Did you know there is a specification for water leak detection products that protects your customers’ home or business from damage caused by leaking pipes, failed flexible connectors and overflowing toilets? These systems are installed on the incoming water line to the home, after the water meter and pressure regulator. They are known as whole Read more
Featured Articles
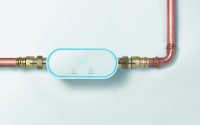
Did you know there is a specification for water leak detection products that protects your customers’ home or business from damage caused by leaking pipes, failed flexible connectors and overflowing toilets?
These systems are installed on the incoming water line to the home, after the water meter and pressure regulator. They are known as whole house water leak detection systems, and the specification governing their installation and usage is IAPMO Guide Criteria (IGC) 349, Electronic Plumbing Supply System Integrity Protection Devices.
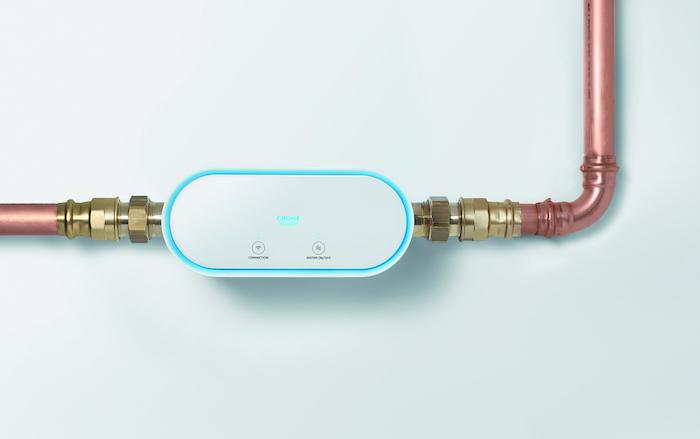
IGCs are standards developed by IAPMO, often at the request of a manufacturer, specifically for products that have not previously been covered by any existing standard.
As part of satisfying the provisions of IAPMO IGC 349, water leak detection systems must go through several tests that include, but are not limited to:
- Toxicity testing to ensure the device is safe for drinking water
- Electrical testing or review
- Pressure testing to ensure the device will not leak once it shuts off water
- Flow capacity testing to ensure the device does not restrict the flow of water to fixtures when the valve is open
- Life cycle testing to ensure it can be reset after each occurrence of water leakage
- Leak detection testing to ensure that even micro-leaks are detected.
All of these tests recreate in a laboratory environment what this product will go through during its expected lifespan.
Many of these devices come with smart phone applications that allow the homeowner to monitor remotely and receive an alert when excessive water flow is detected. Furthermore, some insurance companies offer discounts on their homeowner’s insurance policies if these devices are installed.
New products and technologies often surge ahead faster than existing standards can keep pace. To address this, IAPMO works with industry to provide an opportunity for the development of new standards when no applicable standard exists for a product. Through the IAPMO Guide Criteria procedures, IAPMO provides manufacturers and product developers an opportunity to draft IAPMO standards as a vehicle for introducing new products. Once an IGC is accepted, IAPMO R&T can list products manufactured in compliance with the new requirements.
The manufacturers of leak detection devices affix the UPC shield upon their products to demonstrate to both consumers and plumbing inspectors that they have been tested and comply with the unique standard and plumbing code requirements. The UPC shield mark of conformity is only available from the most trusted name in the plumbing industry, IAPMO Research and Testing, Inc.
Donna Estrada is the Senior Vice President of IAPMO R&T Lab, located in Ontario, Calif. Estrada has worked for laboratories for nearly 40 years, helping manufacturers in testing and certifying their products in the United States, Canada and Mexico.
