By Jana Summey A few months after the “reopening” of the economy, understandably, business owners and government officials welcomed a return to normalcy. However, new and different risks are faced when reopening dormant buildings with stagnant water systems. Several weeks of zero flow, low flow, and tempered water can result in microbiological growth, leeching heavy Read more
COVID-19
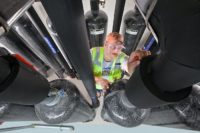
By Jana Summey
A few months after the “reopening” of the economy, understandably, business owners and government officials welcomed a return to normalcy. However, new and different risks are faced when reopening dormant buildings with stagnant water systems.
Several weeks of zero flow, low flow, and tempered water can result in microbiological growth, leeching heavy metals, and corrosion within our plumbing systems.
Planning is key
Let’s take a close look at steps building facility managers should consider in order to maintain water quality and safety in plumbing systems of unused or slightly used buildings (as defined by industry organizations including NSF International, Centers for Disease Control and Prevention (CDC), and the International Association of Plumbing & Mechanical Officials (IAPMO).
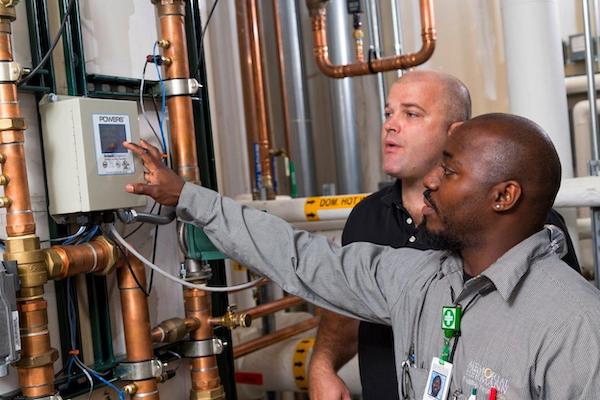
The IntelliStation digital water mixing system delivers mixed hot water throughout a hot water recirculation loop in commercial and institutional facilities. This digital solution can be integrated into a building automation system (BAS) to allow facilities managers to remotely monitor and control water temperatures.
Begin by documenting protection measures for staff and visitors. Consider working with a water quality expert or consultant. And, ask the local water utility the following questions:
- Have there been any recent water supply disruptions?
- Have standard checkpoints been inspected?
- What is the current disinfectant concentration?
If one isn’t already in place, create a map of the building’s plumbing system.
Before the initial flush, sketch out the building water system to identify low-use water outlets. Map out a flushing regimen in a unidirectional process starting at the water supply’s point-of-entry, to the peripheral distalpoints, and point-of-use outlets such as faucets and showerheads.
In large buildings, the water supply is often designed in zones and branches, such as different wings. Typically, each wing or set of branches will be served by the same riser. When mapping out the plumbing system, always start from the outlet nearest the water supply and proceed to the most distal outlets. Along this route, the flushing regimen should include the entire recirculating loop, both cold and hot water, all associated equipment and appliances, and all outlets including faucets, showerheads, eye wash stations, ice machines, hot tubs, therapy pools, and water features.
Establish or reestablish a flushing and cleaning regimen. Flushing is important because it clears out the low-quality water that accumulated during low use and replaces it with high-quality water from the municipal supply. The fresh water helps mitigate loss of protective scale as well as biofilm growth that emerged while the water was stagnant.
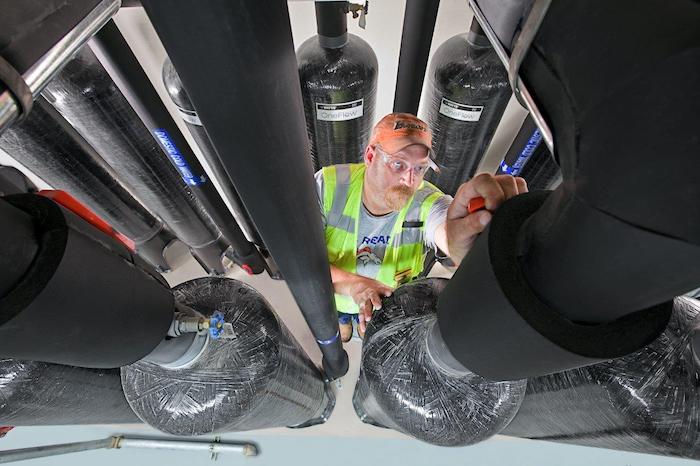
After the initial flush, ongoing flushes should be scheduled; continual flushes help to repair destabilized scale and minimize biofilm growth. Watts’ OneFlow System, shown here, uses a specially designed media where scale forming molecules are transformed into harmless crystals that won’t stick to pipes and components, eliminating scale for good.
These conditions need to be addressed because they proliferate the growth of Legionella and other waterborne pathogens, creating a high-risk environment for those with compromised immune systems. Proper flushing is a multi-step process including an initial flush, sequenced flushing, cleaning of fixtures and equipment, testing and monitoring, and additional flushing as needed.
Initial flushing and cleaning must be completed before resuming normal building operations. The sooner flushing is begun, the better. If possible, have staff start flushing now, even if the building’s reopening date is still unknown. The earlier a flushing regimen is initiated, the sooner water quality will return to normal. Prior to flushing, appropriate training for staff should be completed and PPE (personal protective equipment) should be provided. Guidance for this can be found on OSHA’s website.
It’s vital to flush the entire piping system from point-of-entry to point-of-use. This includes all water outlets, utility sinks, hose taps, piping currently used, as well as piping and fixtures in place for future installations. However, it doesn’t hurt to take special notice to the parts of the water system that have the greatest opportunity to make people sick. These include:
- Faucets used for drinking water or food preparation
- Drinking fountains
- Ice machines and refrigerators with ice makers
- Showers
- Kitchen sink sprayers
- Water features that generate aerosols (fountains, spas, etc.)
