Every month Mechanical Hub and the Plumbing Museum will be collaborating to bring you a piece of plumbing history. We kick off the segment with what was thought to be a game changer in alternative pipe joining methods. Introduced in 2009 for a limited time, the StreamTECH adhesive joining system from Mueller Industries was launched Read more
Featured Articles
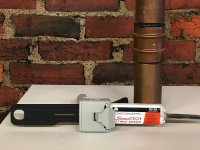
Every month Mechanical Hub and the Plumbing Museum will be collaborating to bring you a piece of plumbing history. We kick off the segment with what was thought to be a game changer in alternative pipe joining methods.
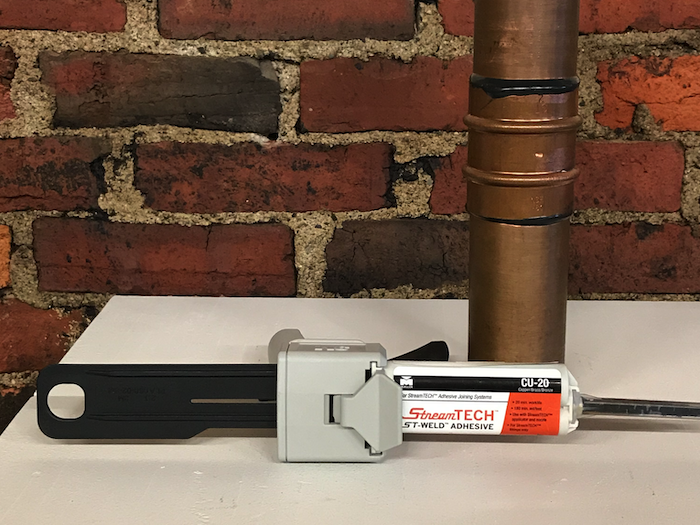
The StreamTECH system on display at the Plumbing Museum.
Introduced in 2009 for a limited time, the StreamTECH adhesive joining system from Mueller Industries was launched as an alternative to soldering and as a flame-free option. It was the alternative to pipe joining systems.
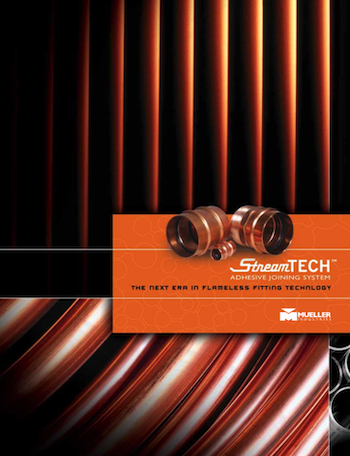
The StreamTECH brochure
According to the catalog, the company recognized that the existing mechanical joining systems were either too expensive or cumbersome. The StreamTECH System offered the lowest installed cost of any flameless copper piping system currently available. No expensive fittings or compression tools were required, only economical StreamTECH fittings and adhesives, which were easy to use and assemble quickly.
Working in close collaboration with Mueller engineers, 3M’s research team developed a 2-part epoxy adhesive based on their Scotch-Weld technology which was specially formulated for joining copper, brass and bronze metals.
Recognizing that even the strongest adhesive might not provide a 100% reliable joint by itself, Mueller® engineers developed a proprietary internal elastomeric seal for the new StreamTECH copper fittings, which provided a self-adjusting one-way barrier to maximize the effectiveness of the bond and unparalleled protection against leakage or joint failure.
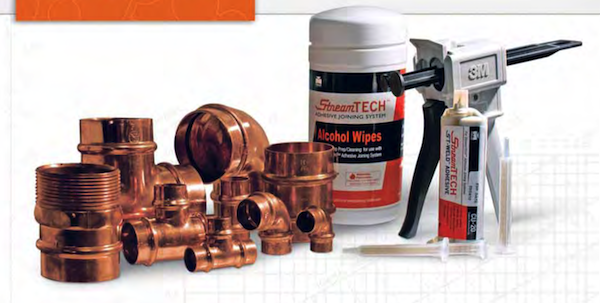
It all started with StreamTECH’s one-way lip seal, which provides more surface contact, therefore better sealing than traditional O-rings, says the brochure. It also acts like an internal wiper to evenly disperse the adhesive over the entire surface of both tube and fitting, and adjusts to imperfections in the surface of the copper tube. This results in the most reliable sealing mechanisms among mechanical, heat-free joining systems.
Located in a renovated ice house in Watertown, Mass., the American Sanitary Plumbing Museum is dedicated to promoting the contributions of the plumbing industry and its talented craftsmen across the United States. Through its unique mix of industrial history and modern art, it showcases artifacts and exhibits that range from 19th century tubs to modern toilets and a functioning rainwater reclamation system. The museum welcomes nearly a thousand visitors each year for tours and private events, and has been featured in the Wall Street Journal. For more information, visit: www.theplumbingmuseum.org.
