It doesn’t seem so long ago we were fending off the “green” movement that was being force-fed into the vocab of working contractors. From green building to green technology, greenwashing was so prevalent that really the only “green” contractors were concerned with was the one they were chasing every day—a profit. But alas, a new Read more
Featured Articles
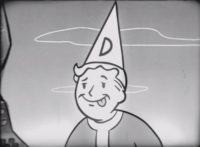
It doesn’t seem so long ago we were fending off the “green” movement that was being force-fed into the vocab of working contractors. From green building to green technology, greenwashing was so prevalent that really the only “green” contractors were concerned with was the one they were chasing every day—a profit.
But alas, a new word has dominated the marketing lexicon—“smart.” Smart cars, smart phones, smart homes and yes, even smart pumps. “The problem is they’re not that smart,” says John Barba, contractor training manager, Taco Comfort Systems. “I’ve heard people who you’d think would know better say idiotic stuff like ‘these pumps do the thinking for you,’ and ‘they take the thinking out of it,’” says Barba.
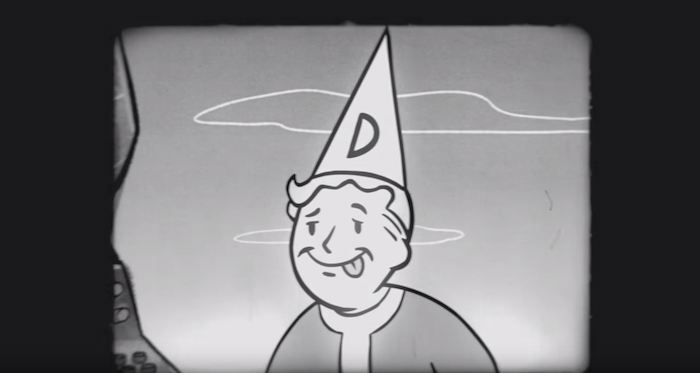
Image Credit: Noven; Bethesda.net
How about giving credit to the users who actually interact with such devices? “The thing that separates the professional from the DIY’er or the handyman is his or her ability to think and their understanding of systems. That’s why people hire professionals, and that’s why our profession is so valuable. When it comes to systems and components, the professional is the smart one,” says Barba
“The professional knows what he’s holding in his hands, why he’s using it and what impact it’s going to have on the overall system performance. There’s not a pump made that can replace what the pro knows. The machines haven’t taken over yet,” continues Barba.
Intelligent Systems
If the integration or connectivity of disparate components to a holistic, communicative system is considered smart, then I’m buying in. Why not just say that in the first place? Because it’s not market-y, and it’s too long for a tagline. Okay, then the evolution of homebuilding can be categorized as being smart or intelligent because the integration of, say, lighting, security, home entertainment, etc., can be accessed from the convenience of your smart phone (more on that later). But I’d say that is more a matter or convenience than smarts.
In fact, as part of these communicative devices, perhaps on a broader, commercial stage, we are witnessing new phrases popping up such as the Internet of Things (IoT). According to Sokwoo Rhee, former associate director of the Cyber-Physical Systems Program at the National Institute of Standards and Technology (NIST) from 2014 to 2021, IoT can be described as the advancements in sensors and communication technologies that enable us to collect data which was not previously practical; the explosive increase of the amount of collected data enabled us to perform analytics which was not previously practical or meaningful; and the advancements in data analytics that will enable us to better control and optimize the systems to benefit our daily life. Again, I can buy into that.
Remember when cell phones were labeled smart phones? I think they still are. It’s 2007 and my fancy handheld device can make calls and perform functions as a computer. Well guess what? Today, they are just considered phones. And, if they don’t perform almost any function you can think of, well, then perhaps they are just dumb.