- Parts of the water system used by children, the elderly, and other susceptible people
An initial flush clears out contaminants that accumulated during stagnation and draws in fresh, high-quality water to the piping. Cleaning the fixtures removes contaminants from the complex internal structures at the point of discharge. Flushing requires an initial flush to get out low-quality water and contaminants, and follow up flushes that may bring the building back to pre-COVID-19 water quality. Ongoing flushing draws particles through and out of the system and brings in disinfectant from the municipal system that can help control biological growth. The longer service is interrupted, the more effort will be required for restoration.
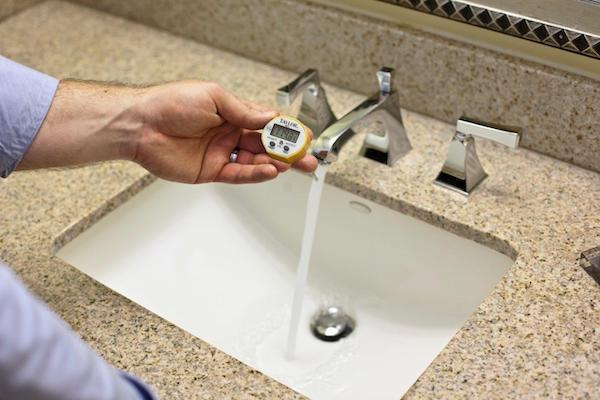
Once the building is reopened, conduct normal process of ensuring tempering valves are maintaining the desired temperature.
Flush zone by zone, starting with the zone closest to the water building supply. In each zone, start with the cold water plumbing first, followed by the hot water. Within the zone, open taps starting with the outlet closest to the zone origin, working toward the farthest point. Flushing should not end until the farthest point-of-use tap has flushed for a minimum of five minutes, and the cold water temperature at the most distal tap is constant.
In order for flushing to be most effective, consider the following:
- All valves should be in a fully opened position during the entire flushing process
- All aerators should be removed. If continued use is planned, clean or replace the screens prior to reinstalling the aerators
- Showerheads and faucets should be disinfected and sterilized. Consider replacing outlets if vulnerable populations have access
- Prior to operating the system after flushing, adjust valves back to normal operating positions
As part of the flush, all locations where water is stored should be identified, drained, and flushed with clean cold water. Examples include humidifiers, ice machines, and dishwashers. Most buildings have some form of water treatment in their plumbing system such as filters and water softeners. These should run as normal, be included in the flush, and should not be bypassed.
Once flow has returned after this initial flush, all hot water tanks should be drained. Temperature should be maintained, and the heater should not be turned off. Continual operation is important to prevent microorganisms from growing. Make sure that water heat storage temperature are sufficient to kill bacteria (131 to 140°F).
After the initial flush, ongoing flushes should be scheduled; continual flushes help to repair destabilized scale and minimize biofilm growth. The American Water Works Association (AWWA) recommends continued flushing for a minimum of 12 weeks. This allows the protective scale to re-stabilize and for harmful lead particles to be washed through the plumbing system.
Recommendations for ongoing flushes include:
- Open each point-of-use tap at least once per day
- Flush the entire building once per week during ongoing flushing
- It is not necessary to drain water storage during ongoing flushing
- Continue to flush the cold and hot water systems separately; cold first, hot second
Monitoring and testing
Monitoring and testing should start for Legionella, other bacteria growth, and disinfectant levels prior to the initial flush, throughout the ongoing flushing, and on a predetermined schedule going forward. Monitoring and testing are the only ways to know the health of the plumbing system.
At the end of the initial flush, disinfectant levels should be checked. The concentration level of chlorine, the most commonly used disinfectant, should be measured at the point-of-entry and in the cold water of the most distant tap of each zone after the tap is flushed. Comparison of the point-of-entry concentration to the distal tap concentration will give an indication of the protection being provided to the entire plumbing system.
If other disinfectants are used, such as monochloramine, be sure to measure and compare its concentration at point-of-entry and distal outlets. Water temperature should be regularly tested and recorded.
The system should be tested for Legionella by a certified laboratory. Many facilities will choose to work with a consultant for this process. Samples should be collected at least 48 hours after final flushing and return of normal operation of the water system. Multiple samples should be collected to ensure accuracy and prevent false negative results. Samples should be taken at multiple locations throughout the system, from point-of-entry to point-of-use.
Hyperchlorination or shock disinfection should be conducted if testing proves unacceptable levels of Legionella. This is where a higher than normal level of chlorine is flushed through the plumbing system for a specific length of time, and the water temperature is raised for rapid kill. The cold water system should be flushed from point-of-entry to point-of-use, including all fixtures. The water should reach a CT of no less than 3,000 mg-min/L. “CT” value is the concentration of disinfectant and contact time with the water being disinfected.
Systems that have high levels of Legionella, or are known to have heavy biofilm, may require even higher CT targets. Higher chlorine dosage may allow for shorter disinfection contact times. Always take proper precautions to ensure there is no inadvertent exposure to occupants. Strict access controls should be in place. Conduct testing to ensure chlorine levels are in normal ranges at the conclusion of treatment. When hyperchlorination is complete, the system should go through an additional thermal flushing.
Even if unacceptable Legionella levels are not found after thermal flushing, hyperchlorination should still be considered, especially in buildings where high risk or immune compromised populations could be exposed.
Following, adjusting, and creating a water management plan
A facility management team should record all monitoring and testing practices including the frequency, locations, and results. If there is a water management plan, those findings should be integrated into the record keeping portion of the plan. If a water management plan does not exist, we strongly encouraged the creation of one. Most healthcare facilities are required under the Centers for Medicare & Medicaid (CMS) mandate to have a water management plan. Failing to do so can cause a facility to lose Medicaid and Medicare reimbursements.
Implementing a water management plan as outlined in ASHRAE 188 will help maintain a high-quality level in a building. The Centers for Disease Control (CDC) has developed a water management plan toolkit based on ASHRAE 188. The toolkit aids in the understanding of risk levels of different building types and devices and walks step by step through the requirements of a healthy water management plan.