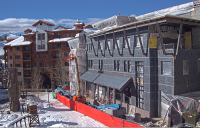
The Adaptive Sports Center in Crested Butte, Colorado, has been helping people with disabilities, as well as veterans, go on therapeutic recreation adventures for 30-plus years. Now the group is finally getting the building—and the space—it deserves so it can amp up its offerings and help even more people. The nonprofit organization, located in the Read more
The Adaptive Sports Center in Crested Butte, Colorado, has been helping people with disabilities, as well as veterans, go on therapeutic recreation adventures for 30-plus years. Now the group is finally getting the building—and the space—it deserves so it can amp up its offerings and help even more people.
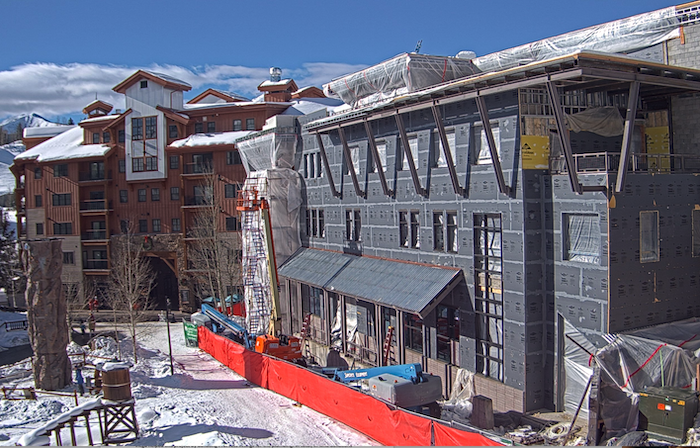
The nonprofit organization, located in the Colorado Rocky Mountains, is constructing a new building all its own. For the past decade, the organization knew it was running short on space, but real estate at the base of Crested Butte Mountain Resort is expensive and hard to come by, so it’s taken a while to make dreams reality.
Two years ago, the organization purchased land and began raising funds. Now the 25,000-square-foot building is just months from opening and leaders of the ASC can hardly wait.
“There has been a lot of work into this new building,” said Brian Barker, Marketing Manager for the ASC. “Our community has been hugely supportive, and we’re lucky to have help from a lot of really generous people and organizations that are both local to the Crested Butte area and across the country. We received donations from local individuals to major foundations and organizations—like Viega—who want to help out, because so many people believe in helping people.”
Viega helped this project by donating ProPress fittings for the plumbing. In total, in-kind donations for the construction efforts totaled more than $1 million, and Viega had a hand in it. Not only does the donation of ProPress fittings help monetarily, but ASC Executive Director Chris Hensley said it also helps by saving the contractors time—which also equals money.
The schedule for construction of the building was only 13 months, so there was no time to waste. During planning, there were lots of conversations about how to save the ASC money, and ProPress was one solid option.
Alpha Mechanical Solutions, LLC, out of Gunnison, Colorado, was hired to plumb the building, and Fred Niederer, a managing member of Alpha Mechanical, was already familiar with Viega and with ProPress.
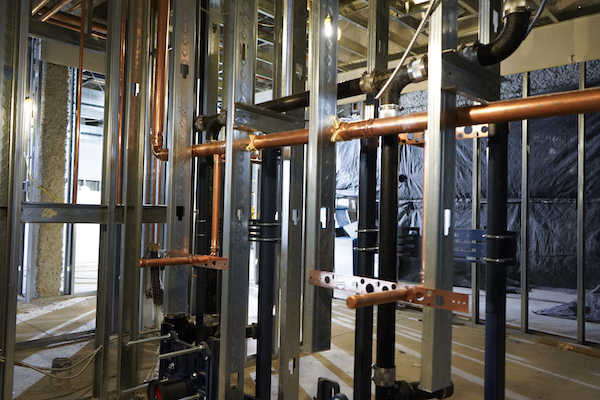
“Viega’s training facility in Nashua (New Hampshire) made it possible to see the entire product line and made it easy to justify setting up our first ProPress gun seven years ago,” he said. “Our second gun was a matter of necessity, based on how often we use the Viega system.
“ProPress was really great for this project because it had a very tight timeframe and I couldn’t think of a better product to use. The time savings method over standard joining is huge.”
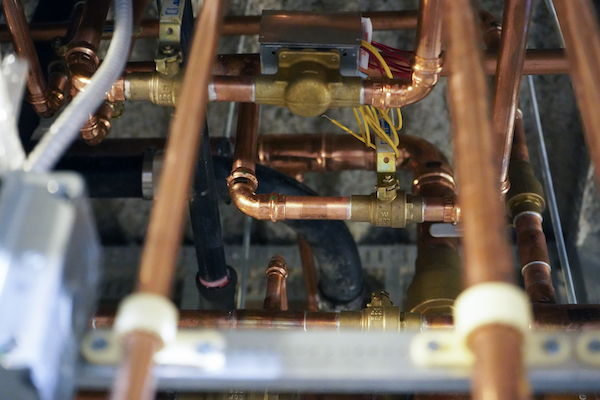
Alpha Mechanical had between 15 and 20 workers on the project to plumb nearly a mile of copper lines. The copper with ProPress fittings is for hot, cold and hot water recirculation lines, as well as hydronic lines, some variable air volume units, some in-floor heating and a little snowmelt.
“This has been press and go. Easy,” Niederer said.
The building is officially named the Kelsey Wright Building. Kelsey was a longtime participant of the ASC, and after she died her parents gave a generous gift to the organization in her honor to help get the fundraising project started. Barker said her family “really believed in what we do and what we did for her,” and they wanted to share it with others.