And, oh yeah, what makes a smart car? Good gas mileage? Actually, the term Smart Car came from a venture between watchmaker Swatch and Mercedes-Benz, with Smart standing for Swatch Mercedes Art, a branding stroke of genius. Its small stature was designed for city driving with big gas savings and easy maneuverability, with not-so-good safety ratings, I’d imagine. Debuting in the U.S. in 2008, last I read, it was discontinued in 2019.
And back to those smart, magical pumps? “The only word I hate more than ‘smart’ is ‘magic,’” says Barba. “Anyone who says something like that really doesn’t know how ECM circulators really work, or how they interact with systems. No matter how ‘smart’ people claim these things are, you can’t get away from the fundamentals of circulators. These things have performance—or ‘control’ curves—and the system still has a system curve,” says Barba.
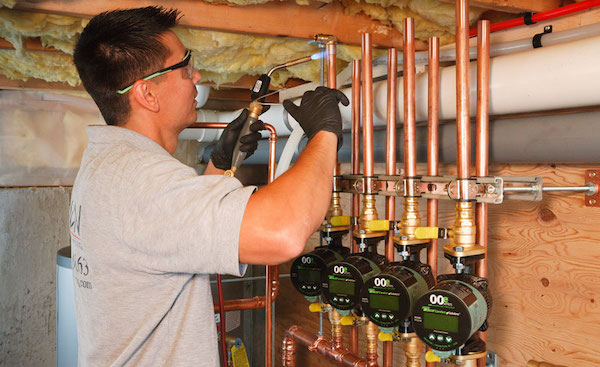
According to Barba, there’s no such thing as magic, and the only circulator that can even come remotely close to sizing itself is the Taco VT2218—it’s a Delta-T circulator and varies its speed to maintain a fixed delta-T in the system.
“And I don’t care how many lights and buttons you put on the circulator, you can’t change the fact that when you have a fixed performance curve—as every Delta-P variable speed circulator has—the system has to work where the system curve intersects the control curve. If it’s a zone valve system, speed and flow will change as zone valves open and close, but it still works on the selected control curve. If it’s a zone pump system, a Delta-P circulator won’t vary its speed because there’s nothing in a zone that would create a change in pressure differential. It goes one speed and that’s it. That’s not what I’d call smart.
“Now, that doesn’t mean you shouldn’t use a Delta-P pump as a zone pump. You should—it’ll do some pretty cool things for you provided it’s set up properly. And for that, you need a smart installer who understands what these circulators do, what they don’t do and how they interact with the system,” says Barba.
“Just because a circulator is variable speed, that doesn’t make it magic. This isn’t Hogwarts and you’re not Harry-freaking-Potter.”
What’s my point in all of this? Dig deeper, educate yourself, rely on your experience and knowledge, and don’t rely on marketing taglines such as Smart or Green to sell you completely on something.
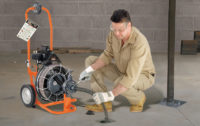
“We get 100% of our business through word-of-mouth. Our customers expect professionalism in our service. And we expect our drain cleaning tools to work first time, every time – no exceptions.” So says Charles “Chuck” Maggiore, owner of Grassroots Plumbing in Perryville, Maryland. “I only put my hard earned money into trustworthy, durable equipment – Read more
“We get 100% of our business through word-of-mouth. Our customers expect professionalism in our service. And we expect our drain cleaning tools to work first time, every time – no exceptions.”
So says Charles “Chuck” Maggiore, owner of Grassroots Plumbing in Perryville, Maryland.
“I only put my hard earned money into trustworthy, durable equipment – tools that handle the toughest jobs, and tools that make satisfied customers.”
And that’s why he’s anchored his growing drain cleaning business in rugged, reliable equipment from General Pipe Cleaners.
Generations of General Users
A third-generation plumbing and drain cleaning pro, Chuck comes by that choice honestly. Both his father and grandfather were strong proponents of General tools. And he’s literally witnessed decades of reliable General performance.
But Chuck is the first in his family who actually owns the business. And with his name on the door, he’s doubly serious about keeping his expanding customer base happy.