Maintenance and Recommissioning
As part of the process of reopening a building, all mechanical equipment should be inspected. Examples include cooling towers, boilers, pumps, backflow preventers and digital mixing stations. Essentially, the water systems and equipment should be recommissioned as if it were a new building. Make sure any scheduled maintenance that may have been missed during building closings are completed and recorded in accordance with normal practices.
Some general guidelines include:
Digital thermostatic mixing
During/before closing
- Drain the piping system prior to closing if planning for a long-term building closure
- If draining the system isn’t an option, increase production and storage of hot water above 150° F, and keep the building pump running at full temperature by bypassing a TMV or setting the DMV to full hot
- Conduct a periodic purge of all dead legs to keep the system reasonably clean
At reopening
- Conduct either a high temperature water purge, hyperchlorination shock, or both
- Generally, calibration of mixing valves is not needed
- Once the building is reopened, conduct normal process of ensuring tempering valves are maintaining the desired temperature
Backflow
- Conduct a visual inspection
- If the water supply was completely shut off and the pressure decreased, all reduced pressure zone units need to be repressurized correctly, and the relief valve should be closed
- All pressure breaker valves also need to be repressurized correctly and the relief valve should be closed.
- The pressure breaker valve should be spill resistant, but it should still be checked
Gas connectors
- Assuming equipment has been turned off, a device such as FloPro™-MD can assist with a startup check to ensure each piece is operating at manufacturer’s specification
- Verify proper gas supply to any gas burning appliance with a BTU rating of 325,000 BTU’s or less, whether it is in a commercial kitchen or not
Drainage systems
- For general drains, there are no special requirements. However, a visual inspection should be part of the reopening plan
Stainless steel piping and drainage systems
- Other than the absence of water in the traps from either back siphonage or evaporation, stainless steel piping systems require no special considerations when being returned to full service after periods of non-use
- Stainless steel pipe and fittings are resistant to corrosion caused by decomposition of organic matter and the subsequent formation of hydrogen sulfide gas or microbiologically-influenced corrosion
Rainwater harvesting
- Purge the system via the hose bibs or flush out the system by opening the flush valves to create a steady flow of water
- Check the tanks to ensure the aerator is functioning and the inlet pre-filter is in service
Water quality solutions
For most water quality devices, it is a good idea to flush the unit. However, it’s always best to consult manufacturer guidelines for each device.
UV systems
- Inspect to ensure the light is working correctly
- Check to make sure any scheduled maintenance wasn’t missed
- Visually inspect the vessel
Sediment/point-of-entry filtration
- Visually inspect
- Clean any clogs and replace filters when needed
Point-of-use filters
- Visually inspect
- Clean any clogs and replace filters when needed
- Check to make sure any scheduled maintenance wasn’t missed
Measuring instrumentation
- In measuring instruments such as the CIX Instrument from HF scientific (chlorine measurement), there is a potential for reagents to crystallize in the tubes if there is a sudden loss of power or power is off for an extended time
- During inspection, in the rare event that crystallization has occurred, the unit needs to be primed and reagents replaced
Snow melt
- The snow/ice detector should be cleaned with soap and water
- Inspect the control display to ensure there are no error messages due to faulty sensors
Water Heaters
- Determine if the manufacturer recommends draining the water heater after a prolonged period of non-use
- Ensure that all maintenance activities are carried out by professionals or according to the manufacturer’s instructions
- Make sure the water heater is set to at least 122°F and consider higher temperatures (131°F -140°F) for a quicker kill
- Ensure that measures are taken to prevent scalding if the water heater is set to >130°F
- Wipe down the outside and control with disinfectant
- Conduct proper startup by authorized service agent
- Conduct a significant blowdown of all components
- Check combustion and calibration, perform all safety device testing, and verify all system operating parameters are correct and functioning
Additional Equipment to Be Inspected:
Hot tubs, spas, therapy pools
- Check for existing guidelines from local or state regulatory agency(ies) before opening for use
- Visually inspect for slime and biofilm prior to refilling
- Perform a hot tub/spa disinfection procedure before use per CDC guidance
Cooling towers
- Revisit startup and shutdown procedures
- Follow manufacturer guidelines and industry best practices
- Visually inspect for slime and biofilm prior to use
- Assuming the cooling tower has been well maintained, proceed with disinfection procedures. Guidance can be found from the Cooling Technology Institute: http://www.cti.org/downloads/WTP-148.pdf
Maintaining system after reopening
Planned and detail cleaning should be part of the reopening process. This includes proper maintenance of all equipment and fixtures, and the replacement of filters from point-of-entry to point-of-use. Be sure to follow manufacturer guidelines and contact the proper authorities when necessary.
Twenty-four hours before reopening the building, it’s recommended to conduct a round of checks. Bring the hot water system back up to 140° F. Open all outlets and flush until they reach a minimum of 131° F. After flushing, conduct a final round of sampling to ensure there is no contamination.
Once the building has resumed normal operation and the water system is back to standard function, the main priority will be maintaining water system quality and safety. If there is no water management plan prior to the disruption, create one immediately. This should include a schedule for monitoring and testing disinfectants, bacteria levels, and water temperature. Follow the plan, document activities, and adjust as needed. If an issue arises, promptly address it and notify authorities if deemed necessary.
If the building is scheduled to reopen within one month, continue a normal control regimen if possible. If the time to reopen the building is unknown, or if its scheduled to reopen longer than 1 month away, there are precautions that can be taken during that time to increase water quality prior to pre-open flushing and chlorination.