The four-story building (plus basement) will allow the ASC to double its capacity. Previously the organization only had the ability to offer overnight accommodations for a group of 15-20 people at a time, at a lodge in town. The new building will have housing on the third floor to allow for a second group to be served at the same time.
The facility is ski-in, ski-out, and fully accessible for all participants no matter their ability. Groups of participants come from various hospitals, VA medical centers, Walter Reed National Military Medical Center and more.
There are other activities and amenities within the Kelsey Wright building as well, including an indoor rock climbing wall, programming area and kitchen facilities. Within the basement there will be lockers that can be rented out as an additional revenue stream for the ASC, and there is an area for participants to be fitted with their skis or other apparatuses before they head out.
Adventures through the ASC don’t just happen in the winter… There are activities like canoeing, cycling, hiking and mountain climbing in the summer, or skiing, snowshoeing and ice climbing in the winter.
Founded in 1987, and originally known as the Physically Challenged Ski Program of Crested Butte, 33 lessons were given during the first winter by an all-volunteer staff. Today, more than 6,000 lessons are provided to more than 700 individuals each year. The team includes 15 board members, 14 full-time staff, more than 25 professional instructors and hundreds of volunteers. The main focus is on the long-term impact of programming on participants, aiming to get—and keep—them more physically active.
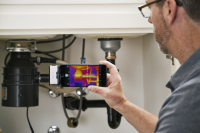
Identifies hard to see problems and saves homeowners money For many years, utilities and large companies used thermal imaging to uncover potential heat problems across large areas and to keep track of heavy machinery. But more recently, thermal imaging has truly become a game changer for most contractors and others in the building trades. Thermal Read more
Identifies hard to see problems and saves homeowners money
For many years, utilities and large companies used thermal imaging to uncover potential heat problems across large areas and to keep track of heavy machinery. But more recently, thermal imaging has truly become a game changer for most contractors and others in the building trades. Thermal cameras help contractors find and document energy loss and other problems they could not otherwise easily find. This saves them time and money – which ultimately results in homeowners saving money. Most recently, contractors have begun to combine portable thermal imaging cameras with moisture meters. Using thermal imaging to find the issue and the moisture meter to verify it saves time and helps avoid surprises that will ultimately cost homeowners more.
Thermal imaging benefits contractors and homeowners
Thermal imaging detects heat given off by an object or person. It takes the energy and translates it into light that can be seen. Using the typical “Ironbow” color palette, the viewer sees the light in a range of colors: red, orange, and yellow indicates heat, while dark blue, black, or purple signifies colder temperature. Cold can represent air leaks through door and window frames, missing insulation, and water – especially evaporating water. No other technology can provide this information. Using radiation energy, contractors can now actually “see” energy loss. It is like giving contractors a super power! Thermal imaging is extremely sensitive; potential problems stand out and can be found and documented in real time.
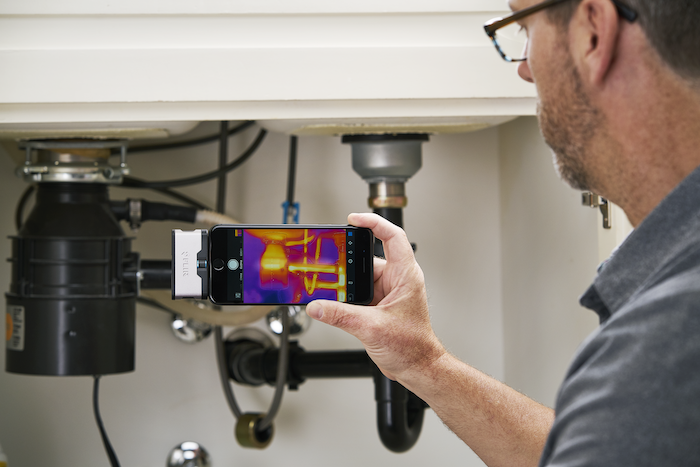
Thermal imaging camera in action.
Home inspectors were the first to adopt the use of thermal imaging, but all the building trades are now jumping on board. Most recently electricians, HVAC technicians, and plumbers have started to use thermal imaging to find problem areas quicker—and from a safer distance. In essence, thermal imaging can be used by all trades – if they are not using it now they should start using it.
The number one application contractors use thermal imaging for is to locate energy loss in hotter and colder months caused by missing insulation and poor sealing around doors and windows. Interestingly, the number two use is to locate pest infestations, including termites and rodents. While thermal imaging cannot “see” a single termite, it is excellent for locating termite nests, because of the massive amount of heat generated by huge numbers of termites living together. The third most common application is for detecting water intrusion in houses and business. Thermal imaging points contractors in the right direction, and moisture meters are then used to isolate the problem.
One other essential feature of thermal imaging is that it can be used to document issues to show customers. As a contractor who works closely with clients, I believe it is absolutely crucial that customers have a clear and in-depth understanding of what is going on with their project. Thermal imaging gives contractors the ability to proactively bring up and demonstrate issues. If the issue is something they should be concerned with, it is important to be able to document that issue with a picture or video. The more information homeowners have, the better off they will be.