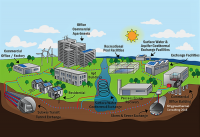
Many government jurisdictions have impressive goals set to reduce greenhouse gas emissions significantly. What if the reduction of greenhouse gas emissions from commercial buildings had a correlation to the reduction of Legionella outbreaks? In New York, the new goal is to be 100% Carbon Neutral by 2040. ConEd has issued a gas moratorium as of Read more
Many government jurisdictions have impressive goals set to reduce greenhouse gas emissions significantly. What if the reduction of greenhouse gas emissions from commercial buildings had a correlation to the reduction of Legionella outbreaks?
In New York, the new goal is to be 100% Carbon Neutral by 2040. ConEd has issued a gas moratorium as of March 15th. They will no longer be accepting applications for natural gas connections from new customers in most of their Westchester County service area beginning March 15, 2019
Interestingly, the new regulations for cooling towers are getting pretty tight. NYC health inspectors are required to test cooling towers every three months. When you add the increased costs to treat, maintain, and inspect cooling towers to the social cost of Legionella outbreaks associated with cooling towers, it might be easier than we think to just label cooling towers as a danger to health and human safety.
By doing the right thing; coupling buildings with infrastructure and the earth, we not only eliminate greenhouse gas emissions, but we eliminate the possibility of legionnaire’s disease outbreaks from cooling towers.
Just a quick look during a Google search on the day that I’m writing this article reveals several concerns, many of which are related directly to cooling towers in building cooling systems. Here are the top few:
- 1 dead, 1 sickened after Legionnaires’ outbreak at former Best Western Times Union-In New York, including New York City, between 500 and 1,000 cases of legionellosis are diagnosed annually.
- Legionnaires’ disease reports up more than fivefold since 2000; oversight is lacking USA Today – An outbreak in the South Bronx sickened 138 people and killed 16 in 2015. New York has since adopted the nation’s most aggressive measures against the disease: The city required property owners to register cooling towers and get them inspected every 90 days when they are in use.
- City sues ritzy co-op to inspect for Legionnaires’ disease NY Post- City officials don’t know if the co-op’s cooling tower was responsible but say bacteria grows in water systems like the one at the property. An inspection is necessary for “to protect human life and health,” Department of Health Deputy Commissioner Demetre Daskalakis says in the Manhattan Supreme Court suit.
Legionnaires’ disease, a severe form of pneumonia, is caused by the bacterium Legionella found naturally in freshwater environments. It can become a health concern when it breeds and spreads in human-made water systems. Each year in the United States an estimated 10,000 to 18,000 people are infected.
As we get further into this solution, it becomes more obvious to rethink building energy, which needs to be managed anyway. As an example, Stanford University studied their own campus and found that most of the energy expended through combustion could be eliminated when they took advantage of the waste heat coming from the cooling operations for the campus. In fact, the sharing of energy between the buildings on the campus reduced combustion and related emissions, and also reduced the cooling load. This is part of a “thermal energy grid,” and is an illustration of the “Water-Energy Nexus”. The water-energy nexus is the relationship between how much water is used to generate and transmit energy, and how much energy it takes to collect, clean, move, store, and dispose of water.
Speaking of hydronics, geothermal adds unprecedented benefits and possibilities. Moving beyond the scale of single buildings, think of a city blocks, or a “grid” as it’s sometimes referred to. In the winter the residential apartments are going to need heat at the same time as the commercial buildings are rejecting heat (commercial buildings are often nearly 100% cooling dominant due to internal gains). Instead of those commercial buildings rejecting heat to the outdoors through the cooling towers, that heat is now confined in a geothermal pipe-line, easily distributed to the heat-hungry GHPs serving the residential apartments; energy synergy at its best.
Present-day water and energy systems are interdependent. Water is used in all phases of energy production and electricity generation. Energy is required to extract, convey and deliver water of appropriate quality for diverse human uses, and then again to treat wastewater before its return to the environment.
It’s important to understand the different terminologies of water in use in our communities. Potable water is the water deemed safe for drinking. After that, water may be reclaimed and recycled, categorized and described as follows:
- Rainwater (rain caught from the roof or other direct methods of rain capture),
- Storm water (rainwater that has reached the ground or other hard surfaces on the ground such as roads, ovals and paddocks).