Consider the following:
- Conduct low-usage weekly maintenance
- Conduct weekly visual inspections
- Initiate operation of moving parts such as pumps for at least 10 minutes per week to prevent seizure and failure
- Increase water temperature to 140° F for at least 1 hour per week to reduce bacteria growth
- If equipment such as a water heater has a thermal sterilization cycle, utilize it per manufacturer recommendations
- Maintain normal disinfectant levels
- Flush outlets on a weekly basis
- Ensure all storage maintains proper disinfectant levels
- Document all activity, monitoring, and testing
- If it is decided to close certain systems, drain and dry if possible
If the decision has been made to not heat water within the plumbing system during closure, then consider the following:
- Close the building and do not drain the system
- Turn off storage tanks, drain, and the water supply
- Consider conducting thermal flushing and hyperchlorination prior to shutdown
If a building is not being fully shut down but will be under low-use conditions, consider the following options to maintain the system:
- Flush cold water systems on a regular schedule to maintain temperature and disinfectant. Free chlorine residual should be at or above .2 mg/L
- Monitor and maintain the hot water system at distal outlets
- Monitor and record supply water temperature and disinfectant concentration
- Restrict access to any unused portions of the building
- Document all monitoring, testing, and maintenance
Additional Resources
There are a multitude of tools and guidance to assist in maximizing water safety and minimizing water risks when preparing to reopen an unused or slightly used building:
- CDC Toolkit: https://www.cdc.gov/legionella/wmp/toolkit/index.html
- Preventing Legionnaires’ Disease: A Training on Legionella Water Management Programs: https://www.cdc.gov/nceh/ehs/elearn/prevent-LD-training
- Hotel Guidance: Considerations for Hotel Owners and Managers: How to Prevent Legionnaires’ Disease: https://www.cdc.gov/legionella/wmp/hotel-owners-managers.html
- From Plumbing to Patients: https://www.cdc.gov/hai/prevent/environment/water.html
- Preventing Occupational Exposure to Legionella: https://www.cdc.gov/niosh/docs/wp-solutions/2019-131/default.html
- CDC Model Aquatic Health Code
- CDC Healthcare Water System Repair and Recovery Following a Boil Water Advisory or Disruption of Water Supply
- ASHRAE Standard 188: Legionellosis Risk Management for Building Water Systems
- ASHRAE Guideline 12: Minimizing the Risk of Legionellosis Associated with Building Water Systems
- Cooling Technology Institute Legionellosis Guideline 2008 (WTP-148)
- Cooling Technology Institute Legionellosis Guideline 2019 (GLD 159)
Learn more about ensuring safety in commercial buildings by mitigating the risk of Legionella and other waterborne bacteria at www.legionella-strategies.com.
Jana Summey, MBA, Watts Healthcare Vertical Market Manager, has nearly 20 years’ experience in the MEP (mechanical/electrical/plumbing) design and architectural design industries. She is a popular speaker on mitigating Legionella through a multi-barrier approach in on-premise plumbing systems – from point of source to tap. Recently Jana navigated her mother through the experience of being exposed to Legionnaires’ as a hospital patient, gaining valuable insight into the serious threat Legionella poses for at-risk populations.
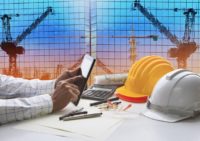
In July 2020, we ran a feature highlighting the release of Marcum LLP’s first annual Marcum National Construction Survey. Overall, the survey reflected a fairly positive outlook by respondents about the current and future state of the industry, despite the COVID-19 pandemic. The survey was conducted in the first quarter of 2020 by Marcum’s national Construction Read more
In July 2020, we ran a feature highlighting the release of Marcum LLP’s first annual Marcum National Construction Survey. Overall, the survey reflected a fairly positive outlook by respondents about the current and future state of the industry, despite the COVID-19 pandemic.
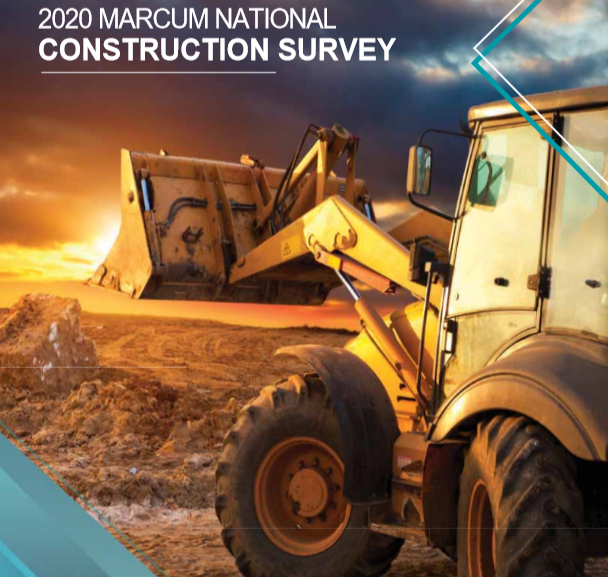
The survey was conducted in the first quarter of 2020 by Marcum’s national Construction Services group, a premier provider of accounting, tax, and advisory services to the construction industry.
According to Joseph Natarelli, Marcum’s national construction industry leader, said, “The industry was well-positioned prior to the pandemic, even with a potential recession looming. Those going into COVID-19 with weaker balance sheets will be negatively impacted. We believe that as long as firms work with their internal teams and professional advisors to address labor safety issues and material sourcing, and have a pandemic plan in place, they will come out of this in good shape.”
We recently conducted a Hub Chat with Mr. Natarelli to expand on the survey, industry trends, hot button topics as well as discuss his direction of Marcum LLP’s Construction Services Group, which is dedicated to assisting contractors with personalized and attentive service, strong technical expertise, and uncompromising integrity.
Mr. Natarelli is leader of the Firm’s national Construction Industry Practice group, as well as the Firm’s office managing partner in the Long Wharf Drive office in New Haven, Connecticut. In addition, he is a member of the Firm’s Management Committee. Natarelli has more than 30 years of experience with international accounting and consulting firms. He frequently serves as the lead audit engagement partner for a variety of consulting matters.
Mr. Natarelli frequently speaks on accounting and auditing matters. For more than two decades, he has served as a technical reviewer for the AICPA’s Audit Risk Alert for Real Estate and Construction Industry Developments and the AICPA Audit and Accounting Guide — Construction Contractors.