Pairing thermal imaging with moisture meters offers a one-two punch
Recently, many in the building trades have begun to realize the benefits of pairing thermal imaging with moisture meters. This combination is especially effective because thermal imaging by itself does not distinguish between cold temperatures and moisture. Both show up as a dark blue image, so contractors cannot tell if the image indicates moisture or cold air. Using the two technologies together, they can simultaneously find energy loss and moisture intrusion – giving contractors a real one-two punch.
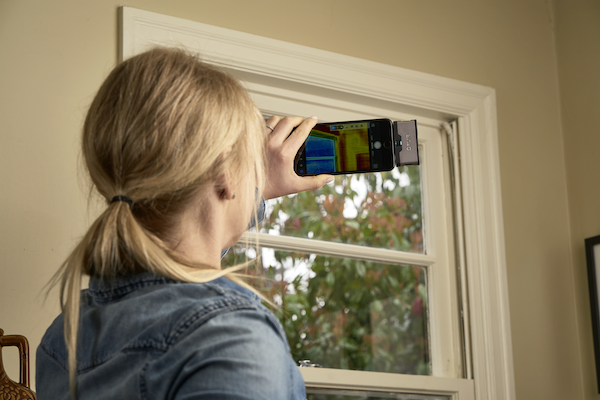
Thermal imaging can reveal issue regarding missing insulation or poor sealing around window or door.
Using thermal imaging to find the issue and the moisture meter to verify it saves time – by taking the moisture meter to the area of concern a contractor can isolate the problem and quickly determine its seriousness and extent. Before the ability to pair the two technologies, contractors had moisture meters, but they had to tear the entire wall down to address a suspected problem. Using the non-contact or non-invasive/non-destructive detection methods together helps contractors confine the problem to a smaller area so they can avoid taking that wall down. The moisture meter will indicate if the spot is a matter for concern.
New affordable technology makes combining thermal imaging and moisture reading a snap
In the past few years I have been bringing thermal imaging and moisture reading equipment to every job site I visit. I use the FLIR ONE® PRO thermal imaging camera attachment in combination with the FLIR MR40 moisture meter. Both are extremely easy to use, which is especially helpful for those contractors who are not particularly tech savvy. You can attach the thermal camera to your smart phone, and the phone becomes the viewer.
I started using FLIR thermal imaging technology some years ago and this latest third generation technology has significantly improved, with even better image quality. At a cost of only $399, the FLIR ONE Pro is much more affordable for contractors than in the past. It also pays off quickly because of the money saved by finding problems more quickly.
Especially useful is the multi spectral dynamic imaging (MSX) technology, which enables users to overlay the visual with the thermal to get a clear image that the contractor can then decipher. This means users are not just seeing a screen of colors, they are seeing the definition of what they are looking at.
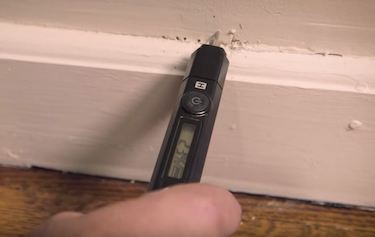
FLIR MR40 moisture meter in use.
MSX incorporates real-time thermal video enhanced with visible spectrum definition. It produces exceptional thermal clarity to highlight exactly where the problem is. MSX ensures easier target identification without compromising radiometric data. The quality of the thermal images is excellent, with almost no need for a separate digital image. With MSX, thermal images look sharper, the orientation of the target is done more quickly and the reports are clutter-free. Users can see the results of MSX technology directly on the touchscreen of the camera, in real time.
Another practical feature of the FLIR ONE Pro is the 1-fit connector. This allows users to adjust the camera’s fit, so they can use the attachment with thicker cell phone cases.
The FLIR MR40 moisture meter is my go-to option, primarily because it is so easy to use. Anyone can operate it easily, even if they have never used a moisture meter before. The portable, rugged moisture meter comes with an integrated flashlight. It is also small and tough, fitting easily in a pocket. I have used it in tight spaces and I have dropped it, and the meter remains accurate and incredibly reliable. It is affordable and a quick tool to find and quantify moisture content. When used in combination with a thermal camera, MR40 can help confirm whether a cold spot in a thermal image is moisture, and measure the severity of the problem. If it measures in the 20 percent range or above, it would be considered a problem. Below 10 percent it would not be considered a problem.
Other all in one imagers plus moisture meter options include the FLIR MR160 and the MR176. With these options there is no need to carry two separate pieces of equipment.
New technology provides contractors with peace of mind
Using the FLIR ONE Pro in combination with the FLIR MR40 moisture meter has made a big difference in my business. I look on them as tools like all the others that would be used on a job, but they are especially important in the initial phase of dealing with customers and quoting jobs. In the past unforeseen issues would arise that would bring higher costs. Now, contractors can virtually see the invisible, reducing unforeseen and unwelcome surprises often costing more money to repair.
As a contractor, the tools provide peace of mind, and also ensure the situation has been thoroughly examined. I never leave home without them.
By Jason Cameron, licensed contractor and host of DIY Network’s Desperate Landscape, Man Caves and Sledgehammer.