His main tool of choice? General’s tough, durable Metro® mid-size drain cleaner.
The popular machine packs the performance, punch, and portability to unclog 3” to 6” diameter lines up to 100 feet long.
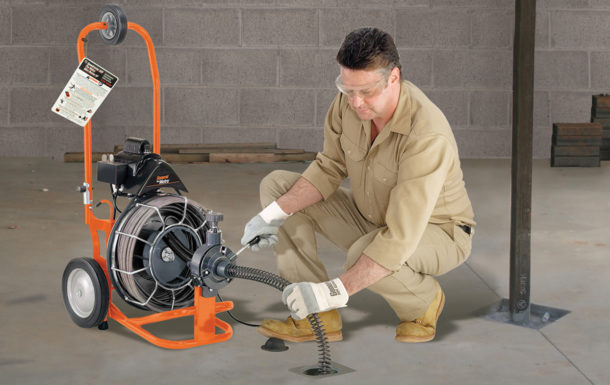
Compact, Powerful Package
“We handle a wide range of ‘commercial’ customers – emergency drain cleaning for restaurants, auto body shops, breweries, condos, apartment buildings, even churches,” Chuck says. “And the Metro definitely takes a beating – and handles 90% of my jobs!”
Plumbing, drain cleaning, and maintenance pros love it. With more cleaning power than its predecessor, the Metro now carries 100 feet of 9/16” Flexicore® cable to clear stubborn stoppages in 3” to 4” inside lines. Heavy duty 9/16” cable provides more torque than traditional 1/2” cables offer, yet can clean the same size drain lines.
General’s heavy duty Flexicore cable offers superior kinking resistance and unequalled strength with the right amount of flexibility. It’s so tough that it carries the industry’s best warranty protection – one-year against breakage.
Features Enhance Productivity
To clear tree roots and other tough clogs from 3” to 6” lines, simply switch drums to 75 feet of 5/8” Flexicore cable. To adjust to different cable sizes, just turn a knob atop the feed. No special tools are required.
“The Metro has helped me through lots of tough clogs – like roots,” Chuck agrees. “That little machine has taken care of some really big jobs – including clearing out main lines!”
The Metro’s variable speed Power Cable Feed helps. General’s labor saving feature offers enhanced safety and control through blockages. Users easily guide the cable in and out of the line at up to 20 feet per minute – yet keep hands clean and off spinning cable.
“The feed is awesome,” Chuck beams. “Even my apprentice uses it with ease – and she loves it!”
The Metro is lighter and more compact than other mid-range drain cleaners. Its narrow profile facilitates handling in tight spots, on stairs, and during vehicle loading. The maneuverable machine features a fold-down handle, stair climbers, truck-loading wheel, and tough, lightweight frame on heavy duty 10” wheels for easy transport.
Renting Expands Service Options
Chuck quickly adds that, while the Metro packs plenty of muscle, he occasionally rents General equipment for longer tough jobs. And top of the list is the Speedrooter 92R®.
“It’s a favorite of my dad and grandfather,” He recalls. “In particular, my company uses it on one local franchise restaurant that regularly needs long-distance clog removal.”
The Speedrooter 92R clears stubborn stoppages in 3” to 10” lines. Variable speed cable feed offers raw driving and pulling power for long, tough jobs – feeding and retrieving 3/4” and 5/8” cables at up to 20 feet per minute.
Renting also led to a real bargain when Chuck purchased a used General Metro from a local rental center.
“That was about five years ago,” he continues. “We had rented the Metro before, and knew it’d be a great addition to our equipment.”
Professionalism Counts
Chuck likes tools that produce satisfied customers – and help his young business grow.
“That’s why I prefer General machines over competitive brands,” he adds. “They’re tough, job-proven, and easy to maintain.”
“General’s customer service is stellar, too!” Chuck Maggiore continues. “When I started my business, I called competitors for equipment information, and General’s specialists were, by far, the most professional and helpful.”