He has been interviewed by a number of prestigious media outlets including the Wall Street Journal, Bloomberg, Businessweek, Fox Business and now, Mechanical Hub Media.
The following is our Hub Chat with Mr. Natarelli.
MH: Thanks for taking some time to chat with us. What’s the Marcum LLP elevator speech and how does your team create construction curriculum for construction contractors and industry observers such as the National Construction Survey, which we shared with our readers last month?
JN: Marcum is a top national accounting and advisory firm that places a high value on being industry experts and resources for our clients and friends in the marketplace. We know contractors can get their basic financial reporting needs met at a lot of firms but what sets us apart is our commitment to excellence and leadership in their specific sector. This mission is further realized in a curriculum of in-depth thought leadership, instruction, benchmarking and more. For example, our nationally renowned Chief Construction Economist, Anirban Basu, provides hard data and analysis about and for the construction industry each quarter to our subscribers.
MH: Tell us a bit about yourself – how long have you been involved with Marcum, focused on Construction Services and what has your journey looked like up to this point in your career?
JN: For over 10 years, I have served as the Firm’s office managing partner in New Haven, Connecticut, and the leader of our National Construction Industry Practice group. I previously served as the national construction leader at UHY LLP before the UHY’s New England region merged with Marcum in 2010. I have over 30 years of experience with providing auditing and consulting services and remain a resource on various construction projects, offering expertise on job performance and enhancing profitability to contractors. I also spend my time providing thought leadership on accounting and auditing matters for various industry events and publications, and I have served for more than 10 years as a technical reviewer for the AICPA Audit and Accounting Guide – Construction Contractors and the AICPA’s Audit Risk Alert for Real Estate and Construction Industry Developments. I had the privilege of chairing the AICPA National Construction Program Conference Committee from 2012-2014. With one of the best teams in the industry, I have helped lead Marcum to become a top national accounting services leader for contractors.
MH: The COVID pandemic has created disruption and uncertainty across all segments of society, how is Marcum working to address issues that affect construction markets such as loan programs, taxing issues, and business interruptions?
JN: In a crisis, people need answers and they need them right away. Marcum established a Coronavirus Resource Center in mid-March and has been producing timely and essential thought leadership specific to the construction industry, ever since. Whether that takes the form of an alert, a tax flash or an in-depth webinar, our construction industry clients and other subscribers have access to the newest information available via the resource center. We have been leading the charge with our construction clients to make sure that they are taking full advantage of governmental programs that can support and preserve their businesses during this difficult time. At the end of the day, we know that our clients aren’t just companies, they are people who have worked to provide for their families and communities for years and we will do everything in our power to see that they make it through this intact.
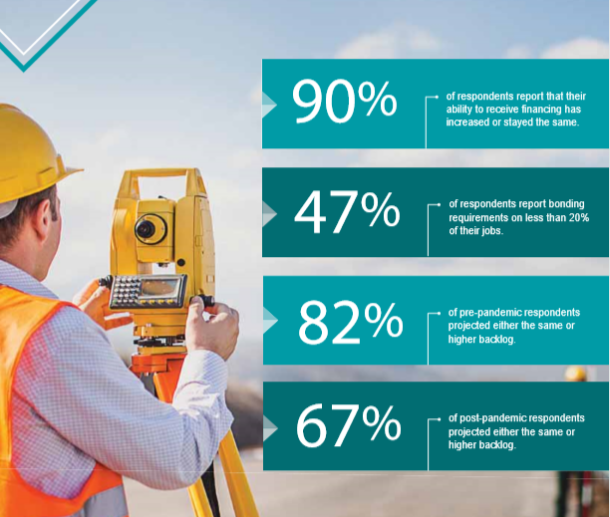
MH: As we started 2020 the construction market had seen significant growth over the past 5+ years, how is the current economic climate affecting the industry? What are some of the challenges and how is Marcum addressing those challenges? How can contractors use market data to set their business in a better direction?
JN: The crisis has really put a spotlight on challenges that have been haunting the corners of the industry for a while. Specifically, the labor shortage. In our quarterly Marcum Commercial Construction Index we’ve seen access to skilled labor bubble up to the top of the challenge list for the past few quarters. While unemployment is up in general, a lack of an organized trade educational system and other factors have put commercial contractors in a vice where there aren’t enough workers to execute all of the jobs they have and those that are available are being paid at a premium. Our annual JOLT survey is an essential tool for contractors to reference as it indexes wages across subsectors and positions and would be a valuable benchmark.
MH: Tariffs and trade policies are hot button topics as we get deeper into the election year. What are a few trends you’re seeing based around the election or how is the election affecting the market?
JN: The threat of trade war and an uncertain diplomatic future with China can have a bottom line impact on construction contractors, today. For example, tariffs on essential material such as steel or aluminum can cause hard cost price increases. The global pandemic has also choked off or threatened to choke off supply chain routes and sources – another area worthy of concern and, more importantly, innovative solution. Industry best practice should be to secure your key materials from a geographically diverse but still economical set of sources, lock in your pricing, and get those goods stateside and on the jobsite, ASAP.
MH: How is Marcum addressing environmental issues in the industry?
JN: The construction industry has been at the forefront of changing the way America interacts with its environment, since the beginning. Whether it is the use of innovative materials, high tech insulation techniques, green technologies, water recapture, or the reclamation of abandoned or “brown field” land for redevelopment, there is someone in a hardhat making it happen. Aside from the obvious social capital that helping the environment provides, there are credits and incentives from the government which construction contractors can take advantage of to align their environmental goals with their financial success. We work with numerous clients in that exact position and it can really make a difference.
MH: What are a few trends that Marcum has identified in the industry?