- Irrigation and run-off (from sprinkler drainage, overspray and driveways).
- Greywater (from the bath, shower, basin and maybe the kitchen).
- Treated effluent (from a sewage treatment plant).
- Dewatering (for subways and underground infrastructure)
Any of the above fluids piped in the vicinity of a building may potentially be used for heat exchange. Geothermal exchanger-sourced buildings fit the worldwide model of sustainability perfectly. A geothermal building uses less energy than any other HVAC system, whether equipped with central chiller plants or distributed heat pumps. They use renewable energy, pumped to and from the earth, eliminate on-site combustion heating, and eliminate fresh water consumption related to cooling tower operation. With no cooling towers, the normal monthly chemical maintenance, cleanings and health risks are eliminated.
Jay Egg is a geothermal consultant, writer, and the owner of EggGeothermal. He has co-authored two textbooks on geothermal HVAC systems published by McGraw-Hill Professional. He can be reached at jayegg.geo@gmail.com. The views of this article are strictly those of the author and not necessarily those of Mechanical Hub.
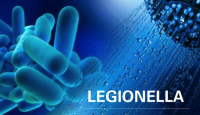
The oyster appetizer tray made its way around the table during our group dinner, and I asked the guy sitting next to me if he wanted first dibs, to which he replied, “No thanks, I know where they’ve been.” I mean, I kinda knew, but maybe not as much as this guy? So I declined Read more
The oyster appetizer tray made its way around the table during our group dinner, and I asked the guy sitting next to me if he wanted first dibs, to which he replied, “No thanks, I know where they’ve been.” I mean, I kinda knew, but maybe not as much as this guy? So I declined, as well.
Turns out, “that guy” sitting next to me was Frank Sidari, PE, BCEE, Technical Director, Special Pathogens Laboratory (SPL), and one of the featured speakers at a recent Watts Water Technologies Healthcare Symposium. Sidari was there to speak about Legionella and its growth, and the growing concern in the industry.
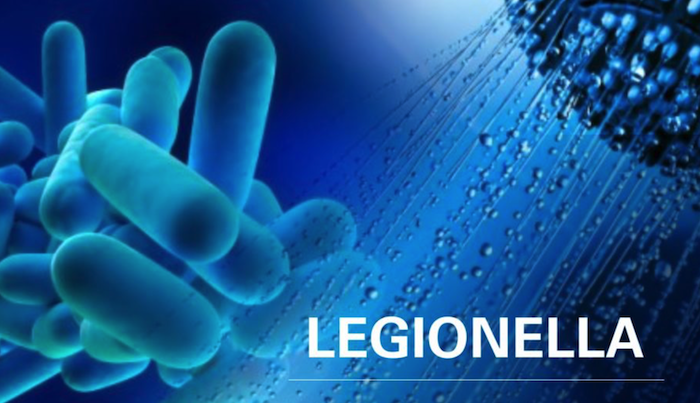
“No one should die from a preventable disease caused by bacteria in water,” said Sidari, suggesting that Legionnaires’ Disease is on the rise. Part of this rise correlates to the fact that there wasn’t really any testing being done for Legionella. Yet, it’s one of those “It’s never going to happen to me”-type diseases. What could have been mistaken for other ailments, the disease was often times diagnosed as pneumonia or the flu in older people, or those with auto-immune disorders.
According to the SPL presentation, public water supplies may contaminate the plumbing systems of hospitals and other large buildings. In fact, Legionella bacteria is not ubiquitous, but are found in 50% of building water systems—not all—which consist of:
- 12-70% of hospital water systems
- Up to 60% of large high-rise buildings
- 10-40% of residential homes
- 30-50% of cooling towers colonized with Legionella
Legionella can be found in building warm water systems such as faucets, showers, hot water tanks, decorative fountains, pools, spas and cooling towers, for example.