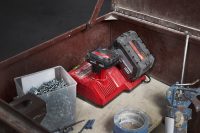
Milwaukee Tool found its “promised land” in tool technology, or its definite game changer, if you will, when it graduated from NiCad to lithium-Ion batteries. “In 2005 Milwaukee turned the power tool industry on its head when we invented the technology that enabled the use of lithium-ion in power tools. This was an achievement the Read more
Milwaukee Tool found its “promised land” in tool technology, or its definite game changer, if you will, when it graduated from NiCad to lithium-Ion batteries. “In 2005 Milwaukee turned the power tool industry on its head when we invented the technology that enabled the use of lithium-ion in power tools. This was an achievement the industry had never experienced before and, while many other companies have utilized this technology to deliver their own cordless systems, we’ve remained at the forefront of lithium-ion technology innovation,” said Babacar Diop, product manager for Milwaukee Tool.
Boy, have they ever. What’s interesting to note is that a couple of years ago Milwaukee was giddy about the launch of its RED LITHIUM High Demand 9.0Ah battery pack shown at its annual New Product Showcase (NPS). Today, Milwaukee shatters that ceiling with a breakthrough with its M18 Cordless System by extending its range of M18 REDLITHIUM HIGH OUTPUT Batteries.
The new M18 REDLITHIUM HIGH OUTPUT XC8.0 and CP3.0 battery packs will join the company’s current HIGH OUTPUT HD12.0 and XC6.0 offerings, establishing new top-tiers of performance for the XC (Extended Capacity) and CP (Compact) battery segments.
All M18 REDLITHIUM HIGH OUTPUT batteries provide 50% more power, run 50% cooler, and offer increased run-time over standard M18 REDLITHIUM batteries, all while being compatible with the entire M18 System of more than 175 tools. Backward compatibility is key as “we can’t abandon any of our existing users,” says Diop.
Milwaukee offers three segments of batteries, optimizing performance designated as:
- CP — powerful, with less weight for reduced user fatigue and smaller size to better fit in tight spaces.
- XC— more power and run-time versus CP, a great balance of performance and weight for a wide variety of tools and applications.
- HD— the most power and run-time, ideal performance for high demand applications and stationary tools.
Concurrent to the HIGH OUTPUT battery release, Milwaukee has launched its M18 and M12 Super Charger. Coming straight from the nearest phone booth, if those even exist anymore, is the new Super Charger, more powerful than a locomotive. Ok, maybe that’s a stretch, but it’s pretty frickin’ powerful, compared to older iterations of chargers, and others on the market today. The new offering charges up to 4x faster—or 40% less charge time—than Milwaukee’s standard chargers, as well as the best combination of charge time and pack life. It’s pretty simple, “the longer tools run, the more they need charging,” says Diop.
The charger leverages Milwaukee’s REDLINK Intelligence to optimize the charge rate based on the battery type and temperature—high performance down to 0 F, and with the High Output HD 12.0 reaching full performance capability at temps as low as -20 F, according to Diop. This all culminates in all HIGH OUTPUT batteries charging in one hour or less, which is pretty significant for today’s jobsite.
When asked recently if Milwaukee found its next battery technology Shangri-la, Diop intomated that the company is not only committed to lithium-ion technology, but it is committed to the best possible technology for its tools. Stay tuned.
M18™ REDLITHIUM™ HIGH OUTPUT™ Batteries
- CP
- HIGH OUTPUT™ CP3.0(48-11-1835) – NEW!
- Launch: April 2019 ($99)
- HIGH OUTPUT™ CP3.02-Pack (48-11-1837) – NEW!
- Launch: April 2019 ($149)
- HIGH OUTPUT™ CP3.0Starter Kit (48-59-1835) – NEW!
- Launch: May 2019 ($139)
- XC
- HIGH OUTPUT™ XC6.0(48-11-1865)
- HIGH OUTPUT™ XC6.0 2-Pack(48-11-1862)
- HIGH OUTPUT™ XC8.0(48-11-1880) – NEW!
- Launch: May 2019 ($199)
- HIGH OUTPUT™ XC8.0 Starter Kit(48-59-1880) – NEW!
- Launch: May 2019 ($249)
- HD
- HIGH OUTPUT™ HD12.0(48-11-1812)
- HIGH OUTPUT™ CP3.0(48-11-1835) – NEW!
Chargers Optimized for HIGH OUTPUT™
- M18™ & M12™ Super Charger(48-59-1811) – NEW!
- Launch: July 2019 ($159)
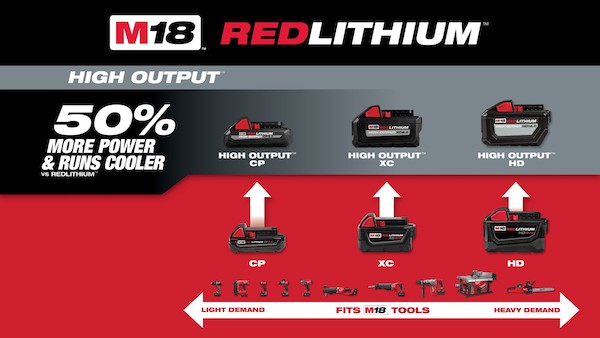
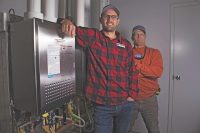
You might say that Joel Iverson was predestined to go tankless in his newest craft brewery in Atlanta. The co-founder of Monday Night Brewing (MNB) — with close friends Jonathan Baker and Jeff Heck — enjoyed first-hand the benefits of tankless water heating technology as a child, growing up in Japan, where he lived for Read more
You might say that Joel Iverson was predestined to go tankless in his newest craft brewery in Atlanta.