“It’s another reason why I’m sticking with General.”
It’s evidently working.
“I’m looking to hire more employees now!” he beams.
To learn more about The Metro, and General’s complete line of rental-tough drain cleaning machines, visit http://www.drainbrain.com/rental or call the Drain Brains at 800-245-6200.
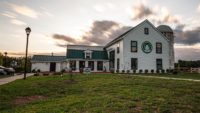
Source Brewing is a destination, a place to enjoy a craft brew in a scenic location. And while you’re there, look overhead – you’ll see some Viega products adding to the décor. Located in Colts Neck, New Jersey, Source Brewing is in a 125-year-old converted barn. In trying to maintain some of the character of Read more
Source Brewing is a destination, a place to enjoy a craft brew in a scenic location. And while you’re there, look overhead – you’ll see some Viega products adding to the décor.
Located in Colts Neck, New Jersey, Source Brewing is in a 125-year-old converted barn. In trying to maintain some of the character of the barn, there are exposed beams.
Matt Fleming, Vice President of All Star Plumbing, knew he’d be running copper and carbon steel lines in the building. He also knew some lines would remain exposed, so he suggested Viega, because of its clean look and for several other beneficial reasons.
“The owners liked the look of it, with the exposed lines and such,” Fleming said. “When this job came up, I thought, ‘Let’s press everything in here and see how it goes.’
The flameless connection of Viega press technology was another benefit, since the crew was working in an old wooden structure. There was nothing to worry about, with no flame needed.
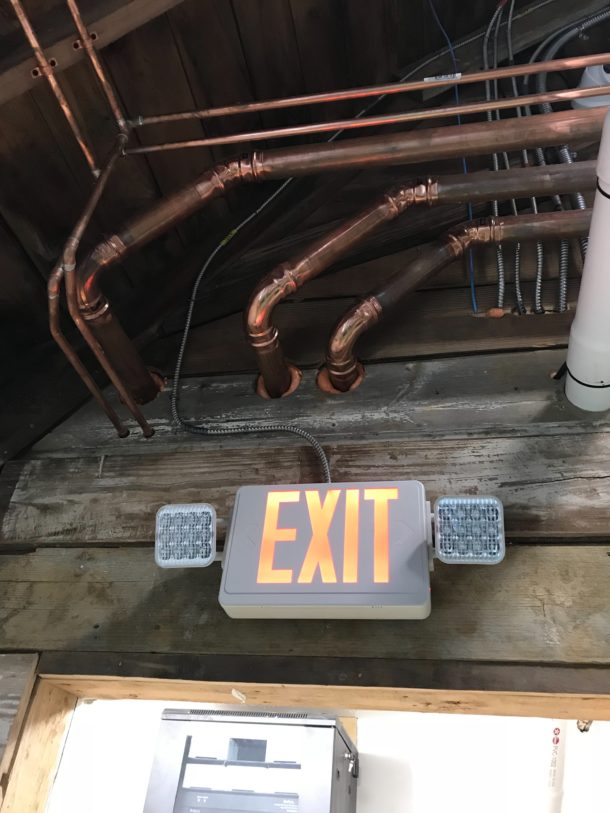
The brewery contains 12 tanks with glycol for chilling, and 2″ ProPress fittings were used on those copper lines. The 2″ carbon steel line feeding steam to three tanks was pressed with MegaPress fittings, and there are ¾″ branches from the tanks also done with MegaPress.
For the gas, a 1½” line equipped with MegaPressG fittings runs to the steam boiler. There’s about 100 feet of 1″ carbon steel line with MegaPressG fittings going to the mechanical room.
Mike Glaser, President of Aqua Solutions, installed the water filtration system for the brewery. Nearly all of his Annihilator Ultra Systems are installed with ProPress, and have been for the past decade. He said he uses Viega, because he knows he can’t beat the product.