Transmission of pathogenic Legionella in the water system is the aerosolization and aspiration from an environmental source into the lungs—when the exposure to contaminated water reaches the airways—and because it is chlorine tolerant, it can survive the water treatment process and pass into the water distribution system. It grows in the water systems in the right conditions, i.e. water temperature, sediment and commensal microbes. Again, the disease can occur if the host is susceptible.
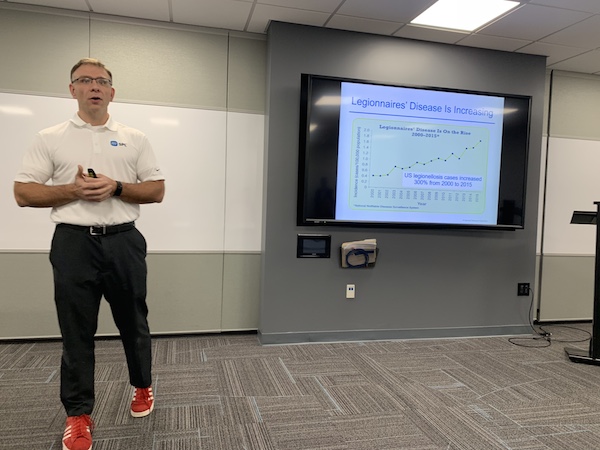
Frank Sidari
Variables such as water flow, distribution, velocity and temperature and play an important part for risk reduction. Risk factors such as water supply, building use and size, system design and hot water set-up all contribute to a safe and effective plumbing system.
The Center for Disease Control and Prevention has reported that Legionella accounted for 66% of reported drinking water-associated outbreaks, and Legionella in building plumbing systems lead to drinking water-associated outbreaks.
As there has been movement for the Center of Disease Control to develop a water management program to reduce Legionella growth in buildings, Illinois senators, for example, sent a letter to the leaders of three health-related agencies—the Centers for Disease Control and Prevention, the Department of Veterans Affairs, and the EPA—asking for their help in responding to a Legionnaires’ disease outbreak at a state-run veterans home, in Manteno, says Dain Hansen, Senior Vice President, Government Relations, The IAPMO Group.
This comes on the heels of a Legionnaires’ disease outbreak at an Illinois veterans’ home in Quincy that killed 14 people since 2015.Traction is being made in Illinois. “In response to the ongoing crisis, Illinois’ new governor, J.B. Pritzker, has established a Legionnaires’ disease task force, and the senators also requested that the three federal agencies participate in that effort,” says Hansen.
In New York state, environmental assessments are required with a Legionella sampling and risk management plan is in place where <30% distal outlet positivity requires corrective action.
Industry-wide, ASHRAE Standard 188, the first Legionella standard in the U.S., which was approved in 2015 and revised in 2018, establishes minimum Legionellosis risk management requirements for building water systems.
According to the Special Pathogens Laboratory, zero Legionella is virtually impossible to achieve in complex water systems so zero cases is the goal, not zero Legionella through Legionella control. The SPL suggests that in hospitals and long-term care facilities—and other facilities I would presume—establishing water management policies to reduce the risk of growth and spread of Legionella and other opportunistic pathogens, conducting a risk assessment and implementing a water management program are all very good ideas for a facility.
Each building owner must assess the risk and validate their water management plans to demonstrate control of the hazard. The SPL suggests that in hospitals and long-term care facilities—and other facilities, I would presume—establishing water management policies to reduce the risk of growth and spread of Legionella and other opportunistic pathogens, conducting a risk assessment and implementing a water management program are all very reasonable considerations for a facility.