The co-founder of Monday Night Brewing (MNB) — with close friends Jonathan Baker and Jeff Heck — enjoyed first-hand the benefits of tankless water heating technology as a child, growing up in Japan, where he lived for 14 years. Limited natural resources in that country inevitably puts a premium on energy efficiency. Meanwhile, limited household square footage favors the small-to-nonexistent footprint tankless routinely provides. (Many Japanese mount their water heaters outdoors.)
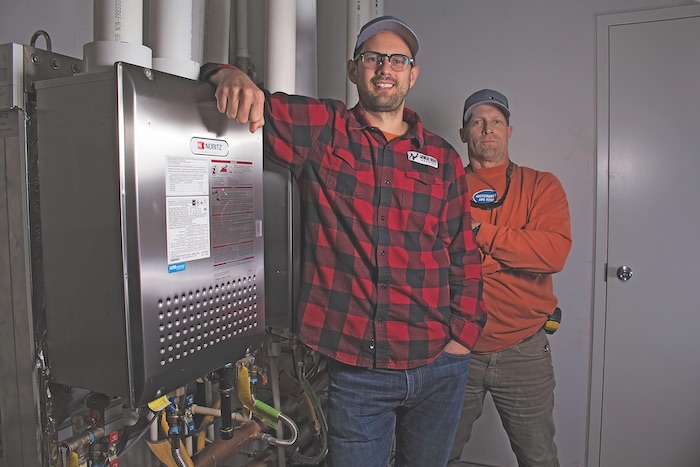
David Hardegree, Owner/Operator, Hard-Cas Mechanical & Home Services (right) and Joel Iverson, Co-Founder, Monday Night Brewing, shown inside the mechanical room at Monday Night Garage with the tankless water heater installation.
But, most important of all, with a properly sized tankless water heater, you never need worry about running short of hot water in the shower.
Returning to the U.S. as a teenager, Iverson and his family reverted to getting their hot water from a storage-tank water heater. “I quickly learned that, if you’re unlucky enough to be the third or fourth person taking a shower every morning, you’re going to be cold,” he recalls. “I could never understand why Americans just didn’t switch to the better technology found in every Japanese home.”
Needed: Very hot water … and lots of it
As it turned out, space savings and even energy savings were not the prime drivers behind MNB’s move to tankless at The Garage, the six-year-old company’s second Atlanta brewhouse, opened last fall. But large volumes of hot water delivered continuously and at consistently correct — and often very high — temperatures definitely were.
Located in the southwest section of the city, the new MNB barrel-aging and souring facility consumes approximately 10,000 gallons of hot water daily in its beer-making processes. For example, water at a temperature of 150°F is combined with barley and hops to produce an enzymatic reaction that yields a sugar. This watery “mash” then is mixed with yeast to become alcohol.
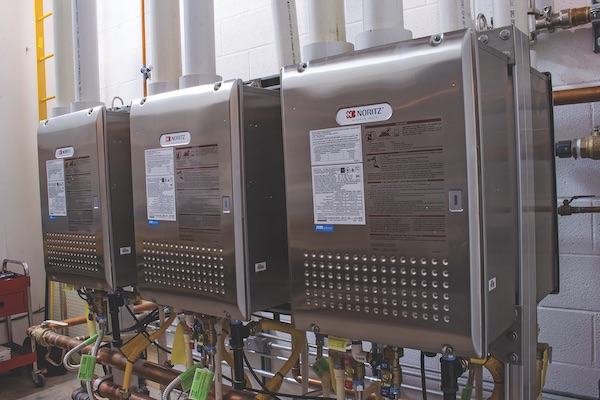
The combined maximum inputs of the five tankless water heaters total 999,500 Btu/hour, meeting not only the brewing and sanitation requirements of the beer production process, but also the general hot-water service needs of the rest of the 22,000-square-foot structure.
Elsewhere inside The Garage, 180°F water is used to steam and sterilize its collection of wine, whiskey and rum barrels that give the various brews their distinctive flavors. “This sanitation of the wood is a critical piece of the operation,” explains Iverson. “We could do chemical sanitation of our equipment, but the best way to ensure a clean and sterile environment is hot water. And by ‘hot water,’ I mean no less than 180°F.”
The solution to these demanding hot-water needs came from Noritz America in the form of five, high-efficiency (95 percent) water heaters. The Model NCC199-DV condensing units were pre-engineered, prefabricated and pre-plumbed with a system controller as a single, integrated package on a metal rack before being shipped intact to Atlanta — resulting in a major savings in installation labor, as we will see. Their combined maximum inputs total 999,500 Btu/hour, meeting not only the brewing and sanitation requirements of the beer production process, but also the general hot-water service needs of the rest of the 22,000-square-foot structure.