“Viega is always consistent,” he said simply. “The fittings don’t break, they are reliable, and we don’t have issues with ProPress.”
“This is the first brewery that we’ve done everything with pressing,” Fleming added. “We’re realizing the time savings and efficiency, plus the lack of leaks. We’re not a big company, but we have five other brewery projects now on the forefront!”
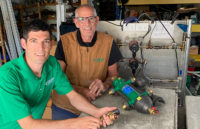
No doubt about it, COVID-19 quickly changed the way we work, and play. Travel and in person visits came to a screeching halt. Professional offices, suppliers, even many working shops closed their doors to visitors. Training in the not to distant past was done, for the most part, in person. Conveniently, most trainers adapted quickly Read more
No doubt about it, COVID-19 quickly changed the way we work, and play. Travel and in person visits came to a screeching halt. Professional offices, suppliers, even many working shops closed their doors to visitors. Training in the not to distant past was done, for the most part, in person. Conveniently, most trainers adapted quickly to offer online training options. Many of the companies in our industry were already familiar with platforms like Go To meeting. This made the switch to virtual training fairly easy for those trainers.
Some trainers I met through the ESCO group devised hybrid virtual training events. With a few cameras, one that would follow you around a room they kept the hands on training available also.
An instructor in front of a piece of equipment would be led through the troubleshooting in real time, clever and almost like being there.
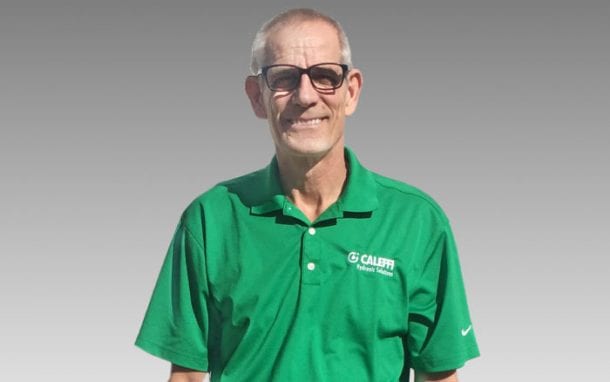
The question remains, what happens going forward in the training world. In some cases offices that made the change to virtual workspaces plan on staying that way. In some larger cities’ that has created office space vacancies and those building owners are scrambling to repurpose those spaces to get the rent rolling back in.
In cities like San Francisco it was a tough slog to see more than two engineering firms in a day due to traffic and parking logistics. With online, virtual sessions you can present to their entire staff as well as any locations they have scattered around the world.
I’ve started limited travel myself for training events. I doubt cramming 30 or more folks into a hotel meeting room will ever be attractive anymore. In some cases moving the training into the shop area, parking lot or a large cafeteria area is a good option to allow attendees to spread out more.
I doubt anyone knows for sure how this will shake out or what “bug” will hit us next that makes people want to avoid crowded rooms and spaces, but plan on having options. Come up with new ways to engage the attendees. Not being able to see faces, expressions and not getting that in person feedback changes the game for a trainer. Add polls to your training to get some interaction and a feel for the groups. Consider multiple speakers or trainers to get some back and forth conversation in your online trainings.
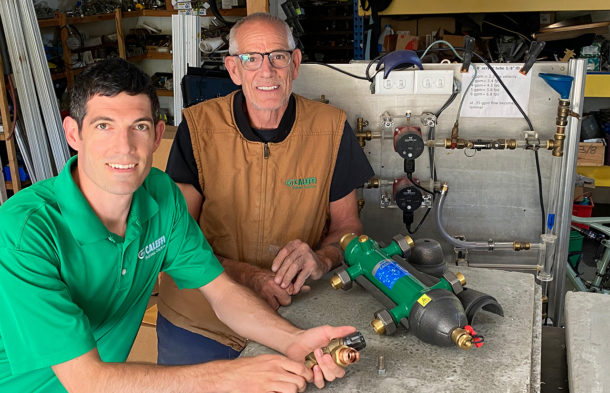
The need for having a trained workforce is critical. Equipment is becoming more sophisticated and specific, so factory training will march forward. We would love to hear from all the players in the industry, thoughts suggestions, what we can do to keep you’ all coming back.