JN: There are several issues and trends Marcum has identified in the construction market. These include ESOPs, revenue recognition, cybersecurity, succession planning, burden analytics, SALT consulting, valuations, due diligence & quality of earnings, public private partnerships and Section 179D energy deductions. Additionally, we have identified 3 trending categories for construction: technology and innovation (i.e., project management software, building information modeling, drone usage, green design & construction technology, improved safety equipment), profitability (i.e., growing material costs, maximizing labor while decreasing labor force, targeting Gen Z in the work force, analytics and data) and sustainability (preservation of the environment, efficient use of resources).
MH: How do you see Marcum helping to create change in the future?
JN: Marcum, as a firm, has embraced technology in all parts. For our clients, we take the same approach. Whether it be through software consulting, robotic process automation, cloud computing or other new tech, we’re always looking to help our clients improve their processes and increase their profitability.
MH: What are some of the things you’re doing to boost Marcum’s visibility and grow market share?
JN: Marcum’s Construction Group is proud of their long history of membership and leadership with all of the major national and regional construction trade organizations. We just can’t overstate how important it is be shoulder-to-shoulder with your clients in the places where they play. To see and be seen. Of course, we hope that our commitment to the creation of business-critical content such as the Marcum Commercial Construction Index, the JOLT report, the national Marcum Construction Survey, our newsletter and flashes also helps keep us in front of decision-makers and position us for growth with them. We also host our own large-scale industry events in several regions, the Marcum Construction Summit. Our events are dedicated to updating construction contractors and finance and accounting professionals on the economic state of the construction industry. The Summit features high-profile, nationally recognized speakers who are experts in the construction arena.
MH: Crystal ball time, what’s 2021 and 2022 look like in the construction industry after all the turmoil of 2020?
JN: The long-term effects of COVID-19 are unknown, and the future of the construction industry is uncertain; however, we remain optimistic. Pre-COVID, 72% of economists were predicting a recession would occur by the end of 2021. As such we were encouraging firms susceptible to business cycles to take steps in building up cash reserves and strengthening relationships with bankers and insurers to prepare for 2022 and 2023. However, the pandemic affected the economy at a faster pace than expected and moved up the predicted timetable. With the country slowly reopening and with the hopes of a vaccine in early 2021, we are now more optimistic about the construction industry in late 2021 and 2022.
MH: In closing, is there anything you’d like to add?
JN: Stay the course, continue the blocking and tackling. We are going through a tough time but we are optimistic moving forward.
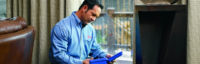
Now more than ever, homeowners are looking for alternative ways to safely address seasonal maintenance needs and/or home repairs given changes to standard procedures set in place due to the COVID-19 pandemic. From social distancing protocols to mask requirements, home visits provide new challenges. The HVAC industry has worked quickly to adapt to this new Read more
Now more than ever, homeowners are looking for alternative ways to safely address seasonal maintenance needs and/or home repairs given changes to standard procedures set in place due to the COVID-19 pandemic. From social distancing protocols to mask requirements, home visits provide new challenges. The HVAC industry has worked quickly to adapt to this new normal. Our professionals continue delivering necessary services to homeowners in a safety-first way, especially as we enter peak cooling season, to ensure HVAC systems operate smoothly and are prepared to withstand the summer heat.
With new precautions in place that impact in-person maintenance appointments, the need for digital dealers with remote solutions has become more urgent. Digital remote technology provides technicians with resources to streamline the service process, which enables an HVAC technician to investigate a system from afar with the safest and most cost-effective strategies. Further, the rise of the digital dealer and remote capabilities reinforces how smart technology can bring homeowners convenience, comfort and peace of mind.
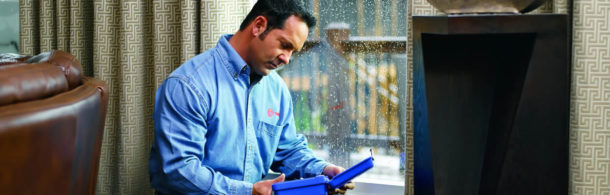
As a trusted HVAC partner, we can share tips for approaching cooling season more efficiently through remote diagnostics.
Stay in tune with the latest remote diagnostic capabilities
- Take advantage of training programs to better understand how the remote diagnostic programs operate. Learn how/when to use these offerings to determine if an in-person visit is necessary, or if the issue can be resolved without having face-to-face contact with the homeowner. These programs offer a more holistic explanation of remote diagnostics, allowing you to add more tools to your virtual toolbox. Also, it’s important to stay in touch with your network to learn about future training opportunities, as well.
Clearly communicate the benefits of digital offerings to the homeowner
- Many homeowners assume that HVAC updates or fixes can only be handled by having a technician physically enter their home. In the era of COVID-19, there is heightened concern as to how safe it is to have someone entering the house, particularly when an immune-compromised person is living in the household. With remote diagnostics and the homeowner’s permission, it’s possible to access the system’s information, diagnose the issue, and sometimes completely address the issue remotely. If the matter cannot be fixed remotely, some diagnostics programs allow the technician to determine what parts will be needed for the in-person repair, let the tech explain the situation by phone and thereby greatly reduce the time spent inside the customer’s home.
- Because remote diagnostics is new to most customers, it’s important to share easy-to-follow infographics, short commercial assets, and other digestible materials that clearly explain the benefits of this new offering. Have these materials readily available on your tablet or online for homeowners to review and build confidence in opting into this service.
Be overly responsive and aware of your customer’s concerns
- Knowing in-person service calls have been halted or delayed due to COVID-19, thorough communication and frequent touch bases with your customers are even more important. Looking ahead to heating season, continue to reinforce the benefits of remote diagnostics and remain ready to inform customers of alternative solutions and safety protocols.
Following these tips and procedures paves the way for sustained growth for digital dealers and provides homeowners another way to make sure their systems are running properly – whether or not in-person visits are an option.
Carri Norton, Portfolio leader for Nexia Diagnostics on behalf of American Standard Heating and Air Conditioning.