Beyond a continuous supply of hot water, two other criteria were equally influential in Iverson’s decision to install tankless: 1) system redundancy to keep the beer flowing and, believe it or not, 2) significantly lower, up-front purchase costs.
No more waiting
MNB’s original 30-barrel brewhouse on Trabert Avenue, five miles north of downtown, gets its hot water from a conventional steam boiler that feeds a 2,000-gallon storage tank. The drawback is identical to what Iverson encountered as a teenager when his family returned from Japan: When the storage tank runs out of hot water, all you can do is… wait. And when the boiler itself breaks down and needs servicing, the wait can extend for a day or two until help and/or a repair part arrive. “In these instances, we cannot do anything,” he says. “There’s no backup.”
All of which led Iverson to contemplate the tankless alternative for the new brewery.
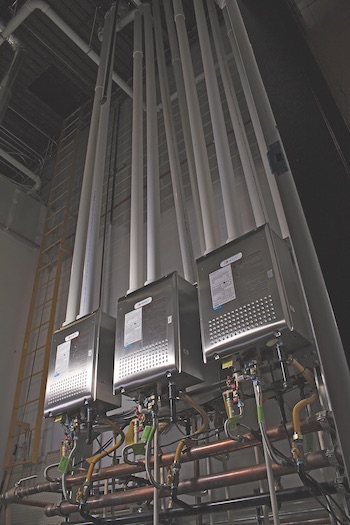
Each of the five tankless water heaters is vented separately with a 20-foot vertical stack of four-inch Schedule 80, high-pressure PVC pipe. Each stack consisted of a pair of 20-foot lengths connected with a Schedule 40 PVC fitting.
While attending a brewing industry conference, Iverson spoke with a fellow brewmaster about MNB’s plans for The Garage and the need for a more reliable source of hot water. Iverson’s new friend mentioned that a number of smaller breweries had taken to experimenting with tankless technology, jerryrigging two or more units together to get the hot water they needed.
Iverson didn’t care for the idea of “hacking” water heaters together to build a makeshift system, but he was intrigued enough to begin researching the possibilities of connecting multiple units to generate the hot water he needed. He subsequently learned that Noritz offered a prefabricated system, including a central controller, and immediately thought: That’s exactly what we need.
“I contacted the manufacturer’s headquarters in California, got with someone in their technical department and walked them through my sizing calculations for the maximum flow rate” of approximately 16 gallons per minute at 180°F. Working back from that metric, Noritz tech support helped Iverson determine that he needed a 1 million-BTU system, with five heaters connected in a series, he says.
Throughout his work with the manufacturer, Iverson and his colleagues never wavered from their conviction that tankless was the right choice, according to Iverson. “Our lone concern was: What happens if a sudden need for an unusually high volume of hot water arises? So we devised a creative way to deal with that in the form of a 150-gallon holding tank,” says Iverson. This backup tank is not absolutely required, but it does provide reassurance and peace of mind.
System redundancy at an affordable price
First and foremost among the factors persuading MNB management they were on the right track with tankless was a sharply lower acquisition cost. Iverson figures a million-BTU steam boiler would have demanded double the price of the prefabricated tankless system, installed.
Prefabrication of the rack system accounted for some of the tank-versus-tankless cost gap, thanks to a dramatic reduction in labor time and expense. Compared with tankless, a steam boiler is a far more complicated, labor-intensive install. “Much of the time and expense is the steel pipe needed to connect the boiler to equipment, all of which must be insulated,” Iverson explains. “Then there are all the relief valves and other safety devices required by code. Steam boilers must also undergo regular inspections by the state, another major cost.”
It’s not a perfect apples-to-apples comparison between a steam boiler and tankless, he admits, but he harbors no doubt about the more attractive economics of the latter. “We should have lower gas bills simply because tankless is on-demand: We won’t be heating water all the time, but only when we need it.” This benefit is somewhat muted by the comparatively low natural gas prices right now, admits Iverson. But “it was the up-front savings in equipment and labor that tipped the scales in favor of tankless.”
The other major attraction for MNB was system redundancy, which should all but eliminate downtime during servicing situations. “Shutdowns are a big negative in any brewery,” notes Iverson, who says the occasions when all five will operate simultaneously should be few. “That means, when maintenance for one unit is required, one or more of the other four will remain online, so we can continue brewing beer.”
Plug-and-play eases installation
If not exactly “plug-and-play,” the prefabricated, pre-plumbed tankless system simplified the installation considerably. Besides mounting the heaters to the rack, three in the front and two in the back, the prefab team also made all the internal water and gas connections prior to shipment. When the unit arrived at The Garage, plumbing installer David Mansfield of Mansfield Contracting Inc. (Conyers, GA) had to make only three connections — hot water, cold water and gas — for the entire assembly, rather than three for each of the five units. Three versus 15: That’s an 80 percent reduction in connections.