Let’s rid the ‘VID and get back to the normal face to face that we all crave.
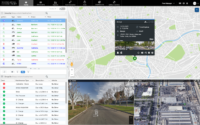
Wireless network technology is continuing to evolve, and members of the transportation industry who have come to rely on 3G networks for telematics in their connected vehicles have to consider how they’re going to keep up, lest they get left behind. Driven by ever-growing demands for more and faster data, major network providers are working Read more
Wireless network technology is continuing to evolve, and members of the transportation industry who have come to rely on 3G networks for telematics in their connected vehicles have to consider how they’re going to keep up, lest they get left behind.
Driven by ever-growing demands for more and faster data, major network providers are working ceaselessly on their respective rollouts of the fifth generation of mobile network capabilities, known as 5G, promising greatly reduced latency along with incredible speed and the ability to transmit large amounts of data in much reduced time. At the same time, the 3G networks are being phased out, with most networks set to go offline next year. Current 3G hardware is incompatible with the newer networks, and fleets that don’t upgrade in time will find themselves in the dark before long.
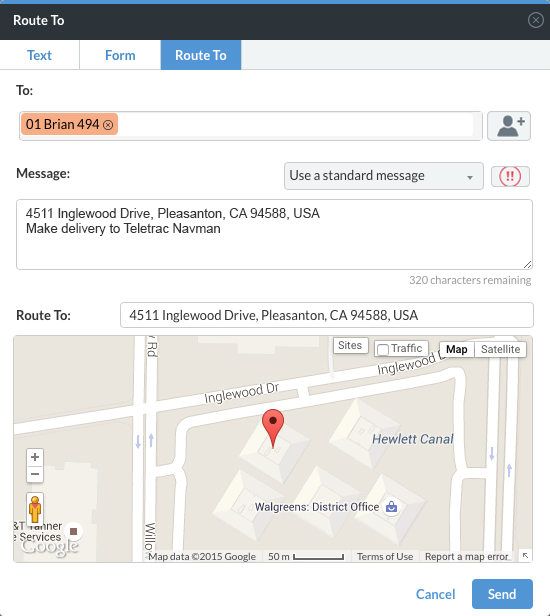
3G’s Clock is Ticking
Fortunately for fleet owners, there is still time to make the transition. Of the biggest providers, only AT&T is currently set to sunset 3G early next year – in February – with both Sprint and Verizon planning their shutdowns for December 2022.
Those dates come with a caveat, however: depending on the region, existing 3G infrastructure isn’t guaranteed to last until the sunset date, as regular maintenance may be dropped in favor of implementing hotly demanded 4G and 5G infrastructure instead.
Faced with uncertainty, fleet owners would be wise to get ahead of this technological leap. This is especially true for fleets that are using electronic logging devices (ELD). No fleets are more at risk of being negatively impacted by this change than those mandated to use ELDs. If these fleets fall offline, the systems will no longer be accurately tracking hours of service, and the drivers will be non-compliant, introducing a risk of those vehicles being pulled from service. To make this jump correctly, companies must carefully craft an internet of things (IoT) strategy that accounts for these newer, high-speed networks. Doing so will require implementation planning, cost analysis and training, giving all the more reason to act quickly.
The Benefits of Modern Hardware
Newer technology introduces greater functionality that will undoubtedly come in handy in the regular operation of a fleet. Even going from one step from 3G to 4G, the improvement will be immediately noticeable. Further futureproofing for 5G will ensure fleet owners stay at the forefront of technology for decades to come, all while enjoying the smoothest experience possible as the new networks roll out. The perks of being on a cutting-edge network are myriad, but highlights include:
- Faster speed and a wider network mean more reliable connections, particularly in areas where the wireless network is congested.