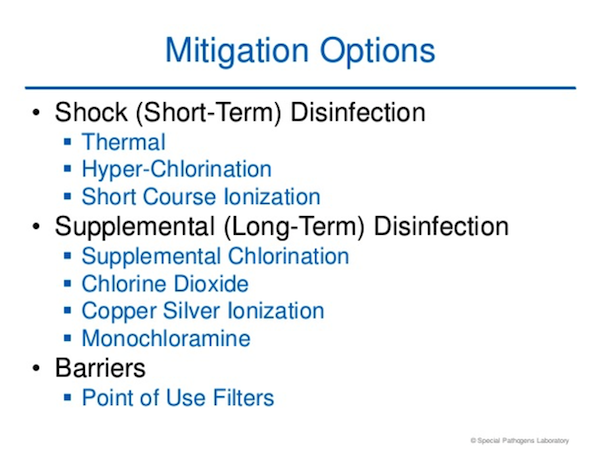
Source: Special Pathogens Lab
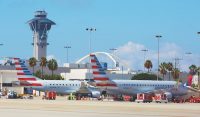
With nine terminals totaling several million square feet of floor space, Los Angeles International Airport (LAX) is massive. It’s also crowded: the 75 million passengers who passed through it in 2015 made it the world’s seventh busiest airport. Keeping those travelers comfortable and safe falls to the airport’s facility management teams, who routinely look to Read more
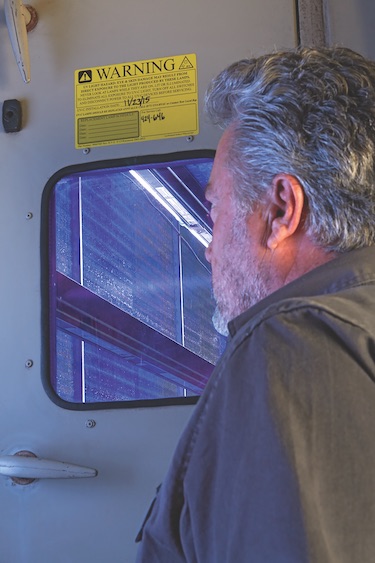
Jim Edson of NUView Environmental, a distributor for UV Resources, inspects High-output DEF (Double-Ended Fixture) UV-C fixtures installed in one of LAX’s more than 200 air handlers. The lamps’ UV-C energy inactivates microbial growth on the air handler’s cooling coils, boosting energy efficiency and indoor air quality.
With nine terminals totaling several million square feet of floor space, Los Angeles International Airport (LAX) is massive. It’s also crowded: the 75 million passengers who passed through it in 2015 made it the world’s seventh busiest airport.
Keeping those travelers comfortable and safe falls to the airport’s facility management teams, who routinely look to boost efficiencies and decrease maintenance calls across their immense service area. So it’s no surprise that while solving a minor air conditioning issue, one facility manager identified a way to improve indoor air quality (IAQ) for the entire airport.
“A tenant in Terminal 2 complained of a musty smell in their offices,” recalls Richard Yakel, the airport’s air conditioning supervisor. “We quickly determined that the odor resulted from the buildup of mold and bacteria on the air handler evaporator coil; a very common condition, especially given our humid, seaside environment.”
Although Yakel’s maintenance crews could remove the mold with solvents and elbow grease, he knew that mechanical cleanings and antimicrobial agents were only a temporary solution. He recognized that—like all equipment—without a continuous maintenance program, the conditions would quickly reappear.
Moreover, the organic buildup on the coil had caused a pressure drop that reduced the volume of air passing through the coil, as well as its heat-transfer efficiency. In other words, biofilms that can be several millimeters thick can ‘choke’ an air handler, severely inhibiting system performance.
And, he reasoned that if there was trouble in one of the airport’s air handling units (AHU), similar conditions might be found in some of the facility’s other 200+ AHUs.
In Search of Better Indoor Environmental Quality
Seeking a more permanent solution, Yakel turned to Jim Edson with Santa Clarita-based NUView Environmental in 2009, to learn if ultraviolet germicidal irradiation (UVGI) would be a cost-efficient and lasting means to remove such biological growth in HVAC cooling coils, plenum interiors, drain pans and air filters.