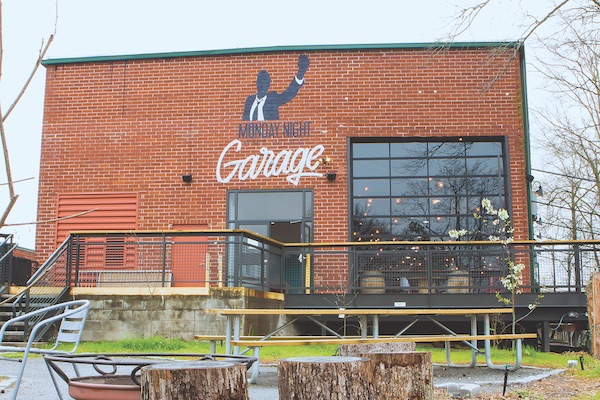
Exterior of Monday Night Brewing’s “Garage” location, with the patio for visitors in the foreground.
As for the controller, the primary concern was to connect each of the five pre-installed cords to its appropriate unit with no wires hanging slack. Otherwise, this prefabbed piece, which can be hung virtually anywhere nearby, typically takes only a half-hour to install.
The gas lines and vent runs were another matter. Owner David Hardegree of Hard-Cas Mechanical LLC (Winder, GA) and project manager Tim Casper installed 3,000 feet of two-inch black iron pipe at The Garage, to service various appliances, including HVAC equipment, 12 gas lamp posts and a fire pit for brewery guests, plus the tankless setup, which needed 1,000 feet by itself. Describing the installation as a “massive undertaking,” Hardegree estimates the gas-pipe installation spanned a week.
Each tankless water heater is vented separately with a 20-foot vertical stack of four-inch Schedule 80, high-pressure PVC pipe. Each stack consisted of a pair of 20-foot lengths connected with a Schedule 40 PVC fitting. The five runs merge at the roof into a specially prefabbed, 3” x 3” x 3” wye fitting. The venting terminates in a five-foot, vertical length of concentric piping, five inches in diameter. The inside pipe, which delivers makeup air, is encased in a slightly wider pipe that removes the exhaust.
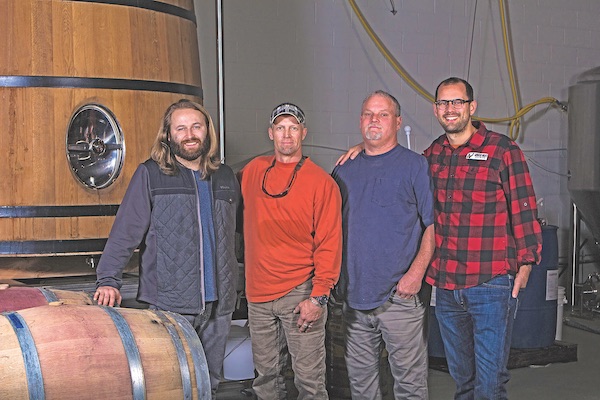
From l to r: Peter Kiley, Head Brewer, Monday Night Brewing; David Hardegree and Tim Casper, Owner/Operators, Hard-Cas Mechanical & Home Services; and Joel Iverson, Co-Founder, Monday Night Brewing.
The venting setup required two days, says Hardgree, “including a day on a scissor lift, after the manifold was set, to rough-in most of the pipe; and a second day, to top it all out on the roof.”
But whatever the challenges of the gas and vent runs, Hardegree has only compliments for the tankless rack system, which had to be carefully squeezed into The Garage’s 8-foot-square mechanical room.
“It was a tight fit, no question,” he remembers, “but once the rack was in place, the heaters themselves were ready to go. If we had to mount each of them on the wall, we might’ve needed another week. Prefabrication made the installation so much easier — whoever came up with the idea of that rack is a genius!”
Return to their roots
Hear the name, and you might well conclude that Monday Night Brewing must be connected to football: a bunch of “bros” watching the pros on TV, September through December. In fact, the venture began as a pastime for the three founders who were all members of the same church in Atlanta. They would meet on — of course — Monday nights, not to watch football, but to taste each other’s latest brews and revel in the camaraderie.
“We were all white-collar dudes doing our day jobs,” says Iverson, “but always pointing to what we’d be brewing come Monday night. Instead of dreading Mondays, we actively looked forward to them.”
But after opening the “West Midtown” brewhouse on Trabert in 2011, their hobby and passion quickly transformed into a major business enterprise with all the pressures and complications that accompany rapid growth. The focus inevitably turned to making “big batches of beer and improving our efficiencies,” says Iverson. Business success certainly has its satisfactions. But the founding trio found themselves drifting away from their original intent: To foster fun, innovation and, above all, “deepening human relationships over some of the best beer in the country.”
Thus, The Garage is in many ways a return to the founding spirit of Monday Night Brewing, Iverson explains. Built along one of the country’s largest urban renewal projects, the new Westside Beltline trail, it features a public tasting room with a patio for touring guests, plus an adjacent “urban orchard” for brewing beers the old-fashioned way, via wild fermentation. Most important of all, there’s simply more room under roof.
“We have all this additional space for multiple barrel-aging and souring rooms to experiment with the sort of specialty beers that have won us so many awards,” says Iverson. “Originally, the idea seemed a little crazy, but viewed within the context of our main mission, it clearly was a step we had to take.”
In that regard, high-performance tankless technology is a good fit for an innovative enterprise committed to excellence through creative experimentation. You cannot brew beer without lots of hot water; and you can’t brew “some of the best beer in the country” without a first-rate and dependable water heating system.