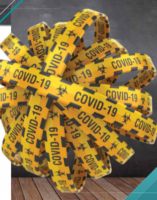
Marcum LLP today released the first annual Marcum National Construction Survey. Overall, the survey reflects a positive outlook by respondents about the current and future state of the industry, despite the COVID-19 pandemic. Influencing their optimism were the ability to secure financing for new projects and to find new sources for building materials, the respondents said. In Read more
Marcum LLP today released the first annual Marcum National Construction Survey. Overall, the survey reflects a positive outlook by respondents about the current and future state of the industry, despite the COVID-19 pandemic.

Influencing their optimism were the ability to secure financing for new projects and to find new sources for building materials, the respondents said. In addition, while job backlogs remain strong, they anticipate the need for diversified supply chains, new worksite safety protocols, and strategic planning to secure new contracts.
The survey was conducted in the first quarter of 2020 by Marcum’s national Construction Services group, a premier provider of accounting, tax, and advisory services to the construction industry. To account for the influence of the coronavirus crisis, responses were separated into pre- and post-March 15 periods.
Selected Findings
- 90% of respondents reported that their ability to receive project financing has increased or stayed the same as compared to last year.
- 47% of respondents reported banks required bonding on less than 20% of their jobs.
- 82% of pre-pandemic respondents projected either the same or higher backlogs for 2020.
- 67% of post-pandemic respondents projected either the same or higher backlogs.
- Just over a third of respondents (36%) predicted they will increase expenditures in the next year.
- 41% of pre-pandemic respondents chose “securing skilled labor” as the No. 1 threat to their businesses.
- 29% of post-pandemic respondents chose “lack of work” as the No.1 threat.
- 51% of respondents are increasing compensation to address the shortage of skilled labor.
- 85% of respondents said they were applying for loans under the Paycheck Protection Program (PPP) to mitigate the impact of the virus on their businesses.
- 56% of respondents said their top priority going forward is strategic planning.
- 37% of respondents have realized tax savings in the past year, from the Tax Cuts and Jobs Act of 2017.
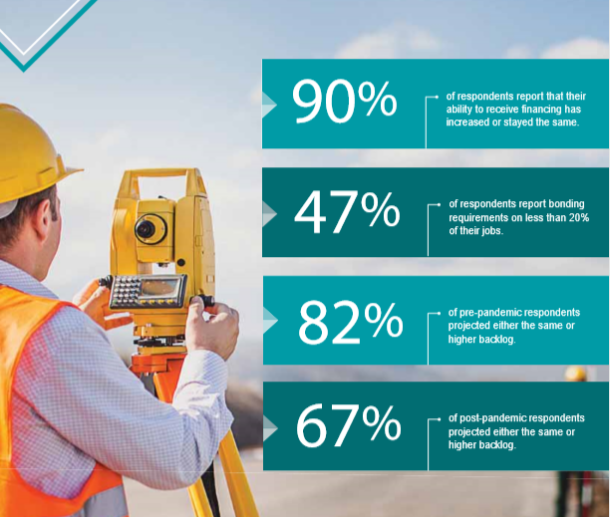
Joseph Natarelli, Marcum’s national construction industry leader, said, “The industry was well-positioned prior to the pandemic, even with a potential recession looming. Those going into COVID-19 with weaker balance sheets will be negatively impacted. We believe that as long as firms work with their internal teams and professional advisors to address labor safety issues and material sourcing, and have a pandemic plan in place, they will come out of this in good shape.”
Marcum Partner Roger T. Gingerich, regional construction leader for Ohio and survey project manager, said, “When we distributed the survey in early February, the epicenter of the novel coronavirus was in China, an important hub for steel production and general manufacturing, and that country’s subsequent economic shutdown had an immediate ripple effect on the U.S. construction industry that still persists. With the exception of several regional markets hardest hit by the pandemic, where job sites were closed, most U.S. construction workers were deemed essential and have continued to work. In alignment with these developments, positivity among survey respondents began to dip by mid-March.”
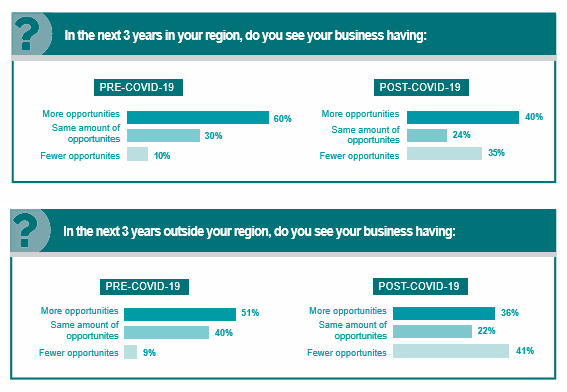
“The pre-COVID-19 economy was blissful for many contractors. A combination of strong job growth, technology-induced transformation, and healthier state and local government finances, rising incomes, consumer confidence, low inflation, and minuscule interest rates propelled construction spending higher. The post-COVID-19 economy is the mirror opposite,” wrote Marcum’s chief construction economist, Anirban Basu.
“The second quarter of 2020 is likely to prove the worst quarter of our economic lives. By February, the nation was already in recession. U.S. GDP declined 4.8% for the quarter… Often, construction is spared during the early stages of a broader economic downturn due to a combination of ongoing work and backlog. That didn’t happen this time… Construction’s recovery will be far more rapid if two things occur: 1) federal stimulus directed toward state and local governments to help them balance their budgets; and 2) a federal infrastructure investment package,” he said.

Recently, Mechanical Hub spoke with Mike Fowler, franchisee of Benjamin Franklin Plumbing and One Hour Heating & Air Conditioning in Charlotte, NC., about his business, COVID-19 and what it’s like to have the backing of such known company and brand. Now that the country had “reopened,” are there any different procedures in place for the Read more
Recently, Mechanical Hub spoke with Mike Fowler, franchisee of Benjamin Franklin Plumbing and One Hour Heating & Air Conditioning in Charlotte, NC., about his business, COVID-19 and what it’s like to have the backing of such known company and brand.