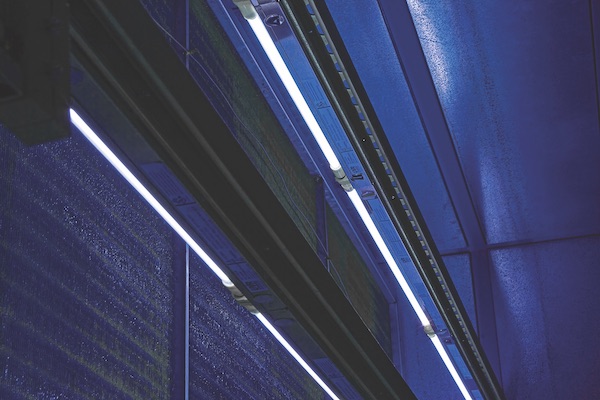
High-output DEF (Double-Ended Fixture) UV-C fixtures from UV Resources were installed in a troubled LAX air handling unit, where, by eliminating coil-fouling microorganisms, they yielded a 15 percent increase in airflow levels.
According to Edson—a distributor for UV Resources, the company whose founders pioneered the use of UV-C in HVAC equipment in the early 1990s—the UV-C energy degrades the organic matter. Ionization drives UV-C’s power to alter chemical bonds, causing lasting damage to DNA, ultimately killing the cell. Over time, the 254-nm germicidal wavelength also reflects deep into the coils to eliminate the build-up that mechanical and chemical washing often misses. Once gone, biological growth won’t re-form as long as the lamps are maintained.
This would solve Yakel’s air quality issue. However, Edson explained that this benefit is just the tip of the UV-C iceberg.
Besides improving air quality, the hidden value of UV-C is its ability to improve airflow, boost heat exchange efficiency and reduce maintenance needs.1 It accomplishes this veritable HVAC hat trick for an average equipment cost of less than $0.15 per cfm. In fact, the cost of the efficiency-enhancing UV-C equipment is a mere fraction of the 10-35 percent potential reduction in energy and maintenance costs it offers. In a facility the size of LAX, that’s a potentially huge annual savings.
Needless to say, Yakel was intrigued with UV-C technology.
A Successful Test
Although UV-C is a proven technology, with tens of thousands of systems sold each year, he wanted to verify its performance before committing to using it airport-wide.
He decided to conduct a test installation on the odorous AHU. Yakel’s team first measured the unit’s static pressure and airflow levels using a Magnehelic differential pressure gauge.
Following this baseline measurement, the team installed high-output DEF (Double-Ended Fixture) UV-C fixtures from UV Resources in the 14,000 CFM AHU. The high-output DEF series generates up to twice the ultraviolet irradiation levels compared to standard fixtures, to kill and/or degrade the toughest microorganisms and organic matter, whether surface or airborne.
Pressure readings were taken monthly for the following six months.
“My team and I were surprised by how quickly the germicidal wavelength cleaned the HVAC evaporator coil, fan motor housing and blades. However, we were truly stunned to witness a 15 percent (2,000 cfm) increase in airflow levels after just a week of operation.”
“Almost immediately after installing the UV-C fixtures, the troubled air handler was able to meet thermostat set points and there was no odor,” he says.
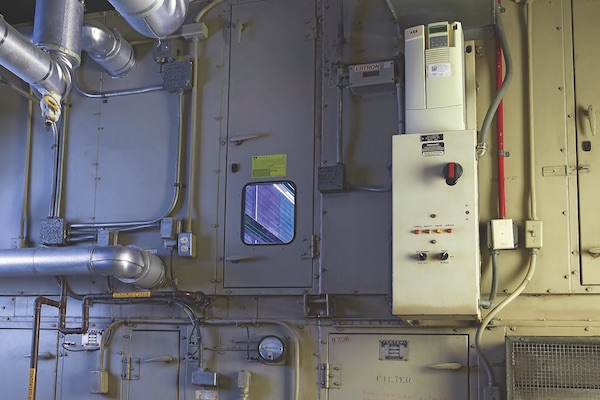
The experiment’s timing proved fortuitous. The airport was in the initial stages of planning a multi-year, $4.11 billion improvement and redevelopment project that would include renovation of existing facilities, as well as a major expansion of the Tom Bradley International Terminal. UV-C Lighting has been included in the HVAC design standards for LAX.