- Improved latency allows for sending a large mass of data such as alerts and events, including data-heavy content such as video.
- Communications between connected vehicles and the surrounding infrastructure is far more reliable and operate in close to real-time on high-speed connections providing instant information from the fleet and drivers.
- Massive amounts of data can be fed into AI-enabled telematics systems, turning real-time data into actionable safety, efficiency and compliance gains.
The key takeaway is that moving to new hardware isn’t a needless burden, but a net gain for a fleet’s drivers, customers and bottom line. Owners who get ahead now will avoid challenges down the line and reap the benefits above in the meantime.
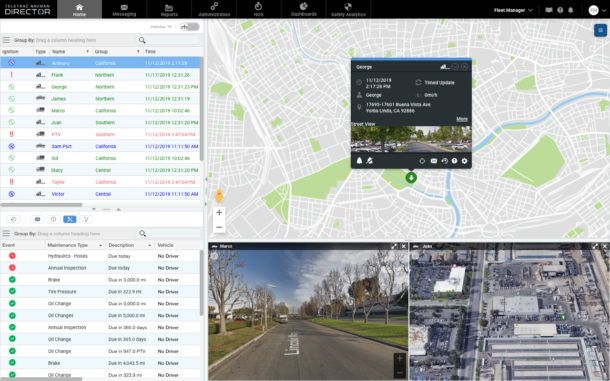
The Road Ahead
Adopting 4G and 5G capable hardware is both an exciting opportunity and a growing requirement as older networks sunset, but the biggest reason for fleet owners to get started sooner is to make sure they have time to do it right. In the coming months, owners will want to take the following steps:
- Determine how many devices are still on the 3G network, and how many need to be migrated.
- Understand what kind of lifecycle to expect from new telematics equipment.
- Research modern telematics speed- and data-focused features made possible by new hardware, including AI and machine learning options, and consider how they can improve the fleet’s operation.
- Discuss the upgrade with the fleet’s telematics provider and learn about modern telematics and future facing solutions.
- Discover whether or not the telematics provider is charging their current customers for this type of upgrade, this can give you a glimpse into how they will handle related future tech refreshes.
- Ensure the new hardware is properly certified and has a pathway to helping companies with their regulatory requirements such as ELD or other regional specific programs
- Schedule the necessary vehicle downtime to make the upgrade with the minimum possible impact on downtime.
- Once everything is in place, implement a migration plan well ahead of your wireless network provider’s 3G sunset period.
These steps will take time, and fleet owners will want to feel confident in every step of the process. As such, waiting until the last minute to get started on the transition is ill-advised. Moving up from 3G isn’t as easy as flipping a switch. However, those owners who do put in the effort will avoid having to worry about their telematic systems potentially going out on them, crippling their essential dataflow for safety, compliance and business efficiency.
Now is the time to check with your telematics provider about the imminent 3G sunsetting or find a new vendor who can handle the inevitable upgrade.
Guest Blog By Andrew Rossington
Andrew Rossington joined Teletrac Navman in February 2016, working first as Vice President of Transtech (Division) before becoming Vice President, Transport Solutions in February 2018 then onto becoming Chief Product Officer in October 2020. In this role, Andrew is responsible for all transport industry solutions, including product development, go to market, team development and financial responsibilities. Since joining the business, he has overseen year-on-year growth in the transport vertical across the Australia/New Zealand region of Teletrac Navman. Prior to this, Andrew was the Chief Executive Officer for Transtech, which was acquired by Teletrac Navman. He has spent the last 20 years focused on transport industry solutions and has extensive experience managing software development teams and implementing key business systems for some of Australia’s largest transport operators and software companies, including Toll, ComTech and Dimensions Data. He is passionate about the transport industry and using technology to enable successful business outcomes.