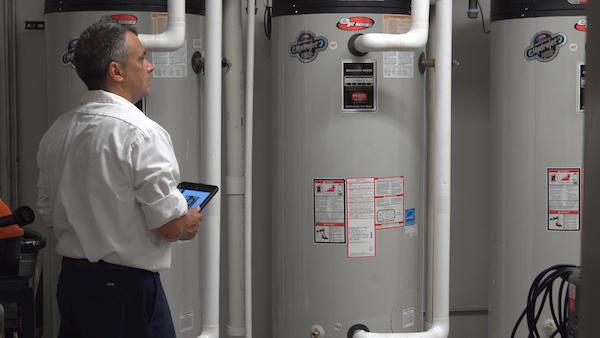
MH: How do you as manufacturers work with customers who are dealing with longer lead times and/or higher prices? Is it a matter of open lines of communication?
Carnevale: Each manufacturer deals with it differently. Our team has communicated very openly with customers when issues arise, or even when we expect issues to arise so that our customers can have the most time and information to make appropriate adjustments in their operations. So, yes, transparent communication is the best way to deal with rapidly changing conditions.
MH: It seems that in today’s employment landscape, it’s hard to find good labor, whether it’s truck drivers, waiters at restaurants, etc. In our industry, how do we continue the fight to highlight the trades as a great career choice?
Carnevale: Very true. The restaurant where I had lunch this afternoon had a sign on their entrance door that read: “Every business is short on labor. Please be kind to those who showed up to work!” That really sums up the current labor environment.
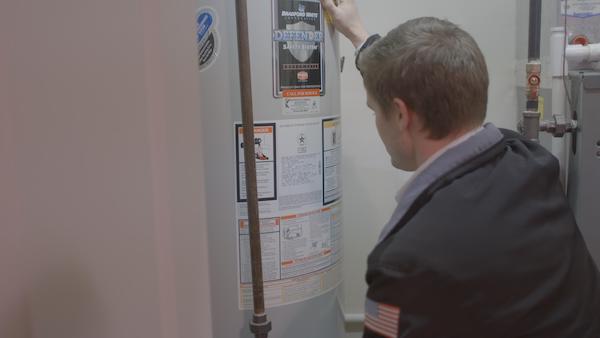
As everyone in our industry knows, the labor shortage was our biggest challenge before COVID, and it will continue to be post-COVID. There are many industry initiatives working to position the trades as a great career choice, and many companies in our industry are working diligently to promote the trades as well. I still believe what we are missing is a well-funded, well-coordinated public/private message with a big voice and a clear message that would connect with younger audiences. While we continue to work towards that, Bradford White will continue our initiatives, and 2022 we will be launching an entirely new foundation designed to promote our industry and attract new people.
MH: In spite of COVID, people must move on. How has your company evolved—or continued to march forward—over the past two years, and talk about any new initiatives, expansions, etc.
You’re right, organizations and individuals must move on. We have found that it is very helpful to shorten the time horizon for goals and objectives, otherwise you can really get bogged down by all the negative things happening all around you. So, whereas you might have had the monthly or quarterly goals, now you have to look at them weekly, or even daily. That doesn’t mean that you don’t still have long term, strategic goals, but rather that you shift more of your focus to just getting through each day or week.
From a business philosophy perspective, we, and I think most organizations are looking at supply chain improvements and diversification. I think some of the important trends will be shortening supply chains by working with suppliers closer to manufacturing operations and reviewing the risks of just-in-time inventory models versus the overall value.