With budget funds available for HVAC improvements, Yakel made a case for equipping all of the airport’s 200+ air handlers with UV-C as a way to enhance indoor environmental quality for passengers and employees.
Breathing Easier
One of the reasons that Yakel opted for UV Resources’ High-Output DEF series was its robust design. With a 120-277 volt waterproof ballast, stainless steel construction and built-in weep holes, the DEF can withstand the harshest commercial or industrial HVAC environments. Power supplies and lamps are electronically matched to provide the highest output while maintaining the longest life expectancy. Yakel also liked the fact that the DEF comes with a three-year warranty, compared to one year for competing products.
“Our application requires the most durable equipment. Anything we specify has to run 24/7 and it has to last for at least 20 years,” notes Yakel. “It has to be compatible with new and existing air handlers and other system components, as well as the building management and remote monitoring systems. Parts must also be readily available.”
Each of the airport’s terminals has multiple air handlers, ranging from five in Terminal 1 to 30 in Terminal 4. AHUs range in cooling capacity from 10 to 40 tons; some of which have been in place for decades.
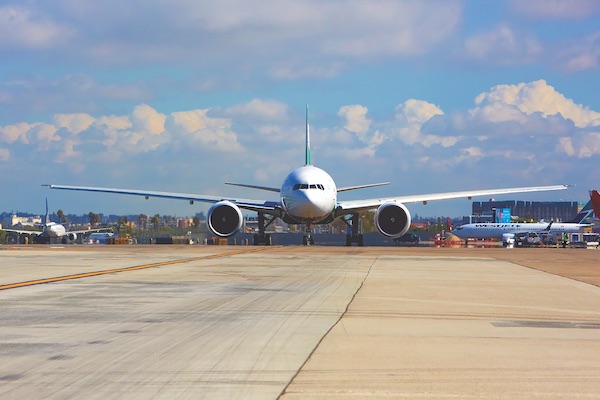
According to Edson, none of this was a problem: the beauty of UV-C is that it will work with any type of air handling equipment regardless of brand, capacity or age—the science remains the same. The required number of UV-C fixtures varies by unit size, but UV Resources’ software program specifies the exact amount of UV-C energy needed based on the height and width of the coil and plenum. Some of LAX’s really big air handlers needed 24 UV-C fixtures to do the job.
At the end of the first three-year contract period, more than 75 air handlers had been retrofitted with UV-C. The UV-C contract went out to bid again in June 2014 and NUView was the lowest bidder, securing the contract for the second three-year term.
The plug-and-play wiring meant that Yakel’s crew could retrofit the DEF fixtures in-house, while new AHUs would be required to have UV-C already installed. Workers prefabricate rows of fixture assemblies in the shop, minimizing downtime for the air handlers. They can then install the prefabbed fixture rows and bulbs for a medium sized air handler in a single work shift (typically from 12 midnight to about 5:00 a.m. when the disruption is minimal).
The UV-C fixtures have reduced maintenance costs and freed crews up for other tasks. With union positions earning an average $28 per hour, the typical eight-hour physical air handler cleanings were each costing roughly $230 and needed to be performed on a quarterly basis. At nearly $900/year/AHU multiplied across 200 AHUs—the new technology could eventually save upwards of $180,000 annually in maintenance costs alone.
Following the addition of the UV-C fixtures, the airport’s maintenance crews still visually inspect the air handlers and coils, but generally don’t have to clean the cooling coils as often.