Now that the country had “reopened,” are there any different procedures in place for the company
FOWLER: In Charlotte, North Carolina, the reopening of the economy is in full effect. Our servicemen in the field are continuing to implement the safety procedures required by the CDC and our company, and those measures will be in place indefinitely. As we prepared to reopen our office for our office staff, there were a lot of things to consider. The call center and dispatch teams make up a large portion of our employees. We had to invest in plenty of materials to ensure the office staff could safely return.
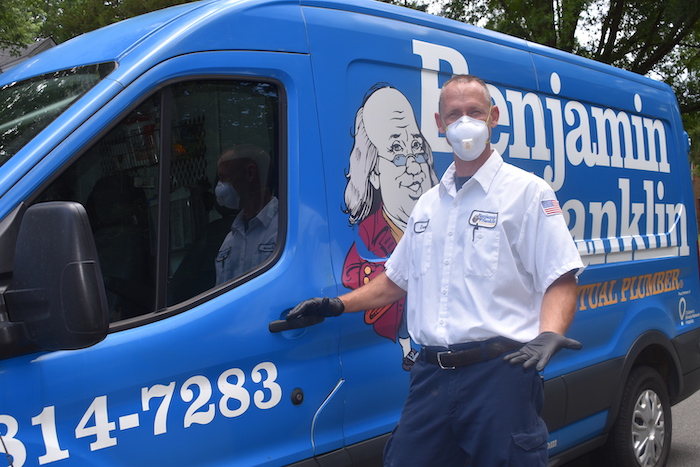
A Benjamin Frankling Plumbing employee displays the PPE used on the job.
We created new layouts and seating arrangements to ensure social distancing is observed, we have thorough cleanings daily for all high touch points, and we allocated a larger budget to purchase hand sanitizer, soap and paper towels since frequent hand washing is required. Our employees in the field have been practicing these safety protocols for months, so our employees in the office are now our primary focus as we adapt to the new normal. Our main priority is the safety of our employees, and throughout the process we strive to ensure they each feels comfortable and safe coming back in.
What protocols or procedures did Benjamin Franklin Plumbing implement as a result of COVID-19?
FOWLER: The health and safety of our customers and employees is paramount, so we implemented stringent protocols and procedures based on the latest information from the Centers for Disease Control and Prevention (CDC). By mid-March, we rolled out more strict guidelines to help ensure the safety of our staff and those we service. Since that time, we have required all employees to wear Personal Protective Equipment (PPE) including masks and gloves, as well as practice social distancing and regularly wash their hands and sanitize, especially when it’s required for us to enter a home to fulfill a project.
Since we are entering our customers’ homes, we require our employees to wear PPE the entire time they are working. We continue to supply all PPE to our staff members, so they’re fully equipped with safety gear while they’re on the job. We have asked all of our customers to inform us immediately if someone in their home becomes sick, and we’re being flexible and understanding when service appointments need to be rescheduled or cancelled due to illness. Thankfully we already had contactless payment options throughout our system, so the biggest protocol update in terms of customer interaction was utilizing FaceTime and videos for consultations and moving all of our documents to be signed and completed digitally.
Were there any advantages to being a franchisee during these uncertain times?
FOWLER: Absolutely. While we were deemed as an essential business and could continue to operate while many businesses could not, there were a lot of necessary changes and we were still impacted. Our franchisor, Authority Brands, is the parent company of seven leading home service franchisors, America’s Swimming Pool Company, Benjamin Franklin Plumbing, The Cleaning Authority, Homewatch CareGivers, Mister Sparky Electric, Mosquito Squad, and One Hour Heating and Air Conditioning.
The corporate team has always excelled in providing strong marketing, technology and operational support to our business, and over the past few months, their exceptional leadership and guidance helped us stay afloat.They kept us up-to-date with everything going on throughout the pandemic, from COVID-19 safety procedures and regulations to guidance for applying for government relief such as the Paycheck Protection Program. We’re grateful to have had ongoing communication with them over the past few months, and they continue to play a big role in keeping us informed and providing us with knowledge and resources.
What do some aspects of the business model blueprint look like at Benjamin Franklin Plumbing?
FOWLER: Being part of a franchise system and being surrounded by a strong network of business owners across the United States proved to be invaluable as we all navigated through the unknown. Benjamin Franklin Plumbing already had a Franchisee Leadership Team (FLT) established prior to the pandemic, and it exists to continuously improve our brand as a whole with systemwide collaboration and ongoing communication.
The motto ‘working for yourself, but not by yourself’ is echoed from all aspects of the Benjamin Franklin Plumbing franchise, and forming relationships with both the home office and fellow franchisees, in addition to the support of my family and the communities we operate in, continues to propel my business forward.
I’ve been a franchisee with the company since 2003 in Charlotte, North Carolina and I’m proud of how we’ve molded the proven business model from Benjamin Franklin Plumbing to fit our community. Everything starts with marketing. We have a dedicated marketing staff that executes monthly initiatives to ensure the call center receives calls.
We take training very seriously, and every new hire—whether it be as a marketing team member, accountant, a dispatcher or a service plumber in the field—goes through intensive training to ensure our customers experience a seamless process from start to finish. We’ve needed to change how some things are done over the past few months, for example conducting interviews through FaceTime, but with a strong structure for our business already in place, we’ve continued to provide services locally with the support of our franchisor.
What types of investments are being made by Benjamin Franklin Plumbing to ensure better success and continued growth?
FOWLER: Through the FLT, Benjamin Franklin Plumbing is always listening to its franchisees and implementing enhanced operational procedures as needed. They invest in the tools we need as franchisees to operate our business successfully.
For our business in Charlotte, we like to invest in our community both by giving back through charitable efforts, but also investing in the next generation of the workforce through our best-in-class training programs. With the unavoidable shortage of plumbers, we’re always working to educate those looking for their next career about the opportunity to join our team.
Our services were deemed as essential throughout the pandemic because, put simply, our community needs us as much as we need them. With the support of our franchise system and our dedicated employees, we continue to grow.