“I have personally inspected the drain pans and plenums of several units and have seen no mold growth,” concludes Yakel. “The lack of organic growth on the coils has also improved the heat-transfer efficiency and airflow levels, thereby reducing electrical consumption.”
But Yakel sees cost and time savings as fringe benefits. His main goal was to improve indoor air quality for the millions of people who use the airport each year, and that has certainly been the case. “We haven’t had any more complaints,” he beams.
In more ways than one, everyone at LAX can now breathe more easily.
1 ASHRAE. (2015). ASHRAE handbook – HVAC applications (ch. 60.8). Atlanta: ASHRAE. https://www.ashrae.org/resources–publications/handbook/description-of-the-2015-ashrae-handbook-hvac-applications
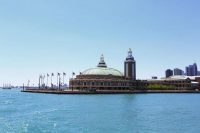
Navy Pier opened its People’s Energy Welcome Pavilion in 2017, designed to greet people as they get set to enjoy one of the Pier’s various amenities and provide them with information as they arrive. For the more-than-9 million guests that visit the Pier annually, the Welcome Pavilion needs to make a good first impression on Read more
Navy Pier opened its People’s Energy Welcome Pavilion in 2017, designed to greet people as they get set to enjoy one of the Pier’s various amenities and provide them with information as they arrive. For the more-than-9 million guests that visit the Pier annually, the Welcome Pavilion needs to make a good first impression on visitors, while setting the tone for what they’re to expect throughout the rest of the facility.
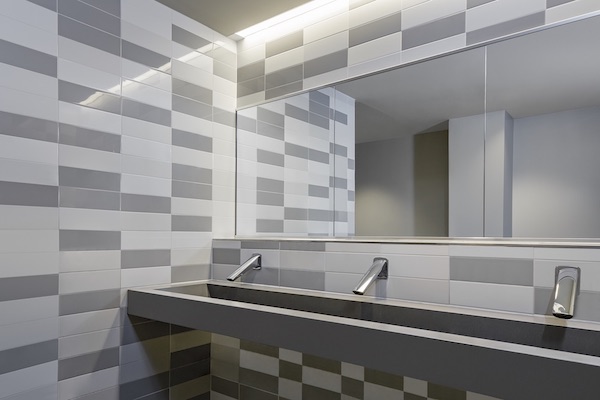
When it came time to specify commercial restroom products at the Welcome Center, not only did Sloan’s products present the elegant aesthetic that greets guests in a pleasant environment, but they also provide the durability to stand up to the millions of users each year. The Pier also needed products that would match its commitment to sustainability, and along with the facility’s energy-saving green roof and LED lighting, Sloan’s products help to make the building over 20 percent more efficient than traditional structures.
With Lake Michigan in its backyard, the Pier strives to protect and conserve water and the life around it. That’s why Navy Pier wanted water-saving flushometers that would contribute to its sustainability efforts in maximizing the guest experience while minimizing the environmental impact. Sloan SU-7009 small washdown urinal fixtures were paired with Sloan Royal® Sensor Flushometers (Royal 186 SFSM) to deliver an efficient 0.125 gallons per flush (gpf). Additionally, Sloan ST-2459 Elongated Wall-Mounted Water Closets were installed with Sloan Royal 111 SFSM Sensor Flushometers. With a static load rating of 750 pounds, the water closets can withstand the Welcome Center’s high-traffic environment, while the flushometer’s 1.28 gpf contribute to water savings across the facility.
The Pier paired Sloan DSG Designer Series sinks with its BASYS EFX800 wall-mounted faucets to present an aesthetically pleasing, yet sustainable handwashing experience. Featuring a cool Silestone Spa Suede finish, the ADA-compliant sinks complement the faucets’ sleek polished chrome appearance. The faucets’ infrared sensors enable a hygienic-friendly and touch-free handwashing process, with a flow rate of just 1.5 gpm and a line purge feature to eliminate stagnant water.